入荷検品のよくある課題と改善策:バーコード管理と在庫管理システムでミスをなくす方法
公開日:2024年09月17日
最終更新日:2025年01月30日
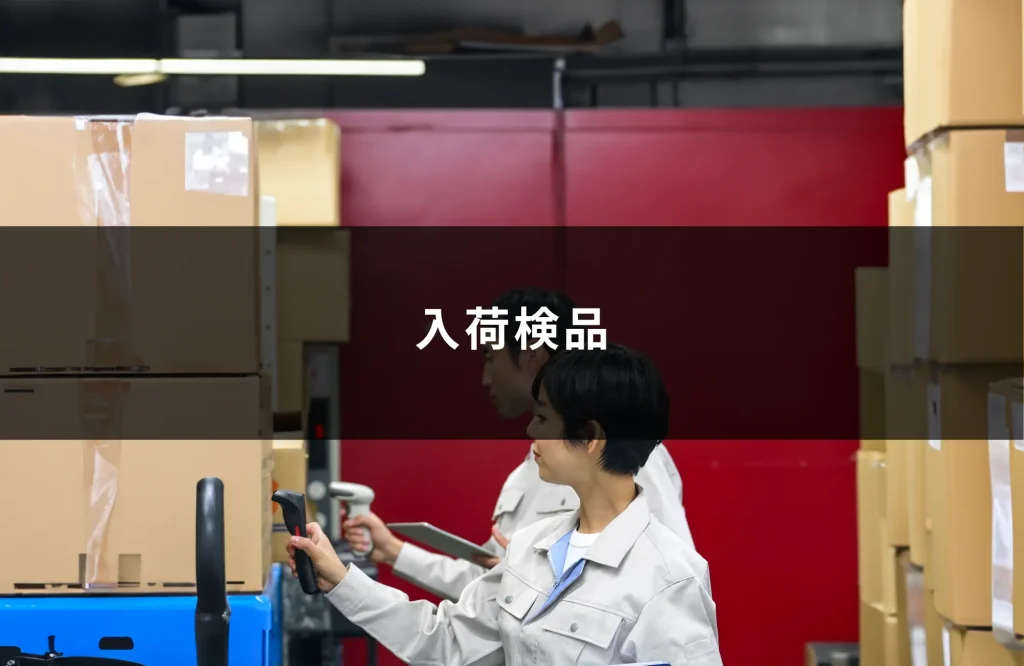
入荷検品をしない中小・中堅製造業の企業は、少なくありません。しかし、入荷検品は、在庫管理の精度を保ち、顧客満足度を高めるための重要なプロセスです。
本記事では、入荷検品の目的や「入庫」との違いを解説し、その重要性について在庫のズレや誤出荷の防止、顧客の信頼獲得の観点から掘り下げます。さらに、手作業からデジタル化までの具体的な方法やよくある課題、改善方法としてのバーコード管理と在庫管理システムの導入事例もご紹介します。
入荷検品とは何か
入荷検品は、企業が仕入れた製品や原材料が倉庫に届いた際に、その数量や品質を確認するプロセスです。仕入れ先から届いた物品が発注通りであるかをチェックし、受け入れの可否を判断します。入荷検品を行わない中小・中堅企業も多々ありますが、適切に入荷検品を行うことで在庫管理の精度向上に大きく貢献します。
入荷検品の目的
入荷検品の主な目的は、数量や品質の確認を通じて発注した通りの製品が届いているかを確かめることです。これにより、実在庫と理論在庫の差異や、品質不良を防ぐことができます。また、入荷検品を行うことで仕入先のパフォーマンスを評価する指標ともなり、サプライチェーンの最適化に役立ちます。
適切な検品によって不良品や誤出荷を防止し、最終的には顧客満足度の向上につながります。
「入庫」との違い
入庫とは、入荷検品が完了した製品を、正式に倉庫の在庫として登録するプロセスです。例えば、入荷担当者が受入エリアで入荷検査を行う作業は「入荷」、その後にA倉庫に保管すると「入庫」を終えたといえます。つまり、入荷検品は入庫の前段階として、品質や数量を確認するステップを指します。入荷検品が問題なく完了した後、製品は倉庫に保管され、在庫として管理されるようになります。
入荷検品の重要性とは
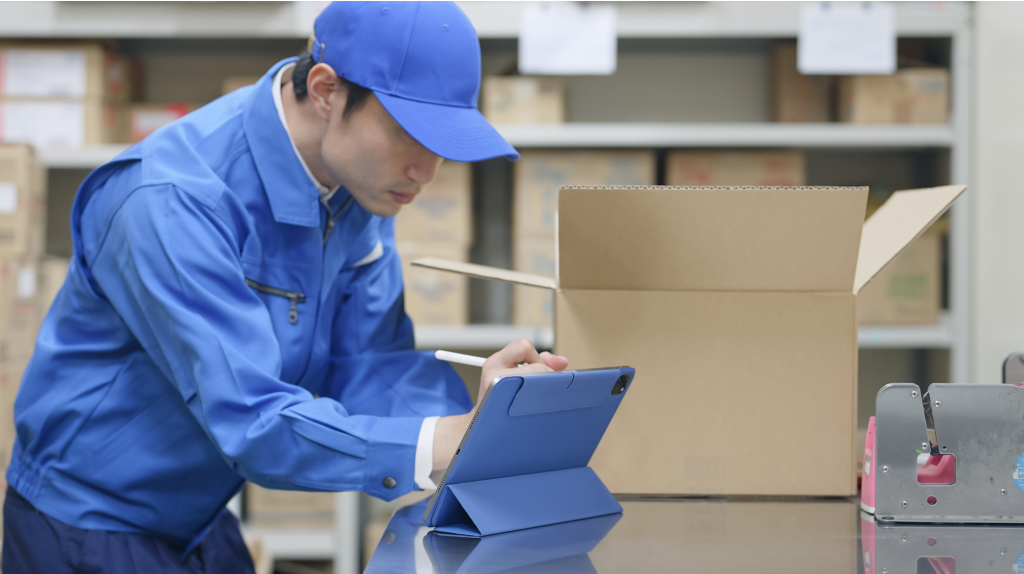
入荷検品は、単なる作業ではなく、在庫管理においてる重要な役割を果たします。入荷検品をまだ行っていない企業は、以下のメリットを理解した上で、入荷検品の導入を検討することをおすすめします。
在庫のズレの防止
入荷検品を適切に行うことで、発注した数量と実際に届いた数量を突合でき、在庫の過不足を未然に防ぐことができます。
