ECRSの原則で生産・管理業務の改善活動を後押し!具体例と活用方法を図解付きで紹介
公開日:2024年09月17日
最終更新日:2025年03月15日
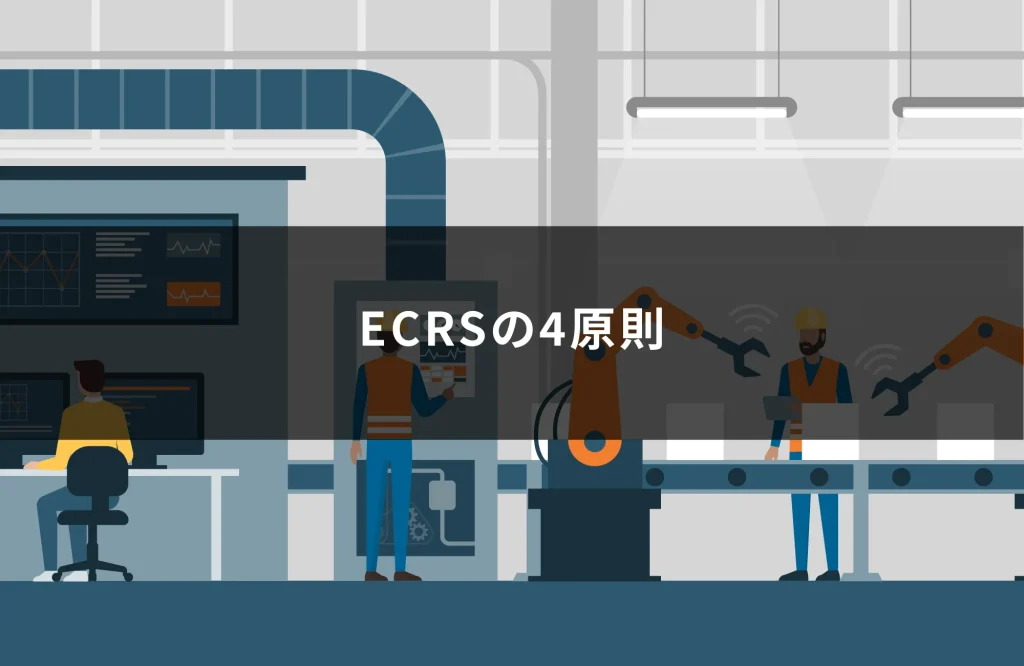
ECRSの原則は、製造業を中心とした業務改善を加速し、業務効率化やコスト削減を実現できるフレームワークです。不要な工程の排除や工程の統合、作業順序の見直し、そしてシンプルなプロセスへの転換、の4つの要素からなります。
本記事では、ECRS視点での改善活動のメリットについて、生産現場・管理業務における改善例を図解付きで解説します。さらに、生産管理システムを活用して効率化を実現した企業様の事例を紹介します。
ECRSの4原則とは
ECRSの4原則とは、業務プロセスを見直し、あらゆる業務を効率化するためのフレームワークです。
ECRSの各項目 | 概要 |
Eliminate(排除) | 不要な作業をなくす |
Combine(結合) | 作業をまとめて効率化 |
Rearrange(交換) | 作業順序の最適化 |
SimplifyU(簡素化) | シンプルな工程にする |
製造業では、生産業務のみならず、管理業務における改善活動で活用されます。改善検討は、E→C→R→Sの順番で実施することで、より早く高い改善効果を得られます。
Eliminate(排除):不要な作業をなくす
Eliminateは、無駄な作業や不要な工程を排除することを指します。製造現場では、しばしば効率的でない作業や価値を生まない工程が存在します。これらを見つけ出して排除すれば、作業時間の短縮やコスト削減が可能になります。
既にある工程をなくすだけなので、ECRSの4原則の中で最も早く取り組むことができ、効果も見込めるステップといえます。一例ですが、次のような工程は排除しやすい工程と言えます。
- 不良率が極めて低い品物の全数検査
- 過剰な確認フロー
- 活用されていない管理表
業務の排除を検討する際は、現場の観察とデータ分析に基づく業務棚卸し、排除した場合に影響が出る業務や部署の確認が重要です。
Combine(結合):作業をまとめて効率化
Combineは、複数の工程・作業を結合して効率化を図ることを指します。似たような工程を一つにまとめることで、作業の効率が上がり、無駄な動作が減少します。Combineも、Eliminateに次いで実施コストやリスクが少なく、改善効果が出しやすい方法です。
例えば、異なる製品の組み立て工程を一つのラインで処理すれば、生産速度が向上します。また、管理業務においても、データ入力やレポート作成などの工程をまとめることで、労力と時間の節約が可能です。
