発注点管理の決め方~実践方法までわかりやすく解説 安全在庫や適正在庫との関係性も知る
公開日:2024年06月20日
最終更新日:2024年09月09日
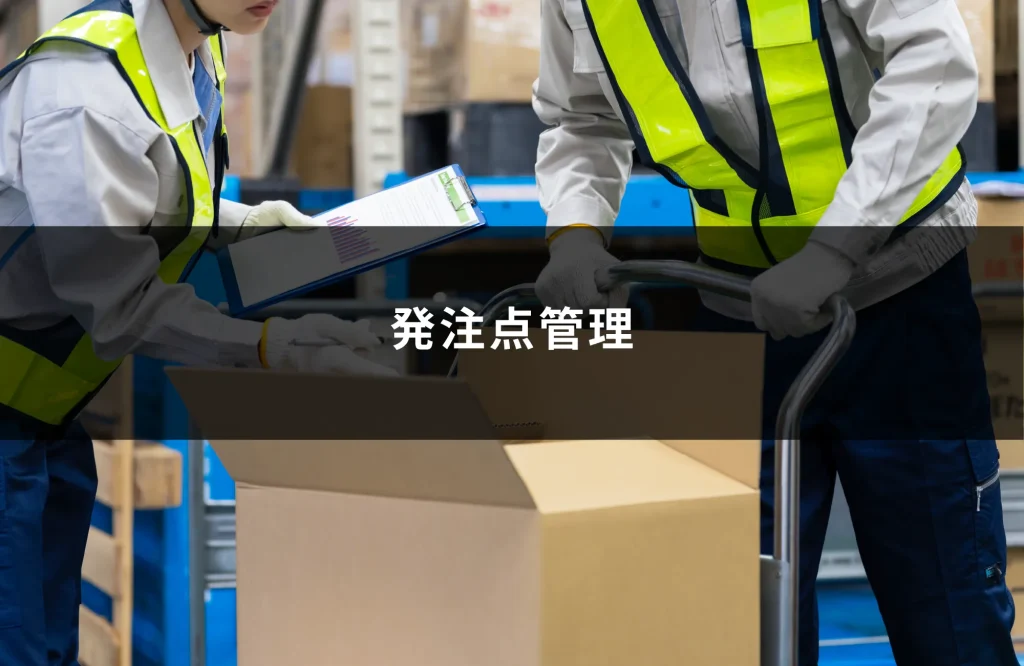
発注点管理は、製造業において適切な在庫管理と経営の効率化を目指す上で必要不可欠です。本記事では、発注点の基本概念から、重要性や目的、さらには効果的な管理方法や成功事例まで、幅広く解説します。安全在庫や適正在庫との関係性や、定量発注方式と定期発注方式の違い、リードタイムの考慮や在庫管理システムの導入手順まで、実践的なアプローチも紹介します。
製造業における発注点とは
製造業における発注点は、商品や部品の 発注が必要になる時点の数量を指します。「この製品は50個を切ったら発注する」という場合、この製品の発注点は50個といえます。これは製造プロセスにおいて、生産ラインが中断することなく必要な資材や原材料を確保するために、極めて重要な要素です。
安全在庫・適正在庫との違い・関係性
発注点の決定には、安全在庫や適正在庫などの概念を知り、それぞれの違いを理解することが重要です。
発注点 | 安全在庫 | 適正在庫 | |
どのような指標か | 一定を下回ったら発注する在庫水準 | 万が一に備えて、最低限確保しておく在庫 | 需要を満たすために保つべき最適な在庫 |
管理の目的 | 発注タイミングを決めるため | 不測の事態に備えるため | 在庫を過不足のない適正な状態に保つため |
安全在庫は、予期せぬ需要変動や調達遅延に備えて最低限確保される在庫です。安全在庫を確保することで、需要が急増した場合や仕入先の納品が遅れた場合でも対応でき、企業への信頼を高めることができます。よって、発注点を決める場合は、安全在庫を下回らないように気をつける必要があります。
適正在庫は、需要を満たすための最適な在庫レベルを示します。適正在庫を持つことで、在庫の過不足を防ぎ、生産や販売のスムーズな運営を可能にします。発注点の検討時は、なるべく適正在庫の維持ができる水準を目指せるのが理想です。
