【図解・事例付き】QCストーリーで再現性・継続性を高めよう:改善活動の定着への道しるべ
公開日:2025年03月19日
最終更新日:2025年03月19日
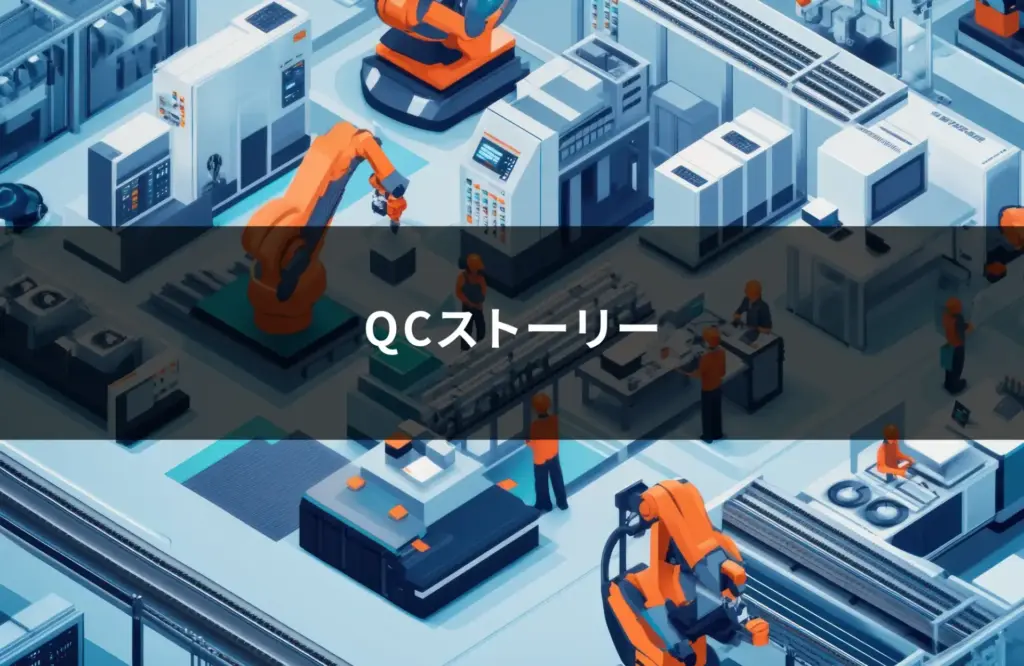
QCストーリーは、製造現場の悩みの解決方法をパターン化したものです。PDCAサイクルに基づく流れを標準化することで、現場の品質改善における再現性、継続性を高めます。
本記事では、QCストーリーの基本構成を紹介し、4つの活用型(問題解決型・課題達成型・施策実行型・未然防止型)の特徴を図解付きで解説します。さらに事例に沿った進め方、失敗しないためのポイントを解説。改善活動の質を高めたい現場担当者必見の内容です。
QCストーリーとは
QCストーリーは、問題解決に効果的な方法を体系的にパターン化したもので、製造業を中心に広く導入されています。
QCストーリーの基本構成はPDCA
QCストーリーの基本構成はPDCAであり、具体的には次の4ステップからなります。
- Plan(計画) :現場の悩みを明確化、改善計画の立案
- Do(実行) :データを基に分析し、改善策を実行
- Check(評価):改善策の効果を検証
- Act(改善) :効果的な取り組みの標準化と定着
こうした基本構成をもつQCストーリーは、品質管理や業務改善におけるカイゼンの再現性を高め、効率的な組織運営を実現するために有効です。
QCストーリーが求められる理由:品質管理の現場課題
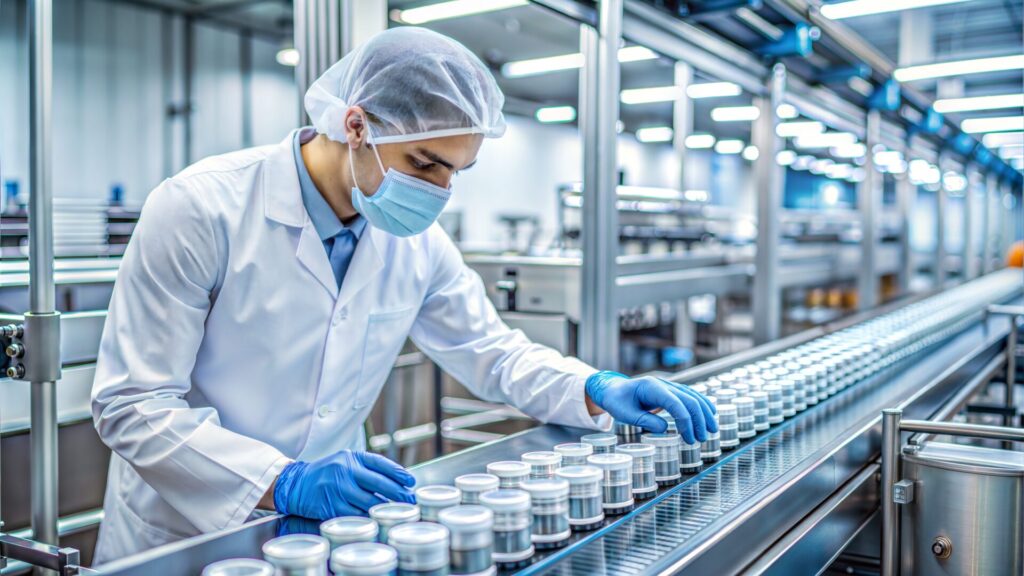
製造業の現場では、常に現状を改善したいという悩みを抱えています。その悩みへのアプローチとしてQCストーリーが求められる背景には、以下のような問題が挙げられます。
- 突発的な問題が頻発し、原因が明確にならない
- 改善活動が属人的で、ノウハウが蓄積されない
- 品質向上の取り組みが長続きしない
生産現場では、「なぜか不良が増えている」「設備のトラブルが多い」といった問題が多く発生します。しかし、こうした問題に対して、対症療法的な対応に留まったり、ベテランの経験に基づくカン・コツに頼るケースも少なくありません。さらに、短期的な改善策に留まり、改善の効果が持続しない現場も多く存在します。
このような課題に対応するために、論理的かつ継続性のある問題解決手法として、QCストーリーは活用されます。
TQM(総合的品質管理)とQCストーリーとの関係
QCストーリーは、品質管理の実践手法の一つであり、その背景にはTQM(Total Quality Management:総合的品質管理)の思想が深く関連しています。
TQMは、組織全体で品質向上を目指すための経営手法であり、以下のような基本原則を軸にしています。
- 品質向上は経営の中心課題であり、全員参加で行う
- 継続的に品質改善を進める
- データを活用した合理的な意思決定を行う
TQMで経営レベルの品質戦略をリードし、その戦略を現場で実践するためのツールがQCストーリーです。QCストーリーがあって、初めてTQMの考え方が成り立つと言えます。TQMとQCストーリーの考え方を整理すると、次の表のようになります。
TQM(総合的品質管理) | QCストーリー | |
適用範囲 | 企業全体の品質向上(経営、設計、営業なども含む) | 現場レベルの品質改善 |
目的 | 組織全体で品質向上を推進 | 現場のお悩み解決を体系化 |
