誤出荷を防ぐ!よくあるミスと原因、対策を解説 誤出荷ゼロの成功事例も紹介
公開日:2024年09月12日
最終更新日:2024年09月26日
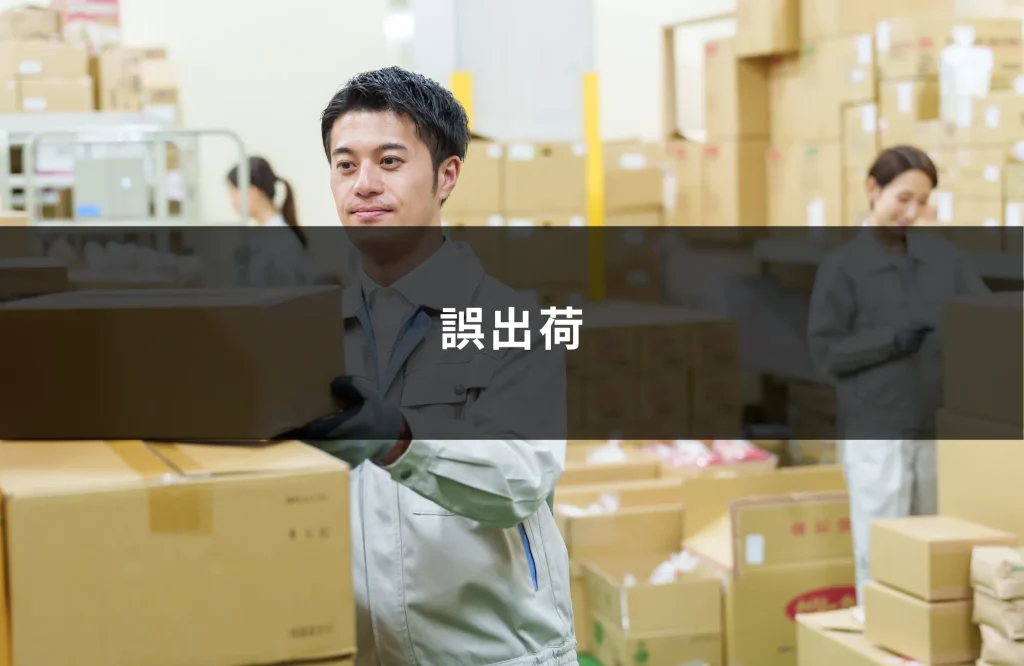
誤出荷は、製造業における大きな課題の一つです。ピッキングミスを始め、異なる製品の出荷や納品書の入れ間違い、数量のミスなど、誤出荷の原因はさまざまです。これらのミスは、顧客からの信用低下やコスト増大、さらには在庫過多や欠品を引き起こす可能性があります。
誤出荷の再発防止としてよく行われるのが、ダブルチェックです。もちろん、二重に確認することでミスは減らせますが、ヒューマンエラーをゼロにすることはできません。本記事では、誤出荷の種類とその影響、そして具体的かつ効果的な防止対策について解説します。最後には「誤出荷ゼロ」を実現した企業事例も紹介します。
誤出荷とは:よくある誤出荷は4種類
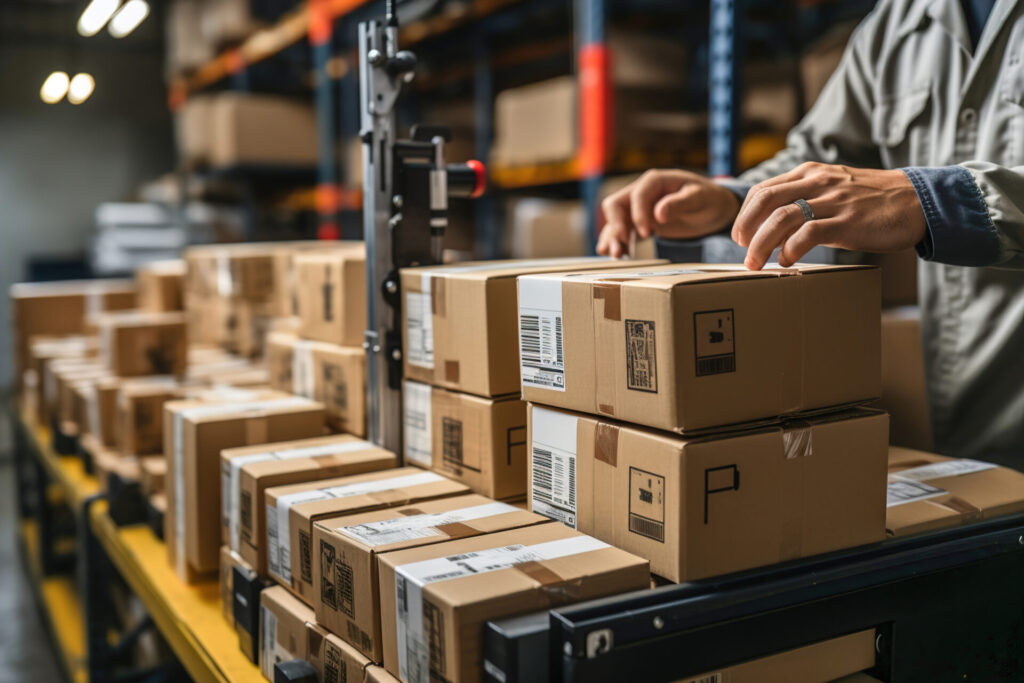
誤出荷は、企業にとって重大な問題となり得るミスの一つであり、顧客との信頼関係に大きな影響を与えることがあります。誤出荷の中でも特に頻繁に発生する4つの種類について、それぞれの特徴と原因を詳しく解説します。
異なる製品の出荷
誤って異なる製品が出荷されるケースは、製造業でよく見られるミスの一つです。この種の誤出荷は、通常、ピッキング作業や出荷指示の確認不足から生じます。具体的には、類似品番を誤ってピッキングしてしまう、外観が似ている製品を思い込みで誤出荷してしまうなどの事例があります。
納品書の入れ間違い
注文内容と異なる納品書を同梱してしまうことも、誤出荷の一種です。特に、納品書が2社でテレコになってしまうと、双方の販売単価が知られてしまうリスクとなります。
このミスは、納品書の確認作業が不十分な場合に発生します。誤った納品書は、顧客に混乱を招き、場合によっては不正確な在庫管理や支払いトラブルを引き起こす原因となるため、十分な注意が必要です。
数量の間違い
発注数量と異なる数の製品が出荷されるミスも、よくある誤出荷の一つです。納品書や出荷指示書の見間違えや、手作業での数え間違いが原因となることが多く、ヒューマンエラーの一種と言えます。
テレコ出荷
