製造業の生産性を向上するたった3つの方法 生産管理システムの効果・事例も紹介
公開日:2025年04月10日
最終更新日:2025年04月10日
在庫管理システム メリット-1024x576.jpg)
製造業の生産性向上の主要因は、人手不足や3M(ムダ・ムラ・ムリ)、生産計画の精度不足などです。自働化や設備改善、生産管理システムの導入により、工程の見える化や品質の安定化、利益向上を実現できます。当記事では、生産性向上の重要性や具体的な改善方法、中小・中堅企業の成功事例を解説します。
製造業における生産性向上とは
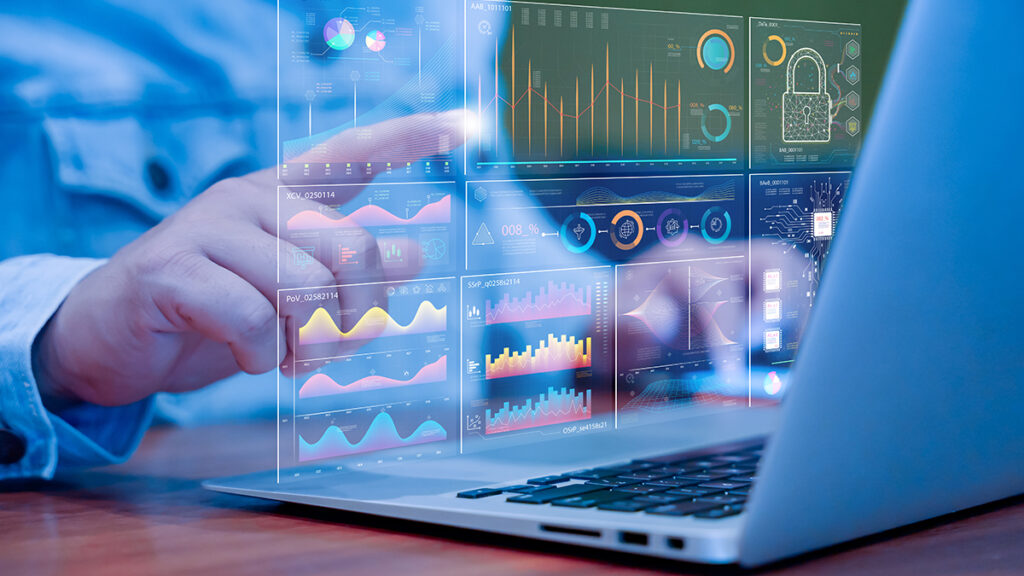
製造業における生産性向上とは、限られた資源(人・設備・時間・コスト)で最大の成果を生み出すことを指します。具体的には、同じ時間・コストでより多くの製品を作る、もしくは同じ製品をより少ないリソースで製造することを目指します。具体的な取り組みとしては、製造現場のムダの削減や、業務効率化などが必要となります。
また、生産性の向上は、利益の最大化にとどまらず、品質の安定、人材不足の解消、競争力の維持にも寄与します。長期的な企業成長にとって、不可欠な取り組みといえます。
なぜ今、製造業で生産性向上が求められるのか?
