在庫管理を効率化する4つの方法 よくある課題の解決策も成功事例つきで解説
公開日:2024年03月29日
最終更新日:2025年04月21日
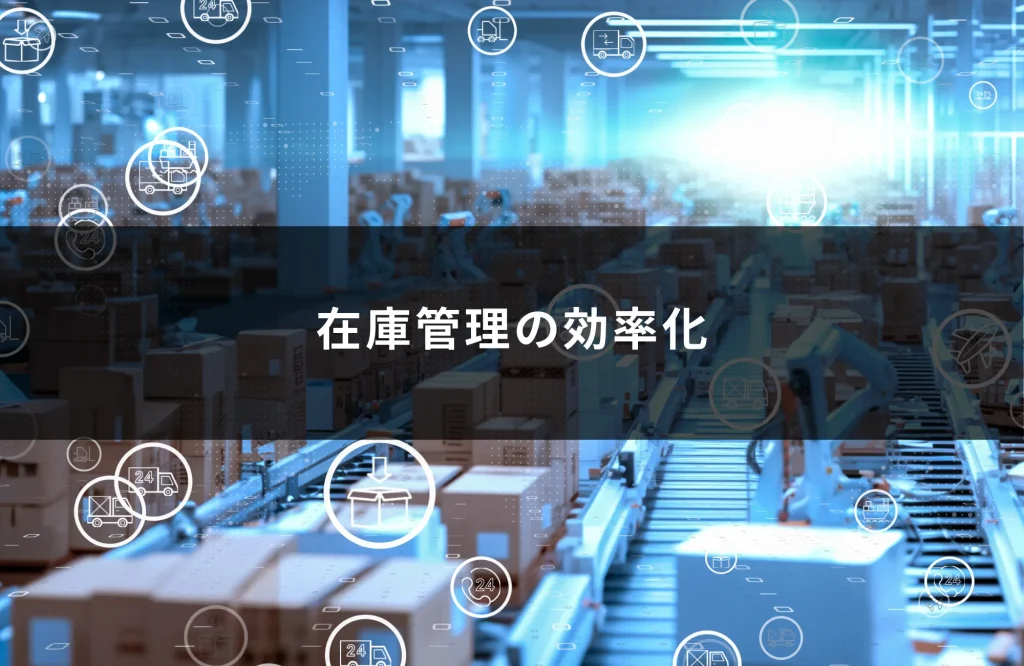
在庫管理の効率化は、コスト削減や業務負荷の軽減に直結する重要な課題です。在庫が過剰だと管理コストが増え、不足すると機会損失につながります。
これらは紙・エクセルによる在庫管理が原因と思われがちですが、システムを入れるだけでは解決できない場合もあります。
本記事では、製造業における在庫管理の効率化を行う具体的な方法を、成功事例も合わせて解説します。
在庫管理とは
在庫管理とは、企業が保有する商品や資材を適切に管理し、安定した供給やコスト削減を目指す業務です。
在庫が適正量に対して少ないことを在庫不足、余剰にあることを過剰在庫と呼びます。在庫不足と過剰在庫は企業の経営に悪影響を与えるため、在庫管理を効率化し、適正在庫を維持することが重要です。
在庫管理が企業経営に与える影響
在庫管理が適切に行われている場合と、そうでない場合では企業経営に以下のような影響を与えます。
◯適切な在庫管理 | △不適切な在庫管理 | |
コスト管理 | 保管コストや調達コストを削減できる | 過剰在庫による保管コスト増加や、緊急調達によるコスト増加 |
売上・利益 | 欠品を防ぎ、販売機会を最大化できる | 在庫不足で販売機会を逃し、売上が減少する |
業務効率 | 倉庫作業の効率が向上し、人件費も削減できる | 倉庫作業の混乱やミスが増え、業務の効率が低下する |
顧客満足度 | 商品供給が安定し、顧客の信頼を獲得できる | 欠品が発生し、顧客からの信用を失う可能性がある |
資金繰り | 在庫回転率が向上し、キャッシュフローが改善する | 資金が在庫に固定され、資金繰りが悪化する |
リスク管理 | 需要変動に柔軟に対応し、リスクを最小限にできる | 急な需要変動に対応できず、機会損失や廃棄リスクが高まる |
在庫管理は従業員の業務負荷、コスト、顧客満足度など、企業を安定的に運営する上で重要なさまざまな指標に影響します。
在庫管理を効率化するメリット
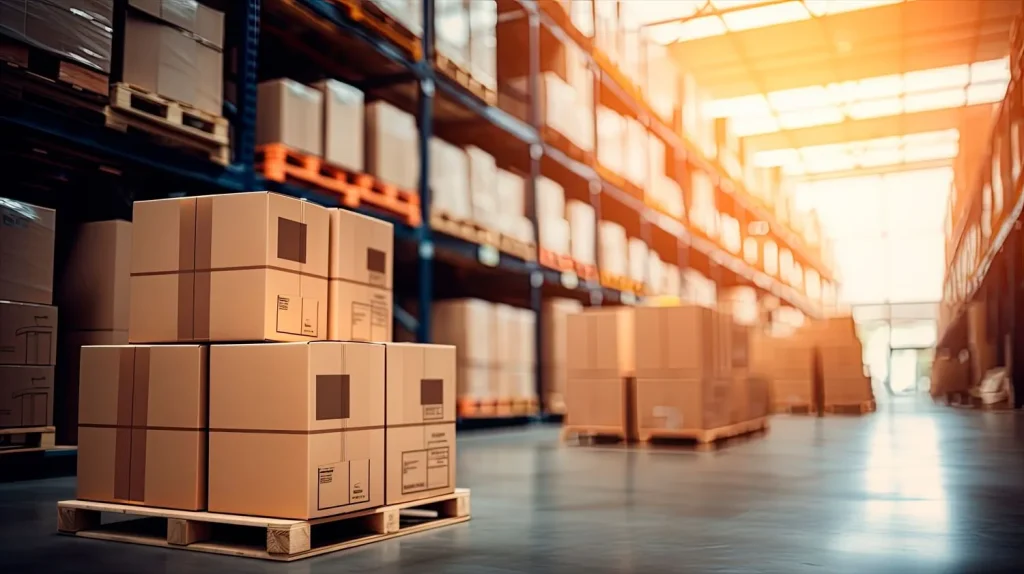