テレコ出荷とは、注文内容が異なる二つの顧客に対して、互いの商品が誤って発送されてしまうミスのことです。例えば、A社に送るべき商品がB社に送られ、B社に送るべき商品がA社に送られるといったケースです。このようなミスは、特に複数の注文を同時に処理する際や、出荷手配の段階で起こりやすいミスです。
代表的な例は、類似製品のピッキングを同時に行い、テレコで梱包してしまうケースです。他にも、梱包後に送り状をテレコに貼ってしまう事例もあります。
誤出荷が与える影響
誤出荷は、顧客との信頼関係に大きな影響を与えるだけでなく、返品や再発送によるコストの増加、在庫差異の発生による在庫過多や欠品、さらに場合によっては企業情報の漏洩につながるリスクもあります。これらの影響を理解し、対策を講じることが重要です。
顧客からの信用低下
誤出荷は、顧客との信頼関係を大きく揺るがします。顧客は企業の管理体制に疑念を抱き、今後の取引を見直す可能性があります。
誤出荷が繰り返されると、顧客が他社へ流れるリスクが高まり、企業の売上や市場シェアに悪影響を与えることになります。また、信用低下は一度起きると回復が難しく、企業ブランドの価値も損なわれるため、迅速かつ効果的な対応が求められます。
返品・再送などのコスト発生
誤出荷が発生すると、その後処理に多大なコストがかかります。返品された商品の再梱包や再配送には、直接的な費用が発生します。
また、返品商品の検品や再処理、場合によっては廃棄にかかるコストも無視できません。これらのコストは、企業の利益を直接的に圧迫し、経営効率を低下させる要因となります。
これらの対応には時間とリソースが必要であり、本来の業務に影響を及ぼすことも避けられません。結果として、企業全体の運営に負の影響を与える可能性があります。
在庫差異による在庫過多・欠品
誤出荷が原因で発生する在庫差異は、在庫過多や欠品といった問題を引き起こします。誤って出荷された商品の在庫は過少となり、本来必要な商品が不足することで欠品が発生します。そのため、顧客のニーズに応えられなくなる事態が起こります。
一方で、誤出荷後に返品された製品の数量を在庫管理表に反映しないと、在庫過多を引き起こします。例えば、在庫が100個のときに30個が返品されると、実在庫は130個になります。しかし、在庫管理表を100個のまま更新し忘れると、返品された30個分を加味せずに発注してしまい、想定より過剰在庫を抱えることになります。
