トヨタ生産方式の「ジャストインタイム」とは?メリットやデメリット、向いている企業を解説
公開日:2024年08月29日
最終更新日:2024年12月24日
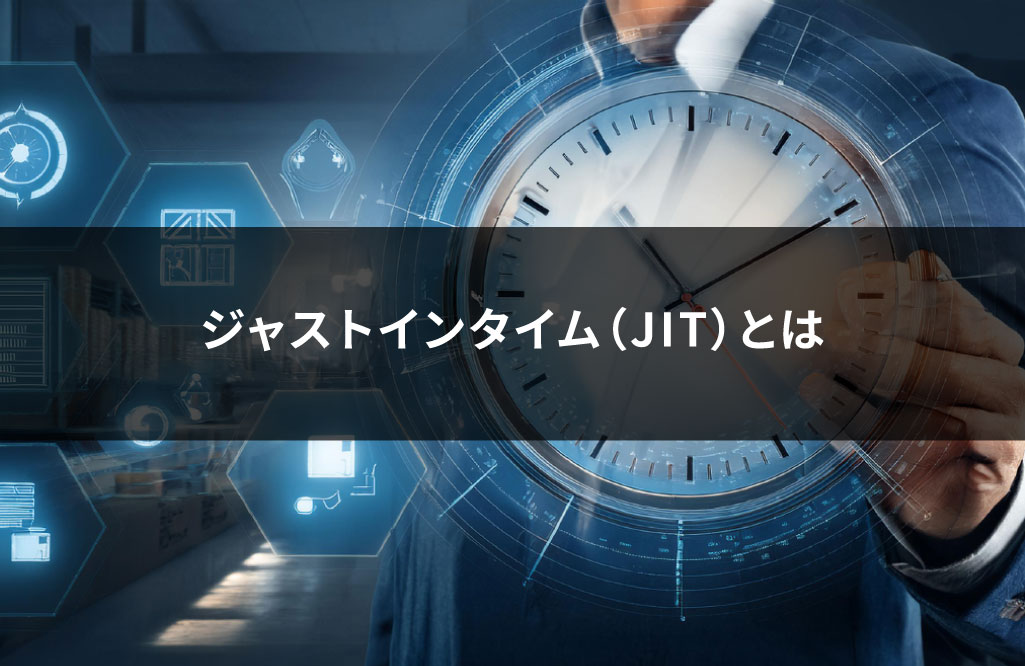
ジャストインタイム生産方式は、むだを徹底的に排除する仕組みにより、在庫削減や生産リードタイムの短縮を実現することができます。この記事では、ジャストインタイムの基本概念からその導入メリット、さらに取り組むべき課題について詳しく解説します。ジャストインタイムが自社に向いている生産方式かどうか、判断するヒントにしていただけると幸いです。
ジャストインタイム(JIT)とは
ジャストインタイム(JIT)とは、必要なものを必要なときに必要な量だけ生産することで、無駄な在庫の発生を最小限に抑えることができる生産の仕組みです。トヨタ生産方式の2本柱の1つとして知られ、現在は製造業や物流業界で幅広く活用されています。
ジャストインタイムの目的
ジャストインタイムの最も大きな目的は、あらゆる「ムダ」を減らし、生産リードタイムを短縮することです。過剰な在庫や無駄な動きを排除し、売れた分をタイムリーに生産することで、生産コストの削減と効率化を目指します。
必要な部品が必要なタイミングで供給されることで、在庫の保管コストやスペースの削減が可能になります。また、製造ラインの効率を最大限に高め、生産リードタイムを短縮することで、全体の生産性を向上させることができます。トヨタ自動車は、このジャストインタイムと自働化という独自の仕組みにより、最小限の在庫で受注後にすばやく製造できるトヨタ生産方式(TPS)を作り上げました(詳しくは後述)。
JITは平準化生産が前提の仕組み
JITは平準化生産、つまり生産量や生産品目の種類を均等化することが前提となっています。いつでも一定の量・種類の生産を流し続ける平準化生産ができるからこそ、ジャストインタイムの3原則の1つである「後工程引き取り」が可能になります(詳しくは後述)。
ジャストインタイムの3原則
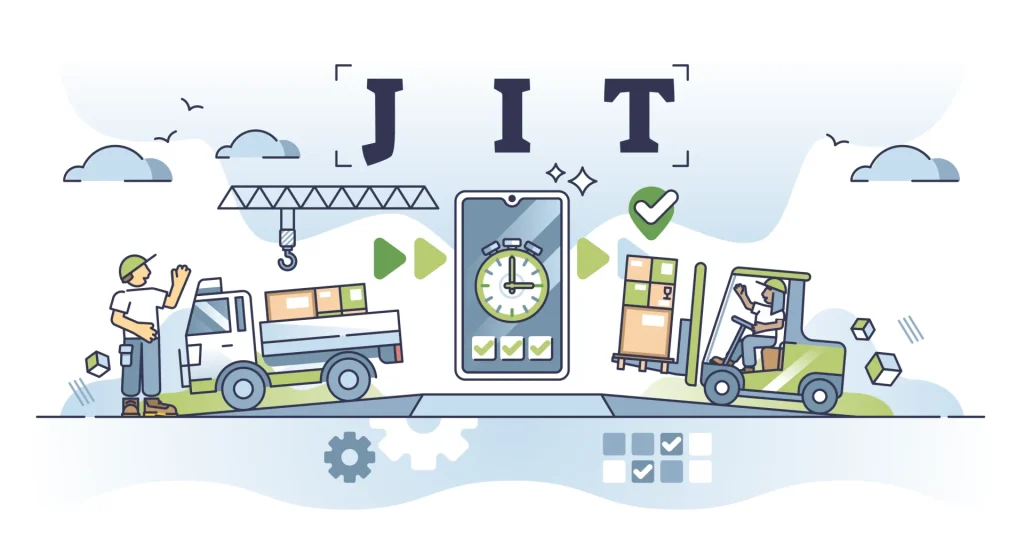
ジャストインタイムを効果的に運用するための、3原則について説明します。
後工程引き取り
後工程引き取りとは、次の工程が前の工程から必要なものだけを引き取る仕組みのことです。ジャストインタイムの根幹となる仕組みといえます。
一般的な生産ラインでは、前工程から順に部品を製造し、後工程に渡していく流れで完成品を作り上げます。しかし、受注後に一から作り始めると生産リードタイムが長くなり、あらかじめ部品を生産したうえで後工程に回していくと過剰在庫のリスクが出てきます。
