品質不良の原因と解決する方法を徹底解説:生産管理システムについても紹介
公開日:2024年06月18日
最終更新日:2024年09月26日
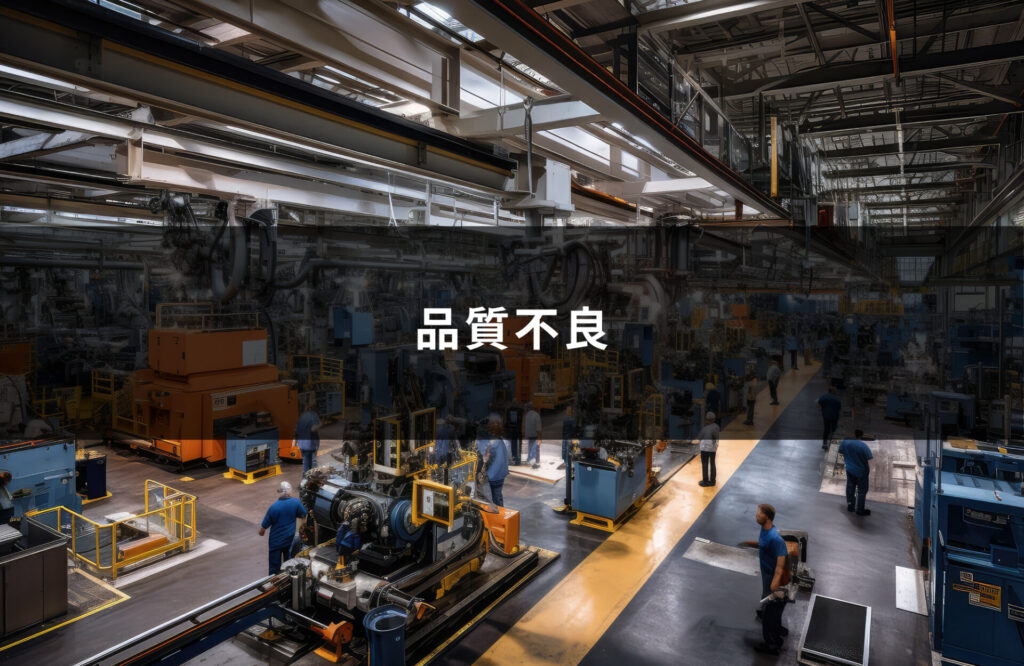
製造業において、品質不良は避けて通れない課題です。品質不良が発生すると、企業の信頼性や収益に大きな悪影響を及ぼします。本記事では、品質とは何か、品質不良が企業に与える影響、原因の分析方法や防止策について解説します。
品質とは
品質とは、製品やサービスの、顧客の期待や要求を満たす能力のことです。製品に求められる品質は、設計段階と製造段階で大きく2つに分けられます。
設計品質
設計品質とは、製品が設計段階で定められた基準や仕様を満たしているかどうかを指します。設計が優れているほど、製品の性能や使いやすさが向上します。例えば、耐久性が高い素材の選定やメンテナンス性、コスト、デザイン性などが設計品質の一例です。
製造品質
製造品質とは、製品が設計図面通りに作られ、規定の基準を満たしているかどうかを指します。製造品質の管理には、製造工程の監視や検査が含まれます。厳密な品質検査を行うことで、不良品の流出を防ぐことができます。また、製造プロセスの改善や設備のメンテナンスも重要です。
品質不良とは
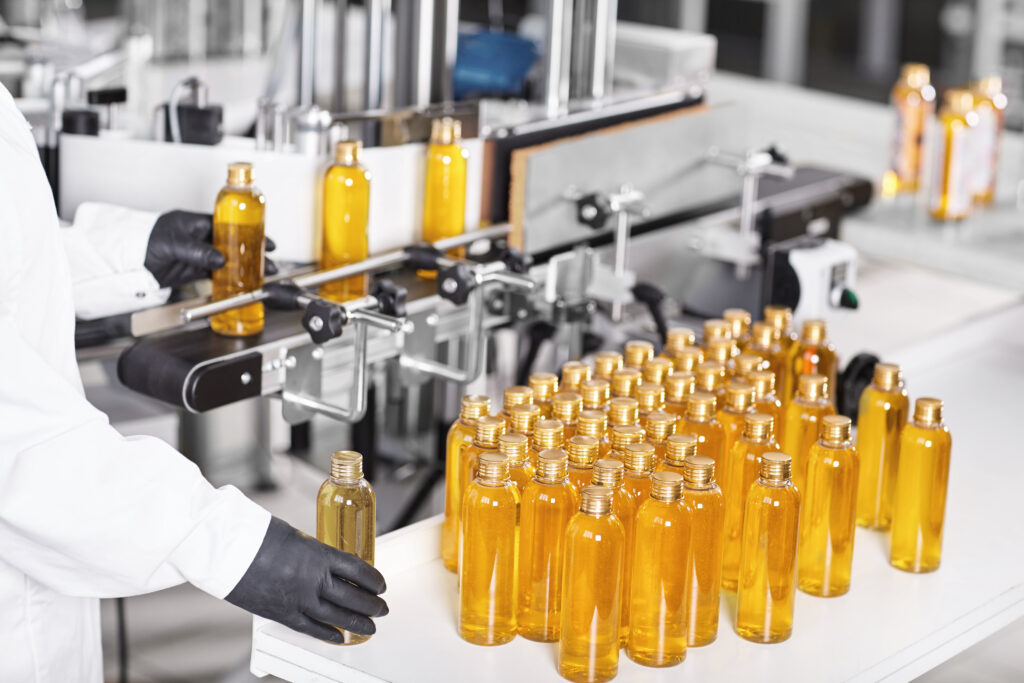
品質不良とは、製品やサービスが求められてる品質基準を満たしていない状態を指します。具体的には、以下のような例が挙げられます。
- 製品の機能や性能が不十分
- 外観に欠陥がある
- 安全性に問題がある
- 耐久性が低い
- 材料や製造プロセスに問題がある
