適正在庫を維持し、過剰在庫・欠品を解消する方法 計算方法から事例まで解説
公開日:2024年05月17日
最終更新日:2025年02月20日
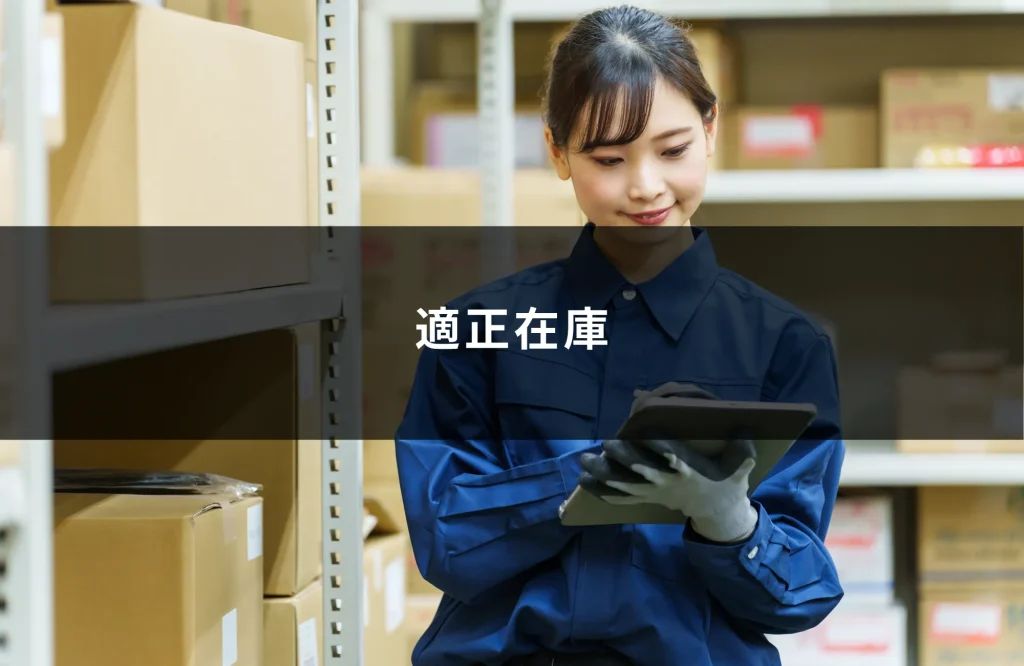
適正在庫を保つことは、コスト削減や需給のタイミングを的確に把握する上でとても重要です。過剰在庫による運転資金の拘束や、在庫不足による機会損失を防ぐため、まずは適切な在庫水準を知る必要があります。
本記事では、適正在庫を保つ目的や具体的な計算方法、適正在庫を維持する上での注意点などを解説します。記事の後半では、システム導入で適正在庫を正確に保てるようになった事例も紹介します。
適正在庫とは
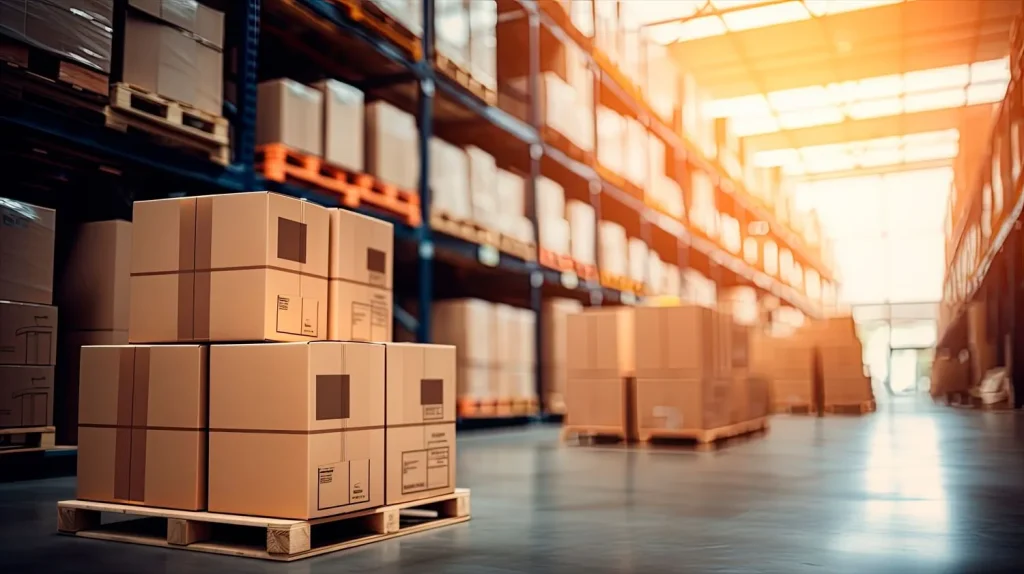
適正在庫とは、需要を満たしつつ過剰在庫や欠品を防ぐ最適な在庫量のことです。適正在庫を超える在庫は、過剰在庫や余剰在庫と呼ばれます。過剰在庫は在庫金額や保管コストを増やし、在庫不足は機会損失を生むため、適正在庫の維持は非常に重要です。
適正在庫を維持する目的
企業が適正在庫を維持する目的は主に次の6つです。
- 欠品防止:需要に対応し、販売機会の損失防止
- 過剰在庫の回避:不要な保管コストや廃棄リスクを低減
- キャッシュフローの最適化:在庫資金の適正化で財務健全性を維持
- 生産・調達の効率化:適切な発注・補充で業務の無駄を削減
- 顧客満足度向上:安定供給により信頼性を確保
- リスク管理:市場変動やサプライチェーンのリスクに対応
適正在庫を維持するうえで特に重要なのは、欠品防止、過剰在庫の抑制、そしてサプライチェーンリスクへの対応です。まず、欠品を防ぐことで販売機会の損失を回避し、顧客満足度を維持できます。特に製造業などのBtoB企業では、安定供給が取引先との信頼関係の維持につながります。
安全在庫との違い
適正在庫を考える上で「安全在庫」という概念も重要です。安全在庫とは、予期せぬ注文や納期遅延などに備え、一定量を確保しておく最低限の在庫です。適正在庫にはこの安全在庫分も含まれます。
サイクル在庫との違い
サイクル在庫とは、定期的な発注や生産のサイクルに従って維持される在庫のことです。これは、一定期間の需要に対応するために確保され、次の補充が行われるまでに消費されることを前提としています。安全在庫とサイクル在庫を組み合わせることで、製品ごとの適正在庫を算出します。
