設備保全とは 種類別・課題の解決方法と設備保全システム事例を紹介
公開日:2020年03月03日
最終更新日:2025年05月31日
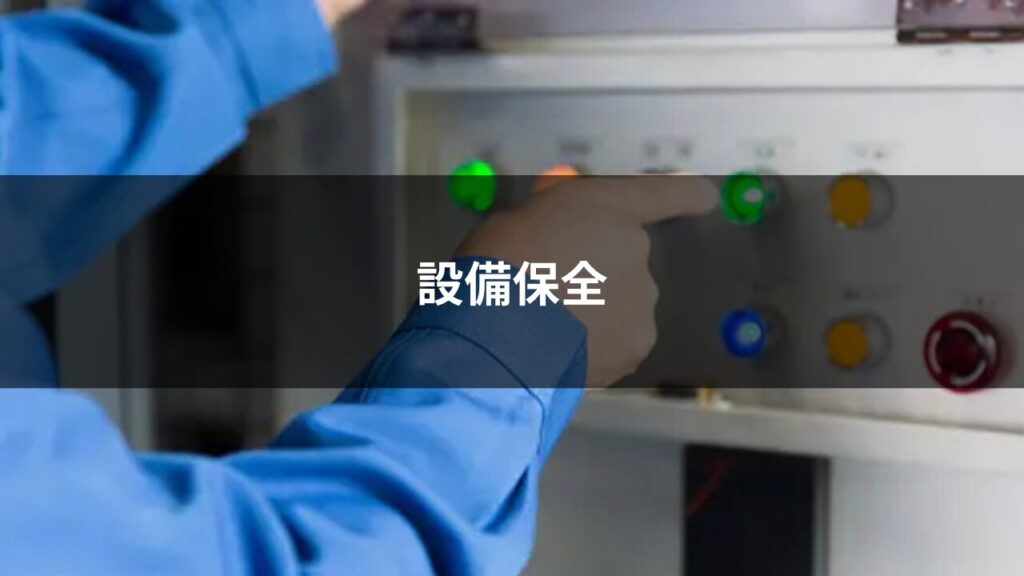
工場やオフィスビルなど、あらゆる現場で「設備」は日々動いています。その設備を安全かつ効率的に使い続けるために欠かせないのが「設備保全」です。
製造業において設備保全は、生産性を左右する重要な業務といえます。しかし、設備保全が不十分で、属人的な管理となってしまっている企業は少なくありません。
本記事では、設備保全の種類や具体的手法・活動フローなどの基本だけでなく、設備保全のあるべき姿まで解説します。設備管理システムの活用についても、事例つきで紹介します。
設備保全とは
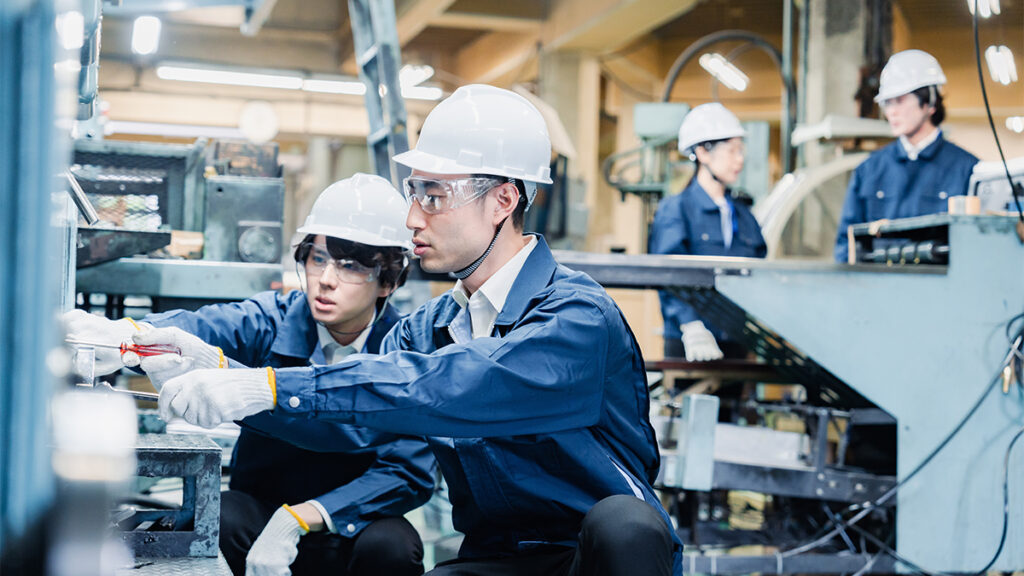
設備保全とは、設備が「故障する前に予防する」「性能が低下するのを防ぐ」ために行う一連の活動で、設備を常に正常な状態で維持することを指します。これにより、設備の寿命を延ばし、稼働効率を高めることが目的です。
設備保全には、以下のような活動が含まれます。
●計画:設備の保全活動を計画的に実施するためのスケジュール作成
●点検:定期的に設備の状態をチェックし、異常がないかを確認
●検査:設備の性能や安全性を確認するための詳細な検査
●調整:設備が最適に動作するように、設定や動作を微調整
●修理:故障や不具合が発生した場合に、早急に修理を行い、復旧する
●取替え:消耗品や老朽化した部品を新しいものに交換する
簡単に言えば、設備保全とは「設備が壊れないように定期的に点検を行い」「汚れを取り除いたり」「消耗部品を交換することで」、設備が常に正常に動くように保つ活動のことです。
設備保全の重要性と目的
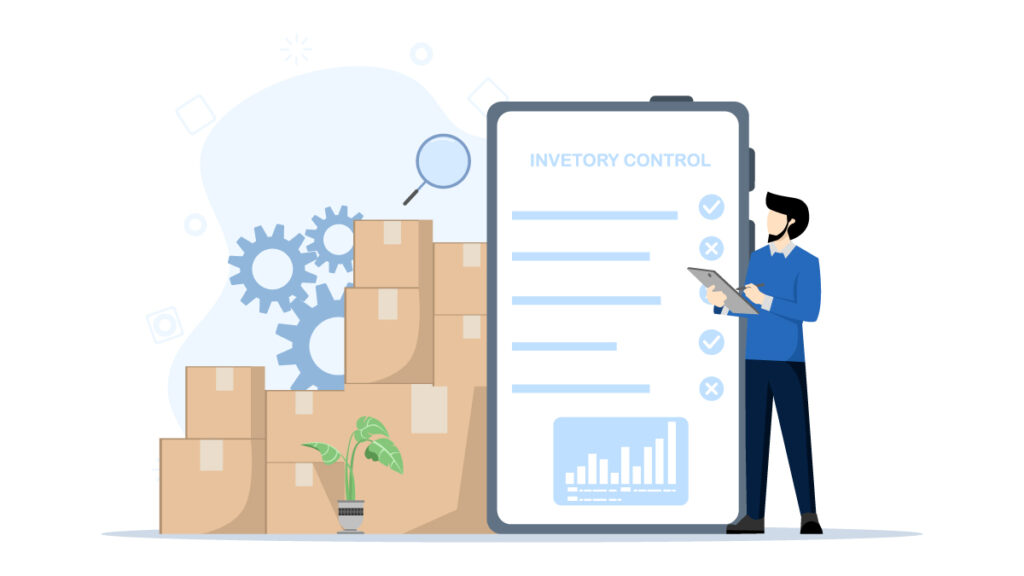
設備保全は、工場の生産性を維持し、現場の安全と安定稼働を実現するために欠かせない重要な取り組みです。
主な目的は、突発的な故障の防止・安全性の確保・コスト削減、品質の安定です。
工場では、設備の一部が故障するだけで生産ライン全体が停止し、生産性が大きく落ちてしまいます。こうした事態を防ぐためにも、日頃から定期的な点検や部品交換を行い、設備を常に正常な状態に保つことが不可欠です。設備保全は、現場の安全と安定稼働を支える重要な活動といえます。
もしも工場でライン上の設備が1か所壊れてしまい、ラインが止まってしまうとします。
そうなると、ラインで働いている全員の手が止まってしまい、生産性がかなり落ちてしまうことになります。
そのため、普段から設備保全を行い、ラインが停止しないように、設備が問題なく動くように定期的な点検や部品交換を行っておかなくてはなりません。
