安全在庫とは?在庫最適化のメリットやリスク回避の方法、適正在庫との違いを解説
公開日:2024年04月16日
最終更新日:2024年09月26日
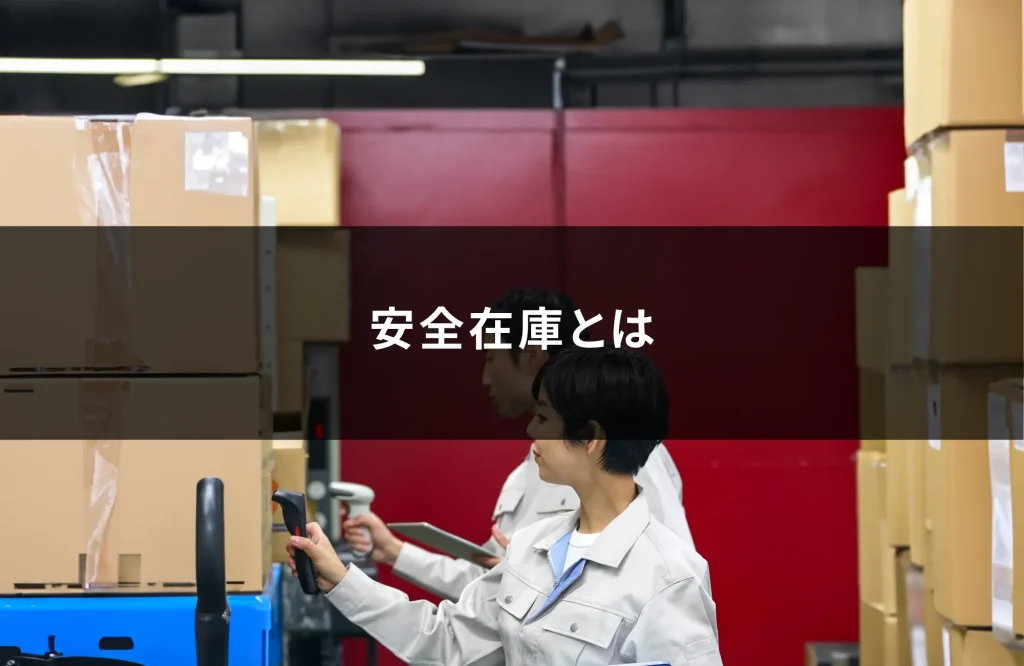
製造業の「安全在庫」の管理は、予期せぬ市場の変動や供給網の不安定さに対応し、業績を安定させるために必要不可欠です。この記事では、安全在庫の重要性から計算方法、そして効果的な管理技術まで、企業が直面するリスクを最小限に抑えつつ、効率的な在庫管理を実現するための戦略を紹介します。安全在庫の最適化を通じて、市場での競争力を高める参考にしていただけると幸いです。
安全在庫とは:役割と重要性
安全在庫とは、予測不能な需要変動や供給の遅延に対応するために最小限確保しておく在庫のことです。欠品を防ぎ、製品供給の安定性を保ちながら顧客満足度を高めるために、適切な安全在庫を保つことは重要です。安全在庫を持つことで、突発的な需要増加や予期せぬ供給の中断に対処し、生産や販売を続けることができます。
安全在庫の計算方法
安全在庫量の最も一般的な計算方法は、以下のとおりです。
安全在庫量 = 安全係数 × 平均使用量の標準偏差 × √(リードタイム+発注 or 製造間隔)
上記は、在庫の推移を一定のパターン(サイクル)と捉え、在庫水準を適正化する「在庫サイクル理論」に基づく計算式です。安全係数など、上記計算のために必要な項目の設定方法は、以下のとおりです。
①安全係数(安全在庫係数)を設定する
安全係数とは、予期せぬ需要変動や供給の遅れに対応するために設ける係数です。市場の変動性や過去のデータを分析し、「品切れ許容率(欠品リスクをどの程度まで許容するか)」を算出したあとに、安全係数に換算することで設定します。
品切れ許容率は、どれくらいの欠品を許容できるかによって変動します。たとえば、100回分の注文に対し、3回までの品切れなら許容できるなら、品切れ許容率は3%です。10回までの品切れを許容できるなら品切れ許容率は10%です。この品切れ許容率をもとに、安全係数を計算します。
安全係数はエクセルでも計算できますが、以下の表に当てはめることも換算可能です。
【品切れ許容率→安全係数への換算表】
品切れ許容率 | 安全係数 |
0.1% | 3.10 |
1% | 2.33 |
2% | 2.06 |
5% | 1.65 |
10% | 1.29 |
20% | 0.85 |
