カイゼンから始める現場改革:進め方から、改善案を考える具体的な切り口も紹介
公開日:2025年01月15日
最終更新日:2025年01月16日
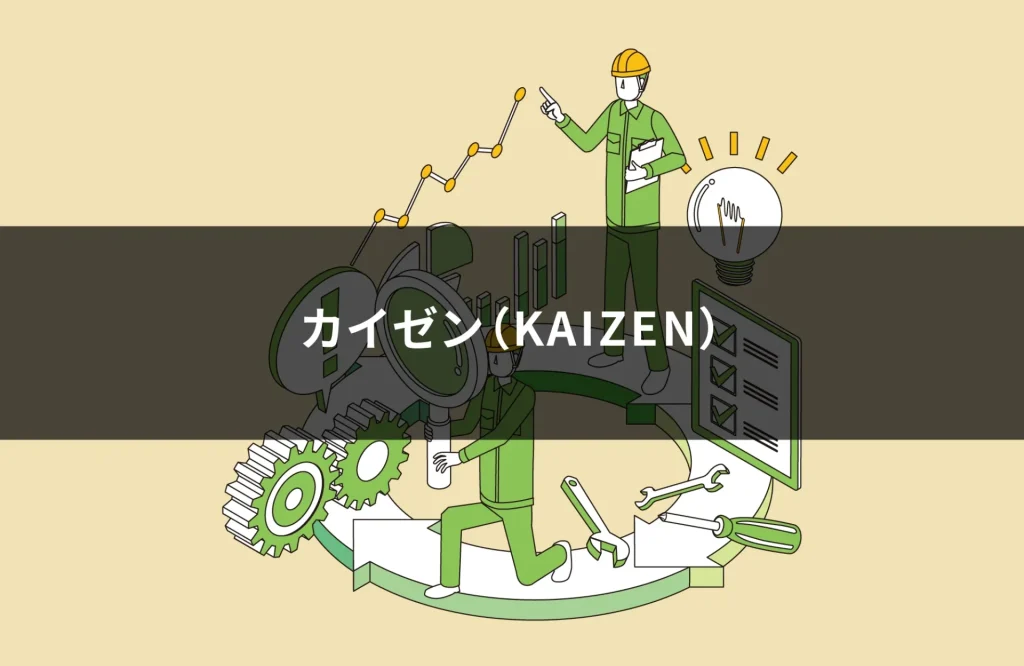
製造現場で生まれた「カイゼン」は、現場の従業員一人ひとりの知恵と工夫で小さな改善を積み重ね、大きな成果を生むアプローチです。トヨタ生産方式(TPS)の基礎となる3M(ムリ・ムラ・ムダ)の削減や、5Sの徹底による現場の効率化に関する考え方が鍵となります。
本記事では、カイゼンの方法を具体的な事例も紹介しながら解説します。さらに、継続的な改善を実現するためのPDCAサイクルの回し方、ECRSの4原則などの活用法なども解説します。
カイゼン(KAIZEN)とは?
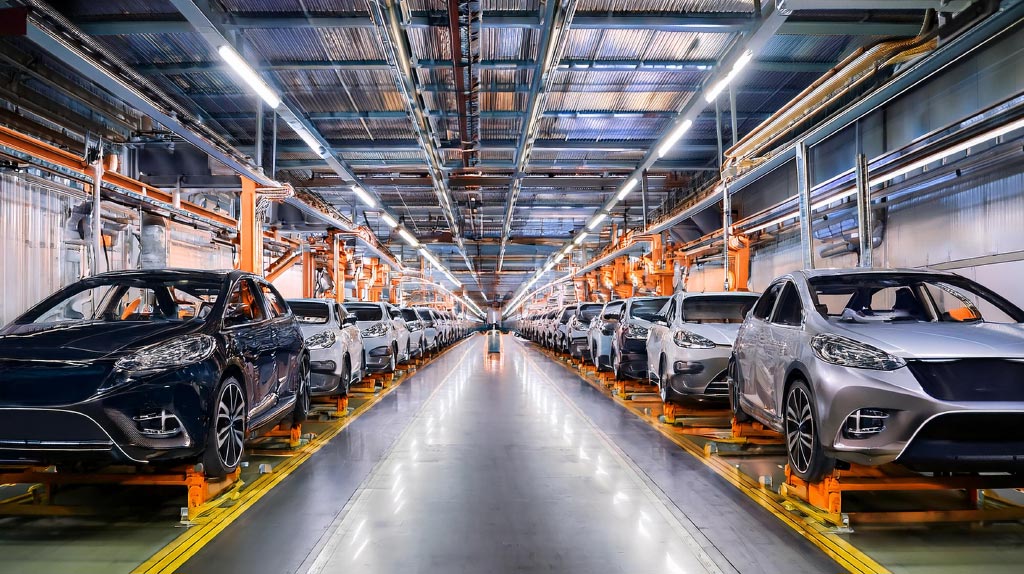
カイゼン(KAIZEN)とは、製造現場で働く人たちが主体となって業務の効率化を推進する取り組みです。現場で働く人々が主体となって、小さな工夫を継続的に積み重ねることで大きな成果を目指します。
トヨタ生産方式(TPS)から生まれた考え方
カイゼンの概念は、トヨタ生産方式(TPS)の中核的な概念の一つであり、「ジャストインタイム」と「自働化」を柱として、品質向上と効率化を追求します。TPSが目指す効率化や品質向上を実現するためには、トップダウンでの取り組みだけでは不十分であり、現場での主体的な工夫の積み重ねが欠かせません。
現場主導で、生産現場や日常業務で次に示す3つの観点で非効率を見つけ出し、解消します。
- ムリ:作業や設備に過剰な負荷がかかる状態
- ムラ:作業量や負荷のばらつきが大きい状態
- ムダ:付加価値を生まない行動や資源の浪費
このような着眼点を意識した上で、現場の知恵を活かしながら非効率を解消する取り組みは、カイゼンの一つの形です。結果として、効率化やコスト削減だけでなく、働きやすい環境の整備や品質向上にもつながります。このような現場主導の改善活動こそが、TPSを支えるカイゼンの本質と言えます。
製造現場を今よりもっと良くする活動
カイゼンは、「現状を良しとせず、常に改善を目指す」というシンプルな考え方に基づいています。望ましくない事象への対処だけに留まらず、大きな問題はないが「今よりも良い状態」を目指すものです。製造現場の従業員が主体的に課題を設定し、作業や仕組みを見直して効率・品質を高めます。この活動は、大規模な投資や劇的な改革ではなく、現場の日常的な努力を重視します。
例えば、以下のような取り組みが含まれます。
- 工具や部品の定位置管理:必要なものをすぐ取り出せる状態にする
- 作業の標準化:効率的な作業手順を定め、従業員全員がそれに従う
- ムダな在庫の削減:「かんばん方式」の徹底などで、保管スペースを圧縮する
このような取り組みは、QCサークル活動(品質管理サークル)として進めるケースもあります。現場の従業員がチームで課題を設定し、自ら分析して改善策を推進することで、現場主導での作業改善が促進されます。