品質不良は企業にとって重大な問題であり、コスト増加やブランドイメージの低下、法的トラブルを引き起こす可能性があります。また、消費者に対しては安全リスクや経済的損失、心理的な不満を与えることになります。
品質不良が企業に与える影響
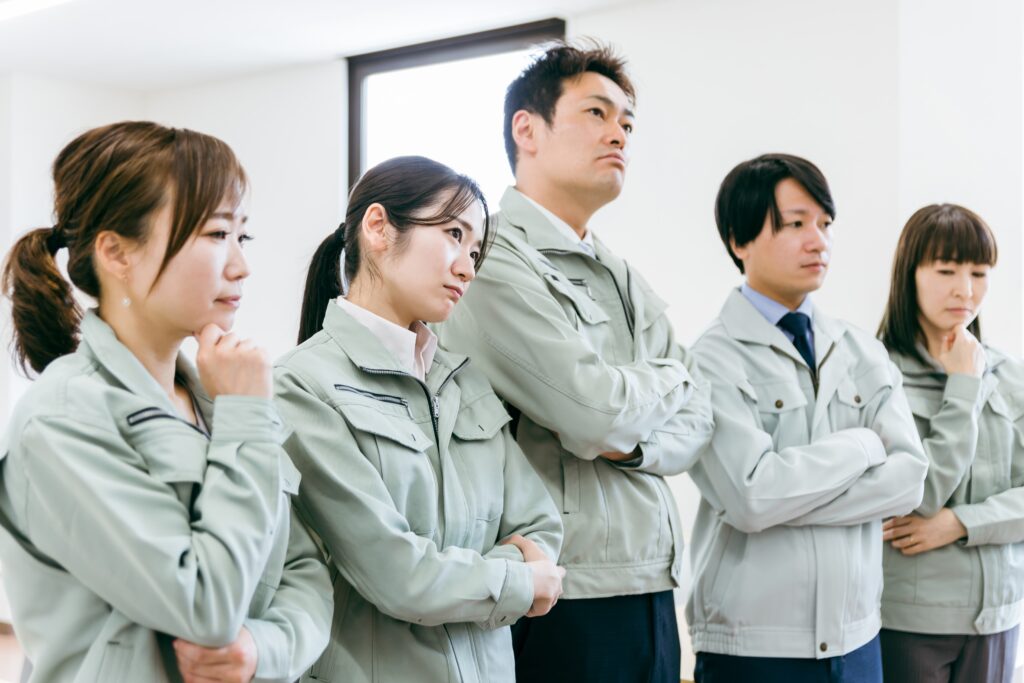
品質不良が発生すると企業や消費者に次のような悪影響を与えます。
コストの増加
品質不良が発生すると、企業はさまざまな追加コストを負担する必要があります。例えば、不良品の修理、再製造、廃棄の費用、顧客からの返品、交換対応の費用などが挙げられます。
また、不良原因を特定し、再発防止策を講じるための検査、試験のコストも発生します。これらの追加コストは企業の収益を圧迫し、財務状況に悪影響を与えます。
ブランドイメージの低下
品質不良は企業のブランドイメージに直接影響します。顧客が購入した製品に不満を感じると、その不満は口コミやレビューを通じて広がります。特に、SNSやオンラインレビューサイトでは、ネガティブな評価は迅速に拡散するため、ブランドイメージの低下は避けられません。信頼性が損なわれると、既存顧客だけでなく、新規顧客の獲得も難しくなり、市場での競争力が低下します。
法的問題の発生
品質不良が重大な場合、企業は法的責任を問われることがあります。不良品が市場に出回ることで、消費者に対する損害賠償請求や集団訴訟のリスクが高まります。また、製品が法律や規制に違反している場合、罰金や制裁が課されることもあります。これらの法的問題は企業の信用を損ない、経済的な負担を増大させます。
品質不良の原因となる4M
品質不良の原因は「4M」に分類されます。「4M」とは、Man(人)、Machine(機械)、Material(材料)、Method(方法)です。