保守・メンテナンス・修理との違い
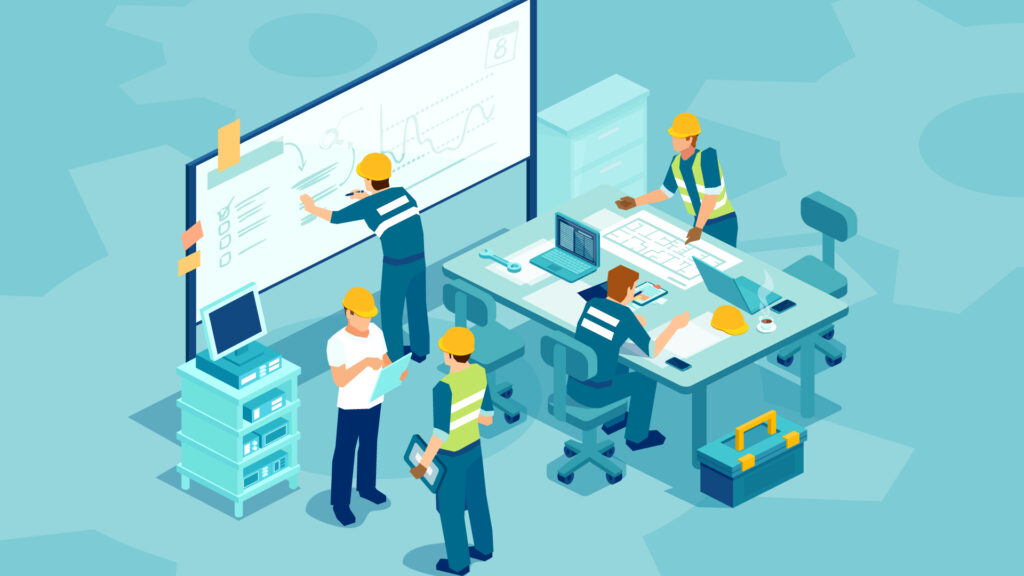
「保守」「メンテナンス」「修理」「設備保全」は、いずれも機械や設備の管理に関わる言葉ですが、それぞれ少しずつ意味が異なります。
保守とは
まず「保守」とは、設備や機械が壊れないように日常的に点検したり、清掃や調整をしたりして状態を維持することを指します。目的はあくまでトラブルを未然に防ぐことで、たとえば定期的な点検や潤滑油の補充、劣化部品の交換などが保守にあたります。
メンテナンスとは
「メンテナンス(maintenance)」は、日本語の「保守」とほぼ同じ意味合いで使われることが多く、正常な状態を維持するための活動を指します。特に近年では、IT機器やソフトウェア分野でも「メンテナンス」という表現が一般的になっています。
修理とは
一方、「修理」は機械や設備が実際に故障したあとに行う対応です。すでに問題が発生した状態を元に戻すための作業であり、モーターが止まって動かなくなった場合に部品を交換して復旧させるといった行為が修理に該当します。
最後に「設備保全」は、こうした保守や修理を含むもっと広い概念です。単に故障を防ぐだけではなく、設備を長期的かつ安定的に使い続けるために、計画的に点検、整備、改善を行う総合的な活動を指します。
予防的な管理だけでなく、故障発生後の対応や改善活動など、設備全体のライフサイクルに関わる幅広い業務が設備保全の中に含まれています。
まとめると以下のようになります。
用語 | 意味 |
保守・メンテナンス | 壊れないように守る(予防・維持) |
修理 | 壊れたあとに直す(トラブル対応) |
設備保全 | 計画的に設備全体を管理・維持する(保守や修理も含む) |
設備保全の種類一覧
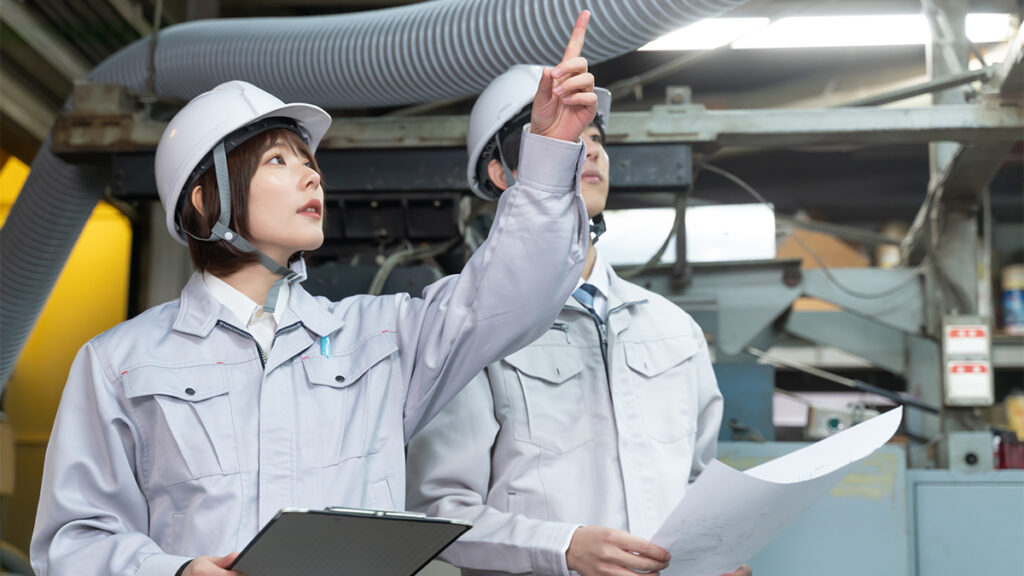
設備保全には大きく「維持活動」と「改善活動」に分類されます。
さらに、維持活動には設備が故障してから修理を行う「事後保全」と、故障を未然に防ぐためにあらかじめ対策を講じる「予防保全」があります。
一方、「改善活動」には、設備の性能や信頼性を高めることを目的とした「改良保全」と、設備の設計段階から保全性を考慮してトラブルを減らす「保全予防」が含まれます。これらの分類は、JIS Z8141:2000においても以下の図のように整理されています。
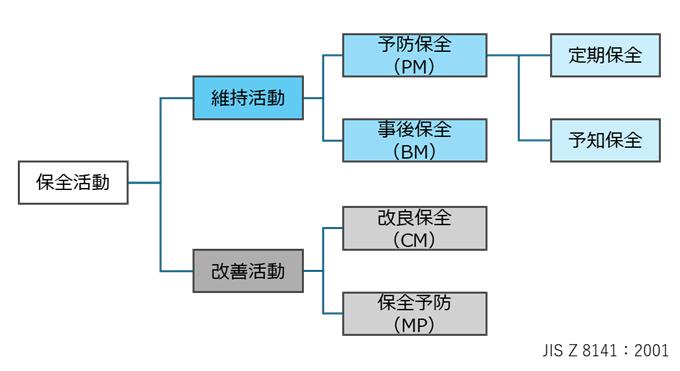
事後保全とは
事後保全とは、設備や機器が故障した後に修理や対応を行う保全方法です。予防的な点検や計画的な保守が行われていない場合、設備が壊れた際に初めて対応を始めます。故障が発生するまで状態の把握や予測を行わないため、予期せぬダウンタイムが発生するリスクがあります。