例えば、入荷時に部品納入数が異なることに気づかず、製造時に発覚すると、材料の欠品が生産ラインの停止につながる場合があります。また、理論在庫と実在庫のズレが大きくなると、過剰在庫や欠品に繋がり、棚卸工数も増えてしまいます。欠品は納期遅延や信用低下、過剰在庫はキャッシュフローの悪化に繋がります。
誤出荷の防止
入荷検品でしっかりと製品をチェックすることで、最終的には誤出荷を減らすことに繋がります。仕入先が誤った品物を納入する可能性はゼロではありません。入荷検品時に誤納入に気づかず、製造や出荷に回してしまうと、誤出荷となってしまいます。誤出荷が発生すると、返品や再製作・再送などのコストが発生する上に、企業としての信用問題にも関わります。
顧客の信頼獲得
適切な入荷検品は、顧客からの信頼を得るためにも不可欠です。前述の欠品や誤出荷を防ぐことで、顧客に対して一貫した品質と信頼性を示すことができます。
入荷検品の具体的な手順
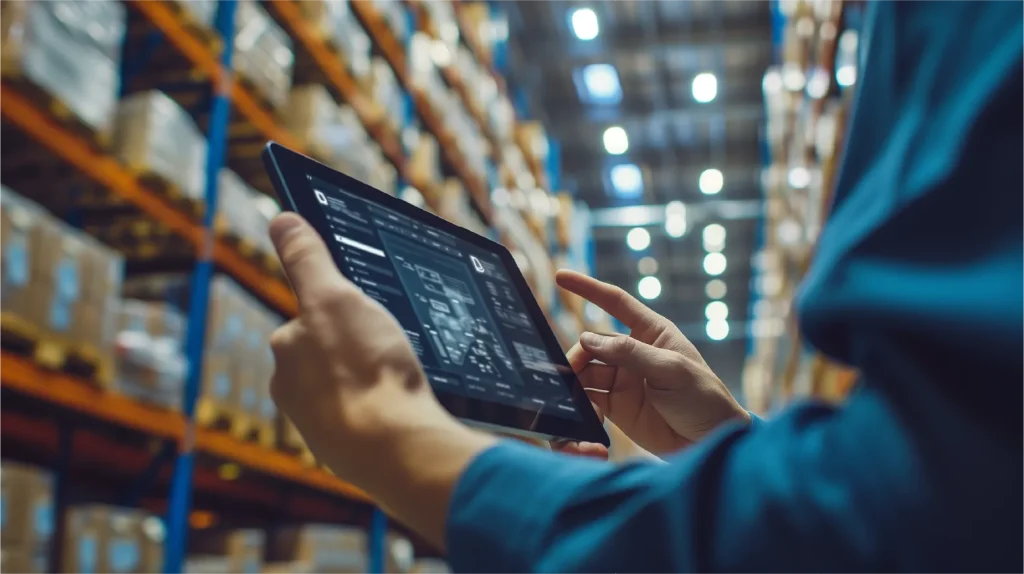
入荷検品の手順は企業や業界によって異なる場合がありますが、大きく分けると手作業とITツールを活用する方法に分けられます。
それぞれの方法にはメリットとデメリットがあり、状況に応じて最適な方法を選択することが重要です。
手作業による入荷検品
手作業による入荷検品では、作業者が目視や手作業で数量や品質を確認します。コストが掛からないため、どのような企業でもすぐに取り入れられる方法です。しかし、作業者のスキルや経験に依存するため、人為的なミスが発生しやすく、検品精度にばらつきが出る可能性があります。
属人的になりやすい手作業の入荷検品の代表例は、類似品の受け入れです。品番が1桁しか違わず、外観もほぼ同じ製品の入荷検品などになると、類似品の存在を知らない担当者が思い込みで異品を受け入れてしまうリスクがあります。
また、検品作業に多くの時間と労力を要するため、大量の入荷を処理する際には担当者への負荷が大きくなります。
ITツールを活用する入荷検品
入荷検品に、バーコードやQRコード、RFIDなどのITツールを使用することで、検品作業のスピード向上やヒューマンエラーの削減が可能です。さらに、デジタルデータとして記録されるため、検品履歴を簡単に管理・分析することが可能です。この手法は初期導入コストがかかるものの、長期的には大幅なコスト削減と効率化が期待できます。
入荷検品でよくある課題と原因
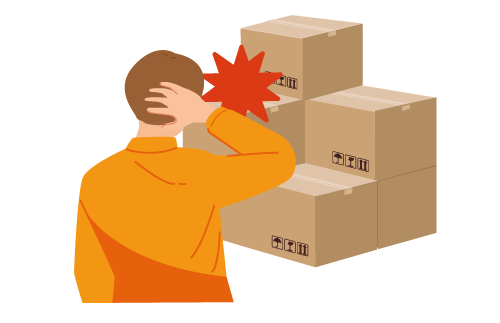
入荷検品を実施している企業の中で、よくある課題は大きく2通りあります。これらの課題に対する原因を把握し、適切な対策を講じることが重要です。
目視確認のミスがゼロにならない
