全数検査とは?抜き取り検査との違い、運用上の課題から効率化を実現した事例まで紹介
公開日:2025年04月21日
最終更新日:2025年04月21日
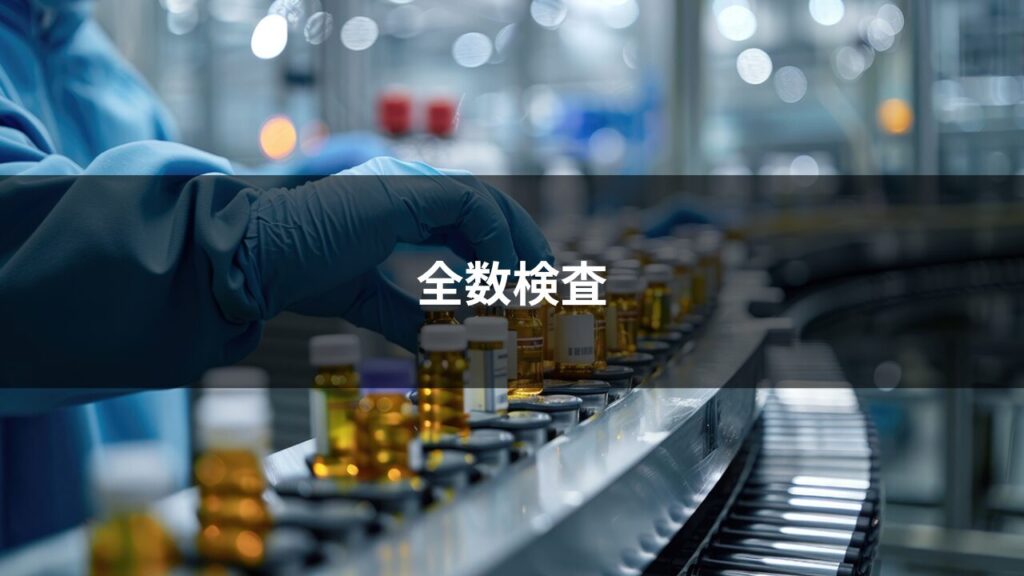
全数検査は、すべての製品を1個ずつ検査することで、高度なトレーサビリティと品質保証を実現する手法です。製品の安全性が重視される製品では不可欠なプロセスとなっています。しかし、工数が増える点や、見逃しリスクが0にならない点は注意が必要です。
本記事では、全数検査の基本から抜き取り検査との違い、導入のメリットと運用上の課題を解説しました。また、全数検査の効率化を支える技術、運用に欠かせないシステムツールの活用事例についても紹介します。
全数検査とは?
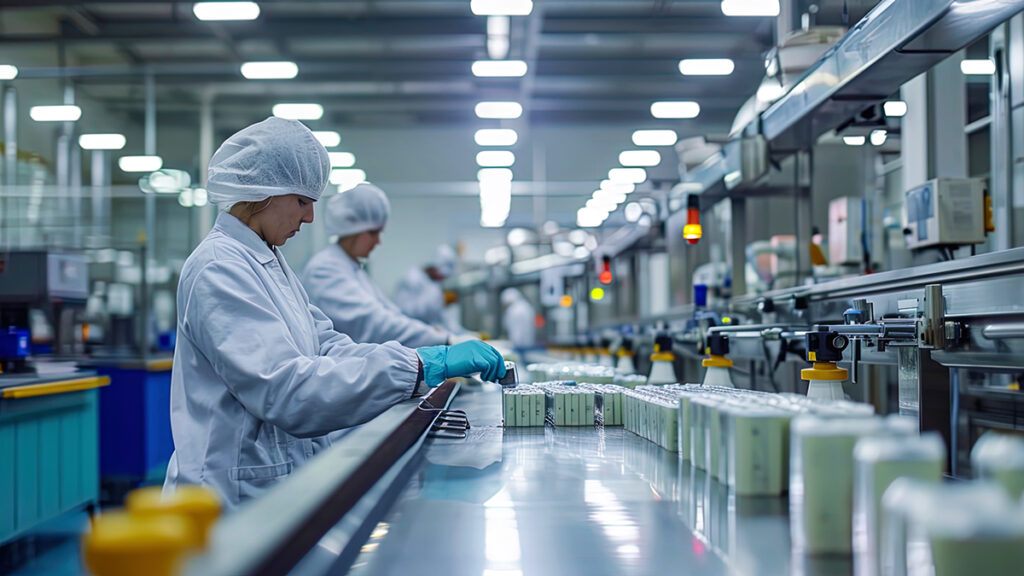
全数検査とは、対象製品を一つひとつもれなく検査する品質保証の手法です。全数検査には、個々の製品における品質を追跡しやすい、という大きなメリットがあります。
一方で、全製品・検査項目すべてに対して、全数検査を実施することは現実的ではありません。製品の置かれている状況を踏まえ、限られた重要項目に絞って行うのが一般的です。
全数検査と抜き取り検査の違い
製造現場における品質検査には、「全数検査」の他に「抜き取り検査」があります。全数検査では、製造されたすべての製品に対して検査を実施し、品質保証を行います。一方、抜き取り検査では、製品の一部をランダムに検査し、その結果からロット全体の品質を推定します。
一例ですが、製造者の立場で全数検査、抜き取り検査のどちらを選択するかは、以下のようなポイントに沿って判断します。
- 非破壊検査かどうか:製品を壊す手法では、全数検査できない
- 検査コストが許容できるか:一般に全数検査は高コストになりやすい
- 工程能力(Cpk)が十分か:Cpk<1.33の場合、全数検査必須と考えるケースが多い
全数検査が必要な場面
製品毎のトレーサビリティが必要な場合には、原則として全数検査が必要です。特に、出荷後に個別の品質データ提出が求められる場合に該当します。具体的に全数検査が必要となるのは、次のような場面です。
