在庫リスクを減らす受注生産とは?見込み生産との違いやよくある課題と解決事例を解説
公開日:2024年11月07日
最終更新日:2024年11月07日
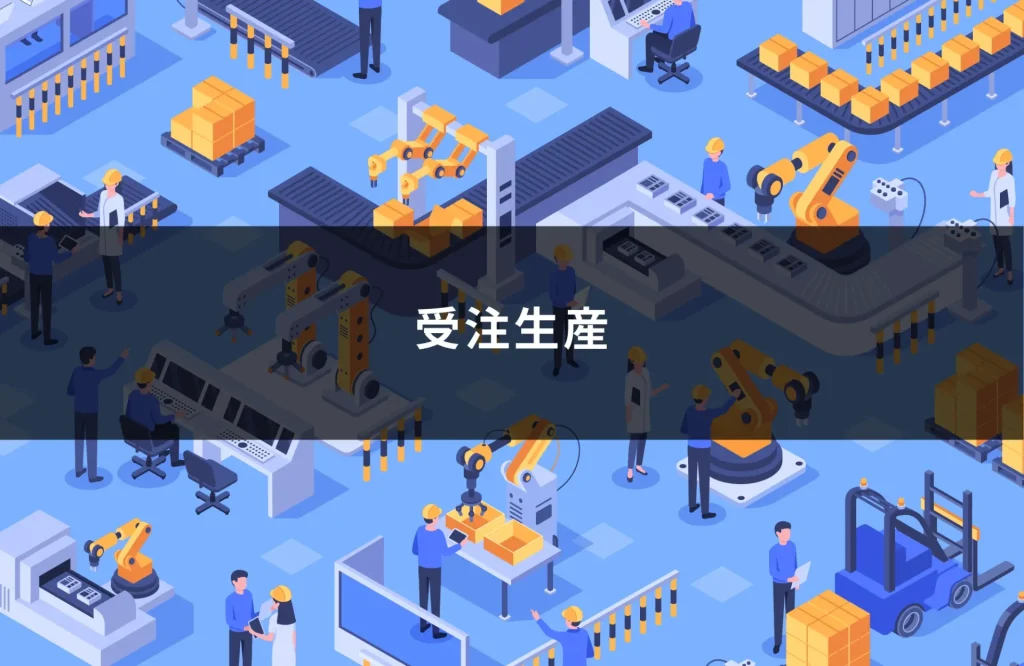
受注生産では、在庫リスクを抑えつつ、顧客要望に応じた製品を提供できますが、在庫・納期・原価の管理などが課題となることも多いです。本記事では、受注生産の基本から、個別受注生産と繰返受注生産の違い、製造方法に着目した生産方式との関連を解説します。また受注生産・見込み生産それぞれのメリットやデメリットまでを解説します。受注生産における在庫管理、原価管理の課題について、生産管理システムの活用事例も紹介します。
受注生産とは:注文対応型生産
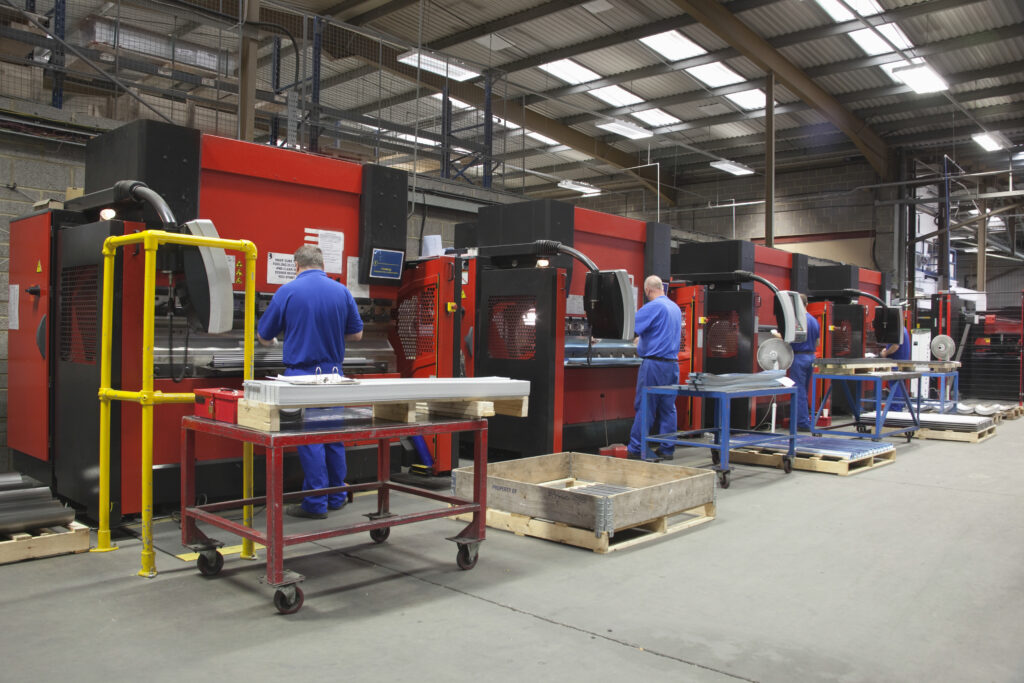
受注生産とは、顧客からの注文を受けてから製品の生産を開始する方式をいいます。この生産方式では、事前に需要を見込んで製造するのではなく、個別の注文ごとに生産計画を立てるため、在庫リスクを抑えることができます。
受注生産と見込み生産の違い
顧客からの注文に着目した生産方式として、受注生産と見込み生産の2つがあります。これらの最大の違いは、製品の生産タイミングと在庫管理の方法です。
受注生産では実際の注文を受けてから製品生産しますが、見込み生産では、市場の需要予測に基づいて製品をあらかじめ製造しておきます。このため、余剰在庫・欠品リスク、在庫管理、納入リードタイムという観点で、主に以下の表のような違いがあります。
生産方式 | 受注生産 | 見込み生産 |
生産タイミング | 受注後 | 受注前 |
余剰在庫・欠品リスク | 〇(なし) | ×(あり) |
在庫管理 | 〇(簡単、都度発注中心) | ×(煩雑、難易度が高い) |
納入リードタイム | ×(長い) | 〇(短い) |
受注生産は、受注を受けた分のみ生産するので、部品や原材料は都度発注が中心となります。そのため、在庫過多になるリスクは低いといえます。しかし、受注後に生産を始めるため、納入までのリードタイムは長くなりがちです。
