コントロールプラン(CP)とは品質リスク管理文書:QC工程表との違いも解説
公開日:2024年11月18日
最終更新日:2024年11月20日
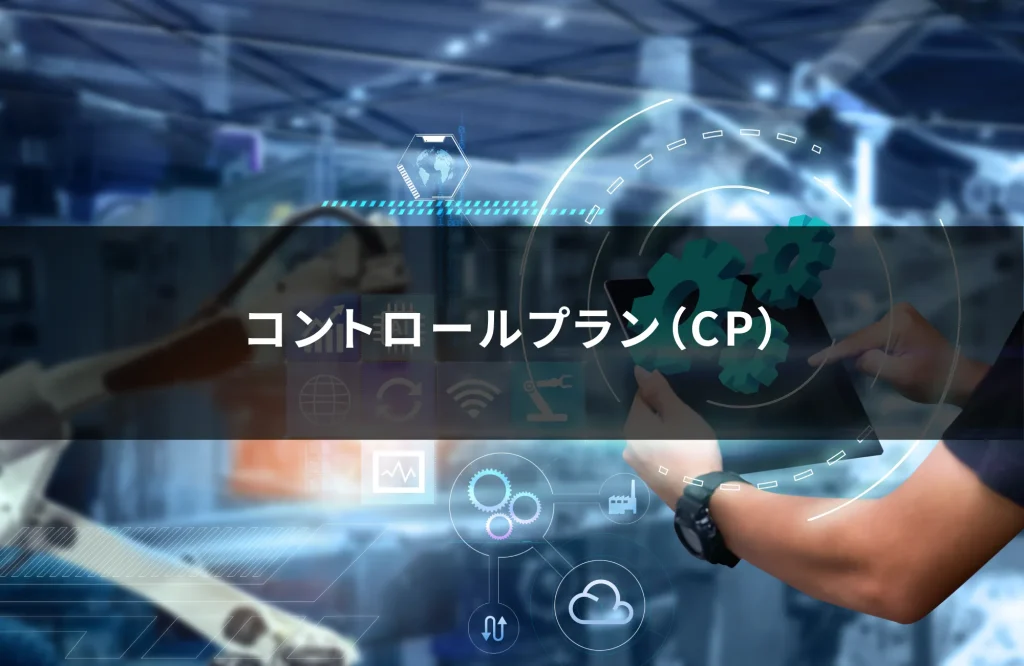
コントロールプランは、IATF16949の規格で推奨されているコアツールの一つです。厳しい品質を維持し、不良品の発生を防ぐために、適切なリスク管理計画が示されたQMS文書です。
この記事では、コントロールプランの基本的な考え方から、QC工程図との違い、含めるべき情報について詳しく解説します。また、設計段階から量産に至るまで、コントロールプランの作成単位の考え方や注意ポイントについて、具体例とともに詳しく解説します。
コントロールプラン(CP)とは?
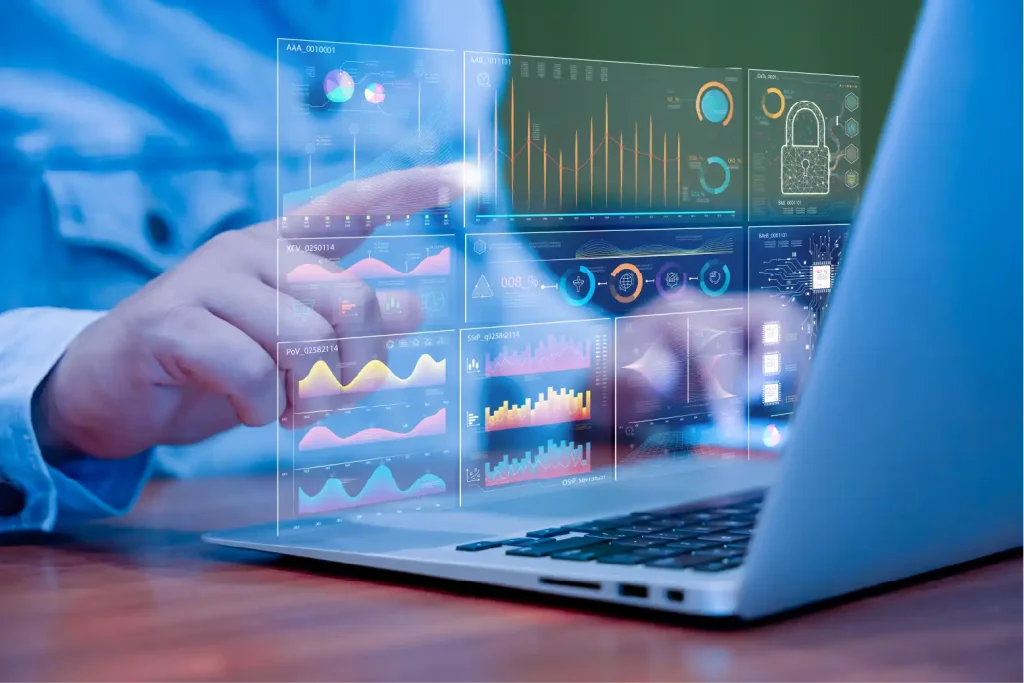
コントロールプラン(Control Plan)とは、製品プロセスで品質を維持するためのリスク管理計画が記載された文書です。この文書は、製品の設計段階から量産に至るまで、各工程における品質リスクを管理するためのガイドラインとして機能します。
IATF16949規格の工程リスク管理表:要求事項8.5.1.1 コントロールプラン
コントロールプランは、IATF16949規格要求事項で定められたコアツールの一つで、製品設計や製造プロセスにおける品質リスク管理を実行するための詳細な計画書です。
設計FMEA(故障モード影響解析)やプロセスFMEAの結果を反映させて作成され、潜在的な不具合・欠陥を未然に防ぐための管理方法を策定します。
QC工程表との違い
QC工程表は、特定の製造工程における管理基準を一覧化した表のことをいいます。一方、コントロールプランは、IATF16949規格の要求事項に基づき、以下に示す要件の記載を含む必要があります。
- 段取り替え検証を含む製造工程の管理手段
- 初品、終品の妥当性確認
- 特殊特性に関する管理項目の監視方法
- 顧客からの要求事項
- 不適合発生時や、製造工程が不安定になった場合の処置
コントロールプランの作成単位
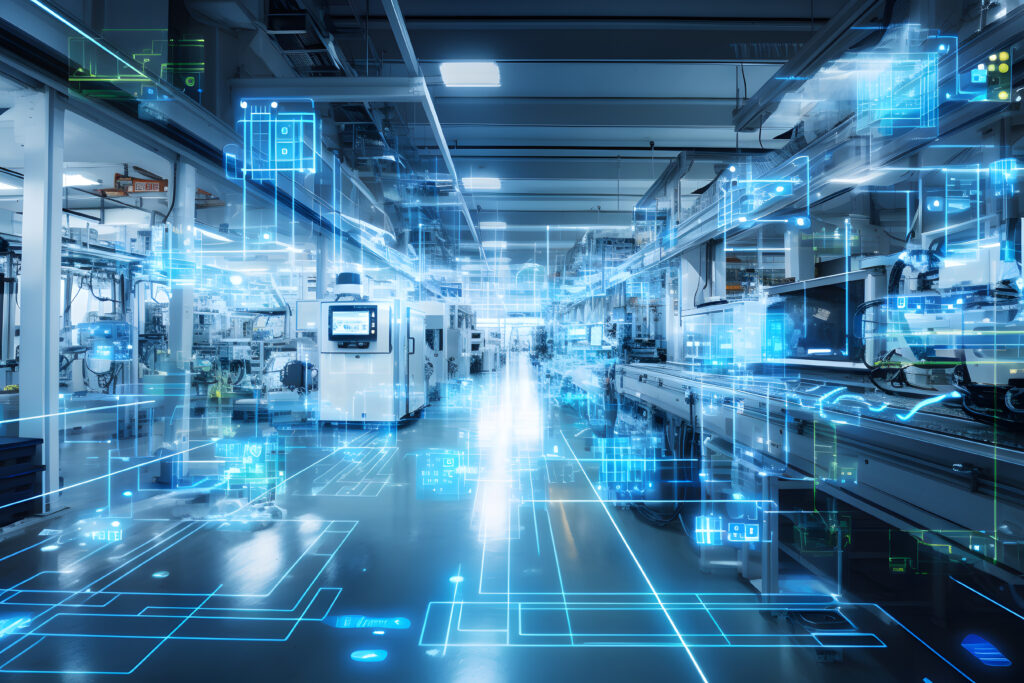
コントロールプランは、製品の設計や製造プロセスを階層に分けて、サプライチェーンの中で各階層ごとに作成します。これにより、各階層ごとの管理ポイントが明確になり、リスクを高い確度で品質面でのコントロールが可能となります。
