製造原価率とは。定義・計算式・改善策を徹底解説
公開日:2025年04月25日
最終更新日:2025年04月25日
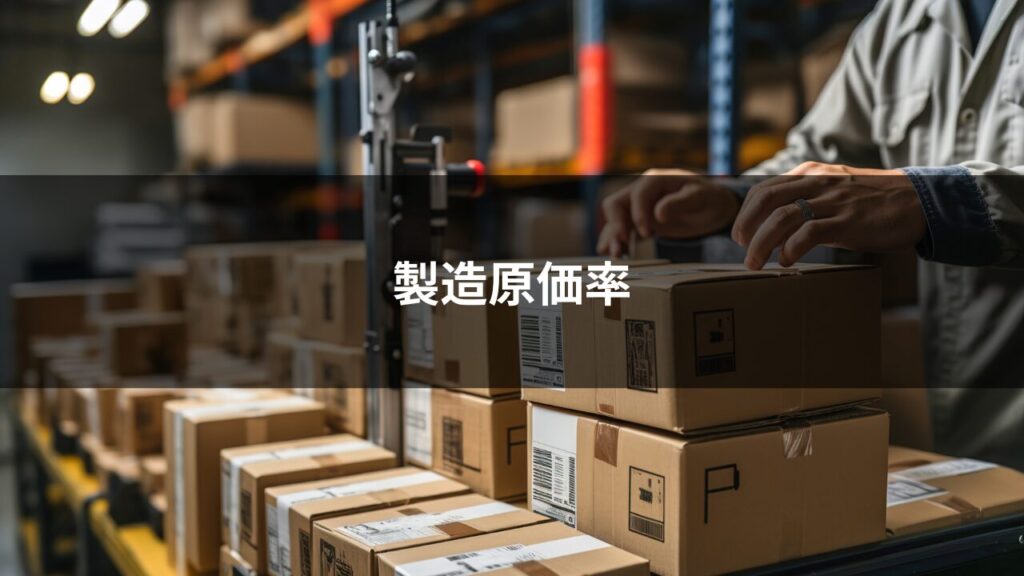
製造業において製造原価率は、収益性や生産効率を評価するための重要な指標です。
本記事では、製造原価率の定義から売上原価率との違い、製造原価の構成要素、業種別の平均値、改善策までを詳しく解説します。また、算出の際の注意点や効率的な管理手法についても紹介します。
製造原価率とは
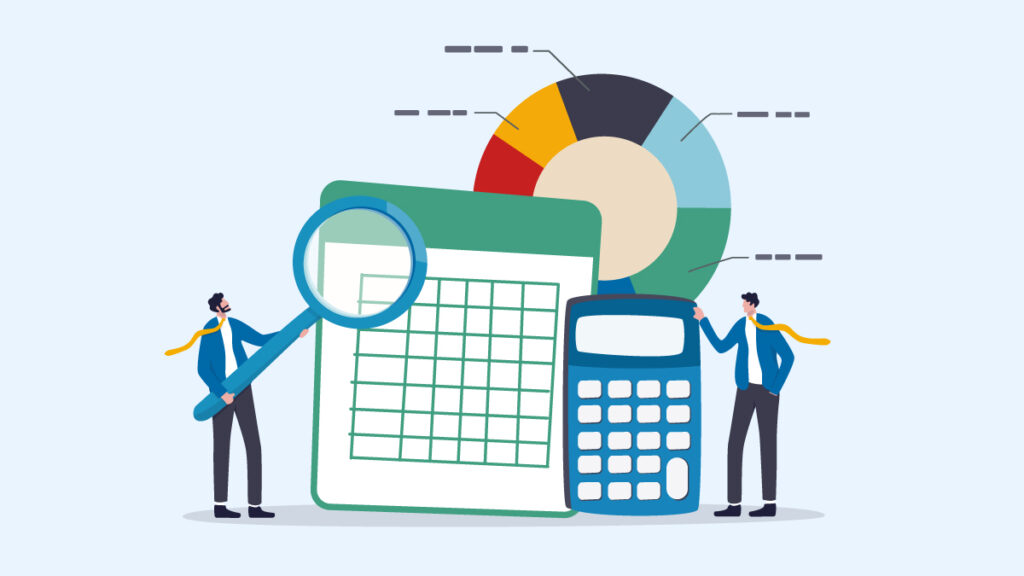
製造原価率とは、売上高に対して製造にかかったコスト(材料費、労務費、経費など)の割合を示す指標です。製造業では原価管理や利益率の分析を行う際に使用します。製造原価率が高いと、製造コストが利益を圧迫します。また、似た指標に「売上原価率」がありますが、両者には明確な違いがあります。
製造原価率の定義
製造原価率の計算式は以下のとおりです。
製造原価率の計算式
製造原価率(%)= 製造原価 ÷ 売上高 × 100
この指標を使うことで、自社の生産効率やコスト構造を把握できます。また、同業他社との比較や、年度毎の推移を確認することで、製造工程の課題を明確にできます。
例えば、製造原価率が高い場合、原材料費の増加や作業効率の低下、過剰な設備投資などが要因として挙げられます。また、価格戦略を立てる際や見積もりを作成する際にも、製造原価率は利用できます。製造原価の内訳を分析すれば、どの工程や資材が高コストなのかを把握し、改善につなげることができます。
売上原価率との違い
製造原価率とよく似た言葉に「売上原価率」がありますが、この2つは目的も定義も異なります。売上原価式は以下の式で表せます。
売上原価率の計算式
売上原価率(%)= 売上原価 ÷ 売上高 × 100
売上原価率は、販売した商品の原価(製造原価や仕入原価)をもとに算出し、販売活動まで含めた利益構造を確認するために使います。
製造業では、製造原価率と売上原価率の両方の指標を使うことで、製造と販売の両面から原価を分析します。製造原価率と売上原価率の違いをまとめると次の表のようになります。
製造原価率 | 売上原価率 | |