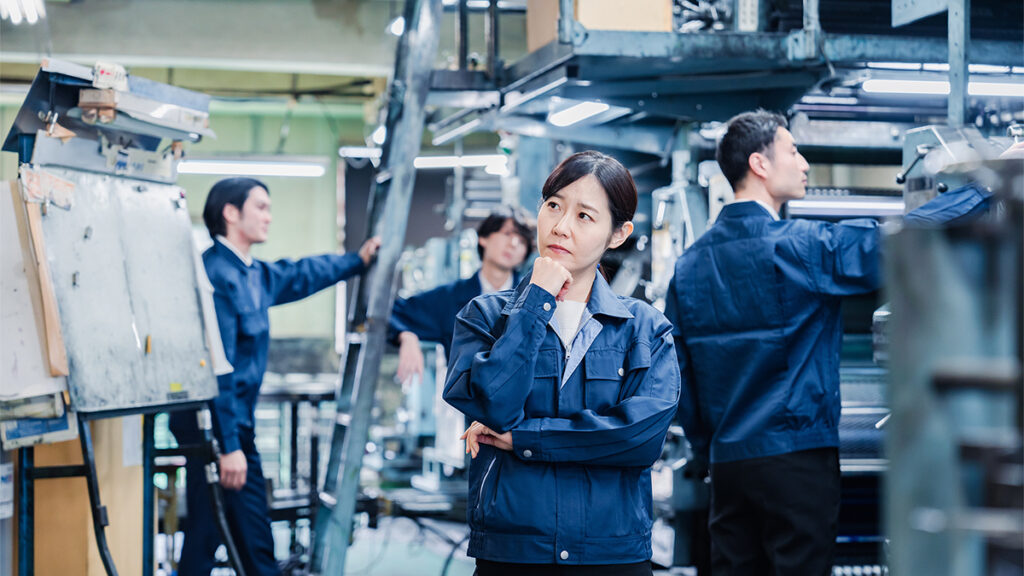
近年、日本の製造業は、グローバル市場との競争激化や深刻な人手不足といった課題に直面しています。さらに、原材料価格やエネルギーコストの上昇により、従来の方法では収益を確保するのが困難になりつつあります。
こうした背景から、生産性を高め、より少ないリソースでより多くの成果を出す仕組み作りが急務となっています。企業が継続的に成長し、市場での競争優位を維持するためには、現場単位での効率化だけでなく、経営レベルでの構造改革が不可欠です。
特に直近では、以下のような時事的背景が重なり、生産性向上の必要性がこれまで以上に高まっています。
労働人口の減少と働き方改革
日本では生産年齢人口の減少が加速しており、団塊世代の大量退職や技能伝承の断絶が現場に大きな影響を及ぼしています。さらに、働き方改革関連法により、時間外労働の上限規制が厳格化されたことで、「人を増やせない中で成果を出す」ことが求められています。
特に、中小企業では大企業よりも人材確保が難しく、「少人数でいかに成果を出すか」が大きな課題となっています。
カーボンニュートラル・GX(グリーントランスフォーメーション)対応
省エネルギーや排出量削減といった環境課題も、企業にとって無視できない経営テーマです。資源を無駄にしない、エネルギー効率の良い生産体制への移行は、まさに生産性向上と表裏一体の関係にあります。
近年は中小企業においても、取引先やサプライチェーンから環境配慮を求められるケースが増えています。生産性向上による環境配慮は、企業の信頼性や取引継続に直結する点でも重要といえます。
海外依存からの脱却と地政学リスク
パンデミックや国際情勢の不安定化により、調達の不確実性が増しています。国内回帰や内製化が進むなか、限られた工場リソースを最大限に活かすためには、効率的な生産体制の構築が不可欠です。
デジタル化(DX)の加速
AI・IoT・クラウドといったデジタル技術が急速に普及する中で、それらを活用した生産性向上への取り組みが競争力の分かれ目となっています。単なる省力化ではなく、データ活用による「賢い現場づくり」が、製造業の次のステージに進むための鍵です。
生産性向上のメリット
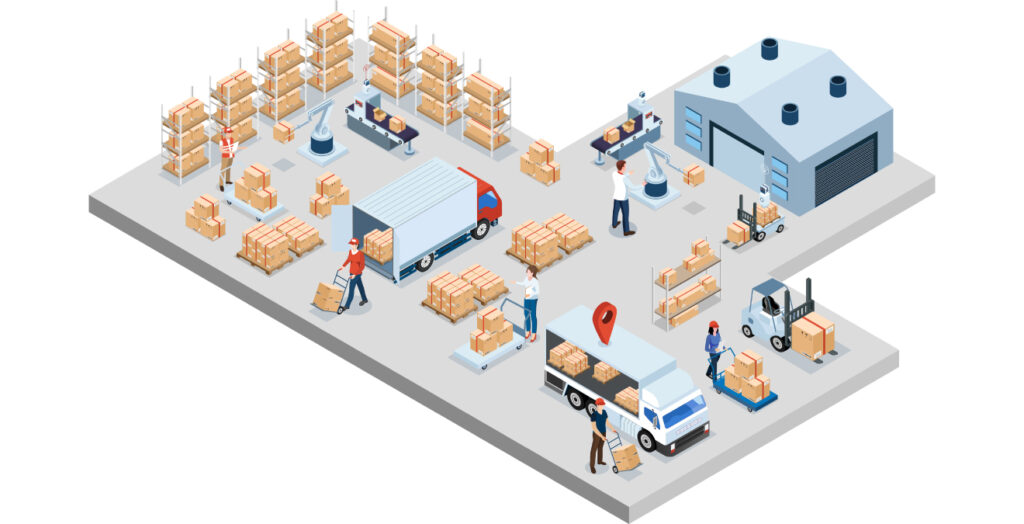
生産性を高めると、単に効率が良くなるだけでなく、企業全体にとって多方面の効果をもたらします。特に「人手不足の解消」「利益向上」「製品品質の維持・向上」の3つの面での恩恵が大きく、製造業における競争力強化に直結します。
人手不足の解消
