MRP(資材所要量計画)とは ERPや生産管理システムなどのツールや具体的な流れまで解説
公開日:2023年07月05日
最終更新日:2025年03月19日
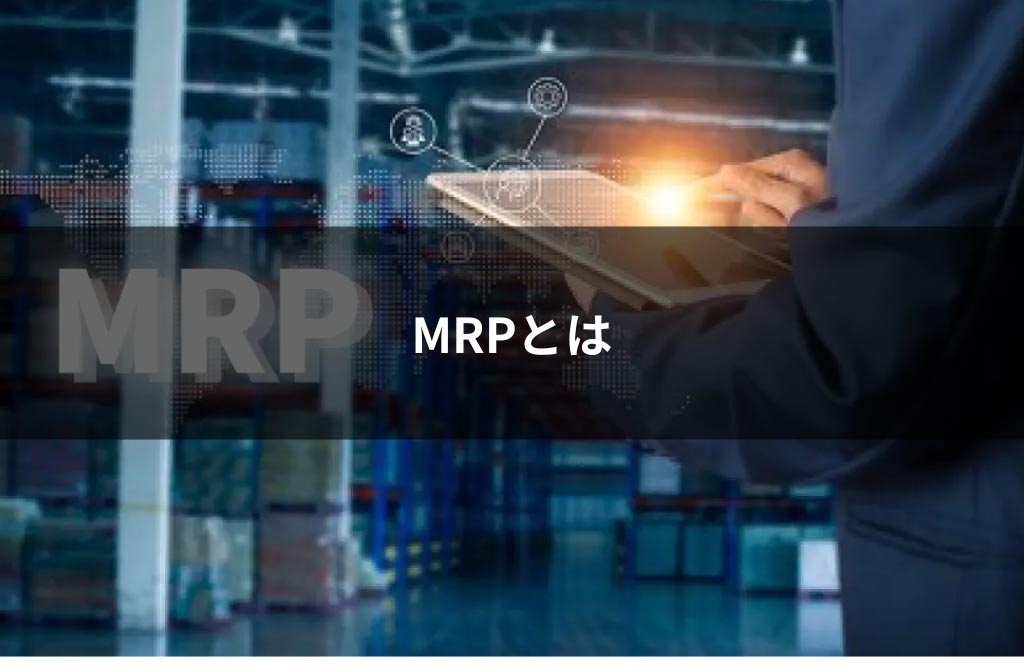
過剰在庫や資材不足を防ぎ、生産効率を高めるシステムの一つにMRP(資材所要量計画)があります。しかし、MRPは時代とともに変化し、MRPⅡ、ERPと新しい管理手法が主流になりつつあります。
本記事では、MRPの概要、よく比較される製番管理やJITとの違い、具体的な運用方法について解説します。最後には、MRPをシステム化する方法についても、事例付きで紹介します。
MRPとは
MRP(Material Requirements Planning)は、資材所要量計画とも呼ばれ、必要な資材を適切な数量・タイミングで手配する計画を立てる手法です。需要に基づく生産スケジュールや在庫データ、部品構成表(BOM)から、材料・部品・半製品などの所要量を計算し、適切な発注時期や数量を決定します。
MRPと製番管理の違い
MRPと製番管理は、いずれも代表的な生産管理手法ですが、その目的や運用方法に違いがあります。
MRP | 製番管理 | |
資材の手配方法 | 資材の品目単位で手配 | 製番単位で手配(受注情報を本に発注) |
共通品番の資材 | 同品番の資材を別製品の生産に利用できる | 同じ品番の資材でも原則共有しない |
向いている生産方式 | 計画生産による量産 | 個別受注生産 |
MRPは、資材の品目単位で手配数量を管理し、必要な資材を効率よく手配するために設計された手法です。異なる製品の共通部材も、同じ品番であればまとめて手配可能です。主に、量産品の生産で使用される「部品」中心の管理手法といえます。
一方、製番管理は、個別の受注に対し製番を割り振り、製品ごとのトレーサビリティや生産進捗を管理する方法です。資材にも受注ごとに製番を割り振るため、同じ品番の資材でも、異なる製番のものは使用できません。受注を基準とする「製品」中心の管理手法です。この性質上、製番管理は個別受注生産に適しています。