コントロールプランの作成単位には、システム、サブシステム、構成部品、材料などがあります。以下は、ブレーキシステムについて作成単位ごとに具体例を記載したものです。
■ブレーキシステムの例
システム | 自動車ブレーキシステム | ||
サブシステム | 油圧ユニット | センサー | 電子制御ユニット(ECU) |
構成部品 | ブレーキキャリパー | 回転速度を検知するABSセンサー | マイクロプロセッサ |
材料 | ブレーキパッドの摩擦材 | センサーケーブルの被覆材 | プリント基板の絶縁材 |
システム
この階層では、システム全体の性能・信頼性に関する管理ポイントを定義します。例えば、ブレーキペダルを踏んだ際に、車両がどのように減速するか、システムが期待通りに機能するか、等の性能について管理方法を記載します。
サブシステム
サブシステムとは、システムを構成する部分的な機能・構造のことを指します。サブシステム単位のコントロールプランは、システム全体のコントロールプランを補完する位置づけとなります。
ブレーキシステムの例では、構成する要素の一つが油圧サブシステムです。このサブシステムでは、ブレーキペダルを踏んだ際に油圧が発生し、ブレーキキャリパーを動かして車輪に制動力を伝えます。コントロールプランでは、油圧の発生・伝達の精度や異常時の動作などについて、具体的な管理方法を記載します。
構成部品
サブシステムを構成する、独立した機能を持ったコンポーネントに対して、サブシステムの信頼性を確保するための品質管理ポイントを明確にします。
油圧サブシステムの基幹部品であるブレーキキャリパーは、ブレーキパッドをディスクに押し付けて摩擦を発生させます。キャリパーが正常に動かなかったり、部品の隙間が均一でなかったりすると、ブレーキの効きが悪くなるリスクがあります。そのため、キャリパーの組み立て時に、決められた品質基準や部品寸法の誤差が規定範囲内であるか、その管理方法と合わせてコントロールプランに盛り込みます。
材料
構成部品に使用される素材の品質管理方法を規定します。具体的には金属・樹脂などが該当し、材料特性に関する検査基準やサプライヤーでの工程管理手順管理手順を文書化します。
ブレーキパッドに使われる摩擦材は、ブレーキ性能に大きく影響する重要な材料です。材料レベルでは、摩擦材の硬度や耐熱性、摩耗特性が規格を満たしているかを、具体的な検査方法とともにコントロールプランに明記します。この管理により、製品が長期間にわたって安定して動作し、性能を発揮することが保証されます。
作成単位の選び方とその影響