発注点管理の目的と重要性
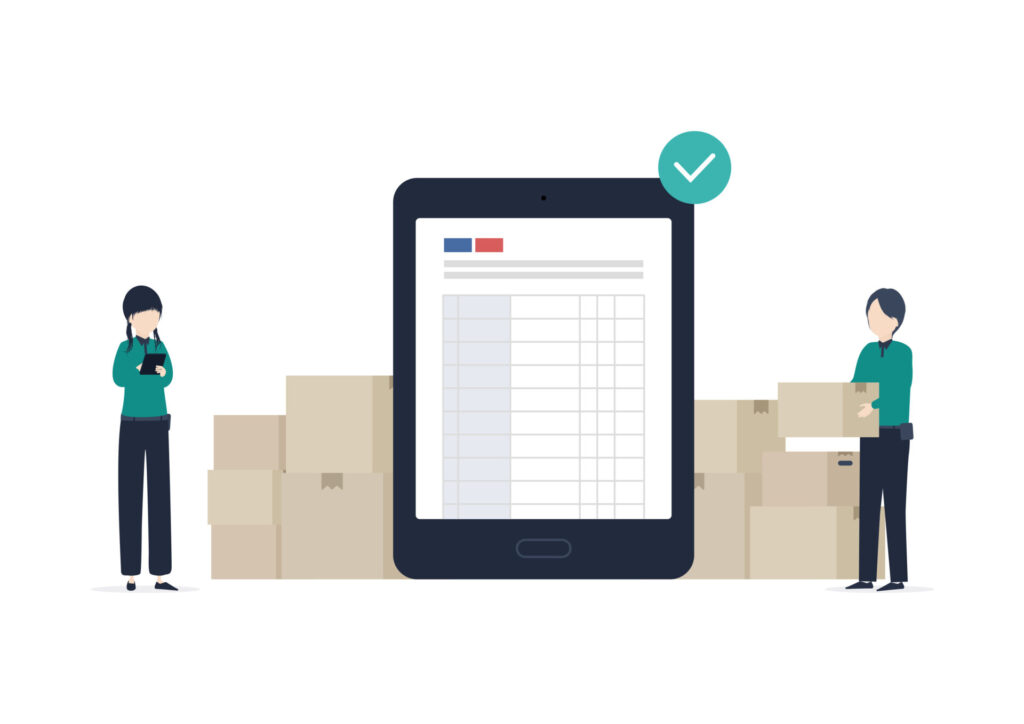
発注点管理は、必要な部品や原材料を適切なタイミングで発注し、生産ラインがスムーズに稼働するための重要なプロセスです。適切な発注点管理により、在庫が過剰になることなく、生産計画が円滑に進行し、生産性が向上します。
また、発注点という基準を決めることで、発注タイミングの判断が簡単になり、少ない手間で適正在庫を保つことができます。発注者の経験も必要ないため、発注業務の属人化解消にも繋がります。発注点管理は生産の効率性を高め、コストを最適化する上でも不可欠です。
効率的な発注点管理のメリット
効率的な発注点管理により、過剰在庫の防止だけでなく、生産ラインの停止や製品の欠品といったリスクを最小限に抑えることができます。また、適切な発注点の設定により、在庫コストを最適化し、キャッシュフローを改善することができます。さらに、需要変動に迅速に対応するための柔軟性を確保し、顧客満足度を高めることも可能です。
発注点管理の課題とリスク
発注点管理には、需要予測の不確実性や発注リードタイムの変動、在庫の持ち方の最適化など、さまざまな課題やリスクがあります。例えば、以下のような状況になると、在庫型や欠品になってしまいます。
<発注点管理がうまくいかない例>
- 需要が急増し、想定より早く在庫切れとなった
- 顧客の注文数が内示を下回り、在庫過多となってしまった
- 通常1週間で入荷する製品が、仕入先での欠品で納期が1ヶ月になってしまった
このように、不適切な発注点の設定や適切な情報の不足は、在庫の過剰や不足といった問題を引き起こす可能性があります。また、市場の変動や競合他社の動向に適切に対応できない場合、企業の競争力や利益に影響を及ぼす恐れがあります。
発注点の決定要素
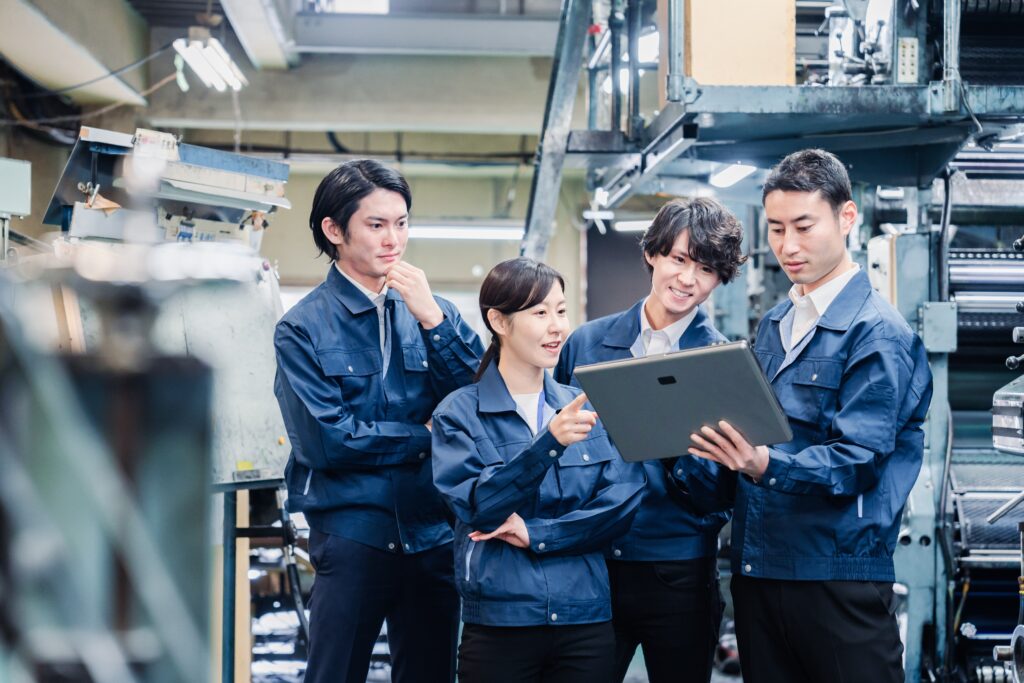
製造業における発注点の設定には、いくつかの要素が影響します。これらの要素を理解することは、効果的な在庫管理と生産計画のために不可欠です。
1日あたりの平均出荷量