Man
人為的なミスや誤操作が品質不良を招くことがあります。従業員のスキルや意識、教育・訓練の不足が主な原因です。例えば、作業手順の間違いや、確認不足などがあげられます。
Machine
機械の故障や不具合が品質不良を引き起こすこともあります。部品の消耗などにより機械の精度が低下すると、製品の寸法や形状が設計通りにならないことがあります。これを防ぐためには、定期的な点検を実施し、機械の性能を維持することが重要です。
Material
材料の質が悪いと、製品の品質も低下してしまいます。例えば、材料に不純物が多いと、製品の強度や耐久性が低下することがあります。これを防ぐためには、材料の品質を厳密にチェックし、信頼できるサプライヤから調達することが重要です。
Method
製造方法の問題も品質不良の原因となります。製造プロセスの一例として、温度や湿度、圧力などの環境要因や、部品の締め付けトルクなどが適切でない場合、製品の品質が均一にならないことがあります。これを防ぐためには、製造プロセスの条件を明確にし、作業手順書を作成することが重要です。
品質不良の原因を分析する方法
品質不良の原因を特定し、対策を考えるには、さまざまな分析方法を活用することが重要です。
PDCAサイクル
最も良く利用されている手法が、PDCAサイクルです。計画(Plan)を立て、実行(Do)し、評価(Check)し、改善(Action)するサイクルを繰り返すことで、品質向上を図ります。例えば、品質不良の防止策を計画し、実際に実行した後に結果を評価し、改善を加えていくことで最適案を生み出します。
フィッシュボーンダイアグラム(特性要因図)
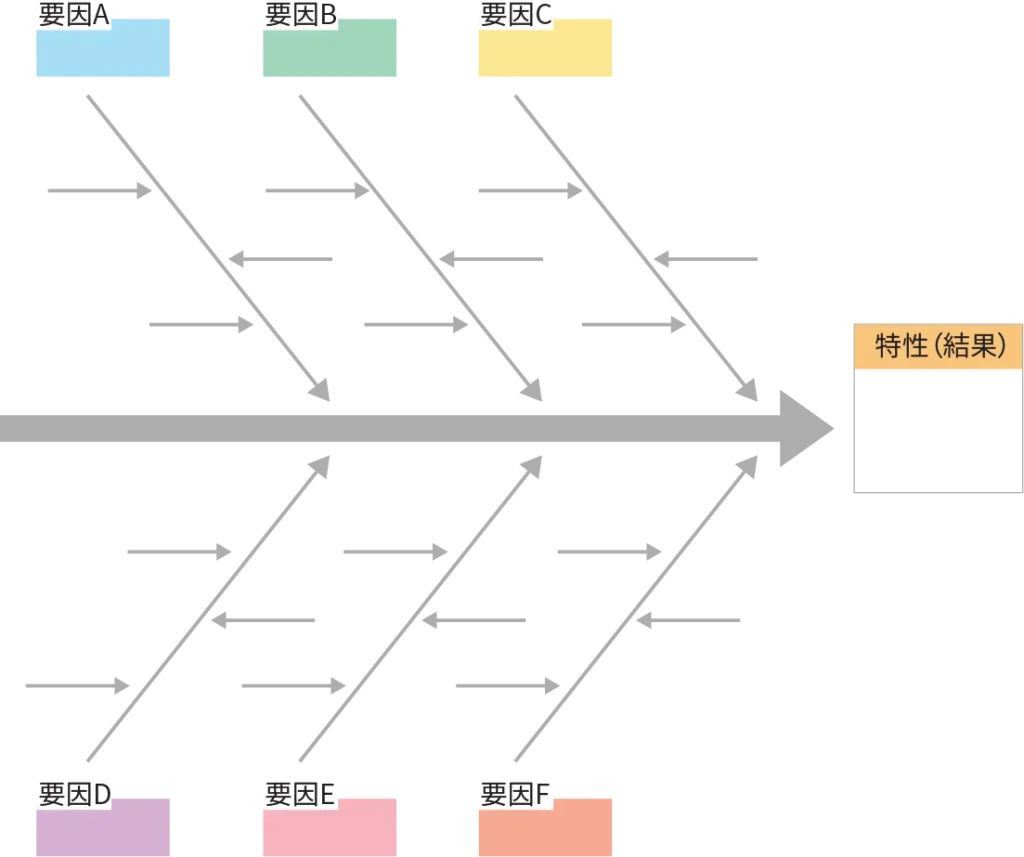