アプローチ | 全社の文化・組織の改革 | 現場のデータ活用、論理的思考を加速 |
活用場面 | 全社戦略・経営方針の立案・実行 | QCサークル活動、品質・工程の改善 |
品質管理活動におけるQCストーリーの位置づけ・メリット
企業の品質管理活動は、品質保証・品質管理・品質改善の3つに分類され、QCストーリーは品質改善の領域で活用されます。
品質管理における標準作業の遵守や工程管理も大切ですが、これだけで品質の悩みを根本的に解決することはできません。日常的な管理業務に加え、QCストーリーの考え方を活用した改善活動により、品質レベルの更なる向上が可能です。
QCストーリーを活用すれば、次のようなメリットが得られます。
- 誰が取り組んでも同じプロセスで進められるため、属人化を防げる
- 感覚や経験に頼らず、数値データ分析を活用した客観的な判断が可能
- 一度の改善で終わらず、PDCAサイクルを回しながら、品質向上を継続できる
- 現場主導の改善を進めるQCサークル活動の質を高める
このように、QCストーリーは品質不良の低減や工程の最適化に貢献し、企業の競争力向上にも寄与する重要な手法です。
【図解】QCストーリーの4つの型と使い分け
QCストーリーには、問題解決型、課題達成型、施策実行型、未然防止型の4つの型があり、それぞれ異なる目的やアプローチで活用されます。どの型を用いるかは、改善の対象や目的によって選択されます。
4つの型のイメージは、それぞれ以下の図の通りです。
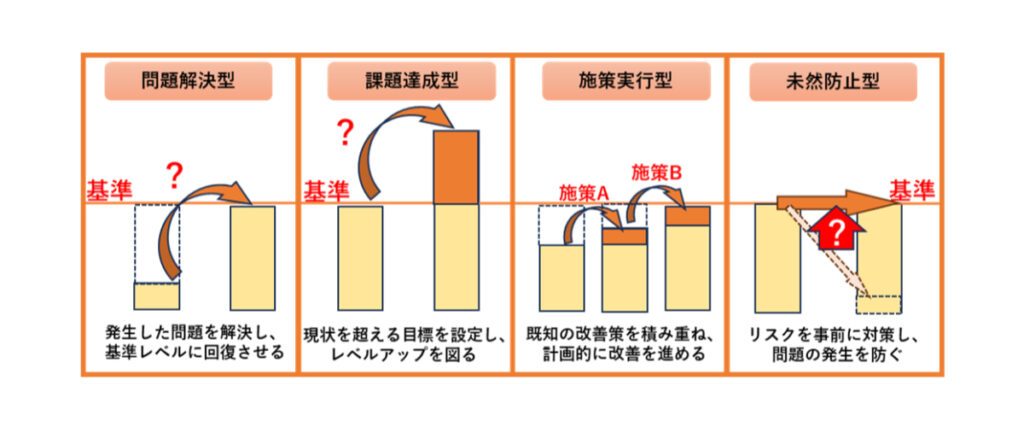
4つの型とPDCAサイクルの関係
QCストーリーの基本は、PDCAサイクルに沿った問題解決の流れにあります。目的や取り組み方によって、PDCAのそれぞれのステップで具体的な手順が異なります。これらを整理したのが以下の表です。
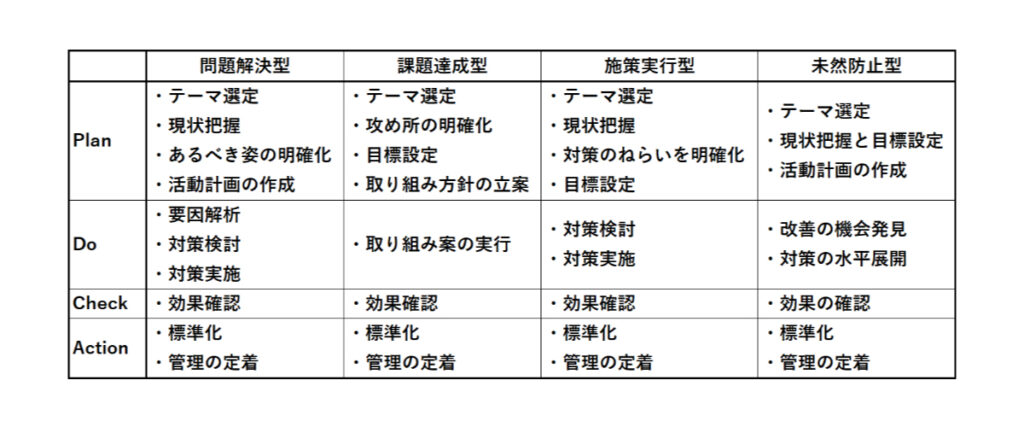
目的に応じて異なる点はありますが、いずれもPDCAの流れに沿った手順を特徴とします。
問題解決型:あるべき姿を基準とした取り組み
問題解決型のQCストーリーは、発生している問題に対して、あるべきでない状態の解消を目指すための考え方です。ここでの問題とは、何らかの望ましくない事態によって、現状が本来の姿(あるべき姿)から乖離していることを指します。具体的には、次のような事象が問題に相当します。
- 特定の品質不良内容が突出して多い
- 特定品種に限って、廃棄ロスが多い
- 一部の工程で設備トラブルが頻発している
こうした問題に対して、客観的データに基づいて問題を分析し、目標を設定します。その後、問題の原因を追求し、その原因に対して効果的な対策を立案、優先順位を付けて実行します。改善策の実行後、その効果を確認し、十分な効果があれば標準化して定着させます。この流れを継続的に実行し、望ましくない品質状態を解消することが問題解決型のQCストーリーです。
問題解決型のポイントは、問題のある現状を基準として、あるべき姿をどのように設定するかです。例えば、金属加工工場の品質不良発生状況を分析した結果、以下の事実が判明したとします。
品質不良の内容 | 不良発生率 | 発生件数 |
穴位置ずれ | 5.2% | 430件 |
バリ発生 | 2.8% | 235件 |
穴径の異常 | 1.3% | 105件 |