→ 製番管理とは
これらは対称的な管理手法ではあるものの、MRPと製番管理を併用するケースもあります。例えば、製番による受注生産で、多くの製品で共通利用できる部材(ねじやボルトなど)のみMRP手配する事例などがあります。
MRPとJITの違い
MRPとJIT(ジャストインタイム)は、どちらも「必要なものを、必要なときに、必要な量だけ手配する」ことを目指す方法です。しかし、アプローチ方法に違いがあります。
MRP | JIT(ジャストインタイム) | |
生産方式 | 押し出し方式(プッシュ型) | 引っ張り方式(プル型) |
向いている生産方式 | 計画生産による量産 | 多品種少量生産など |
メリット | 将来の需要を加味した計画的な資材調達が可能 | 在庫数を最小限に抑えられる |
デメリット | より複雑な在庫管理や生産計画が必要 | 急な需要変動に弱い |
MRPは将来の生産計画に基づいて資材を前もって手配し、在庫を確保する方法です。初めに立てた生産計画をもとに生産を進める「押し出し方式(プッシュ型)」と呼ばれる手法の一つです。計画的に資材調達できるため、大量生産向けといえます。
一方、JITは、後工程から必要な資材を必要なタイミングで必要なだけ調達する「引っ張り方式(プル型)」の生産方式です。極力在庫を持たないことを目指すため、在庫コスト削減や生産効率化が重視される環境に適しています。
MRPからERPへ発展した歴史
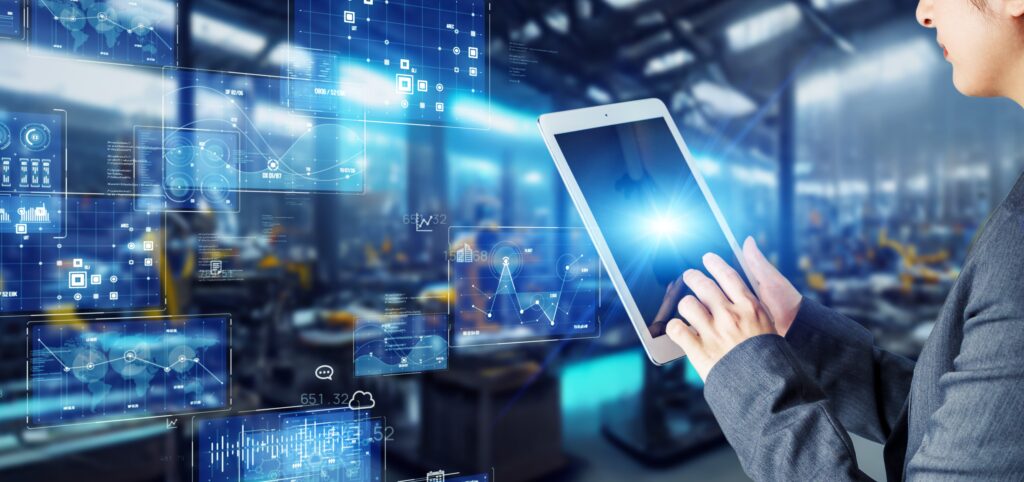
MRPは生産管理の進化とともに発展し、MRPⅡ、ERP(Enterprise Resource Planning)と、統合的な管理システムへ主流が移っていきました。それに伴い、カバーする業務範囲も広がってきました。
1970年代 MRPⅠ:基本的な資材所要量計画
