2025年05月02日
【生産管理システム】1人あたり売上1.4倍!脱アナログ・脱属人化で棚卸工数は1/10に圧縮、欠品や出荷遅れはゼロに
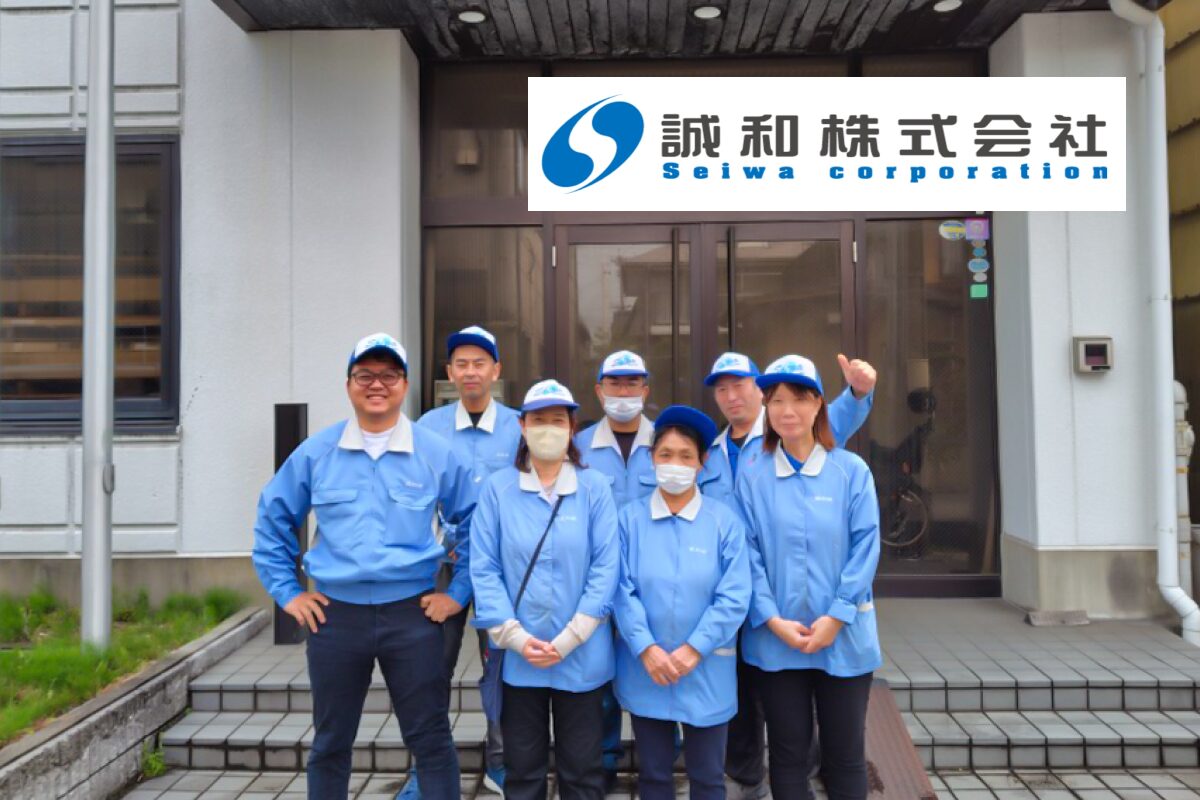
誠和株式会社
業界 | 成型品業界 |
---|---|
会社規模 | 30~99人 |
機能 | 受発注管理、在庫管理、工程管理、生産管理 |
システム概要
課題
- 完成品の在庫管理は紙・エクセル 在庫差異が原因で急ぎ生産が発生
- 部材の在庫管理は目視確認のみ、欠品で出荷日調整が必要になる場合も
- 紙の棚卸しで現場負担が大きく、月末に終えられないことも
- 紙とエクセルを使った棚卸しを、複数人で1日以上かけて実施
- 生産計画は現場へ一任、加工担当者しか進捗を把握できなかった
- 出荷検品は目視確認 人的ミスによる誤出荷をなくすことが難しかった
解決策
- SmartFとハンディ端末によるQRコード管理を導入
- 入出庫や棚卸しはハンディ端末によるQRコード管理化
- 自動計画機能で受注データをもとにした生産計画を自動作成
効果
- QRコードを活用した在庫管理で、欠品の頻度は10分の1に
- 部材在庫をシステム上で管理できるようになり、出荷遅れ0件
- 完成品の棚卸工数を10分の1に圧縮 循環棚卸も可能に
- 部材の棚卸しはほぼ1人で完結、工数は3分の1以下に圧縮
- 工程管理機能で、生産計画・進捗管理の脱属人化
- QRコードによる出荷検品で、誤出荷はほぼ0件に
導入の背景
生産性向上には現場の脱アナログ・脱属人化が必要だと感じた
自動車業界向けの工業用スポンジやテープ、プラスチック製品を製造する誠和様。社長交代以降、より一層の生産性向上を推進されていました。
さまざまな改善を試みる中、特に現場において以下2つの課題を感じていらっしゃいました。
- 紙・エクセルの在庫管理:最新の現在庫数がわからない
- 属人化している製造工程が多い:多能工化が進まない
この現場の状況を変えるために、生産管理システムの検討を始めました。
