初期流動管理とは?ISO9001・IATF16949との関連、進め方のポイントも紹介
公開日:2025年03月26日
最終更新日:2025年03月26日
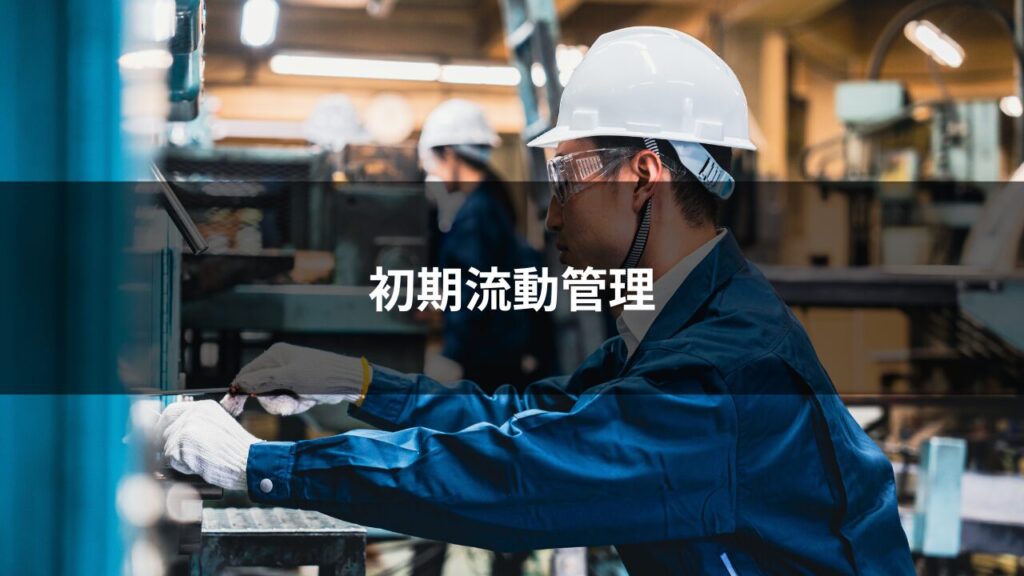
初期流動管理は、量産移行時の品質と安定性を確認するための最終チェックであり、新製品の立ち上げや工程変更時に欠かせないプロセスです。本記事では、初期流動管理の基本概念から、その目的、進め方、QMS規格との関連までを網羅的に解説しました。さらに現場の不具合リスクを事前に把握し、初期流動管理の効果を高めるポイントも紹介します。品質トラブルを未然に防ぎ、安定した量産立ち上げを実現するためのヒントを提供します。
初期流動管理とは:量産移行の最終チェック
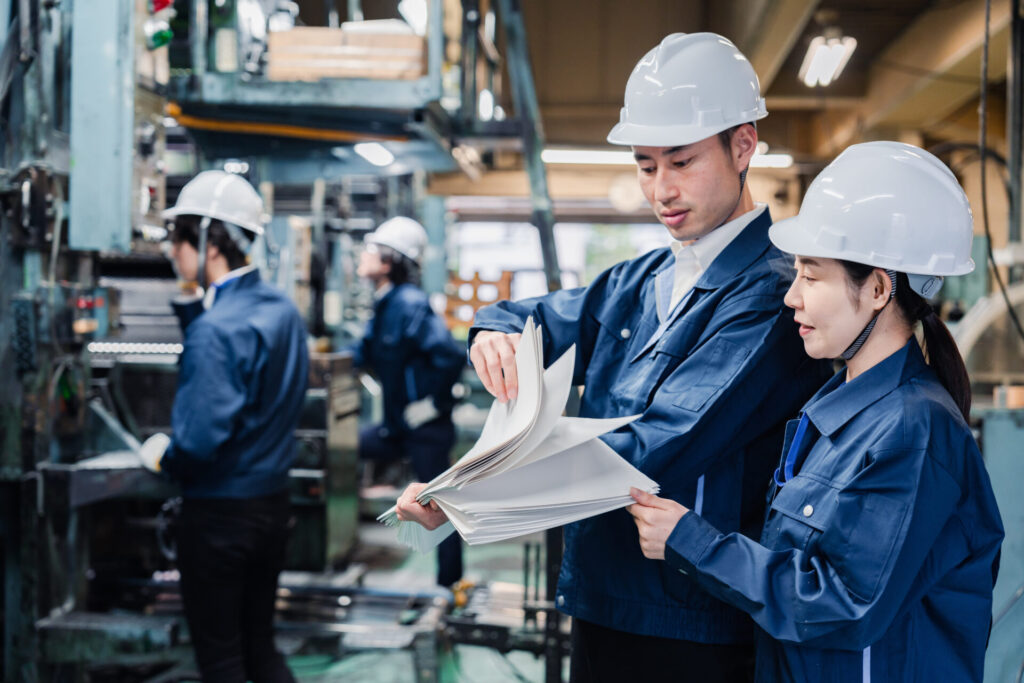
初期流動管理とは、新製品の立ち上げなどの量産検証において、製品品質や生産プロセスの安定性を確認する取り組みを指します。新製品の立ち上げ以外にも、以下のような「工程変更」を行った直後にも、同様の検証を実施します。
- 工程設計・設備レイアウトの変更時
- 外注先の変更・追加時
- 材料・部品の仕様変更時
- 長期間休止していた工程・設備の再稼働時
このような状況では、想定通りの品質が得られるか不明であるため、初期段階で十分な検証が必要です。初期流動管理では、期間を定めて実際の量産条件で生産を行い、設計通りの性能が出ているか、工程が安定しているかを重点的に監視します。さらに、生産現場で発生する「現場・現物・現実」に即したリスクの抽出も可能です。
初期流動管理が必要な理由
量産に向けた準備を十分に行っていても、実際に本番条件(設備・材料・作業者)で生産課題が見つかることも少なくありません。一例ですが、次のような問題の発生が挙げられます。
- 寸法のバラツキが大きい
- 色味などの外観に違いがある
- 品質検査で不具合が発見されず、後工程へ流出する
こうした問題は試作段階では気づきにくく、本番稼働後に初めて顕在化するケースが多いのが実情です。そのため、初期流動管理では、実際の生産条件で一定期間生産しながら、設計通りの品質が得られているか、工程が安定しているかを重点的に確認します。