1970年代に登場したMRPⅠは、資材所要量計画の基本的なシステムです。MPS(基準生産計画)に基づき、必要な資材量を計算し、発注や手配を行うことが可能になりました。
MRPⅠは、基本的な資材管理に特化しており、製品の仕様や生産スケジュールに基づいて資材を効率よく手配することが主な目的です。この時代のMRPⅠは、手作業や簡易的なコンピュータシステムで運用されることが一般的でした。
1980年代 MRPⅡ:生産管理全体を網羅
1980年代に発展したMRPⅡは、MRPⅠをさらに拡張し、生産管理全体をカバーするようになりました。MRPⅡは、資材管理だけでなく、設備の負荷計算や人員・生産スケジュールの調整など、製造プロセス全体の最適化を目指す手法です。
これにより、生産計画と実際の生産活動を連携させ、効率的な生産管理が可能となりました。また、在庫管理や生産コストの計算にも対応し、製造業における総合的な管理ツールとして活用されました。
1990年代 ERP:財務や会計も一元管理
1990年代には、MRPⅡがさらに進化し、ERPという企業全体の資源管理を行うシステムが登場しました。ERPは生産情報だけでなく、販売、財務、会計などのビジネス全体を統合的に管理するシステムです。
これにより、情報が部門間で連携し、全社的な最適化が可能となりました。ERPは、製造業に限らず、幅広い業界で活用されるようになり、企業経営における重要なツールとなっています。
このように、今は「MRPはERPの機能の一つ」と言えますが、ERPはMRPから発展したシステムでもあります。
→ ERPとは
近年においてMRPと表現するときは、単に資材所要量計画だけを指す場合もあれば、生産管理や会計周りまで広義に捉える場合もあります。
MRPの計算に必要な情報
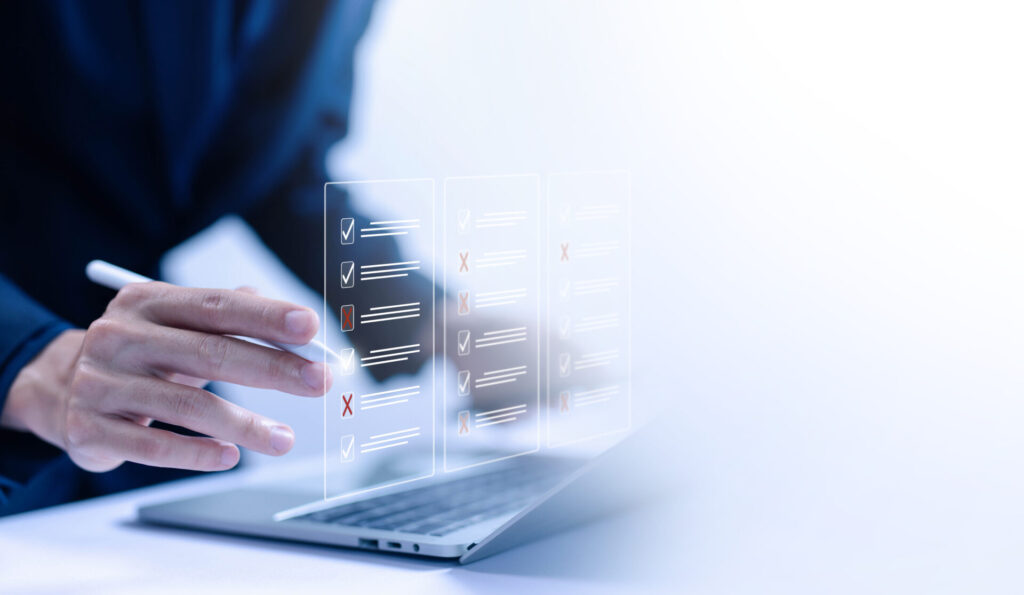
まず、最も基本的な資材所要量計画を行うためには、基準生産計画(MPS)、部品構成表(BOM)、在庫情報を正確に把握することが必要です。
基準生産計画(MPS)