- 医薬品、食品、自動車部品など、生命や安全に関わる製品
- 顧客先との契約や仕様で、不良ゼロが求められるケース
- 品質規格適合や輸出管理の観点で、厳格なトレーサビリティが必要となる製品
- ラベルや包装など、目視確認が必要な外観項目
上記以外でも、量産立ち上げ時やクレームを発生させた製品群などは、期間限定で全数検査が求められる場合があります。
全数検査への移行が増えている
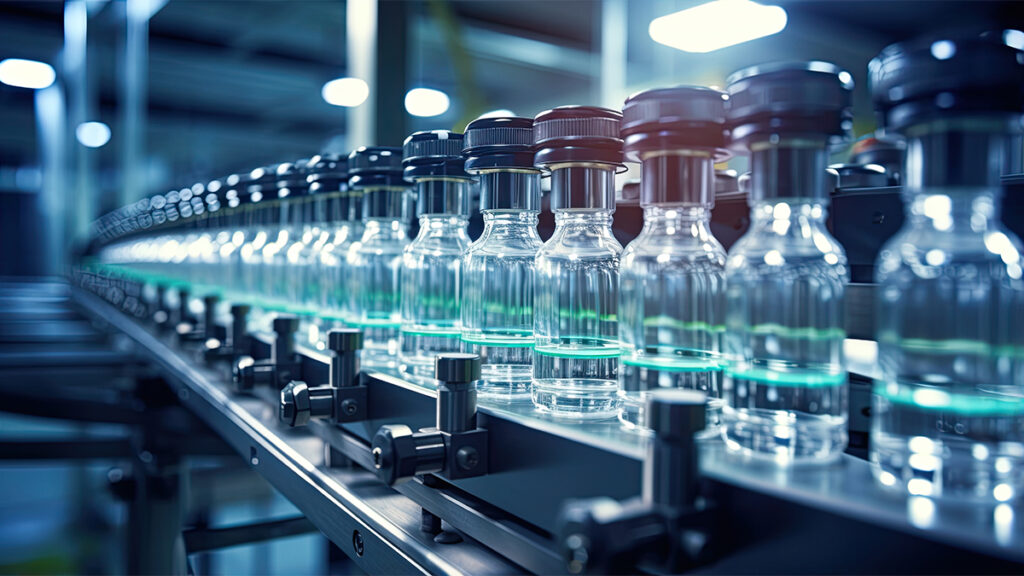
製品の高精度化や情報技術・検査技術の著しい発達を背景に、全数検査のニーズは増加の一途をたどっています。
市場変化に伴う品質要求が高まっている
顧客製品の小型化や高精細化が進む中で、品質不良に対する厳しさは年々増しています。特に、前工程や投入品のわずかな不具合でも、最終製品に重大な影響を及ぼすケースも多くなってきました。
さらに、製造プロセスの複雑化により、品質不良の早期発見がこれまで以上に重視されるようになっています。最大の理由は、品質不良が後工程や顧客に流出した場合、コスト面での損失が大きくなるためです。さらに、不良品がボトルネック工程に投入されると、本来処理できた良品の生産機会が奪われ、機会損失を招くリスクもあります。
このため、製造業のサプライチェーン全体において、品質の確からしさを証明する仕組みが必要です。この仕組みを支える手段として、全数検査が改めて注目されています。
全数検査で品質の証明が求められる
今、製造現場では「品質を証明できる体制」がこれまで以上に求められています。実際に、顧客から次のような要望が寄せられることも少なくありません。
- すべての製品で品質検査を実施したことを証明してほしい
- 個々の製品について、実際の検査測定データを開示してほしい
これまでは、製品の一部を検査してロット全体の品質を推定する、抜き取り検査が一般的な手法でした。しかし近年、要求品質の厳格化に伴い、軽微な不良品であっても、流出した場合の損失が拡大する場面も見受けられます。このため、従来の抜き取り検査では、顧客の納得を得られないケースが増えています。
品質への責任を「見えるかたち」で果たすための手段として、敬遠されがちな全数検査が再評価されています。