適正在庫の計算方法
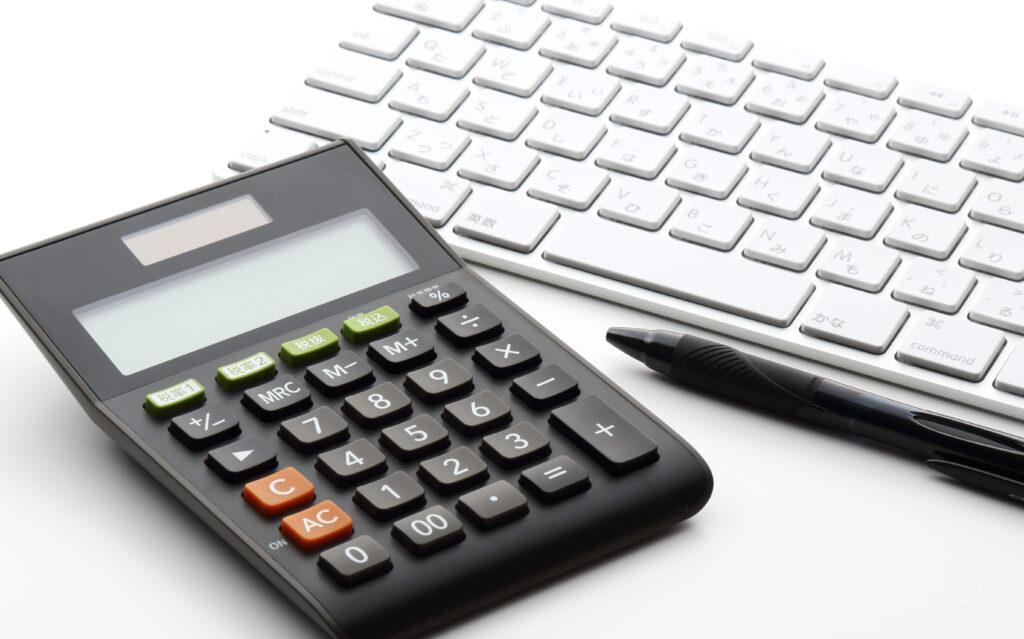
適正在庫には様々な計算方法があり、自社に合う適切な方法を選ぶ必要があります。基本的には、安全在庫とサイクル在庫を利用して計算するのが一般的です。
また、在庫回転率や需要数などを考慮する方法や、在庫金額をベースに算出する方法もあります。順に解説していきます。
安全在庫とサイクル在庫から算出
最も一般的な適正在庫の計算方法の一つは、「安全在庫」と「サイクル在庫」を合計する方法です。
適正在庫の計算式(安全在庫とサイクル在庫から算出)
適正在庫=安全在庫+サイクル在庫
前述の通り、安全在庫とは、予期せぬ需要の増加や納期遅延に備えた最低限の在庫です。安全在庫は以下の式で計算できます。
安全在庫の計算式
安全在庫 = 安全係数 × 平均使用量の標準偏差 × √(リードタイム+発注 or 製造間隔)
- 安全係数:予期せぬ需要変動や供給の遅れに対応するために設ける係数
- 標準偏差:データのばらつきを示す指標
- リードタイム:発注から納品までにかかる時間
※安全在庫の計算方法を、わかりやすく解説した記事はこちら
サイクル在庫は、以下の式で計算できます。
サイクル在庫の計算式
サイクル在庫=発注量(または生産量)÷2
サイクル在庫は、次の発注または生産までに消費される在庫の平均量を示します。発注後、在庫は最大になり、消費が進むにつれて減少します。次の補充時に再び増えるため、発注量の半分が平均的なサイクル在庫として算出されます。
例:1ヶ月に1度、100個製造する製品の場合…サイクル在庫:50個
ただし、季節変動の大きい業種や部材のリードタイムが前後する場合は、この計算式が合わない場合もあります。過去の出庫実績なども参考にしてください。例えば、原材料の仕入先が納入遅延を起こしやすいのであれば、サイクル在庫を半数より多めに見ておくなどの対応が必要です。
在庫回転率や在庫回転期間から算出
在庫回転率や在庫回転期間からも適正在庫を計算できます。
在庫回転率とは、一定期間で在庫がどれくらい入れ替わったかを表す指標です。在庫回転率を利用して適正在庫を算出する場合、以下の式を用います。
適正在庫の計算式(在庫回転率から計算)
