ボトルネック工程はどこ?見つけ方と解消までの道筋について、具体例を交えて解説
公開日:2025年04月23日
最終更新日:2025年04月23日
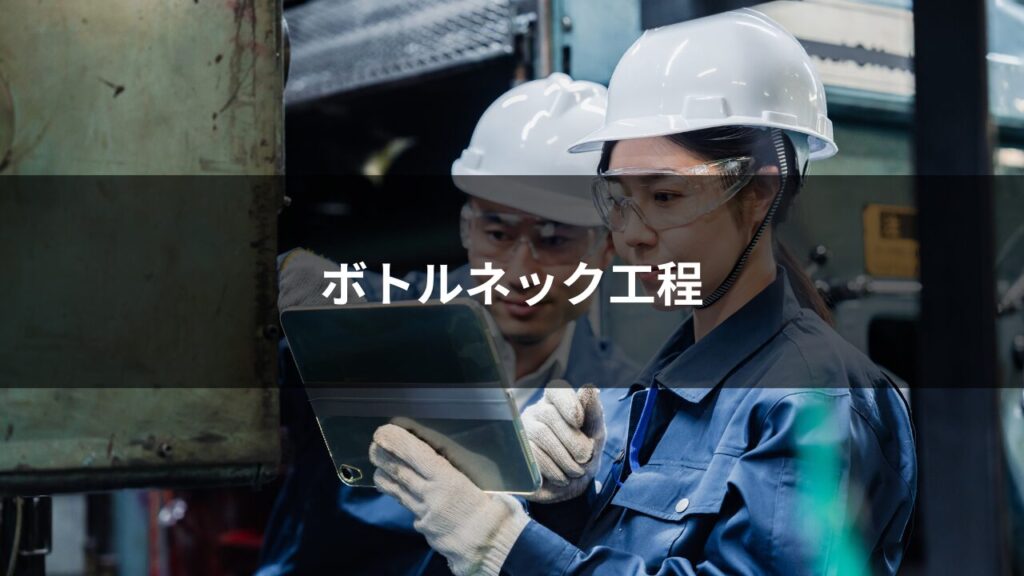
製造ラインの生産性向上には、最も処理能力の低い「ボトルネック工程」の特定と改善が鍵を握ります。本記事では、実際の製造工程を例に挙げ、ボトルネック工程の基本的な考え方について解説。さらに、ボトルネックの見つけ方、原因分析、改善に向けた5段階ステップにも触れ、限られたリソースで最大の効果を上げるための優先改善ポイントや、生産管理システムを活用したボトルネック解消の道筋についても紹介します。
ボトルネック工程とは?
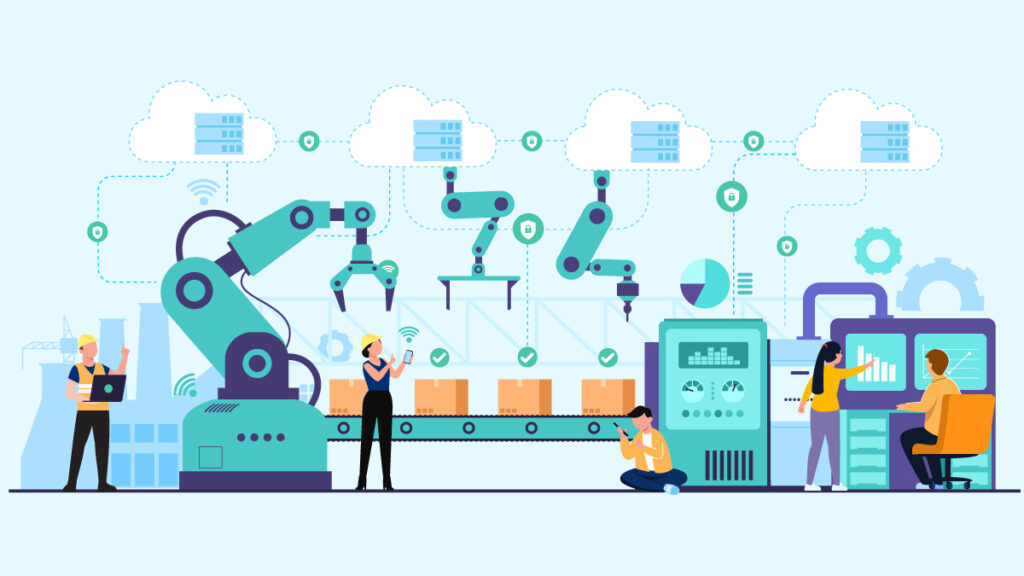
製造現場において、ボトルネック工程とは、ライン全体の処理能力を決める工程です。生産性を改善するためには、ボトルネック工程への取り組みが最も効果的です。
ラインの生産能力を決める工程
ボトルネック工程とは、製造ライン全体の生産能力を決める工程です。生産ラインは複数の工程から構成されるケースが一般的です。特定の工程で生産性の改善を重ねても、最も処理速度(スループット)が遅い工程を超える生産能力は実現不可能です。
一例ですが、機械装置の駆動部に使用される歯車は、金属の素線から、下図に示す4つの工程を経て製造されます。
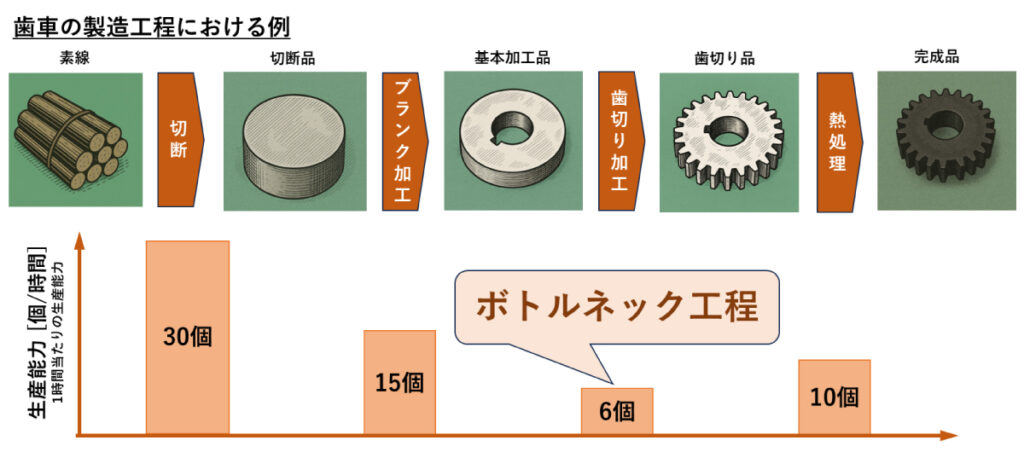
この中で、1時間当たりの生産能力が最も低いのは、歯切り加工の6個です。このため、歯車の製造工程におけるボトルネックは、歯切り加工になります。このままでは、切断や熱処理に関する生産性をどれだけ改善しても、1時間当たり6個以上の製造はできません。
なお、ボトルネックという言葉は、瓶の口が最も狭く、そこから中身が流れ出す速さが制限されることに由来します。ボトルネック工程とは、製造ライン全体における瓶の口のような存在です。その絞りが狭いほど、すなわち最も遅い工程の生産性が低いほど、生産ライン全体の流れが遅くなります。