自働化や業務標準化などを進めることで、少ない人数でも安定した生産を維持できるようになります。熟練者に頼らずとも同等の品質・効率を実現できる仕組みが整えば、新人や非正規人材でも即戦力化が可能です。結果として、人材育成にかかる負担も軽減され、持続可能な人材運用が可能になります。
利益向上
生産効率が上がれば、同じ時間・コストでより多くの製品を出荷できるため、単位あたりの利益が拡大します。また、ムダや不良の削減により、直接費・間接費の両面でコストダウンが実現します。こうした利益改善は価格競争力の強化や、設備投資・人材育成への再投資にもつながります。
製品品質の維持・向上
標準化や見える化を通じて品質管理の精度が高まり、不良品の発生を抑制できます。品質が安定することで顧客からの信頼も向上し、リピートやブランド力の強化につながります。また、トレーサビリティの確保により、不具合発生時の対応も迅速に行え、リスク管理力の向上にも寄与します。
生産性悪化の要因
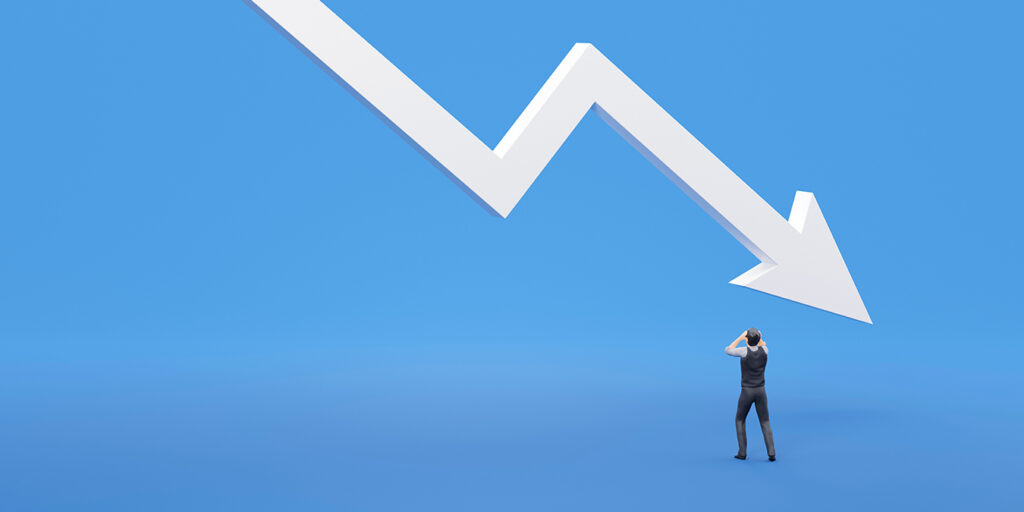
生産性の低下は、現場や経営のさまざまな要因によって引き起こされます。特に以下4つの事象は、生産性低下に大きく関わっています。
現場の人手不足による負荷増加
多くの製造業では、少子高齢化により若年層の確保が難しくなっています。さらに、ベテラン従業員の退職による技能継承問題も出てきます。この人手不足が慢性化すると、一人当たりの作業量が増加し、品質のばらつきや生産ラインの停滞につながります。
また、教育・研修を充分に行う時間が取れず、新人の即戦力化が遅れ、生産効率がなかなか上がらないという問題も発生します。
3M(ムダ・ムラ・ムリ)
製造現場では、ムダ(不要な作業や動作)、ムラ(作業のばらつき)、ムリ(過負荷)が生産性を著しく低下させます。
例えば、過剰在庫や段取りの手戻りといったムダな工程が存在すると、労力と時間が浪費されます。生産にムラがあれば、品質問題を起こす原因になります。さらに、工数圧迫によるムリが放置されると、作業者の疲弊や設備の劣化も進み、長期的に見てトラブル発生の温床にもなります。
部署・個人間のコミュニケーション不足
設計・製造・品質管理など部署間の連携が不十分だと、認識の相違や手戻りが頻発します。他にも、現場で発生した問題が管理者に伝わらず放置されてしまい、重大な問題に発展してしまう事もあります。
また、個人間の情報共有が不十分だと、作業の属人化が進み、トラブル時の対応力が低下します。このように、生産性向上には「全体最適」を目指した情報共有と連携体制が不可欠です。
