標準原価・実際原価・見積原価の違い、計算方法や原価差異の分析方法について解説
公開日:2025年03月26日
最終更新日:2025年03月26日
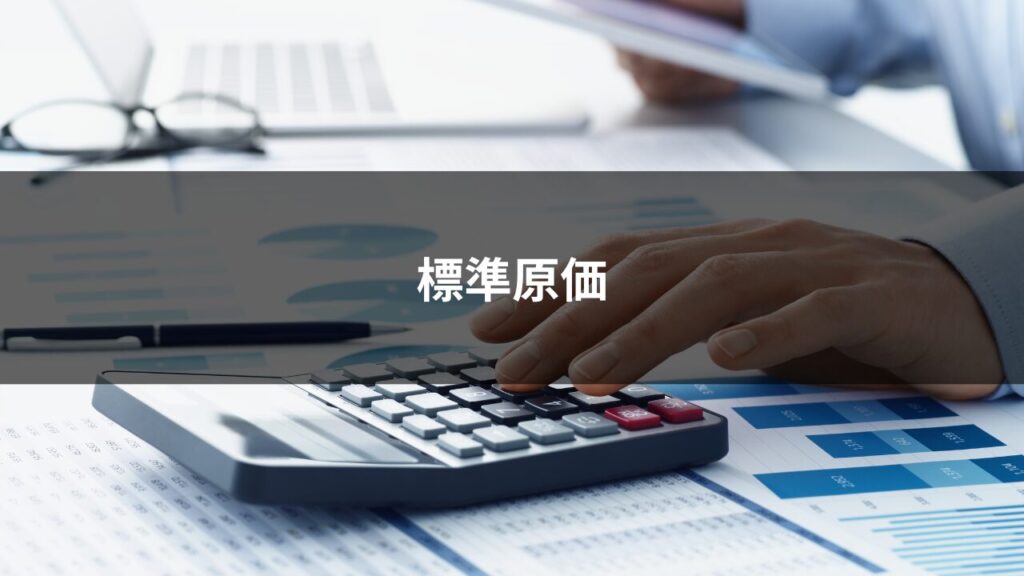
標準原価を知り、標準原価計算で実際原価との差異を把握・分析することは、製造業の利益確保と競争力維持に不可欠です。
本記事では、標準原価の基礎から、実際原価・見積原価との違い、4つの標準原価の分類、標準原価計算の具体的な流れをわかりやすく解説します。
さらに、原価差異の分析方法や、差異を解消するためのツールとして原価管理システムの導入についても紹介します。原価管理の全体像を体系的に理解し、現場改善や経営判断に役立てましょう。
標準原価とは:原価の目標値
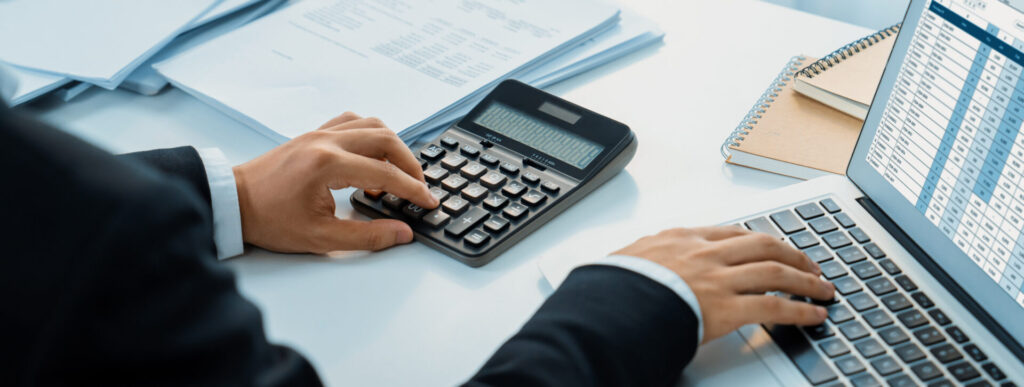
標準原価とは、製造業などの企業が製品やサービスを生産・提供する際に、あらかじめ定めておく「基準となる原価」です。材料費、労務費、経費などを合理的に見積もって設定し、実際の原価との比較することで、コスト管理や業務改善に活用します。
目指すべき原価ともいえる標準原価の計算は、製品の適正価格を設定し、経営判断や予算策定を行うためにも重要です。
標準原価の分類
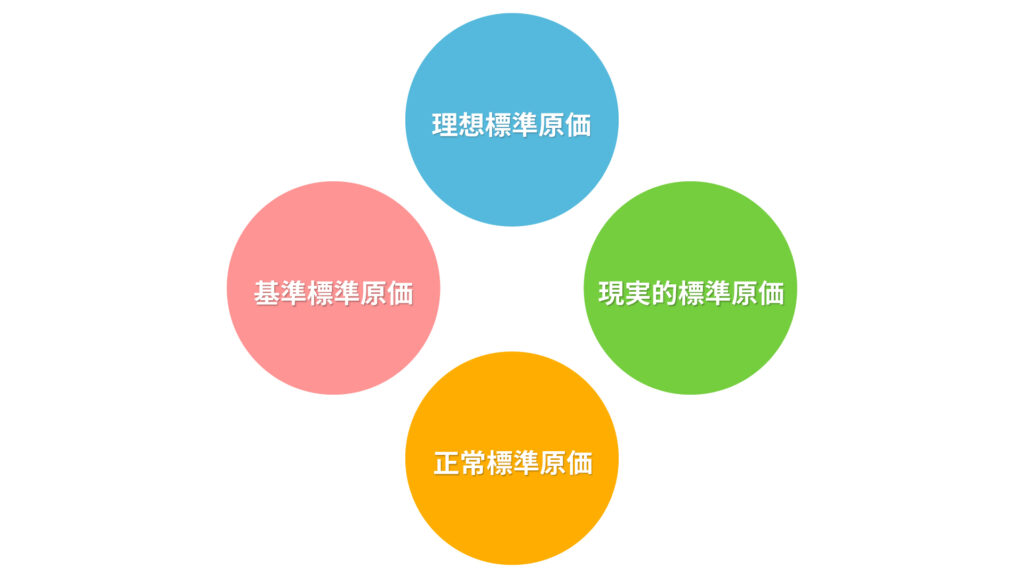
標準原価は、目的や運用の考え方によって複数の分類が存在します。主な分類には、理想標準原価・現実的標準原価・正常標準原価・基準標準原価の4種類があり、それぞれ異なる特徴があります。
理想標準原価
理想標準原価とは、無駄やロスを一切排除した、理論上の最も効率的な生産を前提に設定される原価です。つまり、人や機械が100%の効率で稼働し、材料の歩留まりも完璧であると仮定した場合の数値となります。
理想標準は現実離れしている場合が多く、実際の原価との差異が大きく出ますが、その分、改善点が明確になるというメリットがあります。そのため、工程改善やコスト削減の目標設定のための「ベンチマーク」として使われることが多いです。一方で、現場との乖離が大きすぎると、モチベーション低下を招く恐れがあるため、運用には注意が必要です。
現実的標準原価
現実的標準原価は、実際の作業環境や平均的な生産効率を前提として設定される、より現実に即した標準原価です。例えば、一定の材料ロスや機械の停止時間、人の作業ミスなどをある程度織り込んで設定されるため、現場での運用がしやすく、差異分析においても適切な判断材料となります。
