欠品を防ぐためには?欠品の原因、影響から、欠品リスクを下げる方法を解説
公開日:2024年12月22日
最終更新日:2024年12月23日
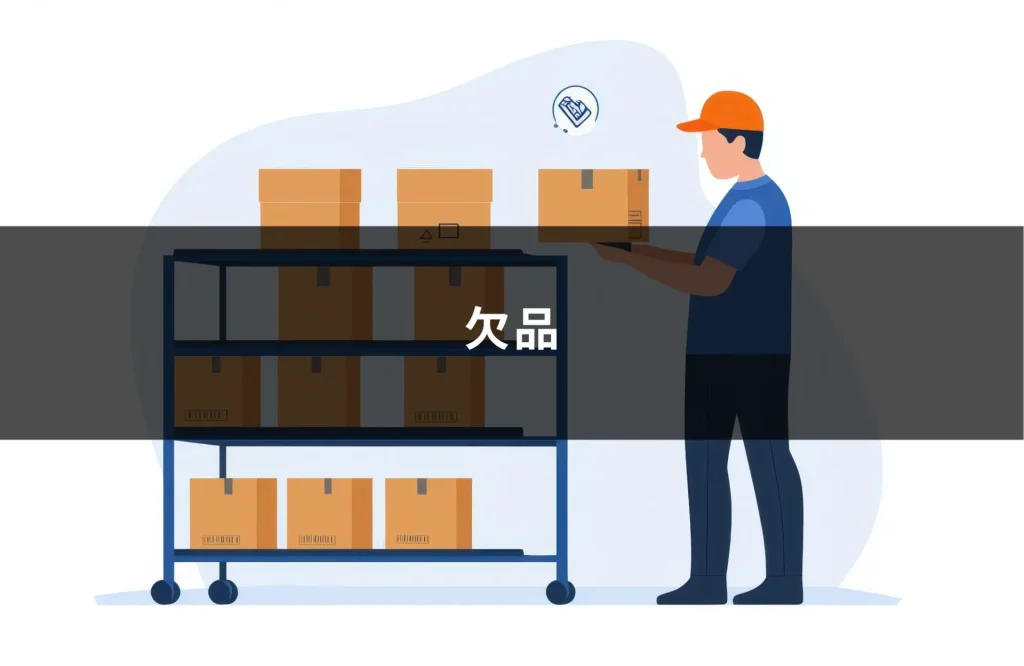
製造業における「欠品」は、売上機会の損失や顧客からの信用失墜など、さまざまな影響引き起こします。本記事では、多岐にわたる欠品の原因、欠品によるリスクを解説し、製品や原材料の在庫不足によって販売や生産に支障をきたす状況を回避するための具体的な対策についても紹介します。さらに、生産管理システムの導入によるメリットについても触れ、欠品リスクを減らすためのヒントを提供します。
欠品とは
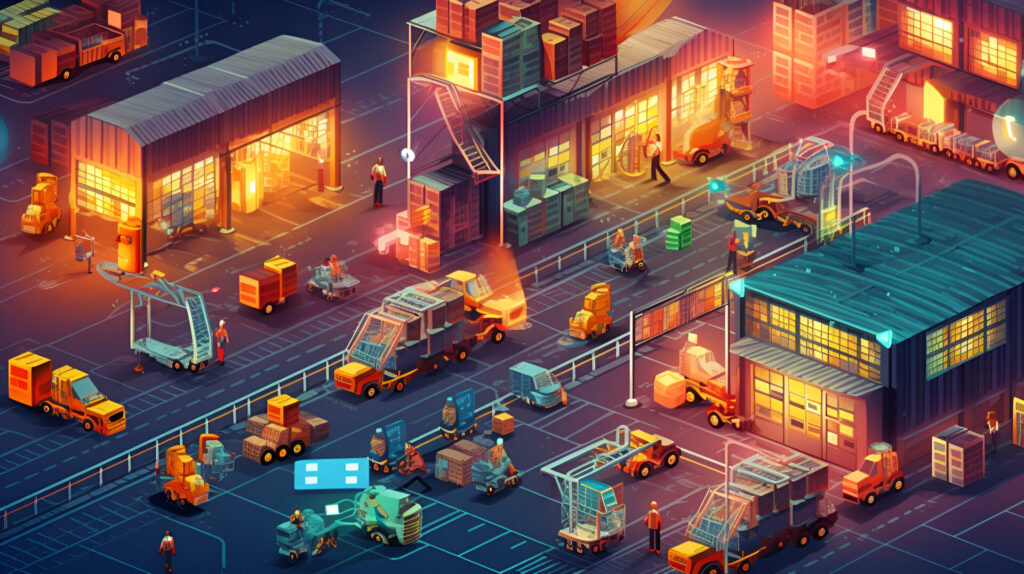
欠品とは、製品や部材の在庫が不足し、販売や生産に支障をきたす状況を指します。在庫不足に関連する問題全般を意味し、製造業や小売業におけるサプライチェーン管理上の大きなリスクとなります。
欠品は企業の収益性やブランド価値に悪影響を及ぼすだけでなく、顧客満足度の低下にもつながるため、迅速かつ適切な対策が求められます。
欠品、品切れ、在庫切れの違い
「欠品」と混同されやすい用語として、「品切れ」や「在庫切れ」がありますが、それぞれの意味には明確な違いがあります。
「品切れ」は主に顧客視点で使われることが多く、販売中の製品が一時的に売り切れている状態を指します。「在庫切れ」は店舗や倉庫の在庫管理の観点で用いることが多く、販売可能な製品が全くない状況です。
一方で、「欠品」には、販売用の在庫不足や、生産に必要な部品の不足、輸送遅延などのサプライチェーンの問題など、さまざまな観点を含む表現です。
欠品が発生する原因は何か
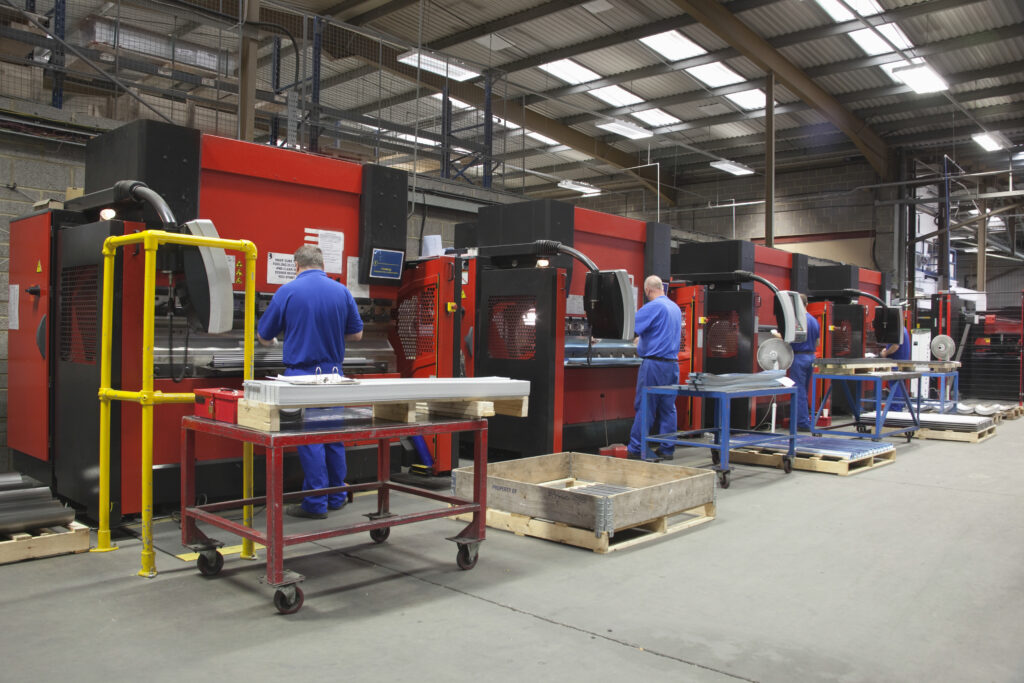
欠品は様々な要因が積み重なった結果起こります。それぞれの要因を明らかにし、個別に対策を講じることが、欠品リスクを改善するための第一歩です。そこで、以下では、具体的な欠品の原因について説明します。
フォーキャストの精度が低い
フォーキャスト(需要予測)の精度不足は、欠品の最も一般的な原因の一つです。