スマートFに決めた理由
初期費用を抑えてスモールスタートできる
SmartFの一番の決め手は、初期費用を抑えてスモールスタートできる点でした。
同社は生産管理システムの検討に際し、金融機関からの紹介を中心に情報収集をされました。そして、最終的には4社比較となりました。しかし、SmartF以外のシステムは初期費用が1000万円以上かかる見込みで、予算取りが難しい状況でした。
SmartFはクラウド型で初期費用を抑えられ、IT補助金も活用できることから、スムーズに検討できたとのことです。
また、SmartFは低価格でありながら、在庫管理や基幹システムとのCSV連携など、求めていた機能面も揃っていました。週1回のアップデートで機能が拡充されていく点も、メリットを感じていただきました。
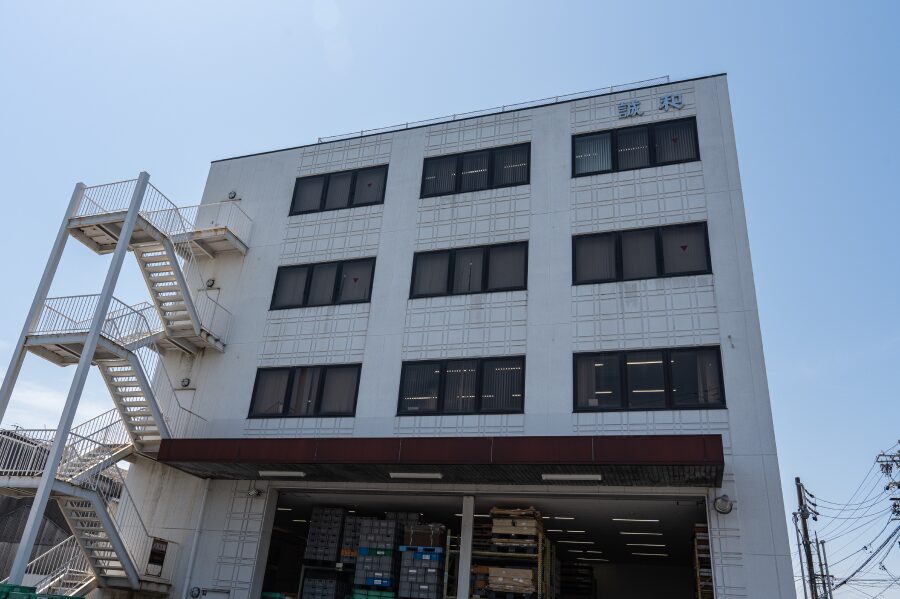
導入効果
完成品の在庫管理の見える化・脱アナログ管理に成功
【導入前】完成品の在庫管理は紙・エクセル 在庫差異が原因で急ぎ生産が発生
完成品の在庫管理は、紙の在庫表やエクセルで行っていた。人の手による作業のためヒューマンエラーをなくすことが難しく、実在庫と理論在庫の差異が発生していた。
例えば、完成品の出荷記録が漏れてしまい、「あるはずの在庫がない」という状況になることも。急ぎ生産の差し込みが、週に数回発生してしまっていた。
【導入後】QRコードを活用した在庫管理で、欠品の頻度は10分の1に
SmartFの在庫管理機能と、ハンディ端末によるQRコード管理を導入。QRコードから入出庫登録する運用に変更し、記録漏れが大幅に減少した。その結果、完成品在庫の欠品による急ぎ生産の頻度は10分の1に減った。
また、取引先の内示変動が多い製品には、安全在庫を設定。内示数が増えても安全在庫で備えられるようになり、今まで急ぎ生産が起きやすい製品でも計画生産が可能となった。
この計画生産の実現により、ピッキング担当者が早めに出荷準備を進められるようになり、出荷業務も効率化できた。
【在庫管理/完成品】SmartF 導入前後の変化