現実的標準原価は、実際原価と比較して無理のない基準となり、日常的な原価管理や部門評価において高く評価されています。特に、多くの製造業ではこの現実的標準原価が採用されています。
正常標準原価
正常標準原価は、過去の実績データや長期的な平均値を基に、通常発生し得るロスや変動を考慮して設定される原価です。突発的な異常や非定常な要因を除外しつつ、ある程度の変動を含めた「平均的な正常状態」を反映しているのが特徴です。
例えば、年間を通しての設備稼働率や材料価格の変動幅、作業効率のばらつきなどを織り込み、異常値を排除した上で設定されるため、比較的安定した基準として運用できます。正常標準原価は、長期的な原価傾向の把握や、経営分析・計画立案における信頼性の高い基礎データとなりやすく、企業の中長期戦略にも有効です。
基準標準原価
基準標準原価は、過去の標準原価をそのまま継続して使用するもので、比較的頻繁な見直しを行わない「固定的な基準」として運用されます。長期的なトレンドや他の原価要素との整合性を保つために使われることが多く、財務会計や経営計画との連携がしやすいというメリットがあります。
ただし、市場環境や原材料価格の変動が激しい場合には、現実との乖離が広がるリスクがあるため、定期的な見直しや補正が必要となります。基準標準原価は、経年変化を追跡するための基準軸としての役割も果たし、過去との比較分析や業績評価の際に利用します。
標準原価・実際原価・見積原価の違い
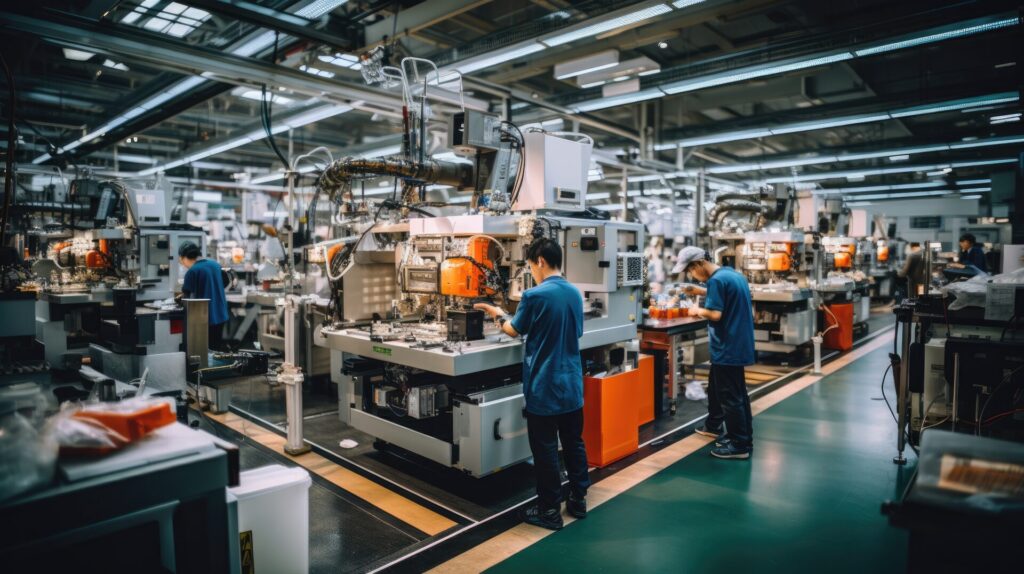
標準原価と実際原価の最大の違いは、「事前に設定された基準原価」と「実際に発生した原価」という点にあります。
実際原価とは、製造にかかった実際のコストを集計する方法です。原価変動が大きい製品を生産している場合は、標準原価を設定しても早々に陳腐化するため、実際原価のみ管理するケースがあります。
実際原価には、以下2通りの計算方法があります。
区分 | 個別原価計算 (Job Order Costing) | 総合原価計算(Process Costing) |
概要 | 1つ1つの案件・注文ごとに原価を集計 | 大量生産品の製造工程ごとに平均的な 原価を算出 |
向いている業種 | 個別受注生産(特注品製造など) | 連続生産(食品、化学、鉄鋼、石油、電子部品など) |
計算方法 | 案件ごとに直接費・間接費を集計 | 一定期間の総コストを生産数量で割る |