定義 | 製造にかかったコストの売上高に 対する割合 | 売上原価の売上高に対する割合 |
対象となるコスト | 製造原価 (材料費・労務費・経費など) | 売上原価 (製造原価+期首・期末在庫調整など) |
目的 | 製造工程のコスト効率を評価する | 販売全体の粗利益構造を把握する |
主な活用場面 | 生産管理、見積もり作成、 価格戦略の検討 | 財務分析、粗利率の把握、販売戦略の検討 |
業種による違い | 製造業で主に使用される | 製造業・卸売業・小売業など幅広く 使用される |
製造原価の構成要素
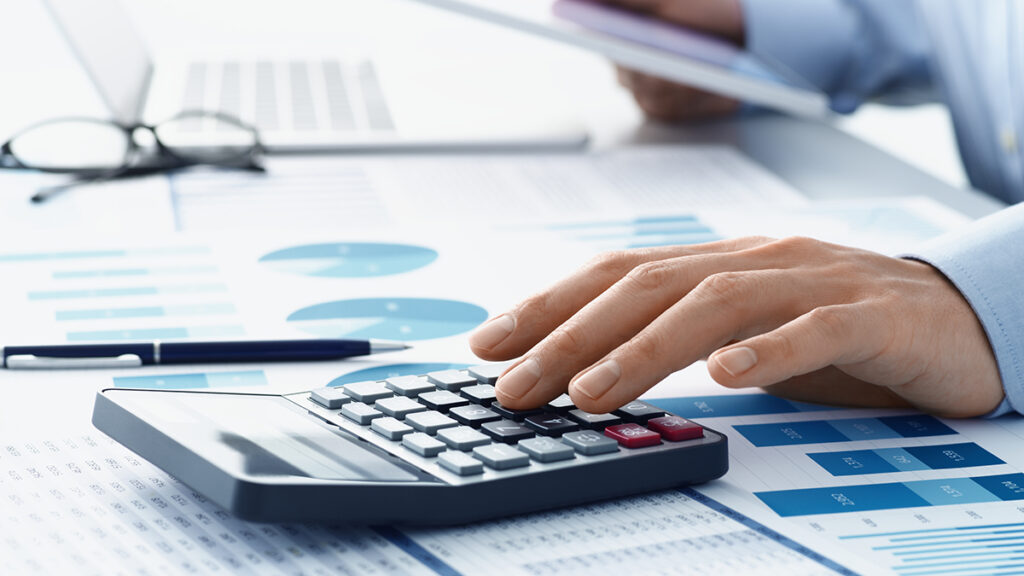
製造原価率を計算するための製造原価は、主に「材料費」「労務費」「経費」の3つに分類できます。それぞれの項目を正確に把握することで、原価管理の精度が高まります。また、それぞれの費用は単位製品あたりに明確にかかる直接費と製品ごとに特定できない間接費に分けることができます。
材料費
材料費は、製品を製造するために使用した原材料や部品などにかかる費用です。例えば金属や樹脂、ねじやボルトなど、完成品に組み込まれるものすべてが対象となります。材料費は仕入価格や使用量を削減することで、無駄な支出を減らせます。
- 直接材料費:製品1つあたりに明確に紐づく材料(例:自動車のボディ鋼板、電子機器の基板など)
- 間接材料費:製品ごとに特定できないが製造に使われる材料(例:潤滑油、洗浄剤など)
労務費
労務費は、製品の製造に直接かかわる作業員の人件費を指します。時給や日給、残業代などが含まれます。生産性を高めるには、作業時間と成果物のバランスを常に意識し、工程ごとの工数を見直すことが重要です。
- 直接労務費:製品の製造に直接かかわる作業者の賃金や手当
- 間接労務費:間接的な作業にかかわる人件費(管理職や保全・検査担当など)
経費
経費には、機械の電気代、工具の減価償却費、作業場の消耗品など、製造に必要な間接的な費用が含まれます。見落としやすい項目も多いため、一覧で項目を整理し、定期的に実態とのずれを確認することが重要です。
- 直接経費:特注品のために外注した加工費、金型費、特別検査費など
- 間接経費:減価償却費、水道光熱費など