在庫過多は保管スペースを圧迫し、保管コストの増大につながるだけでなく、製品の劣化リスクも高まります。これらの在庫管理の不備は、効率的な生産と流通を妨げ、企業の収益性を低下させる大きな要因となります。
テレコ出荷による企業情報流出
テレコ出荷が発生すると、単なる誤配送の問題にとどまらず、企業の機密情報が意図せずして漏洩するリスクが大きくなります。
特に、納品書をテレコで出荷してしまうと、2社に他社に対する販売価格が知られることとなります。誤配送によって顧客情報が流出した場合、法的な問題に発展するリスクも考えられます。
テレコ出荷による情報流出は、企業の存続に関わる重大なリスクであり、厳重な対策が求められます。
誤出荷の主な原因
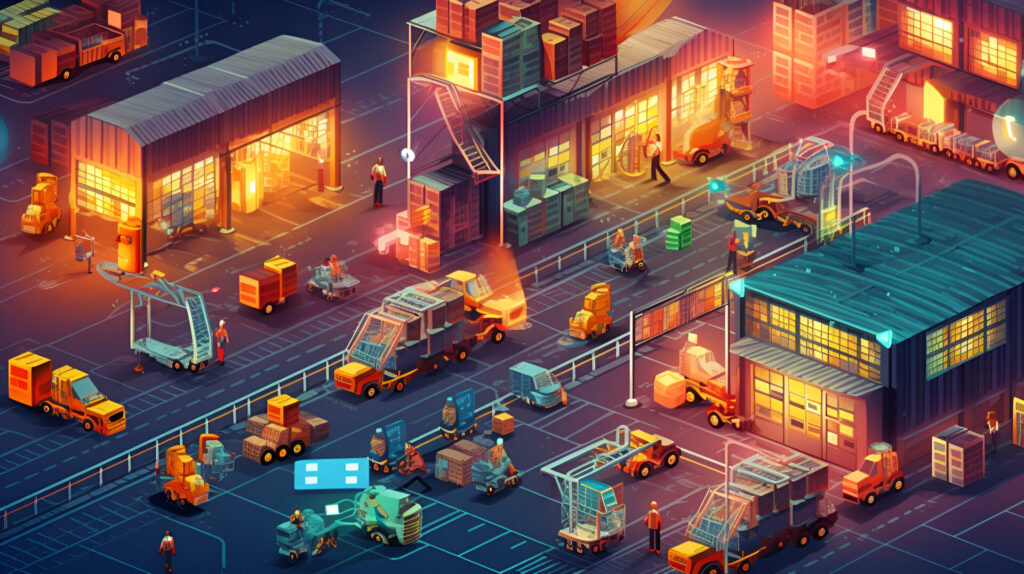
誤出荷の原因を明確に理解し、対策を講じることが、誤出荷を未然に防ぐための鍵となります。以下に、誤出荷の主な原因を発生段階別に解説します。
ピッキングミス
ピッキングミスは、誤出荷の中でも頻繁に発生する原因です。
- 倉庫内での製品の取り間違い(類似品など)
- ピッキング数量の誤認
- 入荷時点での選別ミス(異なる製品ラベル貼付など)
特に、外観や品番が似ている製品が隣接して保管されている場合や、急いで作業を行う状況では、ピッキングミスが起こりやすくなります。また、目視中心でのピッキング作業は、ヒューマンエラーをゼロにするのが難しいといえます。
出荷準備中のミス
ピッキング後の出荷準備中にも、誤出荷の原因となるミスが発生する可能性があります。
- ラベルの貼り間違い
- 梱包作業中の製品の入れ間違い
- 出荷前検品の不足、もしくは未実施
特に、急ぎの出荷対応や作業環境が混雑している場合、これらのミスが発生しやすくなります。また、企業によってはピッキング後の出荷前検品を行っておらず、チェック体制が不十分なケースもあります。
出荷手配中のミス
出荷手配の段階で発生する誤出荷の主な原因は、以下のとおりです。
- 出荷先情報の入力ミス
- 複数の出荷品のテレコ手配
これらのミスが発生すると、間違った場所に製品が送られ、結果として顧客の期待に応えられない状況を引き起こします。特に、繁忙期や多品種少量生産の現場では、こうしたミスが発生しやすく、出荷手配時の確認不足が大きなリスクとなります。
システムトラブル
