かんばん方式の種類やメリット・デメリットをわかりやすく解説 在庫管理システムへの移行事例も紹介
公開日:2024年09月06日
最終更新日:2025年01月07日
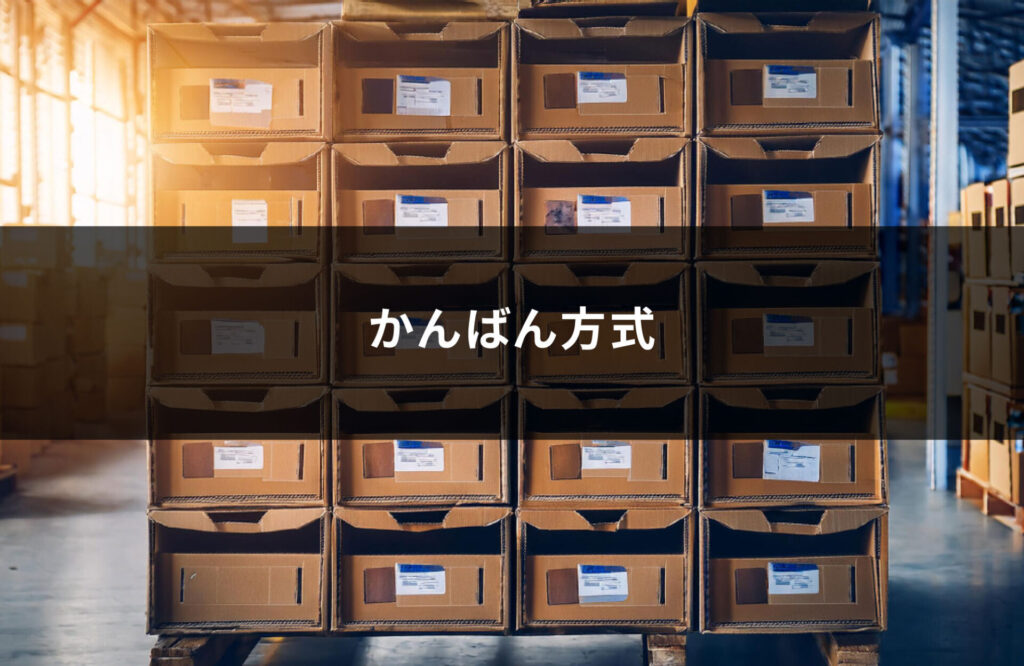
トヨタ生産方式にて生まれた「かんばん方式」という管理手法は、製造業において効率的な生産管理の実現に役立ちます。しかし、どの企業にもかんばん方式が向いているわけではありません。この記事では、かんばん方式の基本的な概念や種類導入メリット・デメリット、そして実践的な運用方法までを詳しく解説します。
最後には、かんばん方式から在庫管理システムに切り替え、在庫金額の圧縮に成功した企業事例も紹介します。
かんばん方式とは
かんばん方式は、「かんばん」と呼ばれるカードを用いて、部品や製品の生産・移動を管理し、製造業において効率的な在庫管理を目指す方式です。かんばん方式は、無駄をなくし、必要なものを必要なときに供給することを目的としており、トヨタ生産方式(TPS)の中心的な要素であるジャストインタイム(JIT)のツールとして広く知られています。
かんばん方式の仕組み
かんばん方式の基本的な仕組みは、ジャストインタイムの原則でもある「後工程引き取り(後補充生産、プル型生産)、つまり、需要に応じて生産を行うという考え方に基づいています。各工程は次の工程からの要請に応じて生産を行い、かんばんによって必要な資材や部品の数量が管理されます。
かんばん方式による在庫管理では、在庫が一定数以下になったらかんばんが外れ、そのタイミングで発注するという運用になります。基本的な考え方は、発注点を設定する定量発注方式と同じといえます。
かんばん方式の種類
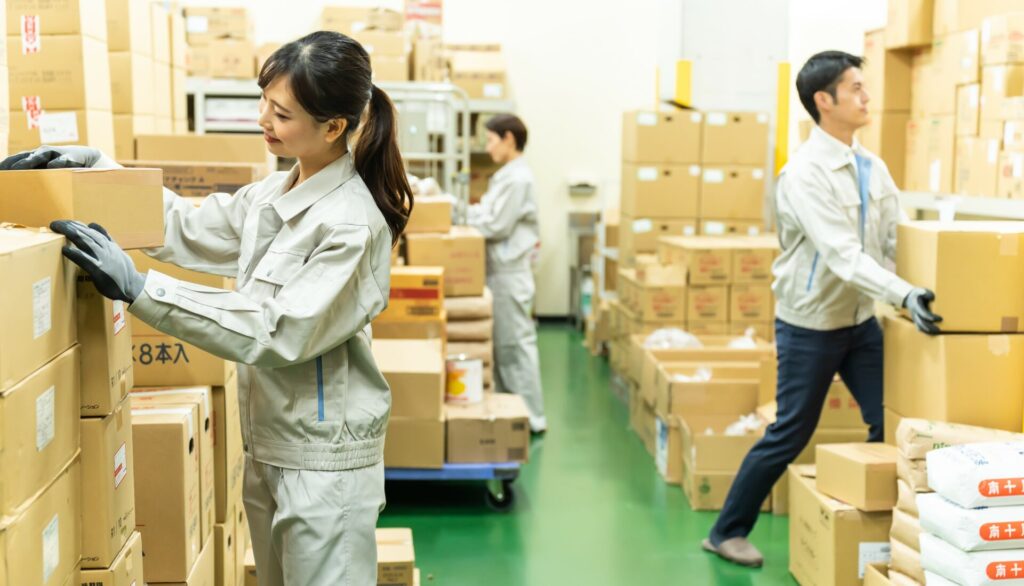