リスクを放置した場合の影響
この段階での管理が不十分である場合、以下のような重大な問題を引き起こす可能性があります。
- 市場への不良品流出
- 顧客からの信頼失墜
- 大規模な手直しによる費用負担・作業負荷の増大
- 原因究明・再発防止活動のための生産ライン停止・納期遅延
逆に言えば、初期流動管理を適切に行うことで、これらのリスクを未然に防ぐことができます。つまり、初期流動管理とは単なる確認作業ではなく、量産移行の成否を左右する品質保証活動とも言えます。
初期流動管理の目的:量産検証の課題を早期解決する
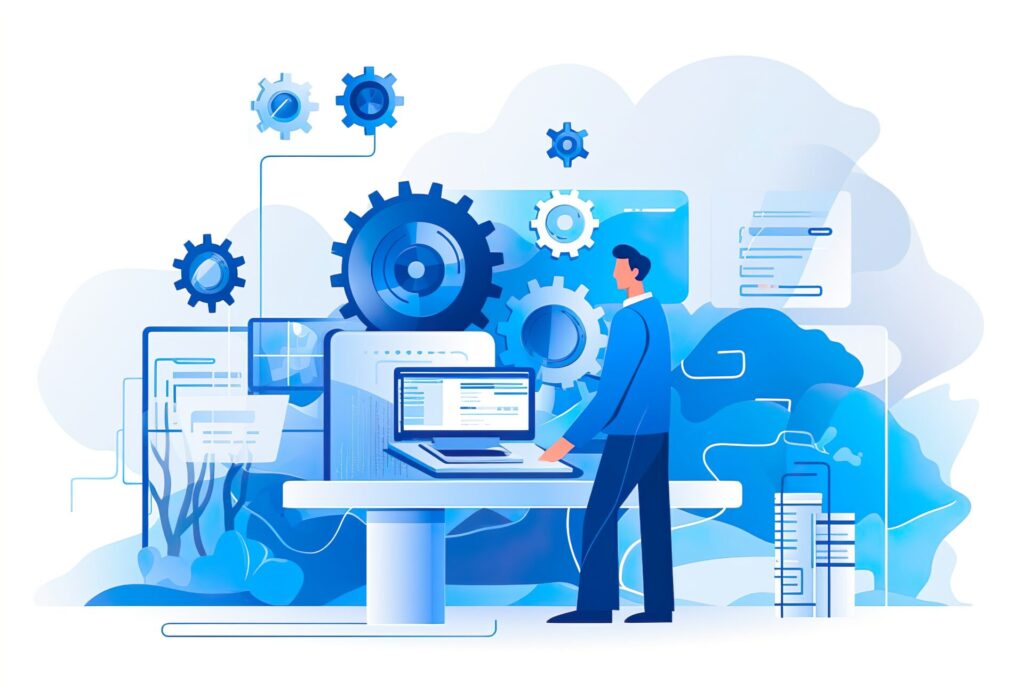
初期流動管理の目的は、量産検証で課題を抽出して、早期に解決することです。組織体制を活用することで、多角的な検証が可能となり、迅速な課題解消が実現します。
以下では、その目的を達成するための3つの視点を紹介します。
潜在的な課題を早期に抽出する
初期流動期間中で最も重要なのは、これまで見えていなかった問題やトラブルの芽を早く見つけることです。
微細な不具合の場合、試作段階やパイロット設備(試験用工場)での生産では見逃されやすく、工程バラツキによる影響度の適切な見積もりも困難です。たとえば、以下のような課題は試作検証では顕在化せず、量産条件で行う初期流動管理で初めて確認されるケースも少なくありません。
- 一部の作業者だけで発生する品質バラツキ
- 材料ロットごとの組立製品の寸法変動
- 量産設備の微妙な調整ズレによる工程内不良
こうした問題は、仕様書や図面だけでは判断できない、現場特有の要因による影響が大きいものです。このため、試作段階やパイロット検証では見つけにくいのが実情です。
初期流動管理では、量産条件下で「いつ、どこで、何が起きているか」を見える化し、不具合の兆候やバラツキの要因を定量的に把握します。これには、工程管理としてのデータ監視だけでなく、検証を行っているタイミングでの現場巡回や定点観測なども効果的です。
部門横断的に課題を共有する
初期流動管理では、品質部門だけでなく、設計・生産技術・購買・現場作業者など、多くの関係部門との情報共有が欠かせません。
初期流動管理で品質不具合が発生したとしても、例えば以下のような幅広い可能性が考えられます。