在庫管理を効率化すると、コスト削減、業務負荷の軽減、顧客満足度の向上などさまざまなメリットを得られます。また、適正な在庫量を維持でき、資金固定化の防止や資金効率の改善にもつながります。
コスト削減
在庫管理を効率化し、適正在庫を保てるようになると、不要な在庫の削減や無駄な発注を防止し、利益率を向上できます。過剰在庫による保管費や廃棄ロスも減少し、在庫コストも抑えられます。
また、欠品による緊急発注の発生を防ぎ、割高な仕入れを避けられると、調達コストを低減できる可能性もあります。
業務負担の軽減
在庫管理の効率化を進めるには、手作業やエクセル手入力などの非効率な作業の削減が重要です。アナログ作業を減らし、手作業による在庫チェックや発注管理の手間を削減すると、従業員の負担が軽くなります。
特に在庫管理において、従業員の大きな負荷になるケースが多い業務が「棚卸し」です。棚卸し作業を効率化し、短時間で終えられるようになると、従業員は本来の業務に集中できるようになります。その結果、業務全体の生産性向上が期待できます。
顧客満足度の向上
在庫の適正管理で欠品を防ぎ、迅速な出荷が可能になると、顧客満足度の向上が期待できます。特に受注生産や小売業では、在庫不足による販売機会の損失を防ぎ、安定供給を維持することが重要です。顧客の信頼を獲得し、リピート率が向上すれば、製造業としての競争力の強化にもつながります。
資金効率の改善
過剰在庫を減らし、必要な在庫を適切に保つことで、資金の流動性が向上します。余剰な在庫に資金を固定せず、他の重要な投資や運営資金に回せるため、財務状況の健全化にもつながります。また、適切な発注サイクルの管理により、キャッシュフローを安定させることも可能です。
在庫管理が非効率になる原因(よくある課題)
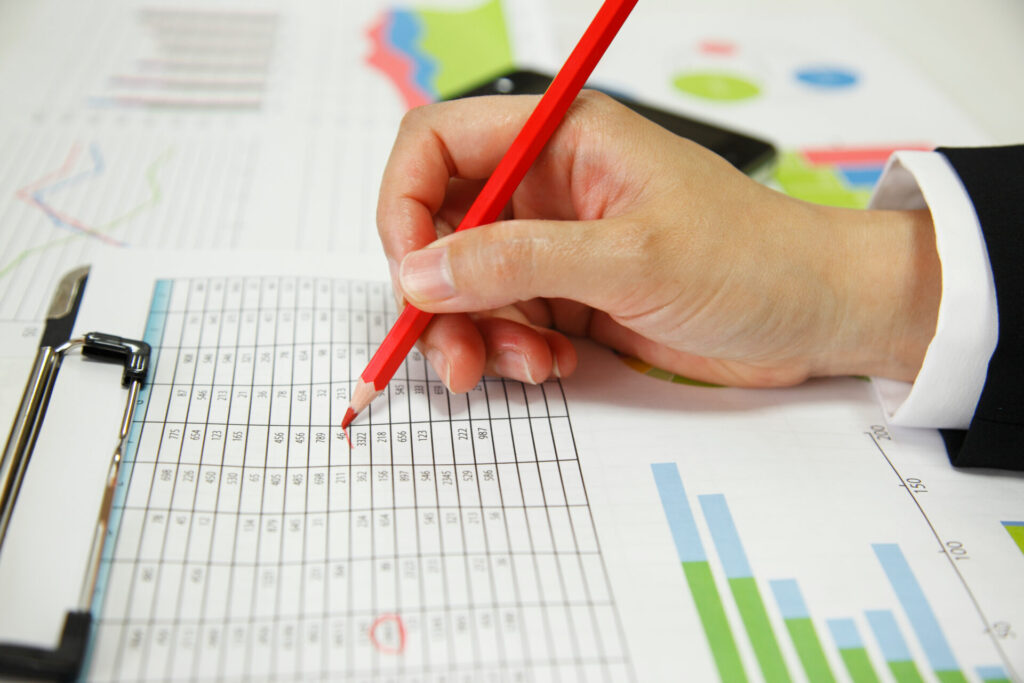
在庫管理が非効率になる原因は、次の5つです。
- 紙やエクセルによる手間・人的ミスが多い
- 在庫情報がリアルタイムに把握できない
- 他部門との情報共有が十分でない
- 棚卸しの工数・負荷が大きい
- 倉庫の導線や環境が悪い
これらの課題を理解し、適切に対策を講じることが、効率的な在庫管理の第一歩となります。
紙・エクセルによる手間・人的ミスが多い