フィッシュボーンダイアグラム(特性要因図、魚の骨図とも)は、品質不良の原因を視覚的に整理するためのツールで、QC7つ道具の一つです。原因と結果の関係を明確化できます。例えば、フィッシュボーンダイアグラムを用いて、4M(人、機械、材料、方法)の各要因を分析し、品質不良の根本の原因を特定する場合などに利用します。
なぜなぜ分析
なぜなぜ分析(5 Whys Analysis)は、問題の根本原因を特定するためのシンプルで効果的な手法です。品質不良が発生した際に、その原因を掘り下げるために「なぜ」を繰り返し尋ねることで、表面的な原因から本質的な原因にたどり着くことができます。
例えば、機械の不調による品質不良の場合、なぜなぜ分析を利用することで、単に不良箇所を修理するだけではなく、メンテナンス周期の見直しや設備そのものの入れ替え、別の生産ラインの活用など適切な防止策が変わる場合があります。
品質不良の防止策10選
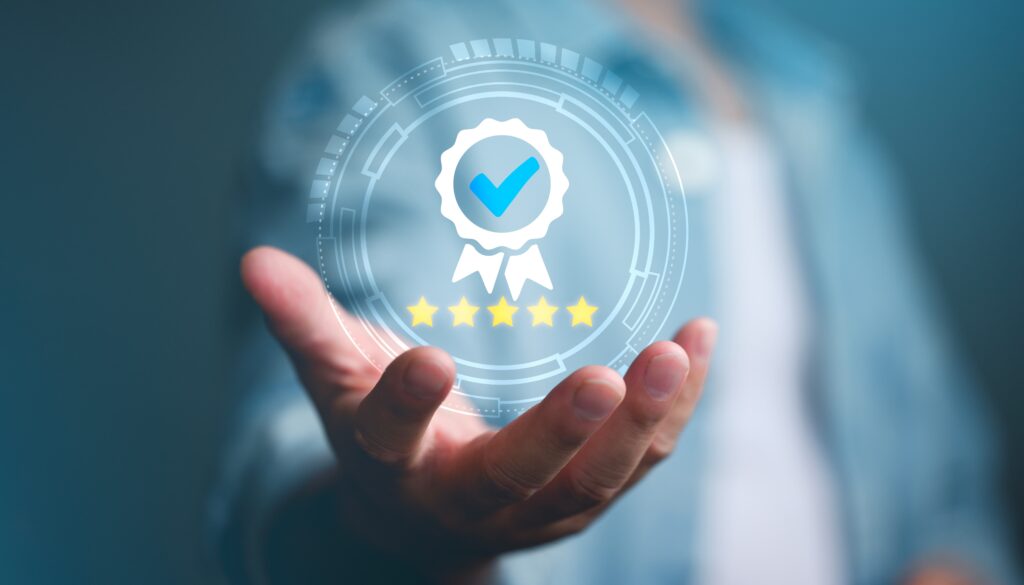
品質不良を未然に防ぐためには、さまざまな対策を考えることが必要です。
材料の入荷検査の強化
入荷時に材料の品質検査を実施し、材料の品質を確保して、不良品の発生を未然に防ぎます。具体的には、受け入れ検査の基準を明確にし、定期的なサンプルチェックや詳細な検査を行うことで、品質のばらつきを最小限に抑えます。
作業標準化
作業手順を標準化することで、品質のばらつきを減らすことができます。標準作業手順書を作成し、全従業員に共有することが必要です。従業員が同じ手順で作業を行うことで、製品品質の一貫性が確保され、ミスや不良品の発生を防ぎます。
ルール作り
