ポカヨケ対策は仕組みが全て:導入メリット、製造工程飛ばし・ラベル貼り間違いの対策事例を紹介
公開日:2020年03月03日
最終更新日:2025年01月22日
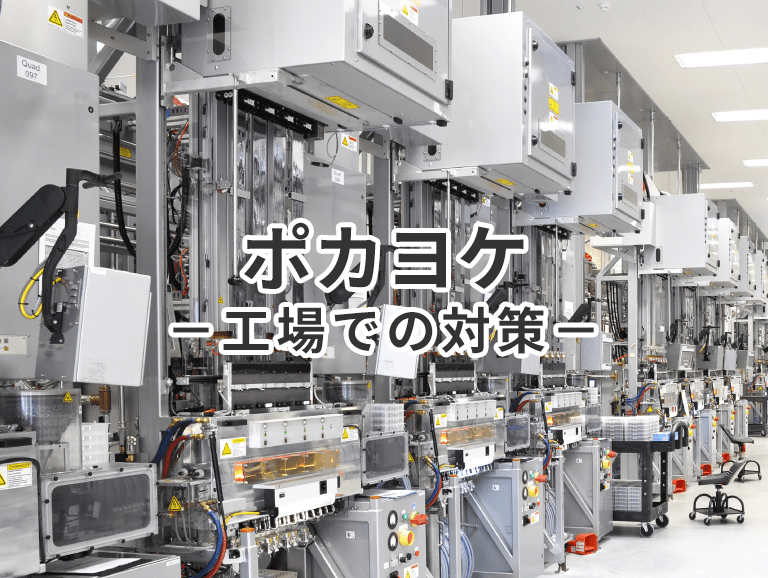
ポカヨケは、ヒューマンエラーによる作業ミスを防ぐための仕組みで、安全性・品質・生産性の向上に寄与します。運用面での改善であるソフト対策に加え、専用装置や自動化装置導入などのハード対策を組み合わせるとより効果的です。
本記事では、ポカミスの主な原因、ポカヨケ導入のメリットに加え、実際に工場で採用されている工程飛ばしやラベル貼り間違いへの対策など、低コストで実施可能なポカヨケを紹介します。
ポカヨケとポカミス
ポカヨケとは何かを知るためには、製造業におけるポカミスについても知る必要があります。
ポカミスとは:ヒューマンエラーが起こす作業ミス
ポカミスとは、うっかりミスや不良のことで、より具体的には作業者の不注意や勘違い、誤解などにより発生する作業ミスを指します。特に製造現場では、些細なミスが重大な品質不良に繋がったり、安全上大きな問題となったりします。
ポカミスの完全な排除は難しいですが、適切な対策を行えば発生頻度を大幅に減らすことが可能です。
ポカヨケとは:ポカミスを防ぐ仕組み
ポカヨケとは、日本語の「ポカミス」と「ヨケる」を組み合わせた言葉で、作業ミスを未然に防ぐための工夫や仕組みを指します。これには現場での簡易な仕掛けや装置の導入から、作業工程や手順の改善まで幅広い取り組みが含まれます。
ポカヨケには大きく分けて次の2つの考え方で、対策を行います。
- そもそもミスを発生させない
- 速やかにミスを検知して不良品を流出さない
例えば、「そもそもミスを出さない」という考え方ではUSBポートSDカードが挙げられます。Type AのUSBコネクタは非対称な形で、誤った方向で抜き差しできないようになっています。また、Type Cの場合、USBポートのコネクタが対称な形状に設計されているため、間違った方向が存在しない作りとなっています。
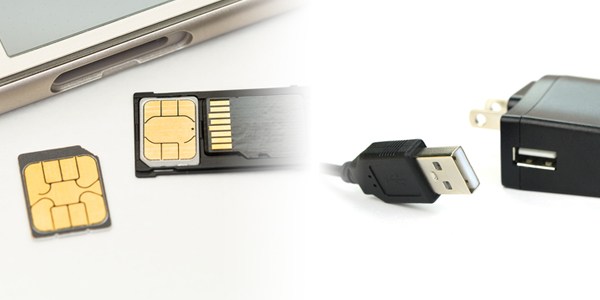
しかし、製品によっては、物理的な対策ができない場合もあります。その場合、ミスの発生そのものは許容し、速やかにミスを検知して不良品を流出させないようにします。例えば、組立後にセンサーを用いて、部品の有無や取付位置の正確性を自動検査する方法が挙げられます。ミスや不良が起こった際に「エラー音」や「ランプ」でお知らせし、その場で迅速な対応を行うことで、不良品が次工程に流れるのを防ぎます。
