「自働化」とは?自動化との違いは?基本から導入メリットまで徹底解説
公開日:2024年08月29日
最終更新日:2024年09月06日
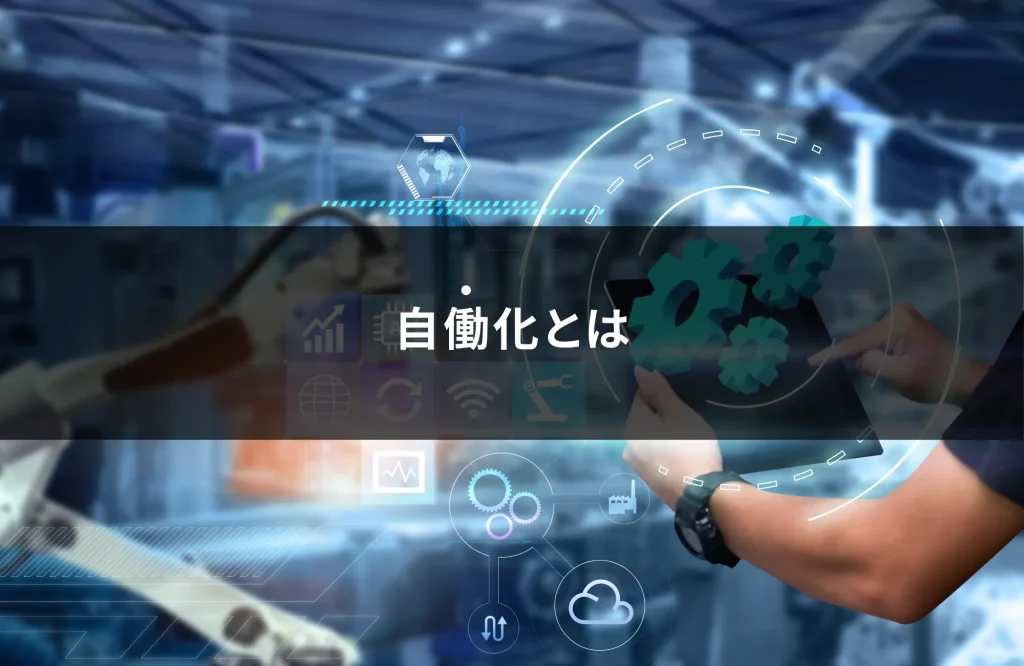
自働化は、製造業の生産効率を飛躍的に向上させるのにとても重要です。この記事では、自働化の基本概念から導入によるメリット、そして成功させるための重要なポイントまで解説します。また、異常の早期発見やコスト削減、品質向上を可能にするポイントを説明します。
自働化とは
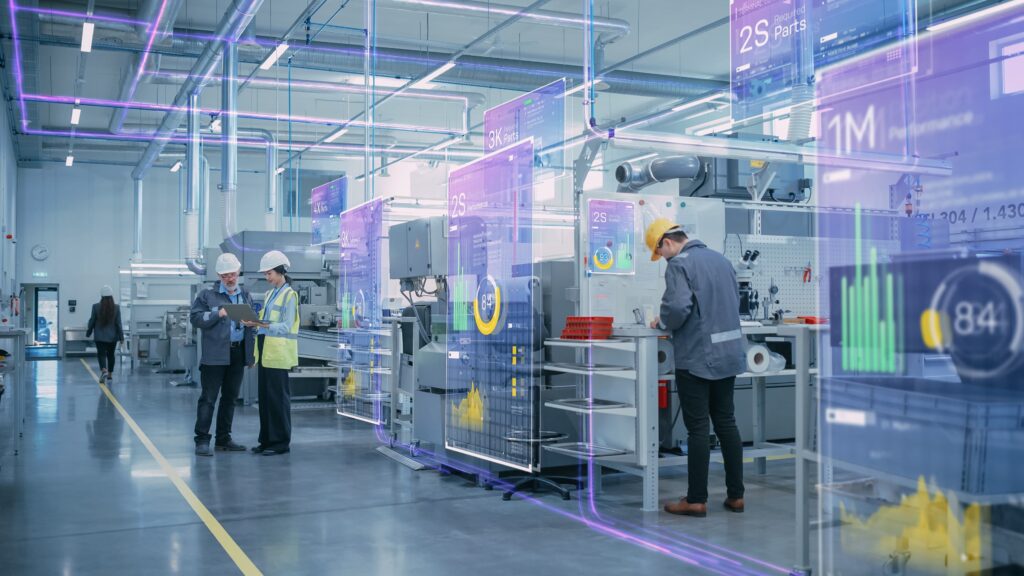
自働化とは、機械や設備が自動的に作業を行うだけでなく、異常が発生した際に自動で停止し、問題を知らせる仕組みを指します。
この概念は、トヨタ生産方式において重要な要素とされ、「人の知恵が生かされた自動化」とも言われます。自働化により、人の介入が必要な場面が減り、作業効率の向上や品質の安定が図れます。また、異常の早期発見により、不良品の流出防止やコスト削減にも貢献します。
自働化の目的
自働化の目的は、生産工程での異常を素早く検知し、生産ラインを停止させることで不良品の流出を防ぐことです。これにより、品質を維持しながら生産効率を向上させることができます。また、異常が発生した際にはすぐに対応できるため、不良発生などのトラブルの影響を最小限に抑えることができます。
自働化が役立つ場面