かんばん方式にはいくつかの種類があり、それぞれが異なる製造プロセスや物流に対応しています。代表的なものとして以下があります。
- 仕掛け(生産指示)かんばん
- 引き取りかんばん
- 特殊かんばん
仕掛け(生産指示)かんばん
仕掛けかんばんは、ある工程で次の工程に必要な部品の生産を指示するかんばんです。仕掛けかんばんは、さらに以下2種類に分けられます。
- 工程内かんばん
- 信号かんばん(三角かんばん)
工程内かんばんは、受注に基づき、後工程から品物を引き取られた際に、前工程に仕掛けかんばんをつけておくことで、前工程へ生産指示を出します。後工程から前工程への生産指示、あるいは発注書のような位置づけといえます。
信号かんばんは、ロット生産に使われます。在庫が一定数以下になったらかんばんを外し、ロット生産を行います。残りの在庫がなくなるタイミングで新たなロットが補充できるよう、リードタイムや所要量を鑑みる必要があります。発注業務における、発注点管理に似た考え方といえます。トヨタで使われていた信号かんばんは三角形だったことから、三角かんばんと呼ばれることもあります。
引き取りかんばん
引き取りかんばんは、後工程から前工程に部品や材料の移動を指示するかんばんです。引き取りかんばんは、以下の2種類があります。
- 工程内引き取りかんばん
- 外注部品引き取りかんばん
工程内引き取りかんばんは、同じ社内・工場内で使われます。一方、外注部品引取かんばんは、外注先に対する納入指示として使われます。後工程を自社、前工程を外注先ととらえ、部品を使用してかんばんを外したら、外注先への納入指示を行います。
特殊かんばん
かんばん方式の基本である、仕掛けかんばん・引き取りかんばん以外で製造が必要な場合は、特殊かんばんを使います。臨時かんばんとも呼ばれます。他にも、まとまった数量をあらかじめ生産する、プールかんばんなどもあります。