30% | 0.53 |
上記の通り、品切れ許容率が低い(=品切れをなるべく減らしたい)場合は、安全係数が反比例して高くなります。よって、安全係数が高ければ高いほど、より多くの安全在庫を持つことになります。 安全係数は業界によって異なりますが、一般的な水準は安全係数1.65(品切れ許容率5%)程度です。
②使用量の標準偏差を算出する
使用量の標準偏差を算出することで、需要の変動性を数値化します。過去の販売データや使用量の記録を基に、平均使用量からどの程度変動するかを計算し、安全在庫の算出に役立てます。
標準偏差の計算は、エクセルのSTDEV関数での計算がおすすめです。たとえば、月単位での安全在庫を求める場合は、毎月の使用数をエクセルにまとめ、「=STDEV.S(毎月の使用数)」という計算式を入れます
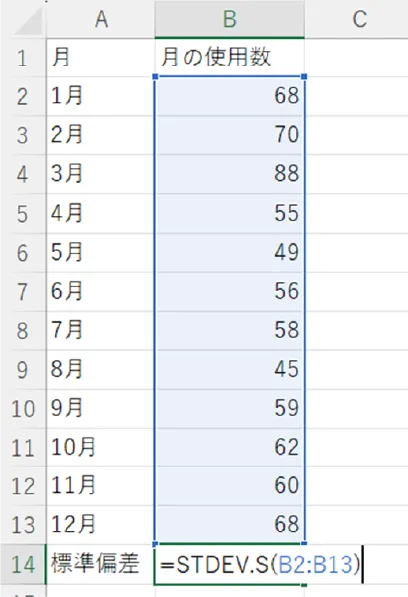
この数値が大きいほど、需要の予測が難しく、それだけ多くの安全在庫が必要になります。
※標準偏差のエクセル関数には、「STDEV.S」と「STDEV.P」があります。「STDEV.S」は、母集団の一部のデータを使用している際に使う関数です。長年使用している製品で、直近1~2年の使用量から標準偏差を出したいときなど、母集団データの一部から計算する際は「STDEV.S」を使用します。対して、「STDEV.P」は、母集団データがすべて揃っているときに使います。
③リードタイム+発注 or 製造間隔を設定する
リードタイムとは、商品を発注してから受け取るまでの時間です。たとえば、発注や製造から3日で届く部品は、リードタイム3日となります。安全在庫の計算には、さらに発注や製造の間隔も加味する必要があります。たとえば、毎週1回発注する製品の場合、発注間隔は7日となります。
※発注点管理など、発注が不定期な場合は、発注間隔は0日で計算してOK
安全在庫の計算をする際は、リードタイムと発注 or 製造間隔の和を√(平方根)で計算します。エクセルで計算する場合は、SQRT関数で求められます。
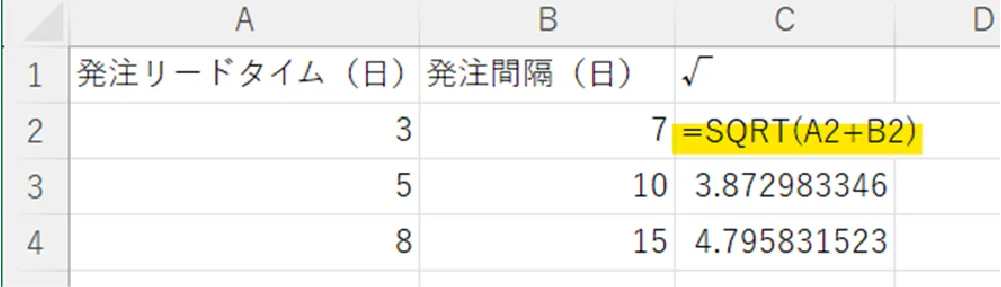
上記エクセルのように、リードタイムや発注・製造間隔が長くなると、「√(発注リードタイム+発注間隔)」の値も大きくなります。そのため、より多くの安全在庫を確保する必要があります。
計算式の例