自働化が特に役立つのは、高い品質が求められる製品や大量生産が必要な場合です。また、人手不足が問題となっている現代の製造業においても、自働化を導入することで人件費の削減や生産効率の向上が可能になります。さらに、複雑な工程や危険な作業においても、自働化を活用することで安全性を確保しながら効率的に作業を進めることができるためとても有効です。
自働化と自動化との違い
自働化と自動化は似た考え方ですが、正確には異なります。自動化は人間の手で行っていた作業を機械化することを指しますが、自働化は、加えて異常を検知し、自動で作業を停止させる機能を持ちます。つまり、自働化は単に作業を自動にするだけでなく、品質管理や異常対応も含めた総合的な仕組みです。一般的な「自動化」という言葉と区別するために、「ニンベンのついた自働化」と呼ぶこともあります。
従来、機械やライン、品質の異常を判断・検知する作業は、人の手で行われていました。異常発生時に機械が自動で止まる仕組みを導入することで、これらの監視業務に人を割く必要がなくなり、生産ラインでの省人化を実現し、人間が他の業務に取り組めるようになります。
ジャストインタイムとの関係
自働化とジャストインタイム(JIT)は、トヨタ生産方式の2本柱で、あらゆるムダをなくすための重要な考え方です。
JITは必要なものを必要なときに供給する生産方式です。そこに自働化を導入し、作業工数と不良品をどちらも減らし生産効率を上げるというのが、トヨタ生産方式の土台となる考え方です。
参考:
トヨタ方式から学ぶ「7つのムダ」をなくす方法 本当に効率的な現場改善とは?