適正在庫 = 年間売上原価(または消費量)÷ 目標在庫回転率
在庫回転率が低いと在庫が滞留していることを意味し、過剰在庫の発生による保管コストや廃棄リスクが増加します。一方で、回転率が高すぎると欠品が発生し、機会損失につながるため、バランスの取れた回転率を維持することが重要です。
在庫回転期間(商品回転期間、棚卸資産回転日数とも)は、在庫を売り切るまでの平均日数を表します。在庫回転期間を利用して適正在庫を算出する場合、以下の式を用います。
適正在庫の計算式(在庫回転期間から計算)
適正在庫=1日当たりの売上原価(または消費量)×目標在庫回転期間(日)
在庫回転期間が短いほど早いサイクルで在庫が効率的に回っており、長いほど在庫が滞留している状態です。業界の水準や自社の運用に適した在庫回転期間を決めることで、無駄のない在庫管理ができます。
また、各在庫品の在庫回転率や在庫回転期間を計算し、業界平均や類似製品と数値を比べることも一つの手です。一定の数値を基準としたうえで適正在庫を再検討すると、客観的に判断しやすくなります。
安全在庫と需要数から算出
安全在庫と需要数から算出する場合、以下の式を用います。
適正在庫の計算式(安全在庫と需要数から計算)
適正在庫=安全在庫+平均日次需要数×製造リードタイム
製造リードタイムとは、受注から製品化までの期間を指し、この間の需要をカバーするための在庫が必要になります。この計算は、最低限の安全在庫+製品化までの日数分をカバーする在庫数を適正在庫と考える手法です。過去の受注データを分析し、需要のばらつきを正しく把握することで、適切な在庫水準を維持できます。
交叉比率から算出
交叉比率とは、在庫がどれだけ利益を上げているかを示す指標です。スーパーやコンビニなどの小売業界で用いられることが多い傾向にあります。在庫の粗利益をもとに、以下の計算式で算出できます。
交叉比率の計算式
交叉比率=在庫回転率 × 粗利益率(粗利益÷売上高)
交叉比率が高い在庫は、効率よく利益を上げられているといえます。交叉比率を利用して、在庫回転率を算出し、適正在庫量を決定します。
適正在庫を決める際に+α で気をつけること
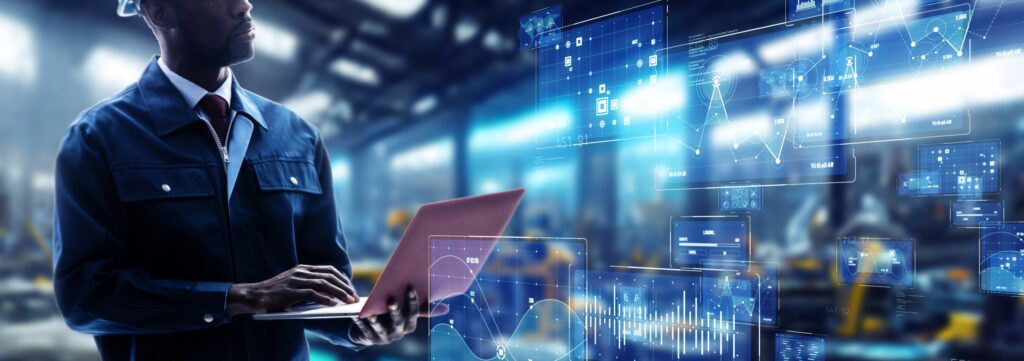
適正在庫は上記の計算で求められますが、さらに以下5点も考慮すると、実態に即した在庫管理ができます。