不具合の要因 | 具体例 |
設計仕様 | 必要以上に厳格な公差 限られた使用環境(温度・湿度)を想定した材質選定 |
生産工程の設備・作業者 | 金型・治具類の微調整不足による寸法バラツキ 作業者ごとの細かな組立手順のバラツキ |
検査工程の検査機器・検査員 | 測定機器ごとの繰り返し測定誤差 検査員の判定基準設定が不十分 |
購入した原材料・部材 | 材料ロット間での色味の差異 納入時の異物混入 |
上記の不具合可能性はほんの一例にすぎません。また、設備トラブルが直接的な原因であったとしても、その背景に部材選定ミスや作業方法のバラツキが潜んでいるケースもあります。
このように、多くの可能性から実際の不具合発生の原因を判断するには、複数部門の視点・データ・蓄積されたノウハウが必要です。定例の初期流動ミーティングや、異常時の緊急レビュー体制があれば、課題の発見から対応までのスピードと精度が大きく向上します。
課題への是正処置を加速する
初期流動管理で見つかった課題に対しては、迅速かつ本質的な是正処置が必要です。初期流動の直後に本格的な量産が控えているケースも多く、対応の遅れは、不具合の再発や品質問題の拡大につながる恐れがあります。
そのためには、不具合発生時の連絡・共有フローをあらかじめ明確化しておくことが重要です。誰がどの情報を、どのように報告・判断・対応するかを定めておけば、初動対応のスピードと確実性が向上します。
さらに、トラブル対応の標準化も欠かせません。以下のように、一連の対応を短時間で実行できる仕組みが整備されていれば、初期流動期間中の問題対応力が高まります。
- 不具合の内容と影響範囲を特定
- 原因を分析(人・設備・材料・方法など)
- 暫定対策を実施し、効果を確認
- 恒久対策を立案・標準化・水平展開
これらを円滑に進めるには、各ステップにおける責任者や関係部門の役割分担を明確にしておくことが欠かせません。
また、過去の不具合履歴やFMEA(故障モード影響分析)を活用すれば、さらなる原因特定ISO9001の迅速化と対策の精度向上が期待できます。これにより、再発防止や他製品・工程への横展開が可能となり、組織全体の品質レベル向上にもつながります。
QMS規格と初期流動管理
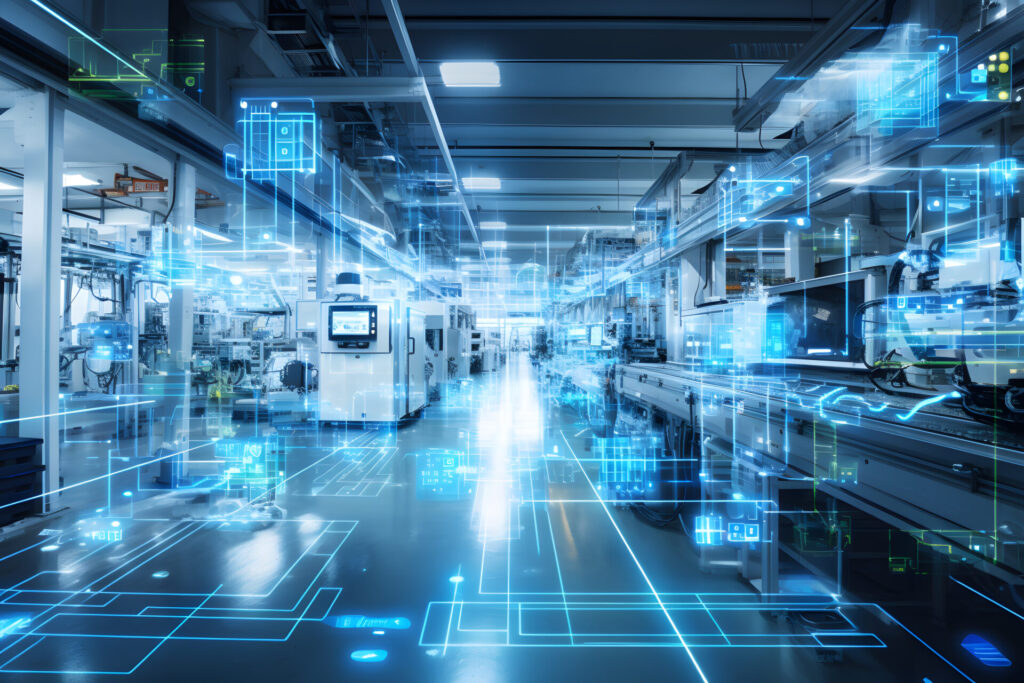