設備のメンテナンス不足
設備故障は生産ライン全体の停止を招き、生産性に甚大な影響を及ぼします。定期的な設備点検・整備を怠ると、大きなトラブルに発展します。
特に、生産計画に余裕がない現場は、生産優先となり設備保全が後回しになりがちです。結果として突発的な修理対応に追われることになり、長期的にみると生産性が低下してしまいます。
業務の標準化不足
作業手順や品質基準が明確に定まっていないと、担当者ごとの判断やスキルに依存し、生産数や品質にバラつきが生じます。特に新人やパート従業員が多い現場は、業務の標準化がされていないとトラブルの温床になります。マニュアルや作業指示書の整備は、安定した生産と品質を維持するために必要不可欠です。
生産計画の精度欠如
実際の受注状況や在庫量を正確に把握せずに生産計画を立てると、過剰在庫や納期遅延といった問題が発生し、生産性が低下します。また、計画変更に柔軟に対応できないと、市場の変化に素早く対応できません。精度の高い生産計画を立てるためには、リアルタイムな情報収集と分析体制の整備が必要です。
生産性を向上する手順
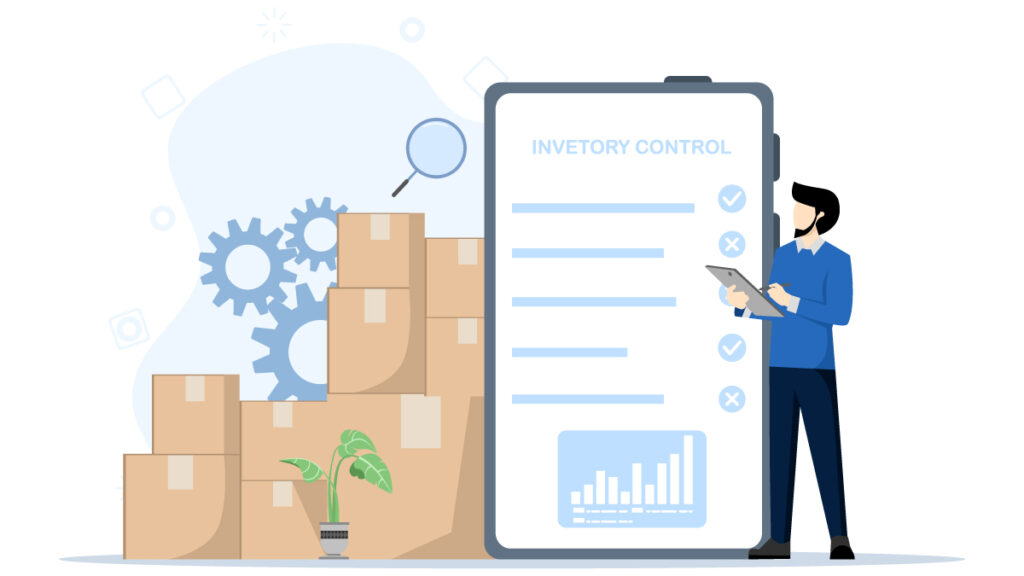
生産性向上には段階的なアプローチが効果的です。以下のステップに沿って取り組むことで、現場の実態に即した改善が可能となり、着実に成果へとつなげられます。
STEP1:目標設定
初めに「どの指標を」「いつまでに」「どのくらい」改善するのかを明確にします。
例:生産ラインAの時間あたり生産数を3ヶ月で15%向上させる
このように定量的な目標を設定することで、施策の方向性がブレずに関係者全体の認識統一が図れます。
STEP2:取り組み課題の明確化と現状把握
現場でのボトルネックや非効率な工程を洗い出し、現状を定量的に可視化します。例えば、ラインバランス分析を用いて、どこの工程がボトルネックになっているのか、どの作業にムリ・ムダがあるかを把握します。
現場でのヒアリングやデータの収集には、この段階でしっかり時間をかけて取り組むことが大切です。そうすることで、次の施策を立てる段階で、より的確な判断ができるようになります。
STEP3:課題解決に対する施策立案と実施・改善
課題が明確になったら、課題解決策を立案・評価し、優先順位に基づいて実行に移します。例えば、自働化設備の導入、作業手順の見直し、管理システムの導入などが代表例です。
実施後は、定期的に効果検証を行い、継続的な改善サイクル(PDCA)を回すことが重要です。
生産性を向上させるための改善策3つ
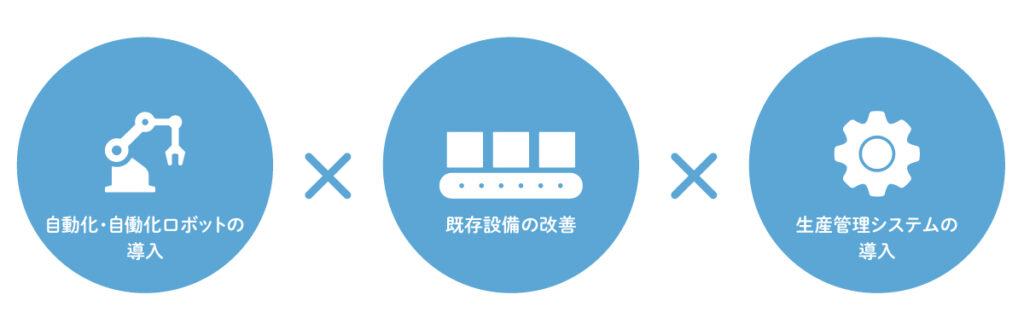