一方、見込み生産は、受注前から需要予測などに基づいて生産するため、予測が外れると在庫を抱えるリスクがあります。また、数ヶ月先などの生産計画に基づき発注する必要があるため、在庫管理も複雑になりやすいです。しかし、受注前から生産することで、納入リードタイムを短縮でき、顧客へスムーズに製品を届けられるメリットがあります(詳しくは後述)。
受注生産に適した製品の特徴
受注生産は、注文を受けてから生産を開始するため、以下のような在庫保有リスクが特に高い製品に向いています。
- 需要予測が難しい製品
- 定期的なモデルチェンジが計画される製品
- 原料が高価で資金繰りを圧迫しやすい製品
一方で、見込み生産は、短納期が求められやすい消費財や標準規格品に適しています。どちらの生産方式も一長一短であり、市場や顧客ニーズに応じて、適切に選択することが望ましいと言えるでしょう。
受注生産には2種類ある
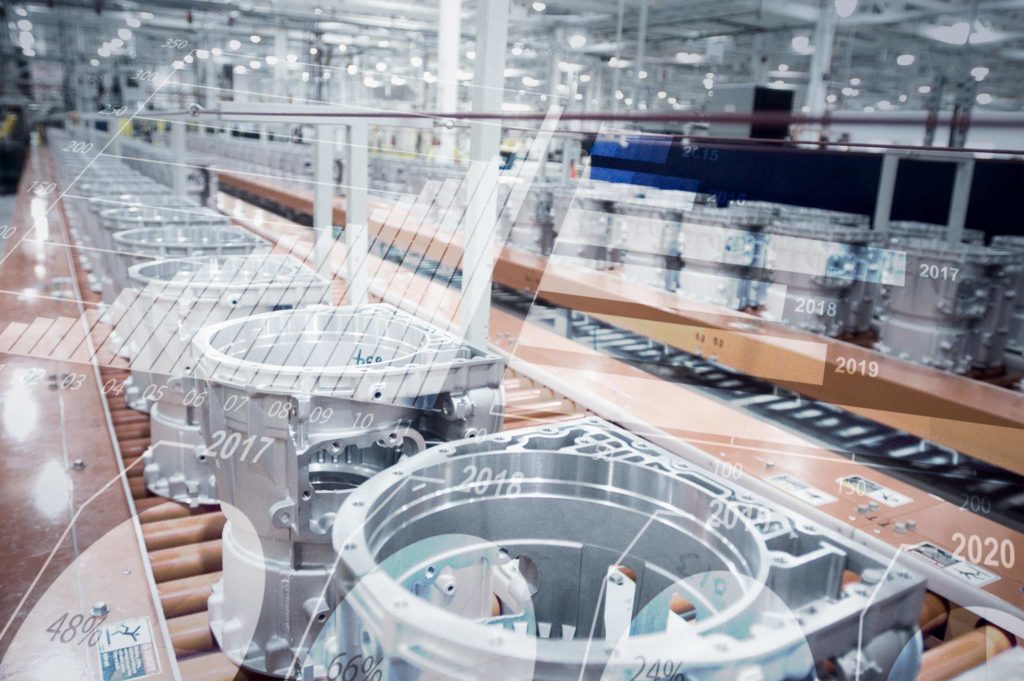
受注生産は「個別受注生産」と「繰返受注生産」に大別され、製品の特性や市場環境に応じて使い分けられます。
個別受注生産
個別受注生産は、顧客ごとに異なる仕様の製品を一つひとつ受注し、それに基づいて設計・製造を行う生産方式です。特にオーダーメイド製品に適しており、例えば産業機械業界、医療機器業界、航空宇宙業界など、細かな仕様調整が必要な分野で多く採用されています。
この生産方式では、顧客の要求に応じて製品・工程の設計を行います。また、製造プロセスでも、素材や部品の調達、加工、組立など、工程ごとに細かい管理が必要であり、特に仕様変更が発生した場合には、迅速かつ的確な対応が求められます。また、製造コスト・納入リードタイムが一品ごとに異なるため、見積もりや原価管理にも手間がかかります。
繰返受注生産
繰返受注生産は、標準仕様の製品を受注する度に製造する方式です。単に「受注生産」と表現する場合、繰返受注生産を指すことが多いです。
実際の注文を受けてから製造を開始する点は個別受注生産と同じですが、注文ごとに製品の仕様が変わらない点が異なります。同じ仕様の製品を何度も作るため、製造工程や部品、材料が標準化されており、生産効率が高いことが特徴です。
