SLP(システマティックレイアウトプランニング)とは 具体的な手順やメリット、デメリットを解説
公開日:2023年07月05日
最終更新日:2025年03月19日
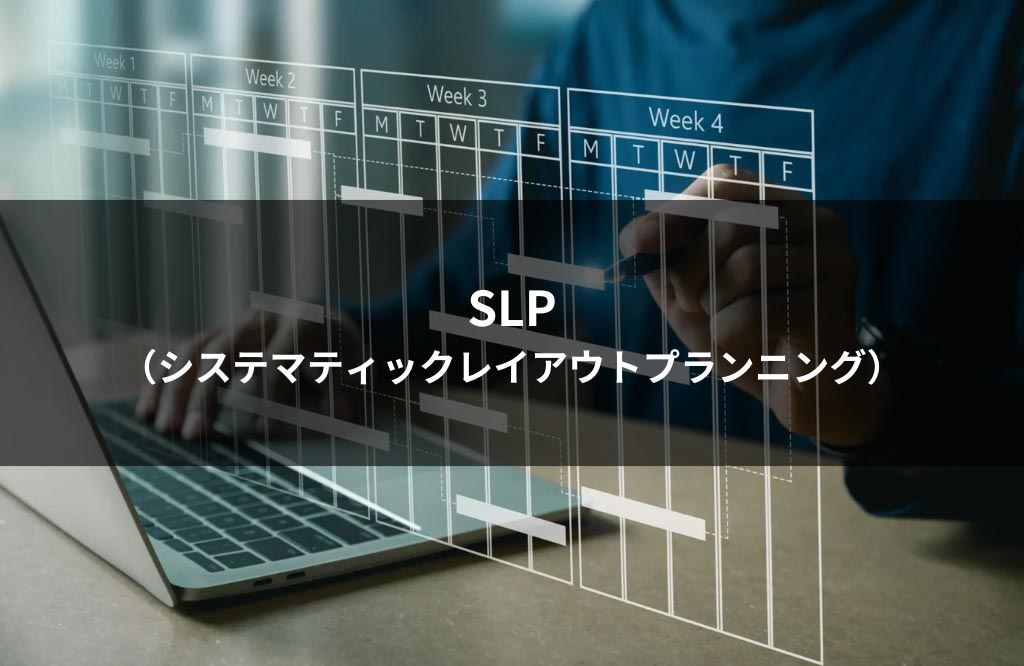
製造業において生産ラインや工場のレイアウトを最適化し、生産性を向上させる手法の一つとしてSLP(システマティックレイアウトプランニング/Systematic Layout Planning)があります。生産管理における生産効率化や、新工場設立時などで活用できる手法です。
本記事では、SLPの基本概念や手順、工程分析の方法について解説します。また、SLP導入の目的や注意すべき点についても解説します。
SLPとは
SLP(システマティックレイアウトプランニング/Systematic Layout Planning)とは、工場や生産ラインのレイアウトを決定するための体系的な手法です。1961年に米国のコンサルタント、リチャード・ミューサーが提唱し、現在も設備レイアウトの基礎として幅広く活用されています。
SLPでは、以下のような幅広い要素を総合的に分析したうえで、生産工程での搬送距離が最短になるようレイアウトを設計・改善します。
- 製品の生産量や種類
- 作業フローや物の流れ
- 人の動き
- 作業環境
- 設備の面積
SLPの目的
SLPの目的は、合理的なレイアウト設計で生産効率を向上することです。具体的なレイアウト設計でいうと、工場立地が決まった後の分析や計画で活用します。
生産工程の中で発生する問題や課題を明確にし、SLPの手法で現場改善を進めると、移動距離の短縮やスペースの有効利用、作業環境の改善などが実現できます。
具体的には、生産管理業務における生産効率向上や、IE(インダストリエンジニアリング)手法によるレイアウト改善の過程などで活用できます。
SLPの手順
SLPは生産予測をもとにした分析、製品の特性に応じた生産方法やフロー、レイアウトの候補案作成、レイアウトの決定という流れで進めていきます。
生産予測の調査
最初に、今後の生産予測の調査を行います。生産計画に基づいて、今後、どの製品がどれくらいの量や頻度で生産されるのかを予測します。将来、増産や減産により設備配置を変更する可能性も見据えてレイアウト設計を行う上で、この予測は非常に重要です。
単に現状の生産量に対して最適化を行うのではなく、将来的に生産量が変化した場合も考慮して、設備や生産ラインの配置を検討します。
P-Q分析
次に、P-Q分析により製品ごとの特性を分類します。
P-Q分析とは、製品種類(Product)と生産量(Quantity)に基づいて製品特性を分類する手法です。縦軸に生産量、横軸に製品の種類をとるグラフを作成し、以下のように製品を三つのグループに分けます。
生産数と品種のバランスに応じて、それぞれに適した以下3つのレイアウトに分類していきます。
- 製品別レイアウト
- グループ別レイアウト
- 機能別レイアウト
製品別レイアウト:少品種多量生産