費用対効果の高い優先改善ポイント
工程改善を進める際に、最も効果的なのはボトルネック工程に対する集中対策です。ボトルネックに対する改善活動は、生産性の大きな向上が期待できます。一般的に、すべての工程で生産性改善に着手すると、多大なコスト・労力が必要です。
そのため、まず、各工程の生産能力を整理し、最も生産性が低い工程を特定します。この工程に対して優先的に対策を実施することで、費用対効果の高い改善が実現しやすくなります。
例えば、前述の歯車製造工程では、歯切り加工がボトルネックになっており、生産ライン全体のスピードを大きく制限しています。このメーカーでは、歯車の納品依頼が多く、顧客の要望に応えきれないため、一部受注を断っている状況でした。そのため、生産性向上を目指して全方位的な改善活動を推進していたものの、劇的な効果には至っていませんでした。
このような状況では、ボトルネック工程である「歯切り加工」の改善に集中することが最も効果的な改善策です。小さな改善で大きな効果を生むため、ボトルネックの改善への注力は、全体の生産性向上につながります。
ボトルネック工程を見つけるための着眼点
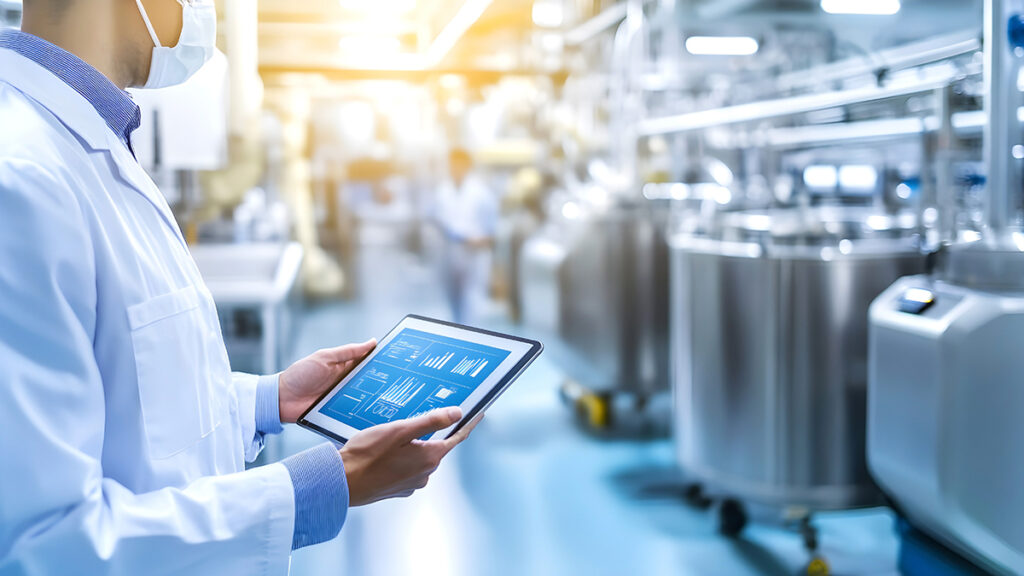
ボトルネックとなる工程には、いくつかの特徴があります。それぞれの企業・現場において、最も見える化しやすい指標に注目して工程管理を行うとよいでしょう。
モノが滞留する工程に注目する
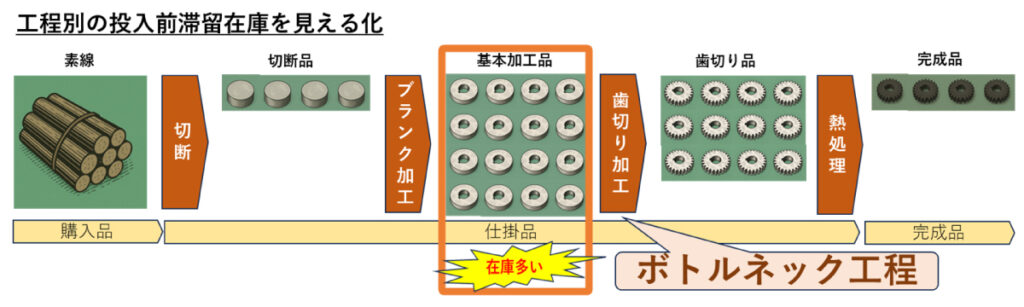
製造現場において、処理前の滞留在庫が目立つ工程は、ボトルネックである可能性が高いです。他の工程と比べて、大量の仕掛前在庫や半製品が滞っている場合、後工程が処理しきれず、生産の流れが詰まっているサインと言えます。
たとえば、前述の歯車製造工程では、歯切り加工設備の前に、「基本加工品」が滞留している場面が頻繁に見受けられました。生産ラインでは、モノが淀みなく流れている状態(整流化)が正しい姿であり、滞留在庫は可視化しやすいボトルネックの兆候です。