フォーキャストが実際の需要より低く見積もられると、在庫が不足し、顧客のニーズに対応できなくなります。特に、需要が急激に増える状況では、不正確なフォーキャストだと適切な在庫を確保できず、販売機会を逃すことになります。
市場の需要は一定ではなく、新製品の投入や季節的な変動、競合他社の動きなど、さまざまな変動要因が存在します。
しかし、予めこれらを完璧に反映させた需要予測をするのは現実的ではありません。最新情報のアップデートを怠らず、こまめな需要変化を捉えることが重要です。
サプライチェーンにおける遅延
サプライチェーン全体の遅延も、欠品の主要な原因の一つです。必要なタイミングで在庫が供給されないと、販売や生産が滞ってしまいます。特に、ジャストインタイム生産のように在庫保有を最小限に抑える運用では、部品や材料の供給遅延が直ちに生産品の欠品につながります。
また、グローバルな供給体制が一般化したため、供給業者や購入業者ではコントロールできない外部要因による遅延リスクが増加しています。サプライチェーンの各ステージにおいて製品供給への大きな影響を及ぼす具体的な可能性は次の通りです。
- 輸送遅延:天候不良、港湾での混雑やストライキ
- 原材料の調達問題:資源価格の高騰や産地の災害、内戦
- 国際的な規制変更:貿易規制の強化、関税の変更などによる通関手続きでのトラブル
- パンデミックや感染症の拡大:労働力不足や工場閉鎖による生産・出荷停止
このように、予測困難な事象が供給計画全体へ影響し、在庫不足を招くことがあります。
生産ラインの保全ができていない
生産ラインにおいて十分な設備保全ができてない場合にも、欠品につながる可能性があります。
設備の定期保全・メンテナンスを怠ると、予期できない故障やトラブルが発生しやすくなります。その結果、製品供給が滞ったり、突発的な生産計画の変更を余儀なくされたりするケースもあります。また、このような生産計画の変更が重なると、全体の生産効率を大きく低下させ、生産能力がひっ迫している製品では欠品に直結します。
さらに、突発的な故障に対する準備が不足している場合、修理や復旧に時間がかかり、その影響がさらに大きくなることもあります。