紙やエクセルでの在庫管理は、データの入力や更新に多大な時間と労力がかかります。また、誤入力や記録漏れなどのヒューマンエラーも起きやすくなります。
代表的なアナログな在庫管理方法として、紙の棚札に入出庫を記録し、エクセル在庫管理表へ転記する方法があります。この運用には、棚札への記入漏れや書き間違い、エクセル手入力時の読み間違いや入力ミスなど、人的エラーが発生しやすい作業が多くあります。
こうしたヒューマンエラーが積み重なると、在庫管理の正確性が損なわれます。
在庫情報がリアルタイムに把握できない
在庫の保管場所が分散していたり、リアルタイムで情報更新されていなかったりすると、正確な在庫把握が難しくなります。このような状況の現場では、発注や生産のたびに倉庫へ在庫を確認しに行く等、さらに非効率な作業が発生しやすくなります。
この課題は、紙とエクセルで在庫管理する企業はもちろん、システムで在庫管理をしている場合でも起きる可能性があります。システム上の在庫情報の更新を、事務所PCで行っているケースがあるためです。これでは現場で即座に入出庫データを更新できず、在庫のリアルタイム把握ができません。
他部門との情報共有が十分でない
在庫情報は、現場担当者以外にも共有すべき部門が複数あります。よくある例は、現場担当者が在庫状況を熟知していても、発注管理担当者が最新の情報を把握できないケースです。これでは正確な発注ができず、さらなる在庫差異が生まれてしまいます。
紙やエクセルでの在庫管理は、複数の担当者との情報共有に不向きなツールです。そのため、どうしても都度在庫を現場に確認する手間が発生します。その結果、発注遅れや在庫の二重計上などの問題が発生するケースが多々あります。
棚卸しの工数・負荷が大きい
前述のような非効率な在庫管理が積み重なると、棚卸工数も膨らみます。実在庫と記録が一致しない場合の原因特定や、在庫数の修正の手間が増えるためです。
また、紙・エクセルで棚卸しをする企業だと、事前に棚卸表を数百枚印刷する等、事務的な工数も多くなりがちです。
倉庫の導線や環境が悪い
倉庫内の在庫の保管方法や作業環境も、在庫管理の効率性に影響します。例えば、頻繁に出庫する原材料が倉庫の奥にあると、ピッキングの手間が増えます。また、ピッキング作業台が暗く、計量器の数量を見間違えやすいなど、環境面に課題がある企業もあります。