初期流動管理の考え方は、国際的な品質マネジメントシステム(QMS)においても明確に規定されています。
ISO9001における初期流動管理:要求事項8.5.6、8.6
ISO9001では、製品生産に関する変更を行う際や新しい製品をリリースする場合に、初期流動管理の計画と実施が要求されています。具体的な要求事項は次の通りです。
要求事項8.5.6
変更の管理組織は、製造またはサービス提供に関する変更を、要求事項への継続的な適合を確実にするために必要な程度までレビューしなけれならない。 要求事項8.6
製品およびサービスのリリース組織は、製品およびサービスの要求事項を満たしていることを検証するために、適切な段階において、計画した取り決めを実行しなければならない。
上記既定の中で「初期流動管理」という言葉は使われていません。しかし、製品品質や生産プロセスが製品仕様・規格を十分満たすことの検証が求められており、初期流動管理の考え方そのものです。
このように、初期流動管理はISO9001の考え方にも合致し、品質管理において非常に重要な検証活動であると言えます。
IATF16949における初期流動管理:要求事項8.6.1
自動車産業向けの品質規格IATF16949では、ISO9001よりも厳しい初期流動管理の実施が要求されています。関連する要求事項は次の通りです。
8.6.1 製品およびサービスのリリース – 補足
組織は、製品及びサービスの要求事項が満たされていることを検証するための計画した取り決めが、コントロールプランを網羅し、(中略)文書化されていることを確実にしなければならない。
自動車業界では、各工程で何をどのように管理するかを明確にするため、コントロールプランと呼ばれる工程管理計画書を作成します。量産開始直後は、この計画に基づいて特別な監視・評価を行い、製品や工程が安定しているかを確認する必要があります。
つまり、IATF16949においても、初期流動管理は、確実性の高い製品生産を可能にする重要な検証プロセスの一つです。
初期流動管理の進め方
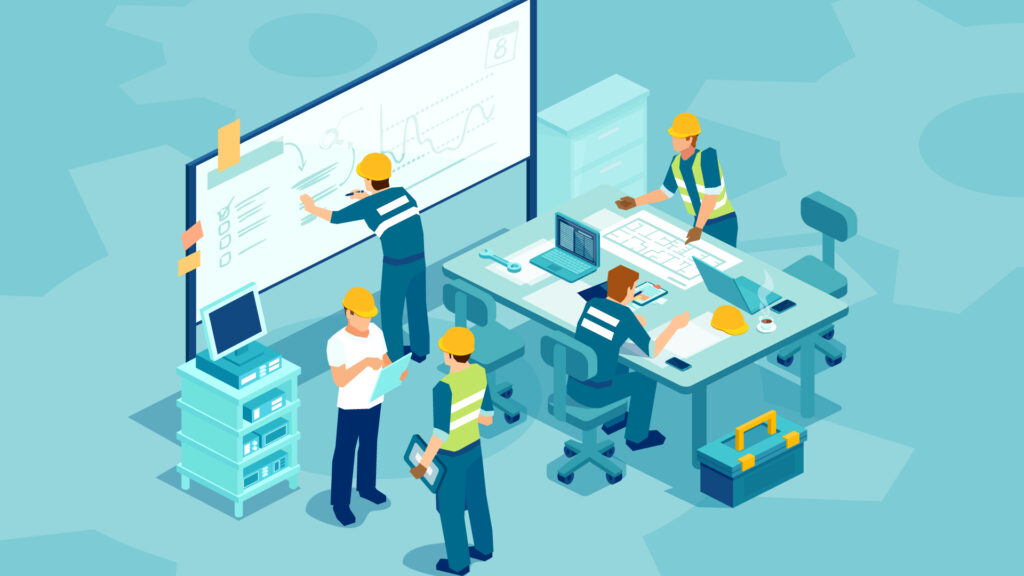
