2024年05月24日
【生産管理システム】手入力の手間をなくし年間200時間以上の工数削減!アナログ管理特有のヒューマンエラーも大幅削減
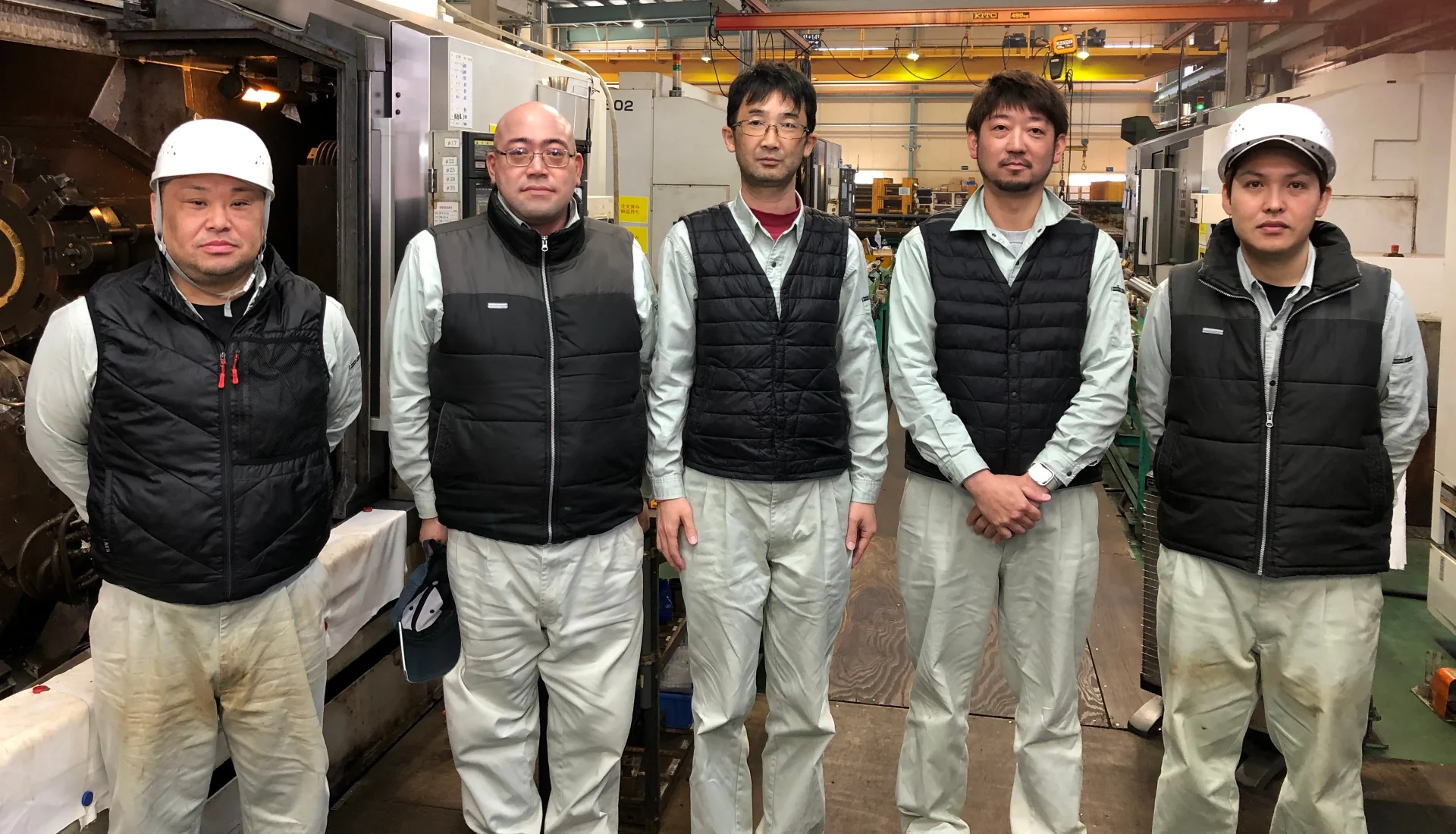
白河バープレシジョン株式会社
業界 | 金属加工業界 |
---|---|
会社規模 | ~30人 |
機能 | 在庫管理、工程管理、生産管理 |
システム概要
課題
- 受注入力は毎日約1時間かけて手入力、ヒューマンエラーをなくせなかった
- 入庫処理のミスになかなか気づけず、入庫後の在庫の動きもリアルタイムに追えなかった
- 発注前に現場へ在庫を見に行き、実在庫を数える必要があった
- 棚卸の在庫集計だけで毎月2時間を割き、目視確認や電卓での集計が中心だった
- 生産進捗や不良データをシステム上で管理できず、紙やエクセルを併用
- 出荷登録に手入力や目視確認の手間がかかり、誤出荷もゼロにできなかった
解決策
- 古い生産管理システムをスマートFに置き換え
- 在庫管理や入出庫登録、工程管理に、ハンディーターミナルを用いたバーコード管理を導入
効果
- 受注登録の手入力をなくし、1日の作業時間は10分に短縮。年間200時間の工数削減を実現
- バーコード管理で在庫見える化やミス防止を実現、顧客対応もスムーズになった
- 最新の在庫数をスマートF上で確認でき、少ない手間で正確な発注が可能に
- 棚卸の在庫カウントがハンディーターミナル片手で完結、電卓集計が不要になり工数半減
- 生産進捗や作業日報をシステム化、不良発生時の確認も迅速化
- ハンディーターミナル導入で手入力作業がなくなり、年間約80時間の工数削減。誤出荷もアラートで防止できるようになった
導入の背景
老朽化した既存システムでは多くの手作業が必要、さらに更新費は数千万円。より自社に合うシステムへの置き換えを検討
