製造業に必須の品質検査とは?信頼性を高めるための基本から実例まで解説
公開日:2024年07月26日
最終更新日:2024年09月26日
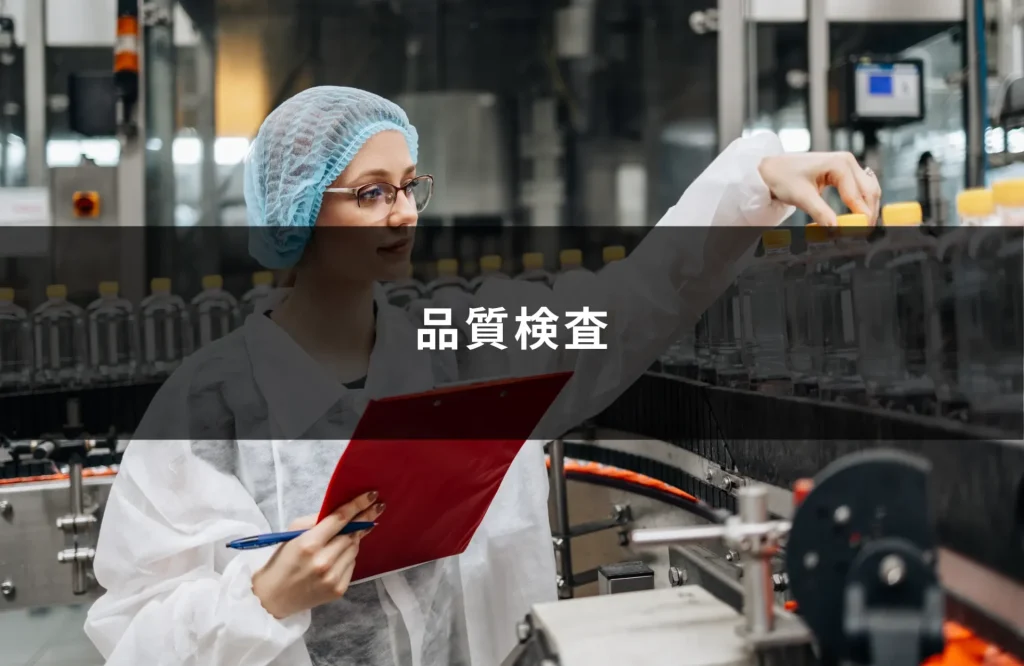
品質検査は、製造業において欠かせないプロセスです。本記事では、品質検査の基本から具体的な検査方法、そしてメリット・デメリットについて詳しく解説します。また、実際の品質検査の流れから、重要性、効率化のための手法やデータ解析も含めた活用事例まで、わかりやすく解説します。製造現場での品質向上とトラブル防止に役立つヒントを提供します。
品質検査とは何か
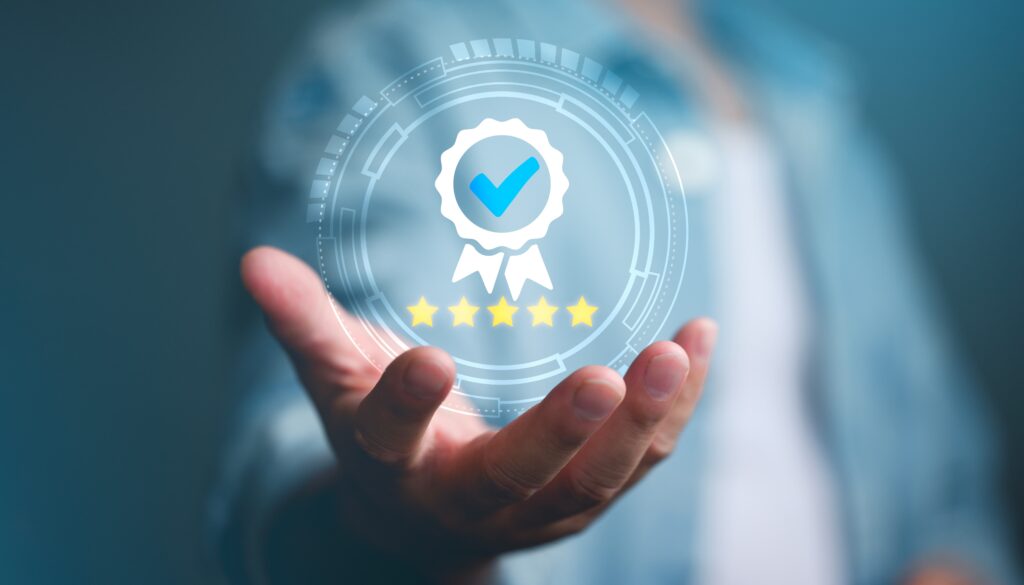
品質検査は、製造工程の各段階で実施されるプロセスです。これにより、不良品の発生を未然に防ぎ、お客様への不良品の流出を防止します。製品の信頼性を確保するための重要な工程であり、お客様の満足度を高めるために不可欠です。
品質検査にはさまざまな方法があり、製品の特性に応じた手法を使うことで、製品全体の品質を総合的に評価します。以下では、品質検査の重要性、目的について詳しく解説します。
品質検査はなぜ重要性なのか
品質検査は、製品の信頼性を保ち、お客様の満足度を維持するために非常に重要です。品質検査を怠ると、不良品が市場に出回り、企業の信頼を失うリスクがあります。また、不良品の修理やリコールには多大なコストがかかります。顧客満足を高めるために必要な「品質マネジメントシステム(QMS)」の推進においても、品質検査は重要といえます。
さらに、品質検査を通じて、製品の品質不良や生産設備のトラブルを早期に発見することで、無駄なコストを削減し、製品全体の生産効率を向上させることができます。
品質検査の2つの目的
品質検査の主な目的の一つは、製品が設計通りに作られているか、品質基準を満たしているかを確認することです。これにより、お客様に不良品を届けず、高品質な製品だけを提供できます。