製造業の平均的な原価率
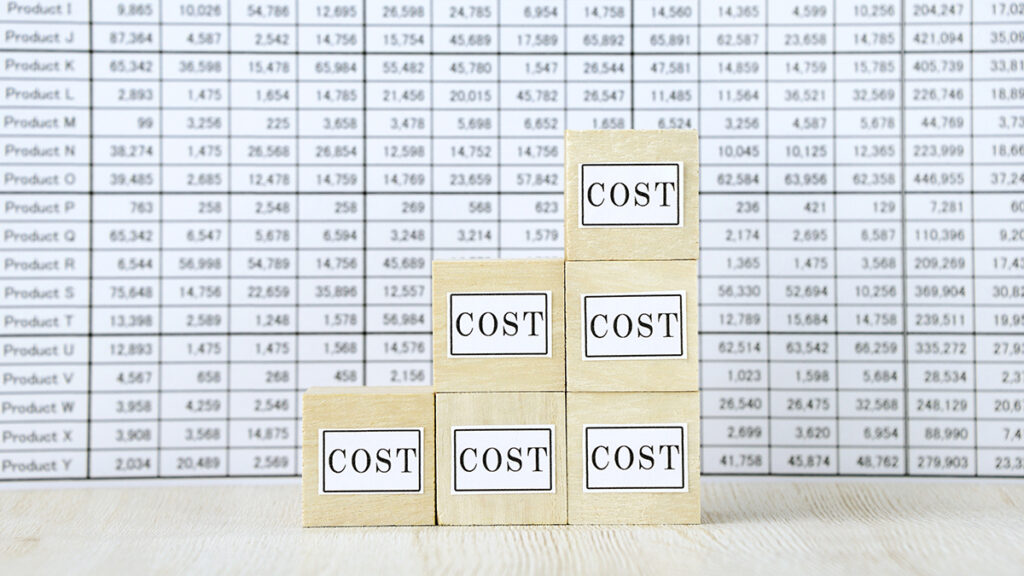
製造原価率は業種や企業規模によって異なるため、自社の数値を他社と比較するには、業界水準を理解することが重要です。
業種ごとの製造原価率の平均値
経済産業省の「工業統計調査」や「企業活動基本調査」によれば、製造業全体の平均的な製造原価率は約70〜80%の範囲に収まるケースが多く見られます。以下は一部の業種別の目安です。
- 食料品製造業:約75〜85%
- 医薬品製造業:約30~35%
- 自動車製造業:約80~85%
- 化学工業(医薬品を除く):約70〜75%
- 電気機器製造業:約60〜70%
- 輸送用機械器具製造業:約70〜80%
- プラスチック製品製造業:約65〜75%
これらの数値はあくまで目安であり、具体的な原価率は各企業の状況や製品特性によって異なります。自社の原価率を業界平均と比較し、コスト管理や価格戦略の参考とすることが重要です。
原価率を比較する際のポイント
原価率を他社や業界と比較する際には、同一業種・同規模の企業データを参考にすることが重要です。また、自社の原価率を分析する際には、以下の観点から見直すと精度が高まります。
内容 | ポイント | |
業種・業態の違い | 同業種・同規模との比較が前提 | 業種によって原価率の平均が異なる (例:素材産業は高く、精密機器は低い) |
製品単価・付加価値 | 高単価・高付加価値製品は 原価率が低くなる傾向 | 原価率が低くても利益が大きいとは 限らない |
固定費・変動費の構成 | 原価率の高低に影響 | 内製化が多いと原価率が高く見える 場合あり |
原価計算の方法 | 実際原価・標準原価などで差が出る | 比較対象の算出基準を揃える必要が ある |
販管費とのバランス | 営業利益率も確認する | 原価率だけで経営効率を判断するのは注意が必要 |
背景 | 技術力・設備・品質方針の 違いにより差が出る | 数値の背景まで踏み込んで理解する ことが重要 |
単純な数値だけでなく、構造的な違いや戦略の違いも考慮しながら分析を行えば、より実践的な改善につながります。
原価率を押し上げる6つの主要要因