・紙・エクセル管理
・出庫記録漏れによる欠品に課題
↓
・QRコード管理を導入(紙・エクセル作業がゼロに)
・安全在庫の設定による計画生産の実現
部材の在庫見える化で欠品防止
【導入前】部材の在庫管理は目視確認のみ、欠品で出荷日調整が必要になる場合も
同社の部材はリードタイムが約1ヶ月必要なため、内示数・現在庫数・将来在庫数を計算し、事前発注している。
しかし、以前は部材数量を管理できておらず、生産のたびに材料置き場へ足を運ぶ必要があった。具体的には、現在庫数と今後の生産計画を担当者の頭の中で計算し、判断していた。
どうしても部材が足りず、出荷日調整が必要になることも2〜3ヶ月に一度ほど起きていた。
【導入後】部材在庫をシステム上で管理できるようになり、出荷遅れ0件
SmartFで入庫処理を行う運用に加え、製造工程完了時に使用部材数を自動引落する機能を導入。部材在庫のリアルタイムな見える化に成功し、現場へ都度確認する手間がなくなった。同社の部材不足が原因の出荷日調整は、現在0件となった。
また、部材の在庫数をシステム上で把握できるようになったことで、現場や発注担当者の負荷も軽減。特に発注業務においては、内示変動時の追加発注を検討しやすくなった。
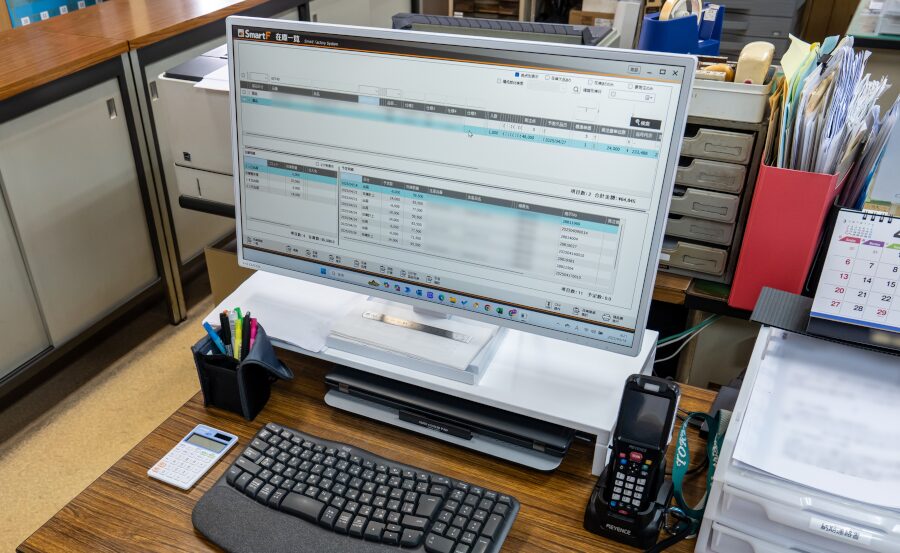
【在庫管理/部材】SmartF 導入前後の変化
・部材の在庫数を管理できていなかった
・在庫置き場で都度、在庫数を確認をしていた
↓
・QRコード管理・自動部材引落を導入(部材の在庫見える化を実現)
完成品在庫の棚卸しにて工数削減・循環棚卸を実現
【導入前】紙の棚卸しで現場負担が大きく、月末に終えられないことも
完成品在庫の棚卸しは、半期に一度実施。1000品番以上ある完成品をカウントし、白紙に品番や在庫数を手書きで記録・集計し、基幹システムへ記録していた。異なる場所に保管されている製品の合算など、煩雑な手作業が多かった。
また、毎日受注が入ってくるため、棚卸しのために生産を止めることができず、月末に棚卸しをやりきることが難しかった。月末に棚卸しが終えられなかった場合、遡って月末在庫を計算しなければならず、さらに工数が増大していた。