もう一つの目的は、不良品を早期に発見し、製造工程の早い段階で修正することです。製造が進むと、多くの材料や加工が加わり、不良品一つあたりのコストが高くなるためです。また、品質検査を通じて得られるデータを分析することで、製造プロセスの改善点を特定し、全体的な品質を向上させることができます。
具体的な検査方法
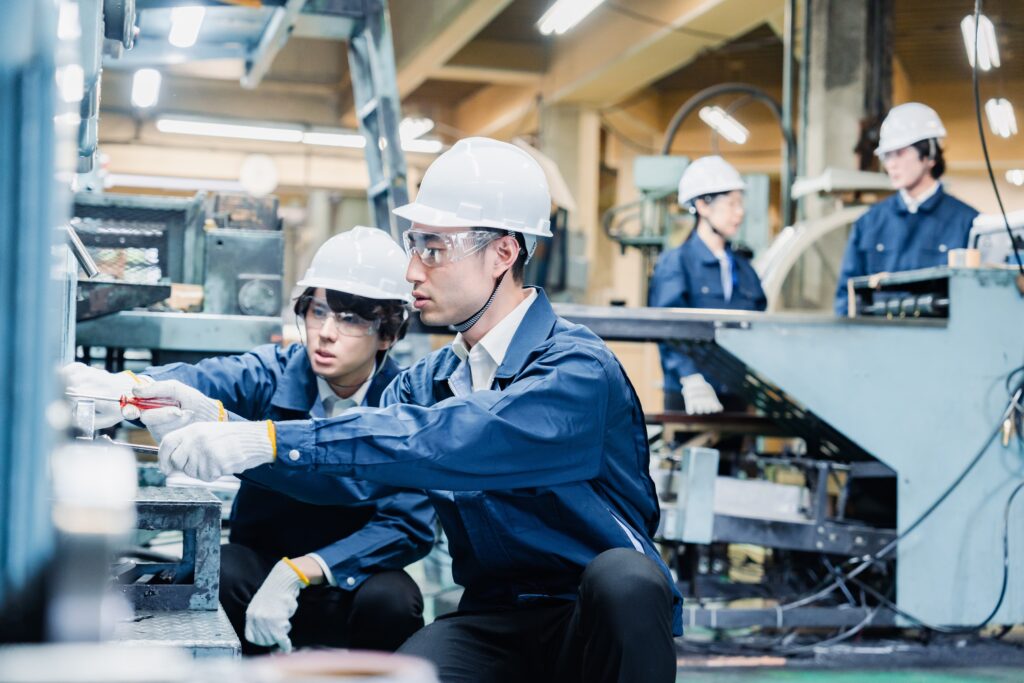
品質検査にはさまざまな方法があり、それぞれの方法は目的に応じて選択します。例えば、以下が代表的な品質検査方法です。
- 外観検査
- 寸法
- 重量検査
- 機能・性能検査
- 材料・成分検査
これらの検査方法を組み合わせて使用することで、製品の品質を総合的に評価することができます。それぞれの検査方法には特定の機器や技術が用いられ、検査の精度と効率を高めるために最新の技術が導入されています。
外観検査の方法とポイント
外観検査は、製品の見た目の品質を保証するための基本的かつ重要な工程です。製品の外観を目視やカメラで確認し、傷や汚れ、変形、色むらなどの異常がないかをチェックします。従来は、検査員が直接目で製品を見て検査することが主流でしたが、検査員の疲労や個人差による影響を受けやすいというデメリットがありました。
近年では、カメラやセンサーを使って自動的に製品の表面をスキャンし、画像処理技術を組み合わせる方法が増えてきました。この自動外観検査は、高速かつ一貫した検査が可能で、人間の疲労や個人差の影響を受けないというメリットがあります。しかし、すべての欠陥を完全に検出することは難しいため、他の検査方法と組み合わせることが望ましいです。
寸法・重量検査の進め方
寸法・重量検査は、製品が設計通りのサイズや重さであるかを確認するために行われます。寸法検査では、ノギス、マイクロメーター、3次元測定機などの精密機器を使って、製品の長さ、幅、高さ、内径、外径などを測定します。重量検査では、精密天秤や台秤、ロードセルなどの計量機器を使って、製品の総重量や部品ごとの重量を測り、重量分布が均一であるかを確認します。
これらの検査を行うことで、部品が正確に組み合わさるかどうかを確かめ、製品の性能や安全性を保証します。近年では、レーザー測定器や重量センサーの精度が向上し、より迅速かつ正確な測定が可能となっています。