カイゼン活動は、現場の知恵や工夫を活かした小さな改善の積み重ねです。これにより、効率化や品質向上が図られるだけでなく、従業員のモチベーションやスキルも向上します。長期的には大きな成果をもたらし、製造現場にとどまらず、あらゆる業界や業務に応用できる普遍的なアプローチです。
一般的な改善との違いは「継続的」かどうか
カイゼンと一般的な改善活動の最大の違いは、その「継続性」にあります。
一般的な改善は、解消すべき事象(問題)が明確であり、その問題を解決するために行われます。このため、問題が解決されれば取り組みは終了し、単発的な活動となることがほとんどです。
一方でカイゼンは、望ましくない事象への対処とは異なり、現場主体で自ら取り組むべき課題を探索し、改善を続けることが特徴です。このため、課題が解決しても活動が終わることはなく、継続的に業務効率や品質を継続的に追求します。
カイゼンの目的
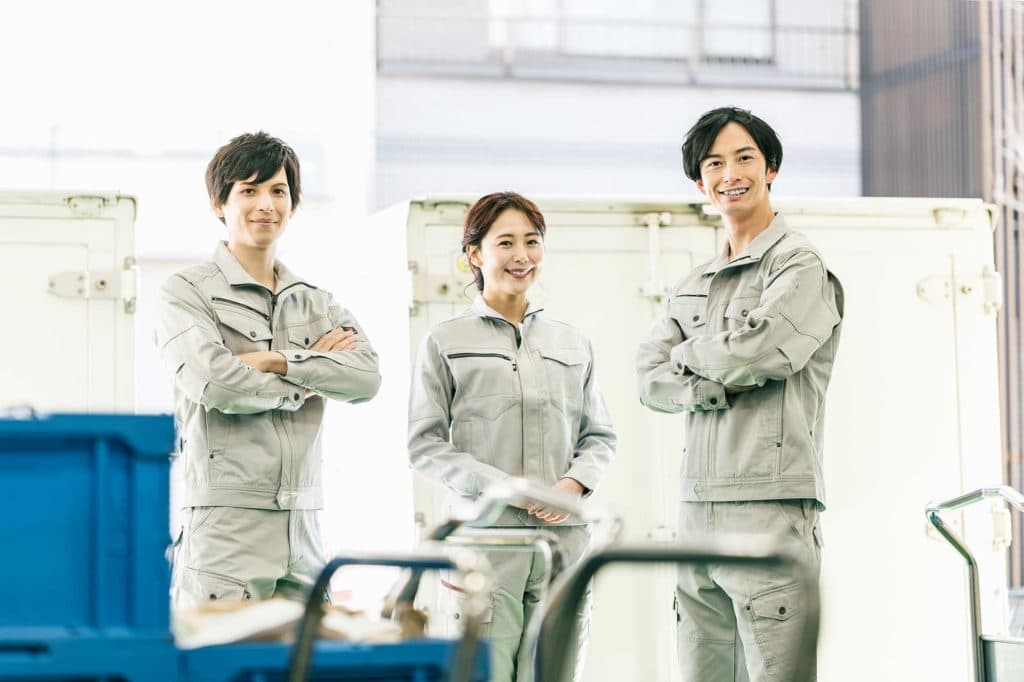
カイゼンは単なる効率化ではなく、現場の意識改革と文化形成を目指すものであり、組織全体の持続可能な成長を支える土台となります。カイゼンを推進する代表的な目的は、以下の通りです。
5S(整理・整頓・清掃・清潔・躾)を徹底する
5Sの徹底は、安全な作業環境を構築するための重要な取り組みで、カイゼン活動の基礎として位置づけられることも多いです。具体的な5Sは次のとおりです。
- 整理:必要なものと不要なものを区別すること
- 整頓:必要なものの位置を決めて、使いやすく並べておくこと
- 清掃:掃除をしてきれいな環境を保つこと
- 清潔:整理・整頓・清掃を意識して清潔な状態を保つこと
- 躾(しつけ):整理・整頓・清掃・清潔をいつでも実行できるように指導すること
カイゼンを進めることで、製造現場の一人ひとりが5S徹底の重要性に気づきを得ることが期待できます。トップダウンで指揮命令を下すのとは異なり、5Sは多くの現場で徹底する必要があるからこそ、現場の従業員が自らの気づきを通して取り組むことが重要です。
自発的な気づきによって、5S活動がより深く根付くと、生産性や品質の向上だけでなく、安全性の確保や職場環境の改善にもつながります。このように、現場主体のカイゼン活動を通じて、従業員自身が5Sの意義を実感し、継続的な改善が促進されます。
3M(ムリ・ムラ・ムダ)を削減する
3M(ムリ・ムラ・ムダ)の削減は、カイゼンの大きな目的の一つです。それぞれの意味は以下の通りです。
- ムリ:無理な作業で能力以上の過剰な負担がかかっていること
- ムラ:作業や生産の不均衡があること
- ムダ:値を生まない無駄な動作や時間のこと
これらの3Mは、生産性や業務効率化を妨げる要因であり、これを排除すれば現場の作業がスムーズになります。
カイゼンにおける課題設定では、これらのムリ・ムラ・ムダをなくす取り組みが多く選定されます。現場での小さな積み重ねを従業員が主体的に進めることで、「ムリ・ムダ・ムラは悪である」という意識が組織全体に浸透します。