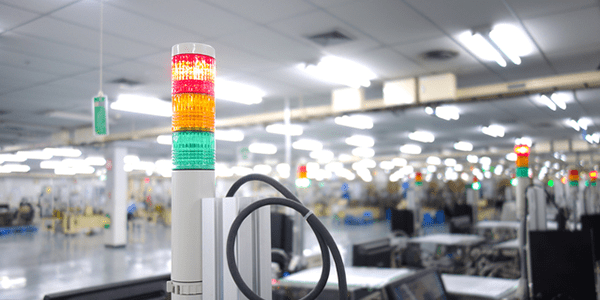
ポカヨケを行う際は原因を考えて対策をすること
ポカヨケを行う際にはその原因もしっかりと考え、なぜミスや不良が起こってしまうのかということも考えながら、対策をしていく必要があります。
AのボタンとBのボタンをよく間違えてしまう場合、「AとBの形が似ているから間違ってしまう」場合と「Aの方がBよりも目立ってしまうからついAを押してしまう」場合とでは対策の方法が違ってくるでしょう。
よくあるポカヨケとして以下のような工夫が多く使われています。このような事例を参考にしながら、ミスや不良の原因に合ったポカヨケを導入するようにしましょう。
ポカヨケを導入するメリット
ポカヨケの導入には、安全面、品質面、生産性の観点で様々なメリットがあります。
安全性を確保できる
ポカヨケの導入は、作業者が安全に作業できる状況を確保します。特に危険な作業では、ポカミスが大きな事故につながる可能性もありますが、仕組みによってリスクを大幅に低減できます。
例えば、プレス機では小型装置でも数トン以上の圧力で金属などを圧縮するため、作業者の手が挟まれるリスクは現場の重大な安全課題です。このリスクに対するポカヨケの一例が、両手操作方式の採用です。この仕組みでは、作業者が両手でスイッチを同時に押しつづけなければ動作しないよう設計されています。両手が操作に使われるため、片手が誤ってプレス機の可動部分に触れる可能性を完全に排除できます。
このように、ポカヨケは安全対策として非常に効果的であり、多くの現場で採用されています。
不良発生が減る
ポカヨケの実施は、品質不良の発生を大幅に減少させる効果があります。特に、不良品の手直しができない製品や、手直しに多大な労力がかかる製品では、その効果が一層大きくなります。
例えば、部品の取り付けや組み立て工程では、ボルトの取り付け誤りなどのポカミスが製品不良に直結し、手直しが必要になるケースがあります。また、医薬品原薬の製造現場では、誤って異なる原料を投入してしまうと手直しが不可能で、すべて廃棄するしかない場合もあります。
こうした場面でも、十分なポカヨケが導入されていれば、これらのポカミスを未然に防げます。その結果、不良発生が大幅に減少し、製品の品質のばらつきも改善されることが期待できます。
生産性が上がる
ポカヨケの導入は、作業効率の向上にも寄与します。
例えば、倉庫から工程内への部品供給でポカミスが起こると、製造ラインが停止し、リカバリー作業が発生します。ポカヨケを行うことで、必要なタイミングで必要な現場へ正しい部品が確実に供給できるようになり、ライン停止のリスクを大幅に低減できます。また、ミスによって発生していた余計な作業がなくなった結果、生産性が改善されます。