在庫管理を効率化する4つの方法
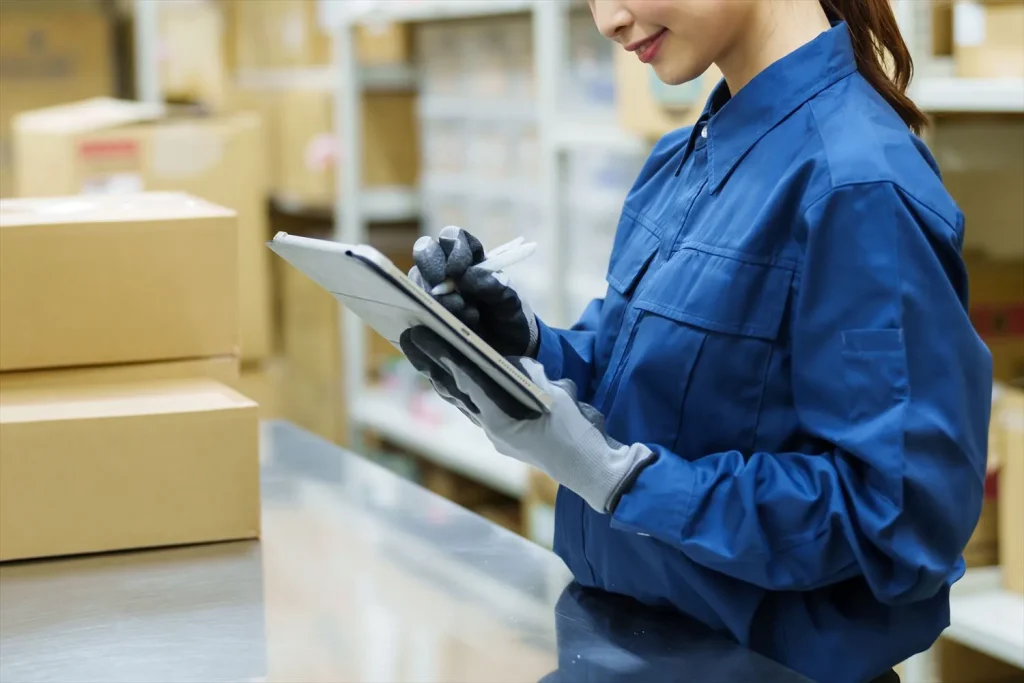
在庫管理の効率化には、倉庫の導線がスムーズで作業しやすく、関係者がリアルタイムに正しい在庫情報を把握できることが重要です。
それらを実現し、在庫管理を効率化する方法として、さまざまな手法やツールがあります。今回は以下の4つの観点から表にまとめました。
- システムやIoT技術の導入
- 在庫管理手法の活用
- 作業方法の改善
- レイアウトの改善
大きな投資が必要な方法もあれば、運用ルールの変更などで効率化できる場合もあります。自社の状況に合わせて、組み合わせて利用します。
システムやIoT技術の導入
在庫管理システムの導入は、在庫管理の効率化において、最も高い効果が期待できます。人的ミスや工数を減らしたうえで、在庫の正確な管理が可能となります。また、他部署でも同じデータベースを共有できるようになるメリットもあります。
それぞれのシステムの特徴を表にまとめると以下のようになります。
名称 | 機能・特徴 |
在庫管理システム | 在庫のリアルタイム可視化入出庫管理の自動化(バーコード/RFID連携)在庫異常のアラート通知 |
ERP | 在庫、販売、調達、生産の統合管理部門間のデータ共有による業務効率化在庫コストの最適化 |
MRP | 生産計画に基づいた部品・材料の在庫管理必要なタイミングで適量を確保(過剰在庫・欠品防止)生産スケジュールと連携 |
EDI | サプライヤーとの電子取引の自動化発注・納品データのリアルタイム更新誤発注・入力ミスの防止 |
自動倉庫管理システム | ロボットやAGV(無人搬送車)による自動ピッキング高層ラックの活用で倉庫スペースを最適化作業員の負担軽減 |
販売管理システム(POS連携) | 店舗やECの販売データと在庫をリアルタイムで同期需要の変動に応じた在庫補充を最適化欠品・過剰在庫の防止 |
気軽に導入しやすいものは、在庫管理システムです。近年は、初期費用を抑えて導入できるクラウド型の在庫管理システムも増えてきており、中小・中堅企業でも検討しやすくなってきています。
→ 在庫管理システムの比較、メリット・デメリット、導入手順はこちら