白河バープレシジョン様は、建設機械向けを中心とした鋼材の旋盤加工を行い、高い品質を求められる長尺加工を得意としています。長年、生産管理システムを使用しており、老朽化していましたが、更新には数千万円の費用がかかる状況でした。しかし、改めて業務を見返したところ、高額なシステムの中で常日頃使用している機能は限定的だと判明。そこで、既存システムの更新ではなく、新しいシステムへの置き換えを検討することになりました。
また、既存システムのデータ管理は手入力が中心で、現場の工数負荷が高いという課題もありました。手作業で管理する工程が多いため、ヒューマンエラーをなくすのも難しい状況でした。さらに古いシステムのため、生産進捗をリアルタイムに確認できない仕様で、現場での目視確認の作業も多く発生していました。
これらの課題を解決できる生産管理システムを探すため、展示会等で情報収集を行いました。主に検討していたのは、クラウド型の生産管理システムです。スクラッチ開発が必要となる生産管理システムは、従来のシステムと同じくコストがかさむため検討から除外しました。自社にサーバーを設置するオンプレミス型も、社内でサーバー管理する工数が大きいことから検討しませんでした。
スマートFに決めた理由
スモールスタートできるクラウド型で、サポート体制も安心できた
スマートFに決めた一番の理由は、機能を絞ってスモールスタートできる点です。スマートF以外の生産管理クラウドシステムも3〜5社ほど検討しましたが、いずれもパッケージの全機能を一度に導入しなければなりませんでした。自社の会社規模も考慮し、まずは機能を絞って導入したいと考えていたため、機能単位で部分導入でき、料金体系もわかりやすいスマートFに決定しました。
また、ネクスタの柔軟なサポート体制も決め手の一つです。自社の運用にフィットする新しい機能が必要な際、打ち合わせ等で開発の相談ができる点が安心材料になりました。他のシステムベンダーは、機能の相談をした際に「パッケージなので仕様変更はできない」と断られたり、打ち合わせ対応についても難色を示されたりすることが度々ありました。