機能・性能検査の手法
機能・性能検査は、製品が設計通りに動作し、期待される性能を発揮するかどうかを確認するための重要なプロセスです。この検査を行うことで、製品が使用目的に適していること、製品が正常に動作して安全であることを確認します。代表的な機能・性能検査として、以下のような方法があります。
- 電気的試験:通電試験、絶縁試験
- 機械的試験:耐久試験、振動試験、衝撃試験
- 環境試験:温度試験、湿度試験、耐水試験
- 化学的試験:腐食試験
- 機能試験:動作テスト、機能チェック
材料・成分検査の基準
材料・成分検査は、製品の材料や成分が決められた品質基準や安全性を満たしているかを確認するために行います。多くの場合、そのままの形では分析できないので、適切なサンプルを採取し、前処理を行います。
例えば、化学分析ではサンプルを薬品に溶かし、微生物検査ではサンプルを培養します。高精度な分析機器を使うことで、ごくわずかな成分を確認したり、異物の混入を検出したりすることができます。代表的な材料・成分検査として、以下のような方法があります。
- 化学分析:材料の化学的成分を調べます。
- 物理的検査:材料の硬さや引っ張り強さなどを調べます。
- 微生物検査:食品や医薬品の微生物汚染を確認します。
- 環境試験:材料が温度や湿度などの環境条件に耐えるかどうかを試します。
品質検査のメリット・デメリット
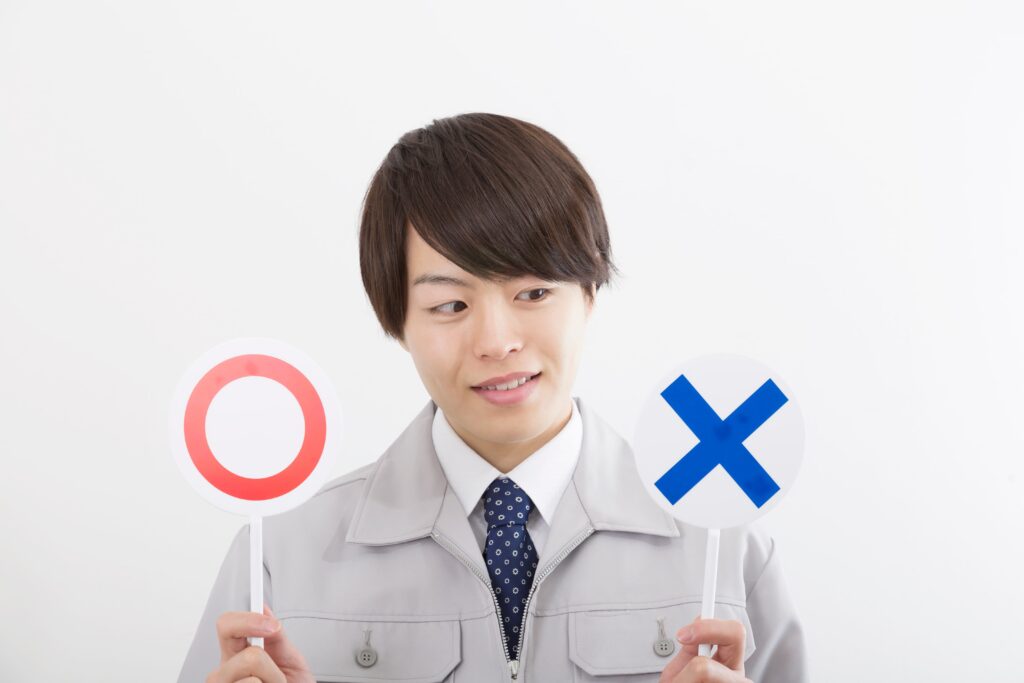
品質検査を行うことで、多くのメリットがあります。例えば、品質保証や品質管理がしっかりでき、お客様の信頼を得ることができます。一方で、検査にはコストがかかったり、時間がかかることもあります。品質検査を効果的に行うためには、これらのメリットとデメリットを理解し、適切なバランスを取ることが重要です。
品質検査のメリットとは?
品質検査の最大のメリットは、不良品の発生・流出を防ぎ、製品の品質を保証できることです。これにより、顧客満足度を向上させ、企業の信頼性を高めることができます。また、品質検査は製造プロセスの改善点を特定し、生産効率を向上させるための重要なデータを提供します。
