定量発注方式のメリット・デメリット、定期発注方式との使い分け方をわかりやすく解説
公開日:2024年07月26日
最終更新日:2024年09月06日
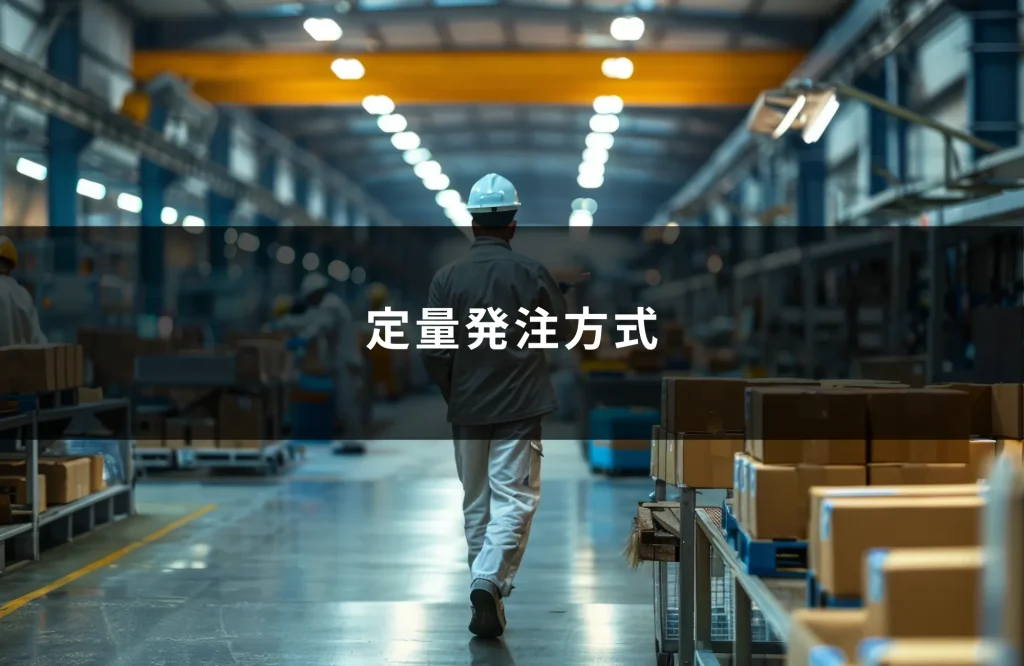
在庫管理における定量発注方式は、発注点を下回ったら一定の発注量で都度発注する手法です。この記事では、定量発注方式の基本概念からそのメリットとデメリット、定期発注方式との違いについて詳しく解説します。さらに、発注点や安全在庫、経済的発注量の算出方法、効率的な運用方法や在庫管理システムの導入成功事例も紹介します。定量発注方式を理解し、実践するためのポイントを押さえ、在庫管理を最適化しましょう。
定量発注方式とは何か
定量発注方式は、予め発注量を一定に決め、在庫数が発注点を切ったら発注する方式です。発注量を都度計算する必要がなく、発注プロセスが簡素化されるメリットがありますが、需要変動に対応しづらいデメリットもあります。
定量発注方式のメリット
定量発注方式では、毎回同じ発注量で注文するため、発注プロセスが簡素化されるというメリットがあります。また、「在庫が100個を切ったら発注する」というようなシンプルな発注方法なので、発注業務の手間も軽減できます。さらに、在庫切れのリスクが低減し、必要なタイミングで適切な量の在庫を確保することが可能となります。
定量発注方式のデメリット
一方で、定量発注方式にはいくつかのデメリットも存在します。まず、需要の変動に対応しづらい点が挙げられます。需要が急増した場合、在庫が不足するリスクがあります。逆に、発注後に需要が減ると、在庫が余剰になるリスクもあります。さらに、発注量が固定されているため、サプライヤーの供給状況や市場の変動に対して柔軟に対応できない場合もあります。
定期定量発注と不定期定量発注
定量発注方式には、定期的に発注を行う「定期定量発注」と、在庫が一定量以下になった時点で発注を行う「不定期定量発注」があります。定期定量発注では、発注のタイミングが予め決められているため、計画的な在庫管理が可能です。