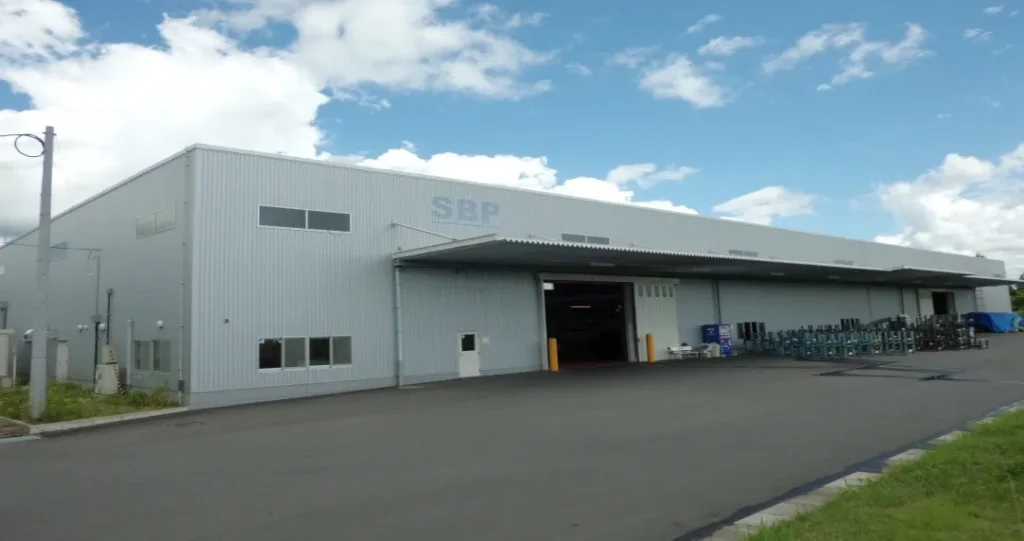
導入効果
手入力していた受注登録をCSV取込で完結、年間200時間の工数削減と入力ミス0を実現
【導入前】受注登録は毎日約1時間かけて手入力、ヒューマンエラーをなくせなかった
FAX注文書が毎日平均20件届き、品番等の情報を目視確認しながら旧システムに手入力していた。さらにシステムの仕様上、受注登録のたびに加工工程も手入力しなければならなかったため、毎日1時間以上は受注情報の入力に費やしていた。
また、担当者が1人で受注登録を行うので、入力ミス等に気づくのが難しいという問題もあった。工程表を印刷してから注文内容の入力ミスに気づき、工程表を作り直さなければならないこともあった。
【導入後】受注登録の手入力をなくし、1日の作業時間は10分に短縮。年間200時間の工数削減を実現
主に注文書を発行する親会社に、注文書をFAXからエクセル形式に変更してもらい、CSV取り込みによってスマートFへ受注登録する流れに変更。紙の注文書からの手入力や、加工工程の都度登録といった手入力作業がすべて不要になった。毎日1時間かかっていた受注登録作業は10分程度で完了するようになり、年間で約200時間の工数削減が実現できた。また、エクセルの注文情報をそのまま取り込めるため、手入力時に発生していたような登録ミスもなくなった。
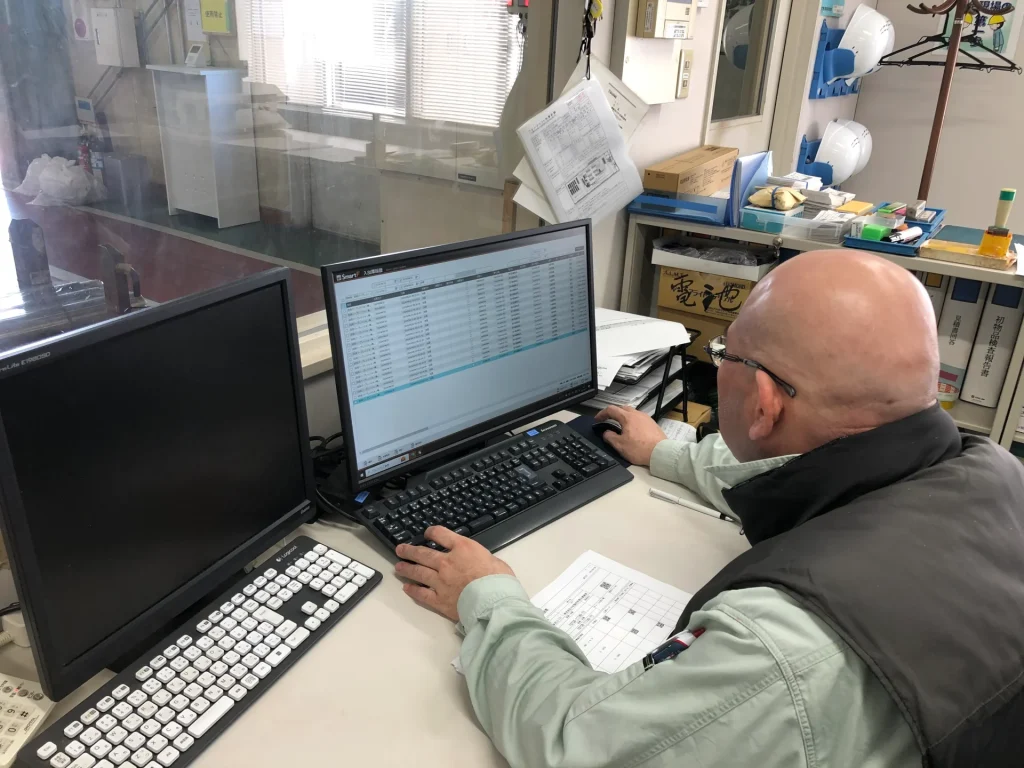
バーコード管理の導入で在庫管理をリアルタイムに見える化、材料取り違え等のミス防止にも成功
【導入前】入庫処理のミスになかなか気づけず、入庫後の在庫の動きもリアルタイムに追えなかった
仕入先からの材料入荷後、納品書を見ながら旧システムに入庫情報を入力していた。3日に1回、10~20束の入荷を受け入れ、そのたびに行う入庫処理に30~40分ほどの時間を割いていた。また、旧システムで入庫は管理できても、生産過程でどれくらいの材料が残っているか等のリアルタイムな在庫情報は把握できなかった。