このため、現場での巡回や在庫量の記録から、過剰在庫が頻発する工程を突き止めることができます。必要以上に多くのモノがある場所には、流れを止めている要因が潜んでいるケースが多いと言えます。
流れが停滞しやすい工程を見つける
滞留時間の長さという切り口も、ボトルネック工程を見つける上で重要な観点です。滞留時間とは、部品や製品が工程内にとどまっている時間です。ここには作業そのものの時間だけでなく、待機や段取り替えなどの準備時間も含まれます。
滞留時間が長い工程は、生産ライン全体の流れに対して、処理能力が追いついていない可能性が高いです。スムーズな流れ(整流化)を阻害する工程があると、ライン全体の生産性が低下します。
前述の歯車製造工程の例でも、下図のように歯切り加工工程では、仕掛品の滞留時間が最も長くなっていました。
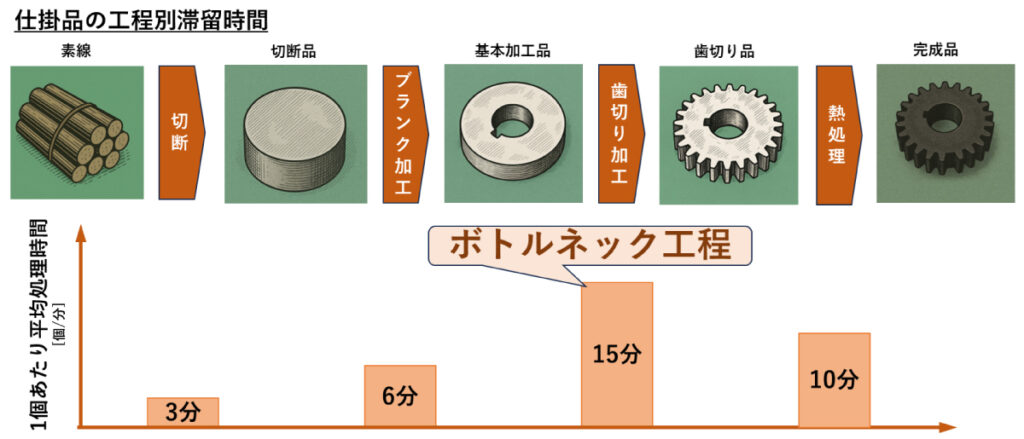
実際に歯切り加工工程を詳しく見てみると、実際の設備稼働時間、段取り替え等による設備待機時間とも長いことがわかりました。
このように、滞留時間の長い工程は、設備能力、作業オペレーションに課題を抱えている可能性が高いです。逆に言えば、こうした課題に対して集中的に取り組めば、改善効果が表れやすいと言えます。
稼働率のアンバランスを指標にする
工程ごとの稼働率に大きな偏りがある場合も、ボトルネック工程を探しやすい状況です。常に高い稼働率の生産ラインは、生産余力がないことを意味します。
例えば、全体の平均稼働率が70〜80%なのに対し、ある工程だけが常時95〜100%の稼働率であったとします。この場合、その工程が流れの律速点(ボトルネック)になっている可能性が高いです。
また、極端に手待ちが多く、稼働率の低いラインがあるケースもあります。この場合は、次の2つの状況が考えられます。
- 「前工程の遅れ」によって、加工すべき仕掛品が手元にない
- 「後工程の詰まり」によって、在庫量調整のため生産調整を行っている
このように、工程ごとの稼働率は、ボトルネックを定量的に判断しやすい指標と言えます。
特定の工程がボトルネックとなる主な原因