この方式は、標準化された機械部品・組立製品で、納期・数量面で細かな調整が必要な分野で広く採用されています。例えば、自動車部品、電気機器などの、定期的なモデルチェンジが予定されており、在庫管理が厳しく、汎用に近い製品で行われています。
実は受注生産にも使われる生産方式:ロット生産・ライン生産
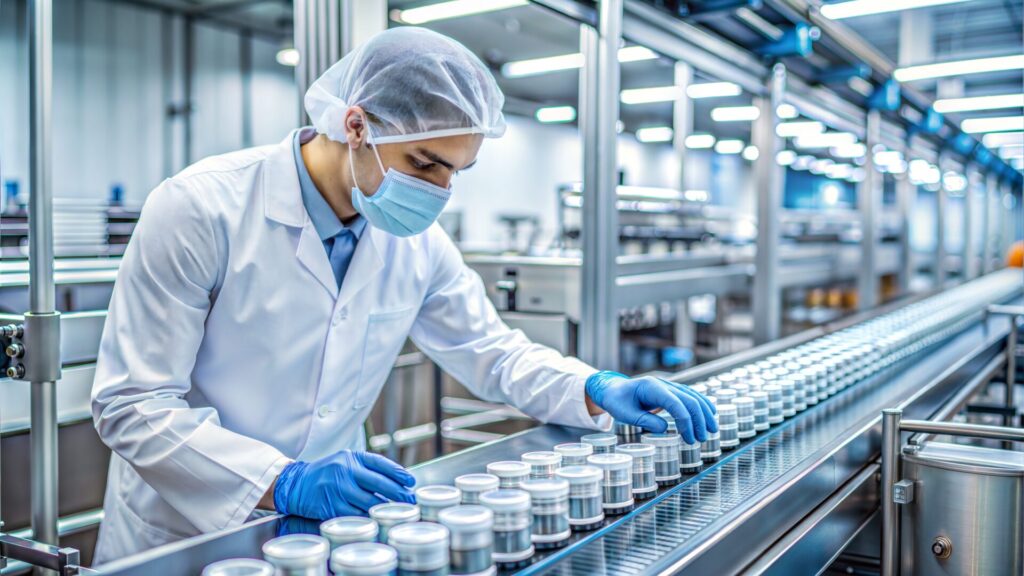
自社の製造方法に着目した生産方式として、連続生産、ロット生産、ライン生産があります。これらは量産や見込み生産で採用されることが多い生産方式ですが、受注生産品でも活用される事例があります。
製造方法に着目した生産方式の特徴、受注生産との関連は、以下の表の通りです。
生産方式 | 特徴 | 受注生産との関連 |
連続生産 | ・同一製品を長期間にわたって大量に生産する方式・需要が安定している製品に向いている | 需要予測に基づいた見込み生産に適しており、受注生産には不向き 受注生産の適用例:一部の素材分野 |
ロット生産 | ・一定量の製品をまとめて製造する方式・中間的な数量で生産効率を求める場面で活用 | 受注ごとのロットサイズに応じて製造するため、効率的な対応が可能同一設備で異品種を作り分ける場合は、段取り替えが必要 受注生産の適用例:アパレル製品、電子部品など |
ライン生産 | ・各工程を順番に進め、ライン上で製品を組み立てる方式・主に大量生産向け | 仕様の種類が限定的である受注生産に向いており、細かな個別カスタマイズには適さない 受注生産の適用例:自動車・家電製品など |
受注生産のメリット
受注生産には、在庫管理の効率化が図れるうえ、顧客の多様な要望にも対応しやすいという特徴があります。
余剰在庫を抱える心配がない
受注生産の最大のメリットは、顧客からの注文に紐づかない在庫を持たずに済む点です。在庫を持たないことで、余剰在庫によるキャッシュフロー悪化を未然に防ぐことができ、保管・管理コストの削減にもつながります。