初期流動管理では、対象範囲や実施内容をあらかじめ計画に落としこみ、これに沿って確実に進める必要があります。初期段階での品質問題の多くは、適切な計画があれば早期検出できます。しかし、計画時点で不備があると、「手戻り」や「納期遅延」などのコスト増に直結しやすくなります。
以下に、一般的な初期流動管理の流れとそのポイントを解説します。
対象範囲・管理項目の特定
まず、初期流動管理の対象とする製品・工程を明確にします。すべての製品に一律で初期流動項目を決めるのではなく、リスクレベルに応じて、監視対象や評価基準を決めるのが現実的です。顧客からの要求やQMS規格に基づく要件に照らし合わせて、対象範囲・管理項目を事前に定めましょう。
自動車部品製造の初期流動管理を例に挙げ、リスクレベルごとの監視対象と評価基準を、以下のように表形式にまとめました。
該当事例 | リスク レベル | 製品例 | 主な監視対象 | 評価基準 |
新機種の立ち上げ | 5 | センサー内臓 組立ユニット | センサー位置の寸法・ 精度センサの応答検査 外観検査(キズ発生率) | 規格満足 工程能力指数(Cpk≧1.67) |
材料・部品の仕様変更 新規サプライヤー導入 | 4 | 自動車向け 外装樹脂部品 | 材料物性 (硬度・熱膨張率等) 寸法精度 製品の外観(光沢ムラ) | 規格満足 工程能力指数(Cpk≧1.67) |
工程設計、 設備レイアウト変更 | 3 | 混流生産における 溶接ロボットの 設置位置変更 | 工程のサイクルタイム 異常停止時間・頻度 在庫滞留時間 | 事前検証による 改善見込みからの 乖離なきこと |
長期停止設備・工程の 再稼働 | 2 | エンジン部品の 仕上げ加工 | 加工精度 | 規格満足 工程能力指数 (Cpk≧1.33) |
また、監視対象の中でも、重要管理項目をあらかじめ明確にしておくことも有効です。特に製品機能や安全性に深く関わる特殊特性は、通常の品質検査よりも丁寧に行うのがよいでしょう。
さらに、品質不良を早期検出しやすくするため、初期流動管理に限り工程内検査を追加したり、検査頻度を増やしたりするケースもあります。このように、初期流動管理の対象となる管理項目をあらかじめ明確にして、製品と工程が想定通りに機能しているかを多面的に確認します。
実施手順の明確化