コントロールプランの作成単位は、購入品および自社工程で管理可能な階層とすることが望ましいです。購入品の製造工程まで掘り下げると、自社で管理できない範囲まで含まれるため、有効性の担保が困難となります。
例えば、自社でブレーキキャリパを製造している場合、ブレーキキャリパの製造プロセスに着目してコントロールプランを作成します。重要な材料であるブレーキ摩擦材をサプライヤーから購入している場合、特殊特性を主軸とした重要管理項目を自社コントロールプランに記載します。その他の摩擦材における重要な製造工程などは、コントロールプランをサプライヤーで作成いただき、監査にて確認します。
コントロールプランを作成する段階
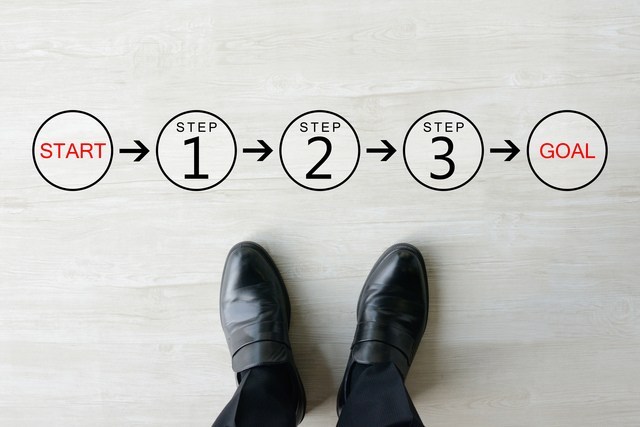
コントロールプランは、顧客から要求があった場合、製品設計における各段階で作成します。設計〜プロトタイプ作製段階、量産試作前段階、量産段階で想定すべきリスクが異なるためです。
製品設計・製造プロセスの試作検証時
製品・製造プロセス構築の設計段階では、試作コントロールプランを作成します。製品の最終仕様がまだ確定していないため、コントロールプランは基本的な内容になり、試作を重ねる中で修正を重ねていきます。
具体的には、設計FMEAやプロセスFMEAの結果を元に、機能、形状、材料特性などの重要な管理特性を特定します。その上で、各管理対象となる数値の範囲が明確になり十分な課題抽出・検証ができるまで、試作検証を繰り返し実施します。この試作検証では、試作用の小規模設備を使って少量で行うことが一般的です。
量産に近い条件での試作時
量産に近い条件での試作時には、量産試作コントロールプランを作成します。製品の設計や製造プロセスがほぼ確定しているため、実際の製造条件、設備、ツールの設定など、量産時に採用予定の作業手順や検査基準・方法で実施します。
この段階では、製品の試作を通じて得られた重要管理項目の工程能力指数Cpkを算出したり、測定システムの精度確認など
本格的な量産移行時
本格的な量産時は、試作段階での抽出された問題点を網羅して作成された、最終形である量産コントロールプランを使用します。
量産時には、量産コントロールプランの記載に則り、製品や製造プロセスにおける品質の安定性を確保します。
さらに、量産開始後も、量産時の初期流動管理を踏まえた対応や、量産の中で起こった異常の是正措置などがあれば、都度アップデートして完成度を高めていきます。
コントロールプランに記載すべき情報