現場で在庫情報を即座に更新できる「IoTツール」の連携活用もおすすめです。紙・エクセル業務を、QR・バーコード管理やRFIDなどのIoT技術に置き換えていくと、人的ミスや工数を削減できます。また、リアルタイムな情報更新も可能となり、常に在庫差異が少ない状態で管理できるようになります。
在庫管理手法の活用
在庫管理や発注の手法の見直しも、在庫管理の効率化には有効です。発注方式や管理方式を含め、代表的な手法と特徴は以下のとおりです。
名称 | 機能・特徴 |
定量発注方式 | 在庫が一定の基準値を下回ると発注する方式発注量は常に一定で、発注頻度は需要に応じて変動需要が安定している商品に適している |
定期発注方式 | 決まった周期(例:毎週・毎月)で発注を行う方式発注量はその時点の在庫状況に応じて変動発注作業のスケジュール管理がしやすい |
ロケーション管理 | 在庫の保管場所を明確にし、ピッキング作業を効率化高頻度使用品を取り出しやすい位置に配置倉庫のスペースを最適化し、無駄な移動を削減 |
先入れ先出し | 先に入庫したものから順に出庫する方式食品や消費期限のある商品に適している在庫の劣化や廃棄ロスを防ぐ |
ダブルビン方式 | 2つの容器を使い、一方が空になったら補充する方式簡単な管理で運用でき、小型部品や消耗品に適する欠品を防ぎつつ、過剰在庫を抑えられる |
ジャストインタイム | 必要なものを、必要な量だけ、必要なタイミングで供給在庫コストを最小限に抑えられるが、供給の遅延リスクがある生産や販売の変動に柔軟に対応できる |
扱う製品や企業規模によって、適切な在庫管理の手法は変わります。多くは自社の運用方式の見直しにより利用できます。一方、ジャストインタイムのように、サプライヤーの協力が必要なものもあります。
作業方法の改善
ピッキングや在庫保管などの作業方法を見直すことも、在庫管理の効率化には重要です。作業を効率化することで、属人化を防ぎ、業務負荷を低減できます。
名称 | 機能・特徴 |
作業の標準化 | 作業標準手順書(SOP)の整備チェックリストの導入業務の属人化を防止 |
作業環境の改善 | 5S(整理・整頓・清掃・清潔・しつけ)の徹底人間工学の導入動線の効率化 |
自動化の導入 | RFIDなどのIoTツール活用AGV(無人搬送車)やコンベアの導入ロボットピッキングシステム |