基準生産計画(MPS)は、何を、いつ、どの程度生産するかを決定する、MRPの中核となる情報です。製品の需要予測や顧客からの注文に基づき、MPSを正確に立案できれば、必要な資材を無駄なく手配できます。また、MPSは、生産管理の他の要素(在庫管理や工程管理)にも直接影響を与えるため、正確かつ現実的な設定が重要です。
→ MPSとは
部品構成表(BOM)
部品構成表(BOM)とは、製品を構成する部品や材料のリストです。製品ごとのBOMには、各部品の数量や構成関係が記載されています。MRPでは、BOMの情報を基に資材の所要量を計算します。
BOMが正確であれば、必要な部品の過不足が防がれ、生産の遅延やコストの増加を回避できます。また、BOMは製品の種類や変更にも対応できる柔軟な管理が求められます。
→ BOMとは
在庫情報
現在の在庫量や発注済みの資材の状況など、在庫情報を正確に把握することも、MRPの計算には重要です。MRPでは、この在庫情報を基に必要な資材数量を計算し、適切なタイミングで手配します。正確な在庫情報がなければ、所要量計算の精度が落ち、過剰在庫や資材不足に陥る可能性があります。
例えば、現在庫数を実際より少なく見積もってMRPを立案すると、実際はまだ在庫がある資材を追加発注し、過剰在庫となる可能性があります。逆に、現在庫数を多く見積もると、発注数不足による欠品が発生し、生産遅延にも繋がりかねません。
特に、部品や材料が多く使用される組立品業界や電子部品業界、基板実装業界などでは、在庫管理の精度が生産効率に直結します。欠品による損失も大きくなりやすいため、在庫情報の適切な管理が求められます。
MRP策定の手順
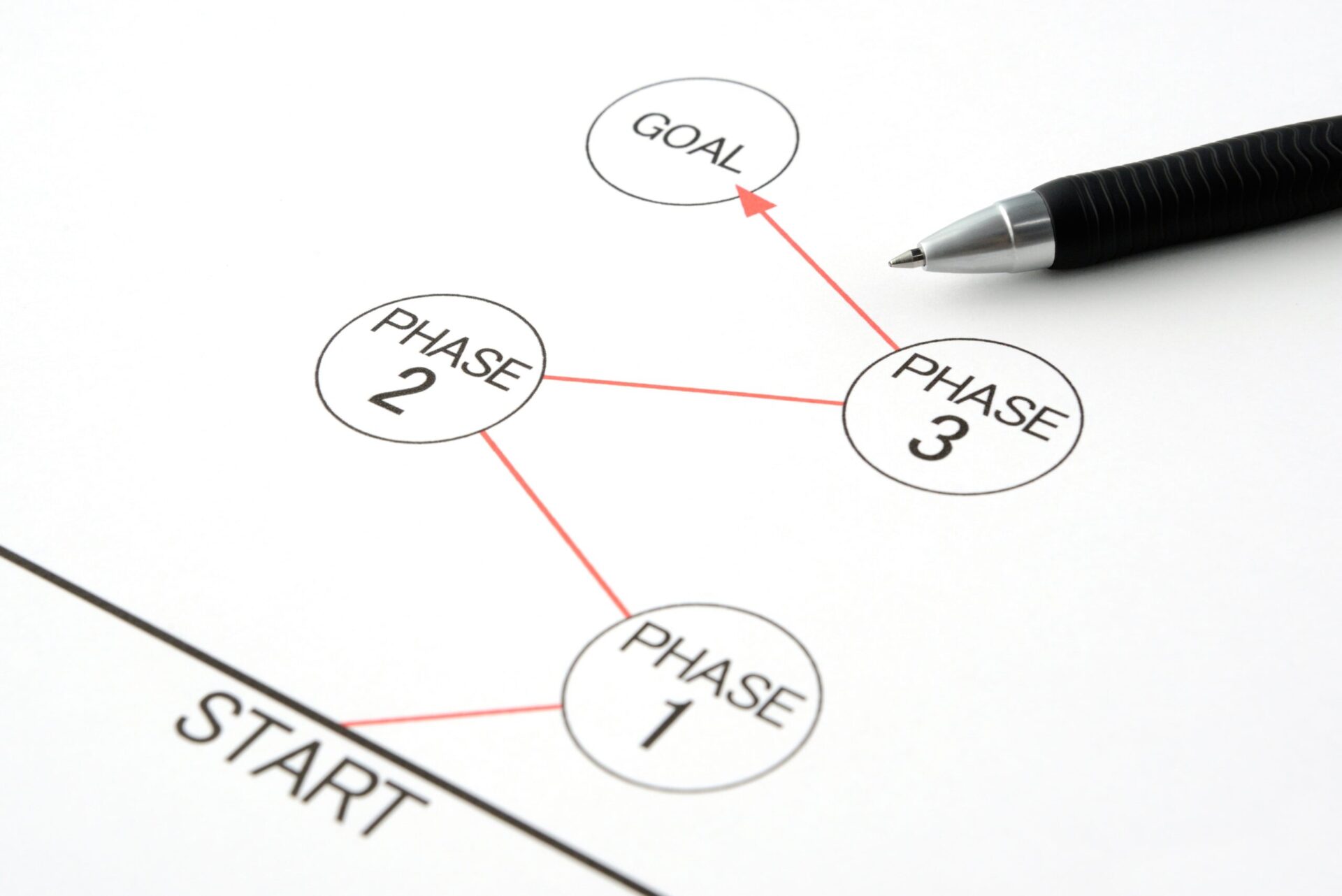
MRPは、次のような流れで策定し、資材の手配を行います。
- 基準生産計画(MPS)の立案
- 総所要量の計算
- 正味所要量の計算
- ロット数の考慮・確認
- リードタイムの計算
- 負荷計算(CRP)
- オーダー生成(発注)
基準生産計画(MPS)の立案