初期流動管理に関わる具体的な実施手順は、文書化として記録を残しておきます。誰が、いつ、何を、どのように確認するのかを文書に残すことで、トレーサビリティが確保しやすくなります。
さらに、日次、週次、ロット単位など、チェックのタイミングを事前に定めておきます。点検記録のフォーマットや報告ルールが整備されていると、よりスムーズに運用できます。
活動体制とメンバーの役割設定
初期流動管理は、一部門で完結する活動ではないため、各部門から適切なメンバーを選出し、チーム体制を構築します。設計・生産・品質・購買・保全など、初期段階での課題に対して即時に対応できる部門横断チームが求められます。
こうした他部門で連携する際には、次の2点が重要です。
- どの部門や担当者が、どの課題に責任を持つのかを明確化する
- 定期的に進捗状況を共有する場を設ける
初期流動期間には突発的な問題発生が頻発します。役割分担と権限をあらかじめ設定することで、意思決定の遅延や対応のバラツキを防止できます。さらに、定期進捗の場では、早急かつ多面的に捉えることができるため、複雑な課題であっても、早期解決へ導きやすくなります。
初期流動管理の効果を高める3つのポイント
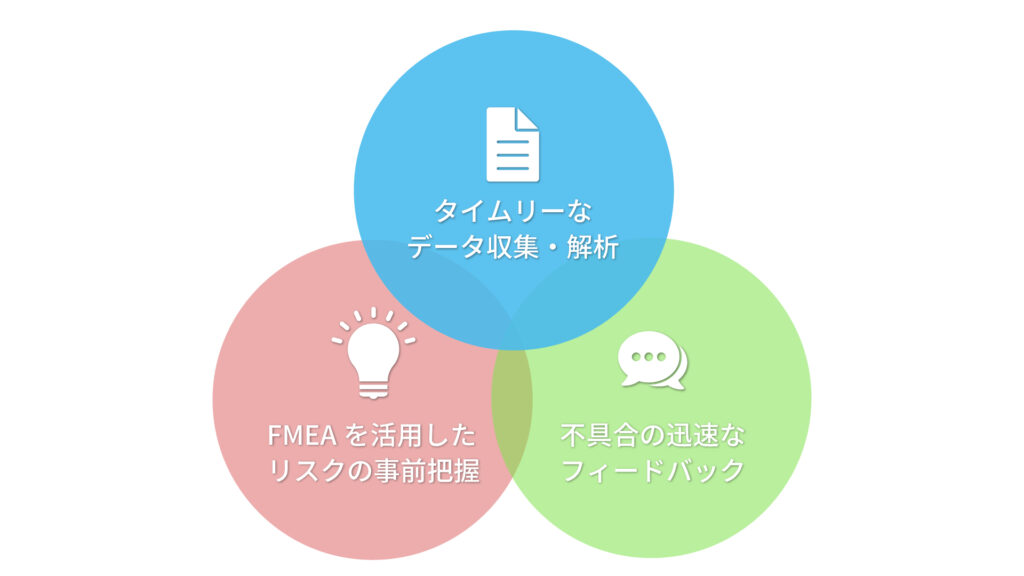
初期流動管理において、現場と管理部門が一体となって、体系的かつスピーディに活動を進めるには、以下の3つの観点に留意するとよいでしょう。
FMEAを活用したリスクの事前把握
初期流動管理の実施にあたり、あらかじめFMEA(故障モード影響解析)を実施することは、品質トラブルの未然防止に極めて有効です。FMEAとは、工程や部品ごとに以下の観点で定量的に評価し、リスクの高いポイントを特定する品質管理手法の一つです。
- どのような不具合が発生する可能性があるか
- その影響はどの程度か
- どの程度の頻度で起こりうるか
- 不具合は容易に見つかるか
この結果を基に、初期流動期間中の重点管理項目を設定することで、高リスクの項目を効率的に監視できます。FMEAの分析結果をチーム全体で共有し、各部門がリスクを認識できていれば、より実効性の高い初期流動管理が実現できます。
一例ですが、樹脂製バンパー製造で材料サプライヤーの変更を想定し、樹脂材料に注目して行ったFMEAを抜粋したものが次の表です。