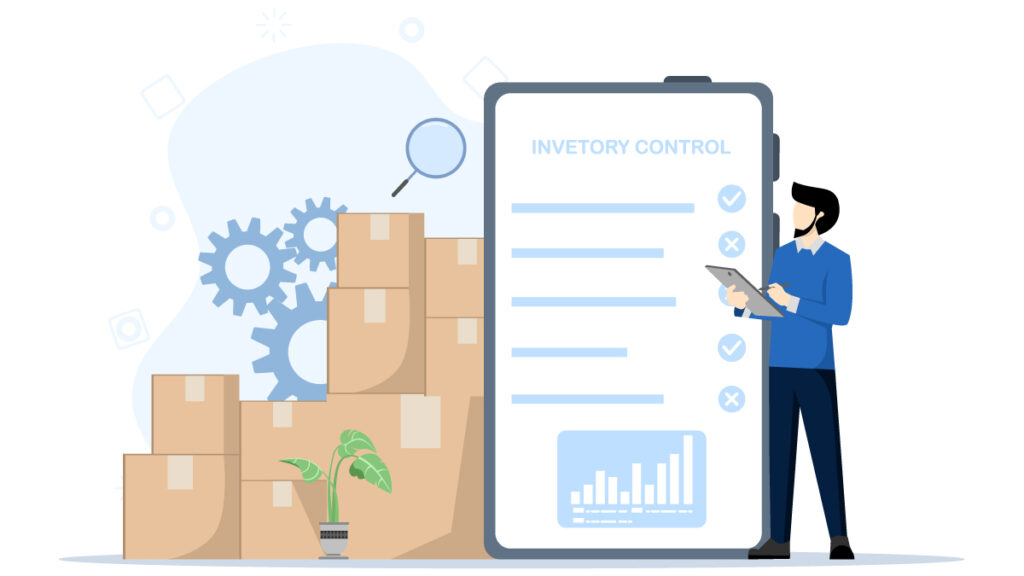
製造現場でボトルネックが発生する際、主な原因は4つあります。
段取り・準備作業の効率が悪い
作業準備や段取り替えが非効率であることは、ボトルネックとなる代表的な原因です。具体的には、次のような状況を指します。
- 機械の停止中に、次の生産に使用する材料や部品を準備する
- 段取り替え手順が標準化されておらず、毎回試行錯誤で機械を調整する
これらに加え、機械の稼働中に進められる準備作業(外段取り)を停止中に行っているケースでは、さらに影響が大きくなります。
段取り作業の非効率を放置すると、「動いていないのに忙しい」という状況が常態化します。その結果、これが原因でボトルネックになると、全体の生産性を押し下げてしまいます。
このような場面では、機械を停止して行う必要のある作業(内段取り)の外段取り化が効果的です。詳しくはこちらの記事で解説しています。
→段取り替えとは?QMSとの関係、ムダの探し方・削減方法・改善事例を紹介
他工程に比べて、設備の処理能力が低い
設備の処理能力そのものが他の工程よりも低い場合、その工程はボトルネックとなりやすくなります。こうした工程には、次のような特徴を抱えているケースが少なくありません。
- 古い設備を使用している
- 人手がかかる作業が多い
- アナログな記録業務に時間を取られている
たとえば、生産工程の多くが自動化されていても、検査工程で重量測定と紙帳票への記録を人力で行っているケースが挙げられます。このような場合、検査工程の処理速度が追いつかず、生産効率をいくら改善しても工場全体の生産性は上がりません。
この場合、検査工程に重点的に人的リソースを配分させることで、ボトルネックを解消できる可能性があります。計量器と生産管理システムを連動させ、測定結果を自動取り込みさせる取り組みも有効でしょう。
計量器と生産管理システムを連携させた事例は、こちらの記事で紹介しています。
→【生産管理システム】計量器連携などでアナログ作業を減らし年間450時間の工数削減!将来在庫の自動計算やCSV取込など、人的ミスをなくす仕組みも活用