少ない品種の製品を大量に生産する少品種多量生産では、基本的に流れ作業となるため、作業場や設備の配置も直線的になることが一般的です。ライン生産など、製品ごとに設備を直線的に配置する製品別レイアウトが適しています。
製品別レイアウトは大量の製品を短期間で作りやすいという反面、工程順序の異なる製品や異なる設備を使用する場合には、段取り変えが必要という特徴があります。同じ生産ラインを長期間にわたって稼働させ、設備の稼働率を上げる大量生産向きのレイアウトといえます。
機能別レイアウト:多品種少量生産
小品種多量生産に対し、多くの種類の製品を少量ずつ生産する多品種少量生産では、需要に柔軟に対応できる反面、効率的な設備の配置設計が難しくなります。主に、機能ごとに独立した生産ラインを持つ機能別レイアウトが適しています。
異なる製品を頻繁に切り替える多品種少量生産においては、製品の流れが複雑になりやすい傾向にあります。よって、作業者の移動や設備の変更切り替えに要する時間を最小化する工夫が必要です。機能別レイアウトでは、類似の機能をもつ設備がまとまって配置されるため、これらの変更をスムーズに進めることで設備稼働率が高くなります。
グループ別レイアウト:中品種中量生産
中品種中量生産は、少品種多量生産と多品種少量生産の中間的な位置になります。中品種中量生産では主に、複数の製品をグループ化し、共通の生産設備を利用するグループ別レイアウト方式が適しています。
中品種中量生産では、ある程度の柔軟性を持たせつつも、製品や設備の類似性が高いものをまとめて、効率的な生産を目指します。配置設計では、工程ごとに直線的にまとめたものや、機能ごとにグループとしてまとめたものを組み合わせます。P-Q分析により製品ごとの特性を分類できたら、次は「モノの流れ分析」を行います。
モノの流れ分析
モノの流れ分析では、材料や部品がどのように生産ラインを移動するかを可視化し、効率的な配置を検討します。具体的には、可視化した製品の流れを見ながら、無駄な移動や削減できる作業が無いかを検討します。
モノの流れ分析を目的別に分けると、以下のような方法があります。
単純工程分析
単純工程分析は、オペレーション・プロセスチャートとも呼ばれ、工程の全体概要を明確にするための手法です。作業の流れや手順を簡単なステップに分けて表現します。
加工や検査などの工程ごとに記号を割り当て、一連の流れを表現することで工程の全体概要が一目で分かるようになります。単純工程分析は、工程が直線的に表現しやすい少品種多量生産の分析に適しています。
多品種工程分析
多品種工程分析は、製品ごとの作業内容が一目で分かるようにする手法です。多種多様な製品を同じ生産ラインや設備で製造する際に、各製品の生産プロセスを類似しているもののグループに分けて表現します。縦軸に工程、横軸に対象となる製品や部品を取り、各製品がどのような工程を経て、生産されるのかを表現します。多品種工程分析の表により、工程が類似している製品をグループ分けできます。
多品種工程分析は、中品種中量生産や多品種少量生産の製品の工程分析に適しています。
フロムツーチャート