また、モデルチェンジや技術革新によるライフサイクルが短い場合、余剰在庫は手直し・廃棄となるリスクがあります。一例を示すと、セラミックス加工部品では、モデルチェンジにより製品の寸法公差が厳しくなる場合があります。この場合、モデルチェンジ前の良品であっても、モデルチェンジ後にそのまま顧客に出荷できなくなってしまいます。このため、余剰在庫を削減できることは大きなメリットといえます。
さらに、製品の経時劣化による品質リスクを回避することもできます。例えば、金属加工製品について、余剰在庫を梅雨時に一般倉庫で保管すると、製品表面が錆びて不良品になってしまうこともあります。
顧客の要望に沿う製品提供が可能
個別受注生産の場合、顧客ごとの具体的な仕様・要望に合わせた製品を提供することができます。産業機械の金属部品では出荷頻度の少ないマイナー品番が多数あるため、注文ごとに素材・加工寸法・表面仕上げ方法など、細部にわたるカスタマイズが求められます。
また、顧客からのフィードバックをもとに、仕様の微調整をすることも容易です。組立製品の部品では、顧客で他の部品とのはめ合わせがしにくい場合、片方の部品寸法の微調整で対応することが多いです。
受注生産のデメリット
受注生産には、納期や生産計画の調整、仕様変更対応、見積もり対応が難しい、というデメリットも存在します。
納期調整や回答に時間がかかる
顧客ごとに異なる仕様で製品を生産する場合、生産計画が複雑になりやすいため、納期の見積もりや調整に時間を要します。
特に、同一設備で複数の注文の製品を作り分ける場合、それぞれの注文に対する生産計画のすり合わせが必要となります。また、製品の設計や製造において、予期せぬトラブルが発生した場合には、納期に遅れが生じるリスクもあります。
生産リードタイムが長くなりやすい
受注生産は、注文を受けてから生産を開始するため、納入までのリードタイムが長くなる傾向にあります。
特に、使用頻度の低い特殊な素材や部品を使用したり、まとまった量を使用したりする場合、これらの調達に時間がかかり、生産開始までに時間を要します。また、受注量が変動することも多いため、設備・工数の調整が必要となり、これもリードタイムの長期化につながります。