そこで、ジャストインタイムにおいては、全工程にて常に最小限の在庫を持っておき、受注後に後工程が前工程の完成部品を引き取る、後工程引き取りが採用されました。後工程が部品を引き取った後は、前工程にて引き取られた分を再び生産し、最小在庫を保つようにします。この仕組みにより、需要に基づいて前工程の生産が調整されるため、仕掛品の無駄がなく効率的な生産が可能になります。
生産工程の流れ化
後工程引き取りを機能させるためには、生産工程の流れ化が不可欠です。「整流化」とも呼ばれます。そのためには、工場内の設備レイアウトの工夫や、生産ロットの最小化などが必要です。ライン生産であれば、生産設備を工程順に並べてむだのない流れを作ったり、多品種少量生産であれば、セル生産方式で1人〜少人数での組立工程を流れ化するなどの方法があります。
必要数でタクトタイムを決める
タクトタイム(ピッチタイムとも)とは、1つの製品を生産するのに必要な時間を指します。JITでは、顧客の需要に基づいてタクトタイムを設定することで、無駄のない生産が可能になります。
→タクトタイムの詳細(計算方法・サイクルタイムとの違いなど)はこちら
ジャストインタイムに関連する用語
ジャストインタイムの理解を深めるためには、関連する用語についても知っておくことが必要です。特に「トヨタ式生産方式」や「かんばん方式」などは、JITを実践する上でとても重要な考え方です。
トヨタ式生産方式
トヨタ式生産方式は、ジャストインタイムと自働化という仕組みを基盤とした生産管理方法です。徹底的にむだを排除した合理的な生産方式として、世界でも「TPS(TOYOTA Production System)」「リーン生産方式」などの名称で知られています。
トヨタ生産方式が登場するまでの自動車製造業では、大量の在庫を持ちながら大量生産する従来の生産方式(フォード方式)が一般的でした。低価格で生産する効果はあったものの、在庫リスクや機会損失のリスクが大きいというデメリットがありました。これらの大量生産の課題を解決する方法として、トヨタ生産方式が考案されました。
かんばん方式
かんばん方式は、ジャストインタイムを支える重要なツールの一つです。代表的なかんばんの種類は、後工程が前工程に必要な部品を引き取る際に使う「引取かんばん」、後工程に引き取られた後の生産指示として使う「仕掛けかんばん」などです。かんばんを使うことで、複雑な在庫管理をすることなく、必要なものを必要なタイミングで供給することができます。
ジャストインタイムのメリット
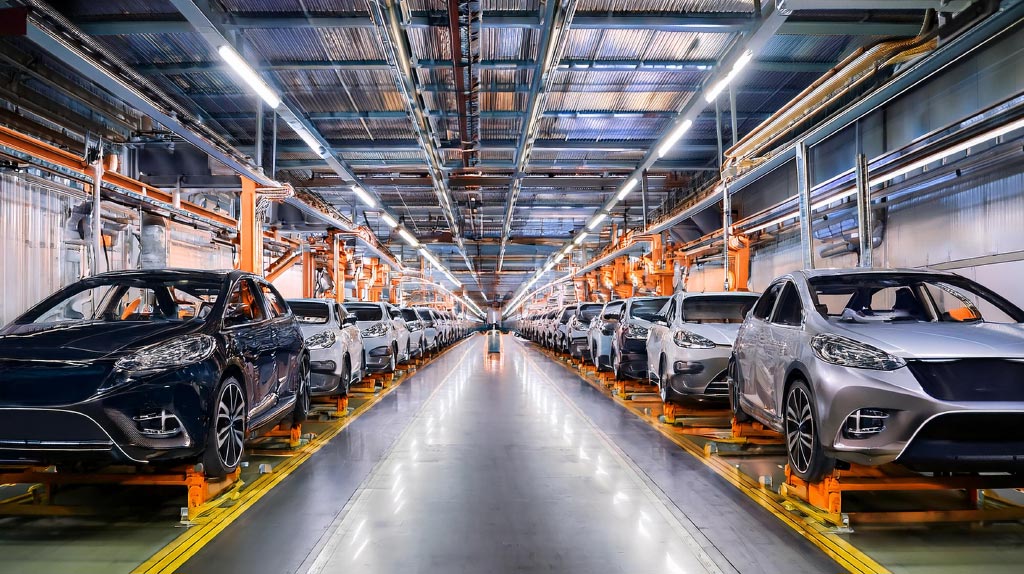
ジャストインタイムは、製造業においてさまざまなメリットがあります。
在庫の最適化