安全在庫の計算式は、上記で得た安全係数、使用量の標準偏差、リードタイムを組み合わせて求めます。この式を用いて、具体的な安全在庫量を算出してみます。
計算式:
安全在庫量 = 安全係数 × 平均使用量の標準偏差 × √(リードタイム+発注 or 製造間隔)
製品例:
安全係数1.65(品切れ許容率5%)、平均使用量の標準偏差11.2(月の使用量60個前後)、発注リードタイム3日、発注間隔7日の製品
↓
安全在庫料=1.65x11.2x√(3+7)=58.3968【安全在庫58個】
適正在庫と安全在庫の違い
在庫管理について考える上で、安全在庫の他に、適正在庫という概念も重要になります。適正在庫とは、欠品リスクに備えるために最低限確保すべき安全在庫に加えて、最適な在庫量で日々の需給バランスを維持するためにさらに持つべき在庫を意味します。
適正在庫の計算方法は、企業によって異なります。よく使われており、かつ計算しやすい方法は以下のとおりです。
適正在庫=安全在庫+サイクル在庫
サイクル在庫とは、発注や製造してから次の発注・製造までに使用する在庫量の半数です。たとえば、2週間に1回のペースで100個発注する部品のサイクル在庫は、50個です。サイクル在庫で日々の製造を回しながら、いざというときに備えて安全在庫を確保しておくイメージです。
他にも、需要予測や過去の販売データ、市場動向などを基に適正在庫を計算する方法もあります。自社に合う方法で、在庫コストの適正化と顧客満足度向上のバランスを取れる適正在庫を設定することが重要です。
安全在庫と発注点の関係性
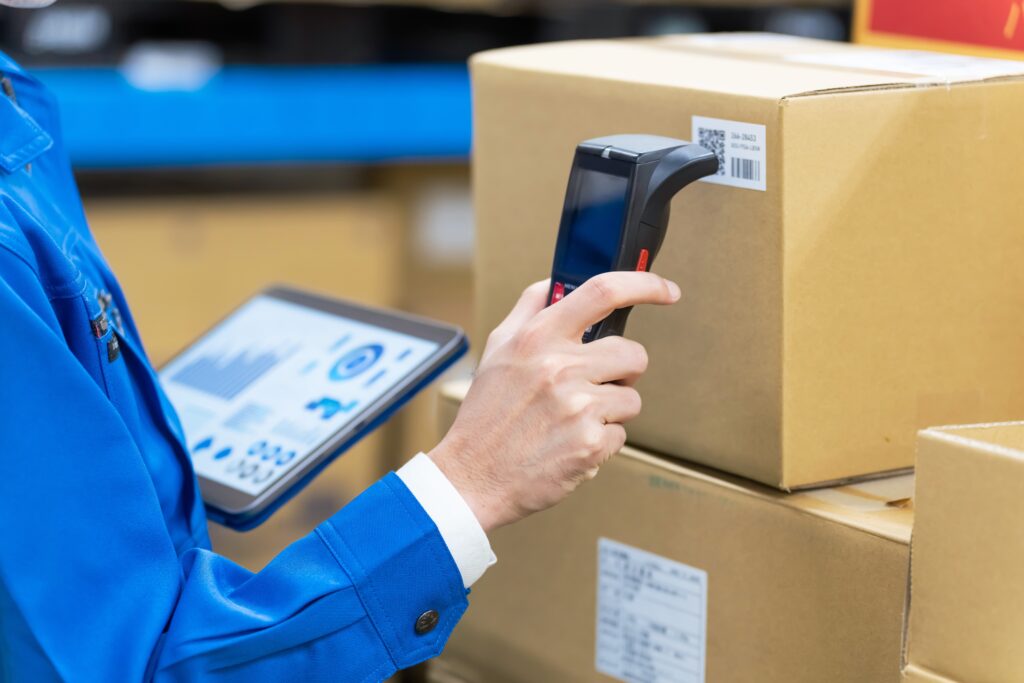
安全在庫を設定する上で、それが発注点設定にどのように影響するかを知っておく必要があります。発注点とは、在庫数が一定レベルに達した時に、新たな注文を出すべきタイミングを示します。つまり、安全在庫を切らないように在庫管理するうえで、発注点を適切に設定する必要があります。
また、安全在庫と発注点は静的な数字ではありません。市場状況の変化、仕入先の信頼性の変動、新製品の導入など、多くの外部要因により調整が必要になります。定期的なレビューを通じて、これらの数字を最適化し、在庫コストの削減とサービスレベルの維持を図ります。
安全在庫算出のメリットと目的
適切な安全在庫量を算出し、維持するメリットは、大きく分けて3点あります。
在庫過多の防止