現場の多能工化を加速できる
ポカヨケは結果として作業の標準化を実現し、多能工化を推進するための環境が整備されます。
具体的には、専用治具などを用いた作業手順の見える化によって、熟練度・知識が乏しい作業員でも高精度な作業が再現しやすくなります。また、センサーや検知システムによりミスの検知が容易となり、作業精度が更に向上します。これらの取り組みは、現場における属人化からの脱却によって、作業標準化が容易となることを意味します。
その結果、教育や習熟度が課題となって進まない多能工化を加速させ、工場全体でフレキシブルな人員配置が可能となります。
品質規格にも対応できる(IATF16949要求事項10.2.4)
自動車産業向けの品質規格IATF16949では、不良品の発生・流出を防ぐためにポカヨケが求められています(要求事項10.2.4)。具体的な要求事項(抜粋)は次の通りです。
10.2.4. ポカヨケ
組織は適切なポカヨケ手法の活用について決定する文書化したプロセスを持たなければならない。
このように、製造プロセスにおけるポカヨケは、工程安定性を高めるだけでなく、品質規格への適合度を高める基礎的な対策の一つでもあります。
IATF16949については、こちらで詳しく解説していますので、必要に応じて参照してみてください。
ポカミスの主な原因
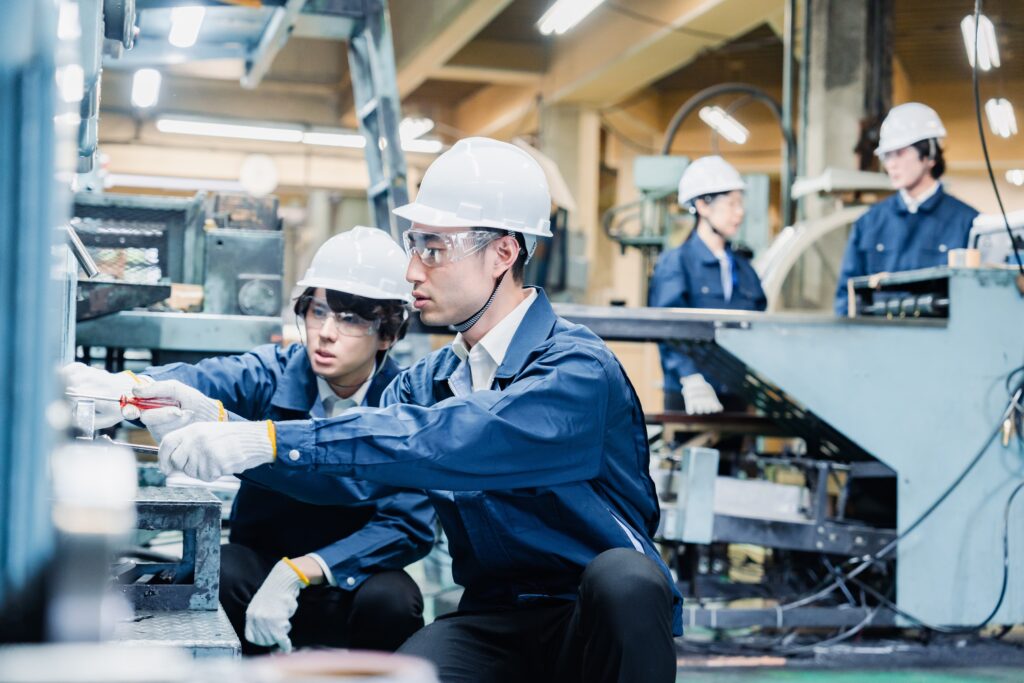
ポカヨケを実施する前には、ポカミスの原因を十分に分析したうえで対策することが必要です。ここでは、大きく分けて、人、環境、システム・規則の観点での原因について、詳しく説明します。
人に起因するもの
ポカミスの大きな課題の一つに、作業者自身の行動や判断によるミスがあります。具体的には、以下のような例が挙げられます。
- 注意不足:疲労やストレスによって集中力が低下し、部品の取り付けミスが発生する
- 勘違い:部分的な作業指示で早合点し、異なる条件・仕様で製造する
- 経験不足:習熟度の浅い作業者が作業を行う際、誤って記憶した手順で作業する
このような原因でポカミスが起こってしまった場合、今後は細心の注意を払って作業しましょう、などの精神論で済ませてはいけません。疲労・ストレスの原因が長時間労働である場合、作業の合間に適切な休憩が必要です。また、このような人的ミスが起こりやすい状況を減らすシステム化を検討すべきでしょう。
環境に起因するもの