事後保全は、設備が正常に稼働している間はコストがかかりません。しかし、生産ラインが突然停止すると、納期遅れ対応などで間接的なコストが発生するリスクがあります。
事後保全の特徴
対応時期: 故障後に設備の修理や交換
メリット: 初期投資は比較的少ない
デメリット: 故障発生後に対応するため、修理に必要な部品の費用や作業時間が必要
事後保全の例1:生産ラインの設備が故障
ある製造業で、工場内の生産ラインで使用していた設備の一部が故障し、その後修理作業が行われました。予防保全がなく、定期的なメンテナンスが実施されていなかったため、設備が停止するまで故障の兆候に気づけませんでした。
故障発生後、修理作業員が現場に駆けつけ、必要な部品を交換しました。しかし、生産ラインが再稼働するまで数時間のダウンタイムが発生しました。その結果、予想外のダウンタイムにより、生産計画が遅延し、納期に影響が出ました。また、修理部品の調達に時間がかかり、さらにコストがかさみました。
事後保全の例2:古い設備での事後保全
ある工場では、設備が長期間使用されていたため、数週間に一度程度のトラブルによる停止が発生していました。そのまま運転していましたが、ある日設備が完全に動かなくなりました。
故障発生後に修理作業を行うも、必要な部品の在庫がなく、古い設備のため部品を取り寄せるにも数日間の生産停止が発生。早く稼働させるために、オークションなどで中古部品を探しても見つからず、稼働停止期間が長引きました。そして、現場の生産効率が低下しました。
このように、事後保全は設備故障後の対応に焦点を当てた保全方法のため、ダウンタイムや追加コストが発生しやすいというデメリットがあります。頻繁に故障が発生する設備や、重要な設備では、「予防保全」や定期的な点検を組み合わせた保全戦略を採用することが求められます。
予防保全とは
予防保全は、故障する前に修復する設備保全の手法です。具体的には、設備全体が故障する前に「点検を行って劣化のある部品を交換する」「一定期間経過した部品は劣化していなくても交換する」といった方法があります。
予防保全の特徴
対応時期: 設備の使用時間や稼働回数に基づき、定期的にメンテナンスや部品交換
メリット: 定期的な保守により、突発的な故障のリスクを低減・安定した稼働が見込る
デメリット: 必ずしも部品が劣化していない場合でも交換を行うため、無駄なコストや作業が発生する可能性がある
予防保全の詳細:予防保全とは?QMS規格との関連、予防保全の基本的考え方から具体例まで解説
さらに、近年はIoTの発達と共に、予防保全をさらに発展させた「予知保全」という手法も増えています。
予知保全とは
予知保全とは、リアルタイムな稼働監視で良い状態・悪い状態の設備データを収集し、データから交換時期を予知して部品を交換する保全方法です。