特徴 | 案件ごとにかかった原価が明確になる | 製品1個あたりの「平均コスト」が分かる |
原価管理の 難易度 | 高い(案件ごとに精緻な管理が必要) | 低い(全体の平均値で管理) |
それぞれの違いをまとめると以下の表のようになります。
標準原価 | 実際原価 | 見積原価 | |
定義 | あらかじめ設定された目標コスト | 実際に発生した費用に基づく原価 | 将来の取引などを 想定して見積もった原価 |
計算タイミング | 生産前に設定 | 生産・取引後に確定 | 見積時点で概算として設定 |
精度 | 過去データや経験に 基づき高精度に 設定可能 | 最も正確(現実の数値) | 概算であり、精度は 標準原価より低いことが多い |
用途 | 原価管理、差異分析、計画立案 | 実績把握、原価報告、決算 | 提案書・見積書作成、受注判断 |
標準原価・実際原価・見積原価の計算方法
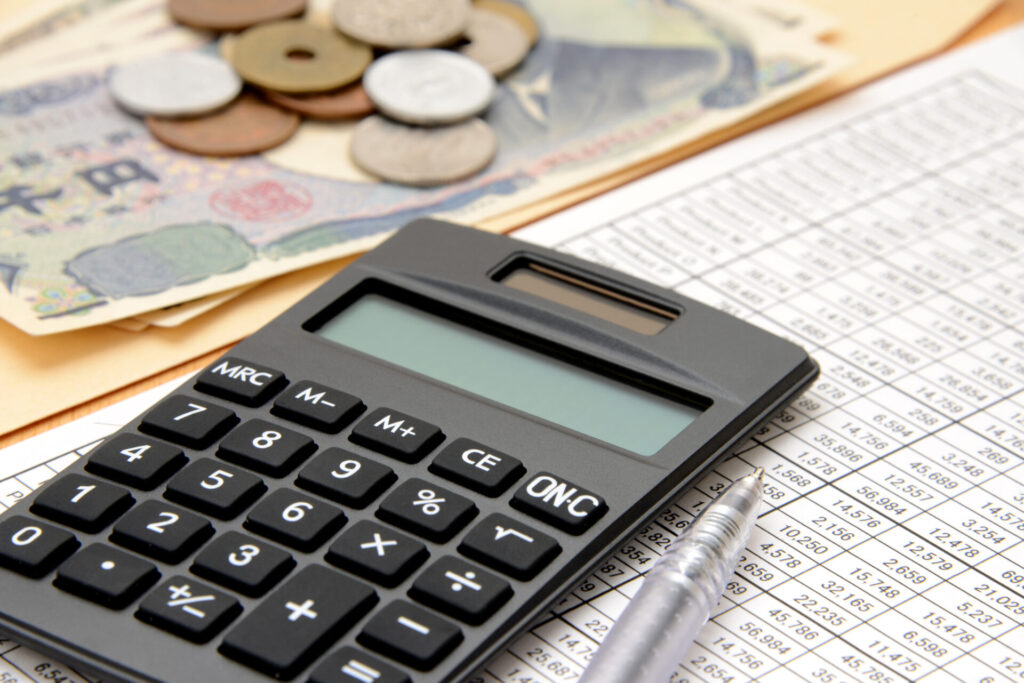
次に具体的な原価の計算方法について解説します。
標準原価の計算方法
標準原価の計算方法は「標準消費量 × 標準単価」に基づいて、各コスト要素を積算する形で行われます。標準消費量とは、製品1単位を生産するために理論上、または現実的に必要とされる材料や作業時間のことです。
標準単価は、過去の実績や将来的な見通しに基づいて設定される、材料の単価や人件費、間接費の配賦率などです。
例えば、製品Aを1個作るのに材料Xが2kg、標準単価が500円/kgであれば、材料費の標準原価は「2kg × 500円 = 1,000円」となります。同様に、作業時間2時間×1時間あたりの標準人件費1,200円であれば、労務費は2,400円となります。
これらを合計して、製品1個あたりの総標準原価を算出します。標準原価の設定と計算は、原価差異分析の基準値となるため、精度と合理性が重要です。
実際原価の計算方法
実際原価は、製品の製造において実際に発生した費用をもとに計算されます。材料の使用量と購入価格、作業時間と実際の人件費、さらには発生した製造間接費までをすべて集計し、「実績データ」に基づいて算出します。
計算は「実際消費量 × 実際単価」の形で行い、個別原価計算・総合原価計算などの手法を用いる場合もあります。
例えば、材料Bを2.5kg使用し、実際の購入単価が520円/kgであった場合、材料費は1,300円となります。労務費についても、作業に3時間かかり、1時間あたりの人件費が1,300円であれば、労務費は3,900円です。