良好な作業環境を確保できてないこともポカミスの一因です。一例として、以下のような影響が考えられます。
- 照度不足:作業現場が暗いと、部品を誤認識したり、検査で見落としが起こったりしやすい
- 騒音:精神的ストレスによるミスを誘発する、口頭指示が聞き取りにくくなる
- 作業スペースの制限:狭い場所での作業は、作業難易度が高まる
- 温度条件:高温環境ではイライラを感じやすく、低温環境では疲労蓄積しやすい
このように、過酷な作業環境は集中力の欠如につながり、作業効率を低下させ、ミスの発生リスクを高めます。
システム・規則に起因するもの
作業手順やシステムが複雑でわかりにくい場合、作業者が誤った判断を下してしまう可能性があります。具体例として、以下のようなものが挙げられます。
- 識別しにくい現場表示
- 類似の部品を複数使用した製品設計
- 複雑すぎる作業手順・システム操作
例えば、AのボタンとBのボタンをよく間違えてしまう場合を想定します。詳しい原因分析を行ったところ、『Aの方がBよりも目立ってしまうからついAを押してしまう』作業者が複数いました。この事例では、ボタン形状・配置などによって識別性が悪いことで、ポカミスを誘発していた可能性が高いといえます。
ポカヨケのためのソフト対策
ソフト対策のポカヨケとは、人やプロセスに焦点を当てた方法です。現場で自主的に実践でき、比較的低コストで取り組めるのが特徴です。
ポカヨケのための教育による意識強化
作業者への教育を通じてポカミスに対する意識工場は、基本的な対策として広く実施されます。定期的なトレーニングやポカミス事例の共有をポカヨケ対策として行うことで、作業者がミスのリスクを常に意識できる環境を作ります。
こういった現場教育は、特に間違いやすい作業などでは比較的効果が出やすいですが、これ以外の対策と組み合わせて初めて有効性が高まります。多くの場合、教育をしたから大丈夫、とはならない点に留意しましょう。
作業手順の標準化・見える化によるポカヨケ
作業手順を標準化し、「見える化」することで、作業者全員が同じ基準で作業できるようになります。具体的には、図解入りの作業マニュアルを作業現場に表示する、作業現場に設置したモニターに手順をリアルタイムで表示するなどの工夫は、工場で多く採用されるポカヨケです。
これらは比較的低コストで実施できますが、作業手順書の作成に多くの工数が取られる割に、作業者はほとんど手順書を参照しないことも少なくありません。例えば、操作ボタンに操作順序の番号を付与するなど、作業時に自然と目に入る形で見える化するのが効果的です。
色による識別性向上によるポカヨケ