たとえ個々のカイゼンで大きな成果が得られなかったとしても、組織全体での取り組みを合算すると、結果的に大きなコスト削減に繋がります。
従業員の課題形成力・解決力を養う
カイゼンの最大の目的は、従業員が自ら課題を発見し、解決する力を養うことにあります。
製造現場では、上意下達のルーティン作業が多く、業務のマンネリ化や従業員の受け身化が課題となりがちです。これを解消するために、カイゼンでは「今よりももっと良くするために何ができるか」を従業員自身が考え、テーマを設定して改善に取り組みます。この活動によって、従業員が現状から課題を発見・言語化する「課題形成能力」や、それを解決する課題解決力を向上することが期待できます。
組織の持続性・競争力を強める
カイゼンの最終的な目的は、組織全体の持続性と競争力の強化です。
5Sの徹底、3Mの削減、従業員の課題形成能力向上を通して、現場を基盤とした「継続的な改善文化」を育むことが目指されます。この取り組みでは、トップダウンの指示ではなく、現場従業員が主体的に改善ポイントを発見し、自ら解決を試みる力を養います。
こうしたカイゼン活動が現場まで浸透すると、組織の基盤が強固になり、持続性と競争力が高まるとともに、外部環境変化への対応力も強化されます。
カイゼンの進め方
効果的なカイゼンには進め方の定石があります。具体的には、以下の流れになります。
現状の分析
カイゼンの出発点は、現場の状況を把握し、改善ポイントを明確化することです。この段階では、「三現主義」(現場・現物・現実)を重視することが大切です。実際に現場を訪れて現物を観察し、現実をデータとして客観的に把握します。たとえば、現場で実作業を自分の目で確認し、作業時間や不良品の発生率、動線の無駄などの改善ポイントを具体的に記録し、現状を見える化します。
また、この際に「QC7つ道具」を活用すれば、客観的な見える化が可能です。これにより、データや論理的根拠に基づく改善策の立案がしやすくなります。
改善すべき課題・優先度の設定
現状分析の結果を基に、改善ポイントの優先順位をつけたうえで、改善すべき課題を設定します。このステップでは、目標を設定し、課題に対する優先順位を明確にします。
ある自動車部品の製造工程におけるカイゼン課題として、次の3点があったとします。
- 工具の定置位置の改善:工具の配置が不適切で、作業効率が下がる
- 作業エリアの照明改善:照明が暗く、作業精度が低下し不良品が発生する
- 一時保管エリアの拡張:仮置きスペースが狭く、作業動線が乱れる
課題に対する優先度をつけるため、それぞれについて、難易度、対策に要する期間、対策費用、取り組みに関するリスクを〇、△、×の3段階で評価しました。以下の表は、この評価結果をまとめたものです。これらの評価結果を総合すると、工具の定置位置の改善アイテムは最も〇の数が多く、ややリスクはあるものの最も優先すべきと判断できます。