安全在庫を保つよう管理することで、必要以上の在庫過多を防ぎます。過剰な在庫は資金を不必要に拘束し、保管コストや廃棄リスクを増加させるため、これを避けることは経営資源の有効活用につながります。
欠品の防止による販売機会の損失回避
安全在庫を適切に設定することで、予期せぬ需要増や供給の遅延に対応し、欠品を防ぎます。これにより、顧客満足度を維持し、販売機会の損失を最小限に抑えることができます。
キャッシュフローの改善
適切な安全在庫の管理は、在庫に関連するコストを最適化し、キャッシュフローを改善します。在庫を過剰に抱えることなく、必要な時に必要な量を確保することで、資金の効率的な運用が可能となります。
安全在庫算出の注意点
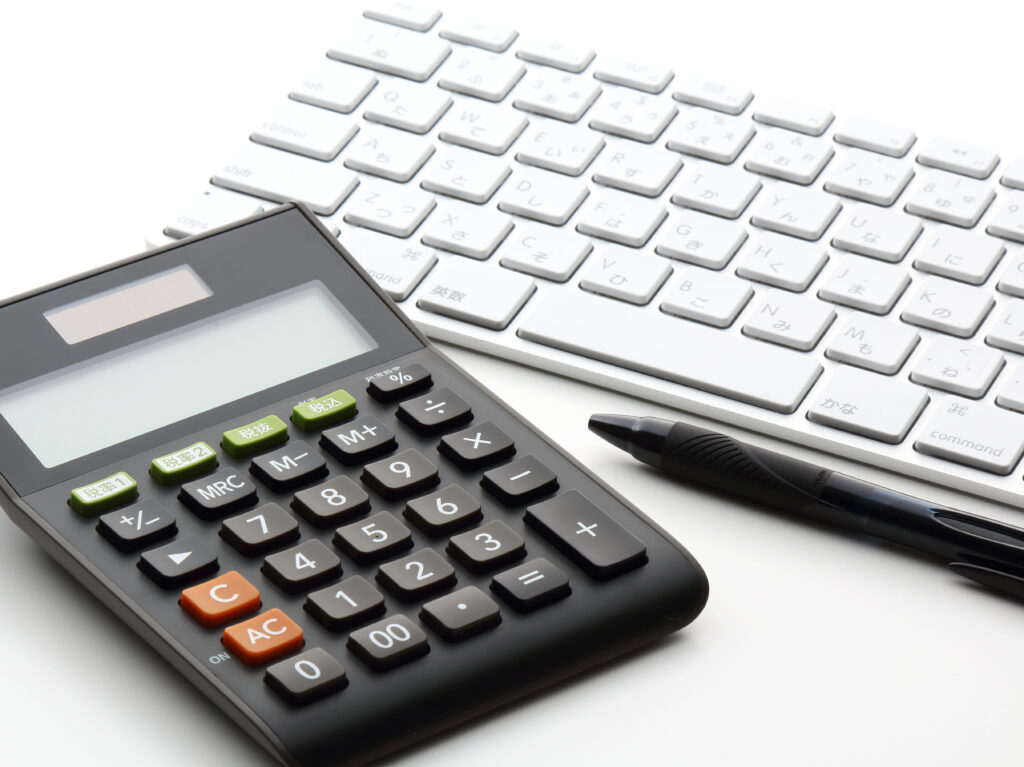
安全在庫を算出する際には、完全な欠品防止を保証するものではないこと、また、すべての商品や材料に対して安全在庫を設定することが適切でない点を理解しておく必要があります。
安全在庫による管理で、気をつけるべき点は以下のとおりです。
すべての欠品は防げない
安全在庫は、あくまで予期せぬ需要の変動や供給の遅れに対応するための保険のようなものです。しかし、極端な市場の変動や予測不可能な事態が発生した場合、安全在庫を持っていても欠品を完全に防ぐことはできません。このような状況を避けるためには、市場の動向を常に注視し、在庫戦略を柔軟に調整する必要があります。
安全在庫の設定に不向きな在庫品もある
すべての在庫品が安全在庫の設定に適しているわけではありません。例えば、季節商品や流行に左右されやすい商品、賞味期限が短い商品などは、安全在庫を設定することでかえって在庫過多に陥るリスクがあります。こうした在庫品に対しては、より精密な需要予測や迅速な在庫回転が求められます。
安全在庫を保つ具体的な管理方法
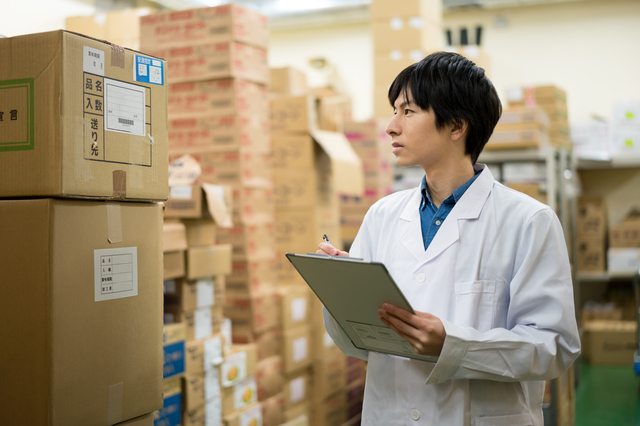
安全在庫を保つためには、在庫品目の詳細な分析・分類、リードタイムの考慮、在庫レベルの精確な設定などが大事です。これらの方法を駆使することで、生産性を高め、欠品リスクを低減させることができます。
在庫品目の分析と分類
安全在庫の管理においては、在庫品目の重要度や使用頻度に基づいて分析し、分類することが重要です。在庫の重要度合いを設定するのに便利な手法が、ABC分析です。在庫管理の優先度を決定し、在庫コストの削減と効率性の向上を図ることができます。
リードタイムの考慮