まず、基準生産計画(MPS)を立案します。具体的には、需要予測や顧客からの注文データを基に、何をいつまでに生産するか、最終製品の生産量や納期を具体的に計画します。
総所要量の計算
次に、MPSに基づいて総所要量(最終製品を生産するために必要な資材の合計量)を計算します。
作業としては、各製品のBOMを参照し、製品に必要な全ての資材の数量を計算することで、全体の資材需要を把握します。この段階で計算された総所要量を基に、資材手配計画を立案します。
正味所要量の計算
必要な資材の総所要量を算出した後は、現在の在庫状況や発注残を考慮し、追加で手配すべき正味の資材所要量を算出します。
在庫が十分にある場合は、追加の資材手配は不要です。不足がある場合には、その分の資材を新たに発注します。正確な在庫情報に基づく正味所要量の計算により、過剰な資材手配を防ぎ、効率的な在庫管理が可能となります。
ロット数の考慮・確認
ロット数とは、一度に発注する資材の最小単位を指します。MRPでは、ロット数を考慮して、手配する資材の量を調整します。
例えば、必要な資材が50個であっても、発注ロットサイズが100個であれば、100個を超える量で発注する必要があります。ロット情報を適切に管理することで、無駄な資材手配を防ぎます。
リードタイムの計算
次に、資材を発注してから実際に手元に届くまでのリードタイム(期間)も計算し、資材を必要なタイミングで手配できるように計画します。
リードタイムが長い場合は、早めに発注する必要があるため、注意して計画する必要があります。海外調達や特殊部品などの場合、数ヶ月〜半年前から手配が必要なケースもあります。リードタイムを正確に把握したうえでMRPを策定すると、必要なタイミングでの資材不足による生産遅延を防ぐことができます。
負荷計算(CRP)
MRPⅠでは、ここまで計算した時点でオーダー(発注)となりますが、MRPⅡにおいては負荷計算(CRP:Capacity Requirements Planning)まで行います。負荷計算とは、MRPの中で、生産設備の稼働状況を考慮して生産スケジュールを調整することです。