課題 | 難易度 | 対策期間 | 対策費用 | リスク | 総合評価(優先度) |
工具の定置位置の改善 | 〇 | 〇 | 〇 | △ | 高 |
作業エリアの照明カイゼン | △ | 〇 | △ | 〇 | 中 |
一時保管エリアの拡張 | × | × | △ | × | 低 |
このように、取り組むテーマを優先順位付けして取り組むことで、費用対効果の高い対策を優先して着手することができます。
また、この課題設定の段階では、目標を数値化できれば、尚良いでしょう。たとえば、「工具の定置位置の改善により、60秒のタクトタイムを3秒改善する」のように、具体的な目標を掲げます。
カイゼンの案を出し合う
課題が決まったら、アイデアをチーム全体で出しあい、対策の方向性を協議します。この段階では、現場の作業員が積極的に参加し、実際の経験に基づいて、ブレインストーミング(ブレスト)を行います。
注意点としては、否定的な意見を控え、実現性の難しい案も含めて多くのアイデアを出すことです。管理者や一緒に参加するメンバーが必ずしも全ての現場事情を把握しているわけではないため、現場ならではの視点からアイデアを出すことを求めます。このようにして多様なアイデアをもとに、具体的な対策案を考えるのが望ましいと言えます。
以下の表は「工具の定置位置の改善」を例に挙げ、具体的なカイゼンの案を出した事例です。改善策を決めるまでの流れは次の通りです。
段階 | 検討内容の具体例 |
現状把握 | 作業員が工具を使うたびに作業台から離れる動作を観察 |
改善案のブレスト | 案①:工具を作業台の近くに吊るす 案②:使用頻度の高い工具を手元に配置する 案③:工具の固定ラックを導入する |
ブレスト案の整理 | 「工具の近接配置」という観点で、具体案を比較 |
優先順位付け | コストが低く、効果が大きい「使用頻度の高い工具を手元に配置」が最優先に。 作業員の意見を聞きつつ「手元への工具配置」を改善案として採用 |
PDCAサイクルを実施する
改善案が決まったら、PDCAサイクルを回して実行します。
前述の例のように、「工具の定置位置の改善」においては、使用頻度の高い工具を手元に配置することが改善案として挙げられます。この取り組みに関するPDCAサイクルの具体例を、次の表にまとめました。
Plan(計画) | 現状:箱にまとめて入っている工具から必要なものを都度探している 改善案:高頻度で使う工具を特定し、作業机の上に配置案を設計 目標:前工程の作業終了後、必要な工具を使い始めるまでの時間を50%短縮 |
Do(実行) | 工具使用頻度を1週間記録し、使用頻度上位5つを選定。 頻度の高い工具が手元に配置されるように、定置管理する |
Check(評価) | 工具取り出し時間を計測し、改善前後を比較 作業全体の効率改善を数値で確かめる ※作業員の意見を収集:使いやすさが十分か、新たな課題がないか、など |
Action(改善) | 目標達成時:新工具配置を標準化し、他の作業台に展開 目標未達成時:工具配置の再設計(頻度や配置方法を再検討) |