以前は納品書だけを見ながら入庫処理をしており、材料現物を確認していなかった。そのため、入力ミス等に気づくのは月締の棚卸時になることが多かった。多忙な時期にまとめてミスに気づくことになり、作業者の負荷が大きかった。
入庫後も、類似材料の取り違えが度々起きていた。特に、同じ長さ、かつ硬さや外周だけ異なる鋼材等は、見た目では類似材料だと気付けず、管理が難しかった。
【導入後】バーコード管理で在庫見える化やミス防止を実現、顧客対応もスムーズになった
仕入先からの納品書をもとにスマートFで入庫処理するのにくわえ、バーコードで在庫管理できるラベルを貼付する運用に変更。品番に紐づくバーコードを印字したラベルを、材料に貼付する管理方法に移行した。生産による在庫引当や不良発生による在庫変動がある際は、現場でハンディーターミナルを用いて払い出し(出庫)を行うことで、在庫数をリアルタイムに管理できるようになった。さらに、棚卸し、入庫処理の時間を1回15~20分に半減できた。
在庫数をリアルタイムに確認できるようになったことで、顧客対応もスムーズになった。たとえば、客先の不良で追加注文の電話があった際、今までは一度電話を切ってから現場まで在庫を数えに行き、その材料を使用する生産予定がないかどうか確認してから、電話を折り返していた。現在は、スマートF上で最新の在庫数と生産予定を確認できるため、現場に行ってから電話をかけ直す必要がなく、迅速な顧客対応が可能となった。
また、入荷材料にラベルを貼る際に現物の検品も行えるため、もし入庫情報にミスがあっても現場で気づけるようになった。生産のために材料を持ち出す際も、バーコードで鋼種をすぐに確認できるため、類似品の取り違いも防止できている。
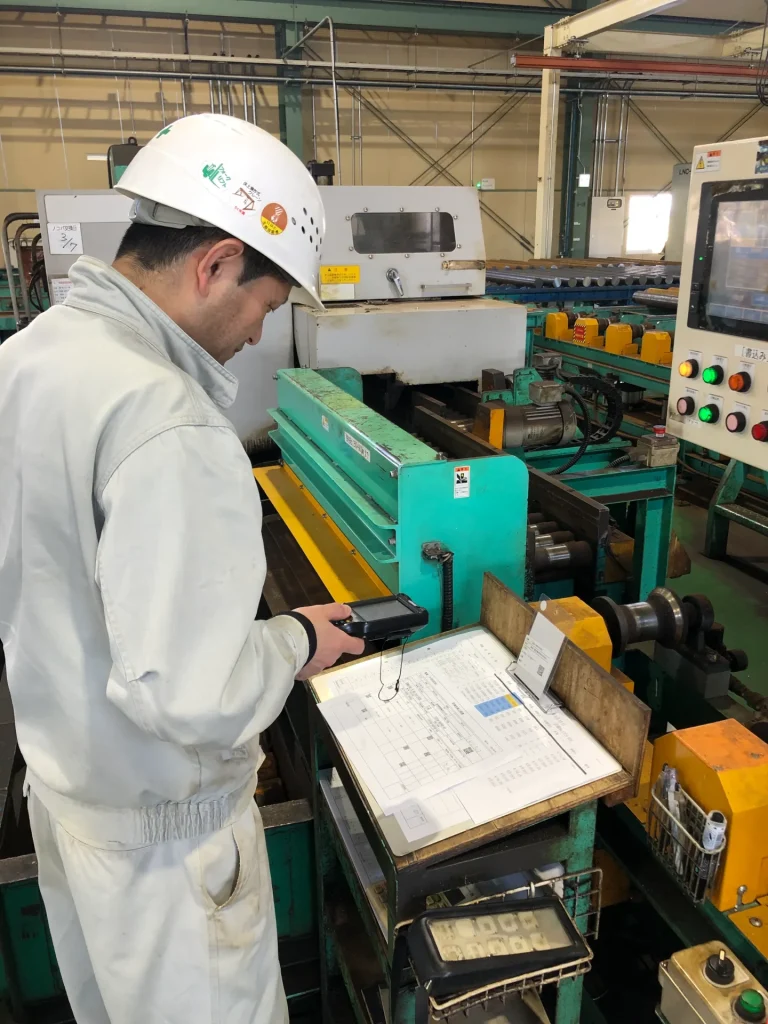