フロムツーチャートは「流入流出図」とも呼ばれ、製品や部品の移動経路や物の流れを整理するための手法です。製品の前後の工程間の関係を、上記のようなマトリックス形式で可視化します。
このチャートは、縦軸にFrom(どこから)横軸にTo(どこへ)を取り、重量や移動距離などの数値をいれることで製品の流れや改善すべき箇所の優先事項が分かります。
製造ラインの工程が複雑である場合、フロムツーチャートを活用すると、どの工程で逆流や無駄な移動が発生しているかを明確にできます。フロムツーチャートは特に、多品種少量生産方式の設備や工程の配置検討に役立ちます。
アクティビティ相互関連図表の作成
アクティビティ相互関連図表は、各作業や工程、作業エリアの関連性を示す図です。出入り口から出荷場までの工場の構成要素を書き出し、それぞれの要素がどの程度の近接性が求められるのかを表現します。
近接性の必要度が高い項目同士を洗い出し、優先的に配置を決定していくことが重要です。
アクティビティ相互関係ダイヤグラム
アクティビティ相互関連図表は、加工や検査などの各活動(アクティビティ)間の関係性や依存性を視覚的に整理するための手法です。加工や輸送、検査などの各活動(アクティビティ)のつながりを線の数によって表現し、関係性の強いもの同士はなるべく近づけるよう検討を行います。
面積相互関係ダイヤグラムの作成
面積相互関係ダイヤグラムでは、各作業スペースや機器がどのくらいのスペースを必要とするかを視覚化し、それに基づいて配置を設計します。工程同士の関連性の強さと近接性の必要度、実際の面積を確認しながら総合的な配置を検討します。
モノの流れ分析ができれば、結果を確認しながら最終的なレイアウト案を作成します。
レイアウト案の作成・決定
様々な分析結果を基に、製品の種類や生産量に応じた最適なレイアウトを決定します。また、レイアウト案は一度作成したら終わりではなく、稼働後は現場のフィードバックをもらいながら、適宜変更を加えていきます。
そのため、配置を決定する要因となった情報はしっかりと残しておき、前提条件が変更となった際に再検討を行えるようにすることが重要です。
SLPを用いるメリット
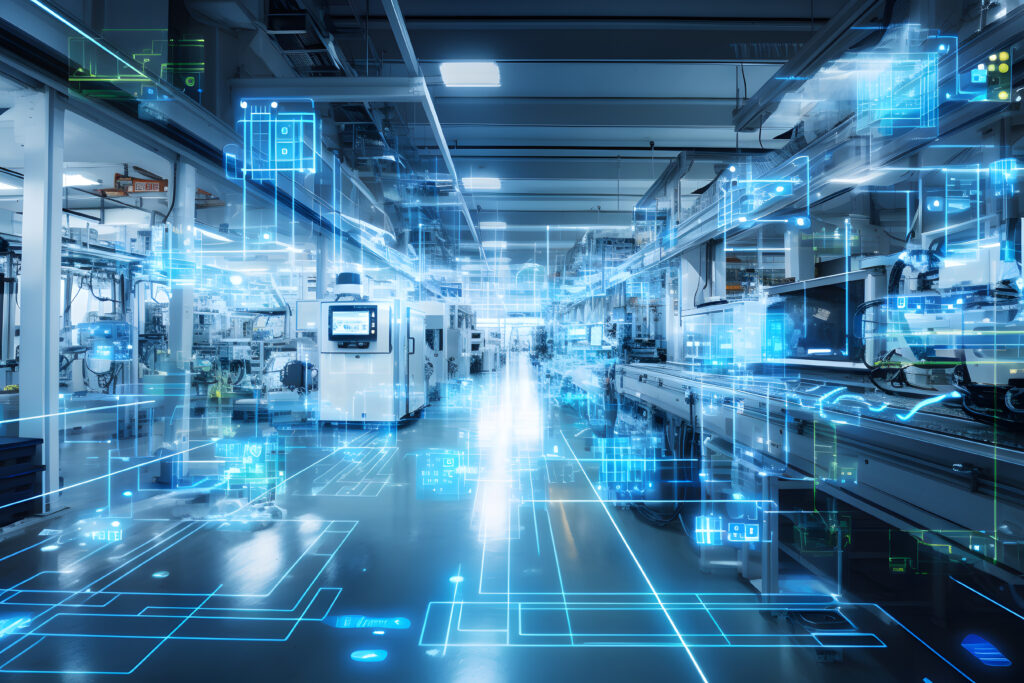
感覚的に配置を決定するのではなく、SLPにより科学的に数値の根拠に基づいた配置検討を行うことで、さまざまなメリットが得られます。具体的には以下のようになります。
- 作業効率の向上
- 移動距離の短縮
- スペースの有効活用
- 生産の柔軟性向上
- 安全性や作業環境の改善
SLPを行うことで、無駄な動作や作業の重複などを削減できるため、作業効率が向上します。また、移動距離の短縮によってリードタイムを改善することができます。結果的に、生産管理において重要な、製造コストの削減や納期短縮に繋がります。
生産性向上の他にも、スペースを有効活用してすることで、急遽、品種が変更となった際の一時保管スペースを確保できたり、生産の柔軟性向上にもつながります。また、作業者の動線について最適化することで、事故の発生リスクなども低減できます。