長期的には、製品の信頼性が向上し、リピート顧客の増加や市場シェアの拡大につながります。さらに、品質検査によって不良品発生量を減らすことで、リコールや返品対応にかかるコストを削減できます。
品質検査のデメリットとは?
品質検査の最大のデメリットは、検査にコストや時間がかかることです。特に詳細な検査を行う場合、専用の設備や熟練した検査員が必要となり、コストが増加します。また、検査に時間がかかると、製造全体のスピードが遅くなることもあります。
さらに、破壊検査と呼ばれる、製品を意図的に壊して性能を確認する検査方法もあります。この場合、検査のために製品が失われることがあります。しかし、適切な検査方法を選び、効率的に運用することで、これらのデメリットを最小限に抑えることができます。
品質検査の流れ
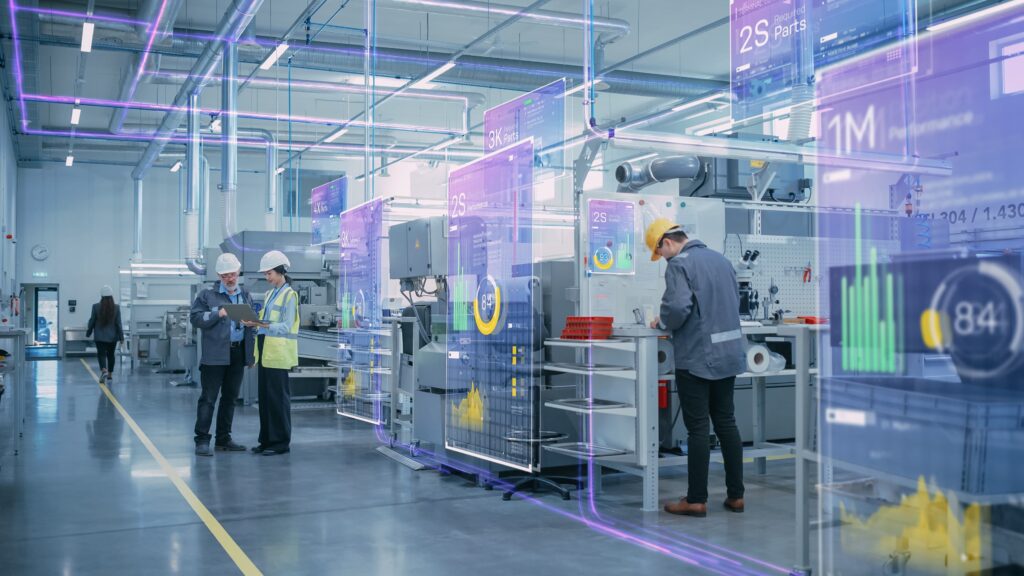
品質検査は、受入検査、工程内検査、最終検査の3つの段階で行われます。受入検査では納入品の品質を確認し、工程内検査ではの品質を管理し、最終検査では製品の品質を保証します。これにより、製品が各段階で品質基準を満たしているかを確認し、不良品の発生を防ぎます。各段階での適切な検査が、最終的な製品品質の維持・向上に繋がります。
受入検査:納入品の品質確認
受入検査は、外部から納入された部品や原材料が品質基準を満たしているか確認するために行います。これは品質管理の一環で、製造工程に入る前に不良品を防ぐことが主な目的です。受入検査を行うことで、不良品の流入を防ぎ、製造工程の効率を高めることができます。
また、供給業者が適切に品質管理できる体制かどうかを確認し、品質マネジメントシステムの一環として、製品の信頼性を高めるための重要な第一歩にもなります。
工程内検査:製造途中の品質管理
工程内検査は、製造の途中で行う品質検査です。この検査は、不良品が次の工程に進まないようにし、早い段階で品質問題を見つけて対策を講じることを目的としています。これにより、不良品の流出を防ぎ、手直しや再製造にかかるコストを削減できます。