劣化があってから交換したり、部品が壊れていなくても交換する予防保全とは違い、部品を最大限利用し、劣化する直前で交換することができます。計画的に設備保全ができるため、ダウンタイムを最小限に抑えることができます。
予知保全の特徴
対応時期: 設備の状態をセンサーデータや点検結果などで常に監視し、異常の兆候が見られた段階で保全活動を行う
メリット: 故障前に異常を検知できるため、計画的に修理や部品交換を行うことができる
デメリット: 状態監視のためのシステム構築やセンサー設置など、初期投資が比較的大きくなる場合がある
予知保全を実現するには、データ解析などの専門知識が必要です。難易度が高い設備保全手法ですが、実現できれば保全業務の効率を大きく向上できます。
予知保全の詳細:予知保全とは?予防保全や予兆保全との違い、メリットを解説<導入事例付>
改良保全とは
設備が繰り返し故障したり、使いにくかったりする部分を、構造や制御、操作方法などを改善・改良していく保全活動のことです。「壊れたから直す」ではなく、「壊れにくくする」「作業しやすくする」が目的です。設備の設計変更や改良を伴う場合もある、時間とコストが必要ですが、根本的な原因を取り除ける点は大きな利点と言えます。
改良保全の特徴
対応時期: 故障や不具合が発生した後、単なる修理にとどまらず、同様の故障が再発しないように設計変更や設備改良を加える
メリット: 将来同じトラブルが起こるリスクを大幅に低減でき、設備の信頼性が向上する
デメリット: 一時的な稼働停止が必要となる場合がある
改良保全の例1:センサーの位置変更
ある工場で、搬送ラインに取り付けられたセンサーが頻繁に誤検出を起こしていました。調べてみると、センサーが振動や粉じんの影響を受けやすい場所に設置されていたのが原因でした。
原因調査後にセンサーの位置を変更し、保護カバーを追加することで誤動作が激減し、生産停止のトラブルもなくなりました。
改良保全の例2:グリスアップの簡素化
定期的にグリスアップが必要なモーター部分がカバーの奥にあり、毎回分解が必要で手間がかかっている工場がありました。そこで、給油口を延長し、作業が容易にできるようにした結果、整備のし忘れが減りました。
保全予防とは
保全予防とは、故障や保全作業が発生しにくいように、設備の設計や運用を考える保全活動です。保全を「やりやすくする」ではなく、「保全しなくて済むように」するため、故障しにくくメンテナンスが簡単な設備づくりを目指すという発想です。
保全予防の特徴
対応時期: 新たに設備を設計・導入する段階で、将来的な保守・修理のしやすさを考慮して設計を最適化する
メリット: 保全作業の負担やコストを大幅に減らすことができ、設備全体のライフサイクルコストを低減できる