トヨタ生産方式で生まれたかんばん方式
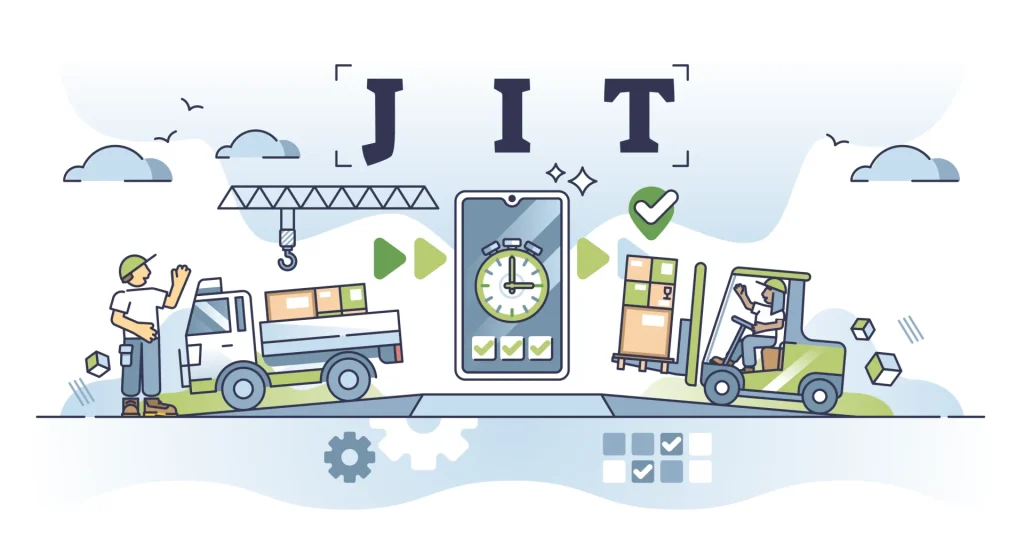
かんばん方式は、トヨタ生産方式(TPS)の中で使われる重要なツールです。TPSを実現するためには以下の2つの要素が重要となり、そのうち「ジャストインタイム(JIT)」という生産方法で使われるツールが、かんばん方式です。
■トヨタ生産方式の重要要素
かんばん方式の歴史
かんばん方式は、1960年代にトヨタ自動車で開発されました。トヨタが戦後の復興期に生産性を高めるためにジャストインタイムを導入し、かんばん方式も活用し始めたことで、製造ラインでの部品供給のタイミングの最適化を追求しました。ジャストインタイムにかんばん方式が加わったことで、トヨタ生産方式が定着していったともいえます。
かんばん方式は、トヨタ本社工場で試した後に全工場で採用され、協力会社まで展開していきました。トヨタの生産現場での成功を受けて、かんばん方式は徐々に他の製造業にも導入されました。現在、トヨタ自動車では電子かんばんも活用し、協力会社へかんばんデータを送る方式に移行しています。
MRPとの違い
かんばん方式とMRP(資材所要計画)は、いずれも在庫管理と生産管理の手法ですが、そのアプローチは大きく異なります。MRPは、需要予測に基づいて生産計画を立て、必要な資材や部品を事前に手配する「プッシュ型」の方式です。一方、かんばん方式は実際の需要に応じて生産を行う「プル型」の方式です。このため、かんばん方式は需要の変動に柔軟に対応できる一方、MRPは計画に基づいて進行するため、大量生産や長期的な計画が求められる場合に適しています。
かんばん方式のメリット
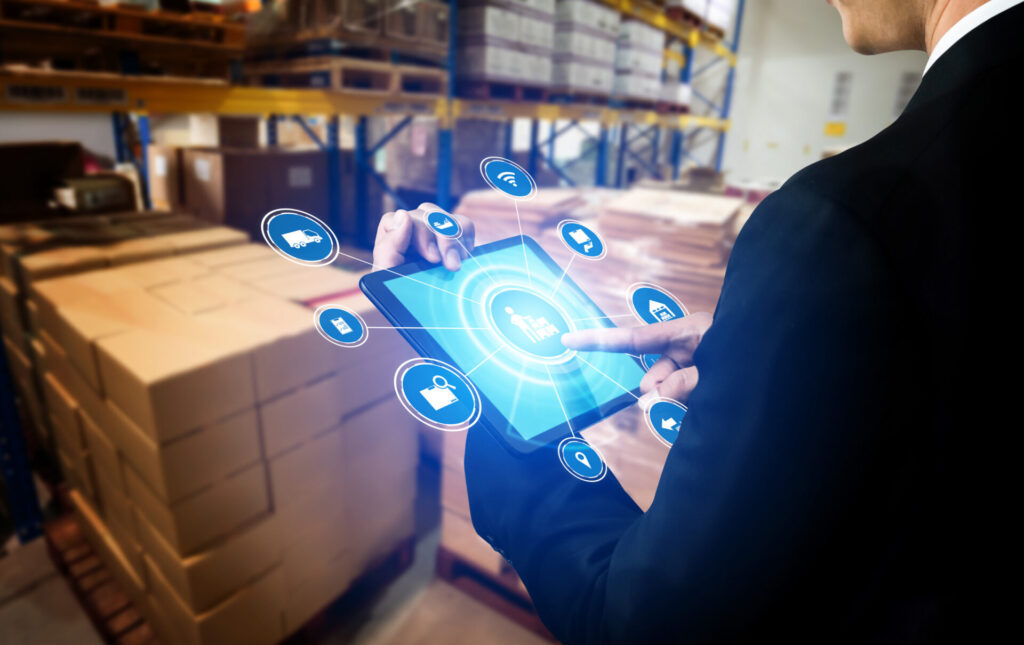