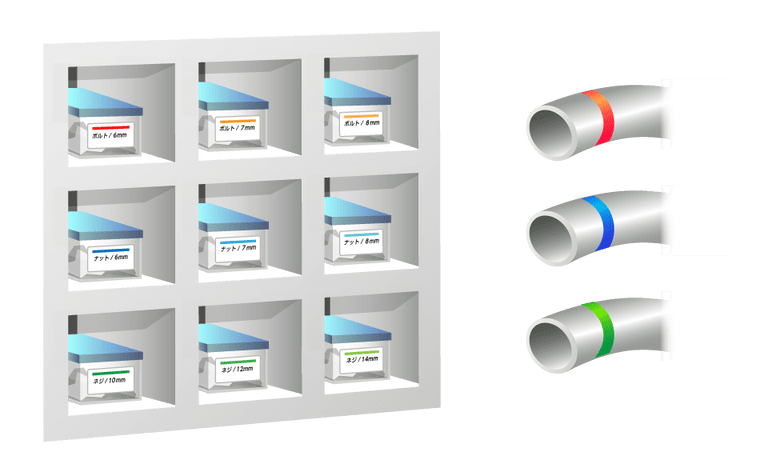
部品や手順への色分け表示によって、作業者が視覚的に正確な判断を行えるようにします。色分けの一例として、スイッチ・ボタン類の色分けが挙げられます。
- 赤色:非常用のスイッチ
- 黄色:異常時のリセット操作ボタン
- 青色:定常作業では使わない特殊操作用スイッチ
これらの色分けが工場内で統一されていれば、潜在意識レベルでポカヨケに大きく寄与できます。
ポカヨケのためのハード対策
ハード面でのポカヨケでは、設備やシステムを活用して物理的・機械的にミスを防ぎます。導入にあたって初期コストが高い傾向にありますが、ミスの発生率を大幅に減らし、長期的に安定した効果が期待できます。
作業環境の整備
作業環境の改善は、ポカヨケに大きく寄与します。作業場の工具配置を例に挙げると、工具箱から都度取り出す運用では、作業ごとに使う工具を探す作業が発生します。さらに、複数のプラスドライバーが同じ工具箱に収納されていると、取り違えが起こる可能性が高い状況です。
+3番ドライバーを使用すべき作業で、より小さい+1番ドライバーを用いてしまった場合、ビス穴を潰してしまうかもしれません。予め+3番ドライバーが一目で識別できるように並べておけば、取り違えリスクを大きく減らせます。前述の色によるソフト対策も組み合わせれば、ポカヨケの効果はさらに高まるでしょう。
このように、工具や部品を間違いにくいように明示して配置することで、作業ミスの未然防止が可能です。
専用治具や部品設計によるポカヨケ
ポカミスを防ぐための専用治具や部品設計は、非常に効果の高い対策です。具体的な部品設計・工程設計に関する対策例は次の通りです。
- 物理的仕組み:誤った方向・順序では部品が装着できない形状にする
- 工程飛ばしの対策:前工程が終わらないと次工程に進めない部品設計にする
- 出荷検査で検知:製品重量が規格内でないと出荷不可にして、取付忘れ品の流出を防ぐ
実際に、ポカヨケ装置のなかでも、ポカヨケ専用治具を導入している工場も少なくありません。製品を組立・加工する際に、部品の形に合った専用冶具を取り付け、部品の向きを間違えないようにする、というものです。専用冶具によって、誤った向きでは物理的に組立・加工ができないため、取り付け間違いによる不良は絶対に発生しません。
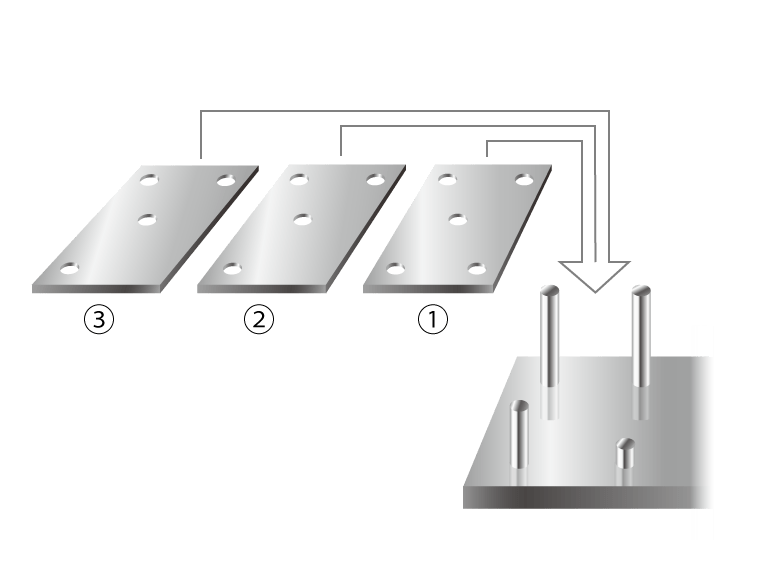
また、部品や道具をしまう際に、部品や道具の形に合った冶具を用意しておく、というケースも工場で散見されます。部品や道具の置き間違い対策として、簡単かつ有効なポカヨケです。