JITの導入によって、在庫を最小限に抑えることが可能になります。必要な部品や製品が必要なときに供給されるため、過剰在庫や不足によるリスクが低減されます。在庫管理の効率化により、保管スペースや管理コストの削減も可能になります。
大量生産で生まれがちなコストの削減
JITは、大量生産によって発生する無駄なコストを削減するための効果的な方法です。例えば、ジャストインタイムと対照的な生産方式であるロット生産では、生産量にムラが生まれやすく、作業員の待ちや手持ちが発生しやすくなります。ジャストインタイムで平準化された生産の流れでは、こういったムダの発生も防止し、製造原価を低く抑えられます。また、効率的な生産体制の構築により、品質管理コストも削減することができます。
生産リードタイム短縮による機会損失防止
JITの導入により、生産リードタイムが短縮され、顧客からの注文に迅速に対応できるようになります。これにより、納期遅れや機会損失のリスクが軽減され、顧客満足度が向上します。
ジャストインタイムのデメリット
ジャストインタイムには多くのメリットがある一方で、在庫切れリスクや品質管理コストの増加、導入コスト、下請け企業への負担増加などのデメリットもあります。これらを理解し、対策を考えることが、JITを効果的に運用するために重要です。
在庫切れリスク
JITは在庫を最小限に抑えることを目的としていますが、その反面、在庫切れのリスクがあります。特に、予期せぬ需要の変動やサプライチェーンの混乱が発生した場合、必要な部品や資材が不足し、生産ラインが停止する可能性があります。実際にコロナ禍では、ジャストインタイムを導入していた多くの企業が、部品不足などの影響でライン停止の危機に追い込まれました。
自然災害や感染症以外にも、仕入先の倒産・廃業や生産能力低下、海外仕入先の政治的混乱による生産停止など、サプライチェーンが混乱する要因は多くあります。変化の波が大きい今日において、ジャストインタイムでの調達では、分散購買などのリスクヘッジがより重要といえます。
品質管理コスト
JITの導入により、生産の効率化が図られる一方で、品質管理コストが増加する可能性があります。少量生産や多品種生産に対応するためには、品質検査や管理の頻度が増えることがあり、これに伴うコストが発生します。また、品質不良が発生した場合の影響も大きくなるため、徹底した品質管理体制が求められます。
導入の手間とコスト
JITの導入には、生産の標準化や流れ化といった仕組み作りの手間、それらの実現のためのコストがかかります。生産工程の見直しや従業員のトレーニング、新しいツールやシステムの導入など、多くの時間と資金が必要です。
下請け企業への負担が増加