一方、不定期定量発注では、在庫量の変動に合わせて柔軟に発注が行われるため、過剰在庫や在庫切れのリスクを軽減することができます。それぞれの方式には一長一短があり、企業の状況に応じて適切に選択することが重要です。
定量発注方式の算出方法
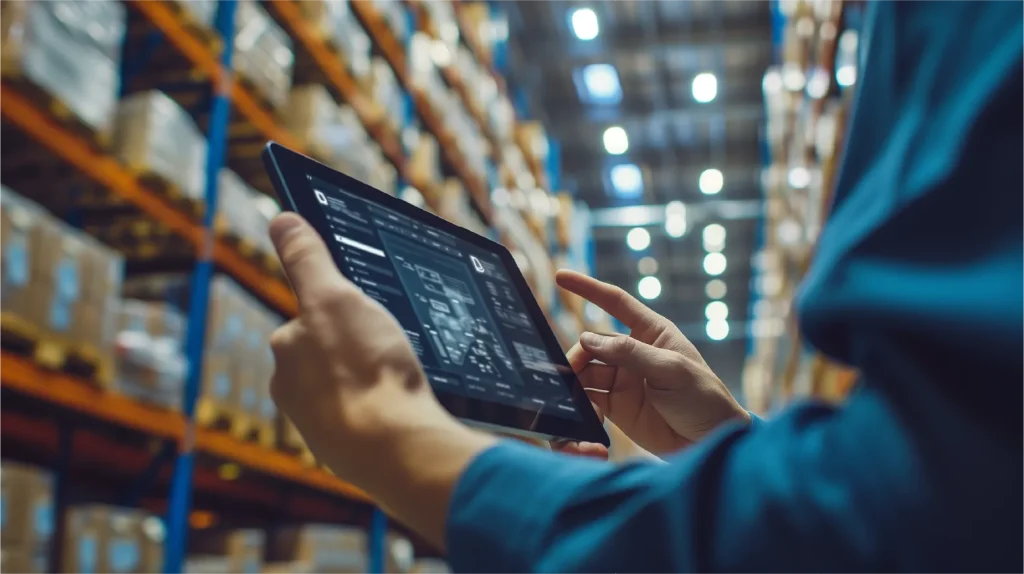
定量発注方式を効果的に行うには、以下3つの要素の算出が重要です。
- 発注点
- 安全在庫
- 経済的発注量
これらの要素は、需要の変動やリードタイムを考慮しながら、最適な発注量とタイミングを決定するために重要です。
発注点
発注点とは、在庫が一定の水準まで減少したときに、新たに発注を行うべき発注数量です。発注点を適切に設定することで、在庫切れや過剰在庫を防ぎます。
発注点の計算は、以下の方法が一般的です。
発注点 = 平均リードタイム(日数)× 日々の平均需要(数量)+ 安全在庫
例えば、リードタイムが10日で平均需要が1日50個の場合、発注点は500個に安全在庫を加えたものとなります。
安全在庫
安全在庫は、需要の変動やリードタイムの不確実性に備えるために最低限確保しておく余裕在庫です。これにより、予期せぬ需要の増加や供給の遅延にも対応でき、在庫切れのリスクを低減します。
安全在庫の量は、需要の変動の大きさやリードタイムのばらつきに基づいて計算されます。一般的には、需要の標準偏差とリードタイムの標準偏差を用いて、安全在庫の適切な量を算出します。
安全在庫量 = 安全係数 × 平均使用量の標準偏差 × √(リードタイム+発注 or 製造間隔)
経済的発注量
経済的発注量(EOQ: Economic Order Quantity)は、発注コストと在庫保持コストを最小化する最適な発注量を指します。EOQを算出することで、在庫コストを抑えつつ、必要な在庫を効率的に補充できます。
EOQの計算には、年間需要量、発注コスト、在庫保持コストが必要です。これらの要素を考慮し、EOQの公式を用いて最適な発注量を導き出します。