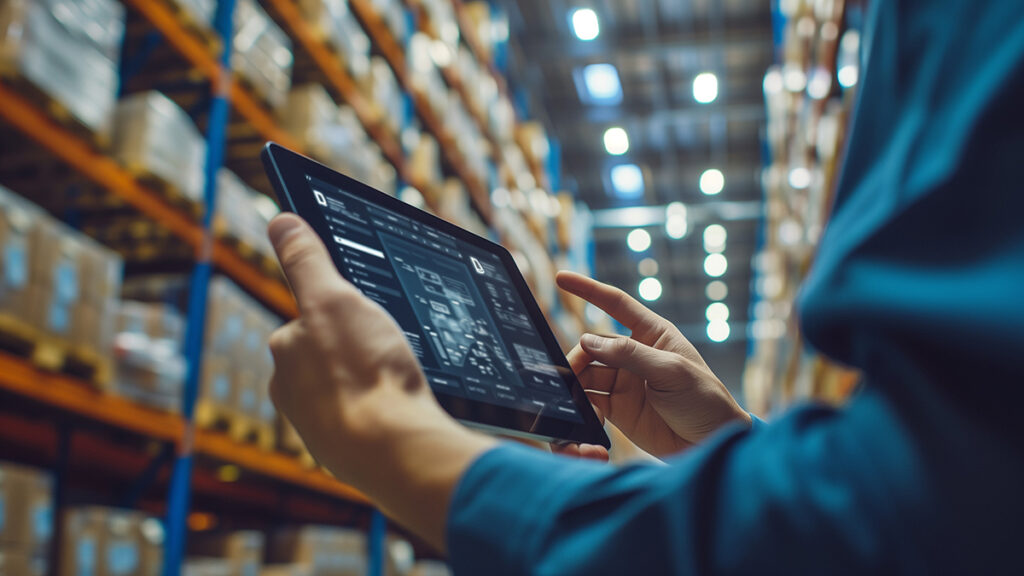
原価率が業界平均や想定より高い場合、以下の要因が考えられます。
- 材料費高騰
- 歩留まり悪化
- 工数ロスと設備稼働率低下
- 過剰在庫・滞留在庫コスト
- 品質不良・リワーク
- サプライチェーンリスクと協業不足
材料費高騰
最もわかりやすい原価率の押し上げ要因は、材料費の高騰です。一例として、非鉄金属や樹脂などの主要原材料の指数は、コロナ禍以降に大きく上昇しています。小麦などの食品原材料の価格も上昇しています。また、輸入材は円安によって割高になり、原価を圧迫するケースが増えています。
歩留まり悪化
歩留まりの悪化による材料ロスの増加も、原価に影響します。例えば、歩留まりが 98%→97%に落ちると、材料費は実質1.03倍となります。小さな歩留まり悪化でも原価率が跳ね上がるため、歩留まり管理=原価管理と考える必要があります。
工数ロスと設備稼働率低下
設備稼働率の低さによる工数ロスによっても、原価率は上昇します。停止時間が増えるほど、固定費が実際原価に上乗せされてしまうためです。
過剰在庫・滞留在庫コスト
過剰・滞留在庫も、直接目に見えないコストを製造原価へ静かに上乗せするため、注意が必要です。必要以上の在庫を保有していると、倉庫賃料や保管設備、光熱費などにくわえ、棚卸労務費も上昇します。在庫を置くだけでコスト増となるといえます。
滞留在庫の処理方法としては、廃棄・値下げ処分・再加工などが考えられます。その損失額は製造原価に直撃するため、期限管理が必要な品物やモデルチェンジ頻度が高い業界は要注意です。
品質不良・リワーク
品質不良によるリワークも、材料・人件費・エネルギーが二重に掛かり、原価押し上げ要因の一つとなります。1%の再加工は原価率を平均0.5 pt押し上げるともいわれ、歩留まり管理と並ぶ「影のコスト要因」と言えます。
サプライチェーンリスクと協業不足
サプライチェーンリスクによって材料費が上がり、原価率が高くなる場合もあります。よくある例は、部品不足や物流の遅延に対処するため、単価が高いサプライヤーから緊急購入するケースです。輸入品だと空輸費なども発生するため、仕入単価が2倍になることも珍しくありません。