デメリット: 設備開発段階での検討事項が増えるため、設計・開発に要する期間やコストが上昇する場合がある
保全予防の例1:設備のカバーをワンタッチ化
とある工場で、定期点検のたびに設備のカバーを開ける必要があり、工具(ドライバー)でビスを外す作業が手間となっていました。作業者によっては、点検を後回しにするケースも見られました。
そこで、カバーをネジ止め式からワンタッチロック式に変更。工具不要で開閉できるようにしたことで、点検作業が簡素化され、保全の実施率が向上しました。
保全予防の例2:高所照明のメンテナンス削減
ある工場の高所に設置された水銀灯照明は、数年ごとにランプ交換が必要です。その都度、高所作業車や複数人での作業が必要でした。照明切れを放置する例もあり、安全性にも影響が出ていました。
これを改善するため、水銀灯を長寿命かつ低発熱のLED照明に変更。約10年間交換不要となり、保守作業そのものがほぼ不要になりました。その結果、作業リスクとコストが大幅に削減されました。
予防保全、事後保全、改良保全、保全予防をまとめると、以下の通りです。
種類 | 内容 | 特徴 | 実施タイミング | 主な目的 |
事後保全 | 故障が発生してから 修理・復旧を行う保全 | 最もシンプルで コストがかかりやすい | 故障や異常発生時 | 速やかな復旧と 稼働再開 |
予防保全 | 故障する前に 定期的に点検・整備・ 部品交換を行う保全 | スケジュールに 基づいて実施する 計画保全 | 設備が正常に 稼働している間 | 故障を未然に防ぐ |
改良保全 | 繰り返し発生する 不具合や使いにくさを 改善する保全 | 構造や設計を 見直す改善型の保全 | 故障や 不具合を経験した後 | 再発防止・作業性向上 |
保全予防 | 故障や保全作業が 発生しにくいように、 設備の設計や運用を 考える活動 | 保全しなくて 済むようにする発想 | 使う前・選定時 | そもそも 故障しないように設計 |
近年では、TPM活動の一環として、オペレーター自身が簡単な保全作業を行う「自主保全」の取り組みが広がっています。
TPMとは
TPMはTotal Productive Maintenanceの略で、「設備の総合効率向上」を目的とした生産現場全体で取り組む保全活動のことです。
生産部門や保全部門だけでなく、管理部門も含めた全員参加型で、故障ゼロ・不良ゼロ・事故ゼロを目指します。
自主保全の主な活動内容は以下になります。
●目視点検(油漏れ、ボルトの緩み、異音・異臭など)
●給油や簡単な部品交換
●小さな異常の記録と報告
●5S活動(整理・整頓・清掃・清潔・しつけ)との連動
では次に、設備保全のあるべき姿とは、具体的にどのような状態を指すのかについて説明します。
設備保全のあるべき姿とは