この場合、穴位置ずれ不良は、他の不良よりも多く、望ましくない事象であることは明らかです。そこで不良発生率の少ない穴径の異常水準をあるべき姿と考え、不良発生率1.3%を目標と設定して、改善に取り組むことと考えました。
このように、データをもとに望ましくない事態とあるべき姿を設定し、改善に取り組むのが問題解決型の進め方です。
課題達成型:現状を基準として、高みを目指す
課題達成型は、現状を出発点として「理想的な高み」である目標を設定し、これまでのやり方とは違う方法で実現を目指す手法です。テーマ設定ののち、改善余地の大きそうなアイテムを「攻め所」として抽出し、取り組み方針を明確にします。改善効果の確認・標準化・定着の流れは、問題解決型と同様です。
問題解決型と異なるのは、現状が特別悪い状態ではなかったとしても、もっと良い状態を目指す点です。
一例として、自動車部品の組み立て工程において、生産効率向上に向けた取り組み改善事例を想定します。この工場では、従来の作業スピードでも、品質・生産数量に問題はありませんでした。しかし、今よりも良い状態を目指すため、部品1個あたりの作業時間(サイクルタイム)を600秒間から60秒間短縮する改善目標を設定しました。
改善のためにチーム内で協議を重ね、作業手順や動線の見直し、部品供給のタイミング調整に加え、段取り替え調整治具も導入。その結果、サイクルタイムを63秒間短縮し、目標を達成しました。
このように、課題達成型のQCストーリーは、よりよい現場を自律的に追求し、理想を実現するための考え方です。こうした取り組みは、継続的なカイゼンの組織風土を維持・向上させます。
施策実行型:取り組みの効果を確認
施策実行型のQCストーリーは、すでに見込みがあると分かっている打ち手の効果を定量的に評価し、その有効性を確認する手法です。問題解決型や課題達成型のように、直接的な問題解決や高みを目指すのではなく、取り組みが期待通りの成果を生んでいるかを検証し、さらなる改善につなげることが目的です。
施策実行型のQCストーリーの流れは、問題解決型の流れから原因調査を除いたステップで実施します。自動車用ブレーキディスク製造を想定し、加工工程において5秒間の加工時間短縮を目標に掲げたとします。加工時間短縮には、一般的に硬い切削工具への変更が有効ですが、短縮効果や他の悪影響の有無は分かっていませんでした。
そこで、データ収集のため、現行品よりも硬い新型品を1か月間試験運用し、加工時間、不良率、工具摩耗状況のモニタリングを実施。試験運用後のデータを分析した結果、以下の成果が得られました。
従来工具 | 新型工具 | 改善効果 | |
1個当たり加工時間 | 45秒 | 39秒 | 13%短縮 |
工具寿命(加工個数) | 5000個 | 7000個 | 40%向上 |
製品不良率 | 1.8% | 1.5% | 17%削減 |
この検証結果により、新型工具による加工時間の短縮効果だけでなく、その他の付随効果が数値データで確認できました。この結果を根拠として、新型工具の導入を正式決定し、全ラインへ展開することにしました。
施策実行型のQCストーリーでは、施策の効果を定量的に評価し、取り組みの成功・失敗を明確にします。これにより、より確実性の高い改善活動を進めることができます。
未然防止型:予測リスクを回避するための対策
未然防止型のQCストーリーは、予測される問題を事前に特定し、対策を講じることでリスクを回避する手法です。問題解決型が「すでに発生した問題の解消」を目的とするのに対し、未然防止型は「将来の問題発生を防ぐ」ことに重点を置きます。