生産性向上のためには、現場の課題に応じた改善策を選択することが重要です。ここでは代表的な3つの施策を紹介します。
自動化・自働化ロボットの導入
単純作業や重労働の一部をロボットに置き換えることで、人手不足を補いながら、作業のスピードと正確性を向上させられます。協働ロボット(コボット)を活用すれば、省スペースかつ低コストで導入可能な場合もあり、中小製造業でも現実的な改善手段となります。
既存設備の改善
すべての既存設備を刷新する必要はなく、設備の点検・改善によっても大幅な効率改善が可能です。例えば、センサによる自動停止機能の追加や、保全スケジュールの見直しでトラブルを未然に防げます。稼働率向上やエネルギー使用の最適化も、重要な改善ポイントです。
生産管理システムの導入
業務の見える化・標準化を進めるうえで、ITツールの活用は欠かせません。生産管理システムを導入することで、手入力作業の削減、生産進捗の可視化、在庫管理の精度向上が実現します。また、日々蓄積する生産データに基づいた意思決定が可能となり、全体最適を見据えた効率的な運用が可能になります。
近年は低コスト・低難度で導入できるクラウド型生産管理システムも増えてきています。IT人材不足や現場のITリテラシーの壁を感じ、システム対応が遅れていた中小企業も、システムが検討しやすくなってきました。
生産管理システムが生産性向上に役立つ理由
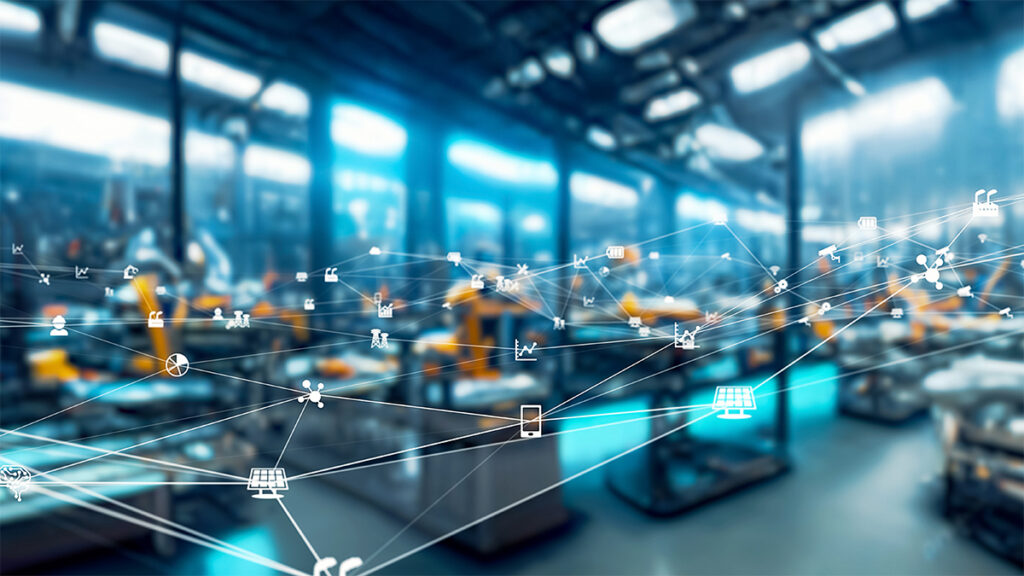
生産管理システムは、属人化しがちな管理業務を標準化し、正確かつ迅速な意思決定をサポートすることで生産性向上に役立ちます。ここでは、システム導入によって得られる具体的な改善効果を紹介します。
手書き・手入力による手間・ミス削減
帳票の手書きやエクセル入力などのアナログ作業は、転記ミスや確認漏れを招きやすく、品質・納期トラブルの原因になります。生産管理システムによるデータ連携を活用すると、このような人的ミスを防止できます。
さらに、入力情報はリアルタイムでシステム全体に反映されるため、現場と管理部門との情報のやり取りもスムーズになります。無駄な確認作業や重複入力も不要になります。
また、ハンディ端末などとの連携で、QR・バーコード管理が活用できるシステムもあります。このようなIoTツールも導入すると、手書き・手入力の手間を大幅削減できます。記録作業の時間短縮によって、現場の負担軽減も期待できます。
生産工程・進捗の見える化によるボトルネック特定・解消