作業の標準化や作業方法の最適化によって、在庫管理業務にかかる時間を削減できます。また、最新の倉庫管理システムとロボットの連携により、入出庫を全自動化させている企業もあります。
参考記事:在庫管理の自動化とは?中小企業こそ必要な理由と失敗しないシステムの選び方
レイアウトの改善
倉庫のレイアウト改善も、在庫管理の効率化につながります。以下のような観点を持って、レイアウトを見直すことが有効です。
名称 | 活用例 |
ABC分析に基づく配置最適化 | Aランク商品を出入口付近に配置Bランク商品は中間エリアに配置Cランク商品は奥に配置 |
動線の最適化(SLPの活用) | 一方通行の動線設計ピッキング順に沿った配置通路幅の適正化 |
ピッキングエリアの分割 | 担当エリアを分けて、作業者の移動距離を削減在庫状況に応じて商品配置を変え、作業効率を向上ピッキング作業を一箇所で集約し、作業負担を軽減 |
特に、在庫の品目が依然と比較して増加している場合は、無駄な動線が発生している可能性があります。定期的にレイアウトを見直すことが必要です。
在庫管理を効率化する際の注意点
在庫管理の効率化は、コスト削減に直結します。しかし、単に在庫を減らすだけではなく、リスク管理や部門間の連携、継続的な改善が重要です。ここでは、在庫管理を効率化する上での注意点を解説します。
リスク管理を徹底する
在庫管理には、欠品や過剰在庫、サプライチェーンの混乱といったリスクが伴います。これを防ぐには、需要変動を考慮した安全在庫の設定が重要です。効率化を優先することで、過剰にリスクを取り過ぎていないか注意が必要です。
関係部門と連携する
在庫管理は生産管理部門だけでなく、営業や製造、調達部門とも密接に関わります。在庫管理の効率化により運用方法を変更する場合には、他部門への影響がどの程度あるかを確認しましょう。また、部門間の定期的なミーティングを設け、他の効率化の案がないか情報を収集することも重要です。
継続的に改善を行う
在庫管理の効率化は、一度の取り組みで完了するものではありません。KPIを設定し、在庫回転率や欠品率、保管コストなどの指標を定期的に見直すことが重要です。特に在庫の品目が変動した場合には、その状況での効率の良い運用方法を検討する必要があります。
参考:在庫管理の効率を測る指標