製造業では、設備故障・品質不良・安全リスクなど、未然に防ぐべき課題が多く存在します。これらのリスクに対し、FMEA(故障モード影響解析)やFTA(故障の木解析)などの手法を活用し、事前に対策を講じることで、事故や品質トラブルの発生を防ぐことが重要です。
未然防止型のQCストーリーでは、リスクの可能性が高い工程や設備をテーマアップし、
リスク要因の抽出、評価、対策立案を行います。予防した実効策について有効性を確認し、効果が確認されれば、標準化により継続運用します。
自動車部品の溶接工程における「溶接部の強度低下リスクの未然防止」を例に挙げます。工程設計の時点で溶接不良が懸念されていたため、類似製品の実績データから、FMEAで要因と影響度、考えられる対策を整理しました。

これらを手順に反映させた結果、対策済の類似製品と同程度の不良率であったため、リスクの未然防止に成功したと判断されました。
未然防止型のQCストーリーは、設備の故障予防や品質不良の防止に留まりません。作業安全対策や環境負荷低減にも応用できるため、企業のリスクマネジメントに広く活用されています。
【事例で解説】QCストーリーの進め方:問題解決型
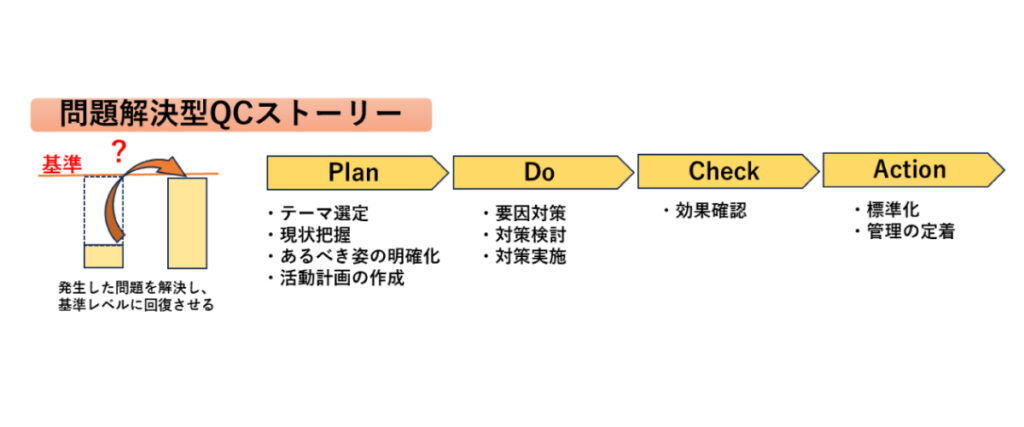
QCストーリーの基本は、問題解決型のQCストーリーです。ここでは問題解決型の流れに沿って、食品工場の異物混入量を減らす取り組みの事例を想定し、進め方を解説します。
職場の悩みからテーマを選定
問題解決型のQCストーリーは、まず現場の悩みを明確にし、改善すべきテーマを選定することから始まります。適切な難易度や切り口でテーマを選択すれば、実行可能な改善活動につながり、効果的な成果を生みます。一方、テーマ選定を誤ると、改善効果が低く、取り組みそのものが形骸化しやすくなります。
テーマ選定のポイントは次の3点です。
- 現場の実情に即していること:実際に現場で発生している課題を選定する
- 改善効果が定量的に測れること:目標を数値化し、改善効果を評価できる
- 実行可能な範囲であること: 現場の工夫や作業改善で解決できる内容にする
上記ポイントをもとに、食品加工工場でのテーマ選定の悪い例、良い例を見ていきましょう。
悪いテーマ選定の例 | 良いテーマ選定の例 |
新しい自動包装機を導入する | 包装工程での異物混入を減らす |
作業員の意識改革を行う | 作業手順を見直し、歩留まりを向上させる |
悪いテーマの例に挙げたのは、設備投資ありきのもの、抽象的で実際に行う改善策が見えにくいものです。「新しい自動包装機の導入」は、現場だけでは決められない大規模投資が伴うため、適切ではありません。また、「作業員の意識改革」も改善効果の数値化が難しく、実行内容も不明確なため、QCストーリーで設定するテーマとしては不適切です。
一方で、良いテーマは、現場の問題を直接改善できる内容であり、実行可能で効果が数値化しやすいものです。「異物混入トラブルの削減」や「歩留まり向上」は、現場の作業手順の見直しや管理強化で対応可能であり、QCサークル活動でも実践しやすいテーマです。
事実ベースでの現状把握
QCストーリーに沿って問題解決を進める際には、経験や感覚に頼らず、客観的なデータをもとにした正確な現状把握が重要です。思い込みだけで改善活動を進めると、問題の本質を見誤ったり、優先すべき課題を見逃したりして、効果の低い対策に留まりがちです。