トラブルやチョコ停の発生頻度が高い
工程内で発生する設備トラブルや、いわゆるチョコ停(短時間停止)が頻繁に起こると、ボトルネックの要因となります。こうしたトラブルがあっても、一度の停止時間は短かいケースも少なくありません。しかし、1日に何度も繰り返されれば、製品1個あたりのサイクルタイムが伸び、稼働ロスも甚大になります。
一例ですが、以下のような小さなトラブルが日常的に発生している現場も散見されます。
- 工具探しに時間を取られ、作業の再開が遅れる
- 作業記録に手間取り、一時的に生産を停止する
- 生産品の合否連絡が遅れ、次の処理が進まない
一つひとつのトラブルの影響度は小さくみえるかもしれません。しかし、これらの小さなロスが積み重なることで、結果として工程全体の流れを滞らせ、ボトルネックを形成することもあります。
工程間で、人・モノの流れが噛み合わない
前工程や後工程との人やモノの動きがうまく連携していない状況も、ボトルネックの一因となります。本来スムーズに流れるはずの製造プロセスが分断されると、一部の工程に作業負荷が集中します。一方で、他の工程では待機時間が発生し、処理能力に余裕がある工程の生産性も下がるケースもあります。
具体的には、次のような状況が挙げられます。
- モノの流れを左右する運搬を人手に依存している
- 作業のタイミングが作業者任せになっている
こうした現場では、仕掛品が一部の工程に滞留し、別の工程では材料待ちが続くといった「アンバランスな状態」が起こりやすくなります。情報連携が不十分な場合、作業のタイミング調整がうまくいかず、こうした稼働ロスが日常的に発生することもあります。
このような状況を防ぐには、各工程における進捗状況をリアルタイムで見える化することが有効です。タイムリーな状況共有によって作業者同士の調整もスムーズになり、搬送・作業指示・確認といった動きのタイミングを最適化できます。
ボトルネックを解消するための5段階ステップ
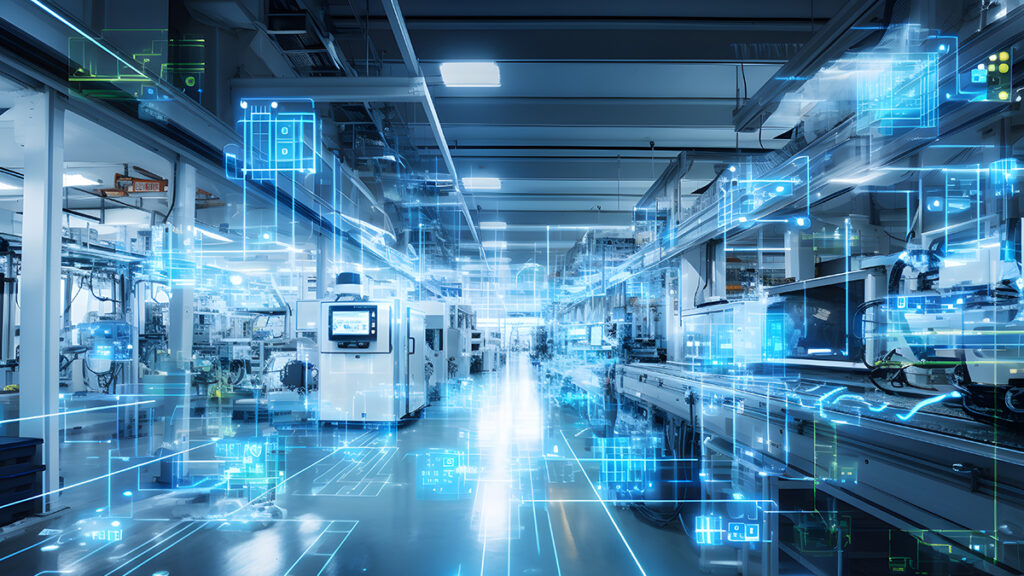