入荷検品の作業の多くで目視確認を行っていると、どうしても人為的なミスが発生しやすくなります。特に、製品の種類や数量が多い場合、作業者の集中力が持続しにくく、ミスが発生する確率が高まります。特に、外観や品番が似ている入荷品が多い場合、見間違いやカウントミスが起こりやすくなります。これらのミスを防ぐためには、作業者のスキル向上や二重確認のプロセスを導入する必要がありますが、それでも人為的ミスをゼロにするのは難しいといえます。
入荷品が見つからない
現場で入荷品が見つからないというケースも頻繁に起こります。これは、仕入先の出荷ミスや、輸送中の紛失、もしくは倉庫内での管理ミスが原因となることが多いです。
このような問題が発生すると、在庫数が合わなくなり、以降の生産や出荷に支障をきたす可能性があります。仕入先が納入済みにも関わらず入荷品が見つからなくなる場合は、その日の入荷検品リストなどを用い、漏れなく検品する工夫が必要です。仕入先の納品漏れが多い場合は、仕入先とのコミュニケーションや輸送中の追跡を強化することが求められます。
入荷検品の改善方法:在庫管理システムとIoTツール
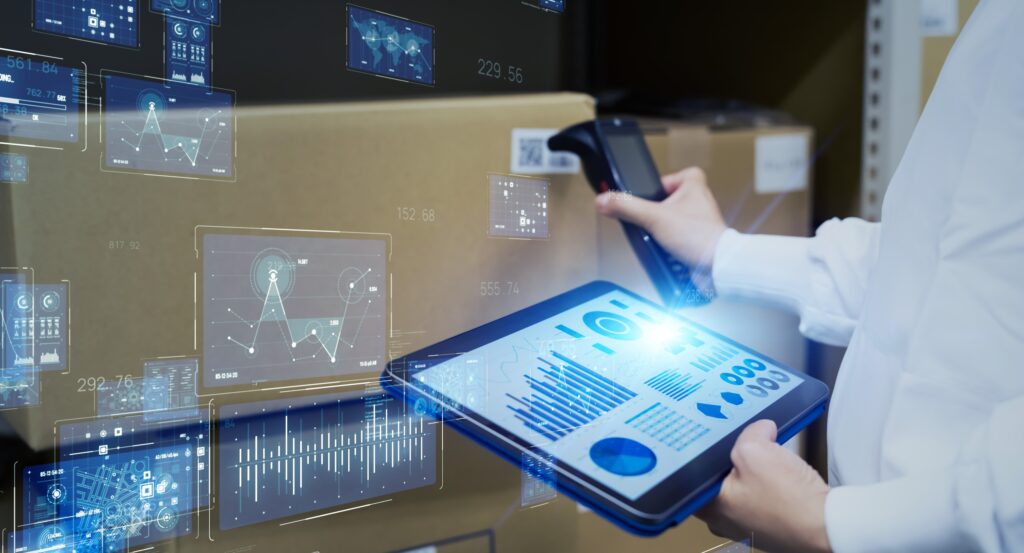
入荷検品の精度と効率を向上させるためには、在庫管理システムと連携し、現場で使用できるIoTツールの導入が効果的です。IoTツールの具体例としては、QRコードやバーコードをスキャンできるハンディーターミナルがあります。このようなIoTツールを活用することで、ヒューマンエラーの削減や作業のスピードアップを図ることができます。
バーコード管理の仕組み
バーコードを用いたハンディ端末での管理では、品番や品名などの製品データが入ったコードを読み取り、在庫管理システムのデータベースに入荷情報を記録します。現場でスキャンすると即座に在庫計上されるため、リアルタイムな在庫管理に繋がります。さらに、異常が検出された場合には即時にアラートが発生し、担当者が迅速に対応することができるため、経験が浅い入荷担当者も簡単にリスクの早期発見と対策が可能です。
このような仕組みを活用することで、数量の確認や品目の特定が迅速かつ正確に行われ、手作業によるミスが大幅に削減されます。また、ロット情報もバーコードで管理することで、入荷から出荷までのトレーサビリティを確保することができる点もメリットといえます。
バーコード管理は低コストで導入できる
バーコード管理は、RFIDタグなどと比べると低コストで導入できるソリューションです。バーコードスキャナーやラベルプリンターなどの機器は手頃な価格で入手可能であり、小規模な倉庫から大規模な物流センターまで幅広く対応できます。まずは小規模なプロジェクトから始めて、徐々に横展開していくと導入リスクを抑えられます。