EOQ = √((2 x 1回あたりの発注コスト x 需要量) / 在庫保持コスト)
定量発注方式と定期発注方式の違い
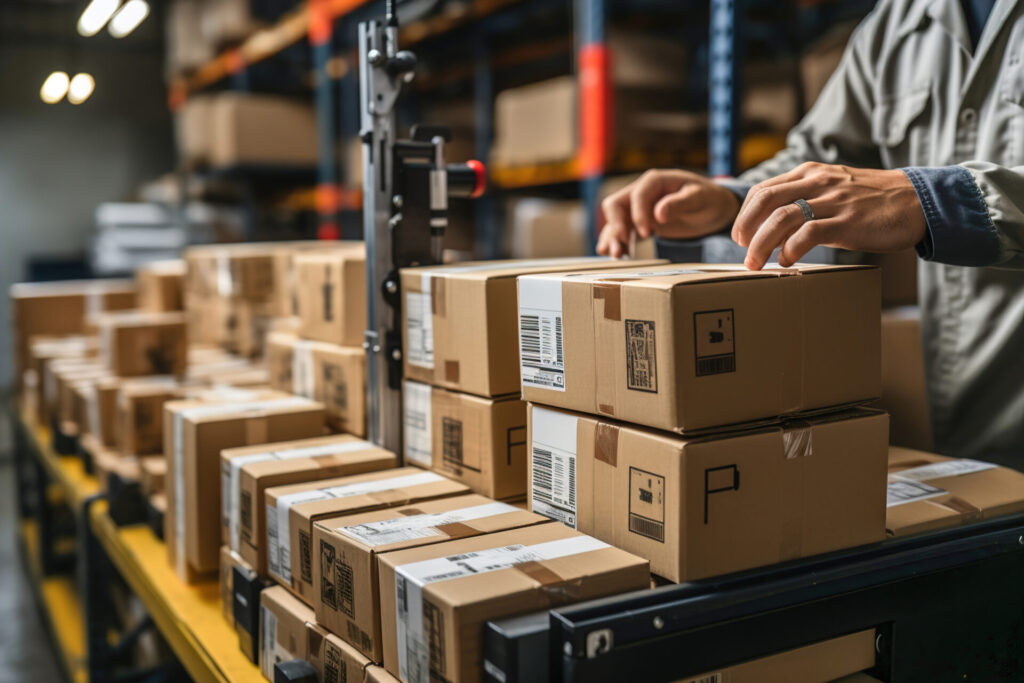
定量発注方式は「発注数量」を決めて発注する一方、定期発注方式は「発注間隔」を決めて発注するという違いがあります。各方式の特徴やメリット、デメリットが異なるため、発注品の種類に応じた適用が求められます。
どちらの発注方式が適しているか
定量発注方式と定期発注方式のどちらを採用するか決める際は、以下の違いを把握したうえで比較検討します。
定量発注方式 | 定期発注方式 | |
発注量 | 一定 | 発注の度に算出 |
発注タイミング | 不定期(発注点を下回ったとき) | 定期的 |
メリット | 管理がシンプル、発注工数が少ない | 需要変動に対応できる |
デメリット | 需要変動の対応が難しい | 発注量の計算が毎回必要 |
向いている発注品 | ・需要が安定した品物・単価が低い品物 | ・需要が変動しやすい品物・単価が高い品物 |
定量発注方式は在庫切れを防ぐために一定量を確保することができるため、需要が安定している製品に向いています。また、少ない手間で一定の在庫数を保てるので、発注工数を抑えたい場合や、低単価で重要度が低い製品にも向く発注方式といえます。
一方、定期発注方式は、発注時期のたびに需要や生産計画を加味して発注量を変えられるため、需要変動が大きい製品に向いています。ただし、発注のたびに発注数量の計算が必要となるので、工数をしっかり割いて管理すべき重要な製品(高単価製品、発注リードタイムが長く欠品リスクが高い製品など)に活用することをおすすめします。
発注方式の使い分けに「ABC分析」が役立つ
「ABC分析」は、在庫品目を重要度に応じてランク付けする手法で、発注方式の使い分けにも大いに役立ちます。Aランクの製品は売上貢献度が高く、欠品させないよう注意すべき重要品なので、定期発注方式が適しています。Cランクの商品は売上貢献度が低く、低単価なものが多く、定量発注方式が適しています。このように、ABC分析を活用することで、各商品に最適な発注方式を選定し、在庫管理の効率を高めることができます。