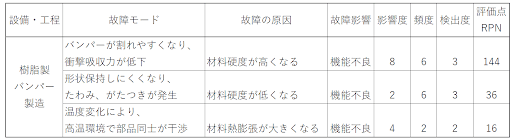
この表は、特に材料硬度が上昇した場合、製品機能への影響度が大きく、発生頻度も高く、品質不良を検出しにくいということを示します。このため、初期流動管理では、材料硬度が高くなっていないかを重点的に監視するのがよいでしょう。
タイムリーなデータ収集・解析
現場での品質・工程データをリアルタイムで収集・分析することも、初期流動管理の成果を大きく左右します。サプライヤー発行の検査表や自社の工程内検査など、数値データをタイムリーに把握できれば、異常傾向や品質不良を早期発見可能です。これにより、早急な対策が可能となり、製造ラインを停止するなどして、大量の不良品を生産してしまう状況を回避できます。
しかし、広く行われている紙やExcelでの管理では、情報の伝達ミスやタイムラグが発生するケースも少なくありません。各種システムやデジタルツールによる一元管理が望ましいでしょう。蓄積されたデータも活用すれば、継続的なトレンドを分析・監視しやすくなり、異常傾向の早期発見も可能になります。
不具合の迅速なフィードバック
初期流動管理において不具合が判明した場合には、関係部門にスピーディかつ正確にフィードバックすることも不可欠です。
初期流動期間中は、通常よりもトラブル発生のリスクが高いため、影響範囲が大きくなる前に、迅速な対策が必要です。システムツールを活用すれば、現場作業者の報告を待たずに状況を把握でき、情報共有もスムーズになります。これにより、不具合の影響が大きくなる前に、フィードバックを反映しやすくなります。
円滑な初期流動管理には、システム活用が有効
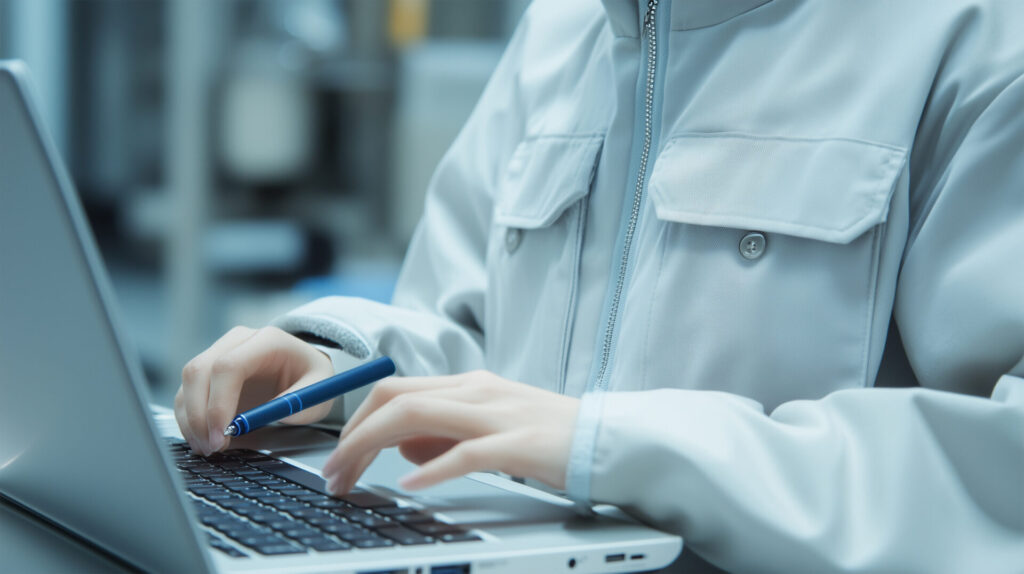
初期流動管理は、対応事項が多く煩雑なため、対応スピードが追い付かないケースも少なくありません。しかし、システムツールを活用すれば、円滑な初期流動管理が実現します。
初期流動管理は、計画、実施、記録、フィードバックと多くのプロセスを伴い、迅速な対応が求められます。生産管理システムの活用により、ロットごとの品質情報や工程データの管理、異常の早期検知などをスピーディーに行うことができます。
システム化で初期流動管理の品質とスピードを両立