これらを合計し、さらに間接費を加算することで、製品1個あたりの実際原価が求められます。実際原価は実績に基づくため、詳細で正確な反面、集計に時間と手間がかかる点に注意が必要です。
見積原価の計算方法
見積原価は、主に受注活動や価格提案のために、将来のコストを予測して計算されます。そのため、標準原価や実際原価よりも柔軟性が高く、短期間で算出されることが多いのが特徴です。
計算方法は、過去の原価データ、社内の技術者の経験値、サプライヤーからの見積価格などを参考にして、材料費、労務費、外注費、経費などを概算で積算します。
具体的には、設計図や仕様書から必要な材料や工程を洗い出し、それぞれに概算単価と数量を掛け合わせて算出します。例えば、材料Aが3kg必要で1kgあたりの見積単価が450円、加工費として5,000円が見込まれる場合、見積原価は「3kg × 450円 + 5,000円 = 6,350円」となります。迅速な対応が求められる営業現場では、多少の誤差を許容しつつ、スピーディに算出することが重視されます。
標準原価計算とは:標準原価・実際原価の差異分析
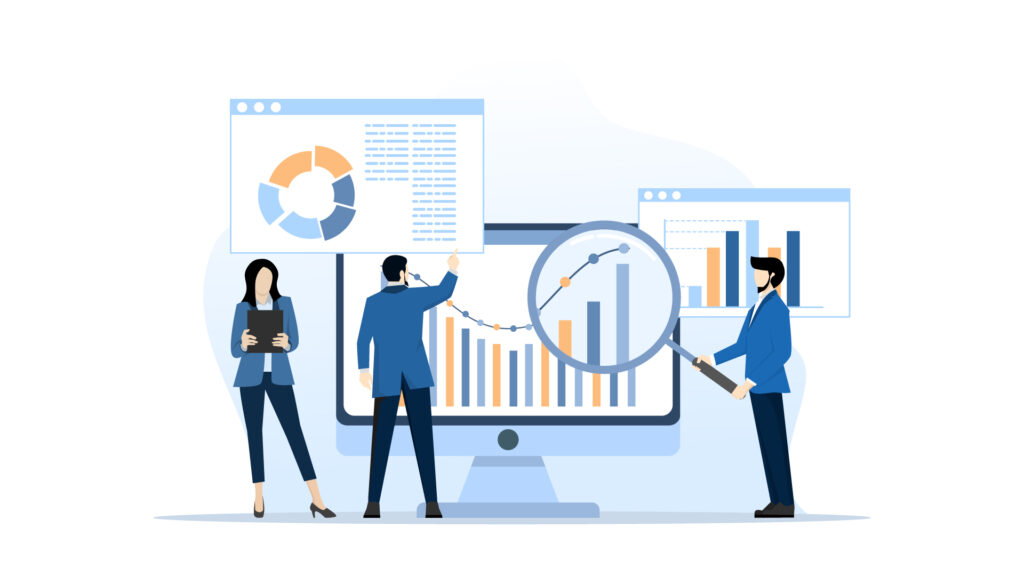
標準原価計算とは、「標準原価」と「実際原価」との差異を分析し、コスト管理や改善に活かす原価計算手法です。標準原価計算を通して、材料の無駄や作業効率などのボトルネックが明確にでき、継続的な改善がしやすくなります。
標準原価計算のメリット
標準原価計算には、主に以下5点のメリットがあります。
- 事前にコスト目標を設定でき、計画的な生産活動が可能になる
- 差異分析により問題点を明確化し、改善活動を促進できる
- 定型的な原価計算により迅速に原価管理ができる
- 管理コストの削減につながる
- 原価基準の統一により社内の意思疎通や評価基準が明確になる
標準原価は、特に見込み生産を行う製造業において、その効果を大きく発揮します。見込み生産では、需要予測に基づき事前に大量生産するため、標準原価を用いることで原価の見通しを立てやすくなります。これにより、販売価格の設定や利益計画の精度を向上できます。
標準原価計算のデメリット
一方で、標準原価計算にはいくつかのデメリットも存在します。
- 標準値の設定に時間と労力がかかる
- 標準値を更新しないと実態との乖離が生じる
- 原材料価格や生産条件の変動に対応しにくい