生産管理システムを活用すると、生産工程・進捗を「見える化」できます。工程ごとの進捗状況や設備の稼働状態をリアルタイムで把握し、遅延やトラブルが発生しても即時に対応し、生産性を保てます。
また、作業実績をシステム上に記録していくと、作業のボトルネック分析や改善もできます。この作業データから、継続的な改善につなげることができます。属人的な判断に頼らず、データに基づいた改善が可能となるため、現場の生産性を安定的に高めることができます。
在庫適正化による余剰・欠品によるムダ削減
生産管理システム上で在庫情報を管理すると、社内の在庫も「見える化」できます。資材や仕掛品、製品在庫の状況を常に把握できるため、必要なときに必要な量だけを調達・生産できる体制が整います。
在庫の過不足は、製造業にとって大きなコストリスクとなります。過剰在庫は保管スペースと資金を圧迫し、欠品は生産停止や納期遅延を引き起こします。これらを解消することで生産性が向上し、資金繰りの健全化にもつながります。
生産計画の精度と柔軟性の向上
生産管理システムには、実際の在庫・受注・進捗状況に基づいて、生産スケジュールを調整できる機能があります。計画と現場のズレを最小限に抑え、急ぎ案件の受注や需要変動に応じた柔軟な生産計画が可能になります。
生産計画の精度が低いと、急な受注や納期変更に柔軟に対応できず、稼働率の低下や在庫の過不足が発生しやすくなります。生産管理システムの計画機能で、現実と乖離しない生産体制が整えられれば、設備や人員の稼働率を安定的に維持できます。その結果として、全体の生産性が底上げされます。
検査管理による品質向上
検査データをリアルタイムで記録・分析し、異常の早期発見や再発防止の仕組みを作ることで、生産の安定性と効率が向上します。生産管理システムでは、このような品質向上も可能です。
品質に関する情報を紙や個別ファイルで管理していると、データの抜け漏れや集計の手間により、不具合の兆候を見逃してしまうことがあります。また、過去のデータに基づいた傾向分析の手間も膨大になりがちです。
生産管理システムでは、検査結果や異常履歴をリアルタイムで記録できるため、品質に関する傾向や問題点を早期に把握できます。データ集計や傾向分析の手間も最小限で済み、品質改善もしやすくなります。
トレーサビリティ強化
生産管理システムは、トレーサビリティの確保に優れており、生産履歴・材料ロット・作業者情報などを一元管理できます。このため、不具合が発生した際も製品の流れをさかのぼり確認し、迅速な原因究明と対応が可能になります。