かんばん方式には多くのメリットがあり、多くの製造業で採用されています。
運用方法が簡単でわかりやすい
かんばん方式の最大のメリットの一つは、シンプルかつ直感的に運用できることです。各工程が次の工程の要求に応じて行動するという「プル型」の生産方式に基づいており、かんばんの指示に従うだけで効率的な生産管理が可能になります。これにより、従業員が特別なトレーニングを受けなくても、簡単にシステムを理解し、実行できる点が大きなメリットとなります。
安価に始められる
かんばん方式は、システム導入と比べて導入コストが低く抑えられる点が魅力です。かんばんや簡単な標識があれば十分であり、高価なソフトウェアや設備を必要としません。
在庫量を一定に保てる
かんばん方式は、必要な時に必要な量だけを生産するため、在庫量を一定に保つことができます。これにより、在庫の過剰や不足を防ぎ、効率的な資材管理が可能となります。
在庫管理の手間が最小限に抑えられる
かんばん方式を導入することで、在庫管理の手間を大幅に削減することができます。かんばんを利用することで、かんばんがある=要生産(要発注)ということがひと目でわかり、手動での在庫チェックや大きな在庫調整作業が不要となります。これにより、在庫管理にかかる人的リソースを削減し、生産活動に集中することができます。
かんばん方式のデメリット
かんばん方式には多くの利点がある一方で、特定の状況ではデメリットもあります。デメリットを理解することで、より効果的な運用が可能となります。
問題発生時の欠品リスクが大きい
かんばん方式は需要に応じた生産を行うため、問題が発生した場合の欠品リスクが高まります。例えば、部品の供給が遅れた場合や生産ラインにトラブルが発生した場合、次の工程で必要な部品が不足し、生産ライン全体が停止する可能性があります。そのため、迅速な対応とリスク管理が重要となります。