リードタイム、すなわち、発注や製造から受け取りまでの期間の正確な把握と考慮は、安全在庫レベルの設定において不可欠です。リードタイムの変動は供給不安定性の一因となるため、この期間を適切に管理し、予測することで、欠品や過剰在庫のリスクを最小限に抑えることができます。 たとえば、よく納期遅れを起こす仕入先への発注時は、リードタイムを長めに確保しておく必要があります。
在庫レベルの設定と調整
在庫レベルの設定には、過去のデータ分析、需給予測、そして安全在庫の計算が含まれます。これらの情報を基に設定された在庫レベルは、定期的に見直し、必要に応じて調整を行うことで、業務の効率化とコスト削減を実現します。
適切な安全在庫量を設定するには
安全在庫の設定には複数の条件が関係するため、適切な量を決めるのは容易ではありません。多くの企業は、不測の事態に備えるあまりに、過剰在庫になりやすい傾向にあります。また、需要の変動に伴い、安全在庫も設定し直す必要が出てくる場合もあります。安全在庫量の見直しや、より精緻な在庫管理が叶う在庫管理システムの活用などで、適切な安全在庫を決定しやすくなります。
需要状況に応じて定期的な見直し
市場の需要は常に変動しています。季節性、経済的要因、競合の動向など、多くの外部要因が需要に影響を与えるため、企業はこれらの変化に迅速に対応する必要があります。定期的な見直しを行うことで、企業は過剰在庫や在庫不足のリスクを減らし、必要な安全在庫量を確実に維持できます。
在庫管理システムの活用
在庫管理システムは、安全在庫量を設定し、維持するために非常に役立つツールです。在庫管理システムを使用することで、リアルタイムで在庫データを追跡し、分析することが可能になります。在庫レベルの自動調整や再発注ポイントの識別、需要予測などが可能なシステムもあります。
在庫管理システムの役割とメリット
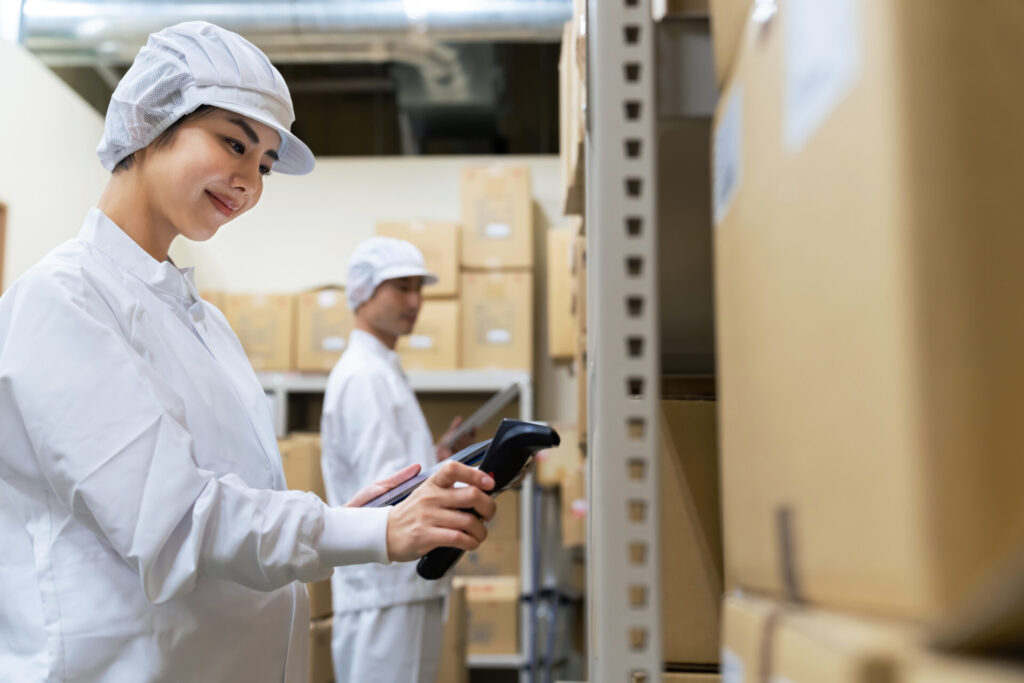
在庫管理システムのメリットは、安全在庫を適切に管理できるだけではありません。正確な在庫データ管理、リアルタイムでの在庫追跡、需要予測の精度向上など、在庫管理の自動化・最適化に役立ちます。
在庫管理システムの機能と特徴
在庫管理システムの主な機能は、以下のとおりです。これらの機能で、在庫レベルの最適化を実現できます。
- リアルタイムでの在庫追跡
- 発注
- 在庫分析
- 需要予測