工程内検査は、現場に近い場所でリアルタイムに行うことが求められ、手間のかからない方法が良いとされます。製造プロセスを安定化させ、製品の生産性と信頼性を高めるために非常に重要です。
最終検査:製品の品質保証
最終検査は、製品が完成した後に行う品質検査です。この検査では、製品が設計仕様や品質基準をすべて満たしているかを確認します。これにより、不良品が市場に出回らないようにし、お客様に高品質な製品を提供できます。また、製品が法律や業界の基準を守っているかもチェックします。最終検査は、製品の品質を保証するための最後のステップであり、製品の改善点を見つけ出し、次の製品に反映させるための重要な情報源でもあります。
品質検査の効率化
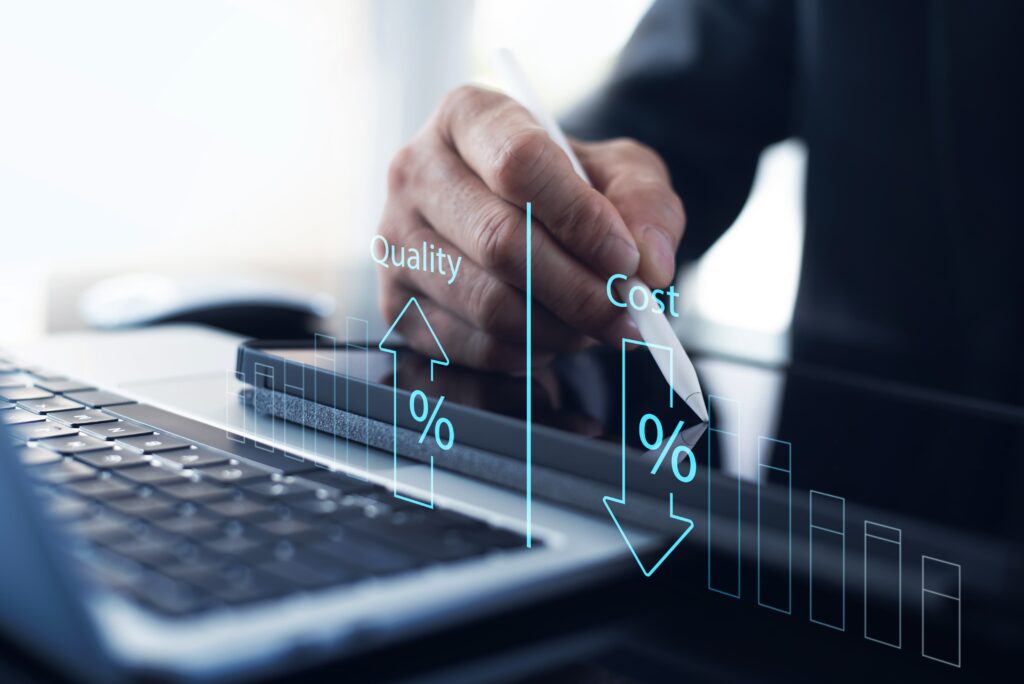
品質検査の効率化は、検査精度の改善、検査時間の短縮、自動化などの方法で実現できます。これにより、検査コストを削減し、生産性を向上させることができます。効率化のための具体的な方法を導入することで、品質検査の全体的なパフォーマンスを向上させることができます。最新技術の導入やプロセスの見直しが鍵となります。
検査精度の改善方法
検査精度の改善には、検査機器の定期的な校正が必要です。これにより、機器の測定誤差を最小限に抑え、正確な検査結果を得ることができます。次に、検査員の教育と訓練を強化することが重要です。熟練した検査員は、微細な欠陥や異常を見逃さずに検出できるため、検査精度が向上します。
検査プロセスの標準化も欠かせません。検査の一貫性を保ち、作業者によるばらつきを減らすために、統一された検査手順を確立することが必要です。全ての検査員が同じ基準で検査を行うようにすることで、検査結果の信頼性が向上します。
検査時間の削減
効率的な検査方法を採用し、無駄な工程を省くことで、全体の生産時間を短縮することができます。また、検査個数の判断も、検査時間の削減に大きく影響します。全数検査を行っており、不良率が低い場合は、抜き取り検査も検討できる可能性があります。