全数検査のメリット
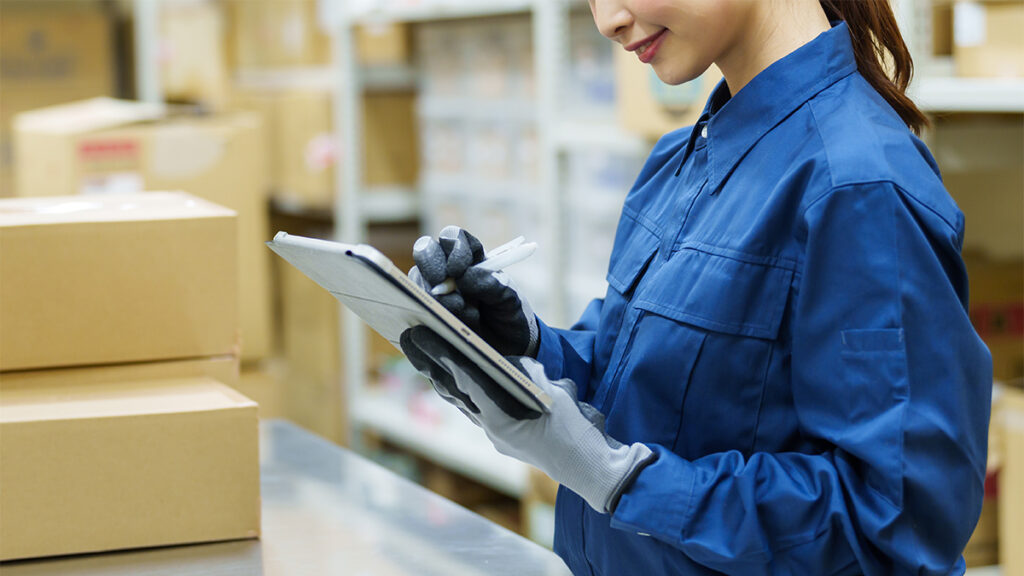
品質管理におけるトレーサビリティ確保、品質保証の観点で、全数検査には大きなメリットがあります。
品質面でのトレーサビリティ強化
全数検査の最大のメリットは、製品一つひとつのトレーサビリティの確実性が高いことです。全ての製品で品質検査を行い、その記録が適切に管理されていれば、後から製品単位で検査結果の追跡が可能です。
出荷後に、顧客から品質データの開示を求められるケースもあります。しかし、全数検査の体制があれば、記録をもとに対象製品・ロット・個体を特定し、データを提供することができます。
実際に、医薬品業界では、GMP(適正製造基準)により、製品単位での検査記録による品質証明が法的に義務づけられています。実質的に全数検査を必要とする運用が求められており、トレーサビリティ強化の手段として広く採用されています。
不良品の流出防止
全数検査は、不良品の流出ゼロを達成しやすい品質保証のための手法です。すべての製品を検査するため、抜き取り検査では見逃されやすい不具合も事前に検出できます。これにより、後工程や顧客に対して、品質不良となった製品の流出リスクを大幅に減らせます。
特に、安全性や機能に直接関わる製品では、不良品の流出は重大な事故や企業の信用失墜につながりかねません。こうしたリスクを防ぐため、全数検査は「最後の砦」として重要な役割を果たします。
自動車業界では品質規格 IATF16949 において、「特殊特性」に指定された項目に対して、全数検査が指定されるケースが多いです。特殊特性は、わずかな不良でも人命に関わる可能性があります。このため、工程の安定性に関わらず、必ず検査を実施し、その記録を証明できる体制構築が求められます。
このように、全数検査は単なる品質管理手法にとどまらず、企業の信頼性や製品安全性を支える不可欠な手段です。特に品質要求が厳しく、不良流出時の影響が大きい業界では、全数検査が強力な切り札となります。
全数検査が抱える運用上の課題
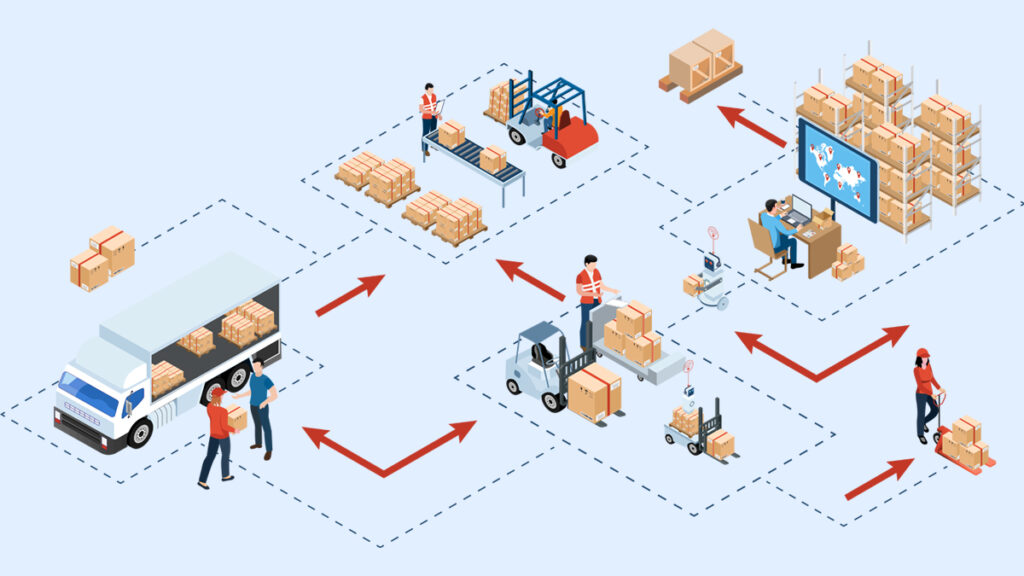