Rearrange(交換):作業順序の最適化
Rearrangeは、作業順序やレイアウトの入れ替えや見直しを通じて、プロセスを効率化することを指します。製造現場では、作業の流れや設備の配置が作業効率に大きく影響します。EliminateやCombineと比べると、1つの施策による改善効果は小さくなる場合もありますが、長期的には重要な改善となるケースも多くあります。
具体的には、部品供給待ちの多い工程では、供給順序の見直しだけでも、作業時間の短縮ができる場合も少なくありません。また、機械の配置変更によって、作業動線を最適化し、作業者への負担軽減も可能です。短縮できた時間が1日当たり5分だとしても、毎日行う作業であれば年間20時間の工数削減につながります。
Simplify(簡素化):シンプルな工程にする
Simplifyは、作業や工程をできるだけシンプルにすることで、効率を上げる原則です。複雑な作業や工程はミスが発生しやすく、生産性が低下する原因となります。
例えば、在庫管理の現場では、在庫数を紙の棚札に手書きし、エクセルの在庫管理表へ転記する運用も少なくありません。しかし、在庫管理システムを導入すれば、よりシンプルな方法で在庫情報の更新や参照が可能となります。
ECRSの視点で進める改善活動のメリットと適用事例
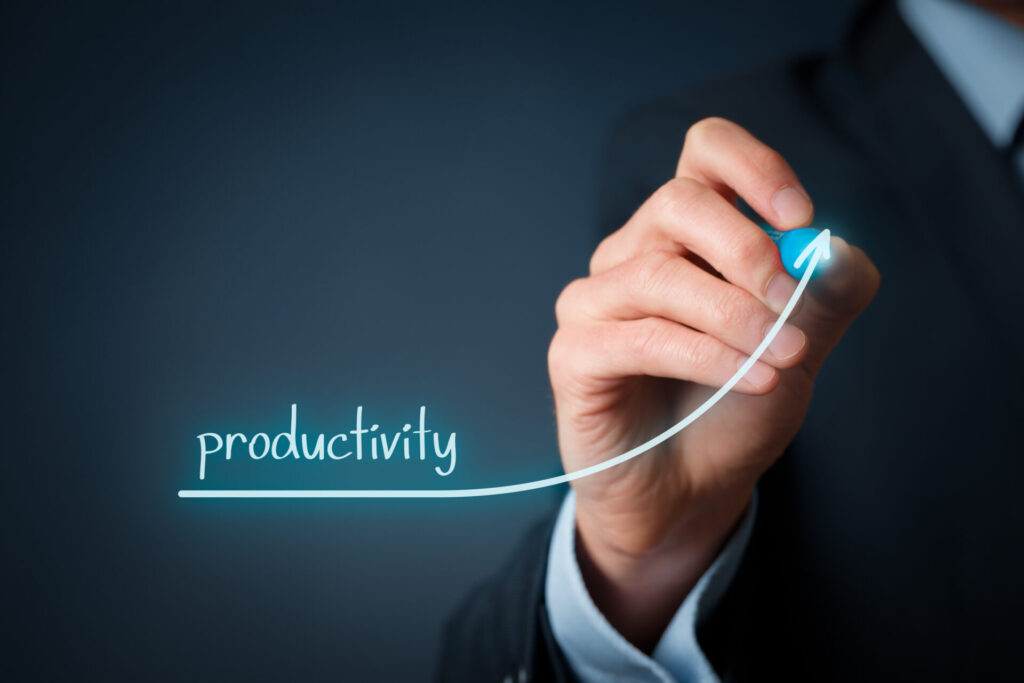
ECRSの視点でカイゼンを進めると、製造現場の生産業務だけでなく、生産管理業務においても多くのメリットが得られます。
生産・管理業務の効率化
ECRSの原則における「排除(Eliminate)」や「簡素化(Simplify)」を活用すれば、日常の生産業務や管理業務を効率化できます。
具体的な改善例として、手書き帳票による生産実績記入を廃止し、タブレット端末での実績入力へ切り替えすることが挙げられます。実績入力は必要ですが、時間情報を記載する手間がなくなり、実績入力した時刻を工程完了時刻として正しく記録できるようになります。さらに、入力したデジタルデータをそのまま活用できるため、手書き帳票をエクセル転記する作業もなくなります。
属人化の解消
「交換(Rearrange)」や「簡素化(Simplify)」の視点を適用し、属人化からの脱却が実現できます。製造現場において、熟練者の経験や勘に依存した作業が多い場合、経験の浅い作業者が対応することは困難です。
ここでは、NC旋盤において、製品品目ごとに作業員が都度手動で調整する作業を想定します。製品品目ごとに加工プログラムをパターン化して番号管理し、製品品目とパターン番号の対応表を作成します。このように作業手順の標準化を行うと、製品品目ごとの加工方法を明確にし、どの作業者でも同じ品質で加工可能にします。