仕様変更が多い
顧客の要望に応じて製品を作るため、特に個別受注生産では設計・仕様の変更が頻繁に発生することもあります。この場合、仕様内容のすり合わせに加えて、生産設備・段取り替えも含めた生産計画の再調整が必要になります。設計工数・生産コストが増加したり、スケジュール調整に難航することも少なくありません。
特に、製品の設計段階で仕様変更が生じた場合、生産設備ラインの変更や材料の再手配が必要となることもあり、この場合は全体の生産フローにも影響を与えます。
見積もりの難易度が高い
各注文に対して受注量・仕様ごとに見積もりを作成するため、それぞれの受注に対して生産工程、材料費などを正確に把握する必要があります。
特に、高度にカスタマイズされている場合や、複雑な設計が必要な場合には、見積もりの精度を高めるため、詳細なコスト分析をします。見積もりの精度が低いと、提示価格が低すぎて採算が取れないほどの安価で受注したり、逆に提示価格が高すぎることで失注することもあります。
見込み生産の特徴
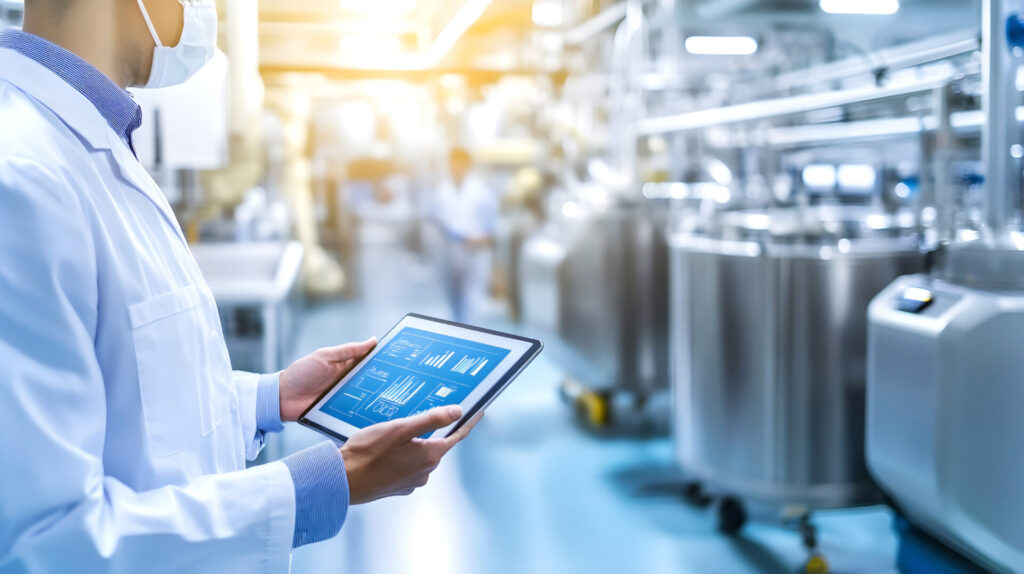
見込み生産には、標準仕様の製品について短納期で対応することができます。特に、安定した需要が見込まれる汎用製品に対しては、見込み生産のメリットが大きいといえます。
汎用的な製品に向いている
見込み生産は、需要が予測しやすい汎用的な製品に向いている生産方式です。標準仕様の部品・製品をあらかじめ大量に生産することで、材料の大量発注や生産効率の良い製造方法でコストを抑えつつ、安定供給を実現できます。
また、汎用品は製造工程を標準化しやすいため、品質管理の精度を高めることができます。
リードタイムが短い
見込み生産では、需要予測に基づいてあらかじめ在庫生産するため、受注後のリードタイムを大幅に短縮できます。
特に消費財や家電製品など、製品仕様の種類が少なく、迅速な対応が求められる業界において、リードタイムの短縮は販売機会の損失を防ぐことにもなります。
生産効率を高めやすい
製造プロセスにおいても、事前に生産計画を立てることで、ラインの稼働率を高め、生産効率を向上させることができます。