全数検査には多くのメリットがある一方で、運用する際に考慮すべき課題もあります。
品質管理コストの増大
一般に、全数検査の運用において、品質管理コストの増大は避けられません。すべての製品を検査するために、相応のマンパワー・時間・設備などのリソースが必要です。さらに、製品一つひとつに対して品質検査を行うため、検査結果の管理業務やデータ処理も煩雑化しやすくなります。
とくに、目視での外観確認や手作業による品質検査が中心の場合、検査作業者のミスや疲労による精度の低下も懸念されます。昨今では、検出技術の進化により、画像処理による外観検査や、センサーによる寸法の高速自動測定も珍しくありません。しかし、こうした技術の導入はマンパワーや時間の負担を減らせる一方、機械装置が高額になりがちです。
このように、全数検査は品質管理コストの負担が重く、全ての検査項目で行うのはコスト面で困難です。トレーサビリティを強化すべき検査項目、不良品の流出リスクや影響度の大きい項目に絞って導入すべきでしょう。
それでも残存する見逃しリスク
全数検査は有効性の高い品質保証の手段ですが、それでも不良流出を撲滅できるとは限りません。一例ですが、以下のような状況では、全数検査を行っていても品質不良が流出する懸念があります。
- 検査基準やチェック項目が不明確・不適切である
- 人手による検査のため、ヒューマンエラーが発生しやすい
- 日常点検や校正・メンテナンスが不十分で、検査機器の精度が維持できない
膨大なコストと手間をかけて全数検査を行っても、見逃しリスクをゼロにすることは難しいのが現実です。そのため、全数検査の導入時には「どうすれば見逃しを減らせるか」「運用精度をどう高めるか」という視点が欠かせません。
こうした課題を解決する手段として、品質検査の自動化が加速しています。自動化するためには、基準や項目を明確に定める必要があります。また、センサー技術やシステムツールも活用すれば、人的ミスを抑えながら、検査精度の再現性を確保することが可能になります。また、自動化とあわせて、検査機器の定期点検やメンテナンスを実施できる仕組み整備も進めるとよいでしょう。
全数検査を効率化する技術
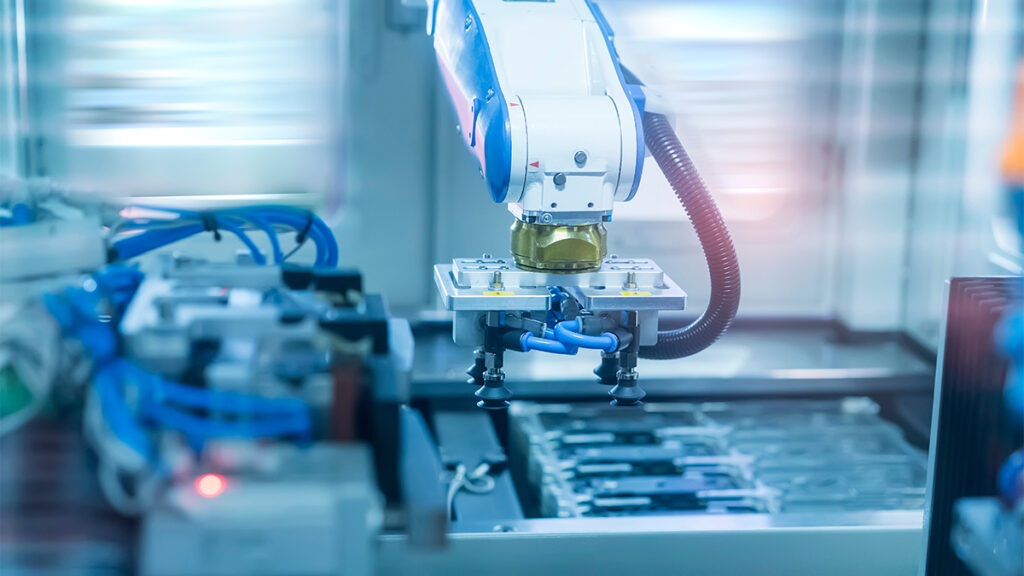