製造コスト削減
「結合(Combine)」「簡素化(Simplify)」の観点でカイゼンを進めれば、製造コストの削減につなげることもできます。
複数品種でそれぞれ異なる規格のボルトを使用しているケースでは、ボルト規格統一により製造コストの削減が可能です。製品設計時点でボルト共通化の思想を徹底すれば、量産時にボルトの調達・在庫管理などがシンプル化できます。これにより、職場での部品点数が削減され、部品管理コストの圧縮が期待できます。部品11点当たりの発注量が増えるため、スケールメリットにより調達コスト交渉も有利になるでしょう。
ヒューマンエラー削減による不良率低下
ECRSの原則に基づいて複雑な作業を減らせば、ヒューマンエラーを削減し、不良率を減らすこともできます。
例えば、部品組み立て作業において、作業員が手作業でネジ締めを行う場合、ネジの緩みや締めすぎによる不具合が発生しやすいです。しかし、ポカヨケとして、手作業でのネジ締め作業を電動トルクドライバーに切り替えれば、適切な強さでのネジ締めが可能になります。
ECRSでの改善活動における4つのポイント
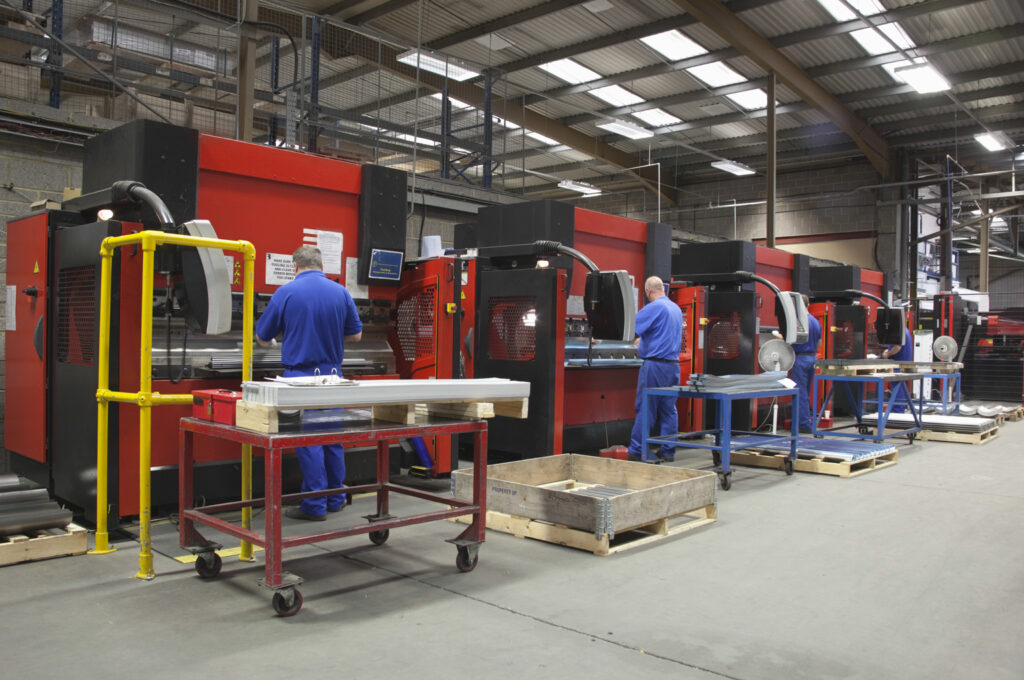
ECRSの原則を業務改善に活かすためには、フレームワークを実践できる形に落とし込むことが重要です。このために意識しておきたい4つのポイントを解説します。
業務改善の目的を明確にしてから取り組む
ECRSを活用した業務改善に取り組む際には、まず目的を明確にします。目的が曖昧なままでは、現場の負担が増えるだけで、効果的な改善に繋がりません。
何を達成したいのか、そのためにどのプロセスをどのように改善したいのか、具体化することが大切です。改善活動の目的が「作業時間を短縮する」なのか、「品質不良を減らす」なのかで、適用すべきECRSの視点も変わります。
正確なデータで現状を分析する
ECRSの原則に基づく改善活動では、感覚や経験だけに頼るのではなく、正確なデータをもとに分析することが欠かせません。一例ですが、次のようなデータを分析して、改善点を洗い出します。
- 作業時間の記録:時間のかかる工程を特定する
- 設備稼働率:ムダな待機時間がないか確認する
- 品質不良の発生率:不良発生頻度の高い工程を絞り込む
このように、客観的データを根拠として改善余地を抽出すれば、ECRSのどの原則を適用すべきか判断しやすくなります。具体的には、「エクセル入力に時間がかかっている」というデータがあれば、手作業の排除(Eliminate)やシステム化(Simplify)が有効だとわかります。