コントロールプランには、製品・プロセスを適切に管理するための情報が必要です。管理特性やその管理方法などを正確かつ詳細に盛り込むことで、製品の品質リスクを管理します。
工程ごとの管理すべき特性
製造工程ごとに、管理すべき特性を特定することは、品質管理の基本です。これには、製品の性能や安全性に影響を与える要素が含まれます。適切なモニタリング・管理で、品質のばらつきを防止します。
これらの特性を明確にすることで、各工程で何をチェックすべきかが明確になり、品質基準を守るための指針となります。
特殊特性
特殊特性(Special Characteristics)は、製品の安全性や機能性に大きな影響を与える特性であり、顧客要求や法規制に基づく厳しい管理が必要です。
例えば、自動車のブレーキパッドでは、材料である摩擦材の硬度や耐熱性、摩耗特性が設計範囲内であることが重要です。このため、これらを特殊特性として管理することで、製品が長期間にわたって安定して動作し、性能を発揮することが保証されます。
特殊特性についての詳しい解説はこちらの記事で解説しているので、合わせてご参照ください。
→特殊特性とは?IATF16949要求事項、CC・SC・KC特性との関係まで徹底解説
規格値とその許容範囲
規格値(Specification Value)とは、製品・プロセスにおける特定の特性について、製品が設計通りの性能を満たす代表的な値をいい、許容範囲(Tolerance)は、その特性値が許される範囲(公差)を示します。
コントロールプランには、各管理特性ごとに規格中央値とその許容範囲が設定され、これを逸脱する場合は不良品として扱います。設計仕様における試作検証の中で特に重要な特性については、上下限検証の評価結果に基づいて許容範囲が決定されます。
検査方法・測定頻度
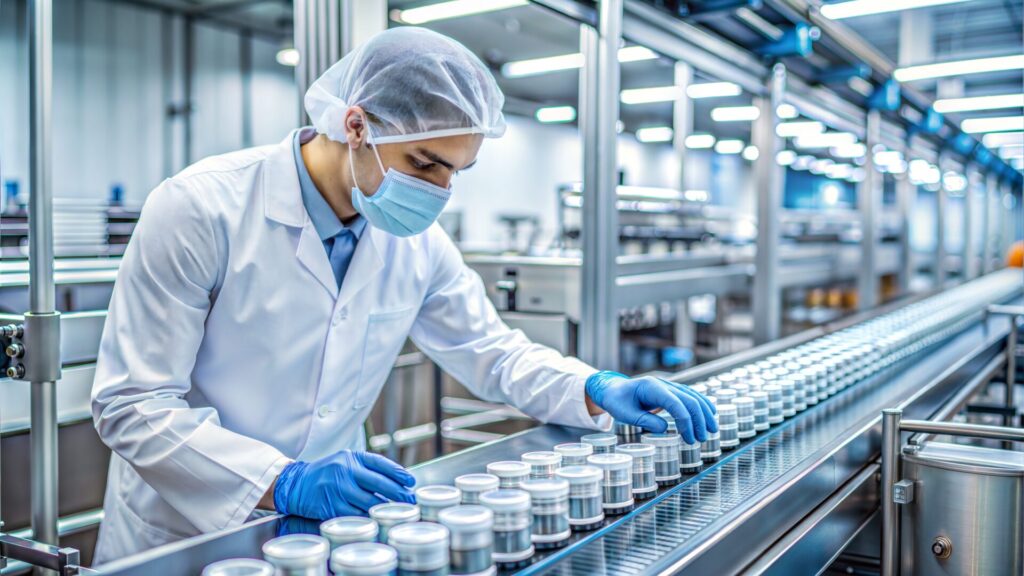
製品やプロセスの品質を確認するために、適切な測定システムで品質検査を行います。品質検査について、コントロールプランで記載すべき項目は次の通りです。
- 各工程でどのような検査を行うか
- どのようなツールや装置を使用するか
- 検査の頻度・サンプル数
具体的な品質検査の方法には、視覚検査、寸法測定、非破壊検査、機能試験などがあり、製品の特性や求められる品質基準に応じて選定します。また、これらの検査に使用する測定システムは、GR&RやMSAによって測定の精度や再現性が確保されている必要があります。