SLPの注意点
SLPにはメリットが多いですが、一方でいくつかの注意点があります。例としてフロー分析の正確性、関連部門間の協力、将来の柔軟性確保、安全性や作業環境の考慮、適切なコスト管理などが挙げられます。
工程分析の正確性
SLPを適切に行うためには、工程分析の正確性が欠かせません。生産工程や物の流れをデータなどの数値を用いて正確に把握し、無駄な移動や工程を特定することが重要です。
不正確なデータに基づいた分析は、効率の低下や無駄なコスト発生を引き起こすため、元となるデータについて本当に信頼性が担保できているのか細心の注意を払う必要があります。生産管理システムでリアルタイムに工程管理データを収集するなど、正確なデータを収集できる体制を構築する工夫が重要です。
関連部門間の協力
SLPを効果的に実施するためには、関連部門間の協力が不可欠です。生産部門だけでなく、購買、品質管理、設備管理など、複数の部門が一体となって協力し、それぞれの情報を共有することで、より効率的で無駄のないレイアウトが実現できます。
部門間のコミュニケーションが不足していると、意図しない配置ミスや機能不全が発生する可能性があります。この課題に対しても、生産管理システムで共通データベースを活用すると、情報共有が容易となります。
将来の柔軟性確保
SLPを導入する際には、将来の変化に柔軟に対応できるように考慮することが重要です。今後の市場の変化や技術革新により、設備や生産ラインの配置変更が必要になることがあります。
そうした状況に柔軟に対応できるよう、設計段階から余裕を持たせることが重要です。
安全性や作業環境の考慮
SLPでは、安全性や作業環境の改善も重要です。効率性ばかりを追求すると、作業環境や安全性が悪化する可能性があります。
従業員が安全に作業できる環境を確保し、快適な労働環境を提供することが重要です。
適切なコスト管理
SLPを導入する際には、コスト管理も重要な注意点です。レイアウト変更や設備導入には初期コストがかかるため、費用対効果を慎重に検討する必要があります。
配置を変更することによって得られる効果と、それに伴い発生するコストのバランスを検討しながら進めていくことが重要です。
まとめ
SLPは、工場や生産ラインのレイアウトを最適化し、生産効率を高めるための非常に便利な手法です。生産予測の調査、P-Q分析、モノの流れ分析などを通じて、生産性向上や作業環境改善を図ることができます。
SLPを利用する際には、他部門と連携し、正確な工程分析や将来の柔軟性、コスト管理などに注意しながら進めましょう。
22種類の生産管理システムをランキングで比較
初期費用相場や選び方のポイントをチェック
生産管理システムをそれぞれの特徴や初期費用相場などで比較したい場合は、「生産管理システムランキング」も是非ご覧ください。生産管理システムは、自社の製品・生産方式・企業規模などに適したものを導入しないと、得られるメリットが限定されてしまいます。事前適合性チェックや生産管理システムを選ぶ前に押さえておきたいポイントも解説していますので、製品選びの参考にしてみてください。