効率的な定量発注方式のやり方
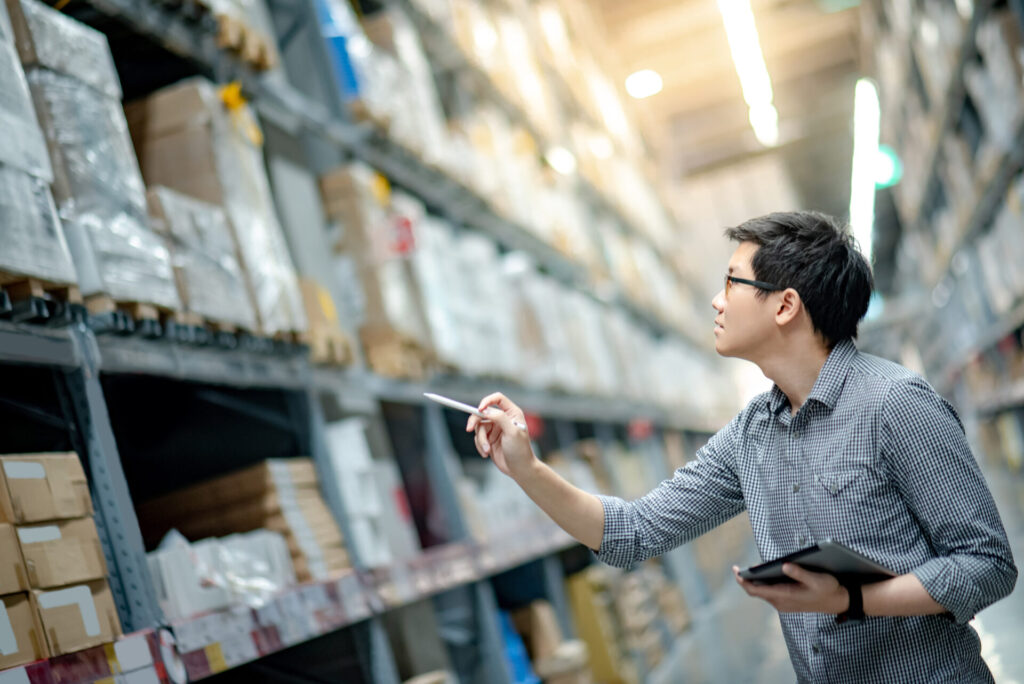
効率的な定量発注方式を実現するためには、発注点と安全在庫の適切な設定、リードタイムの管理、そして正確な需要予測が不可欠です。
まず、発注点と安全在庫を、過去のデータや市場のトレンドに基づいて設定し、在庫切れや過剰在庫を防ぎます。次に、リードタイムを短縮・安定化させるためにサプライヤーとの連携を強化します。ITシステムを活用すると、これらの管理も効率化できます。最後に、需要予測ツールやAI技術を用いて予測の精度を高め、適切な発注量を決定します。
これらのステップを踏むことで、効率的な定量発注方式を実現し、在庫管理の精度を向上させることができます。以下、具体的に解説します。
発注点と安全在庫を適切に設定する
発注点は在庫が一定の量に達したときに発注を行うポイントであり、安全在庫は需要の変動や供給の遅延に備えるための余裕在庫です。これらを正確に設定するには、過去の需要データや供給のリードタイムを分析し、適切な発注タイミングを見極めることが必要です。
さらに、季節変動や市場のトレンドも考慮に入れることで、在庫切れや過剰在庫を防ぎ、効率的な在庫管理を実現できます。
リードタイムを適切に管理する
リードタイム(発注リードタイム)とは、発注から納品までの時間のことです。リードタイムを適切に管理することは、在庫切れや過剰在庫を防ぐために不可欠です。
リードタイムの短縮や安定化を図るためには、サプライヤーとの緊密な連携が重要です。さらに、リードタイムを考慮した発注計画を立てることで、適切なタイミングでの発注が可能になります。在庫管理システムなどでリードタイム管理を効率化することでも、発注の精度を高めることができます。
需要予測を正確に行う