- 個別受注や多品種少量生産では標準原価の設定が困難
標準原価の導入にあたっては、企業の業態や生産体制に合わせた慎重な検討が必要です。個別受注では顧客ごとの仕様に応じた設計・製造が行われ、多品種少量では製品のバリエーションが多くなります。そのため、材料の使用量や作業内容が製品ごとに大きく異なり、一律の標準値を設定するのは難しいでしょう。
特に多品種少量では、設備の切替や工程順の調整など、変動要因が多く、標準化しづらいです。標準原価よりも、個別原価計算で管理する方が現実的です。
標準原価計算の流れ
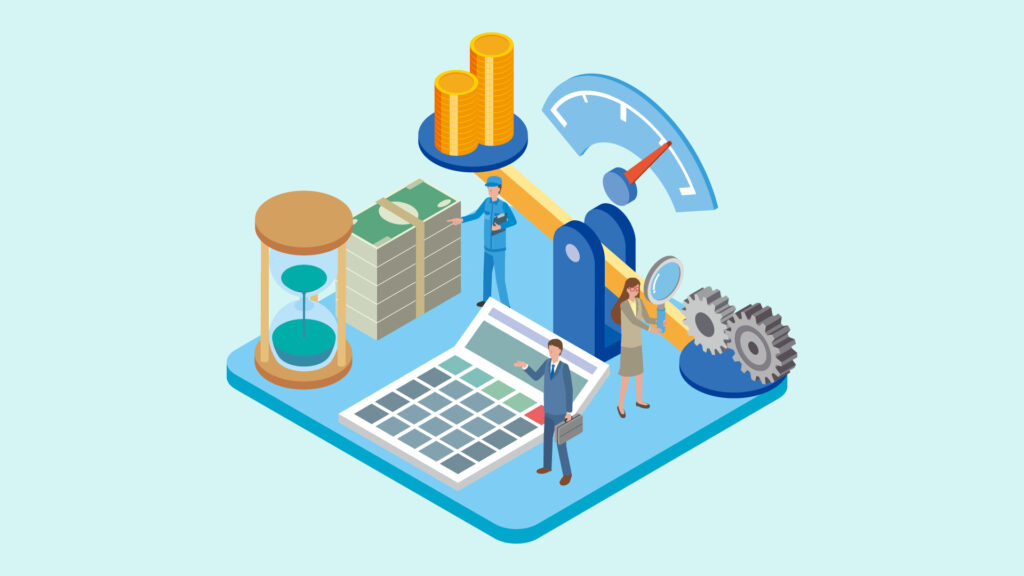
標準原価計算は、製品や業務のコスト管理を体系的に行うためのプロセスです。その流れは大きく6つのステップに分かれています。
- 標準原価の設定
- 標準原価の計算
- 実際原価の計算
- 原価差異の計算
- 原価差異の分析
- 原価差異の処理
それぞれについて解説します。
標準原価の設定
標準原価計算の第一ステップは「標準原価の設定」です。ここでは、材料費・労務費・製造間接費といった各コスト要素ごとに、どの程度のコストが発生するかをあらかじめ決定します。
設定の根拠には、過去の実績データ、工程ごとの作業時間、材料の歩留まり率、設備稼働効率などを使用します。
目標とする生産効率や品質水準を反映させながら、理想または現実的な数値として設定するのが一般的です。企業の方針により、理想標準や現実的標準など、どのタイプの標準を採用するかも決めます。適切な標準原価を設定することが、後の差異分析の信頼性を大きく左右します。
標準原価の計算
標準原価を設定したら、それに基づいて製品1単位あたりの標準原価を計算します。計算式は、「標準消費量 × 標準単価」の形で、材料費、労務費、間接費をそれぞれ算出し、合計して1製品あたりの総標準原価を求めます。
例えば、ある製品に対して「材料Aが5kg × 単価300円」「作業時間が2時間 × 時間当たり賃金1,200円」などの計算を行い、それぞれの標準コストを積算していきます。このプロセスでは、各部門間で数値の整合性を取りながら、業務全体のコスト構造を明確にしていくことが重要です。計算結果は、予算や目標値として原価管理の基礎データとなります。
実際原価の計算
次に、実際の生産活動に基づく「実際原価」を計算します。これは、実際に使った材料の数量と価格、実際にかかった作業時間や人件費、発生した製造間接費などを集計して求めます。