「自働化」のメリット
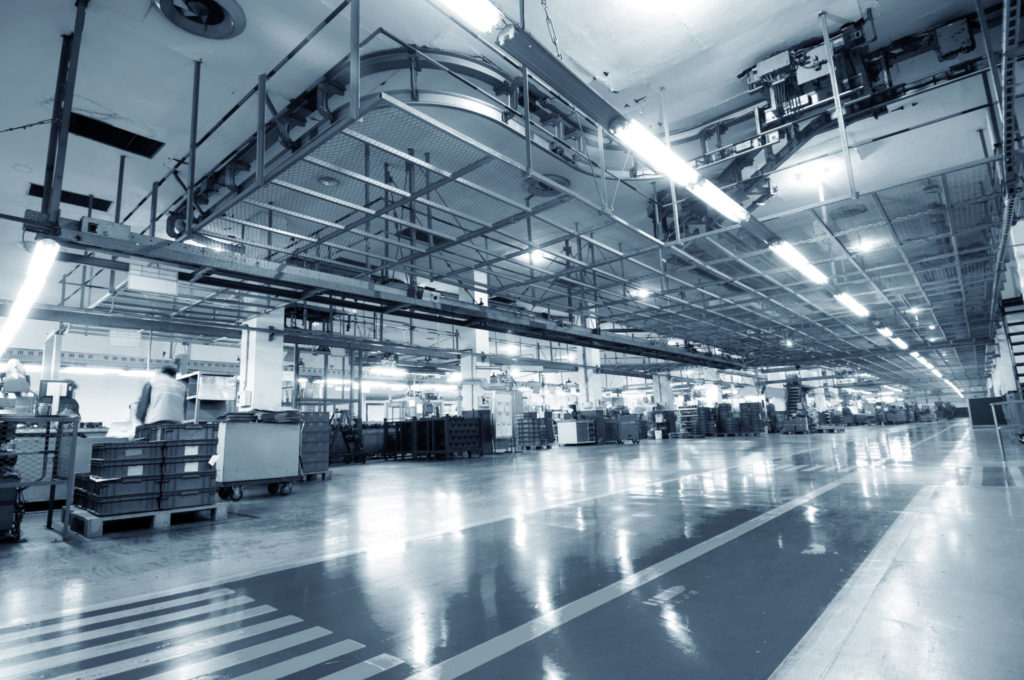
自働化を導入することにより、製造現場での異常を早期に発見することが可能になり、人件費や生産コストの削減、生産効率や品質の向上につながります。
異常の早期発見
自働化の最も大きなメリットの一つに、異常の早期発見があげられます。従来の生産ラインでは、人間の目視や判断に頼って異常を検知していましたが、自働化システムでは、センサーやモニタリング機能が常時稼働し、異常が発生した瞬間にそれを検知します。このようにリアルタイムで異常を検知することで、生産ラインの停止や品質不良の発生を未然に防ぐことができ、製品の品質を保つことが可能となります。
人件費・生産コストの削減
自働化を導入することで、人件費と生産コストの削減が可能になります。自働化システムは、24時間体制で稼働可能であり、人手を介さずに作業を行うため、労働力にかかるコストを大幅に削減することができます。また、作業効率が向上することで、材料やエネルギーの無駄も減り、総合的な生産コストの削減につながります。これらの効果で、原価低減も可能となります。
生産効率の向上
自働化の導入により、生産効率が大幅に向上します。自働化システムは、まず、機械を監視するためだけの人員は不要になり、省人化に繋がります。また、生産ラインから離れられなかった従業員は、他の業務に時間が割けるようになり、例えばより付加価値の大きい業務に集中することも可能です。
また、異常時に機械を止める仕組みにすることで、生産ラインでの問題点の発見がしやすくなります。そのたびに再発防止策を検討し、改善していくことで、生産効率化に繋がります。
品質向上
自働化は、製品の品質向上にも大きく関わっています。自働化システムは、精密なセンサーや自動制御技術を駆使して、製造工程の細部まで監視し、最適な条件で生産を進めることができます。その結果、品質のばらつきが減少し、一貫した高品質な製品を安定的に供給することが可能となります。また、異常が発生した場合も即座に対応できるため、品質不良の発生リスクが最小限に抑えられます。