製品の需要を理解するために、1日あたりの平均出荷量を把握することが重要です。過去の出荷データや需要予測に基づいて、適切な発注点を設定します。
調達期間(リードタイム)
製品を調達するために必要な時間、つまりリードタイムも発注点の決定に影響します。調達にかかる時間が長ければ、より大きな発注点が必要になる可能性があります。
安全在庫
予期せぬ需要変動や調達の遅れに備えるため、安全在庫を考慮することも重要です。安全在庫は在庫レベルの最小限の保持量を示し、発注点を設定する際の余裕を確保するために使用されます。
発注点管理の種類
製造業における発注点管理には、主に定量発注方式と定期発注方式の2種類があります。発注点管理に用いるのは主に定量発注方式ですが、定期発注方式が向いているものもあるので、在庫によって判断が必要です。
定量発注方式 | 定期発注方式 | |
発注量 | 一定 | 発注の度に算出 |
発注タイミング | 不定期(発注点を下回ったとき) | 定期的 |
メリット | 管理がシンプル | 需要変動に対応できる |
デメリット | 需要変動の対応が難しい | 発注量の計算が毎回必要 |
定量発注方式
定量発注方式は、商品の需要に応じて必要な一定量をその都度発注する方法です。この方式では、在庫状況に基づいて発注点を決定します。「発注点を下回ったら発注」というシンプルな方式なので、誰でも管理しやすい一方で、需要の予測が難しい場合はリスクが高いというデメリットがあります。
例えば、月の出荷数量が100個、発注点100個の在庫品があるとします。この品物の需要が減り、月に50個しか出荷しなくなってきたにも関わらず、毎回100個を発注してしまうと、2ヶ月以上の在庫を抱えることになってしまいます。
よって、定量発注方式は、需要変動が少ない品物や単価が低い品物などに向いています。
定期発注方式
定期発注方式は、一定の周期ごとに発注する方法です。定期的に発注するかわりに、発注数量は必要に応じて毎回変えながら、適正在庫の維持を目指します。需要の変動に対応しやすいですが、発注数量を都度計算する手間が発生します。