このように、目標に到達できるまで、PDCAサイクルを回して小さな改善を積み重ねていきます。
カイゼン活動を進める時のポイント
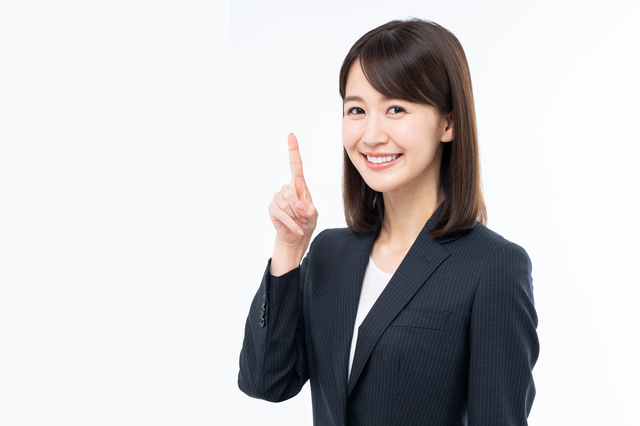
カイゼン活動を成功させるためには、チームで協力しながら自主的に進めていく姿勢が必要です。ここでは、具体的なポイントを詳しく説明します。
現場主導で行う
カイゼン活動はボトムアップ型アプローチで、現場の作業員が主体となって進めることが成功の鍵です。管理職などが一方的に指示するトップダウン方式では、現場の課題感や実現可能性が十分に考慮されないケースもあり、改善が形骸化しやすくなります。
現場の従業員は日々の作業を通じて、業務プロセスそのものや潜在的な課題を最も理解しています。その知見をフル活用することで、実現可能かつ効果的な改善が進められます。
現場主導でカイゼン活動を促す具体的なポイントとしては、例えば以下のような施策があります。
- 定期的な現場ミーティングの時間を設け、作業員全員で課題共有と解決策の議論を行う
- 成果に応じて表彰や奨励金支給を通して、改善活動への参加意欲を高める
作業工程を数字で見える化する
カイゼン活動で取り組む課題やその効果を検証するためには、現場の状況や作業プロセスを定量的に「見える化」することが不可欠です。データや数字を使って現状を定量的に示すことで、課題の重要性・優先順位を適切に評価でき、改善活動の達成度を把握しやすくなります。課題を見える化する具体例には、次のようなものがあります。
- 作業時間の計測:作業ごとに要した時間を計測し、効率の低い工程を特定する
- 不良品率の分析:不良品の数を工程別に記録し、改善できる箇所を洗い出す
- 在庫状況の視覚化:部品の在庫量を棚ごとにラベルで表示し、ムダな在庫や欠品を防ぐ
カイゼン案を考える具体的な切り口
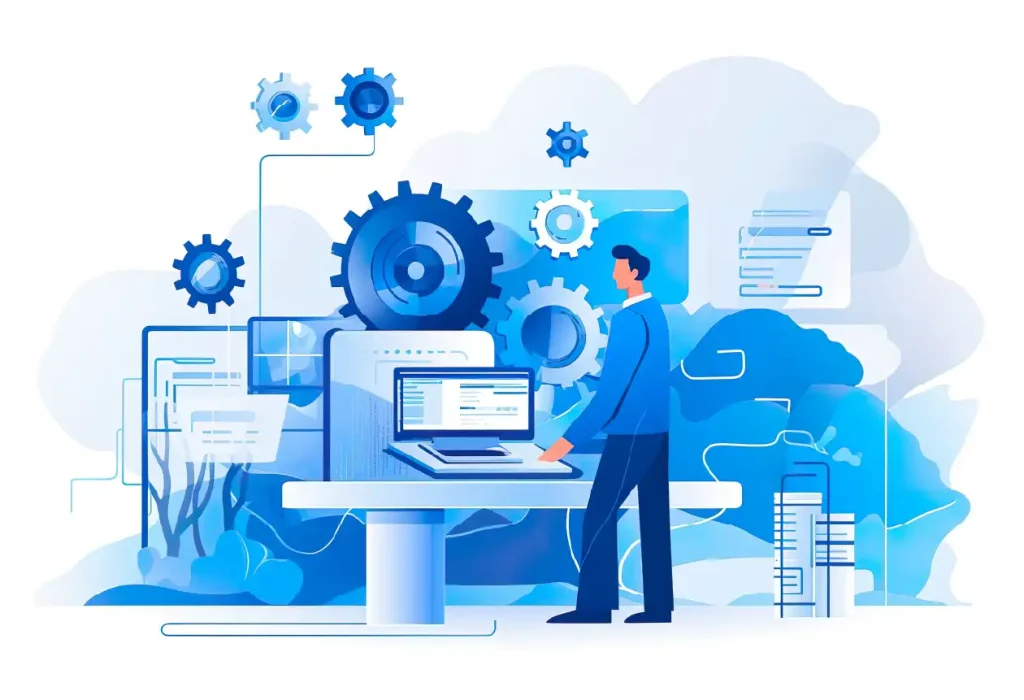
以下に、カイゼン案を考える際に役立つ代表的な切り口を詳しく解説します。
整理・整頓・清掃
5Sを構成する要素のうち整理・整頓・清掃は、現場の作業効率を上げるための基本的な考え方です。基本的ではありますが、日ごろから意識しておくことでカイゼンの着想を得ることができます。一例ですが、次のようなカイゼンが挙げられます。
- 整理:使用頻度の低い工具を別の場所に移動させて作業スペースを拡大し、作業時間短縮につなげる
- 整頓:工具を定位置に保管し、取り出しやすくする
- 清掃:粉体装置を作業日ごとに清掃し、装置トラブルを予防する
ムリ・ムラ・ムダ
カイゼンを進める際には、ムリ・ムラ・ムダを見直すことも基本です。これらは、現場の非効率を生む根本原因であり、取り除くことで、作業効率や製品品質が向上します。それぞれを減らすための具体例とカイゼン案について、次の表にまとめました。
分類 | 具体例 | カイゼン案 |