ボトルネックの要因を把握した後、実際にどのように解消していくかを考えるステップに移ります。ここでは、TOC(制約理論)に基づく「5段階集中プロセス」に沿って、ボトルネックの解消手順を解説します。
このフレームワークの特徴は、単にボトルネックを取り除くことに留まりません。改善効果の持続可能性を上げ、全体最適を実現する考え方でもあります。
ボトルネックを見つける
製造工程全体におけるヒト・モノの流れを可視化し、どの工程・作業がボトルネックになっているかを特定します。全工程の見える化が難しい場合には、現場観察を通じて、重点管理対象を絞り込む方法も有効でしょう。
特に、次のような工程・作業はボトルネックの兆候であるケースも多いため、重点的に調査を行うとよいでしょう。
- 作業者の動きが多い工程
- 設備の不調が常態化している工程
さらに、前述の滞留在庫、滞留時間、稼働率など、定量的な指標を活用することで、より客観的な判断が可能です。この際には、作業日報や稼働実績、工程別の作業記録などのデータが役立ちます。
稼働停止・ロスを減らし、リソースを最大限活用する
ボトルネック工程が特定できたら、次は現状の設備や人員を最大限活用する工夫を行います。ここでの改善は、大がかりな投資を伴うものではなく、現場ですぐに実践できる「小さなロスの排除」が中心です。具体的には、次のような改善が挙げられます。
- 段取り時間の短縮:機械停止時間を減らし、準備作業を効率化する
- チョコ停の削減:小さなトラブルの芽を見つけ、排除する
- 工程のスムーズな引き継ぎ:作業日報やホワイトボードを活用し、伝達ミスを防止する
また、ボトルネック工程では、休憩時間中も設備が止まらないように、部分的なシフト制を導入するのも効果的です。これにより、「止めない」「待たせない」の定常化が実現できます。
こうした改善は一見小さな取り組みに思われるケースも少なくありません。しかし、ボトルネック工程に集中して実施すれば、大きな効果を発揮します。特に、記録されにくい短時間の停止や作業のバラつきを見逃さず、改善の取り組みにつなげることがカギとなります。
他工程の生産能力をボトルネックに合わせる