【導入後】完成品の棚卸工数を10分の1に圧縮 循環棚卸も可能に
SmartFとハンディ端末による棚卸しを導入し、紙での棚卸作業はゼロに。QRコードを読み取り、数量を入力していくだけの運用となった。保管場所が異なる在庫の足し上げなども自動化でき、完成品の棚卸工数は10分の1に大幅削減できた。
また、SmartFで在庫数をリアルタイムに更新できるようになったことで、循環棚卸も可能に。SmartF導入後は、月半ばから順次在庫数をカウントし、月末までもれなく入出庫記録をすれば、月末にそのまま正しい在庫数を計上できるようになった。
【棚卸し/完成品】SmartF 導入前後の変化
・紙への手書き
・複数の保管場所にある同品番の合算も必要
↓
・QRコードによる棚卸し(紙での煩雑な作業がゼロに)
・循環棚卸を実現(月末に集中する棚卸負荷を軽減)
複数人で行っていた部材在庫の棚卸しがほぼ1人で完結
【導入前】紙とエクセルを使った棚卸しを、複数人で1日以上かけて実施
部材在庫の棚卸しは、毎月月末に実施。この月次棚卸の数量と、得意先からの内示数を参考に、部材を発注していた。
部材の棚卸しでは、材料置き場の部材・製造現場の仕掛品の数量を、各担当者が紙で集計していた。これらを集計し、エクセルに手入力するまでの時点で、1日以上の工数が必要だった。
【導入後】部材の棚卸しはほぼ1人で完結、工数は3分の1以下に圧縮
完成品と同様に、部材在庫でもハンディ端末・QRコードを活用した棚卸しを導入。在庫数を記載した紙の集計や、エクセルへの手入力といった、アナログな作業がなくなった。
その結果、今まで複数人で分担しなければならなかった月末棚卸は、ほぼ1人で完結できるようになった。1日以上かかっていた月末棚卸は、1時間程度で終わるようになり、棚卸工数は3分の1以下に圧縮できた。
【棚卸し/部材】SmartF 導入前後の変化
・部材と仕掛品の在庫数量を紙で集計
↓
・QRコードによる棚卸し(紙での煩雑な作業がゼロに)