正確な需要予測を行うことで、適切な発注量を決定し、在庫切れや過剰在庫を防ぐことができます。需要予測を行う際には、過去の販売データや市場動向、季節変動などを分析することが求められます。
また、需要予測ツールやAI技術を活用することで、予測の精度を高めることが可能です。定期的に予測を見直し、実際の需要と比較することで、より正確な予測ができるようになります。
定量発注方式に在庫管理システムが便利な理由
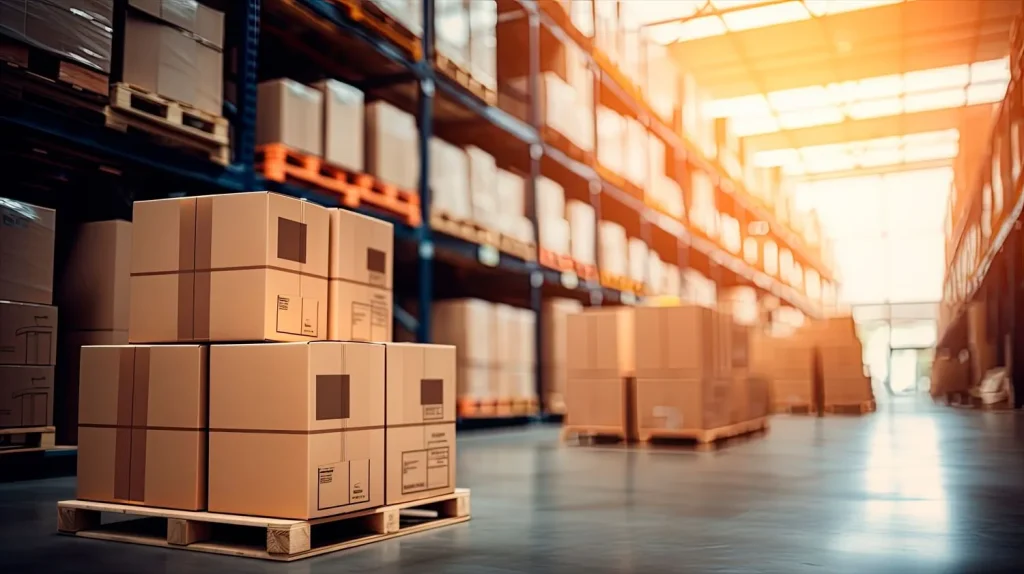
主要な在庫管理システムには以下の機能があり、定量発注方式の効率化と精度向上に大いに役立ちます。
- リアルタイムに最新の在庫数がわかる
- 過去の在庫・発注データが簡単に参照できる
- 将来在庫を見える化できる
- 発注点管理を自動化できる
リアルタイムに最新の在庫数がわかる
定量発注方式において、最も重要な在庫管理システムの機能は「リアルタイムな在庫管理」です。定量発注方式では「発注点を下回ったら発注する」という運用を行うので、常に正確な現在庫を把握する必要があるためです。
在庫管理システムとハンディーターミナルなどのIoTツールを連携して使用すると、現場で更新した入出庫データがリアルタイムで反映され、最新の在庫状況を把握できます。現場へ足を運び現物の在庫数を確認する手間が省けるだけでなく、在庫数の誤差も減らせます。
過去の在庫・発注データが簡単に参照できる
入出庫や発注のデータを在庫管理システム上へ蓄積していくことで、過去の在庫データ分析が容易になります。昨年の出荷量を参照したり、発注リードタイムの統計を取ったりすることで、正確な発注点の設定や見直しに役立ちます。
将来在庫を見える化できる
在庫管理システムは、将来の在庫状況を予測する機能も備えています。生産計画から逆算し、数ヶ月先の在庫数が一目でわかるようになる在庫管理システムもあり、計画的な発注が可能となります。将来の在庫見通しを可視化することで、発注の精度も向上します。
発注点管理を自動化できる