このようなトラブルは、市況や需要の変化などの不可抗力で起きる可能性があります。一方で、サプライヤーとの協業不足で、在庫状況が把握できず起きる場合もあります。
製造原価率の改善方法
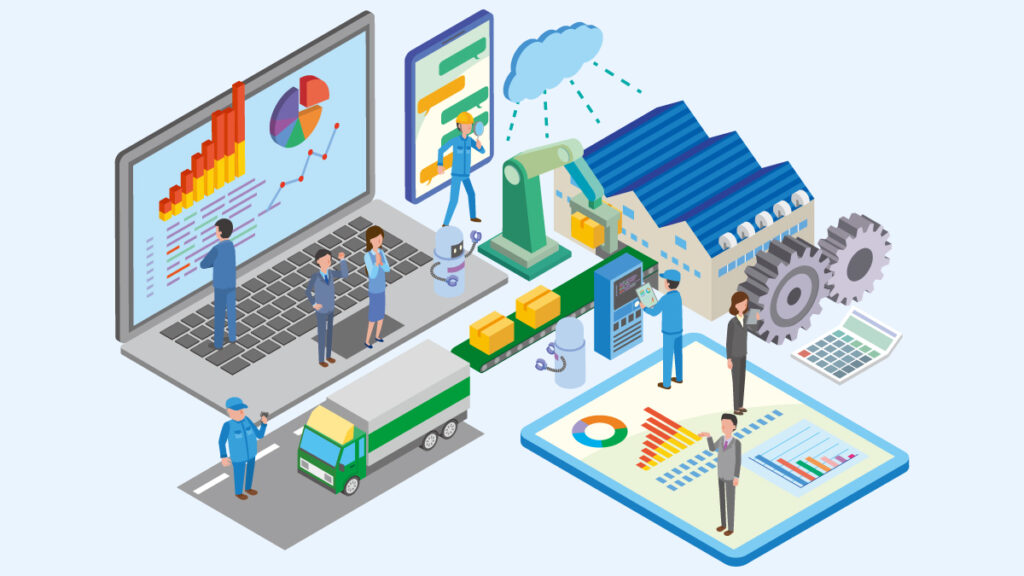
製造原価を改善するための方法として、材料費・労務費・経費の3つの観点から、具体例を紹介します。
材料費の削減
材料費を削減するには、仕入れ先との価格交渉や、まとめて購入することで単価を下げる方法があります。また、代替材料の活用や、設計段階で部品の点数を減らす原価企画も効果的です。具体的には以下のような方法があります。
- 同等品質で単価の安い代替材料への切り替え
- 材料の一括大量購入によるスケールメリットの活用
- 仕入先の見直し
- 不良品削減による無駄な材料ロスの低減
- 材料の標準化による在庫共通化と管理コストの削減
労務費の削減
労務費を抑えるには、作業手順を見直してムダな動きを減らすことが重要です。例えば、設備を自動化・省人化すると、必要な人員数を削減できます。さらに、多能工の育成を進めることで、柔軟な人員配置が可能になり、総労働時間の短縮につながります。具体的には以下のような方法があります。
- 作業の標準化・マニュアル化による作業効率の向上
- IE手法(時間分析・動作分析など)によるムダの排除
- 自動化・機械化による人手作業の削減
- 作業工程の見直しによる人員の適正配置
- 業務の外注化による労務費の変動費化
経費の削減
経費を削減するには、光熱費や保守費用などを細かく分析して、効率的な使い方を検討することが必要です。エネルギー使用を見える化して、無駄な消費を減らすと効果的です。また、在庫の保管スペースや量を見直すことで、倉庫費用や廃棄コストも抑えられます。具体的には以下のような方法があります。
- 工場の電気・水道などのエネルギー使用量の見直し
- 共通資材や間接材料の一括購入による単価低減
- 不要な外注・委託業務の見直しと内製化の検討
- 製造関連ソフトウェアやサービスの契約見直し
- 廃棄物処理費用の削減(分別・リサイクルの徹底)
製造原価率を計算する際の注意点
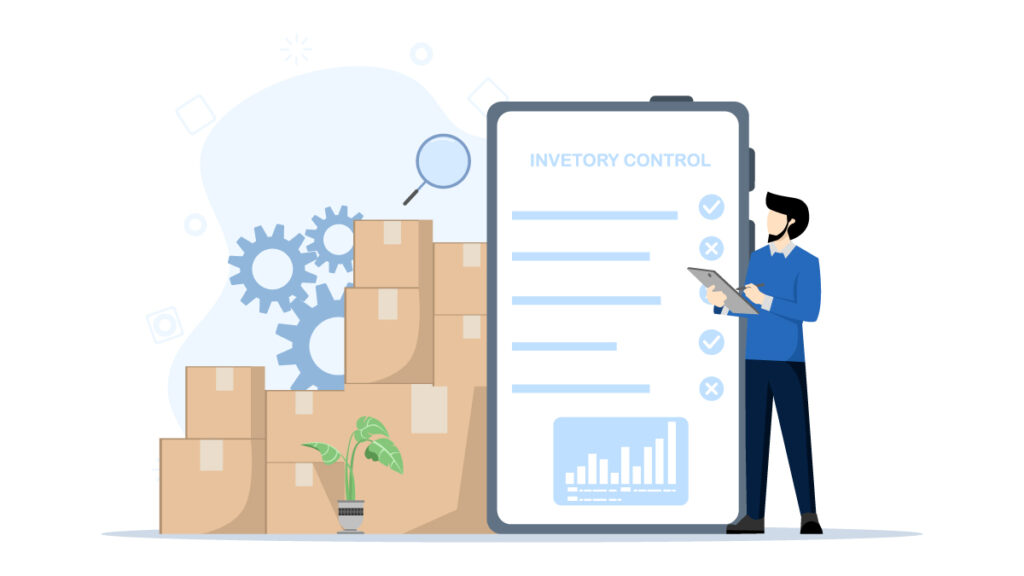