設備能力を超えない範囲で生産計画を立てることで、効率的な生産ができます。
オーダー生成(発注)
最後は、オーダーの生成です。計算された正味所要量やロットサイズ、リードタイムに基づいて、資材や部品の発注を行います。
MRPを導入するメリット
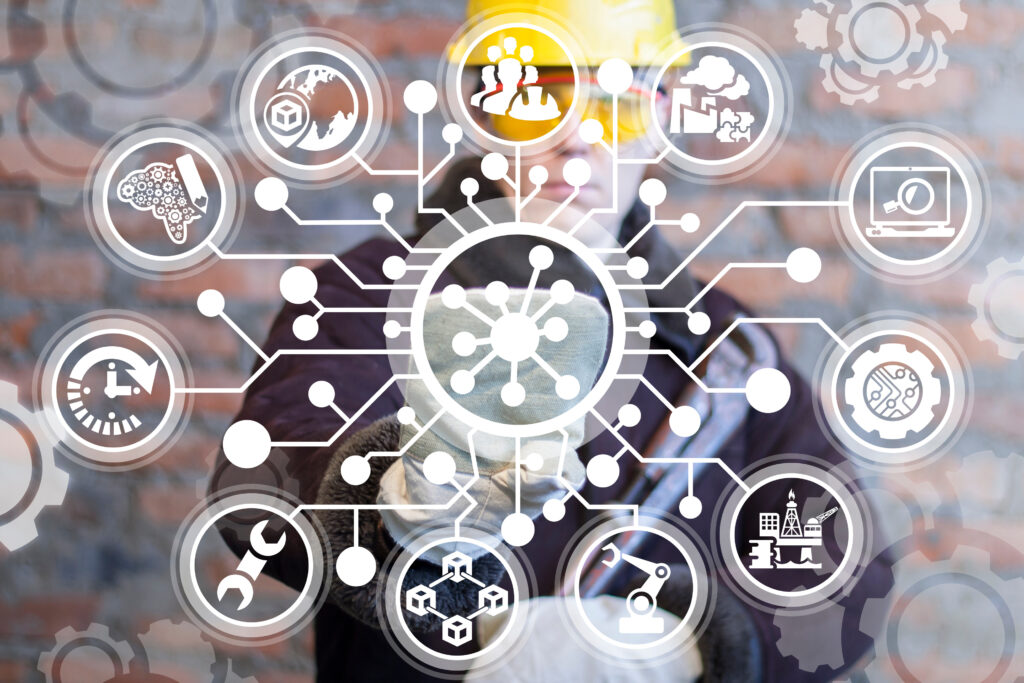
MRPを導入することで、さまざまなメリットが得られます。
適正在庫を維持できる
MRPは、需要予測に基づいて必要な資材を適切なタイミングで発注するため、在庫の過不足を防止できます。MRP活用で在庫リスクを軽減すると、以下のようなメリットが得られます。
- 滞留在庫をなくしキャッシュフローの改善
- 長期在庫による在庫品質の悪化・廃棄ロスを削減
- 保管費などの在庫コストを削減
製造原価を下げられる
MRPを有効活用できると、製造原価の低減も期待できます。
例えば、複数の製品での共通部品を一括発注すると、ボリュームディスカウントで発注単価を下げられる可能性があります。数ヶ月分の所要量をまとめて発注し、単価を下げる手法もあります。このように、MRPは製品単位に都度発注する場合に比べて、発注単価を抑えられる手法と言えます。
また、何度も発注する場合と比べて管理工数も抑えられるため、結果的に製造原価の低減・利益向上に繋がります。
生産性が向上する
MRPで生産計画通りに資材が供給されるようになると、生産ラインの停止や遅延が減少し、生産性が向上します。さらに負荷計算までできると、設備の稼働率を向上できます。
計画の柔軟性が上がる
MRPが効率的に機能すると、需要の変動や計画の変更にも柔軟に対応できます。需要が急増した場合でも、MRPによって資材の手配が迅速に行われ、柔軟な生産計画を立案できます。
製造リードタイムの短縮