システム化・自動化によるポカヨケ
システム化・自動化は、ポカミスをゼロに近づける最も効果的な方法の一つです。製造工程でDX(デジタルトランスフォーメーション)を推進する中で、ロボットを活用して作業を機械に任せれば、人間によるミスをほぼ排除できます。
また、品質検査工程では、外観検査をカメラで撮影し、その画像を自動認識させることで、見逃しリスクを大幅に減らすことができます。ただし、自動化を進めるには、設備やシステムの導入が必要であり、そのコストが導入の大きな障壁となる場合があります。
また、自動化は大規模な設備投資だけを意味するわけではありません。作業実績の記録を紙帳票から電子化に切り替えることも、自動化の一例です。バーコードとハンディーターミナルを使用してシステム入力を行えば、作業実績登録を自動化できるため、入力ミスを防ぐポカヨケが実現できます。
バーコードリーダーによるポケヨケシステムを使った対策と事例
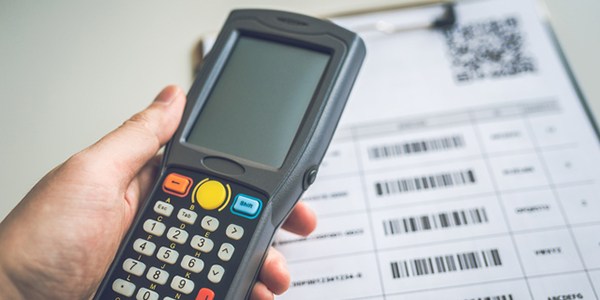
生産管理システムとバーコードリーダー(またはQRコードスキャンができるハンディ端末など)を併用して、ポカミスや工程抜け、誤出荷を防ぐ方法は、比較的低コストでも導入可能です。これにより、工場でよくある「入れ間違い」「選び間違い」「貼り間違い」「読み間違い」「見間違い」といったポカミスの撲滅を加速します。
ここでは、バーコードリーダーを使用することで、ポカヨケを達成した事例を紹介します。
コンビニ弁当のラベル貼り間違いを防ぐポカヨケ事例
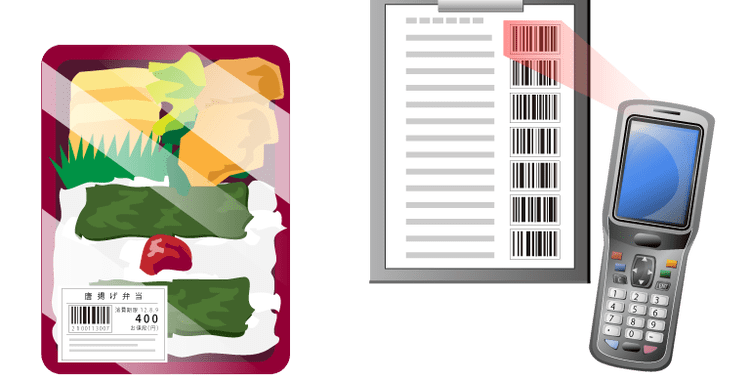
あるコンビニでは、弁当のラベルを事務所で一括発行し、それを現場に持ち込んで商品に貼り付ける仕組みを採用していました。しかし、ラベルと商品の照合を目視で行っていたため、ラベルの貼り間違いが散発するという課題がありました。
そこで、バーコードリーダーを活用したポカヨケシステムを導入しました。このシステムでは、次のような手順でラベル貼り付けを実施します。
- 本日生産予定の弁当の「商品名」や「賞味期限」を記載した台帳を事前に作成
- 現在生産している弁当のバーコードを台帳からバーコードリーダーで読み取り
- ラベルを貼る前に、ラベルのバーコードを読み取り、商品情報と照合
- (間違いがあれば即座にエラーを表示)
- ラベルと商品情報の一致をハンディターミナルで確認し、ラベルを貼り付け
この仕組みの導入により、年に1~2回発生していたラベルの貼り間違いはゼロになりました。