製造原価率を計算する際に注意すべき点について記載します。
製造原価の範囲を明確にする
製造原価に含める費用の範囲を明確に設定することで、計算のブレを防げます。
原材料費、労務費、製造間接費などが基本ですが、会社によっては設計費や品質管理費を含める場合もあります。この定義が不明確だと、部署間で異なる基準に基づいた原価率が出てしまい、正確な比較や改善が難しくなります。まずは、自社で「どこまでを製造原価とみなすか」を明文化し、関係部門と共通認識を持つことが重要です。
棚卸資産(仕掛品・製品)の増減を考慮する
製造原価率を計算する際、棚卸資産の増減も考慮に入れる必要があります。仕掛品や製品の在庫が月初と月末で大きく変動していると、当月の製造原価と売上が一致しないため、正しい原価率が導き出せません。
例えば月末に大量の製品在庫が残っている場合、それらのコストは当月の売上には反映されないため、原価率が一時的に低く見える可能性があります。製造原価率を算出する際には、在庫の変動を調整した実質的なコストで分析する必要があります。
→ 棚卸しとは?よくある課題と解決策、システム導入の注意点を解説
月次でのブレに注意する
製造原価率は月次で変動することがあるため、単月の数値だけで判断しないよう注意が必要です。季節要因による稼働率の変化や、原材料価格の高騰、残業増加など、一時的な要因によって数値がブレることも多くあります。
過去3〜6ヶ月の推移を見ながらトレンドを確認し、一時的な変動か構造的な課題かを見極める必要があります。継続的なモニタリングにより、根拠ある改善策を立てられます。
間接費の配賦方法に注意する
製造原価に含まれる間接費の配賦方法によって、原価率の数値が大きく変動します。間接費は製品ごとに直接対応しづらいため、一定の基準で割り振る必要がありますが、その基準が実態と合っていないと、製造原価が不適切に計上されます。
例えば、作業時間に応じて配賦する方法が多いですが、機械の稼働率やライン構成の変化によって、別の基準の方がより有効な場合もあります。定期的に配賦方法を見直し、実態に即した基準に更新することで、原価管理の精度が向上します。
製造原価率を効率的に算出する方法