生産計画・工程管理の属人化を解消
【導入前】生産計画は現場へ一任、加工担当者しか進捗を把握できなかった
受注後の生産指示は、印刷した注文書を作業者へ渡すのみで、生産の優先順位付けや日程計画は加工担当者に一任していた。そのため、加工担当者しか生産計画を把握していない属人的な状況だった。
【導入後】工程管理機能で、生産計画・進捗管理の脱属人化
SmartFにて、受注情報に基づく生産指示の自動計画機能を導入。在庫の欠品防止の効果と、自動計画により、あらかじめ立案した生産計画に基づいた生産ができるようになった。
また、その日に必要な生産数も一覧で見られるようになり、生産計画や工程進捗が誰でも確認できる体制を整えられた。例えば、以前は外注品が戻ってきていないことに直前で気づくケースがあったが、今は次工程の予定がすぐ確認できるため早期発見できる。
さらに同社の工夫として、内示情報をCSV形式で取り込み、加工担当者もSmartF上で確認できるようにしている。今まで内示情報は紙管理で、発注担当者しか内示を把握できなかったが、現在はSmartFを通じて社内共有している。
【生産計画・工程管理】SmartF 導入前後の変化
・現場が受注情報をもとに生産計画を作成
↓
・受注情報に基づく自動計画(生産計画を脱属人化)
・生産計画・工程進捗・内示情報をSmartF上で見える化(工程管理を脱属人化)
出荷検品のシステム化で出荷ミスが激減
【導入前】出荷検品は目視確認 人的ミスによる誤出荷をなくすことが難しかった
毎日100件以上の製品を出荷する中で、出荷検品は目視確認が中心だった。出荷指示書・現品票・かんばんの3点照合を行っていたものの、類似品番やテレコの誤出荷が数ヶ月に一度起きてしまっていた。
【導入後】QRコードによる出荷検品で、誤出荷はほぼ0件に
SmartFから受注情報をもとにした出荷指示データを自動作成し、QRコードつきの出荷指示書を発行する運用を導入。QRコードによる出荷検品で、誤出荷はほぼ0件になった。
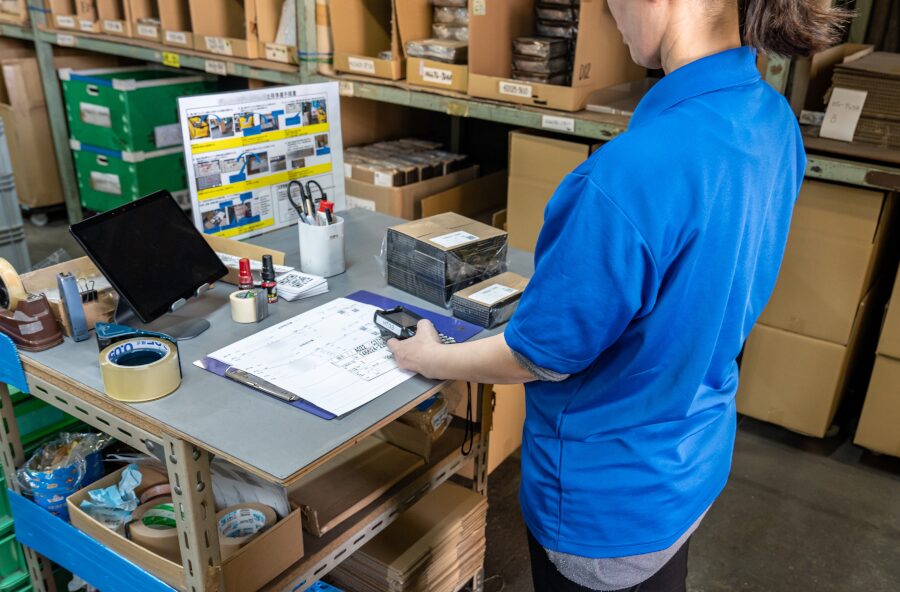