ムリ | 重い部品を1人で運搬 | 運搬用の台車を導入し、作業負荷を軽減 |
ムラ | 特定工程に負荷が集中し、 他工程の待機が多い | ボトルネック工程の自動化推進や人員増強により、 作業工程のバランスを調整する |
ムダ | 部品の移動距離が長い | 部品の配置を見直し、移動距離を短縮する |
また、ムダをなくすためには、トヨタ生産方式で知られる「7つのムダ」の考え方を活用します。具体的には、以下の7種類からなり、付加価値を生まない業務を分類したものです。
- 加工のムダ:不必要な工程や、過剰品質を追求する
- 在庫のムダ:使われず滞留する材料や製品がコストを圧迫する
- 造り過ぎのムダ:必要以上に生産し、在庫や資源を浪費する
- 手待ちのムダ:人や設備が作業待ちで停滞させる
- 動作のムダ:作業員の余計な動きや効率の悪い動作をする
- 運搬のムダ:部品や材料を無駄に移動させる
- 不良・手直しのムダ:不良品や手直し品による手間やリソースを使う
例えば、製品寸法の公差を必要以上に厳しく設定すると、設備の調整や寸法検査などに手間がかかりすぎ「加工のムダ」が発生します。一方で公差を緩やかにする方向で改善を進めるには、慎重な検証が求められます。このようなムダは長年放置されているケースも多く、発見と改善が大きな効果を生むこともあります。
このように、ムリ・ムラ・ムダは、現場で大きな問題が顕在化していない状況でも、カイゼンの余地を見つけるために重要な視点です。
ECRSの4原則の導入
ECRSの4原則は、作業工程を効率化するための改善手法で、作業のムダに気づく有効な着眼点の一つです。具体的には次の4つを指します。
- 排除(Eliminate):必要のない作業や工程を完全に取り除く
- 統合(Combine):複数の作業や工程を1つにまとめる
- 順序変更(Rearrange):作業や工程の順序を変更して効率化する
- 簡略化(Simplify):作業や工程を簡単にし、負担を軽減する
ECRSの4原則を念頭に置いて課題設定することで、作業効率が飛躍的に向上する打ち手に気づきやすくなります。
→ECRSの4原則についてより詳しく説明している記事はこちら
5Sに関連したカイゼン事例
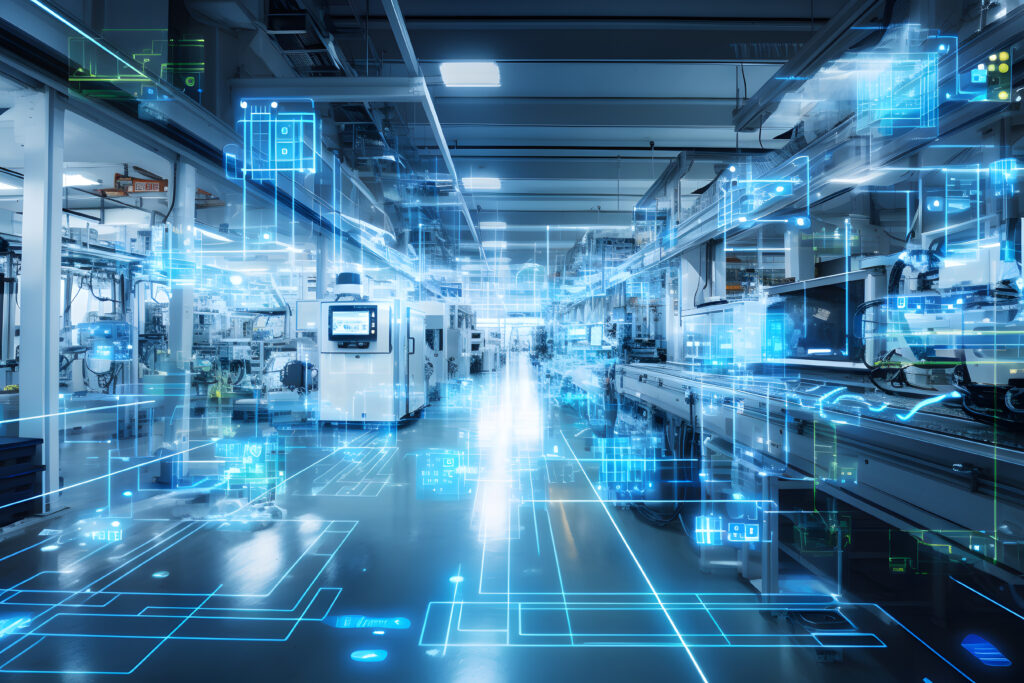
5S活動の中で視覚管理や分別ルール管理に取り組むことで、ヒューマンエラーが解消し、作業効率や安全性が向上します。
スイッチ類の視覚管理
スイッチ類の視覚管理は、5S活動における「整頓」に相当する取り組みです。現場作業の安全性向上と作業ミス低減に有効である、シンプルかつ効果的なカイゼン事例です。ラベル、色分け、図記号などを活用し、スイッチの役割や操作方法を視覚的に明示することで、誰でも簡単に正確な操作が可能になります。
特に、スイッチの色分けは、ヒューマンエラー防止効果の高い優れたカイゼンです。一例ですが、生産設備の制御盤にあるスイッチ類について、色と具体的用途の対応関係を次の表のように変更します。