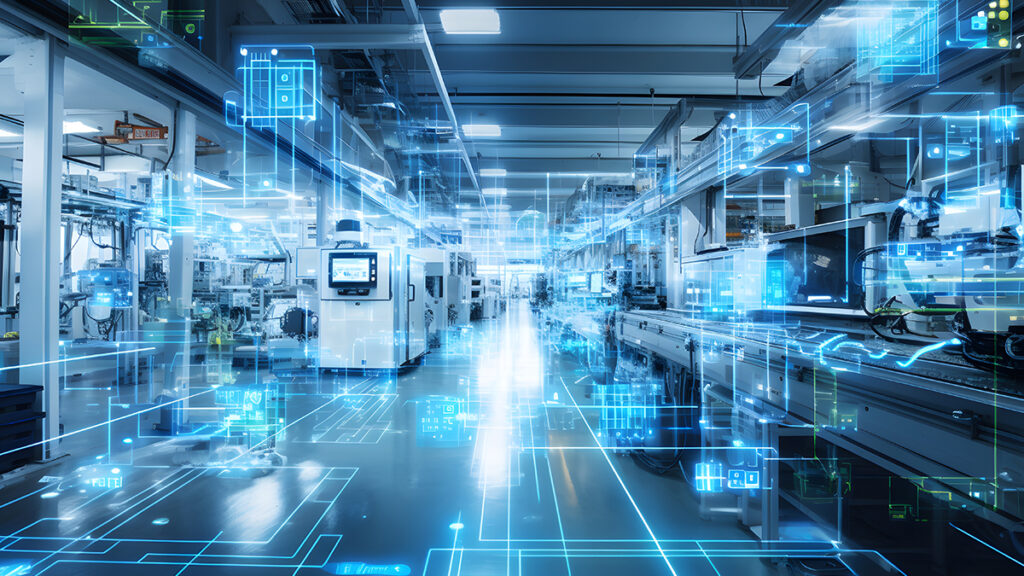
製造原価率を効率的に算出するには、日常業務の中に「見える化」や「自動化」の工夫を取り入れることが重要です。ここでは、製造原価率を効率的に把握するための具体的な方法を紹介します。
製造原価と売上高の見える化
まず、製造原価と売上高の数値を常に把握できる状態を整えます。部門別や製品別にデータを整理し、ダッシュボードや一覧表で視覚的に確認できるようにすれば、原価率の算出作業が格段に楽になります。情報の発散を防ぎ、関係者全員が共通認識を持てるようになります。
原価計算テンプレートの活用
Excelや専用ツールでテンプレートを用意し、誰でも同じ手順で原価率を計算できる仕組みをつくります。テンプレート内に必要な項目や計算式を組み込んでおけば、入力ミスや計算ミスを減らせます。標準化することで、属人化を防ぎ、作業時間も短縮できます。
定期的に自動集計・可視化する
日々の入力データをもとに、月次や週次で自動的に原価率を集計・可視化すれば、手作業による計算の手間を減らせます。BIツールやクラウド型の会計・生産管理システムを活用すると、リアルタイムで数値の変化も把握できます。定点観測により傾向分析も行いやすくなります。
在庫管理と連動して計算精度を高める
製造原価率の算出に在庫情報を正確に反映させることで、より信頼性の高い数値が得られます。在庫管理システムと原価計算シートやツールを連携させれば、棚卸資産の増減を即時に計算へ反映でき、仕掛品や完成品の動きも見ながら正確に原価率を把握できます。
原価率を計算する2つの方法
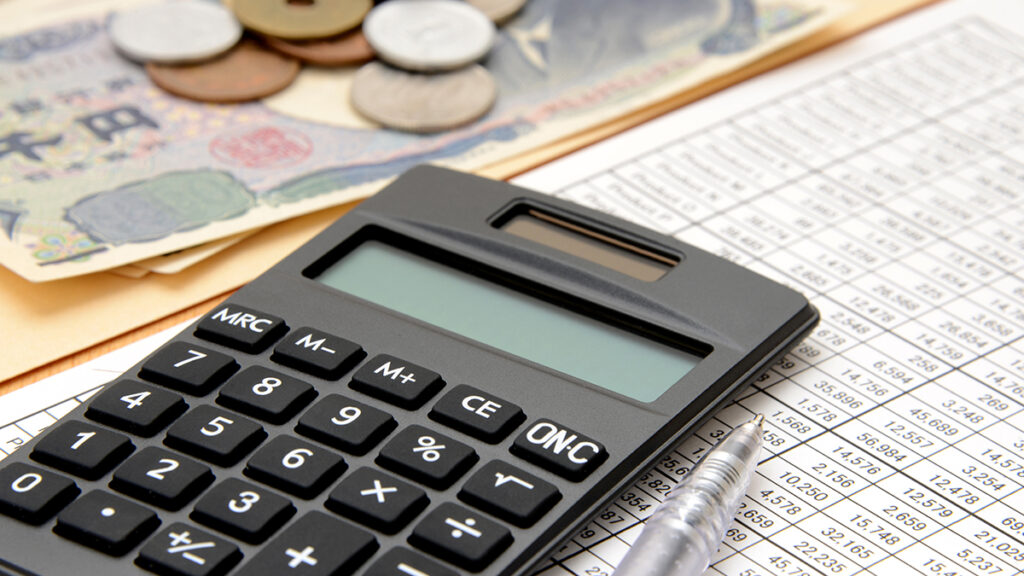
製造原価率の算出にはいくつかの手段がありますが、代表的なのが「エクセルによる手計算」と「原価管理システムの利用」です。自社の体制やコスト管理レベルに応じて、適切な方法を選ぶことが重要です。
それぞれの方法の特徴を表にまとめると以下のようになります。
Excelでの管理 | 原価管理システムの利用 | |
初期導入コスト | 低コスト (既存ソフトで対応可能) | 高め(システム導入費、設定費が必要) |
運用コスト | 基本的にかからない (人件費除く) | 月額費や保守費が発生することが多い |