生産計画にムリがある
生産計画に無理があると、軽微なトラブルでも必要な供給量を確保できなくなり、欠品リスクが高まります。特に、生産管理担当者が製品や関連原材料の生産能力を正確に把握せず、リードタイムの管理が不十分な場合、現場に大きな負担を与えることになります。
特に多品種少量生産を行う企業では、生産スケジュールの調整や、必要な資材や人員の確保が一層難しくなります。一時的にムリのある計画を立てざるを得ない場合もありますが、この状態が継続すると、欠品リスクが高まる原因となります。
在庫管理の不備
在庫が適切に管理できていない場合、欠品に直結します。必要な製品や部品が足りない状況を見逃すと、販売・生産が滞ってしまいます。具体的には、次のような状況が挙げられます。これらの問題が原因で、タイムリーな補充や発注ができなくなる恐れがあります。
- 現在庫をリアルタイムに把握できていない
- 5Sが徹底できておらず、品薄の状態に気づきにくい
- 棚卸しの頻度が少なく、実際の在庫量と記録との乖離が大きい
- 安全在庫や発注点を適切に設定しておらず、需要変動に対して柔軟に対応できない
これらの問題を放置すると在庫不足が慢性化し、欠品が常態化するリスクが高まります。
欠品の影響とリスク
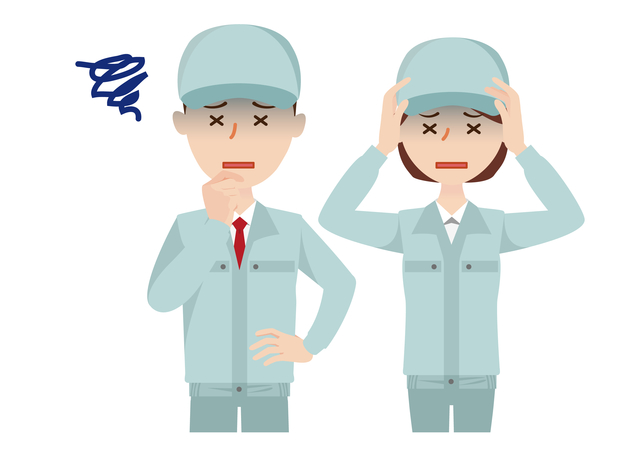
欠品は、自社内部の影響だけでなく、顧客との信頼関係にも大きな影響を及ぼします。具体的な影響・リスクについては次の通りです。
顧客満足度の低下
欠品は、顧客が必要とする製品を即座に入手できない状況を作り出し、顧客の満足度を大きく損ないます。
特に汎用品は製品自体の差別化ができないため、欠品が起きると即座に離脱や競合他社への流出を招く要因となります。「いつでも買える」という信頼が損なわれると、次回の購入時に他社の製品を選ぶ顧客も増えるでしょう。
また、企業が対応に追われ、顧客へのフォローアップが遅れれば、さらなる不満を招きます。このような状況はリピート率の減少につながり、長期的な売上にも影響を及ぼします。
売上機会の損失