データを活用して現状を把握すれば、問題を正しく捉え、改善に向けて効果的な対策を絞り込むことができます。事実ベースでデータ収集を行う際のポイントは次の3点です。
- 不良発生率の測定:どの工程で、どの程度の問題が発生しているかを数値で確認する。
- 作業現場の観察:作業員の手順、設備の状態、作業環境にトラブルの要因がないかをチェックする。
- 過去の記録を参照:トラブルの発生頻度やパターンを分析し、打ち手を絞り込む
問題の種類や発生件数を整理し、データに基づいて改善策を立案します。食品工場における異物混入が問題の場合、まず、以下のように異物の種類、不良発生率、月間発生件数を分析します。この結果から、最も多いのはプラスチック片の混入であり、主な発生源である「原料投入・ミキシング工程」の改善が効果的であると判断できます。
異物の種類 | 不良発生率 | 月間発生件数 | 主な発生工程 |
プラスチック片 | 0.08% | 120件 | 原料投入・ミキシング工程 |
金属片 | 0.02% | 30件 | 包装工程 |
その他(紙・木片) | 0.01% | 15件 | 原料保管・開封工程 |
あるべき姿をもとにした目標設定
現状の問題を把握したら、次に「どの状態を目指すのか」を設定します。QCストーリーにおいて、「あるべき姿」とは、本来目指すべき理想的な状態や、業務や品質の基準に適合した状態を指します。
ただし、「あるべき姿」が実現不可能なほど高いと、実現できる見通しが立たなくなってしまいます。過去の実績や類似事例を参考に、現実的かつ達成可能な数値目標を設定するとよいでしょう。
例えば、食品工場における異物混入問題の事例では、あるべき姿は「異物混入ゼロ」ですが、実際には完全にゼロにするのは困難です。そのため、現状把握での分析結果を参考に、不良発生率が最も低い0.01%を達成可能な基準値と考え、年度内での達成を目標として掲げました。
活動計画の作成
目標達成に向けて、具体的な取り組み内容とスケジュールを決めるステップが「活動計画の作成」です。適切な計画がなければ、改善活動が場当たり的になり、効果が限定的になってしまいます。
一方で、実際に取り組んでみないと、具体的な内容はイメージしにくいものです。計画作成では、実施内容の進める内容、取り組む順序、スケジュール、主担当者を明確にして、メンバー全員で共有します。メンバー間で負担に大きな偏りがないよう、全員で参加できるように担当を割り振るようにしましょう。
食品工場の事例では、以下のように活動計画を作成しました。
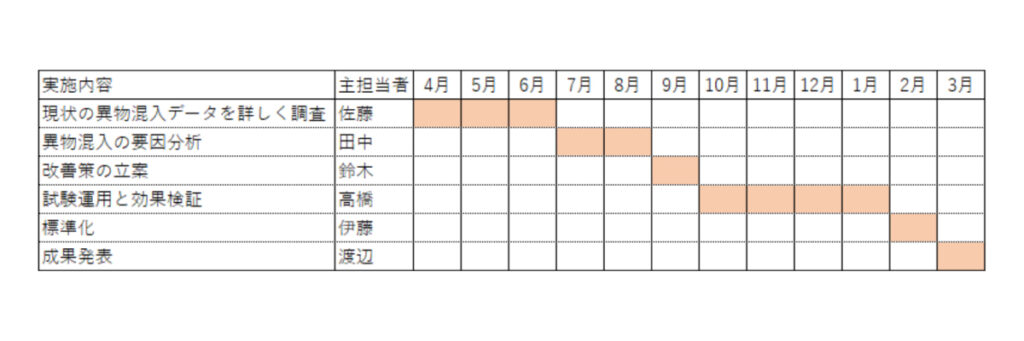
要因分析
QCストーリーでは、「あるべき姿」と現状のギャップを埋めるために、なぜその問題が発生しているのかを分析します。要因分析によって問題の根本原因を特定し、最も影響度の大きい要因に焦点を当てた改善策を導き出すことができます。
要因分析には、QC7つ道具である「特性要因図(フィッシュボーンダイアグラム)」が有効です。特性要因図では、4M(人、材料、機械、方法)の観点から問題の発生原因を整理し、真因を探ります。食品工場の包装工程における異物混入の例では、プラスチック片の異物混入に対して、以下のように分析できます。
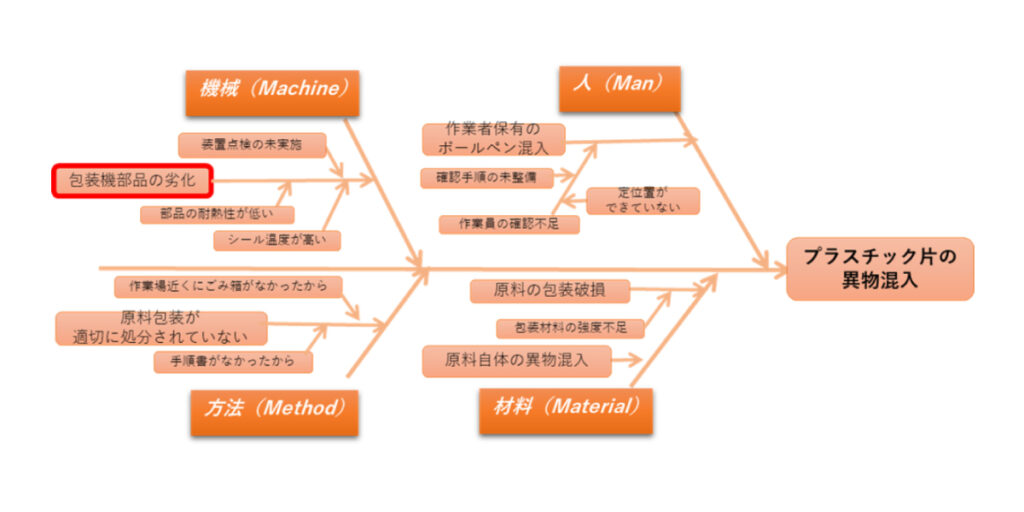