在庫管理システムや出荷管理システムのトラブルも、誤出荷を引き起こす大きな要因です。システムが正確な情報を提供できなかったり、システムダウンによって手作業での対応を余儀なくされた場合、ミスが発生するリスクが高まります。
特に、システムの更新やメンテナンスが不十分であると、誤った情報に基づいた出荷が行われる可能性があります。
物流トラブル
物流業者との連携不備や配送中のトラブルも、誤出荷の原因となります。
- 配送先の間違い
- 輸送中の破損
- 配送希望日の遅延
また、天候や交通状況によって配送が遅延し、急ぎの対応が求められる際に、誤出荷が発生するリスクが高まります。
誤出荷を防ぐための対策方法
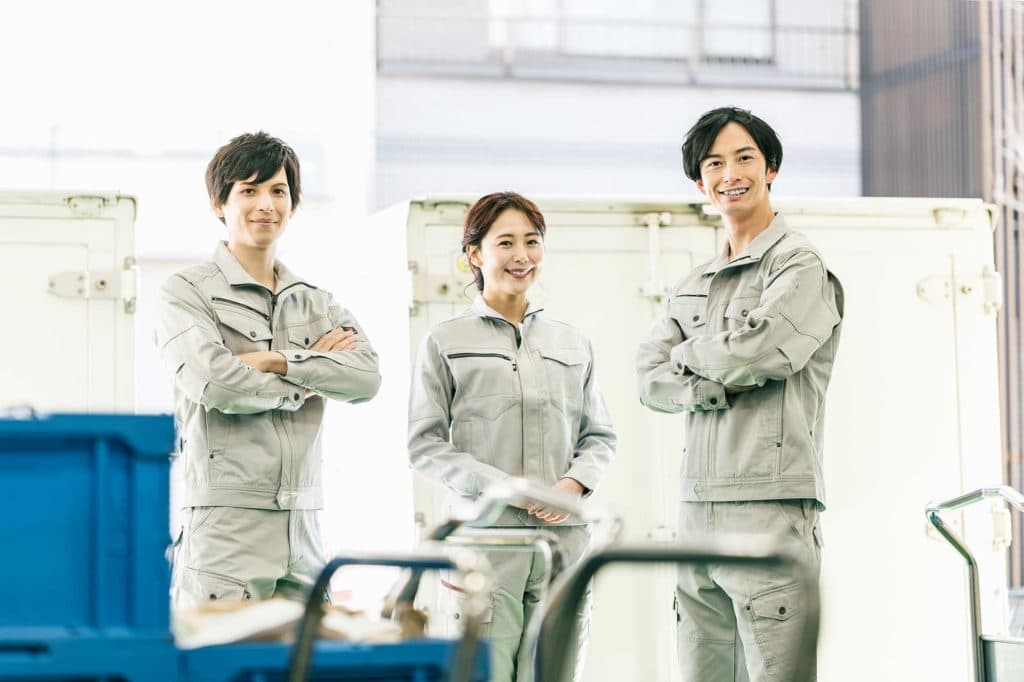
誤出荷を未然に防ぐためには、組織全体での徹底した対策が不可欠です。以下に、具体的な防止策を紹介します。これらの対策を実施することで、誤出荷のリスクを大幅に軽減し、顧客満足度の向上とコスト削減に寄与することができます。
なぜなぜ分析で原因分析
なぜなぜ分析は、問題の根本原因を特定するための手法です。製品の不良発生時などに活用されるケースが多いですが、誤出荷の防止においても活用できます。
なぜ誤出荷が発生したのかを5回程度繰り返し問いかけることで、表面的な原因からより深い根本原因(真因)にたどり着くことができます。これにより、誤出荷の発生原因を明確にし、適切な対策を講じることが可能になります。
【例】新人によるピッキングミスが発生した場合
1回目:なぜ、ピッキングミスが発生した?→類似品番を見間違えた
2回目:なぜ、類似品番を見間違えた?→類似品があることを知らず、思い込みでピッキングしてしまった
3回目:なぜ、類似品があることを知らなかった?→ピッキング指導時に教えられなかった
4回目:なぜ、ピッキング指導時に類似品について教えられなかった?→類似品が多く、すべて教えきれない
5回目:なぜ、類似品について教えきれない?→類似品の把握は経験で覚えていく必要があり、一度に把握しきれない
<真因>経験則に頼るピッキング
<対策>バーコード管理などの導入により、ピッキングミスを自動検知できる仕組みの導入
上記のような分析の結果を全員で共有し、具体的な改善策を現場に適用することで、誤出荷の再発を防止できます。
整理整頓の徹底