JITの導入により、下請け企業への負担が増加することがあります。特に、小規模な下請け企業にとって、頻繁な納品や小ロット生産は負担が大きく、コストや労力の増加につながることがあります。この負担が大きくなりすぎると、サプライチェーン全体の効率が低下するリスクもあります。
実際に、ジャストインタイム方式を採用する企業で、下請け企業が毎日決まった時間に納品しなければならないケースは多々あります。下請け企業側でのドライバー雇用、継続して納入するための見込み生産、時にはサプライヤー側が在庫を抱えなければならないといった状況もあります。自社が在庫を持たない代わりに、下請け企業へしわ寄せがいくという構図にならないよう、内示展開などの配慮が必要といえます。
発注ロット減による仕入れコスト増
JITでは、小ロットでの発注が求められることが多くなるため、仕入れコストが増加する場合があります。小ロット発注では、スケールメリットが失われ、単価が高くなることが一般的です。また、仕入れコストの増加は製品のコストアップに直結するため、価格競争力が低下するリスクもあります。
環境負荷の増加
JITの導入により、生産や輸送の効率が向上する一方で、頻繁な納品や小ロット生産が環境負荷の増加につながる可能性があります。特に、輸送頻度が増加することで、二酸化炭素排出量が増加し、環境への影響が懸念され、持続可能な経営を目指す企業にとって、重要な課題となります。
ジャストインタイムが向いている企業
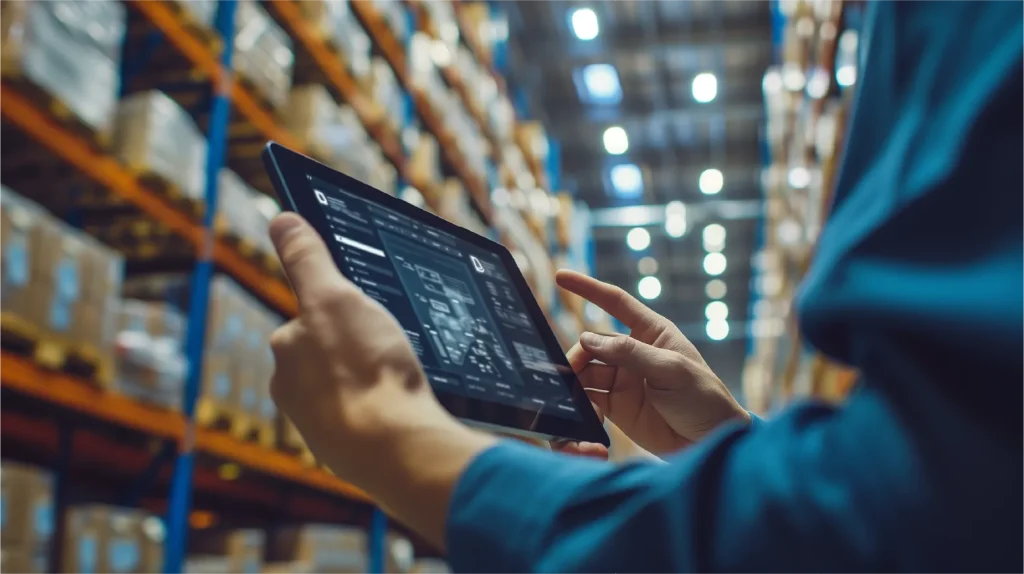
ジャストインタイムはすべての企業に適しているわけではありません。導入に適した企業には特定の特徴があり、自社がJITを導入すべきかどうかを判断するための評価基準となります。
ジャストインタイムの導入に適した企業の特徴
JITの導入に適した企業の条件は、主に以下3点です。
- 安定需要
- 強いサプライチェーン
- 生産工程の整流化
まず安定した需要が見込まれる市場において事業を展開していることが重要です。需要の変動が少ない市場では、平準化生産が実現しやすく、JITの効果が出やすくなります。次に、サプライチェーンが整備されており、信頼性の高いサプライヤーと強固な関係を築いている企業、最後に、生産工程が整流化されており、リアルタイムでの生産管理が可能な企業は、JITの導入に適しています。
22種類の生産管理システムをランキングで比較
初期費用相場や選び方のポイントをチェック
生産管理システムをそれぞれの特徴や初期費用相場などで比較したい場合は、「生産管理システムランキング」も是非ご覧ください。生産管理システムは、自社の製品・生産方式・企業規模などに適したものを導入しないと、得られるメリットが限定されてしまいます。事前適合性チェックや生産管理システムを選ぶ前に押さえておきたいポイントも解説していますので、製品選びの参考にしてみてください。