【出荷管理】SmartF 導入前後の変化
・目視での出荷検品
↓
・QRコード照合による出荷検品(誤出荷がほぼゼロに)
お客様の声
在庫管理・棚卸しに絶大な効果
SmartFの導入以降、「あるはずの在庫がない問題」がほぼ解決できつつあります。在庫不足での急な生産調整もなくなってきたことで、現場の負担も大きく削減できたと思います。急ぎの生産調整は加工担当者にとって大きな負担になるので、改善できてよかったと感じています。
特に効果が大きかったのは、棚卸しです。紙中心での棚卸は、集計作業が大きな負荷となっていましたが、現在はハンディ端末でさくさくと進められます。在庫数が数字として見えるようになったことで、心理的負担も軽減できたように思います。
また、ネクスタ社の導入支援は、全体の運用方法だけでなく、システムの使い方まで丁寧に教えていただけて助かりました。
1人あたりの売上が140%に
SmartFの導入により、かねてよりの経営課題であった「生産性向上」の効果が見えてきました。SmartF導入の1年目と2年目を比較すると、1人あたりの売上が140%に伸びています。
生産性が上がったのは、SmartFの活用でアナログな作業・属人的な業務を改善できたからだと思います。紙での棚卸しはQRコード管理に置き換わり、加工担当者しか把握できなかった工程進捗はシステムで見える化できました。熟練の加工担当者が回してくれていた現場管理をシステム化したことで、より効率的に生産できる体制ができつつあります。
これからもアップデートを重ね、より使いやすいシステムになっていくことを期待しています。
株式会社ネクスタ:営業担当の声
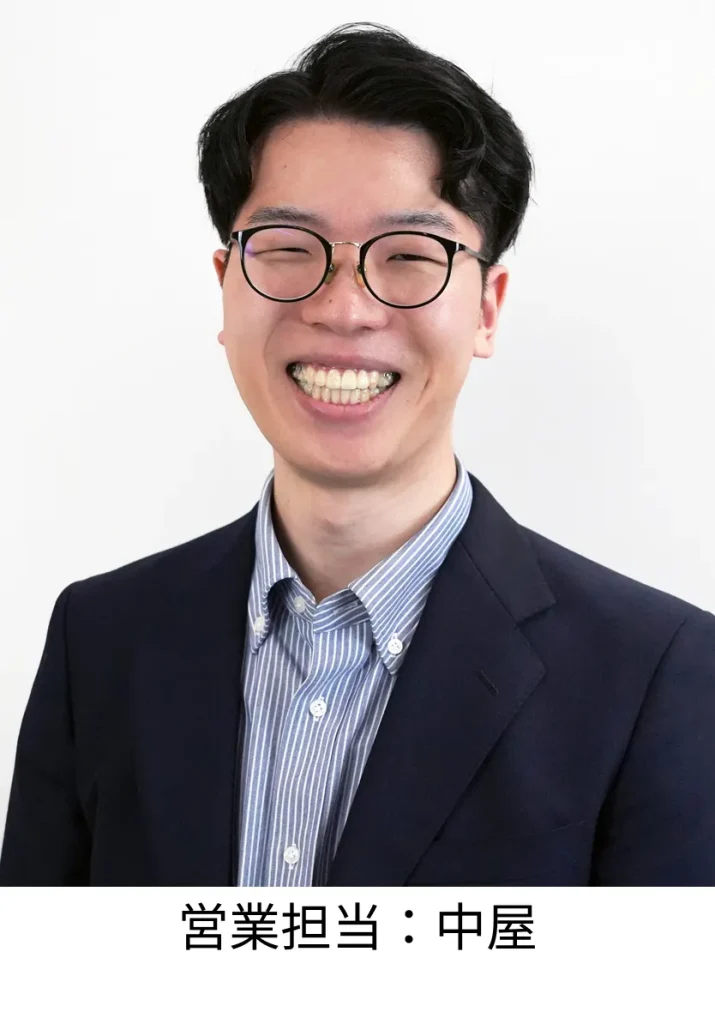
誠和様とのやり取りで最も印象に残っているのは、ファーストコンタクト時の対応です。ビジネスマッチング後のお電話で初めてご連絡を差し上げた際、冒頭で「他社様で決めるつもりで、ネクスタは断るつもり」とおっしゃられました。その言葉を受け、真にご納得いただいているのか、本当に誠和様にマッチするシステムなのかを確認すべく、丁寧にヒアリングを行いました。