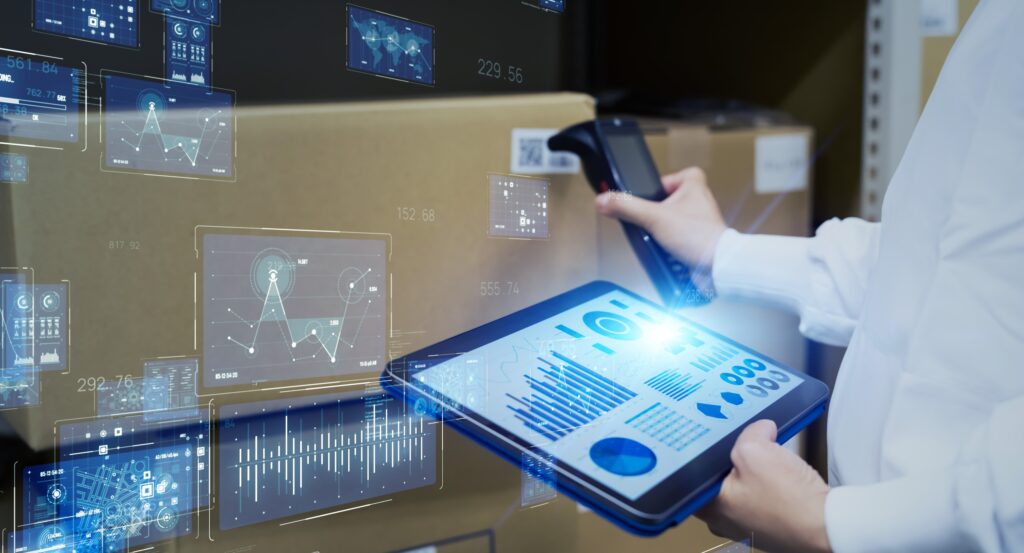
在庫管理の効率は、さまざまな指標で測れます。以下の代表的な指標で効果性を確認すると、改善を回しやすくなります。
在庫回転率
在庫回転率は、在庫がどれだけの頻度で入れ替わっているかを示す指標です。計算式は「売上原価 ÷ 平均在庫高」です。
この値が高いほど、在庫が効率的に活用され、過剰在庫のリスクが低くなります。ただし、回転率が高すぎると欠品のリスクがあるため、適正なバランスを取ることが重要です。
→ 在庫回転率を上げる方法を徹底解説!在庫回転期間との違いや計算式、適正在庫を保つコツとは?
在庫回転期間
在庫回転期間は、在庫が平均してどの程度の期間で消費・販売されるかを示す指標です。計算式は「365 ÷ 在庫回転率」です。
この値が短いほど、在庫が素早く流通しており、管理が効率的であると判断できます。一方で、期間が長い場合は、滞留在庫が増えている可能性があるため、見直しが必要です。
→ 在庫回転期間とは?在庫回転率との違いや在庫管理システムについて解説
在庫日数
在庫日数は、在庫が企業内に留まる平均日数を示す指標です。計算式は「(平均在庫高 ÷ 売上原価)× 365」です。
適正な在庫日数を維持することで、在庫過多による保管コストの増加や、在庫不足による販売機会の損失を防げます。適切な仕入れや販売計画を立てることで、在庫日数を適正に保つことが重要です。
→ 在庫日数とは?在庫回転率との違いや計算式、おすすめの管理方法を紹介
適正在庫率
適正在庫率は、現在の在庫が適正な水準にあるかを測る指標です。計算式は「(適正在庫数 ÷ 実在庫数)× 100」です。
この割合が低すぎると欠品リスクが高まり、高すぎると余剰在庫が発生し、資金効率が悪化します。需要予測や販売データを活用し、適正在庫を維持することが求められます。
→ 適正在庫を維持し、過剰在庫・欠品を解消する方法 計算方法から事例まで解説
在庫管理を効率化した成功事例
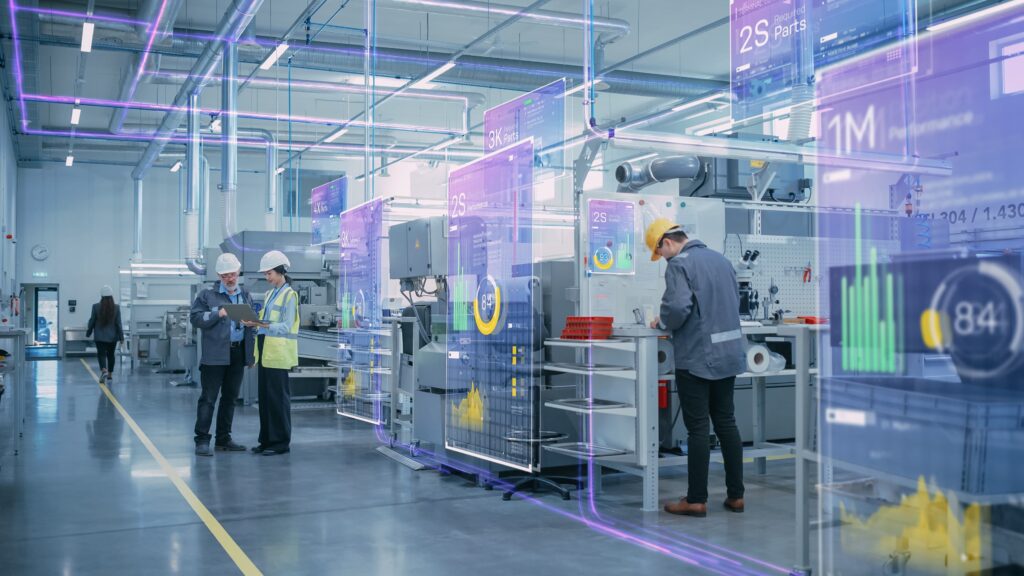
在庫管理の効率化を実現した企業の成功事例を紹介します。具体的な改善策の導入や在庫管理システムの効果的な活用方法など、さまざまなアプローチがあります。
外部倉庫の在庫も含めた一元管理に成功した事例