品質管理のためのルールを決め、全員が必ず守る体制を整えます。これには、作業手順、検査基準、安全規則などが含まれ、ルールの徹底と継続的な見直しが重要です。全員がルールを理解し、遵守することで、品質の向上が期待できます。
体制作り
品質管理のための組織体制を整え、責任の所在を明確にします。品質保証部門の設置や責任者の決定、専門家の配置が重要です。明確な役割分担と責任の設定により、問題が発生した際に迅速かつ適切に対応できます。
サプライヤの選定
信頼できるサプライヤを選び、長期的な協力関係を築くことも必要です。サプライヤの評価基準を設け、定期的に見直しを行うことが重要です。
検査の強化
製造工程での検査を強化し、品質不良を早期に発見します。検査項目の見直しと適切な検査機器の導入が必要です。定期的な品質監査やスポットチェックを実施することで、不良品の流出を防ぎます。
従業員の教育・訓練
従業員のスキル向上と意識改革が重要です。定期的な教育や新入社員教育や継続的なスキルアップトレーニングを実施します。従業員が最新の知識と技術を身につけることで、作業ミスや品質不良を減少させることができます。
設備メンテナンスの強化
設備や機械の定期的なメンテナンスを行い、故障や劣化を防ぎます。メンテナンスの計画をあらかじめ立てておくことが重要です。計画的なメンテナンスにより、製造プロセスの安定性と製品品質が向上します。
品質管理体制の見直し
品質管理体制を見直し、改善点を洗い出します。内部監査や外部監査の結果を基に、品質管理プロセスを継続的に改善することが必要です。これにより、品質管理の効率が向上します。
システム導入