発注のたびに現場へ在庫を数えに行く手間がなくなり、発注精度も向上
【導入前】発注前に現場へ在庫を見に行き、実在庫を数える必要があった
顧客から展開された内示に基づく発注では、所要量計算のために正しい在庫数の把握が必須。しかし、旧システムでは入庫処理後の在庫の動きを追えなかったため、材料発注時は毎回、現場へ在庫数を確認しに行っていた。在庫数を数える際も、類似材料の見間違いで誤った計算をしてしまうことが度々あった。
【導入後】最新の在庫数をスマートF上で確認でき、少ない手間で正確な発注が可能に
材料の動きをハンディーターミナルとバーコードで管理することで、スマートFから最新の在庫数をいつでも確認できるようになった。現場で在庫確認する頻度は格段に減り、発注工数の削減と発注精度の向上を同時に実現できた。
紙と目視確認による棚卸をシステム化、在庫集計の工数が半減
【導入前】棚卸の在庫集計だけで毎月2時間を割き、目視確認や電卓での集計が中心だった
以前の棚卸は、旧システムから棚卸一覧表を大量に印刷し、カウンターを持ちながら目視で数え、手書きで書き込んでいた。仕掛品や完成品も同じ手順で数えたあと、電卓で材料の品番ごとに集計・計算し、旧システムに手入力していた。在庫数量は束数✕重量の材料総重量で計算しているため、1種類の材料に対し、母材・仕掛品・完成品で使われている材料の合計重量を手作業で計算しなければならなかった。
棚卸は月次で実施している。この在庫数カウントや集計だけで毎月2時間はかかっていた。また、材料の保管エリアによっては、材料やタグを確認しにくい狭い場所もあり大変だった。
【導入後】棚卸の在庫カウントがハンディーターミナル片手で完結、電卓集計が不要になり工数半減
材料・完成品ともにバーコード管理に移行。ハンディーターミナルで各コードを読み取り、本数を確認するだけで、集計が完了するようになった。母材・仕掛品・完成品の材料総量を電卓で計算する手間は不要になり、集計2時間かかっていた在庫カウントは1時間程度まで半減できた。