ヒアリングの結果、他社システムをご検討中ではあるものの、まだ比較検討していただく可能性があると感じました。そこで改めて弊社システムの強みと誠和様にとってのメリットをご説明し、お打ち合わせの機会をいただくことができました。
その後、訪問を含めて約10回のお打ち合わせと、何十回にも及ぶお電話でのご相談を重ねました。社長様を中心に熱心にご検討いただき、多くのご要望やご質問をいただきました。それらに対し、最適なご提案が実現できたことで、弊社をお選びいただけたと感じております。
ときには厳しいご指摘をいただくこともありましたが、そのたびに学びを深め、営業として、人間としても大きく成長を実感することができました。今後もこの経験を活かし、より一層お客様に寄り添ったご提案を心がけてまいります。
株式会社ネクスタ:導入支援担当の声
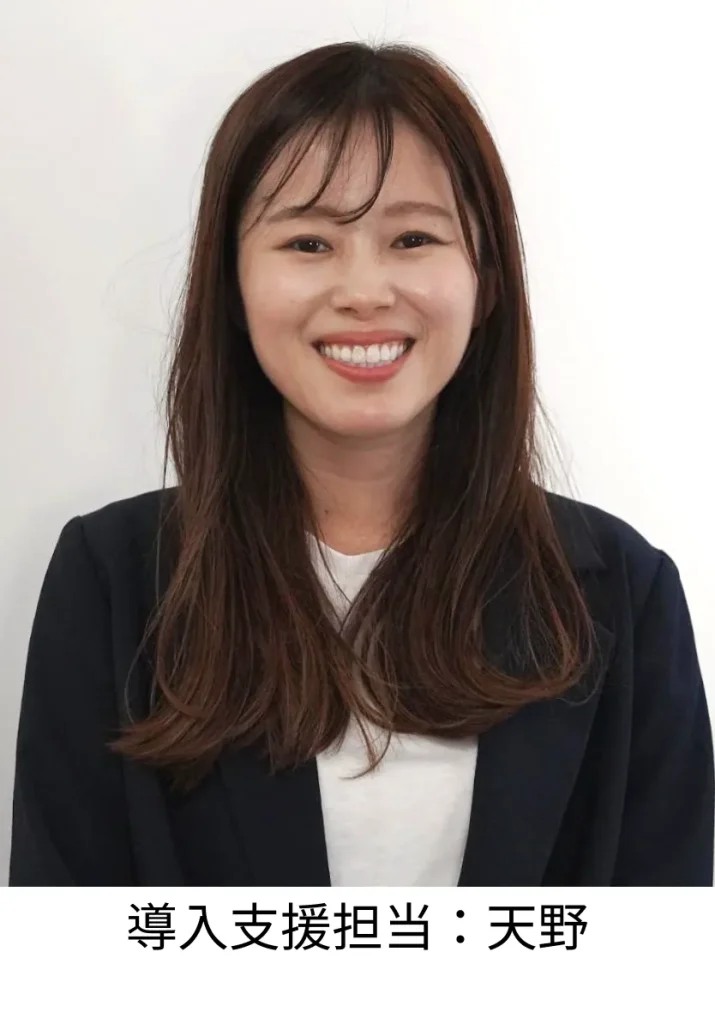
【運用提案する上で心掛けたこと】
誠和様が真剣にお話しくださる現状の業務や課題を、深く理解するよう努めました。課題に対しSmartFで何が可能か、運用フローや優先順位をどう最適化すべきかを考え抜きました。
【導入時を振り返って】
導入を進める中で、まだ未完成な機能もあり、理想の形に辿り着くまでに思った以上の時間がかかりました。それでも、弊社の提案や取り組みを信じ、辛抱強く歩みをともにしてくださったおかげで、少しずつ確実に形にしていくことができたと思います。
解決すべき課題が多く大変な期間だったと思いますが、このインタビューを拝見して、改めて感謝の気持ちでいっぱいです。ご期待に応え続けられるよう、これからもSmartFの進化を重ねていきます。

スポンジ・テープ、プラスチック・ゴム製品の加工から販売を手掛ける。自動車製品や電力向け開閉器など、高い品質が求められる業界でも採用実績多数。幅広い材質や強度、形状の加工が可能な技術力・ノウハウを活かし、設計提案や試作、量産まで対応可能。