現場全体での実施を目指す
ECRSの視点で改善を進める場合、現場全体で連携して進めることが必須です。1つの工程内での取り組みでは個別最適に陥り、現場全体としての効率化に貢献できないケースもあります。一方で、現場の実情を知らずにトップダウンで改善を進めると、かえって作業の負担が増え、現場の混乱を招くこともあります。
現場の作業者とコミュニケーションを取りながら、「どこにムダがあるか?」を一緒に考えていきます。職場全体の意見を取り入れながら、ECRSの原則を当てはめれば、よりスムーズに改善活動を進められます。
例えば、次の図に示す金属部品加工の改善事例では、材料運搬・保管に関する改善、工程の統合に関する改善の2点を行っています。このように工程を跨いだ改善は、職場全体の連携があって初めて実現します。
情報共有や分析にシステムを活用する
ECRSの原則に沿って改善点を見つけるためには、システムを活用した情報整理やデータ分析が有効です。利用するシステムには次のようなものがあります。
- 生産管理システム → 作業時間や生産実績をリアルタイムで記録し、ムダを可視化
- 品質管理システム → 不良品の発生状況をデータで管理し、原因分析を効率化
- 工程管理システム→ 作業進捗をリアルタイムで追跡し、ボトルネックを早期に発見
手書きの記録やエクセル管理では、情報の共有や分析に時間がかかります。しかし、これらのシステムを活用すれば、リアルタイムでデータを確認しながら継続的にPDCAサイクルを回すことができます。
一例ですが、品質検査として重量を測り、測定結果を手書き帳票に記載して、エクセルに集計する一連の作業を考えます。この場合、秤量機をシステムと連動させて記録すれば、手書き帳票への記載、エクセル転記の2つの作業を同時に排除することができます。さらに検査直後からシステム上で結果を確認できるようになり、品質不良発生の早期検出も可能になります。
ECRS視点での改善は生産管理システムで実現できる
製造業におけるECRSの原則を活用した改善活動は、生産管理システムの活用が効果的です。
生産管理システムとは
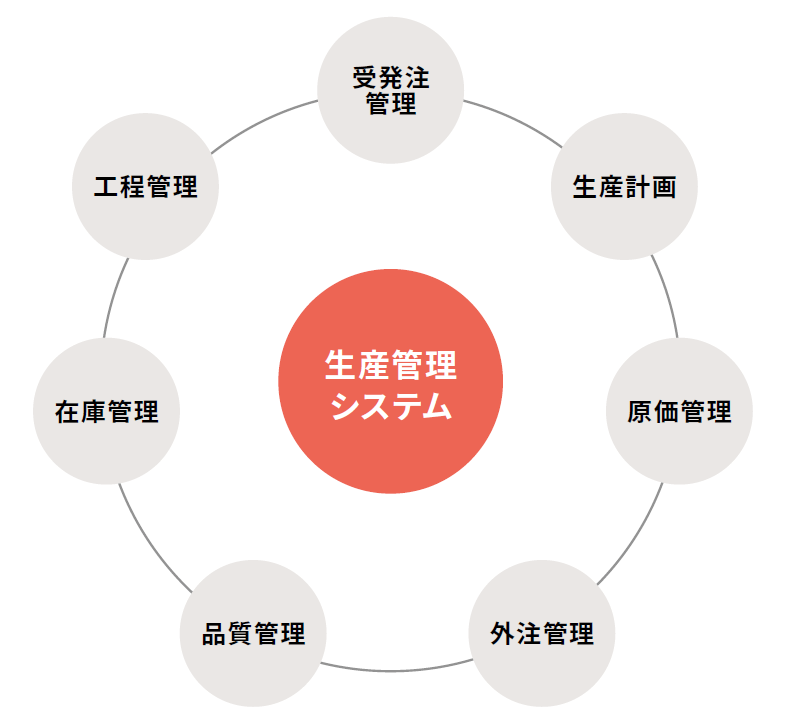
生産管理システムとは、以下のような情報を一元管理できる製造業向けシステムです。
- 在庫情報(日々の入出荷、棚卸しなど)
- 工程進捗(各工程の進捗、実績工数、生産性など)
- 原価(予定原価、実際原価など)
- 品質情報(検査データ、不良率など)
