整流化とは?トヨタ生産方式との関連から、整流化を実現する具体的な改善方法を解説
公開日:2024年12月14日
最終更新日:2024年12月16日
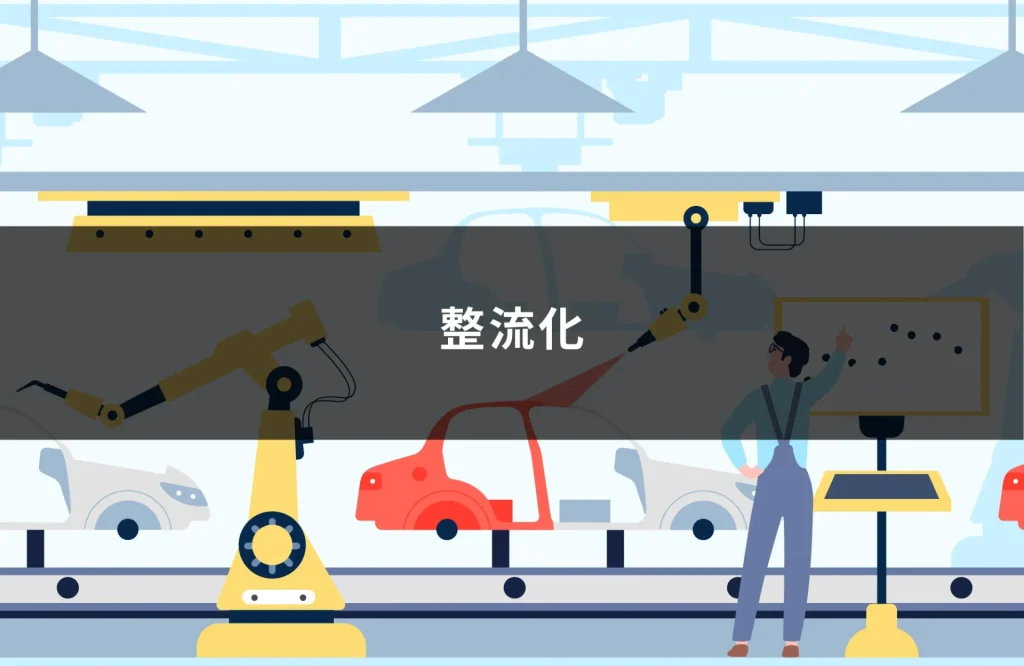
「整流化」とは、製造現場でモノや情報の停滞を排除し、スムーズに工程が流れるようにする手法で、トヨタ生産方式におけるジャストインタイムの原則を支える重要な概念の一つです。整流化によって得られるメリット、整流化を進めるための考え方や改善手法について詳しく解説します。
さらに、整流化の実現に向けた取り組みによる生産の効率化を加速するため、生産管理システムを活用する際のポイントも紹介します。
整流化とは
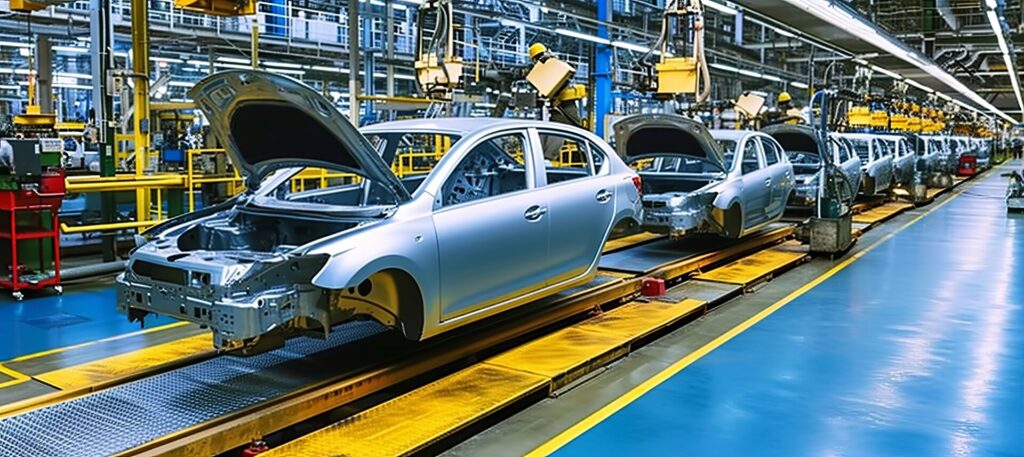
整流化とは、製造工程においてモノ・情報の停滞や無駄をなくし、滞りなくモノ・情報が流れる状態にすることです。
生産現場において、部品・材料・情報が滞ると次の工程が進められず、生産全体に遅れが生じます。整流化は、こうした滞りを防ぎ、全体の流れを最適化します。
ジャストインタイムの3原則のうちの1つ
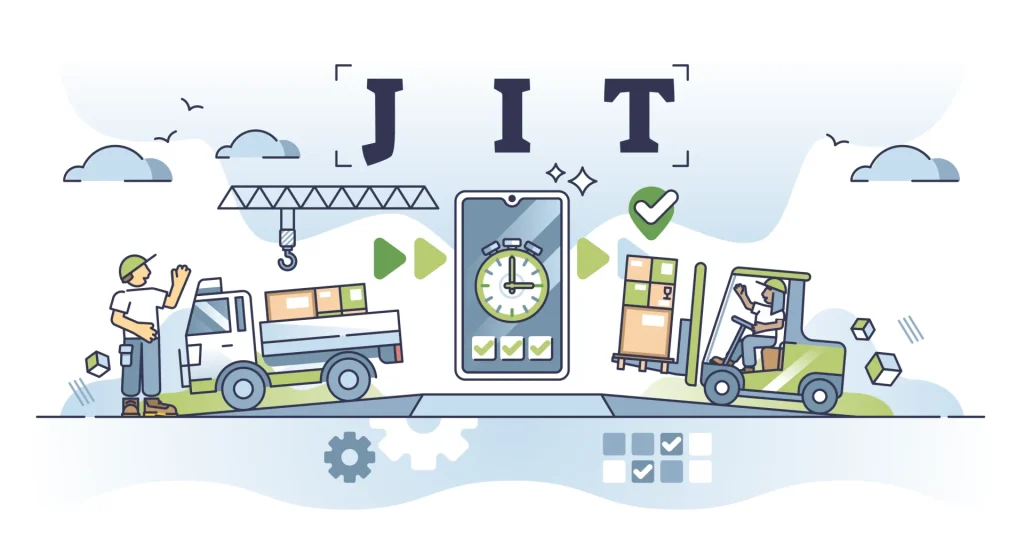
整流化は、以下に示すジャストインタイム(JIT)3原則のうち、「必要なときに」に対応する概念です。
- 必要なものを:必要な部品や材料だけを調達・生産し、無駄な在庫を減らす
- 必要なときに:最適なタイミングで材料・部品を供給し、早すぎる生産を防ぐ
- 必要な量だけ:必要な量だけを作り、過剰生産や余剰在庫をなくす
工程間の流れがスムーズでなければ、必要なタイミングで材料・部品を供給出来なくなります。このため、整流化はトヨタ生産方式(TPS)の根幹をなす取り組みの一つといえます。
整流化のメリット
整流化は、効率的な生産体制が確立され、無駄が削減されるだけでなく、品質やコストの改善も期待できるなど、製造現場全体に大きなメリットをもたらします。
リードタイムの短縮
整流化の最も大きな利点の一つは、製造プロセス内の仕掛在庫の滞留が減り、結果としてリードタイムが大幅に短縮されることです。
リードタイムとは、注文を受けてから製品が完成し、出荷されるまでの総時間を指します。この時間が短ければ短いほど、顧客に早く製品をお届けできます。
在庫の削減
整流化の推進により各工程の仕掛在庫が減少するため、在庫全体の削減が可能になります。
大量生産方式では、各工程でバッファ(余剰在庫)を持つことが一般的です。しかし、工程の流れが不安定だと、製造現場では自工程での欠品リスクを恐れるあまり、必要以上の在庫を抱え込もうとする傾向があります。