生産管理システムの中には、初期流動管理に必要な機能を提供しているものもあります。具体的には、以下のような機能が挙げられます。
- ロットごとのトレーサビリティ管理:誰が・いつ・どの設備で生産したかを自動記録
- 検査・測定データのリアルタイム集計:IoT技術やCSVデータでの集計で異常傾向の早期発見
- 不具合の即時共有・対応履歴の管理:関係部門と素早く情報共有
これにより、紙やExcelなどのアナログ管理では実現しにくい、スピード感のある意思決定と品質改善の仕組みが構築できます。
詳しい導入事例はこちらで紹介しております。
→【生産管理システム】生産情報・検査情報を一元管理!手書き・エクセル作業をシステム化し、生産拡大時の品質リスク対策に成功
デジタル活用で“現場の判断”を“組織の知見”に変える
クラウド型の生産管理システムでは、現場の作業実績や検査結果を電子データとして蓄積できるものも存在します。このようなシステムでは、オンプレミス型システムと比較してリアルタイム性にも優れるという特徴があります。さらに、コスト負担も抑えられるケースが多いため、運用を継続しやすいというメリットがあります。
初期流動管理は一過性の活動ではなく、継続的な品質改善の起点です。過去の現場判断を蓄積することで組織の知見を増やし、組織全体として、品質管理体制の底上げを加速できます。多くのデータ・情報の取り扱いを求められる現代において、このようにデジタルの力を活かした標準化と仕組み化は欠かせません。
生産管理システムで工程管理、不良集計の迅速化を実現した事例は、こちらで紹介しております。
→【生産管理システム】手入力の手間をなくし年間200時間以上の工数削減!アナログ管理特有のヒューマンエラーも大幅削減
22種類の生産管理システムをランキングで比較
初期費用相場や選び方のポイントをチェック
生産管理システムをそれぞれの特徴や初期費用相場などで比較したい場合は、「生産管理システムランキング」も是非ご覧ください。生産管理システムは、自社の製品・生産方式・企業規模などに適したものを導入しないと、得られるメリットが限定されてしまいます。事前適合性チェックや生産管理システムを選ぶ前に押さえておきたいポイントも解説していますので、製品選びの参考にしてみてください。