システムを活用した入荷検品方法
入荷品の種類によって、バーコード管理での入荷方法は異なります。
- バーコードが貼付・印字された入荷品:ハンディ端末で読み取るだけで入荷処理
- バーコードがない入荷品:在庫管理システムから印刷した入荷一覧表に印字されたコードを読み取り入荷処理
バーコードが印刷されていない購入品や加工品の場合、入荷一覧表を印刷してスキャンする運用になることが一般的です。目視確認がゼロにできないというデメリットはありますが、ハンディ端末ですぐに在庫管理システム上に在庫計上できたり、不良数を登録して検査データを蓄積できたりと、在庫情報を管理する上でのメリットは大きいといえます。
また、仕入先への発注機能がある在庫管理システムの中には、仕入先宛の発注書にバーコード付きの現品票も印刷できるものもあります。仕入先にこの現品票を使うよう依頼すれば、もともとバーコードがない品物も、現品票のバーコードからスキャンできるようになります。
入荷検品に在庫管理システムを導入した事例
在庫管理システムを導入した企業のうち、金属加工業のある企業様は、従来の手作業で行っていた原材料の入荷検品をデジタル化することで、年間200時間もの工数を削減し、ミス防止や在庫の見える化を実現しました。
入荷検品や入庫処理にかかる時間を大幅に削減し、在庫数をリアルタイムで確認できるようになったことで、顧客対応もスムーズになりました。さらに、リアルタイムの在庫データを基にした効率的な生産計画が可能となり、全体の業務効率が飛躍的に改善されました。
こちらの企業では、バーコードのない入荷品には、入荷検品後にバーコード付きラベルを貼る運用を導入され、漏れなく受入検査をされています。その後、製造現場に材料を持ち出す際も、バーコードで鋼種を確認できるので、類似品の取り違え防止にも繋がりました。
詳細はこちら:
手入力の手間をなくし年間200時間以上の工数削減!アナログ管理特有のヒューマンエラーも大幅削減
このような事例は、入荷検品のデジタル化がもたらす効果を示す良い例であり、多くの企業が参考にすべき成功モデルといえます。
22種類の生産管理システムをランキングで比較
初期費用相場や選び方のポイントをチェック
生産管理システムをそれぞれの特徴や初期費用相場などで比較したい場合は、「生産管理システムランキング」も是非ご覧ください。生産管理システムは、自社の製品・生産方式・企業規模などに適したものを導入しないと、得られるメリットが限定されてしまいます。事前適合性チェックや生産管理システムを選ぶ前に押さえておきたいポイントも解説していますので、製品選びの参考にしてみてください。