整流化が実現すれば、各工程の欠品リスクを減らすことができ、余剰在庫の最小化が可能です。保管スペース費用や在庫管理コストを圧縮し、余剰在庫そのものの費用も削減できます。
5S・3定による職場環境のカイゼンが進む
整流化を通して生産工程の停滞やムダを排除すれば、5S活動(整理・整頓・清掃・清潔・躾)や3定(定位・定品・定量)が強化されます。
まず、整流化により工程の流れが明確になるため、不要なものを取り除き、必要なものだけを整然と配置できるようになります。これにより、整理・整頓が進み、作業者が効率よく必要な道具や部品を使用できます。また、清掃や清潔の維持が容易になり、汚れや異常を早期発見する体制が整います。さらに、3定を含めたルールの遵守意識が高まり、職場全体で躾(しつけ)が向上します。
整流化を推進することで、5S活動が自然に進展し、これらが相互に作用することで作業環境のカイゼンが促進されます。
7つのムダ排除による生産効率の向上
整流化が進んだ工程では、リードタイムの短縮、在庫の圧縮、5Sや3定の推進が実現し、その結果として生産効率が大幅に向上します。さらに、整流化を徹底して追求すれば、製造工程から以下に示す7つのムダが排除されます。
- 加工のムダ
- 在庫のムダ
- 造り過ぎのムダ
- 手待ちのムダ
- 動作のムダ
- 運搬のムダ
- 不良、手直しのムダ
この結果、生産ラインにおける人員配置や設備の稼働率が最適化され、投入された資本や人員などのリソースをより効率的に活用できるようになります。
整流化の実現に役立つ「ECRSの原則」
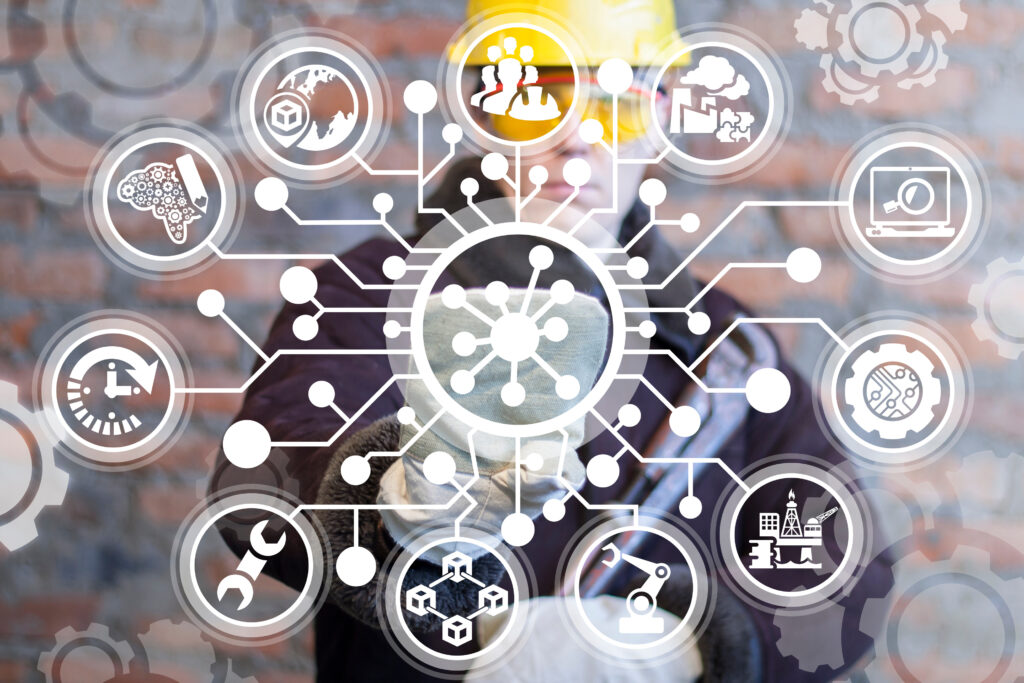
整流化を効果的に進めるための手法の一つとして、「ECRSの原則」があります。ムダを徹底的に排除し、作業の効率を高めるための基本原則であり、生産ラインの改善活動における着眼点のヒントとなります。
人の動き・時間のムダを削減
ECRSの「E」は「Eliminate(排除)」で、具体的には、無駄な人の動きや待ち時間など不要なプロセスを取り除くことです。作業現場では、これまでの経緯や以前あった制約の影響で、無駄な作業が惰性で残っているケースも少なくありません。このようなプロセスを削減することは、整流化の推進に大きく寄与します。
例えば、排除すべき典型的なムダには、次のようなものがあります。
- 部品の受け渡しで、作業者が何度も同じ場所を行ったり来たりする
- 5Sの徹底ができておらず、現場で部品を探すために時間がかかる
- 工場内の仕掛製品の保管における過剰梱包により、次工程の開梱に手間がかかる