欠品によって顧客の需要を満たせない場合、その需要がそのまま他社へ流れる可能性があります。これは、在庫があれば本来自社が獲得したはずの売上機会を失うことを意味します。
特に、高額品や季節製品での欠品では、影響度が甚大となる傾向があります。
この「売上機会の損失」は、1回の販売損失だけではなく、顧客を競合企業へ奪われるリスクを意味します。一度奪われたシェアを奪回することは容易ではありません。製品が売れなかった場合、広告や販売促進に投資したコストも無駄になります。欠品による売上損失は、企業の成長を直接的に妨げる大きなリスクといえるでしょう。
顧客対応の工数増加
欠品が発生すると、顧客対応で多くの工数が必要となり、カスタマーサポート部門や営業部門に大きな負担がかかります。具体的には、顧客からの問合せやクレームに対して、謝罪、納期の確認、返品処理や代替品の提案など、通常業務にはない追加の対応が求められます。これらの作業には多くの手間と時間がかかり、他の重要な業務に充てるリソースを圧迫します。
さらに、欠品を避けるために緊急発注や高コストな輸送手段を選択する場合、追加コストが発生し、利益を圧迫します。欠品が常態化すると、顧客対応部門や営業部門の負担が恒常的に増大し、業務効率の低下や人件費の増加を招き、企業全体のパフォーマンスにも悪影響を及ぼします。
企業イメージの低下
頻繁な欠品は、「必要な製品がいつも買えない」という印象を顧客に与え、企業全体の信頼性が低下します。このようなイメージの悪化は顧客離れを引き起こし、新規顧客の獲得が難しくなるだけでなく、既存顧客が他社に奪われる可能性も高くなります。
さらに、”to C”ビジネスにおいては、SNSやレビューサイトでの否定的な口コミがすぐに拡散します。このため、一度イメージが低下すると、修復に時間とコストがかかります。また、競合他社がその機会を利用して顧客を奪うリスクも高まります。
このように企業イメージの低下は早期回復が難しく、長期的な収益性に悪影響を及ぼします。
欠品リスクを下げるための3つの対策
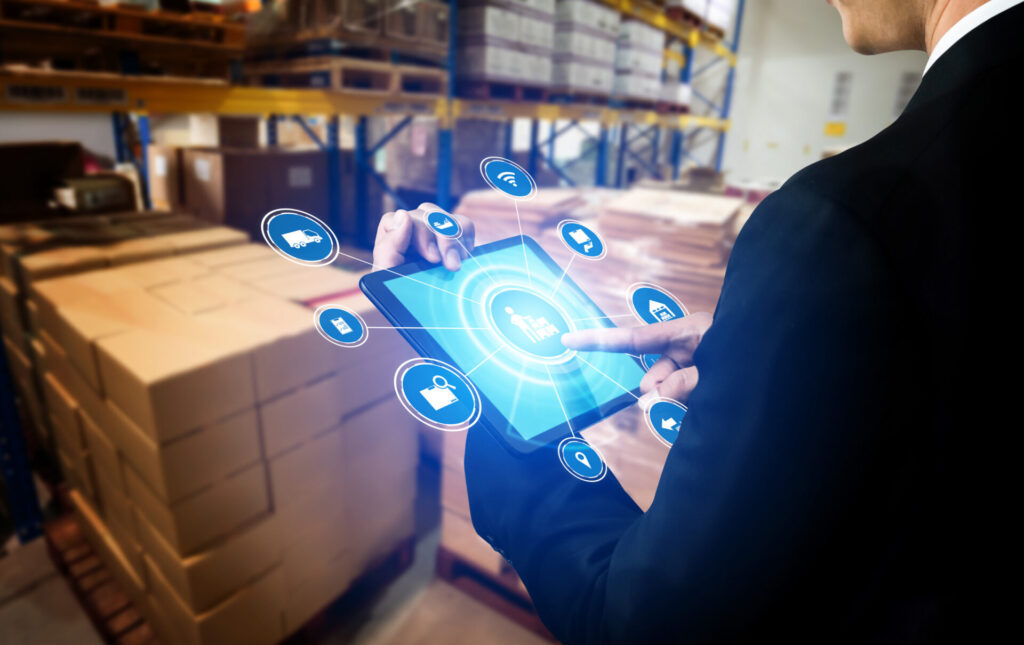
欠品は自社にとって悪影響を及ぼします。これを最小限に抑えるためには、以下の3つの対策が有効です。