実際原価の計算には、購買記録、作業日報、使用電力や設備の稼働記録など、多くの実務データが必要です。標準原価と違い、変動要因をそのまま反映しているため、タイムリーな集計と正確なデータ収集が不可欠です。実際原価は、製品単位・ロット単位・月次など、目的に応じた粒度で集計して、原価差異分析の材料として活用します。
原価差異の計算
標準原価と実際原価が出揃った段階で、両者の差である「原価差異」を計算します。原価差異は「実際原価 − 標準原価」で求められ、その差額がプラスであればコスト超過、マイナスであればコスト削減を意味します。
原価差異は、材料費差異・労務費差異・製造間接費差異など、コスト要素ごとに細かく分類します。また、価格差異(単価の違い)と数量差異(使用量の違い)に分解することで、どの要因がコスト変動に影響を与えたかを明確にします。この段階での正確な差異計算が、後の原因分析と改善策の立案につながります。
原価差異の分析
差異の計算結果をもとに、次は「原価差異の分析」を行います。分析の目的は、差異の原因を明確化し、今後の改善や管理に活かすことです。例えば、材料費の価格差異が大きい場合は購買価格の変動が疑われ、数量差異が大きい場合は歩留まりの悪化やロスの発生が考えられます。
労務費差異であれば、作業効率の低下や人員配置に問題がある可能性があります。差異分析を通じて現場の課題を特定し、改善アクションへと結びつけていくのが重要です。
原価差異の処理
最後に行うのが「原価差異の処理」です。これは、計算された差異をどのように帳簿上処理し、管理会計に反映させるかという作業です。一般的には、差異は「差異勘定」などに振り分け、月次や四半期ごとにまとめて損益へ反映します。
ただし、差異の大きさや性質によっては、即座に経営判断の材料として使われたり、特別損失や改善投資の検討材料とされる場合もあります。また、将来的には標準原価の見直しや予算修正にも影響を与えるため、差異処理は単なる数字の整理にとどまらず、経営活動の意思決定に直結する重要な工程です。
原価差異の分析方法
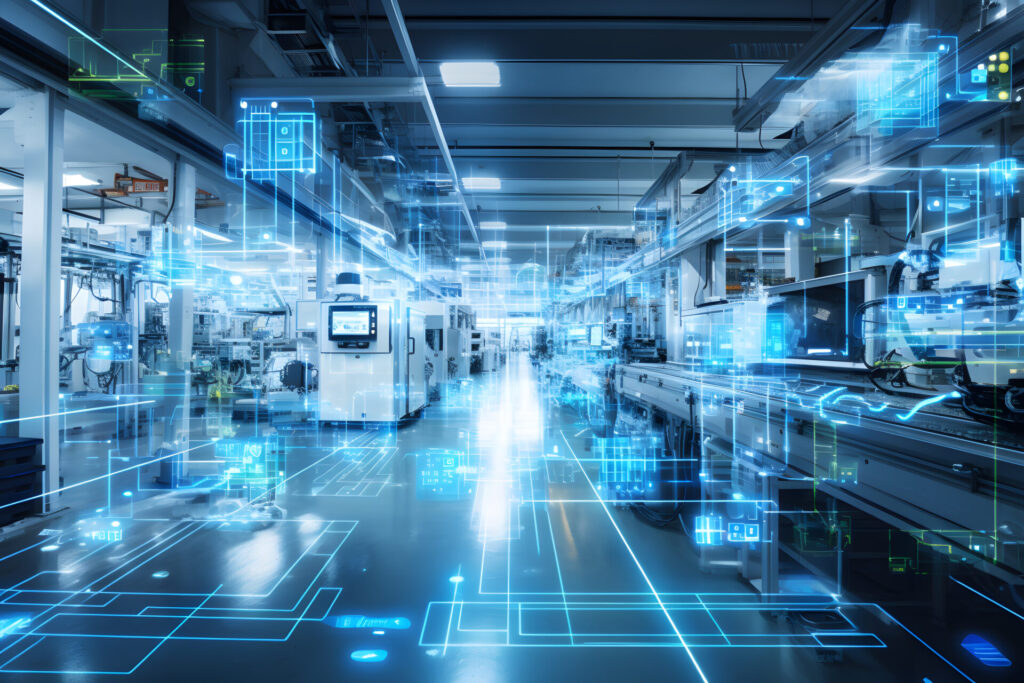
原価差異が大きい場合、その要因を分析・特定し、コスト管理や改善活動に活用することが重要です。
原価差異は主に「価格差異」「数量差異」「賃率差異」「時間差異」に分類されます。それぞれが何に起因するのかを明確にすることで、適切な対策を講じることができます。