リードタイムの変動を考慮する
調達リードタイムが変動しやすい部品や原材料では、リードタイム変動も考慮する必要があります。リードタイムの変動が大きい原材料は、想定より多めに適正在庫を持つ判断も検討することをおすすめします。
特に、グローバルに調達を行う場合は、輸送遅延や供給不足のリスクが高まります。サプライチェーンの混乱に備え、適正在庫を適切に設定することが求められます。また、代替品や複数の仕入れ先から手配する場合がある原材料も、各リードタイムの把握が必要です。
製品ごとに優先順位をつける
生産への影響度やコストに応じて優先順位を設定すると、より効率的な在庫管理が可能です。すべての部品や製品を同じ基準で管理すると、管理工数が膨大になり、人的ミスの原因にもなりかねません。
例えば、主力製品の部品は生産を左右するため、在庫を厚めに確保する必要があります。一方、ねじやボルトなどの汎用品は、調達しやすいため最小限の在庫で運用できます。
具体的な優先順位の付け方としては、ABC分析がおすすめです。Aランクの部品は厳格に管理し、Cランクの部品は管理工数が少ない発注方式を検討することで、無駄な在庫を削減できるようになります。
→ ABC分析とは 製造業の在庫管理への具体的な活用方法、注意点や方法まで解説
需要変動を考慮する
製造業では、顧客からの受注や市場の動向によって需要が変動するため、適正在庫の維持には精度の高い需要予測が欠かせません。特に、自動車や電子部品業界では、モデルチェンジや新技術の導入によって需要が大きく変わることがあります。
過去の生産実績や販売データを基に、需要の増減に応じた適正な在庫量を設定することが重要です。
生産計画の変動を考慮する
製造業では、受注生産や見込み生産など、企業の生産方式によって在庫の管理方法が異なります。生産計画が変更されることも多いため、在庫の過不足を防ぐためには柔軟な管理が必要です。
特に、短納期対応が求められる場合は、部品の在庫を適切に確保しつつ、急な生産スケジュールの変更に対応できる体制を整えることが重要です。ERPや生産スケジューラを活用し、リアルタイムでの生産計画調整を行うと、適正在庫の維持がしやすくなります。
経営判断が必要な場合もある
重要部品などの一部在庫の適正在庫は、部門や部署だけではなく、会社全体で決める必要があります。経営層が、会社の理念や方針に基づいて適正在庫の指針を示す必要がある際は、横断的に管理していくことになります。