品質管理システムを導入し、リアルタイムでデータに基づいた管理を行います。自社にあったシステムの選定と導入計画が必要です。システムを活用することで、品質データの収集、分析、改善が効率的に行えます。
品質不良がなくならない工場の特徴
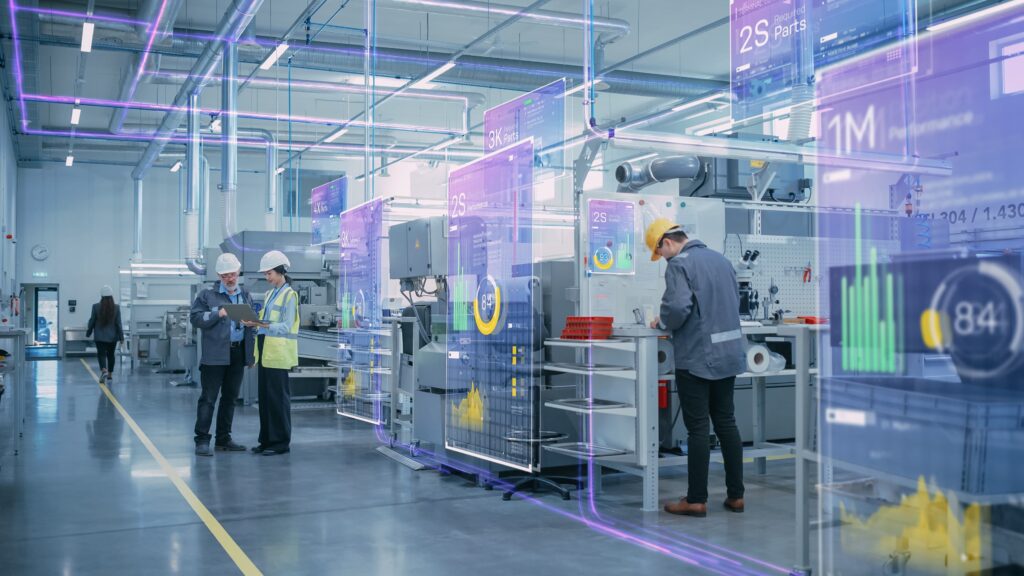
品質不良が多発する工場には、次のような特徴があります。これらの特徴を理解し、改善することが品質向上に役立ちます。
- 品質管理システムが導入されていない
- ルールと手順の未整備で曖昧
- 設備メンテナンス計画がない
- 教育・訓練が適切に行われていない
- 部門間でコミュニケーションが不足している
- サプライヤの管理基準が定められていない
- 品質データが収集、活用されていない
- 品質に対する意識が低い
特に人口減少が進み、人手不足が深刻な問題となるなか、今後は熟練工の経験に頼る生産体制の維持が難しくなります。検査工程の自動化や品質管理システムの導入により、人に依存しない品質管理体制の構築が重要です。
品質不良が発生した際の対応
製品の品質不良が発生した場合、それに迅速かつ効果的に対処することは、企業の信頼性と顧客満足を保つために不可欠です。実際に品質不良が発生した場合には、一般的に次のような対応を行います。
影響範囲の調査
不良品が発生した場合、その影響範囲を迅速に調査し、被害を最小限に抑えます。例えば、不良品が出荷された数や、流通先を特定します。これにより、影響を受ける可能性のある製品を正確に特定し、適切なリコール措置をとることができます。
原因の調査・分析
不良品の発生原因を詳細に調査し、分析を行います。例えば、製造工程の見直しや材料の検査を行い、根本原因を特定します。具体的には、不良品を生産した機械の操作条件、材料の品質、サプライヤー、作業員の技術レベルなど、様々な要因を詳細に調査し、原因を特定します。