在庫管理システムでは、定量発注方式で重要な「発注点管理」を自動化することができます。システムが事前に設定された発注点に達した際に自動的に発注指示を出すため、人的ミスや見落としを防ぎます。これにより、必要な商品が常に適切なタイミングで補充されるため、業務の効率が向上します。自動化された発注点管理により、従業員の負担も軽減され、他の重要な業務に集中できるようになります。
在庫管理システムで定量発注方式を実現し、残業0を実現した事例
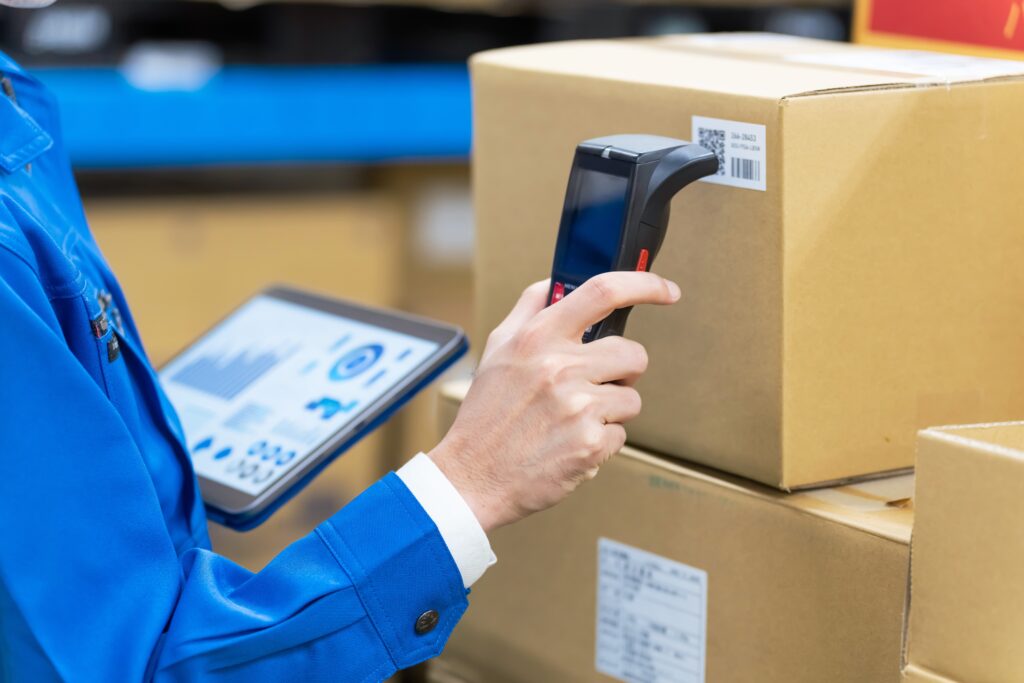
実際に、在庫管理システムの導入で定量発注方式を実現し、「少ない管理工数で発注できる」というメリットを実感された企業の例を紹介します。
ある製薬会社様では、リードタイムが長い原料が多く、3〜6ヶ月ほど先の将来在庫を見越した発注を行っています。これらの発注管理をエクセルで行っていましたが、仕入先のリードタイム把握や将来在庫の計算などの業務は、ベテラン担当者の経験則に基づいており、属人化の課題がありました。
そこで、在庫管理システムを導入し、将来在庫の見える化・発注点管理の自動化を実現しました。発注点や仕入先リードタイムの管理もシステム化したことで、ベテラン担当者以外も定量発注方式による発注業務ができるようになりました。これにより、他担当者との発注業務の分業も可能となり、残業をなくすことにも成功しました。
詳細はこちら:
将来在庫の自動計算で発注の負担・工数を削減!生産計画と在庫を紐づける管理を実現
22種類の生産管理システムをランキングで比較
初期費用相場や選び方のポイントをチェック
生産管理システムをそれぞれの特徴や初期費用相場などで比較したい場合は、「生産管理システムランキング」も是非ご覧ください。生産管理システムは、自社の製品・生産方式・企業規模などに適したものを導入しないと、得られるメリットが限定されてしまいます。事前適合性チェックや生産管理システムを選ぶ前に押さえておきたいポイントも解説していますので、製品選びの参考にしてみてください。