常に整理整頓が行き届いた職場環境を維持し、作業に集中できる環境を作ることも重要です。整理整頓によって作業スペースを十分に確保することで、ピッキングや検品などの作業効率が上がり、ヒューマンエラーも減らすことができます。具体的には、使用する道具や製品の配置を明確にし、常に決められた場所に戻す習慣を徹底します。作業区域の定期的な清掃や点検も効果的です。
作業環境の改善
整理整頓だけでなく、以下のような作業環境全体の整備も、誤出荷の防止に効果的です。
- 作業場の照明を明るく保つ作業台や通路のスペースを広く確保する
- 空調設備や空調服で快適な気温を保つ
特に、製造業の現場や倉庫は、気温管理が難しい場合があります。なるべく作業員が疲れにくいように、快適な作業環境を提供することも重要です。
従業員の教育・訓練
従業員の教育や研修を通じて、誤出荷のリスクやその防止策を全員に周知徹底することも大切です。
また、誤出荷が発生した際には、関係者全員でその原因を共有し、再発防止に向けた対策を検討します。再発防止策として新しい手順やシステムを導入する際には、事前に十分な教育と訓練を行い、全員が適切に対応できるようにすることが求められます。
ダブルチェック
一人が行った作業をもう一人がダブルチェックすることで、見落としやミスを防ぎます。出荷検品を行っていない場合は、出荷検品を別担当者が行うようにすることで二重確認ができるようになります。
特に、製品の種類や数量、納品書の内容を確認する際にダブルチェックを行うことで、誤出荷のリスクを大幅に減らすことができます。ダブルチェックの際は、確認手順を明確にし、全員が同じ基準でチェックを行うようにすることが重要です。
ただし、ダブルチェックでも人的ミスをゼロにすることは難しいと理解しておく必要があります。稀に、誤出荷対策としてダブルチェックを行っていたものの、ミスがなくならず、トリプルチェックなどを行うケースがあります。確認回数を増やしても、人間は慣れや思い込みによるミスはゼロにはできません。
ダブルチェックをしてもミスがなくならない、もしくはダブルチェックの工数を増やすのが難しい場合は、照合システムなどの導入を検討することをおすすめします。
照合システムの導入
品番などの照合システムの導入は、目視確認や二重チェックでも防げないヒューマンエラーを防止する効果があります。バーコードやQRコードを利用して製品情報を正確に管理し、出荷時に自動的に照合することで、異なる製品や数量の間違いを防止します。類似品番チェックなど、人の目では100%正確に確認できない作業でも、システム活用で瞬時に照合できます。