例えば、適正在庫数100個、毎週発注する品物があるとします。1週目の発注タイミングの在庫数が60個なら、このときの発注数は40個となります。2周目の在庫数が30個だったら、70個発注します。このように、適正在庫になるように発注時に調整します。
よって、定期発注方式は、季節性のある製品のような需要変動が大きい製品、適正在庫を維持すべき重要な在庫品に向いているといえます。発注点管理による定量発注方式で、在庫過多や欠品が度々起きる品物は、定期発注方式への変更も検討してみることをおすすめします。
効率的な発注点管理の方法
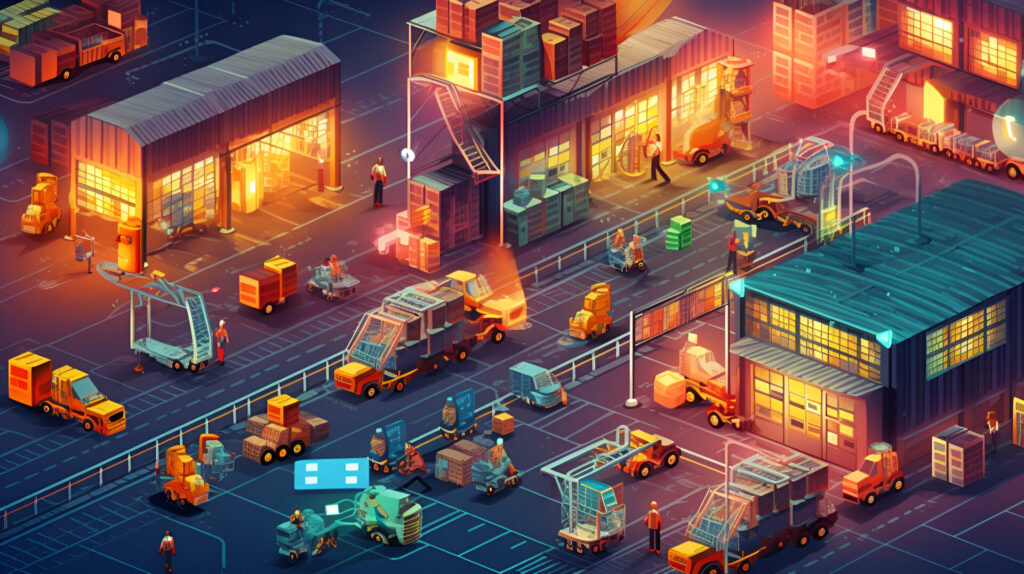
製造業における発注点とは、在庫を補充するためのポイントであり、適切な管理が極めて重要です。以下はその管理方法についての詳細です。
在庫数を把握する精度を上げる
在庫状態の正確な把握は、発注点管理の基本です。定期的な棚卸や在庫管理システムの活用によって、在庫数を正確に把握し、発注点を適切に設定します。
需要予測により発注点を見直す
過去の売上データや市場動向を分析して需要を予測し、それに基づいて発注点を見直します。需要の変動に柔軟に対応するため、定期的な需要予測の実施が必要です。
発注する商品の優先順位を決める
商品の重要度や売上動向に応じて、発注する商品の優先順位を設定します。需要の高い商品や季節商品などを優先的に発注し、在庫を効率的に管理します。
リードタイムを短縮する
製品の調達や生産にかかるリードタイムを短縮することで、発注点管理をより効率的に行えます。リードタイムが長いと、その間に必要な在庫も確保する必要があり、需要変動が大きい品物だとその間に欠品が起きる可能性も高まります。リードタイムの短縮には、供給先との密な連携(発注内示の共有など)や生産プロセスの最適化などが有効です。
業務のマニュアル化を行う
発注点管理の手順やルールを明確にし、業務をマニュアル化することで、作業の効率化とヒューマンエラーの軽減を図ります。従業員間での共通理解を促進します。
在庫管理システムを活用する