全数検査は手間のかかる方法ですが、最新技術を使えば大幅な効率化が可能です。
インライン検査・自動化:ラインを止めずに検査する
生産ライン上で行う「インライン検査」は、リアルタイムかつスピーディーな全数検査を可能にする手法です。製品をラインから取り出すことなく、検査装置へ自動搬送・自動測定を行います。検査のために、工程を止める必要がありません。
特に、寸法測定・外観確認などの検査では、高精度センサーやカメラを活用した自動検査が主流になりつつあります。これにより、人手に頼らず、精密かつ安定した検査を連続的に行うことができます。
さらに、検査で不良と判定された製品は、自動的にライン上から排出されます。これにより、後工程や出荷段階での不良混入リスクも抑えられ、品質保証の確実性が高まります。
生産ラインによっては、生産速度よりも検査速度の方が遅く、処理が追いつかないケースもあります。しかし、この場合でも、複数の検査装置を並列に配置すれば、ライン全体の生産能力の維持が可能です。
このようにインライン検査は、全数検査における精度を保ちつつ、検査工程の効率化を実現します。
IoT化:検査装置とシステムをつなぐ
全数検査の効率化を加速する手段として、検査機器のIoT化も挙げられます。検査装置をネットワーク経由でシステムツールと接続することで、検査データのリアルタイム共有が実現します。
寸法測定を例に挙げると、非接触型の測長センサで自動的に測定した後、その結果が即座にシステムへ自動送信されます。データ送信直後に異常判定も行われ、不良検出時にアラート発報などにより、迅速な情報共有も可能となります。
さらに、検査日時や機器の識別情報も同時に記録されます。これにより、「いつ・どの製品を・どの装置で検査したか」といった履歴の追跡や、検査装置ごとの傾向分析もしやすくなります。
このように、全数検査のIoT化は、単なる検査工程の効率化にとどまらず、品質情報を高度活用する基盤となります。
全数検査の運用にはシステム活用が効果的
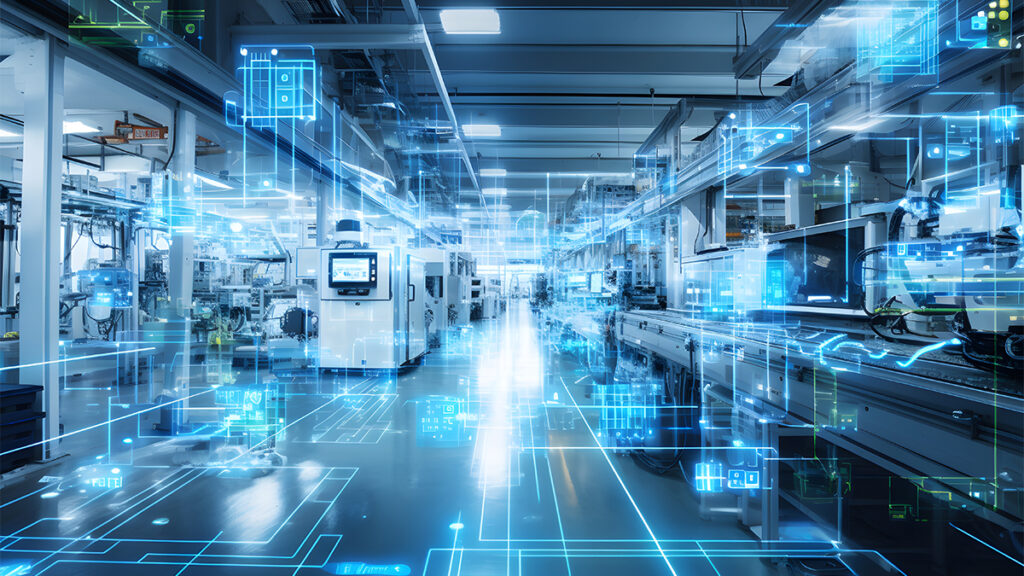
コストのかかる全数検査を十分に活用するためには、システムツールの併用が効果的です。