特に、需要変動の大きい製品では、材料・部品の調達・在庫生産を事前に計画することで、需要ピーク時にも即納できる体制を構築することができます。
見込み生産のデメリット
見込み生産には、在庫リスクや競争の激化といったデメリットがあります。
余剰在庫のリスクがある
需要予測に基づいて事前に製品を生産するため、予測が外れた場合には大量の余剰在庫を抱えることになります。
この在庫は、製品の経時劣化や製品モデルチェンジなどにより、手直しが必要となったり、最悪の場合では廃棄処分となったりすることもあります。さらに、余剰在庫が多い場合には、保管コストの負担が重くなり、経営効率が悪化する可能性もあります。
価格競争になりやすい
見込み生産は、一般的に規格品の大量生産を前提としているため、製品の差別化が難しく、価格競争が激しくなりやすい傾向があります。
特に、製品の技術的な優位性やブランド力がない場合、価格以外の要素で競争することが難しく、激しい価格競争に陥るリスクが高まります。
受注生産のよくある課題
受注生産では、次のような課題を抱えることが多いです。
- 在庫管理:材料の調達ミスや過剰在庫により、効率的な管理が難しい
- 原価管理:製品ごとに異なるコストを把握し、正確な見積もりが難しい
- 納期管理:注文や材料の遅れで納期がずれ、進捗管理が複雑になる
- 生産計画の調整:複数の注文や急な変更により、リソース調整が必要になる
- 生産性向上:予測が立てにくく、設備稼働率の低下を招きやすい
ITツールや生産管理システムを活用し、社内での情報共有を円滑化したり、生産計画を見える化するとよいでしょう。これらを活用することで、ムダのない資材調達、適切な人員配置を行うことで、会社全体の生産効率の向上につながります。
生産管理システムの具体的な活用事例
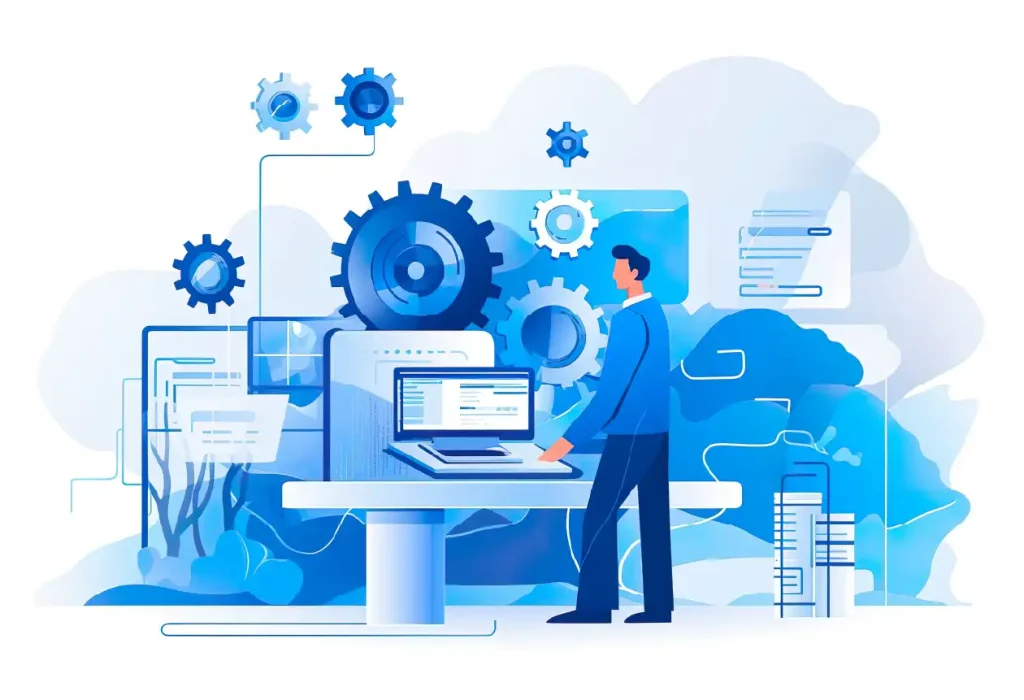
受注生産における課題への取り組みには、生産管理システムの活用が有効です。具体的に、生産管理システムを活用した2つの事例を紹介します。
リアルタイムな在庫管理