ある組立品メーカーではエクセルを中心に在庫管理を行っており、最新の在庫数を確認するためには現場に確認しに行くことが常態化していました。外部倉庫の在庫を確認するには、都度電話せねばならず手間でした。
そこで、外部倉庫も含めてハンディ端末を導入し、入出庫をバーコード管理化しました。外部倉庫も含めた入出庫データがリアルタイムに把握できるようになり、最新の在庫数がシステム上で誰でも確認できるようになりました。
詳細はこちら:在庫管理の一元化と属人化の課題を一挙に解決!ミスほぼゼロで顧客満足度向上
エクセルによる人的ミスを削減した事例
とあるボルトメーカーでは、鋼材の在庫管理を手書き帳票やエクセルで行っていました。しかし、手書き帳票などからエクセル在庫管理表を更新する作業は負担が大きく、ミスも度々起きていた。
そこで、在庫管理システムとバーコード管理を導入し、在庫や入出庫の管理をバーコード管理に移行。将来的には、手書きやエクセルによる作業をほぼゼロに移行できる見込みとなっています。
詳細はこちら:鋼材の在庫管理をバーコード管理化!リアルタイムの在庫把握&ロットトレースが可能に
在庫適正化で在庫金額を年間100万円圧縮した事例
金属加工を手掛ける企業では、かんばん発注方式による部品在庫管理を行っていました。しかし、購買担当が実在庫をリアルタイムに把握できず、二重発注や在庫過多の傾向にありました。
これらの課題を受け、在庫管理システムとハンディ端末を導入し、在庫を見える化。かんばん発注方式で管理していた部品のうち、都度発注でも管理できるものも多く見つかり、在庫金額を年間100万円圧縮することに成功しました。
詳細はこちら:在庫管理のシステム化に成功!リアルタイムな在庫管理で年間100万円の在庫削減
22種類の生産管理システムをランキングで比較
初期費用相場や選び方のポイントをチェック
生産管理システムをそれぞれの特徴や初期費用相場などで比較したい場合は、「生産管理システムランキング」も是非ご覧ください。生産管理システムは、自社の製品・生産方式・企業規模などに適したものを導入しないと、得られるメリットが限定されてしまいます。事前適合性チェックや生産管理システムを選ぶ前に押さえておきたいポイントも解説していますので、製品選びの参考にしてみてください。