工程・作業の統合
ECRSの「C」は「Combine(結合)」のことで、プロセスを段階ごとに整理し、前後の作業や工程を統合することに相当します。
一例として、野菜サラダの加工ラインを例に考えます。原材料である野菜を洗浄した後、装置から取り出して別の機械でカットし、さらに充てん機で所定量を袋詰めする工程が行われています。この工程では、各工程間で原材料の投入や取り出しが必要であり、さらにそれぞれの工程で仕掛品が一時的に保管されるため、モノの流れが乱れた状態になっています。
そこで、洗浄機能を備えた多機能カッターを導入し、充てん機を連結することで、洗浄・カット・袋詰めを一連の流れで実施可能となりました。この工程の統合により作業効率の向上、労務費の削減が実現し、さらに食品材料の大気との接触が減ったことで衛生管理状態も向上しました。
このように工程フローの見直しによる作業・工程の統合は、生産性向上とコスト削減に直結します。
作業工程の流れを最適化
ECRSの「R」は「Rearrange(再配置)」を指し、作業や工程の順序・配置を見直して流れを最適化することを意味しています。
具体的には、工程ごとの物理的な配置を整理することで、部品や製品がスムーズに流れるようなレイアウトを設計できます。これにより、作業者や物品の無駄な移動が大幅に削減され、工程全体の人やモノの流れがスムーズになります。
ボトルネック工程の作業簡素化
ECRSの「S」は「Simplify(単純化)」のことで、作業を簡素化したり分かりやすい形にして、生産ライン全体のスムーズな流れを確保します。
例えば、多くの調整が必要な設備を必要とする工程はボトルネックとなりやすく、仕掛在庫が滞留しやすくなります。調整用治具を導入したり、調整作業が自動化で実施できるよう設備改造することで、調整作業を簡素化してモノの流れの停滞を防ぎます。
整流化実現のための5つの改善方法
整流化を現場で進めるためには、次に示す5つの改善方法が有効です。
標準作業を定める
標準作業とは、人の動きを中心として決められた作業方法を指します。ルール化された作業手順を標準作業として徹底すれば、属人的なムダが排除され、モノなどの流れが乱れにくくなります。
例えば、タクトタイムの短い作業では、材料を次工程に渡すタイミングが作業者ごとに異なるだけで、工程間での滞留や不足が発生します。モノの流れに関する手順まで含めて標準作業として運用すれば、整流化の実現に一歩近づきます。
1個流し生産
1個流し生産は、一度に次工程に流す製品が1個のみである生産方式で、整流化の実現に大きく寄与します。1個流し生産の特徴は次の3点です。