「自働化」導入のポイント
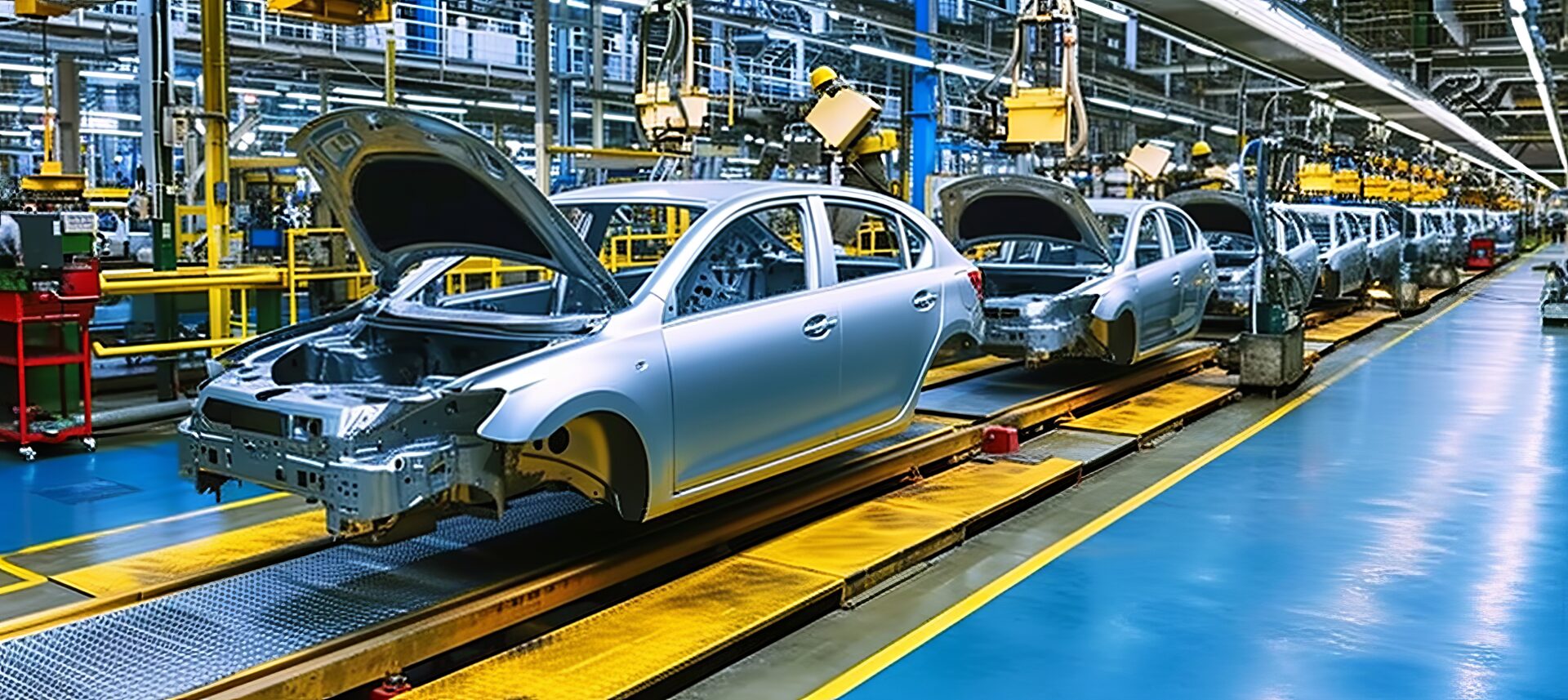
自働化を効果的に導入するには、事前に評価と目標設定、従業員の教育や適切な技術の選定を行うことが必要です。また、試験運用を通じてシステムの安定性を確認し、フィードバックを基に調整を行うことで、効果的な自働化が可能になります。
適切な生産工程の選定
自働化を導入する際には、まず自動化に適した生産工程を選定することが重要です。特に、繰り返し作業が多い工程や、人間の手作業でミスが発生しやすい工程が、自働化の対象となります。作業の複雑さやコスト効果を考慮し、自動化の優先順位を決定します。
システムの選定
自働化を導入する際には、適切なシステムを選定することが重要です。導入予定のシステムや装置が現場の要件を満たすかどうかを慎重に検討し、長期的な運用を見据えてシステムを選定することで、自働化の効果を最大限に引き出すことができます。また、コスト面や将来的な拡張性も考慮することが大切です。
従業員の教育
自働化を効果的に導入するためには、新しいシステムや技術を理解し、自働化によって変化する作業内容や業務フローに対応できるよう、従業員の教育が必要です。新しい自働化システムの操作やトラブルシューティングについての理解を深めることで、スムーズな導入と運用が可能になります。また、従業員が自動化されたプロセスに適応し、システムの効果を最大限に引き出すためのサポートも重要です。
試験運用の実施
自働化のシステムを導入する前に、試験運用を行うことが重要です。試験運用によって、自働化システムが実際の生産環境でどのように機能するかを確認し、問題点や改善点を洗い出すことができます。また、従業員が新しいシステムに慣れるための時間を確保することも可能になります。試験運用を通じて得られたデータを基に、正式導入前に必要な調整や改善を行うことで、スムーズに導入することができます。