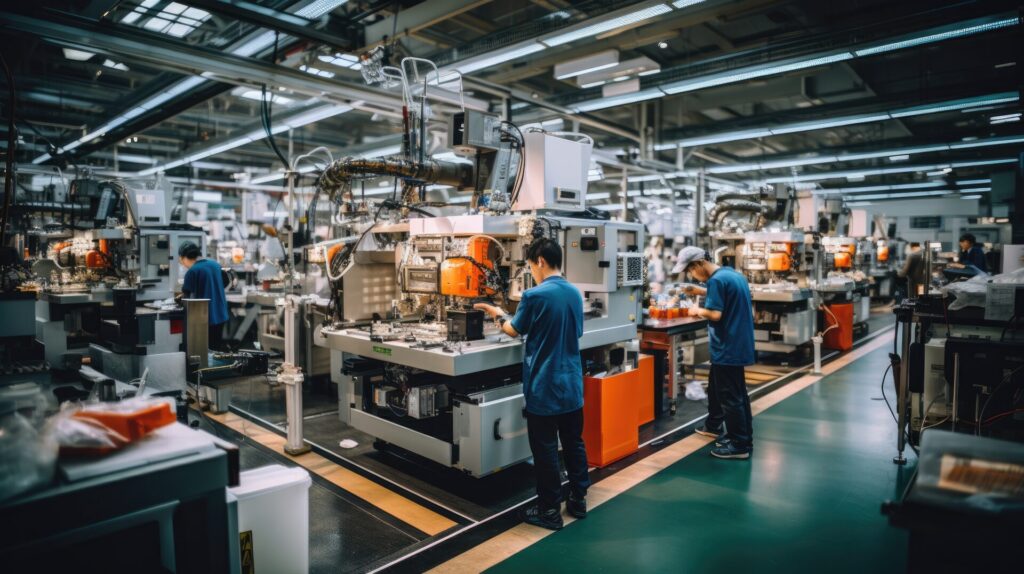
設備保全の理想的な姿とは、「設備が常に最適な状態で安定稼働し、生産性と品質を最大限に引き出すこと」です。
しかし、実際の現場では「故障ゼロ」「品質トラブルゼロ」「安全事故ゼロ」を完全に達成するのは難しいのも事実です。そのため、企業の規模や予算、設備の重要度に応じた適切な保全体制を構築することが現実的なアプローチとなります。
設備保全の理想に近づくためのポイント
理想的な設備保全のあり方に近づくためには、以下4つのポイントを理解し、実行することが重要です。
1.「ゼロ」は理想、現実的な目標を設定する
設備の故障やトラブルを完全になくすことは難しいが、最小限に抑えることは可能です。「年間の設備停止時間を50%削減する」など、具体的な改善目標を設定します。
2. 設備の重要度に応じた保全を行う
すべての設備に最高レベルの保全を行うのはコストがかかりすぎるため、優先順位を決めることが大切です。
例えば、生産のボトルネックになりやすい設備や、高価な設備は予知保全を強化し、補助的な設備は事後保全のまま運用するなど、最適なバランスを考えます。
3. 規模や人材に応じた保全体制をつくる
大企業と中小企業では使えるリソース(人・予算)が異なるため、それに応じた保全戦略を取ることが重要です。
人手が不足している場合は、簡単な点検を現場スタッフが行い、専門的な修理は外部業者に依頼するなどの柔軟な運用が求められます。
4. コストを最適化する
設備保全には、「保全コスト」と「故障による損失コスト」のバランスが重要です。
無駄な修理や部品交換を避けつつ、適切なタイミングで保全を実施することで、トータルコストを削減できます。
次に、システムを導入した保全事例を紹介していきます。
システムで設備保全を効率化する方法(導入事例つき)
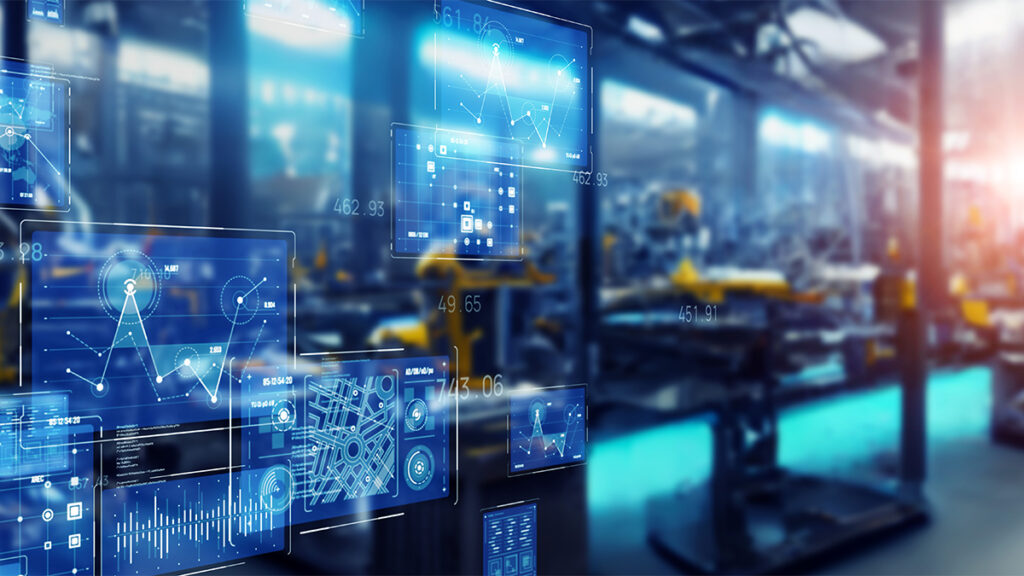
工場における設備トラブルを減らし、生産性を高めるためには、紙やエクセルによるアナログ管理から脱却し、システムによる保全情報の一元管理と現場での簡易入力が不可欠です。
設備保全業務をシステム化できると、「入力漏れ・記録ミスの削減」「点検漏れの防止」「トラブル原因の明確化」といった成果が期待できます。よくある課題とシステム導入による効果と事例を、事後保全・予防保全・予知保全のそれぞれのステージで紹介します。
事後保全の場合
多くの工場では、トラブルを紙に記入して記録することで管理しています。しかし、紙での手書き入力は面倒なこともあり、小さなトラブルだった場合、現場のスタッフが記入をしないといった事態が起こります。
また、手書きの紙を事務所でエクセルに入力して記録している工場もよく見かけますが、入力ミスや記入漏れがあり、管理者は正しくトラブルを把握できていないという状態がよく起こっています。