その要因分析をもとに、包装機の状態を確認したところ、包装機部品のプラスチック部が劣化し、砕片が発生していたことが判明しました。このように、網羅的な要因分析を行えば、思いこみに頼った調査よりも、真因にたどり着ける可能性が高くなります。
さらに、要因分析には単なる問題特定だけでなく、そのプロセスをチーム内で共有し、関係者全員も納得いただくという側面もあります。分析結果や進捗状況を関係者と共有しながら進めることで、協力を得やすくなり、効果的な改善活動につながります。
対策案の比較検討
要因分析の結果をもとに、問題解決に有効な対策案を複数挙げ、その中から最も効果的な対策を選択します。挙げられた対策案について、効果、実現可能性、コストなど、複数の観点から評価し、点数付けして決めるとよいでしょう。
食品工業のプラスチック片の異物混入の例では、次の表のように対策案を挙げ、それぞれ評価を行いました。
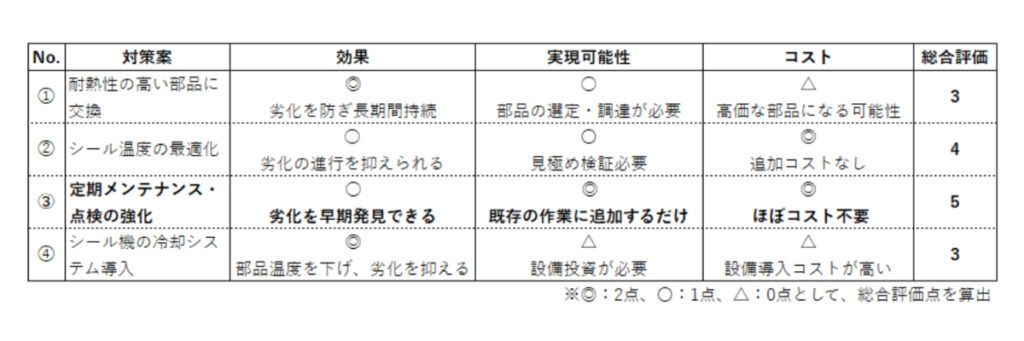
この中では、効果、実現可能性、コストの全てが◎評価の対策案はありません。このため、総合評価点が最も高かった項目である、定期メンテナンス・点検の強化が望ましい、と判断できます。
対策案の実行
対策案の比較検討が完了したら、次のステップは選定した対策の実行です。QCストーリーでは、具体的な実行計画を立て、その中でステップごとの実施内容、担当者、期限を明示します。実行計画がないと、管理者やチームのメンバーは実作業の遅れに気づけません。また、誰かがやっているだろうという他責思考が職場に蔓延し、改善が進まないケースも散見されます。
実行計画立案時に意識すべきポイントは以下の通りです。
- 具体的な実施内容の明確化:どの対策を、どのように実行するか
- スケジュールの明示:いつまでに、どの段階まで実施するか
- 担当者の指名:誰が、どのステップを担当するか
食品工場の異物混入対策の例では、実行する「定期メンテナンス・点検の強化」の進め方について、以下のような実行計画を作成します。その上で各ステップの主担当者が中心となって、実際の現場で改善検証を進めていきます。
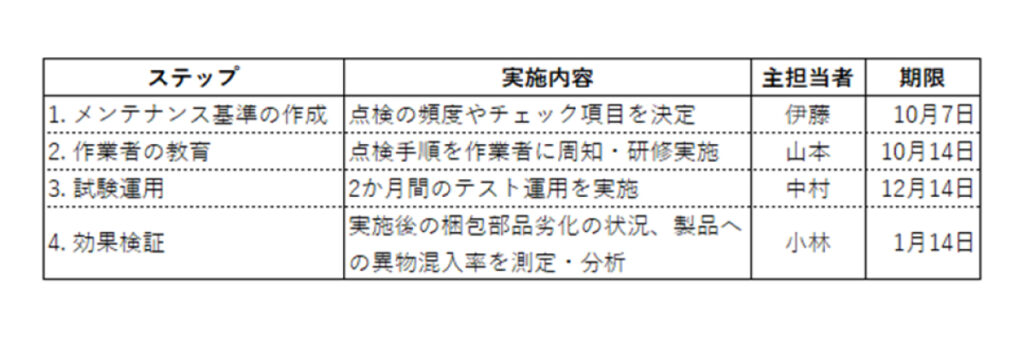
立てた計画に対して、予定通りに進んでいるかを定期的にチェックしながら進めます。スケジュールの進捗管理に加え、想定外の課題が出ていないかのフォローも欠かせません。例えば、定期メンテナンスの試験運用中に、部品の劣化速度が想定より早いことが判明するかもしれません。この場合、追加の対策として点検頻度を増やす調整が必要になります。
改善効果を数値で評価
対策実施前後の比較を数値データで行い、期待通りの成果が出たかを評価します。客観的データで評価することで、検討結果を正しく把握可能です。もし、想定よりも効果が低い場合には、追加の改善策も検討する必要があります。
食品工場の例では、週1回の点検実施により部品の劣化を点検で発見でき、部品交換で不良発生を防げることがわかりました。実際にプラスチック片の混入率は0.08%から0.008%まで減少し、十分な効果が得られたと判断しました。
改善結果の業務標準化
効果のあった改善策は、標準化を行い、長期的に維持できる仕組みを構築します。例えば生産量が増えて忙しくなる等、小さなきっかけで良い取り組みが突然機能しなくなるケースもあります。
作業標準書(SOP)に反映すれば、管理者、作業者メンバー全員が確実に改善策を実行し続ける仕組みとなります。食品工場の取り組み事例では、梱包機の定期点検内容が記載されたフォーマット、その具体的な確認方法をSOPに追記します。