また、このようなバーコードリーダーを活用した「貼り間違い」のポカヨケは、食品以外の分野でも広く利用されています。例えば、従来は医薬品のJANコードを目視確認していましたが、バーコード読み取りによるシステム照合に置き換えることで、ポカミスを未然防止しています。
バーコードを使った在庫管理とハンディターミナルの選び方について、こちらの記事で詳しく解説していますので、ご興味がございましたら合わせて参照ください。
電子チップの選び間違いを防ぐポカヨケ事例
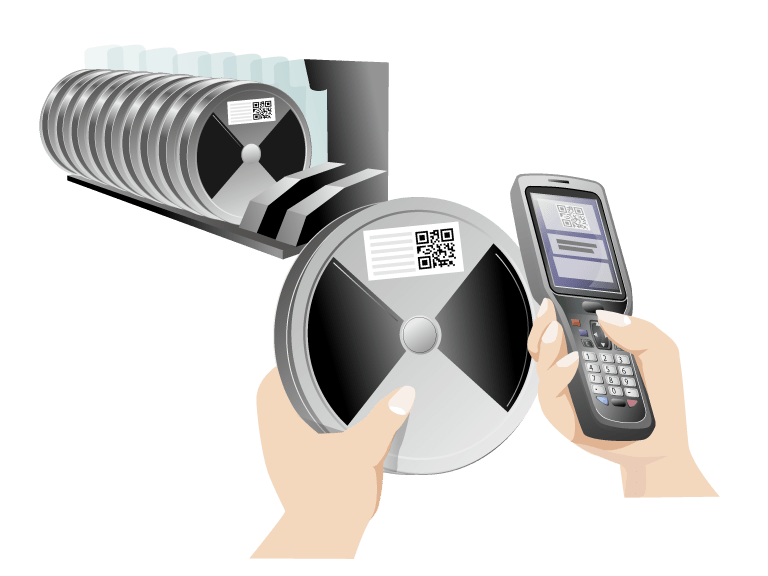
電子チップを基板に設置するための装置は、リール状の電子チップをセットし、自動で基板に配置する仕組みです。
工場内には何百種類もの電子チップがあり、その品番は長い文字列の最後の一文字が違うだけのものも多くあります。電子チップを1つでも間違うと製品不良となり、大きな損失につながります。しかし、人の目による確認だけであったため、間違いが発生しやすい状況でした。
そこで、バーコードリーダーを活用し、次のようなプロセスのポカヨケシステムを導入しました。
- 電子チップの台帳作成:あらかじめ電子チップの品番を台帳に登録する
- バーコードの貼付:リールや装置にバーコードを貼り付け、バーコードで識別可能にする
- バーコードの読み取りと確認:作業時にバーコードリーダーで読み取り、セットされたチップが正しいか照合する
- エラーの検出:万が一、間違ったリールがセットされている場合には、即座にエラーを表示し、作業を停止する
この仕組みにより、電子チップの選び間違いを防止し、製品不良のリスクを大幅に削減することができました。さらに桁数の多い照合を瞬時に行うことができるようになり、作業工数の削減も実現しました。
組立製品の工程飛ばしに関するポカヨケ事例
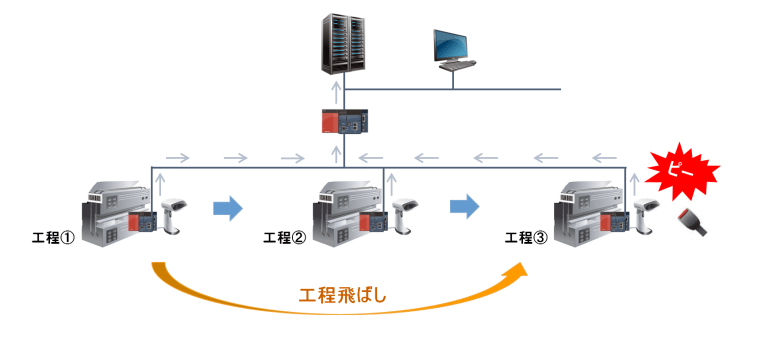
ある工場では、「ねじの締め忘れ」という工程飛ばしが原因の製品不良が課題になっていました。工程飛ばしが起こるとリコール扱いとなり、数億円の損害を生むケースもあります。そこで、バーコードリーダーを活用して、設備と連携したポカヨケシステムを構築しました。
まず、各工程において作業内容や部品情報を予め台帳に登録し、各部品にもバーコードを貼りつけて識別可能な状態にします。作業者が作業を行ったり、部品を設置した際に、作業者が台帳および部品のバーコードを読み取ります。もし、前の工程で部品のバーコードを読み込んでいない状態では、次工程でエラーを通知してラインが停止します。