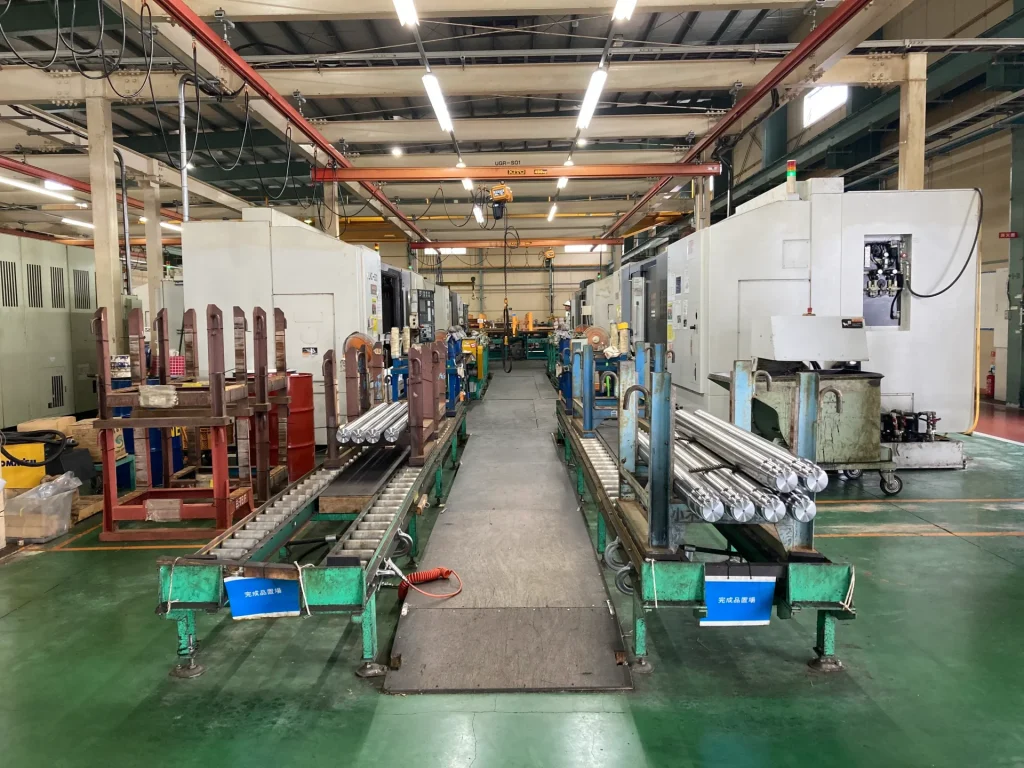
工程管理や不良集計をシステム化、納期回答や不適合発生時に素早い対応が可能に
【導入前】生産進捗や不良データをシステム上で管理できず、紙やエクセルを併用
旧システムでは生産の進捗管理ができなかったため、作業日報や生産履歴を手書きで管理していた。リアルタイムの進捗を管理できていなかったので、顧客からの追加注文があった際は、現場に確認をしに行ってから納期回答をしていた。
また、旧システムでは不良データの集計もできなかった。品質異常が起きた際は、作業日報を1枚ずつ確認しなければならず、データ集計・分析には別途エクセルの管理表を作成していた。
【導入後】生産進捗や作業日報をシステム化、不良発生時の確認も迅速化
スマートFで作業日報や生産進捗等の一元管理を実現。生産進捗をシステム上で確認できるようになったので、追加生産が必要になった場合も対応できるかどうか迅速に判断できるようになった。
使用した材料もすべて工程データに記録することで、不良発生時に材料情報をかんたんにトレースできるようになった。また、スマートF上に不良データが蓄積されていくので、不良集計のエクセル管理表は不要に。スマートFを日々の不良分析に活用している。
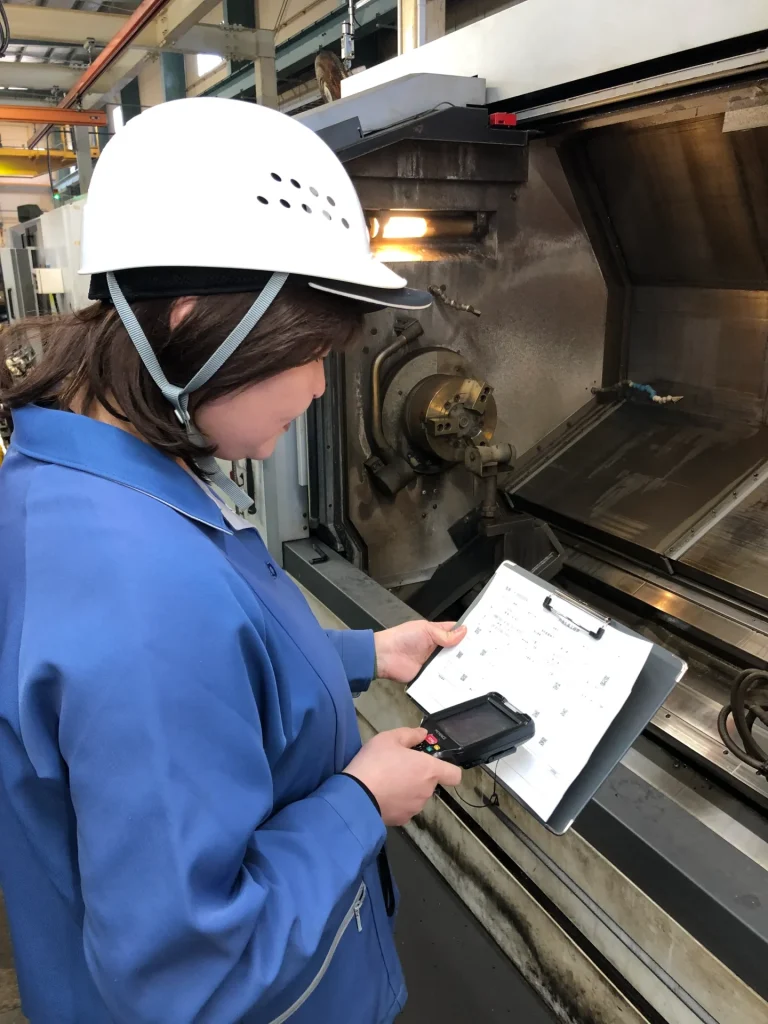
出荷登録も手入力からバーコード入力に置き換え、年間約80時間の工数を削減
【導入前】出荷登録に手入力や目視確認の手間がかかり、誤出荷もゼロにできなかった
以前は、出荷用パレットにある完成品の工程表を1枚ずつ抜き取り、旧システムへ手入力していた。具体的には、生産管理Noを手入力し、品番・長さ・径・本数等を目視確認したうえで出庫登録する作業を行っていた。出荷量が多い場合は1日40パレット分の出荷処理をせねばならず、1日1時間以上を割いていた。