MRPは製番管理と比較すると、製造リードタイムを短縮しやすい管理手法です。受注生産で製番管理を活用する場合、受注を受けてからの資材発注となりますが、MRPは需要に基づく生産計画に応じて資材を手配します。例えば、発注から納入まで1ヶ月かかる資材でも、MRPにて事前発注しておけば、生産時期にちょうど資材が入荷するように調整可能です。
製造リードタイムを短縮できると、顧客への納入リードタイム短縮にも繋がり、顧客満足度の向上にも繋がります。
MRPの注意点
MRPには多くのメリットがありますが、導入にあたっては注意点もあります。以下では、MRP導入に伴う主な課題を説明します。
在庫管理が複雑化する
MRPでは、さまざまな資材の手配や在庫状況をリアルタイムで把握する必要があるため、在庫管理のプロセスが複雑化します。正確な在庫情報が得られないと、正確なMRP計算も難しくなります。
需要予測の精度が低いと在庫過多・不足になる
MRPの効果は、需要予測の精度に大きく依存します。予測が誤っていると、資材の過不足が発生し、場合によっては生産遅延に繋がります。その結果、製造コストの増加や顧客満足度の低下につながる可能性があります。需要の変動が激しい業界では、予測精度を高めるためのデータ分析や予測モデルが必要です。
部門間での緻密な情報共有が必須
MRPにおいては、複数の部門での情報共有が必要になるケースがあり、情報共有の正確性とスピードが求められます。例えば、設計部門での設計変更でBOMが変わった場合、それをMRP担当者が把握できていないと、設変前の資材を手配してしまいます。また、製造現場の実在庫数がMRP担当者に共有されないと、現在庫に基づく資材手配も難しくなります。
MRPをシステム化する代表的な方法3つ
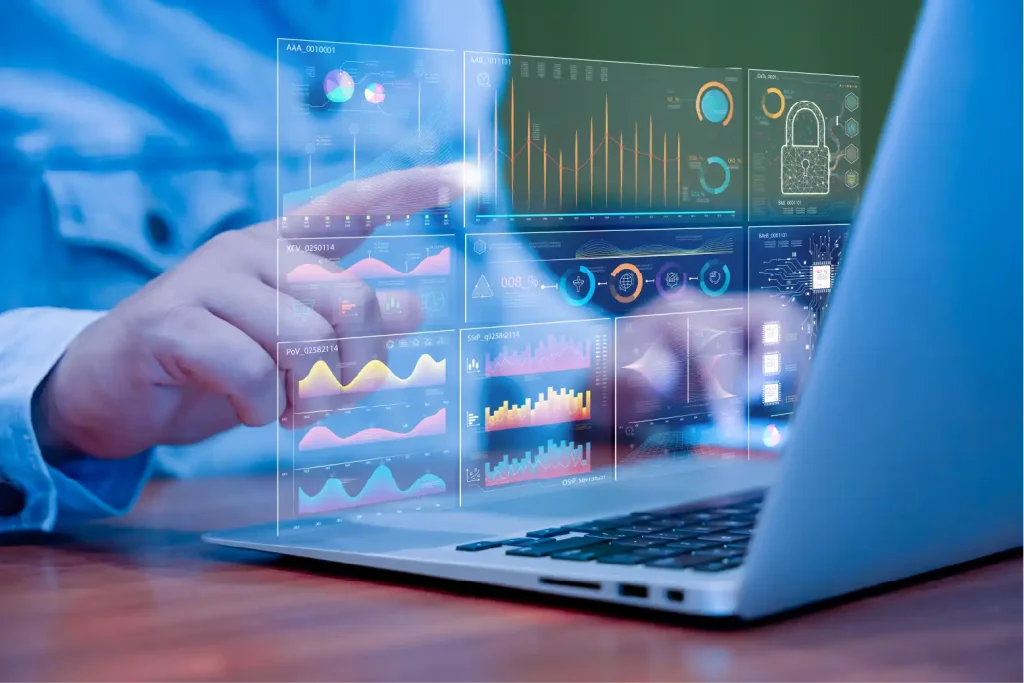
MRPで複雑かつ膨大なデータを扱うにあたり、エクセルなどでのアナログな管理に限界を感じる企業は少なくありません。より少ない工数で、ミスなくMRPを行うには、MRPのシステム化が不可欠と言えます。
MRPをシステム化する主な方法としては、以下3つが考えられます。
- 生産スケジューラ(生産計画システム)
- ERP