こうした課題を解消し、トラブルの原因を正確に究明するためには、現場で簡単に入力でき、かつ自動的にトラブルを記録できるシステムを導入することも一つの有効な方法です。
■故障をシステムで記録することでトラブルが3年で1/3になった改善事例
ある自動車工場では、トラブルの記録を手書きで管理していたのですが、記入漏れが多発しており、すべてのトラブルが把握できない状態になっていました。
そこで、バーコードとハンディ端末による設備管理システムを導入しました。あらかじめ予想されるトラブルを登録しておき、トラブルが起きた際には、設備に貼ってあるバーコードを読み取り、ハンディー端末に表示されるトラブルを選択するだけで、トラブルの記録・集計が簡単にできるようになりました。
このシステムを導入してからというもの、トラブルの原因特定がしやすくなり、トラブルは3年で導入前の1/3に。生産性の向上につながる結果となりました。
予防保全の場合
予防保全は、事後保全の次のステップです。実際に起きたトラブルから「いつ部品を交換しなければならないのか」「いつ点検をしなければならないのか」をリストアップしていくことから始まります。
そのリストをもとに点検や部品交換などを行っていくのですが、多くの工場ではエクセルで管理しています。エクセルでの管理は設備が多くなると複雑になり、入力に時間がかかることも多いのが現状です。
また、現場で点検を行い、事務所で入力するという仕組みがほとんどのため、入力ミスも多発しがちです。そこで点検スケジュールを管理できるような設備保全システムを導入することで、正確に点検や交換の時期を把握でき、実施の有無もすぐに確認できるようになります。
■点検管理をエクセルからバーコード管理に変更して点検漏れをなくす
ある冷凍食品を製造する工場では、600ある設備の点検をエクセルで管理していました。点検や修理・交換を現場で行い、事務所に戻ってから行った設備保全の内容をエクセルに入力するという方法です。設備ごとに1シートで管理しているため、エクセルは600シートもあり、管理がしにくく困っている状態でした。
そこで、ハンディ端末による設備管理システムを導入。各設備と点検周期を事前に登録し、今月点検しなければならない設備の帳票を表示するようにしました。どの設備の何の部品を現在点検・交換しなければならないのかが一目で分かり、点検漏れを防ぐ仕組みです。
さらに、ハンディ端末で点検内容を確認しながら、設備に貼ったバーコードとハンディ端末で点検結果を記録できるようになりました。これにより、記録漏れの防止効果も得られました。
また、保守部品の在庫が少なくなれば自動発注するシステムも同時に導入し、在庫切れを防ぐ仕組みも取り入れました。
予知保全