専用の在庫管理システムを活用することで、在庫情報のリアルタイムな把握や発注点の自動計算が可能となります。人的ミスを減らし、効率的な発注点管理を実現します。
在庫管理システムの役割
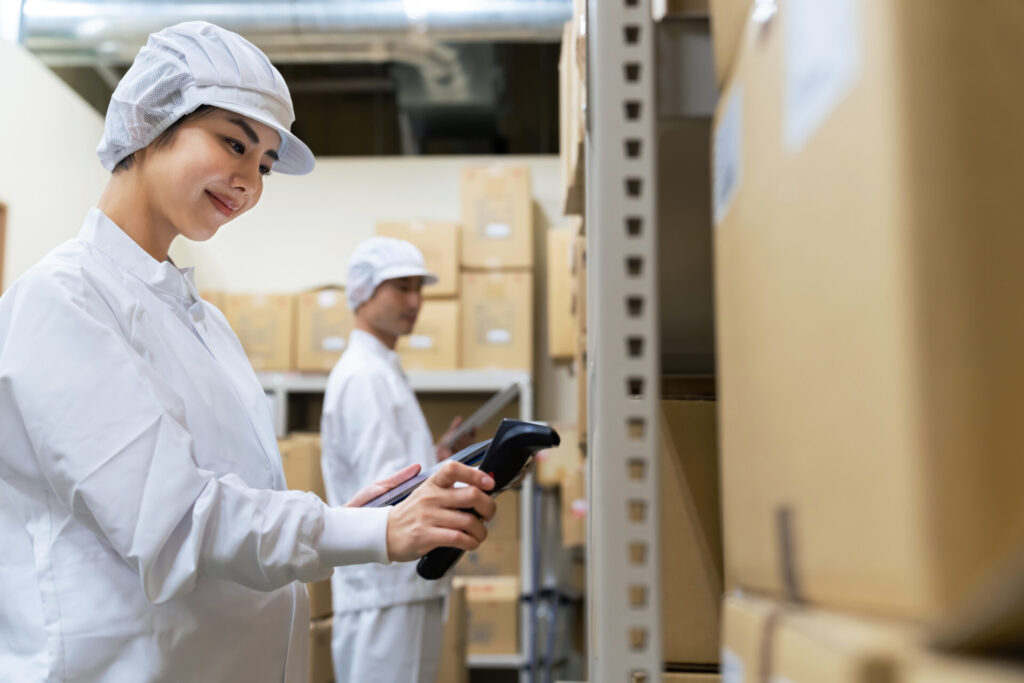
在庫管理システムの役割は、製造業における効率的な在庫管理を実現することです。在庫管理システムを使うと、在庫状況のリアルタイムな把握や、発注点・発注量の適切な管理を少ない手間で行えます。また、需要予測や過去の入出荷実績、リードタイムなどの要素を考慮して、最適な発注点を決定し、生産や購買の計画を立てることができます。これにより、在庫過剰や不足を防ぎ、企業のコスト削減や顧客サービスの向上に貢献します。
在庫管理システムの機能と利点
在庫管理システムには、以下のような主な機能と利点があります。
- 在庫状況の可視化: リアルタイムで在庫の状況を把握し、在庫の量や場所を管理することができます。これにより、在庫のロスや紛失を防ぎます。
- 需要予測と発注点の最適化: 過去のデータや需要予測を元に、最適な発注点を決定し、在庫の適正化を図ります。これにより、在庫過剰や不足を回避し、コストを削減します。
- リードタイムの管理: 製品の調達や製造にかかる時間を管理し、発注点や発注量の調整に反映します。これにより、供給チェーン全体の効率を向上させます。
- 自動化と効率化: 発注や入出庫などの作業を自動化し、作業の効率化を図ります。これにより、人的ミスや手間を削減し、業務の効率化を実現します。
- 顧客サービス向上: 在庫の正確な管理により、顧客への迅速な対応が可能となり、顧客満足度を向上させます。
在庫管理システム導入のステップ
在庫管理システムの導入には、以下のステップがあります。
- 自社に必要な機能の把握: 自社のニーズや課題を把握し、在庫管理システムがどのように役立つかを明確にします。
- システムの選定: 製造業の特性や規模に合った在庫管理システムを選定します(→ 主要な在庫管理システムの比較はこちら)。