適正在庫を維持する方法
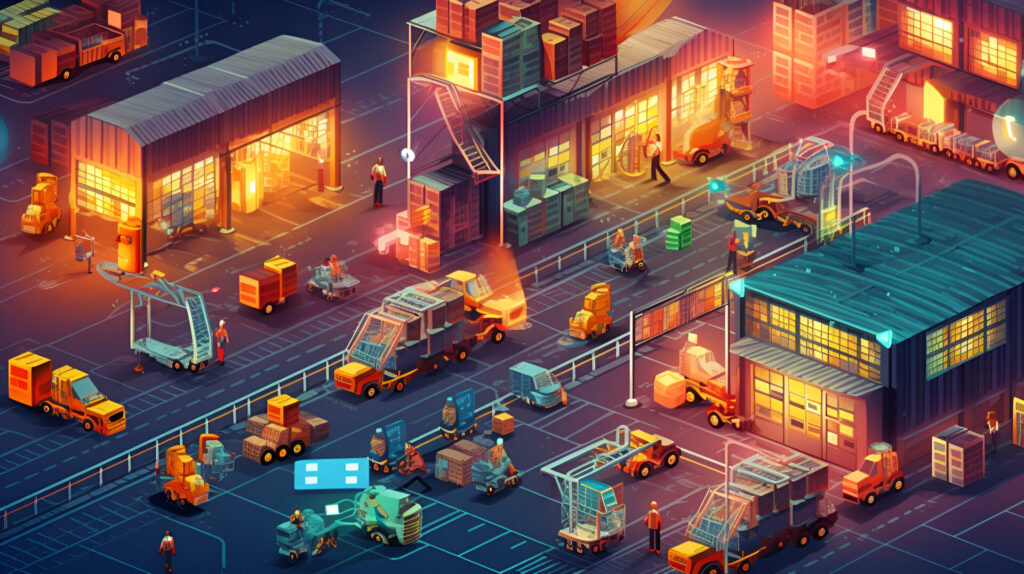
適正在庫を計算したあとは、常に適正水準を維持する必要があります。適正在庫を維持するためには、発注方式の見直しや製造リードタイムの短縮、需要予測の高精度化などが重要です。
発注方式を見直す
適正在庫を維持するために、定期発注と定量発注の2つの発注方式を上手く使い分けることが有効です。
一定期間ごとに発注する定期発注方式は、発注ごとに発注量を調整できるため、需要変動が大きい製品に適しています。一方、在庫が発注点を下回ったら発注する定量発注方式は、シンプルで管理工数も小さいため、低単価品や需要が安定している製品に適しています。
それぞれの発注方式の特性を活かすことで、需要の変動や供給の安定性に応じた柔軟な在庫管理が可能になり、適正在庫を維持できます。
リードタイムを短縮する
受注から製品化までのリードタイムが長いと、その間の需要に見合う在庫を確保する必要があり、過剰在庫になります。そのため、製造リードタイムを短縮させることで、適正在庫の維持に役立ちます。工程の改善や設備の増強、外注先との連携強化など、リードタイム短縮に向けた取り組みが重要です。
需要予測精度を向上させる
適正在庫を維持するには、正確な需要予測も効果的です。過去の販売実績データを分析し、季節変動や経済動向、販促施策の影響などを考慮できると、在庫管理や発注の計画も立てやすくなります。需要予測の精度が高ければ、より適正在庫を維持しやすくなります。
発注数量や発注タイミングを見直す
需要や仕入先の状況に合わせて、発注数量や発注タイミングを見直すことも重要です。最小発注単位を見直したり、発注サイクルや発注点を適切に設定したりすることで、過剰在庫や不足在庫のリスクを最小限に抑えられます。
在庫管理システムを導入する
適正在庫を維持するためには、在庫管理システムの導入が有効です。手作業での在庫管理では、需要予測や現在庫数把握の精度が低くなり、過剰在庫や欠品のリスクが高まります。一方、在庫管理システムを活用すれば、リアルタイムで在庫状況を把握し、適切な発注タイミングを自動計算できるため、過剰在庫を防ぎながら必要な分だけを確保できます。