標準作業の手順書
実施されている品質検査は、手順が明確になるように標準作業を定め、それが速やかに参照できるように文書番号を記載します。具体的には、各項目について、作業標準書(SOP)やチェックシートの文書番号を記載します。
標準作業の手順書をコントロールプランに明記することで、製造現場担当者だけでなく、品質管理担当者や顧客は、製造工程・品質検査の各作業の位置づけを把握しやすくなります。
測定と監視の記録
コントロールプランには、測定と監視の記録について記載する必要があります。これらは、製品やプロセスが確実に実行されたことのエビデンスとして機能します。各工程で行われた作業実施記録、品質検査の結果を記録し、異常があれば直ちに適切な処置を実施します。
また、顧客要望を受けた際や品質監査時に、これらの記録を参照すると、管理基準が遵守されているかが確認可能となります。これにより、品質管理のトレーサビリティが確保され、問題発生時に原因の特定が容易となり、適切な対策を打てます。
また、記録の分析を行い、プロセス改善や品質向上のためのデータとして活用することも可能です。
不適合時の対応計画
測定・監視の結果、規格外の品質不良が発生したり、統計的工程能力であるCpkなどが不足した場合に、必要な対応計画をコントロールプランに明記する必要があります。
例えば、製品の出荷前検査で品質不良が発生した場合、不適合品を識別するためにイエローカードを貼り付け、不適合品専用の保管場所へ移動させます。さらに、速やかに職制へ報告するなどの対応が必要です。
このような対応計画を事前に明示しておくことで、不適合品が誤って良品として出荷されるリスクを防ぎ、不適合品が発生した際に迅速かつ組織的に改善措置が可能になります。
不良品出荷の防止には、検品システムの導入も効果的です。例えば、日付検品システムを導入し、期限切れ製品の出荷を99%防止した事例もあります。システム事例はこちら:【日付検品システム】賞味期限切れの製品出荷を99%防止
22種類の生産管理システムをランキングで比較
初期費用相場や選び方のポイントをチェック
生産管理システムをそれぞれの特徴や初期費用相場などで比較したい場合は、「生産管理システムランキング」も是非ご覧ください。生産管理システムは、自社の製品・生産方式・企業規模などに適したものを導入しないと、得られるメリットが限定されてしまいます。事前適合性チェックや生産管理システムを選ぶ前に押さえておきたいポイントも解説していますので、製品選びの参考にしてみてください。