以下では、それぞれの差異の定義と分析方法について詳しく解説します。
価格差異
価格差異とは、主に材料費において「標準単価」と「実際単価」の差によって発生する差異です。仕入価格の上昇、サプライヤーの変更、緊急購買による割高な仕入れなどが原因で生じます。計算式は以下の通りです。
価格差異の計算式
価格差異 = (標準単価 − 実際単価)× 実際消費量
例えば、標準単価が500円/kg、実際単価が550円/kgで、実際に10kg使用した場合、価格差異は「(500円 − 550円)× 10kg = −500円」となり、500円のコスト超過となります。
価格差異を改善するには、調達部門の交渉力や購買計画の精度を上げる必要があるといえます。
数量差異
数量差異は、材料の「使用量」に着目した差異です。歩留まりの悪化、材料のムダ、作業ミスといった現場起因の問題で生じやすい差異といえます。標準消費量と実際消費量の差に基づき、以下の通り計算します。
数量差異の計算式
数量差異 = (標準消費量 − 実際消費量)× 標準単価
仮に標準では8kg使用する想定だった材料を、実際には10kg使用した場合、標準単価が500円/kgであれば、数量差異は「(8kg − 10kg)× 500円 = −1,000円」となり、過剰使用によるコスト超過を示します。
数量差異の改善には、製造部門と連携して改善策を検討する必要があります。継続的な改善活動(カイゼン)により差異の縮小を目指します。
賃率差異
賃率差異とは、作業者の労務費において「標準賃率」と「実際賃率」の違い、簡単に言うと労務費の単価(時間あたりの賃金)の違いで生じる際です。高いスキルを持った作業員の投入、残業手当の発生、人員構成の変更などに起因することが多いです。計算式は以下の通りです。
賃率差異の計算式
賃率差異 = (標準賃率 − 実際賃率)× 実際作業時間
例えば、標準では1,200円/時間で設定されていたが、実際は1,300円/時間だった場合、実働時間が50時間なら賃率差異は「(1,200円 − 1,300円)× 50時間 = −5,000円」となります。
賃料差異が大きい場合は、人件費の管理や適切な人員配置の見直しが有効です。
時間差異
時間差異は、作業にかかった時間の「効率」に焦点を当てた差異で、標準作業時間と実際作業時間の差によって生じます。作業効率の低下、設備トラブル、作業指示の不備などが原因として考えられます。計算式は以下の通りです。
時間差異の計算式