精度の高いフォーキャストに基づく生産計画
精度の高い需要予測を入手し、これに基づいた生産計画を策定することは、欠品防止に効果的です。
過去の販売データ、季節性、トレンド、市場動向を分析し、将来の需要を予測することで、無理のない計画を立てることが可能になります。近年では、ビッグデータをもとにAIや機械学習を活用すれば、予測精度をさらに向上させ、需要の急な変動を予測しやすくなってきました。
また、需要予測に基づいて生産ラインの稼働率やリードタイムを最適化すれば、余剰在庫を最小化しつつ、安定した供給体制が実現できます。
在庫の見える化
在庫の見える化とは、倉庫や店舗などの在庫状況を把握できる仕組みを構築することを指します。
在庫の見える化によって、在庫の所在・数量を正確に把握でき、欠品リスクを大幅に減少させることが可能です。さらに、社内の業務プロセスが効率的になり、欠品リスクを大きく下げる効果もあります。
発注点の管理
発注点管理とは、在庫が一定のレベルを下回った時点で発注を行う仕組みです。欠品を防ぐためには、データに基づいて発注点を適切に設定し、タイムリーに補充が行える体制を構築することが有効です。
発注点の設定には、生産リードタイム、需要の変動、サプライヤーの納期などを考慮し、最適な在庫レベルを維持します。
発注点管理の代表例として、トヨタ生産方式で採用されているかんばん方式が挙げられます。かんばんの活用により、在庫が発注点に達したタイミングで自動的に補充指示が出されます。これにより、在庫量を効率的に管理しながら欠品を防げます。特に、少量多頻度の補充を行う場面で高い効果を発揮します。
このように適切な発注点管理を行うことで、在庫コストの削減と供給安定性を同時に実現することができます。
生産管理システムの導入によるメリット
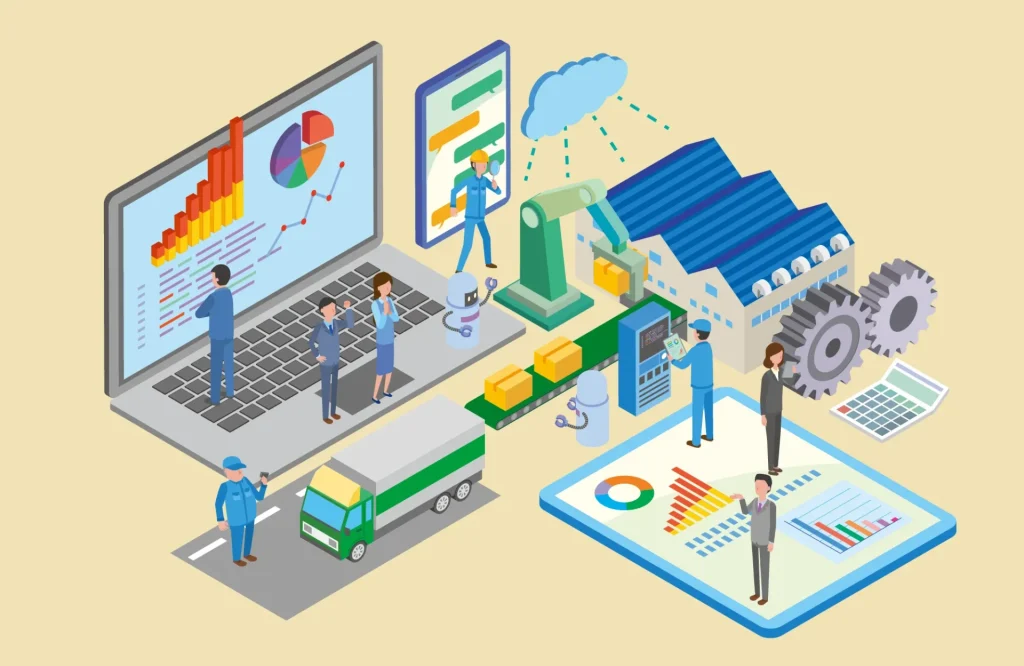
欠品防止には、生産管理システムの導入が効果的です。ここでは、その具体的なメリットについて説明します。
リアルタイムな在庫見える化
生産管理システムを活用すればリアルタイムで在庫状況が把握できるようになり、過不足を防ぐ管理が可能となります。さらに、在庫量の確認や更新作業が自動化され、ヒューマンエラーも防ぐことができます。