時短化・自動化の取り組み
カメラ画像を自動解析する検査やX線・レーザーを用いた検査など、最新の自動化技術を導入することで、目視検査や手動検査にかかる時間を短縮できます。また、サンプルを自動的に測定器へ送り込む装置やシステムを導入することで、人手を減らし、効率化を図ることが可能です。
これらの検査結果を製品管理システムに取り込むことで、データの照合や解析を短時間で確実に行うことができます。これらの方法を組み合わせることで、検査時間を大幅に短縮し、製造効率を向上させることができます。
品質検査の活用事例
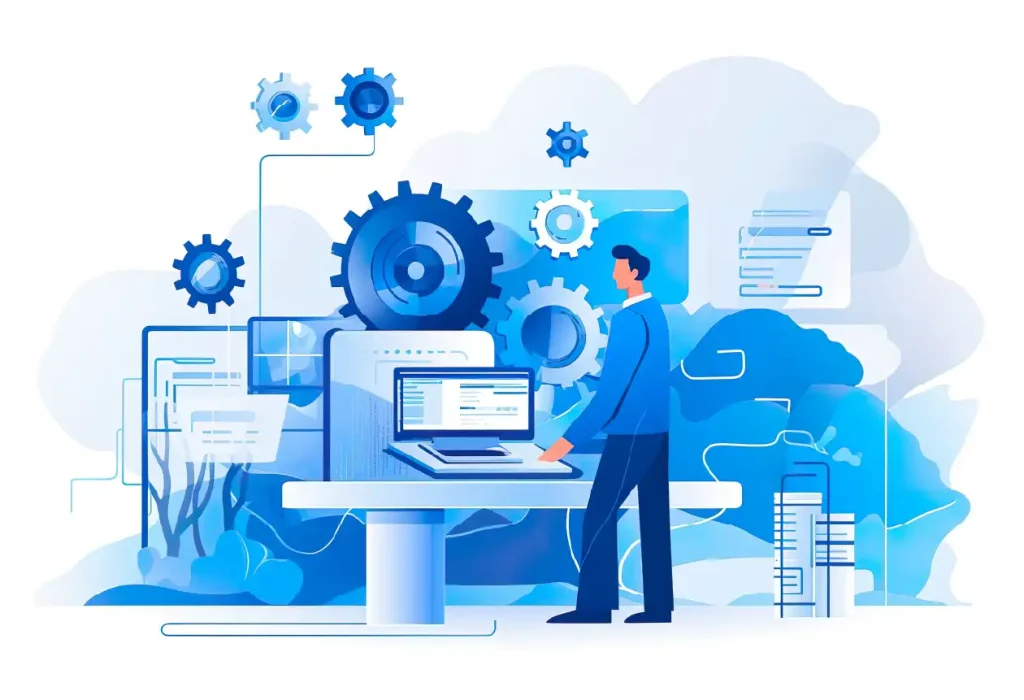
品質検査の活用事例としては、生産トラブルの早期発見と解決、品質不良の改善などがあります。これらの事例を通じて、品質検査の重要性とその効果を具体的に理解することができます。品質検査の効果的な活用は、製造業における品質管理の成功に直結します。
生産トラブルの早期発見と解決事例
品質検査は、生産トラブルの早期発見と解決に役立ちます。例えば、熱処理設備のヒーターが損傷し、製品に十分な熱が加わらないトラブルが発生したとします。この場合、熱処理後の工程内検査で加熱不良が判定されれば、熱処理設備に問題があると判断できます。これにより、生産を一時中断し、設備を修理することが可能です。
適切な工程内検査がない場合、最終検査で異常が検出されるまで問題が見逃され、結果として不良品が大量に発生してしまいます。このように、リアルタイムでの品質モニタリングは、生産トラブルの早期発見に非常に有効です。適切な工程内検査を行うことで、トラブルを早期に発見し、迅速に対応することができるため、製品の品質を維持し、コストを削減することができます。
品質検査データの収集・解析
品質検査データを収集し、解析することは、検査精度の向上に大いに役立ちます。定期的な検査を行うだけでなく、得られたデータを分析することで、品質トレンドや問題点を把握し、予防的な対策を講じることができます。