フィードバックと調整
自働化を導入した後も、継続的なフィードバックと調整が必要です。従業員からの意見や生産データを基に、システムや工程の改善点を洗い出し、必要に応じて調整を行います。これを繰り返すことで、自働化の効果を最大限に引き出し、現場のニーズに合わせて運用できるようになります。
継続的な改善には生産データの分析が必要
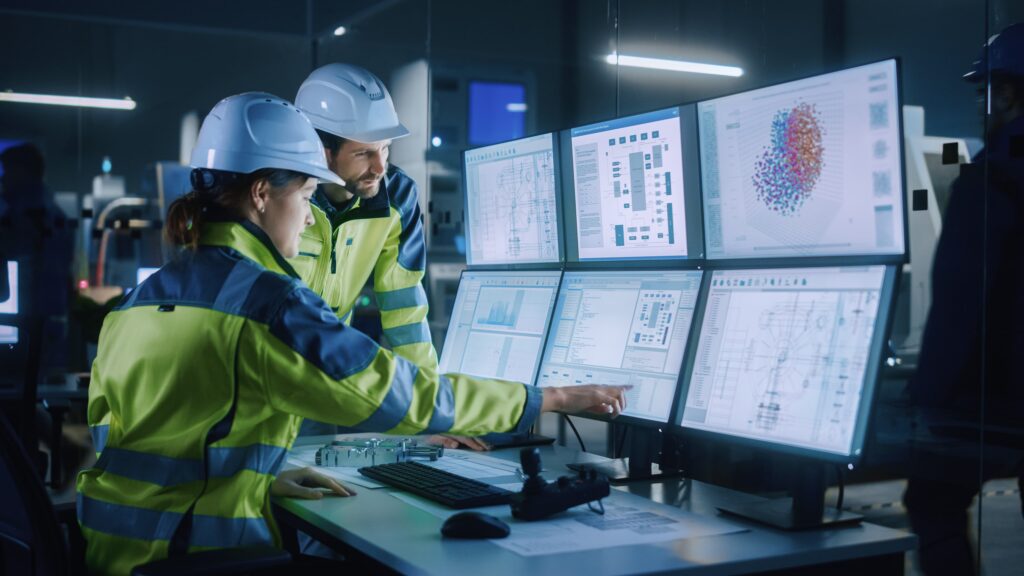
前述の通り、生産ラインに自働化を取り入れた後も、継続的に改善を繰り返していくことが重要です。不良発生率や作業時間などの変化を記録・蓄積し、データに基づく分析をしていくことが重要です。
データ分析には、品質管理システムや、品質管理機能がある生産管理システムなどが役立ちます。生産現場のデータも管理することを踏まえると、品質管理システムだけでなく生産管理システムも含めて検討することをおすすめします。
例えば、生産管理システムの中には、製品ごとの検査データや不良数を記録したり、作業日報を電子化することで作業時間を自動集計したりする機能があります。生産と品質に関わる情報を一元管理することで、分析がしやすくなります。
22種類の生産管理システムをランキングで比較
初期費用相場や選び方のポイントをチェック
生産管理システムをそれぞれの特徴や初期費用相場などで比較したい場合は、「生産管理システムランキング」も是非ご覧ください。生産管理システムは、自社の製品・生産方式・企業規模などに適したものを導入しないと、得られるメリットが限定されてしまいます。事前適合性チェックや生産管理システムを選ぶ前に押さえておきたいポイントも解説していますので、製品選びの参考にしてみてください。