さらに、生産管理システムの活用では、担当者だけでなく部門内で情報共有したり、複数拠点の在庫状況を統合的に管理したりすることも可能となります。このような体制を整えることで、迅速かつ適切な意思決定を行えるようにします。また、必要な在庫を迅速に調整でき、過剰在庫や不足を未然に防ぎます。
さらに、自動で在庫レベルの異常を検知できる仕組みを整えることで、在庫不足が顕在化する前に対策を講じることが可能となります。
精緻な生産計画と発注管理
生産管理システムは、精緻な生産計画を策定し、適切な原材料の発注管理をするための強力なツールです。
部品・材料のリアルタイムな在庫情報に加えて、それぞれのリードタイム情報を簡単に活用することが可能となります。さらに生産計画とリアルタイムのフォーキャストデータも活用すれば、将来在庫の予測が可能となり、欠品を未然に防止できる可能性が高まります。
生産データの一元管理
生産データの一元管理は、生産活動に関わる情報を一つのプラットフォームで集中管理する方法で、欠品リスクへの対策として有効です。具体的には次のような情報を一元管理します。
- 材料・部品の在庫情報
- 製造工程の使用部材ロット情報や作業履歴
- 製品ロットごとの品質検査の結果
これにより、製品に関する情報をリアルタイムで把握するとともにデータの重複や入力ミスを防ぎ、業務効率が向上します。また、データの一元化により、機械学習・AIなどの活用による需要予測や工程最適化を加速させます。
→生産情報・検査情報をシステムで一元管理した事例はこちら
22種類の生産管理システムをランキングで比較
初期費用相場や選び方のポイントをチェック
生産管理システムをそれぞれの特徴や初期費用相場などで比較したい場合は、「生産管理システムランキング」も是非ご覧ください。生産管理システムは、自社の製品・生産方式・企業規模などに適したものを導入しないと、得られるメリットが限定されてしまいます。事前適合性チェックや生産管理システムを選ぶ前に押さえておきたいポイントも解説していますので、製品選びの参考にしてみてください。