適正在庫がなかなか保てない3つの原因&対策
適正在庫を維持しようと心がけていても、頻繁に欠品や過剰在庫が起きてしまうと悩む企業も少なくないかと思います。
適正在庫が保てない原因は、大きく分けて以下3点です。
- 需要予測や生産計画の精度や連携が不十分
- 受注数や在庫数を正確に把握できていない
- 定期的に見直せていない
適正在庫を維持するためには、受注数や生産計画、返品・不良品の扱いなど、様々な要素を考慮する必要があります。
需要予測や生産計画の精度や連携が不十分
適正在庫の管理では、受注や需要に基づく販売計画と、生産計画との連携が不可欠です。しかし、それぞれの精度が低かったり、在庫や発注の計画と連携できていないと、適正在庫に十分に活かせません。需要予測や生産計画の精度改善だけでなく、製造と購買の部門の連携強化も推進することをおすすめします。
受注数や在庫数を正確に把握できていない
適正在庫に課題感を感じている企業の多くが、受注数や在庫数の正確な管理ができていない傾向にあります。
受注内容変更の反映漏れなどで受注情報に誤りが出ると、発注数量や生産量の見込みが外れ、過剰在庫や欠品が発生してしまいます。正確な在庫数を把握できていない場合も、正確な発注ができなくなり、同様の事態を引き起こします。在庫数のズレは、日々の入出庫管理の漏れにくわえ、返品や不良品の反映漏れでも積み上がるため、日々の在庫管理でリアルタイムな管理が求められます。
これらの課題を解決するには、受注データの入力ミス防止や、在庫管理表(理論在庫)と実在庫の差が生まれないようにする対策が必要です。
定期的に見直せていない
製造業では、需要や調達環境の変化に応じて適正在庫の基準を定期的に見直すことが必要です。
例えば、製品の販売需要が減ってきているにもかかわらず、同じペースで製品を作り続けると、過剰在庫となってしまいます。需要予測の変動がないか定期的に確認し、適正在庫の水準を見直しましょう。
調達環境の変化の例では、サプライチェーンの状況が変わり、調達リードタイムが長くなっているケースがあります。調達リードタイムが長くなっているにも関わらず適正在庫が一定だと、想定より発注品の入荷に時間がかかることとなります。その結果、必要なタイミングに品物が届かず、欠品になりかねません。よって、仕入先との連携や情報交換を密に行い、市況の変化に合わせて適正在庫も調節する必要があります。