例えば、熱処理製品の場合、品質検査データから時間経過とともに加熱不良が徐々に増えていることが分かるとします。このデータを基に加熱不良を予測し、不良品が発生する前に設備を修繕することで、生産トラブルを未然に防ぐことができます。
データ分析ツールを活用して、リアルタイムでデータをモニタリングし、結果をフィードバックすることも重要です。これにより、迅速な対応が可能になり、品質改善に繋がります。データの収集と解析は、品質管理の重要な一環として、製品の品質を維持し、向上させるために欠かせません。
一例として、生産管理システムで検査管理も行っているロボット機器製造会社があります。工程検査での検査項目をシステム上で管理することで標準化し、検査結果データを分析することで、必要な検査項目の精査にも活用されています。
より詳しい事例はこちら:
生産情報・検査情報を一元管理!手書き・エクセル作業をシステム化し、生産拡大時の品質リスク対策に成功
品質検査の最終目標:信頼性と生産性の向上
品質検査は、製造工程の各段階で行われる重要なプロセスであり、不良品の発生を防ぎ、製品の信頼性を確保するために欠かせません。具体的な検査方法やメリット・デメリットを理解し、効率的に品質検査を実施することで、製品の品質を高いレベルで維持することができます。
また、検査データを収集・解析することで、品質トレンドを把握し、製造プロセスの改善点を特定することも重要です。効率的な品質検査の実施は、製品の生産性を高め、コスト削減にも繋がります。品質検査の重要性を理解し、適切な方法を選び、効率的に運用することで、製品の品質と企業の信頼性を高めることができます。
22種類の生産管理システムをランキングで比較
初期費用相場や選び方のポイントをチェック
生産管理システムをそれぞれの特徴や初期費用相場などで比較したい場合は、「生産管理システムランキング」も是非ご覧ください。生産管理システムは、自社の製品・生産方式・企業規模などに適したものを導入しないと、得られるメリットが限定されてしまいます。事前適合性チェックや生産管理システムを選ぶ前に押さえておきたいポイントも解説していますので、製品選びの参考にしてみてください。