需要の変化に弱い
かんばん方式は、現在の需要に基づいて生産を行うため、需要の急激な変動には対応しづらいという欠点があります。需要が急増した場合には、必要な量の生産が追いつかず、納期に遅れが生じる可能性があります。このように、需要の変動が激しい業界では、かんばん方式の運用が難しいことがあります。
サプライチェーンへの依存
かんばん方式は、サプライチェーンの安定性に大きく依存しています。サプライヤーからの供給が遅れた場合や、物流に問題が発生した場合、生産ライン全体がストップするリスクがあります。このため、サプライチェーン全体の管理が必要です。
ヒューマンエラーが発生する
かんばん方式は、シンプルで効果的な運用が可能である反面、ヒューマンエラーが発生しやすいという側面もあります。かんばんカードの紛失や誤った指示が出された場合、全体の生産スケジュールが乱れてしまう可能性があります。したがって、適切な管理体制を整えることが重要です。
かんばん運用がうまくいかない理由
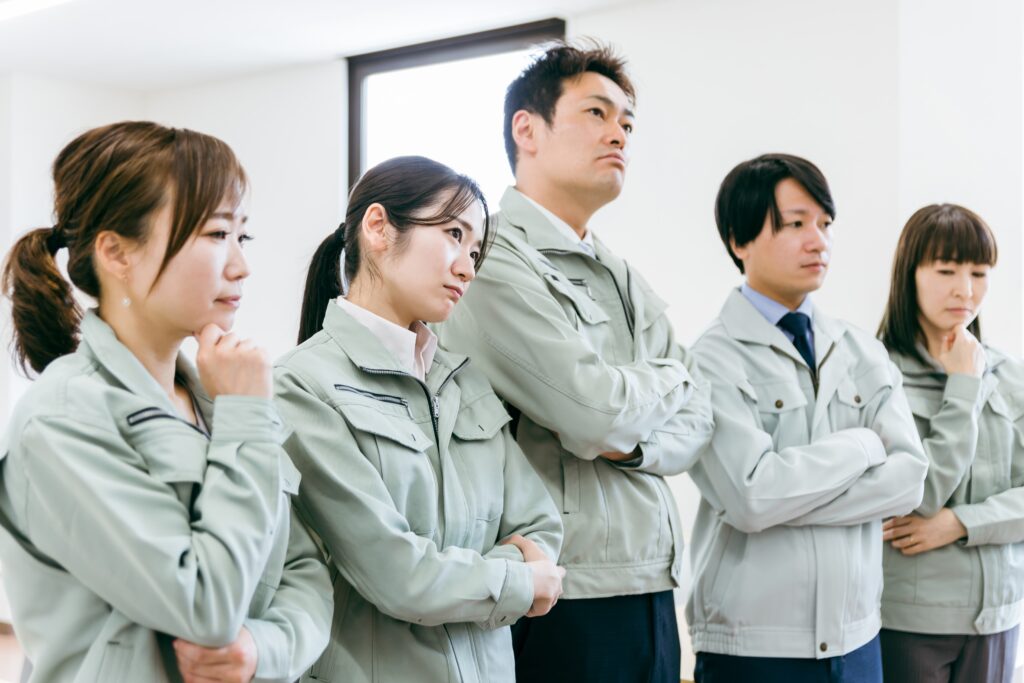
かんばん方式の運用がうまくいかない際は、いくつかの原因が考えられます。これらを理解し、対策を考えることで、かんばん方式をより効率的に運用することができます。
品質管理が不十分
かんばん方式がうまく機能しない大きな要因の一つは、品質管理が不十分であることです。部品や材料の品質が低い場合、次の工程で不良品が発生しやすくなり、生産の流れが滞ることがあります。
現場のルール周知が不十分
かんばん方式が失敗するもう一つの理由は、現場でのルール周知が不十分であることです。かんばんカードの正しい使い方や生産プロセスの流れについて従業員全員が十分に理解していないと、スムーズに運用できない可能性があります。