改善・解決策の実施
原因が特定された後、適切な改善策や解決策を実施します。例えば、製造プロセスの改善や機械のメンテナンス、作業指示の明確化などを行います。これにより、将来的な品質不良発生のリスクを減少させることが可能となります。
品質不良をなくすには生産管理システムの導入がおすすめ
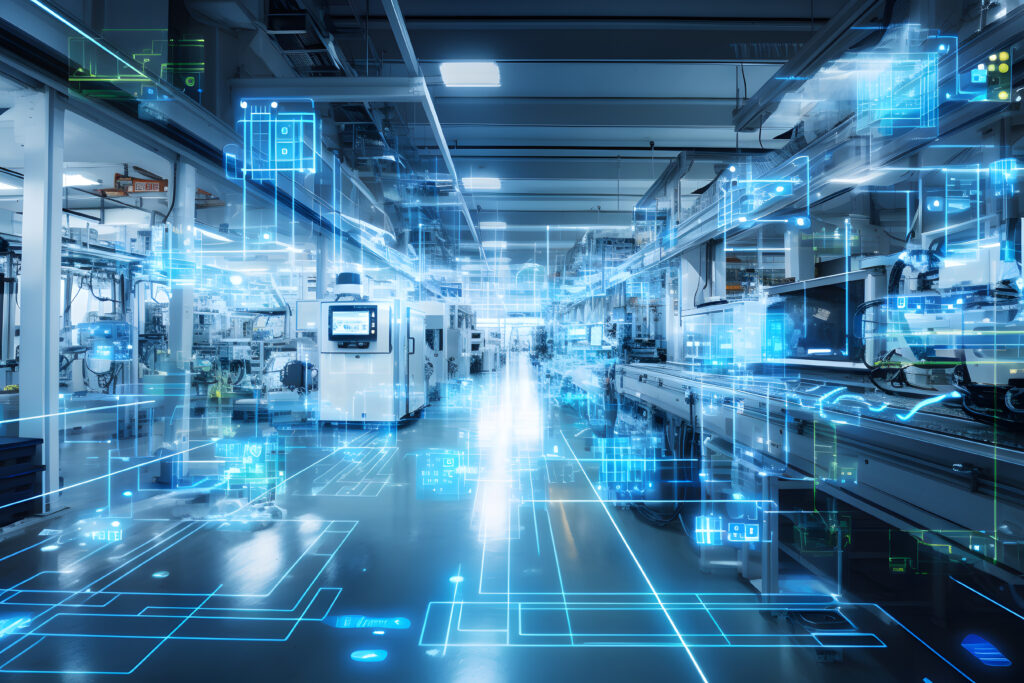
品質不良を減らすには、品質管理機能を備えた生産管理システムの導入がおすすめです。生産管理システムを導入することで、製造工程と品質情報の一元管理が可能になります。
たとえば、完成品で品質不良が見つかった際、各工程や原材料、各検査データを生産管理システム内に記録していると、すぐに製造データを調査できます。このようなトレーサビリティの強化で、品質不良の要因特定に役立てることができます。
生産管理システムの品質管理機能の具体例を挙げると、原料受入検査、工程内検査、製品検査記録、ロット管理、期限管理などがあります。品質管理も行える生産管理システムを選びたい場合は、これらの機能が十分にあるか確認することをおすすめします。
22種類の生産管理システムをランキングで比較
初期費用相場や選び方のポイントをチェック
生産管理システムをそれぞれの特徴や初期費用相場などで比較したい場合は、「生産管理システムランキング」も是非ご覧ください。生産管理システムは、自社の製品・生産方式・企業規模などに適したものを導入しないと、得られるメリットが限定されてしまいます。事前適合性チェックや生産管理システムを選ぶ前に押さえておきたいポイントも解説していますので、製品選びの参考にしてみてください。