スイッチの色 | 具体的な用途 |
赤 | 非常用スイッチ、緊急時に設備・システムを即時停止用 |
緑 | 運転開始や再起動の操作用 |
黄色 | 異常時のリセット操作用 |
青 | 通常操業に使用しない特殊操作用 |
工場内全ての設備でこの色分けを統一すれば、より高い改善効果が発揮できます。
廃棄物の分別ルールを視覚的に見える化
廃棄物の分別は、5S活動の「整理」、「清潔」の推進に相当し、コスト削減にも直結します。特に、産業廃棄物と一般ゴミを正確に分別したり、有価物と廃棄物を適切に分別したりすれば、廃棄物処理費用を圧縮できます。
これには、分別ルールを記載したポスターの掲示が一般的ですが、対策としては十分とは言えません。分別方法の不徹底による誤廃棄が頻発し、分別回収によるコスト改善が実現できなくなるケースも少なくないからです。
正しい分別を徹底するため、現場で廃棄物・有価物ごとに色分けされたゴミ箱を設置し、工場内の全ての現場で色を統一するカイゼンが考えられます。これにより、廃棄物量の処理コストの削減に繋がります。
3M低減に関連したカイゼン事例
ムリ、ムラ、ムダ(3M)低減に関連したカイゼンとして、以下のような活用が考えられます。
先入れ先出しによる在庫管理
先入れ先出しは、商品や材料などの在庫を古い順に使用・出荷する管理手法で、ムダの削減に有効なカイゼン事例です。古いものを優先して使うことで、在庫滞留による品質劣化や期限切れを防ぎ、廃棄ロスを未然に防止します。
例えば、棚で保管管理している材料を想定します。新しく届いた材料を手前に置く運用では、古い在庫が滞留し、使用期限切れとなることがあります。先入れ先出しでは、入庫順に部品が流れるよう棚のレイアウトを変更し、ラベルやバーコードで入庫日を明示します。これにより、誰でも速やかに古い材料を見分けられ、容易に先入れ先出しが徹底できるようになります。その結果、廃棄コスト削減、作業効率向上、品質維持が両立できます。
→ハンディ端末を使用して、確実な先入れ先出しを実現した事例はこちら
かんばん方式による備品の在庫圧縮
かんばん方式は、製造業において効率的な在庫管理を目指す方式の代表例で、過剰在庫や供給のムラを解消することが可能です。
倉庫に保管していた汎用部品が過剰在庫となり、スペースを圧迫する状況が常態化していたとします。この問題を解決するため、「かんばん」と呼ばれるカードを活用した部品供給の仕組みを導入しました。在庫が一定量以下になったタイミングで、「かんばん」に基づいて部品供給を指示し、必要な量を必要なタイミングで供給します。
これにより、部品供給の小ロット・高頻度化が実現し、在庫保有量を大幅に圧縮することで、倉庫スペースを効率的に活用できるようになります。
生産管理システム導入による業務プロセス効率化
生産管理システムの導入により、業務プロセスの見える化の実現や、特にムリ・ムラ・ムダ解消の効果が期待できます。実際に、金属加工業界のある企業では、新しく生産管理システムを導入した結果、年間約200時間もの工数を削減しました。