かんばん方式が向いていない生産方式
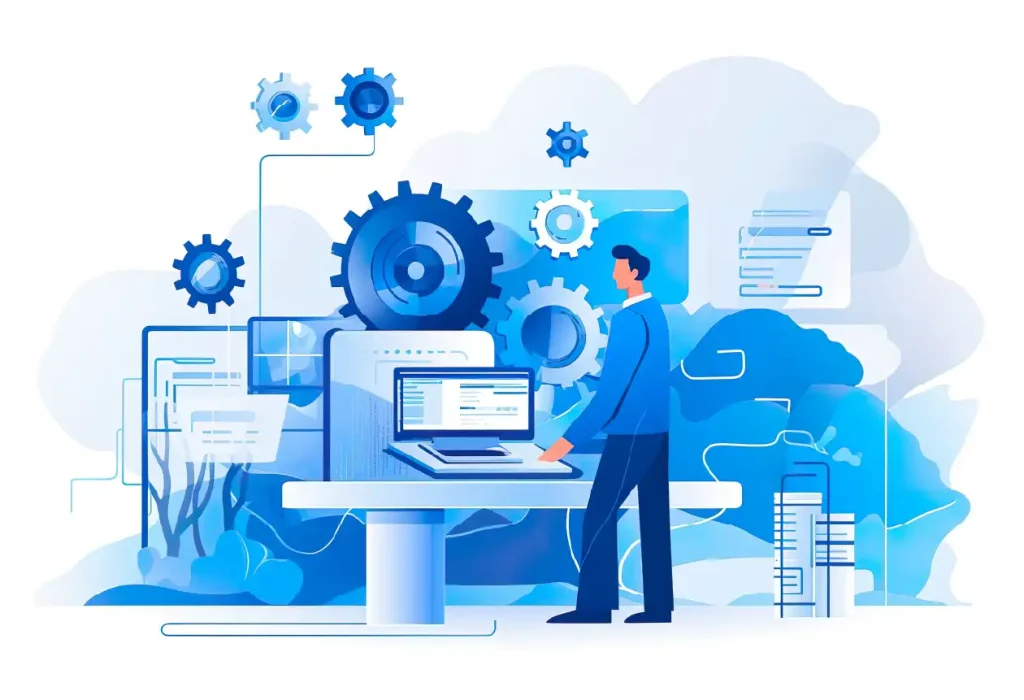
かんばん方式は、すべての生産方式に適しているわけではありません。特に、多品種少量生産や、需要の変動が激しい生産環境では、かんばん方式の効果が十分に発揮されないことがあります。こうした場合には、他の生産管理手法を検討することが重要です。
かんばん方式に代わる在庫管理システム
かんばん方式に代わって、在庫管理システムを導入するのもおすすめです。主要な在庫管理システムは、需要予測に基づいた在庫管理や、自動発注機能を持ち、かんばん方式の欠点を補うだけでなく、在庫管理のさらなる効率化も期待できます。例として、バーコード管理システムでは、在庫の動きをリアルタイムで追跡し、正確な在庫情報を提供することで、ヒューマンエラーを減少させることができます。
ある組立品業界の企業は、かんばん方式から在庫管理システムに移行し、在庫の見える化を進めたところ、実は常に在庫しなくても良い部品が多くあったとわかりました。かんばん方式は、一定の在庫を常に持つ運用なので、都度発注に切り替えることで在庫金額の削減が実現できます。実際に、当該企業は、在庫管理システムの導入後に年間在庫金額を年間100万円削減しました。
22種類の生産管理システムをランキングで比較
初期費用相場や選び方のポイントをチェック
生産管理システムをそれぞれの特徴や初期費用相場などで比較したい場合は、「生産管理システムランキング」も是非ご覧ください。生産管理システムは、自社の製品・生産方式・企業規模などに適したものを導入しないと、得られるメリットが限定されてしまいます。事前適合性チェックや生産管理システムを選ぶ前に押さえておきたいポイントも解説していますので、製品選びの参考にしてみてください。