時間差異 = (標準作業時間 − 実際作業時間)× 標準賃率
例えば、標準作業時間が40時間のところ、実際には50時間かかった場合、標準賃率が1,200円/時間であれば、時間差異は「(40時間 − 50時間)× 1,200円 = −12,000円」となります。
時間差異の抑制を図るには、現場の工程改善や教育訓練の強化が必要です。
予実管理における原価差異を解消する方法
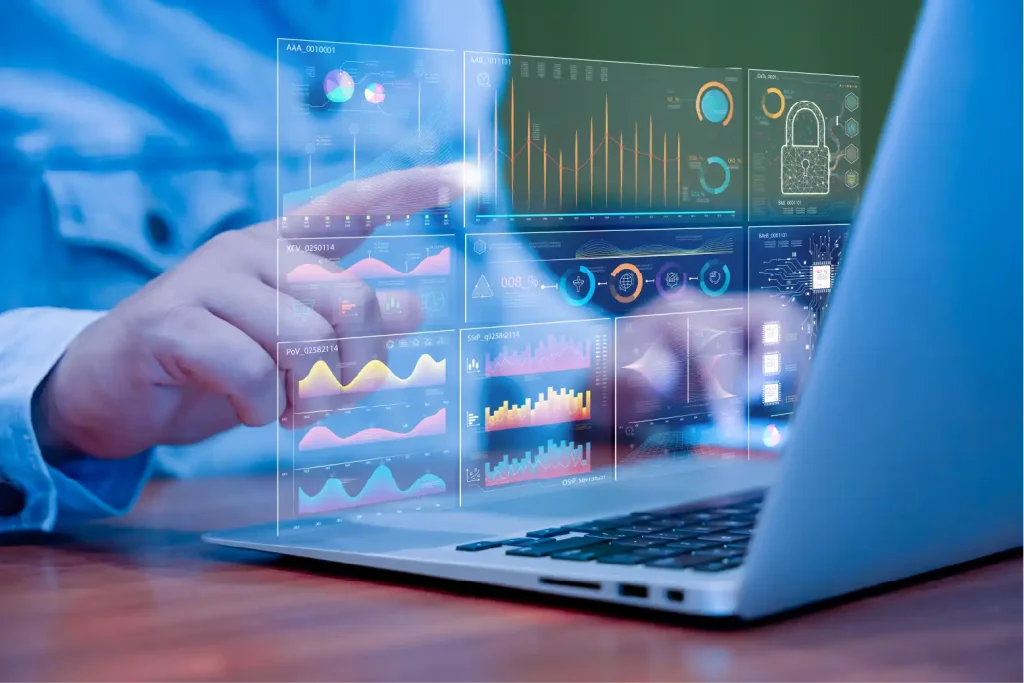
製造業における予実管理(予算と実績の比較管理)は、経営の安定と収益性向上を図るうえで欠かせない業務です。特に原価に関しては、事前に立てた標準原価と実際原価の差異(原価差異)を適切に管理・是正することが、企業の競争力を左右します。
原価差異が大きくなれば利益計画にも狂いが生じるため、早期にその原因を把握し、解消に向けた対策を講じる必要があります。そのための有効な手段として注目されているのが「原価管理システムの導入」です。
原価管理システムの導入
原価差異を継続的に把握し、迅速に対応するためには、人手による帳票集計やエクセル管理だけでは限界があります。そこで有効なのが、「原価管理システム」の導入です。原価管理システムは、材料費・労務費・間接費などの各種原価データをリアルタイムで収集・集計し、標準原価との比較を自動で行う機能を備えています。
原価管理システムを導入することで次のようなことが実現できます。
- 原価差異の「見える化」により問題の早期発見が可能になる
- 材料費などの差異が基準を超えた際、自動アラートを発信する
- 価格差異・数量差異・賃率差異・時間差異などをレポート化できる
- 関係部門との情報共有が円滑になる
- 過去データやトレンド分析による高度な原価分析ができる
- 部門別・製品別のコストを比較分析できる
- ERPや生産管理システムと連携し、原価情報を全社的に一元管理できる
一方で、原価管理システムの導入にはコストと運用体制の整備が必要なため、自社の規模や業務フローに適したツールの選定と、段階的な導入・教育が必要です。
原価管理をシステム化すべきかお悩みなら
原価管理をすべきとはわかりつつ、システム導入まですべきか悩まれている企業は多くいらっしゃいます。
そんな担当者向けに、「原価管理システムは必要?現状見える化ガイド」を無料配布しております。
自社の原価管理の成熟度を診断できるセルフ診断シートも付属していますので、自社の現状分析にもお役立ていただけます。