ボトルネック工程の稼働ロスが減らせたら、他工程の生産能力とのバランス調整を行います。このステップでは、「ボトルネックの能力をライン全体の基準とする」という視点が重要です。
各工程が独立して最適化を目指しても、かえってムダが生じる場合もあります。例えば、ボトルネックの前工程で過剰に生産を行うと、仕掛品の滞留や無駄な在庫の増加に繋がり、保管場所・管理コストが膨らみます。
バッチ生産が主流の工程では、バッチサイズの見直しも有効です。ボトルネック工程の処理能力が1日100個で、前工程のバッチ処理で1日1回1000個作る工程を考えます。この場合、9日分の在庫が余剰になり、保管スペースや在庫管理にムダが生じます。バッチサイズを下げることで、製品需要にあった小回りの効く工程となります。
このように、全体最適の実現には、ボトルネックの処理能力を基準として、他の工程の生産計画や人員配置の調整が欠かせません。その結果、過剰生産や在庫滞留を防ぎ、スムーズな流れを維持することができます。
ボトルネック工程を増強する
次に取り組むのは、ボトルネックそのものの処理能力を強化することです。ここには、単純な加工条件の見直しにとどまらず、設備の増設や自動化の導入など、大きな投資を伴う対策も含まれます。
ただし、この段階に入る前に、前ステップまでの改善が十分に行われていることが前提となります。手順を飛ばして設備投資を行うと、コストに見合う効果が出なかったり、新たなムダを生んだりする可能性もあります。
どの程度の能力増強をすればよいかを適切に決定するためには、定量的なデータに基づく判断が重要です。工程データを効率的に収集・分析できる仕組みがあれば、より効率的かつ迅速な意思決定が可能です。
改善で生まれる新たなボトルネックを探す
ボトルネック工程を能力増強すれば、次は別の工程が新たなボトルネックとなります。外部環境による需要やサプライチェーンの状況は絶えず変化するため、一度きりの改善では完結しません。
新たな律速点を継続的に特定し、同様のプロセスを回していくことで、生産ライン全体のスループットが徐々に底上げされていきます。このようなカイゼンを続けるためには、作業実績をデータとして蓄積し、改善にむけた取り組みの効果を分析することが欠かせません。