トレーサビリティの確保には、ロット管理やシリアル管理が必要となります。これらを紙やエクセルのみで行うと、生産情報をさかのぼる手間が非常に大きくなります。データで追いきれない場合は、現場への聞き込みや再現等に発展し、通常の生産に影響が出かねません。
特に食品・医薬・自動車業界など、厳格なトレーサビリティが求められる業界においては、生産管理システムによるトレーサビリティ強化が効果的です。
複数拠点の一元管理による全体最適化
生産管理システムを導入すると、複数の製造拠点や外注先の情報を一元的に管理できます。全体最適の視点で生産・在庫・リードタイムの調整が可能になり、全社的な視点で生産計画や在庫調整が可能になります。
たとえば、A工場で部材が不足している場合に、B工場の余剰在庫を即座に把握し、再手配することが可能になります。結果として、無駄な発注・在庫・停止を防ぎ、生産リソースの最適配分によって、全体としての生産性を最大化できます。
システム導入による生産性の改善事例
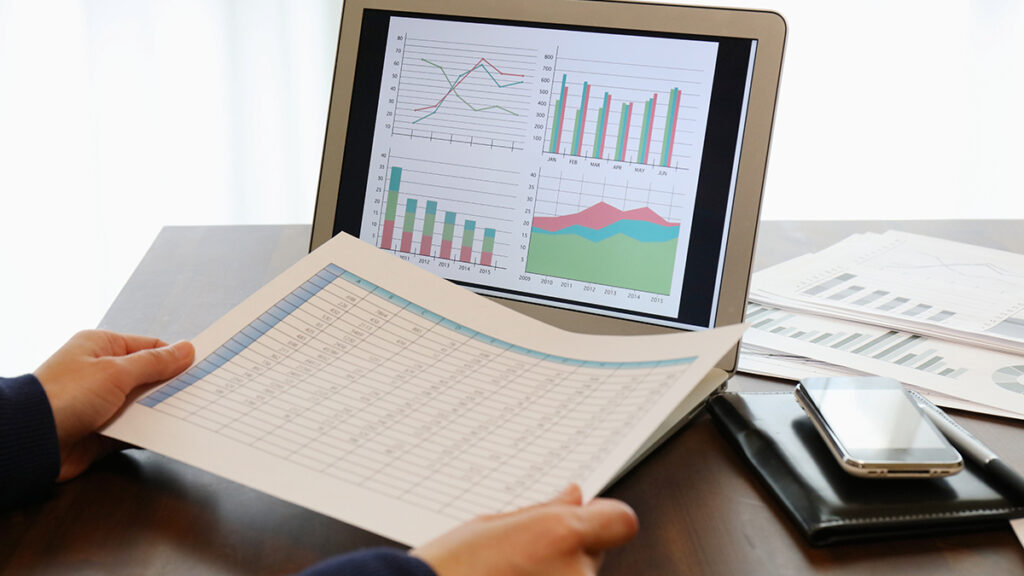
実際に生産管理システムを導入した企業では、目に見える形で生産性向上の効果が現れています。一例として、中小・中堅企業での成功事例を紹介します、
プラスチック成型の中堅製造業では、工程進捗管理を紙から生産管理システムへ切り替え、月間100時間の工数削減に成功しました。これは、1人分の省人化に相当する生産性向上の効果です。また1日30分費やしていた在庫管理業務を0に改善しました。
事例の詳細はこちら:手書き&エクセル入力がゼロに。1人の省人効果+迅速な生産調整で生産性向上
ロボット機器の製造企業では、生産情報・検査情報データの一元管理を実現し、生産拡大時の品質リスクを対策しました。手書き・エクセルで行っていた検査管理をシステム化し、工数削減とトレーサビリティ強化を実現しています。
事例の詳細はこちら:生産情報・検査情報を一元管理!手書き・エクセル作業をシステム化し、生産拡大時の品質リスク対策に成功
このように、システムの活用によって得られる効果は、単なる業務効率化にとどまらず、品質向上・コスト削減・人材活用の最適化にも広がっています。
22種類の生産管理システムをランキングで比較
初期費用相場や選び方のポイントをチェック
生産管理システムをそれぞれの特徴や初期費用相場などで比較したい場合は、「生産管理システムランキング」も是非ご覧ください。生産管理システムは、自社の製品・生産方式・企業規模などに適したものを導入しないと、得られるメリットが限定されてしまいます。事前適合性チェックや生産管理システムを選ぶ前に押さえておきたいポイントも解説していますので、製品選びの参考にしてみてください。