生産管理システムで品質データを一元管理
検査記録・作業実績・出荷情報などを一元的に管理できるシステムは、全数検査のメリットを最大限引き出す強力なツールです。生産管理システムと連携すれば、検査結果を製品ごとに紐付けて記録・検索・分析が可能となり、トレーサビリティや品質保証の対応力が格段に向上します。
測定機とシステムを連携させ、計量記録を自動化した事例
ある化粧品メーカーでは、計量器で数値を目視確認し、手書きで記録した後、エクセルに転記して計量記録を管理していました。しかし、このようなアナログ管理は手間がかかるだけでなく、記録や転記のミスにも悩まされてきました。
そこで生産管理システムを導入し、計量器と連携させる運用としました。これにより、正確な記録を残せるようになり、管理工数も年間120時間削減されました。
詳しい事例はこちらで紹介しています。
→【生産管理システム】生産情報・検査情報を一元管理!手書き・エクセル作業をシステム化し、生産拡大時の品質リスク対策に成功
ハンディ端末導入により、全数検品を効率化した事例
ある食品企業では、指示書と製品ラベルの記載内容が合っているかを、製品梱包前に1個ずつ目視で検品照合していました。しかし、全数を目視確認していたため、作業負荷も高く、確認ミスによる誤出荷も発生している状況でした。
そこで、ハンディ端末を導入し、製品ラベル記載内容を自動照合する運用としました。これにより、出荷ミスは大幅に減り、作業時間も短縮されました。
詳しい事例はこちらで紹介しています。
→ハンディ端末を用いた照合検品で目視確認の手間を大幅に削減【日付検品システム】賞味期限切れの製品出荷を99%防止
22種類の生産管理システムをランキングで比較
初期費用相場や選び方のポイントをチェック
生産管理システムをそれぞれの特徴や初期費用相場などで比較したい場合は、「生産管理システムランキング」も是非ご覧ください。生産管理システムは、自社の製品・生産方式・企業規模などに適したものを導入しないと、得られるメリットが限定されてしまいます。事前適合性チェックや生産管理システムを選ぶ前に押さえておきたいポイントも解説していますので、製品選びの参考にしてみてください。