ボトルネック改善を仕組みに変える:生産管理システムの導入効果
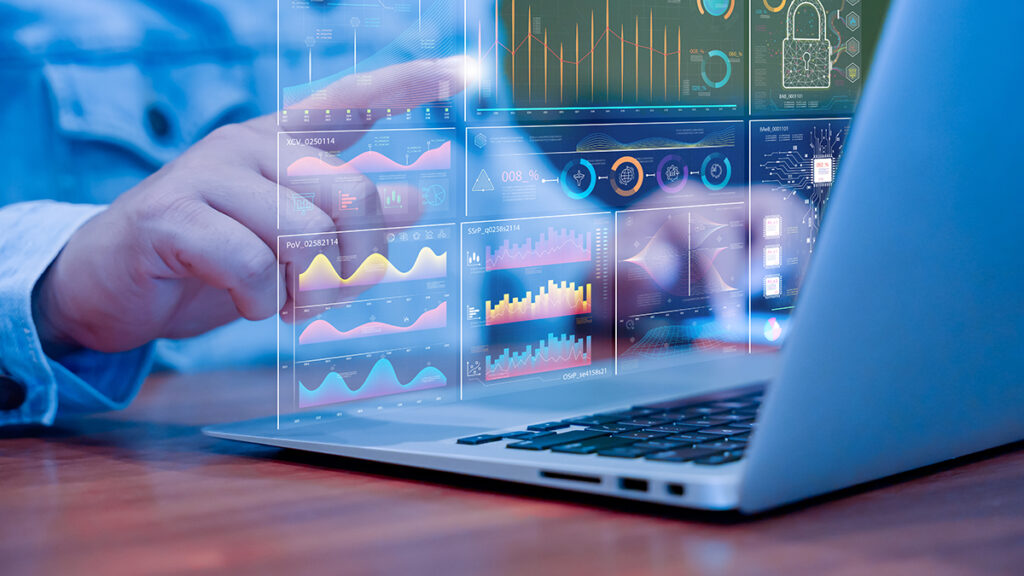
在庫・進捗・稼働を見える化する
ボトルネック工程を把握するための第一歩は、各工程の在庫・進捗・稼働状態をリアルタイムで見える化することです。在庫状況を十分に把握できない現場では、欠品によりボトルネック工程における稼働率を維持できず、工場全体の生産性を悪化させます。
生産管理システムの中には、入出庫状況や設備稼働状況をリアルタイムで反映させることができるものもあります。こうしたシステムを活用すれば、生産性改善のカギとなるボトルネック工程を把握でき、稼働率を高めるための施策の絞り込みが可能です。
ボトルネックである部品在庫の見える化により、生産計画の合理化を実現した例:
→【在庫管理システム】在庫の見える化と年間1000時間以上の工数削減に成功!手作業や残業をなくすことで生産性を向上
ボトルネックを生む欠品を防ぐ
在庫管理の効率化は、ボトルネックの解消に役立ちます。実際に、原材料や部品の欠品により、度重なる生産計画の変更を余儀なくされるケースも少なくありません。
確実な在庫把握のためには、手入力や紙帳票の管理からの脱却が重要です。生産管理システムとハンディ端末による自動記録により、在庫管理の精度を上げ、管理工数を大きく削減することが可能です。
ハンディ端末の導入により、効率的な在庫管理を実現した事例:
→【原料在庫管理システム】毎日の原料在庫数の確認の手間を95%削減
22種類の生産管理システムをランキングで比較
初期費用相場や選び方のポイントをチェック
生産管理システムをそれぞれの特徴や初期費用相場などで比較したい場合は、「生産管理システムランキング」も是非ご覧ください。生産管理システムは、自社の製品・生産方式・企業規模などに適したものを導入しないと、得られるメリットが限定されてしまいます。事前適合性チェックや生産管理システムを選ぶ前に押さえておきたいポイントも解説していますので、製品選びの参考にしてみてください。