- 生産管理システム
生産計画に特化してシステム化したい場合は「生産スケジューラ」、会計などまで広く一元管理したい場合は「ERP(SAPなど)」がおすすめです。
「生産管理システム」は、MRPに必要な情報を一元管理できる点は、ERPに似ていると言えます。ERPとの一番の違いは、製造現場の情報をよりリアルタイムに反映でき、正確なデータをもとにMRP策定ができる点です。
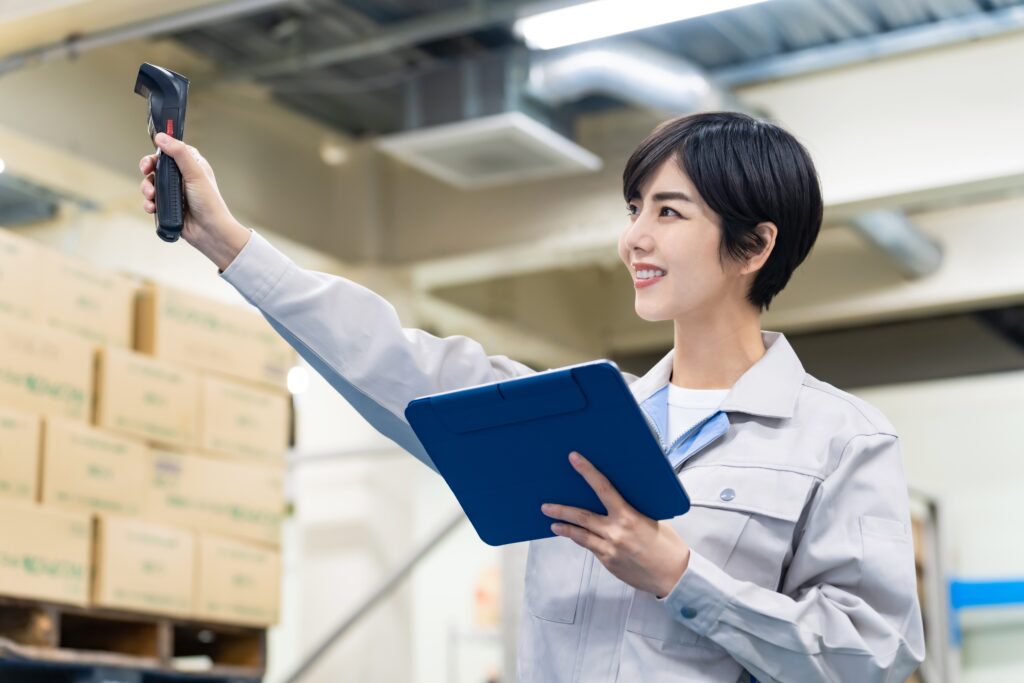
生産管理システムの多くは、バーコードやQRコード管理が可能なIoT端末との連携が可能です。これらの端末を使うと、PCが持ち込めない製造現場でもリアルタイムに在庫情報・工程進捗・設備負荷などの情報を収集できます。これらの正確な情報をもとに、生産計画やMRPを立案できる点は、大きなメリットです。
生産管理システムのデメリットは、会計機能がない製品もある点です。しかし、既存の会計ソフトや基幹システムと連携可能なシステムを使えば、受注~出荷までの情報をスムーズに一元管理できます。近年は、クラウド型で低コストな生産管理システムも増えてきていることもあり、ERPと比べて検討ハードルが低いとも言えます。既存システムを変えずに、低コストな生産管理システムをスピーディに導入する企業も多くあります。
生産管理システムでMRP効率化を実現した導入事例:
所要量計算の手間を年間100時間削減!機能を絞った導入で、既存システムと共存しながらピンポイントに課題を解決
22種類の生産管理システムをランキングで比較
初期費用相場や選び方のポイントをチェック
生産管理システムをそれぞれの特徴や初期費用相場などで比較したい場合は、「生産管理システムランキング」も是非ご覧ください。生産管理システムは、自社の製品・生産方式・企業規模などに適したものを導入しないと、得られるメリットが限定されてしまいます。事前適合性チェックや生産管理システムを選ぶ前に押さえておきたいポイントも解説していますので、製品選びの参考にしてみてください。