このシステムにより、工程飛ばしによる製品不良を検知し、不良品の流出を防止する仕組みとなりました。このようなポカヨケシステムは、ミス発生確率を抜本的に減らす対策として活用されています。
その他の取り違え防止のポカヨケ事例
上記以外にも、食品業界や化粧品、医薬品業界などで、QRコードやバーコードを利用したポカヨケ事例が多く採用されています。具体的には次の通りです。
- 梱包する製品と梱包ケースの間違い対策のためのポカヨケ
- 資材取り間違いのポカヨケ
- 社内現品票と客先現品票の差し替えのポカヨケ
事例:【照合検品システム】製品ラベルと外装ラベルでの貼り間違いを0に
また、食品・化粧品・医薬品業界では、QRコード・バーコードにて「期限切れ原料の誤使用防止」を行う事例も増えつつあります。原料使用時にQRコードやバーコードによる照合を行い、原料の使用期限が切れている場合はアラートが出る仕組みです。実際に、この取り組みで誤使用・誤投入をゼロにし、年間数千万円規模の廃棄コストをゼロにした化粧品製造業の事例もあります。
事例:【化粧品/原料在庫管理システム】誤使用・誤投入0件、年間損失額の数千万円が0円に!ハンディ端末で工数削減・属人化解消も成功
バーコードリーダーでポカヨケを行う際に気を付けること
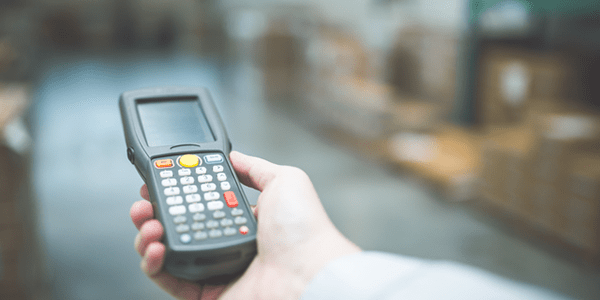
QR・バーコード管理でポカヨケを行う際に最も注意が必要なのは、コードの読み込み忘れです。この読み忘れをいかに防ぐかが、QRコードやバーコードによるポカヨケによる改善効果を発揮する鍵となります。
読み込み忘れを防ぐ仕組み
QRコード・バーコードの読み忘れ防止には、読み取りチェックシステムの整備や、読み込み履歴を保存して後で参照できるようにする方法が効果的です。
さらに、読み取りが完了しない限り次の工程に進めない仕組みであれば、確実なチェックが行われることになります。
生産管理システムとの紐づけ
QRコードやバーコードから取得したデータを生産管理システムと連携させると、ポカヨケの精度の更なる向上が期待できます。作業状況をリアルタイムに監視したり、不良発生時にも迅速に対応することが可能になります。
22種類の生産管理システムをランキングで比較
初期費用相場や選び方のポイントをチェック
生産管理システムをそれぞれの特徴や初期費用相場などで比較したい場合は、「生産管理システムランキング」も是非ご覧ください。生産管理システムは、自社の製品・生産方式・企業規模などに適したものを導入しないと、得られるメリットが限定されてしまいます。事前適合性チェックや生産管理システムを選ぶ前に押さえておきたいポイントも解説していますので、製品選びの参考にしてみてください。