同社は従来はデータを手入力で管理していたため、入庫処理や生産進捗による在庫の動きをリアルタイムで把握できず、ヒューマンエラーが多発している状況でした。しかし、生産管理システムを導入することで、入庫書類を手入力からCSVファイル取り込みに変更し、在庫もバーコード管理可能となりました。
→業務プロセスの効率化によりムリ・ムラ・ムダを低減した事例はこちら
また、生産管理システムの中には、設備やエリアごとの生産負荷を見える化できるものもあります。リアルタイムに負荷をモニタリングし、負荷分散によるムラの解消も実現できます。さらに、作業実績のデータが蓄積すれば、傾向分析に基づくカイゼンも可能となります。
このように、生産管理システムを導入することでムリ・ムラ・ムダの低減が実現できます。
ECRSの4原則に関連するカイゼン事例
ECRSの4原則に関連する具体的事例として、以下のものがあります。
製品検査工程と梱包工程の一体化
製品検査工程と梱包工程の一体化は、ECRSの「結合(Combine)」を活用した代表的な改善事例で、様々な工程間のムダを削減します。具体的には、モノの運搬、作業員の待ち時間、作業スペースが削減されるだけでなく、作業効率が向上します。
生産工程の調整が必要なため、実現難易度の高いカイゼンですが、大幅な生産効率向上・コスト削減をもたらします。
NC旋盤における加工動作プログラムの標準化
NC旋盤の加工動作プログラムの標準化は、ECRSの4原則(排除・結合・再配置・簡素化)を活用し、作業効率を向上させるカイゼン事例です。
あらかじめ単位動作がプログラムされており、それらの単純な組み合わせで加工プログラムが作られているケースがあります。このため、まとまった生産量のある製品では、改善余地が大きいこともあります。具体的なカイゼン事例は、次の表のとおりです。
原則 | カイゼン施策 | 具体例 |
排除 | 不必要な動作をプログラムから削除 | 工具が加工部から遠回りする動作を削除し、最短ルートを設定 |
統合 | 加工工程をまとめ、工具交換の頻度を削減 | 同じ工具で行える加工を一度にまとめて実施 |
簡素化 | プログラムコードを見直し、作業手順を簡単にする | 繰り返し加工部分に自動生成スクリプトを導入してプログラムを短縮 |
このように、NC旋盤での加工動作の標準化は、作業効率が大きく向上し、高価なNC旋盤を設備投資することなく生産量を増やすことができます。
22種類の生産管理システムをランキングで比較
初期費用相場や選び方のポイントをチェック
生産管理システムをそれぞれの特徴や初期費用相場などで比較したい場合は、「生産管理システムランキング」も是非ご覧ください。生産管理システムは、自社の製品・生産方式・企業規模などに適したものを導入しないと、得られるメリットが限定されてしまいます。事前適合性チェックや生産管理システムを選ぶ前に押さえておきたいポイントも解説していますので、製品選びの参考にしてみてください。