このように、改善に成功した内容の標準化もQCストーリーには欠かせません。標準化により組織によりよい作業プロセスを定着させることで、高いレベルの実作業が継続できる体制となります。
QCストーリーで失敗しないためのポイント
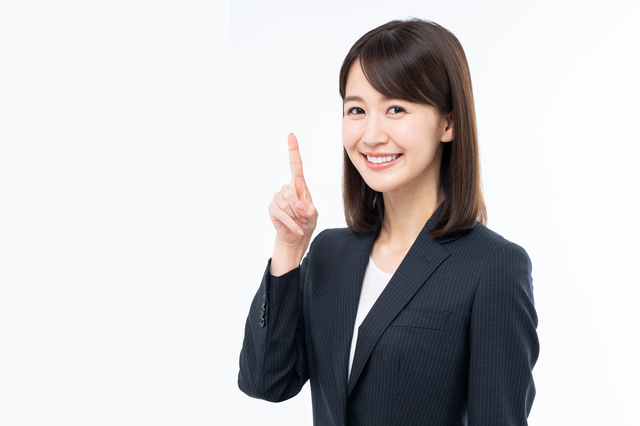
QCストーリーには、実践時に陥りやすい失敗のパターンがあります。具体的には、チーム内での意識不足、目標の不明確さ等が挙げられます。
こうした失敗を回避するためには、次のポイントに留意することが有効です。
チームでの意識共有:協力を求めやすい雰囲気を作る
QCストーリーでは、メンバー全員が目的や進め方を理解し、共通認識を持つことが大前提です。現場のチーム全体で取り組む品質改善活動の考え方であるため、チーム内での協力体制が欠かせません。
もし、意識共有が足りない場合、改善施策の協力が得られなかったり、一部の人に負担が集中して活動が停滞する原因にもなります。取り組み前に活動の目的や進め方を全員で確認するとともに、進捗状況を定期的に共有するとよいでしょう。さらにQCサークルや改善活動の成果報告の場を持つのも、メンバーのモチベーション維持・向上に有効です。
役割分担の明確化:責任感を醸成する
QCストーリーを進める際には、チームメンバーの役割を明確にします。役割が不明確だと、「誰が何をやるのか」が曖昧になり、活動が進まなくなる状況が発生しやすくなります。
こうした活動は全員参加が基本ですが、各取り組みの主担当者が明確になるようにしましょう。まず、推進力のある人をリーダーに指名し、全体統括・進捗管理を担っていただきます。それ以外の役割の人は、具体的な行動計画に対応するように、チーム内で協議して決めていくとよいでしょう。
具体的な目標設定:正しい方向性に導く
明確な目標設定も、QCストーリーに欠かせない要素です。目標が曖昧なままでは、効果測定ができず、正しい改善の方向性を導くのが難しくなります。
目標設定には、 次のように「SMARTの法則」を活用するとよいでしょう。
項目 | 目標設定内容の例 |
Specific(具体的) | 悪い例:異物混入を減らす良い例:包装工程の異物混入率を0.08%→0.02%に削減 |
Measurable(測定可能) | 悪い例:作業効率を向上させる良い例:作業時間を10%短縮 |
Achievable(達成可能) | 悪い例:不良ゼロ良い例:不良率を50%削減 |
Relevant(関連性) | 会社の品質方針や経営目標に沿った内容を設定する |
Time-bound(期限を決める) | 悪い例:近いうちに、できるだけ早く良い例:3か月以内に達成する |
データを活用した分析:改善活動の再現性を高める
QCストーリーの重要なポイントの一つは、データに基づいた現状把握と論理的な分析です。経験や勘に頼った対策では、効果が不確実になり、再発リスクが高まるため、客観的なデータを活用することが重要です。
同様の考え方として、ISO9001(品質マネジメントシステムの国際規格)やJIS Q 9023(TQM実施のための指針)の中でも、次のような記載があります。
意思決定はデータと情報の分析と評価に基づいて行うべきである
JISQ9001:2015 品質マネジメントシステム
経験及び勘だけに頼るのではなく,データに基づいてPDCAサイクルを回すこと