また、システムにより、出荷情報がリアルタイムで更新されるため、在庫管理や出荷状況の確認が容易になります。照合システムは、作業の効率化とミスの防止を同時に実現する優れたツールといえます。
在庫管理システムとバーコード管理で誤出荷ゼロに
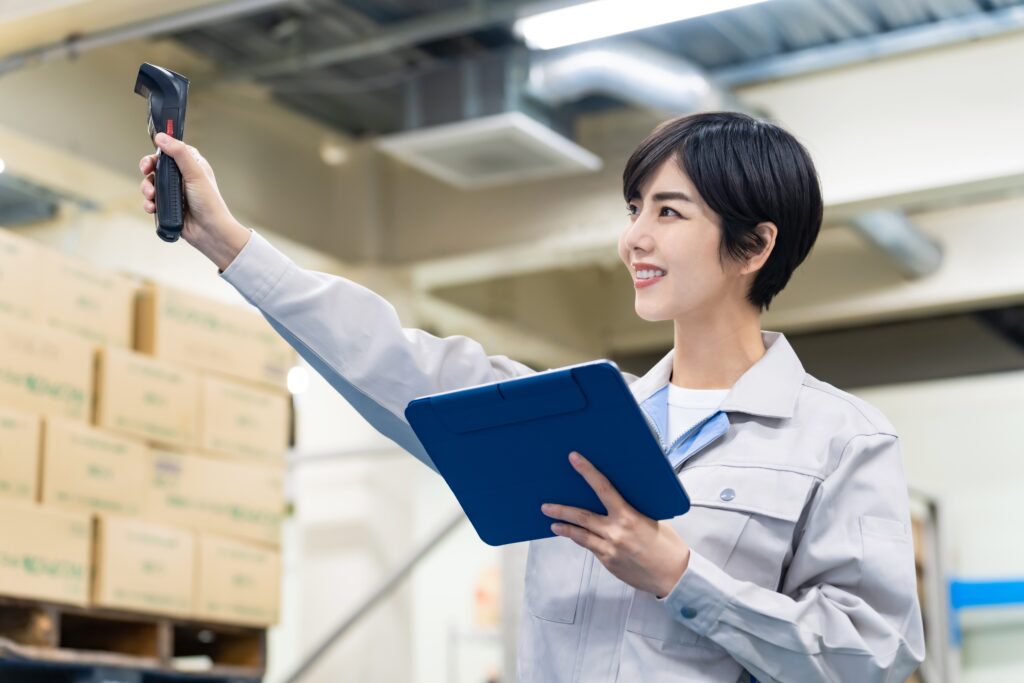
ヒューマンエラーによる誤出荷を防ぐためには、在庫管理システムとバーコード管理の導入が非常に効果的です。これらのツールを活用することで、ピッキングや出荷業務の精度と効率が大幅に向上します。特に、ヒューマンエラーによる誤出荷のリスクを大幅に軽減できます。
バーコード管理のメリット
バーコード管理では、QRコードやバーコードをスキャンすることで、コードに登録された製品情報を読み取り、品番やロットの照合が可能です。品番や出荷先、数量の誤りがある場合にアラートを表示する機能を持つシステムもあり、誤出荷を未然に防げます。また、手動入力の必要がなくなるため、入力ミスによる誤出荷が発生するリスクも軽減します。
バーコード管理により、出荷作業がスピーディーかつ正確に行えるため、作業効率が向上し、結果として顧客満足度の向上にもつながります。
バーコード管理による「誤出荷ゼロ」の成功事例はこちら:
リアルタイム在庫管理の重要性
在庫管理システムを導入することで、在庫の状況がリアルタイムで更新され、在庫不足や過剰在庫による誤出荷のリスクを低減できます。
また、誤出荷が起きてしまった際も、在庫管理システムによるリアルタイム管理が役立ちます。例えば、客先から異品納入の連絡を受けた際、出荷履歴や残りの在庫数を確認することで、テレコの可能性があるかを迅速に確認できます。また、客先からの返送品があった際もすぐに在庫情報を更新することで、在庫差異の発生を防止できます。
22種類の生産管理システムをランキングで比較
初期費用相場や選び方のポイントをチェック
生産管理システムをそれぞれの特徴や初期費用相場などで比較したい場合は、「生産管理システムランキング」も是非ご覧ください。生産管理システムは、自社の製品・生産方式・企業規模などに適したものを導入しないと、得られるメリットが限定されてしまいます。事前適合性チェックや生産管理システムを選ぶ前に押さえておきたいポイントも解説していますので、製品選びの参考にしてみてください。