データ入力 | 手動入力が中心、 ミスが起きやすい | システム連携により自動取得が可能 |
原価率計算の自動化 | 数式やマクロで ある程度対応可能 | 材料費・労務費・経費から原価率を自動算出 |
リアルタイム性 | 手動更新が必要 | 在庫や稼働状況と連動してリアルタイム反映 |
拡張性 | 他部門システムとの連携は困難 | 販売・生産・在庫システムと連携可能 |
エクセルを使えば、売上高や製造原価の数値を入力するだけで簡単に原価率を算出できます。関数(例:=製造原価/売上高*100)を使えば自動化も可能です。ただし、手入力によるミスやデータの更新漏れには注意が必要です。
一方で原価管理システムを導入すれば、部門別・製品別の原価を自動で集計・計算でき、作業効率が大幅に向上します。棚卸データや仕掛品の情報もリアルタイムで反映できるため、正確かつ迅速な原価率の把握が可能です。ただし、導入コストや運用教育の負担も考慮が必要です。
製造原価率の管理には生産管理システムがおすすめ
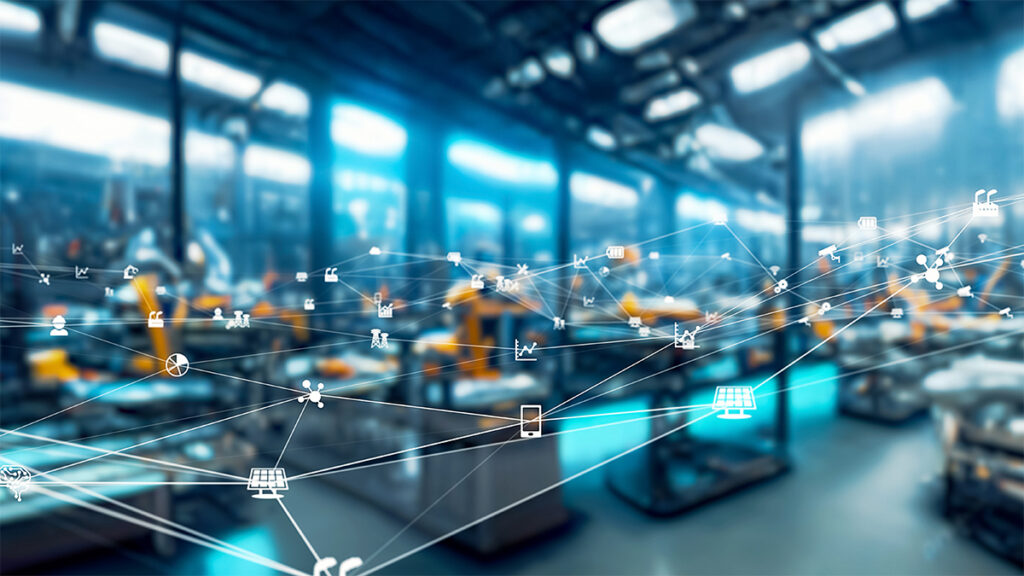
製造原価率の管理には生産管理システムの導入がおすすめです。原材料費や労務費、製造間接費など、複雑に絡み合うコスト要素をリアルタイムで可視化できるため、原価の分析や改善がスムーズに行えます。
さらに、システムを通じて過去のデータと比較しやすくなり、原価率の変動要因を素早く把握できます。手作業では見落としがちなロスやムダも数値で捉えられるため、継続的なコスト改善が実現しやすくなります。
→ 製造業向け原価管理システム9選!機能や特徴、導入メリット、選び方をまとめて紹介
22種類の生産管理システムをランキングで比較
初期費用相場や選び方のポイントをチェック
生産管理システムをそれぞれの特徴や初期費用相場などで比較したい場合は、「生産管理システムランキング」も是非ご覧ください。生産管理システムは、自社の製品・生産方式・企業規模などに適したものを導入しないと、得られるメリットが限定されてしまいます。事前適合性チェックや生産管理システムを選ぶ前に押さえておきたいポイントも解説していますので、製品選びの参考にしてみてください。