安全在庫の設定には、今までの在庫の動きの分析も必要になります。在庫管理システムを利用していると、入出庫などのデータが自動的に蓄積されていくため、在庫分析や実績に基づく需要予測が効率的に行えます。また、紙やエクセルなどでは難しいリアルタイムでの在庫管理ができるため、正確な在庫データからの分析が可能となります。
また、ハンディターミナルなどでのバーコード管理を併用すると、より正確な在庫追跡が可能となり、時間とコストの節約にもつながります。
事例紹介:在庫管理改善の成功事例
在庫管理システムの導入によって、安全在庫の効率的な管理を実現した成功事例を2社、紹介します。
組立品の製造を行う株式会社イワサキ様は、在庫管理のシステム化に成功し、年間約100万円の在庫削減を実現しました。在庫圧縮に成功した理由は、在庫管理システムの活用によって在庫過多に気づけたためです。在庫管理システムで在庫をリアルタイムに見える化し、在庫分析を行ったところ、都度発注で済むにも関わらず安全在庫を持っていた品番や、発注点を高く設定していた品番を発見できました。導入後は、在庫管理の効率化だけでなく、現場と購買の双方が在庫状況をリアルタイムで確認できるようになりました
詳細:在庫管理のシステム化に成功!リアルタイムな在庫管理で年間100万円の在庫削減
冷凍食品の製造販売を行う香住食研株式会社様は、原料在庫管理システムによる発注点管理で、より安全在庫を保ちやすい体制を確立しました。システム導入前は紙やエクセルでの管理が中心で、ヒューマンエラーがなかなかなくならない状況でした。そのため、原料在庫の欠品などで製造を中断したり、納期遅れが発生したりすることがありました。在庫管理システムで発注点管理を始めたことで、設定した在庫数を下回ったらすぐにシステム上で確認できるようになりました。これにより、安全在庫を確保できるようになりました。
詳細:【原料在庫管理システム】毎日の原料在庫数の確認の手間を95%削減
22種類の生産管理システムをランキングで比較
初期費用相場や選び方のポイントをチェック
生産管理システムをそれぞれの特徴や初期費用相場などで比較したい場合は、「生産管理システムランキング」も是非ご覧ください。生産管理システムは、自社の製品・生産方式・企業規模などに適したものを導入しないと、得られるメリットが限定されてしまいます。事前適合性チェックや生産管理システムを選ぶ前に押さえておきたいポイントも解説していますので、製品選びの参考にしてみてください。