JIS Q9023:2018 TQM実施のための指針
QCストーリーでは、事実・データの分析に基づく問題解決が大原則です。これによって、改善活動の再現性も高まります。
継続的なモニタリング:効果を持続させる
QCストーリーは一度きりの改善ではなく、継続的なモニタリングと改善のサイクルが不可欠です。改善後のデータチェックが不足すると、次のような問題が発生しやすくなります。
- 一時的に改善できても、時間が経つと元に戻る
- 問題が再発しても気づかず、トラブルが拡大する
- 改善の成果が持続せず、品質が安定しない
定期的な点検・データ分析を実施し、異常を早期発見するとともに、必要に応じて改善策のマイナーチェンジも行います。こうした取り組みによって、改善の効果を長期間維持させることができます。
チームでの成果発表:上層部にも知ってもらう
QCストーリーの成果は、チーム内だけで完結させず、社内全体に向けて発信することが重要です。改善活動の成果報告の場は、チームメンバーの適度な緊張感や達成感をもたらすと同時に、上層部の理解や評価を得る貴重なチャンスにもなります。特に、改善前後のデータを用いた成果報告は、データに基づく改善活動の有効性を示すことができ、説得力が高まります。
また、成果報告だけでなく、データ分析に必要な環境やツールの整備、基盤構築の重要性を上層部に訴えてもよいでしょう。一例ですが、分析ツールやデータ基盤となるシステムの導入により、組織的な改善活動を加速できる可能性をアピールできます。こうした現場からの改善提案は、費用負担を伴う改善を後押しできるケースもあります。
生産管理システムを活用したデータ分析
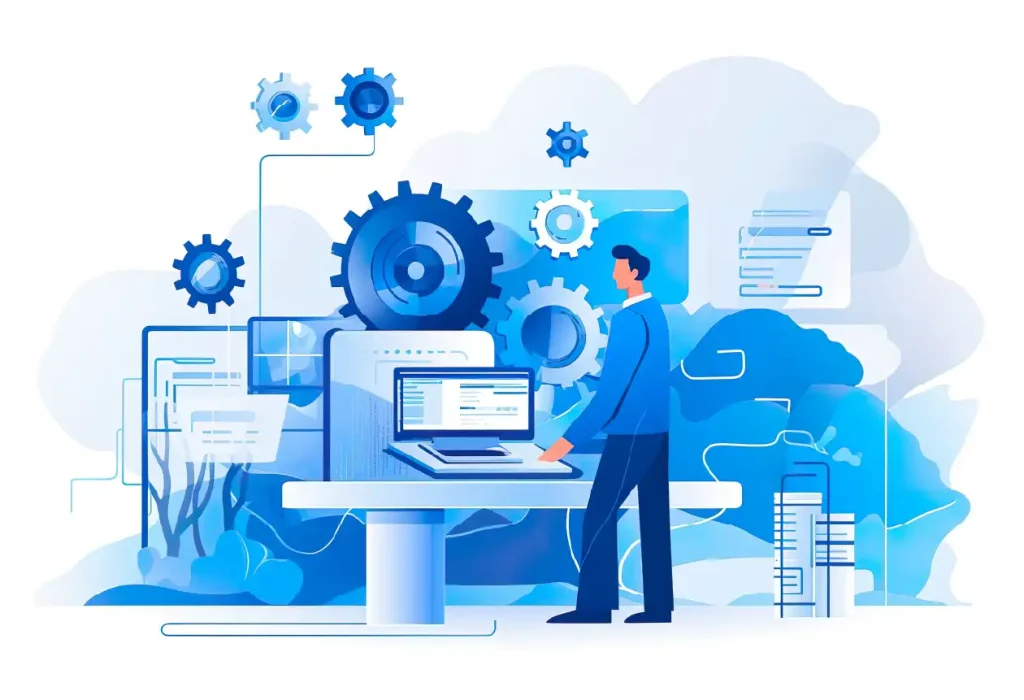
より説得力のあるQCストーリーを展開するためには、効率的なデータの収集・分析が不可欠です。現場で何が起きているのかを客観的に捉えるために、信頼できる数値データに基づく判断が求められます。
改善を加速するシステムツール
QCストーリーの展開において、必要なデータを手作業で収集・分析するのは限界があります。特に多品種・多工程を扱う現場では、データ量が膨大となり、紙帳票やエクセル集計では極めて限られた範囲の分析にとどまります。
そこで有効なのが、生産管理システムなどのツール導入です。データ収集の自動化に加え、集計作業も効率化できるため、様々な気づきが促進されます。QCストーリーを進めるうえで、データを集める・見る仕組みとしてシステムツールがあれば、より大きな成果を導きやすくなります。
生産管理システムの導入により、必要な情報がすぐに検索できるようになった事例はこちら
→【生産管理システム】既存システムで手書き・手入力が必要だった作業をシステム化!
計量値を生産管理システムに自動で取り込み、品質管理体制を強化した事例はこちら
→【生産管理システム】計量器連携などでアナログ作業を減らし年間450時間の工数削減!
22種類の生産管理システムをランキングで比較
初期費用相場や選び方のポイントをチェック
生産管理システムをそれぞれの特徴や初期費用相場などで比較したい場合は、「生産管理システムランキング」も是非ご覧ください。生産管理システムは、自社の製品・生産方式・企業規模などに適したものを導入しないと、得られるメリットが限定されてしまいます。事前適合性チェックや生産管理システムを選ぶ前に押さえておきたいポイントも解説していますので、製品選びの参考にしてみてください。