また、手入力や目視確認による出荷作業となるため、誤出荷をゼロにすることも難しかった。特に、類似品番や、同じ品番で入り数違いの注文等で誤出荷が起きやすかった。
【導入後】ハンディーターミナル導入で手入力作業がなくなり、年間約80時間の工数削減。誤出荷もアラートで防止できるようになった
スマートFへの出荷登録作業は、ハンディーターミナルでのバーコード読み取りのみで完結。1日40パレットの出荷をする場合も、20分程度で終えられるようになった。結果的に、出荷の工数を年間80時間程削減できた。
さらに、品番や本数等の情報に誤りがあれば、バーコードスキャン時にエラーが出るので、入力ミスや誤出荷等のヒューマンエラーを防止できている。
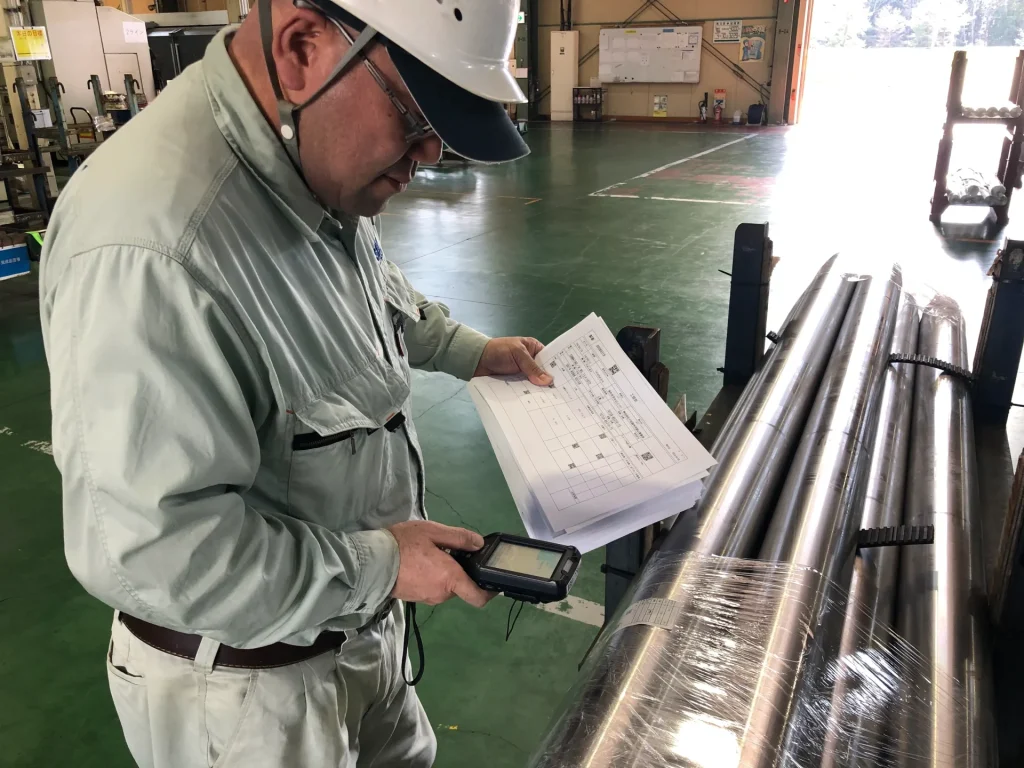
お客様の声
導入ご担当者様
【運用提案する上で心掛けたこと】
既存システムの老朽化更新という観点だけでなく、エクセル管理・転記作業からの脱却とペーパレス化を目指すため、また棚卸作業の簡素化も目的としていました。
一度システムを導入すると、運用開始後のそれぞれのフェーズ段階で、更に追加要望と改善が出てくることは想定していたので、一つのパッケージシステム内に多様なメニューがあり、それらをユーザ―側がタイミングに応じて選択し、将来拡張して利用していくことができるシステムを提案する必要があると感じていました。
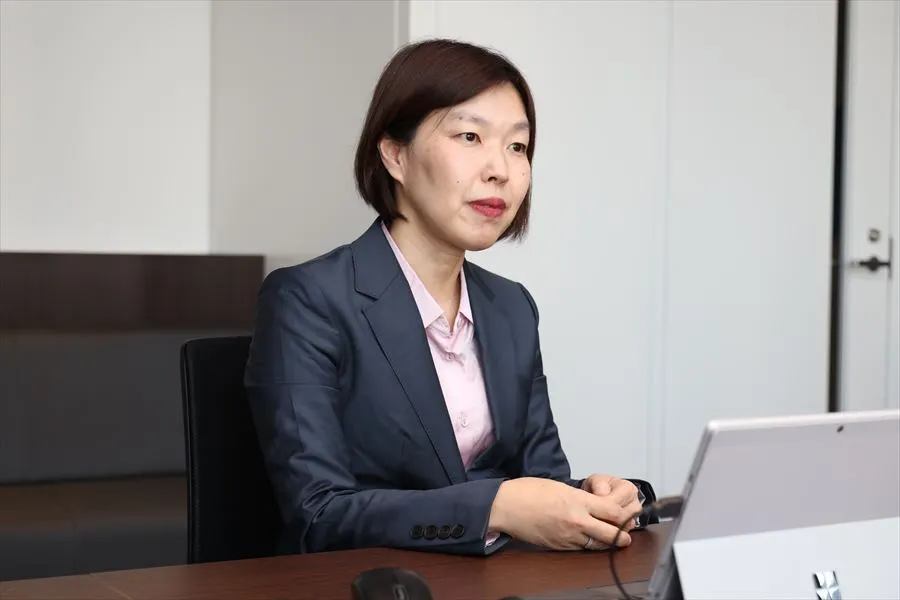
経営企画部 松﨑様
【導入時を振り返って】
本稼働前の並行稼働期間は、既存業務から新システム仕様に向けた工場内の動線最適化に苦労しました。業務や作業に無駄がないようにするためには試行錯誤の連続で、どのようにすれば分かりやすく、ミスが発生せず、スムーズに作業が行えるのか、ハンディーターミナルとSmartFの操作に悪戦苦闘の日々でした。SmartFを導入したことで、現場作業者及び生産管理担当者が快適に業務作業に取り組めており、今後は更なる改善に向けて検討していきたいと思います。