- 必要なものを必要な時に供給
- 工程間での仕掛品在庫を最小化
- スムーズな工程間の連携を実現
高精度が求められる金属加工製品では、1個流し生産の採用が特に効果的です。従来のロット生産方式では、加工、検査、研磨、最終検査を複数個ずつ進めるため、工程間で仕掛品が多く、在庫管理が複雑になる傾向があります。また、各工程間で在庫が滞留し、不良品が複数の工程を通過してしまうリスクもありました。
1個流し生産では、各工程を1個ずつ進め、加工直後に簡易検査を行うことで、不良品が次工程に進むのを防ぎ、仕掛品在庫を最小限に抑えられます。この方式により、工程間のスムーズな流れを確保し、整流化の実現に大きく近づくでしょう。
一方で、工程間のバランス調整やトラブル対応体制の整備など、いくつかの課題も伴いますが、全体的な生産効率の向上と品質向上に寄与する生産方式といえます。
同期化
同期化とは、各工程が同じペースで進むように生産スピードを調整することを指し、整流化の目標である「スムーズな流れ」が強化されます。これにより、工程間の過剰在庫や遅延が発生しにくくなります。各工程がバランスよく進むことで、生産のリズムが整い、無駄な時間やコストが削減されます。
同期化を導入する際は、工程間の作業負荷を均等化し、ライン停止に備えた迅速なトラブル対応体制が不可欠です。また、作業者に同期化の意義を理解させる教育を徹底し、スムーズな運用を確立する必要があります。
工程順設備配置
工程順設備配置とは、製造工程に沿って設備を配置することであり、整流化を実現するために欠かせない要素です。
この配置により、部品や製品がスムーズに次の工程に移動し、作業の流れが途切れなくなります。また、設備の配置が最適化されているため、モノの移動距離が短縮され、動作のムダ、運搬のムダを排除できます。
一方で、設備導入時には、初期設計の精度に加え、のちの製品仕様変更にも柔軟に対応しやすい設備設計が整流化を持続するためのカギとなります。
セル生産方式
セル生産方式では、製造工程を完結可能な小単位の「セル」に分割し、1人または少人数の作業者がセル内で複数の工程を担当します。この方式では、作業スペースの形状が重要で、既存のスペース、生産効率、作業者の動線に応じて、最適な形状が選ばれます。具体的には次のような形状があります。
- U字型:設備をU字型に配置し、作業者が少ない移動で多工程を担当できる
- 直線型:一直線に配置して単純な生産フローを実現、大型製品に適する
- L字型:省スペースで運用可能、短期間のプロジェクトや少人数生産に向く
- 島型:設備を島状に配置、1人の作業者が複数工程を完結させる