これらの情報を紙やエクセルで管理をしている場合、システムを導入するだけでも管理工数を減らす改善効果(Eliminate)が見込めます。複数の作業の一元化(Combine)や作業フローの簡素化(Simplify)も実現できます。生産管理システム上に蓄積された各データを分析すれば、さらなる改善のヒントを得ることもできます。
生産管理システムは一般的に高価ですが、クラウド運用のパッケージシステムでは比較的安価に導入できるケースも多いです。また、費用負担を軽減したいというニーズに応えるため、課題を感じている機能に絞って導入が可能なパッケージも存在します。
→在庫管理機能に絞ったシステム導入で、既存システムと共存しながらピンポイントに課題を解決した事例
【例1】在庫管理システムの分析で在庫コストを削減した事例
生産管理システムの在庫管理や発注機能を活用すると、入荷から出荷までの全工程をリアルタイムで追跡し、データを自動蓄積できます。
例えば、原材料の発注リードタイムと使用量を分析し、在庫を持たずに都度発注で済むものを見つけたり(Eliminate・Simplify)、発注ロットを見直したりできます。この事例では、システム導入によって、在庫圧縮と管理工数の圧縮だけでなく、属人化からの脱却も実現しました。
詳しい事例はこちらで解説しております。
→在庫分析で在庫金額を年間1000万円圧縮し、管理工数削減に成功した事例
【例2】進捗管理のシステム化で柔軟な生産計画調整を実現した事例
生産管理システムには、作業日報をデータ管理し、リアルタイムに工程進捗を確認できるようになる機能を持つものがあります。
ある成形品業界の企業では、紙の作業日報の集計管理に膨大な時間を要していました。しかしこれをシステム化することで、生産状況がリアルタイムで把握できるようになりました。さらに、不良発生そのものを速やかに検出できるようになり、紙の作業日報の束を見返す必要もなくなりました(Eliminate・Combine・Simplify)。
詳しい事例はこちらで解説しております。
→紙の作業日報のエクセル集計業務を排除し、年間1200時間の工数削減に成功した事例
22種類の生産管理システムをランキングで比較
初期費用相場や選び方のポイントをチェック
生産管理システムをそれぞれの特徴や初期費用相場などで比較したい場合は、「生産管理システムランキング」も是非ご覧ください。生産管理システムは、自社の製品・生産方式・企業規模などに適したものを導入しないと、得られるメリットが限定されてしまいます。事前適合性チェックや生産管理システムを選ぶ前に押さえておきたいポイントも解説していますので、製品選びの参考にしてみてください。