- 導入計画の策定: 導入時期やスケジュール、費用などを含む導入計画を策定します。社内の関係者や現場で実際にシステムを使う担当者とのコミュニケーションも重要です。
- システムの導入: 開発や設定、テストなどを行い、システムを導入します。トレーニングやマニュアルの作成も同時に行います。
- 運用と改善: 導入後は定期的な運用と改善を行い、システムの効果を最大化します。ユーザーからのフィードバックを受け入れ、必要に応じてシステムをアップデートします。
成功事例:発注点管理の改善
在庫管理システムの導入により、発注点管理に成功した2社の事例を紹介します。
冷凍食品の製造・販売を行っているA社は、製造業向けの在庫管理システムを導入し、発注点管理を可能にしました。これにより、在庫過剰や不足を防ぎ、製品の供給を安定化させるとともに、業務の効率化とコスト削減を実現しました。
詳細:【原料在庫管理システム】毎日の原料在庫数の確認の手間を95%削減
医薬品の製造・販売を行うB社では、リードタイムの長い原材料の発注前に、生産計画に基づく将来在庫の計算が必要です。今まではこの計算をエクセルで行っていましたが、作業負荷が高く、生産計画を立てた担当者しか当業務ができないことに課題がありました。
そこで、発注点の自動計算ができる在庫管理システムを導入し、この計算の手間をなくすことに成功しました。具体的には、生産計画データを在庫管理システムに取り込み、在庫情報と生産計画を一元管理することで、数カ月後の将来在庫をいつでも確認できる運用にしました。
詳細: 【在庫管理システム】将来在庫の自動計算で発注の負担・工数を削減!生産計画と在庫を紐づける管理を実現
22種類の生産管理システムをランキングで比較
初期費用相場や選び方のポイントをチェック
生産管理システムをそれぞれの特徴や初期費用相場などで比較したい場合は、「生産管理システムランキング」も是非ご覧ください。生産管理システムは、自社の製品・生産方式・企業規模などに適したものを導入しないと、得られるメリットが限定されてしまいます。事前適合性チェックや生産管理システムを選ぶ前に押さえておきたいポイントも解説していますので、製品選びの参考にしてみてください。