適正在庫の維持には在庫管理システムがおすすめ
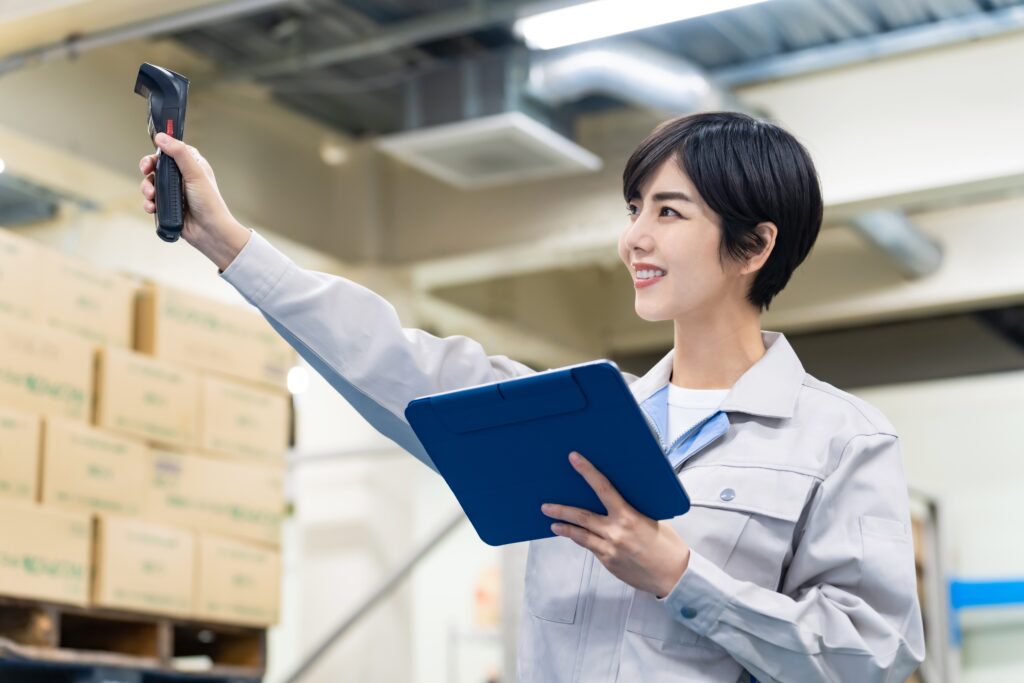
前述の通り、適正在庫を維持し続けるためには、生産計画と在庫データの一元管理や分析が必要です。そのためには、人手に頼らず効率的なデータ管理ができる在庫管理機能付きの生産管理システムがおすすめです。
在庫管理機能付きの生産管理システムには、適正在庫を維持するために必要な以下の機能があります。
- 在庫可視化・リアルタイム管理
- 入出庫管理
- 発注管理
- 生産計画
- 工程・進捗管理
- コスト管理
生産管理システムの最大のメリットは、在庫管理機能だけでなく、生産計画や工程管理、発注などの機能も揃っている点です。在庫管理を精緻化できるだけでなく、実在庫数と生産計画データをもとにした発注点管理も、1つのシステム内で完結できます。
生産管理システムで適正在庫を維持できるようになった事例
ある医薬品メーカーでは、生産管理システムで適正在庫の維持できる体制を実現しました。
同社は、リードタイムが長い原材料も扱っており、半年先まで先の将来在庫を計算して発注する必要があります。従来は、エクセルの生産計画と現在庫数を突き合わせ、手作業で発注量を計算しており、ヒューマンエラーをなかなか無くせずにいました。その結果、発注ミスによる欠品が度々起きるという課題がありました。
そこで、生産管理システムを導入し、生産計画と在庫数から将来在庫を自動計算する仕組みを導入しました。半年先の在庫予定数も見えるようになり、発注点を下回る見込みであれば発注するフローを確立し、発注ミスによる欠品がゼロになりました。
事例の詳細はこちら:将来在庫の自動計算で発注の負担・工数を削減!生産計画と在庫を紐づける管理を実現
22種類の生産管理システムをランキングで比較
初期費用相場や選び方のポイントをチェック
生産管理システムをそれぞれの特徴や初期費用相場などで比較したい場合は、「生産管理システムランキング」も是非ご覧ください。生産管理システムは、自社の製品・生産方式・企業規模などに適したものを導入しないと、得られるメリットが限定されてしまいます。事前適合性チェックや生産管理システムを選ぶ前に押さえておきたいポイントも解説していますので、製品選びの参考にしてみてください。