- 円形型:円形配置で作業者の動線を短縮、小規模生産や試作を効率的に進められる
- Z字型:Z字に配置してスペースを有効活用、狭い工場でも作業動線を短縮できる
各作業者が複数の工程を担当することで、手待ちのムダ・動作のムダ・運搬のムダを最小化でき、その結果、途切れのない製品の流れを維持して作業を進められます。セル生産方式の導入により、チーム全体が効率よく連携可能となり、整流化を実現することでリードタイム短縮や在庫削減につながります。
ただし、多能工の育成や設備配置の最適化が課題となるため、教育・設置スペースのレイアウトに関する慎重な計画が求められます。
現状把握・打ち手の検証には生産管理システムが役立つ
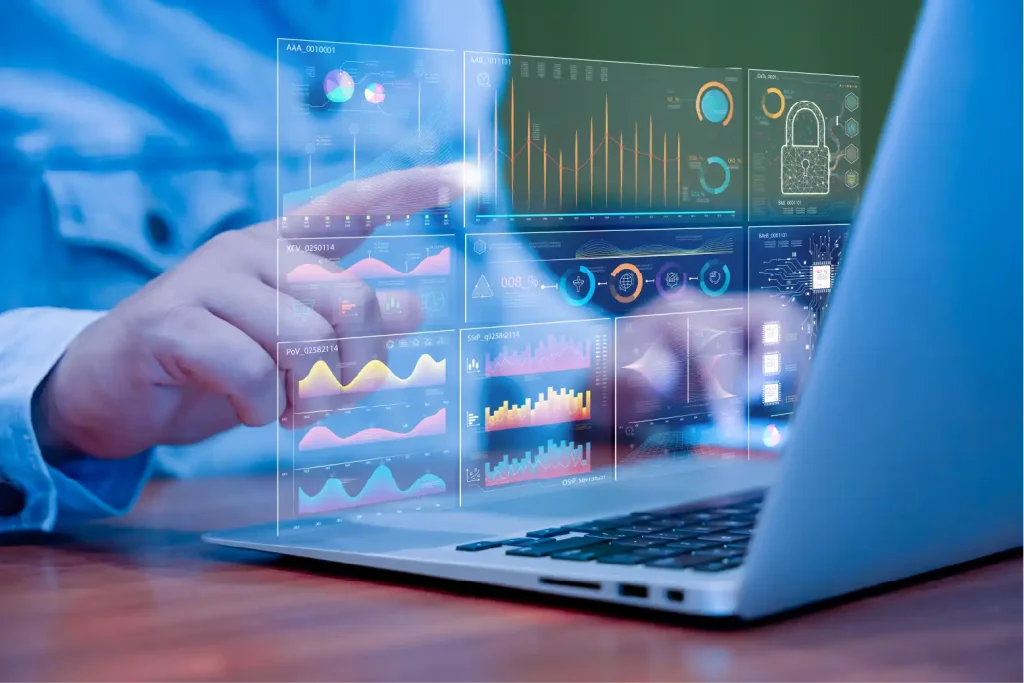
整流化実現に向けた現状や課題を把握したり、打ち手の効果を見える化するためには、生産管理システムの活用が欠かせません。以下は、生産管理システム導入時に注目すべき具体的なポイントの例です。
リアルタイムで在庫や工程のデータを収集できる
生産管理システムは、製造現場で発生するデータをリアルタイムで集計・分析し、現状を客観的に把握するための強力なツールです。リアルタイムでのデータ収集と分析により、現場の状況を的確に見える化することができます。
例えば、各工程の生産量や時間、設備の稼働率などを細かく把握することで、整流化の進捗や改善点をデータに基づいて評価可能です。
問題の早期発見やボトルネックの特定は、整流化実現に向けた第一歩です。より少ない工数で問題を洗い出すためにも、生産管理システムによる現状把握が望ましいでしょう。
参考:生産管理システムを品質の傾向分析に活用している事例はこちら
整流化前後のリードタイム・在庫比較を確認できる
生産管理システムの活用により、整流化に向けた改善施策の取り組み実行前後で、リードタイムや在庫変動の正確な比較が可能です。これにより、改善の取り組みを定量的に評価でき、さらなる改善策を講じることができます。
このように、生産管理システムは、目の前の在庫管理だけでなく、持続的なカイゼンにも有効です。
22種類の生産管理システムをランキングで比較
初期費用相場や選び方のポイントをチェック
生産管理システムをそれぞれの特徴や初期費用相場などで比較したい場合は、「生産管理システムランキング」も是非ご覧ください。生産管理システムは、自社の製品・生産方式・企業規模などに適したものを導入しないと、得られるメリットが限定されてしまいます。事前適合性チェックや生産管理システムを選ぶ前に押さえておきたいポイントも解説していますので、製品選びの参考にしてみてください。