現場ご担当者様
以前使っていた古い生産管理システムは、すべてのデータを手入力する必要があったので大変でした。必然的に現場での管理も紙や目視確認が中心となり、何かと手間がかかっていました。スマートFとハンディーターミナルを導入して、手間のかかるアナログな管理が本当に減りました。結果的に、ヒューマンエラーも工数も減らせたので、現場の負担が軽くなった実感があります。
ハンディーターミナルを使うのが初めての作業者がほとんどだったので、慣れるまでは少し大変でした。ネクスタの担当者の方に設定等の調整も協力してもらい、うまく使えるようになりました。
現在は主に、生産管理担当者がスマートFを使用していますが、今後は現場で誰でもスマートFを確認できる体制にしていこうと考えています。
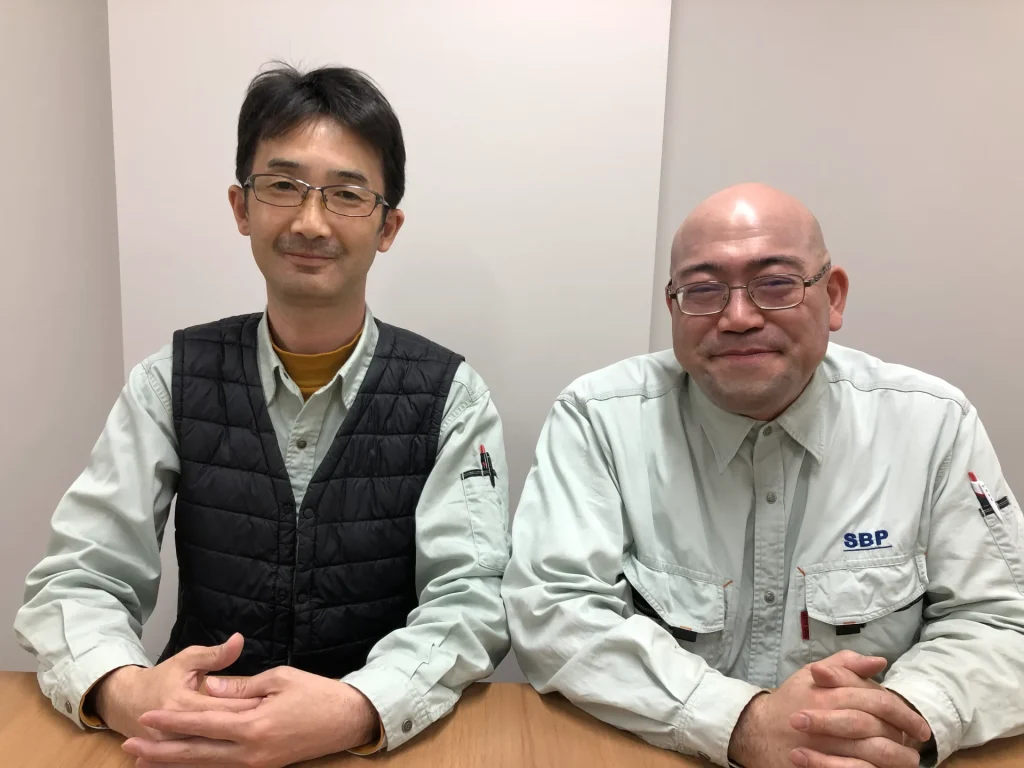
工場長 佐川様・生産管理担当 室様
株式会社ネクスタ:導入支援担当の声
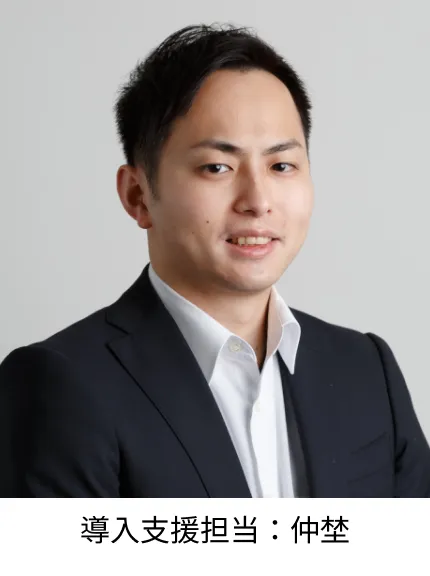
【運用提案する上で心掛けたこと】
お客様の既存の運用やご要望をしっかりと確認させて頂いた上で、従来の業務の流れを変えることなく、かつ、なるべく手順が少ない方法として、ハンディ―ターミナルとバーコードだけで現場で簡単に登録できる操作フローを検討いたしました。
【導入時を振り返って】
業務フローのイメージ図を頂戴しておりましたが、実際に現場を見学させて頂くことで、既存の運用が鮮明に理解できました。最終的な手元での操作はシンプルですが、生産登録時に自動で構成部材を引き落とすなどの設定を行っています。ご担当者の方に各動作の意味までしっかりと理解して頂いたうえで、現場運用に落とし込むことができました。在庫金額/入庫金額/出庫金額の見える化という点についても、運用面の方からも歩み寄って頂き、スマートFのバージョンアップ対応はほぼ無しで着地できました。