予防保全をすでに行っている工場では、点検・交換のスケジュールを組んで効率的に保全を行ってはいても、まだ使える部品でも交換してしまうリスクがあります。
そこで、IoTを導入することで、データを集めて効率のよい交換を行うことができるようになります。
■モーターの振動をセンサーで記録し、トラブル前に交換して有効利用
こちらも冷凍食品工場での事例です。
この工場では冷風機のモーターが度々壊れており、故障が起きた後に交換をしていましたが、効率的に交換できないか悩んでいらっしゃいました。
そこでモーターに振動センサーを付けてモーターの振動を記録。トラブルが起きた前後の振動と通常の振動の波形データを記録していくことで、トラブルを予知する仕組みです。
ある波形になればその後にトラブルが起こるといったことが分かれば、モーターを最大限利用して壊れる前に交換することができるため、モーターを有効的に使用することができます。
設備保全は工場の実情に合わせた選択が鍵
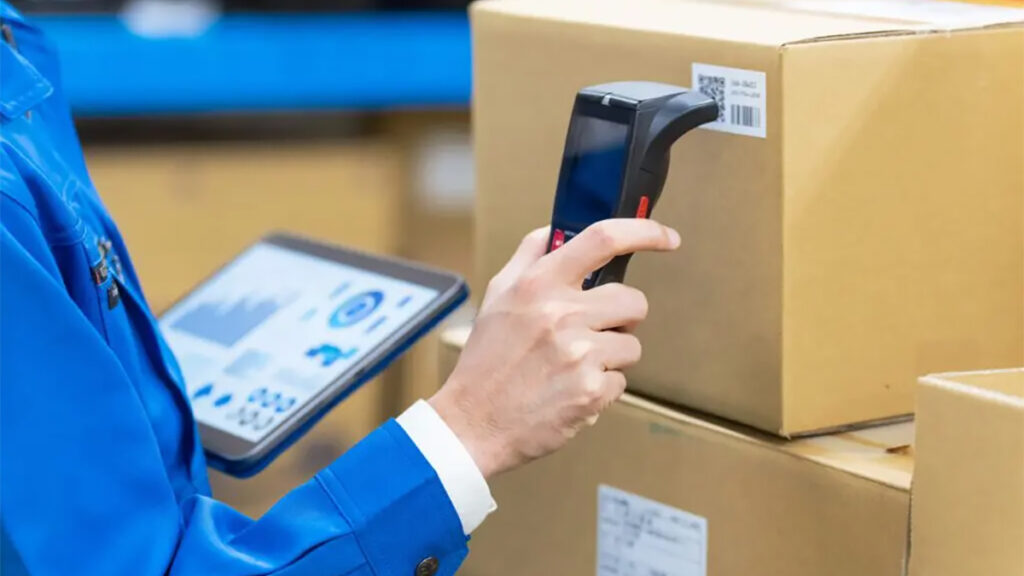
事後保全・予防保全・予知保全のうち、どの保全を導入するかは、設備の重要度や故障時の影響度、工場の規模やリソース状況によって最適な選択が異なります。
たとえば、小規模工場や故障の影響が比較的小さい設備であれば、まずは事後保全をベースにトラブルの傾向を記録し、原因分析から始めるのが現実的です。安定した稼働が求められる重要設備には、あらかじめ点検や部品交換を計画的に実施する予防保全の導入が有効です。
さらに、生産ラインの停止リスクを極力減らしたい工場では、IoTやセンサー技術を活用した予知保全を導入することで、部品を最大限活用しながら、故障を未然に防ぐことができます。
中小・中堅企業が導入しやすいのはQR・バーコード管理
中小・中堅規模の製造業が保全の質向上のため、トライしやすい設備管理のITツールは「QR・バーコード管理」です。
まず、QRコードやバーコードは、安価で導入しやすいIoTツールです。コードスキャンを通じて現場で設備データを入力でき、リアルタイムにシステムへ反映・更新することで、設備状況を可視化できるようになります。
ネクスタ社でも、工場の規模や設備の特性に応じた設備保全システムの開発・導入支援を行っています。お気軽にご相談ください。
22種類の生産管理システムをランキングで比較
初期費用相場や選び方のポイントをチェック
生産管理システムをそれぞれの特徴や初期費用相場などで比較したい場合は、「生産管理システムランキング」も是非ご覧ください。生産管理システムは、自社の製品・生産方式・企業規模などに適したものを導入しないと、得られるメリットが限定されてしまいます。事前適合性チェックや生産管理システムを選ぶ前に押さえておきたいポイントも解説していますので、製品選びの参考にしてみてください。