医療機器・車載機器の部品メーカーでは、多品種少量生産における在庫管理に悩んでいましたが、生産管理システム導入により大幅な改善をされました。
従来、半日以上も生産を止めて手書き帳票による実地棚卸を行い、Excelを用いた手作業での集計管理を行っていました。しかし、実作業や事務処理に膨大な手間を要し、手書き帳票取り扱いでのヒューマンエラーも多発していました。
そこで、生産管理システムを導入し、ハンディーターミナルとの連携により、リアルタイムかつ精度の高い在庫管理を実施できるようになりました。
→在庫管理の効率化に成功した事例はこちら:【在庫管理システム】半年の棚卸工数を1000時間規模で削減!精緻な在庫管理で発注ミス防止やロットトレースも強化
製品別原価管理による見積精度向上
オーディオ機器の多品種少量生産を行うメーカーでは、受注生産における原価管理の課題を抱えていましたが、生産管理システムの導入で大幅に改善しました。
製品別の原価を正確に管理すべく、初めは自社で管理システムの開発を試みたものの、運用の複雑さや工数の多さがハードルとなっていました。そこで、パッケージ型の生産管理システムを導入することで、各案件の材料費や工数をリアルタイムで把握し、複雑な原価を自動で計算できる体制を確立しました。
複雑な個別受注生産の中でも、労務費や材料費の自動集計が可能となり、以前は困難だった製品ごとの製造コストを反映した精度の高い見積もりが実現しました。
→精緻な原価管理を実現した事例はこちら:
【生産管理システム】製品別原価管理・粗利分析が可能に!商品開発の予算化による開発スピード向上もできる体制に
22種類の生産管理システムをランキングで比較
初期費用相場や選び方のポイントをチェック
生産管理システムをそれぞれの特徴や初期費用相場などで比較したい場合は、「生産管理システムランキング」も是非ご覧ください。生産管理システムは、自社の製品・生産方式・企業規模などに適したものを導入しないと、得られるメリットが限定されてしまいます。事前適合性チェックや生産管理システムを選ぶ前に押さえておきたいポイントも解説していますので、製品選びの参考にしてみてください。