標準作業とは 標準作業の3要素や標準3票、作業標準との違いもわかりやすく解説
公開日:2024年08月09日
最終更新日:2024年09月09日
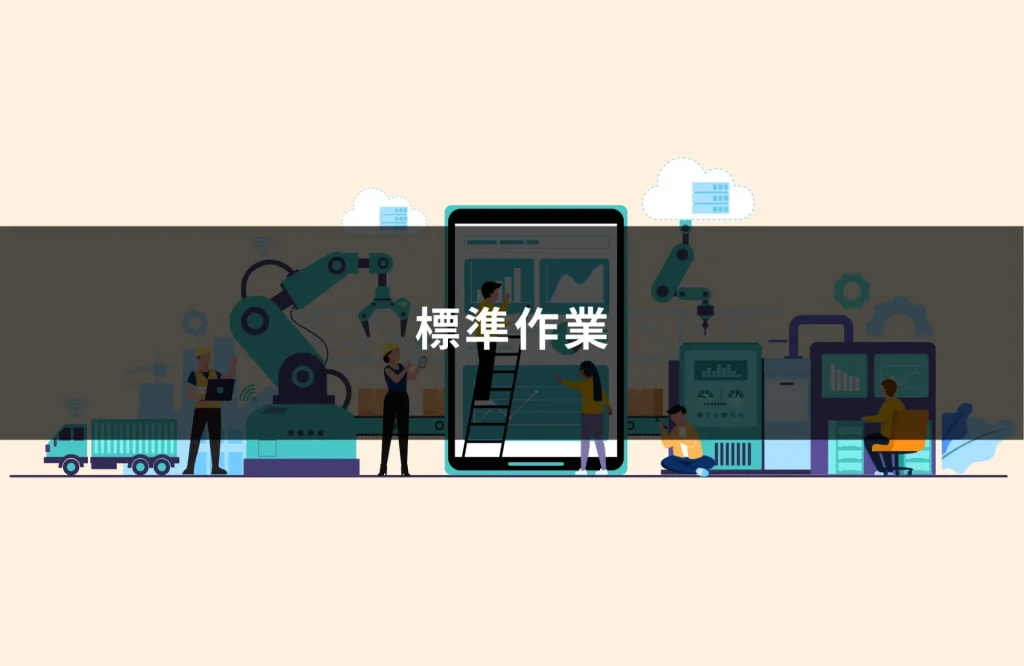
製造業において効率的で安全な作業を実現するためには、標準作業の導入が欠かせません。本記事では、標準作業の基本概念やその目的、具体的なメリットについて詳しく解説します。作業効率や品質の向上、新人教育の効率化、安全性の向上といった利点に加え、標準作業を作るうえで必須の3要素や3票、実際の導入方法についても触れます。
標準作業とは
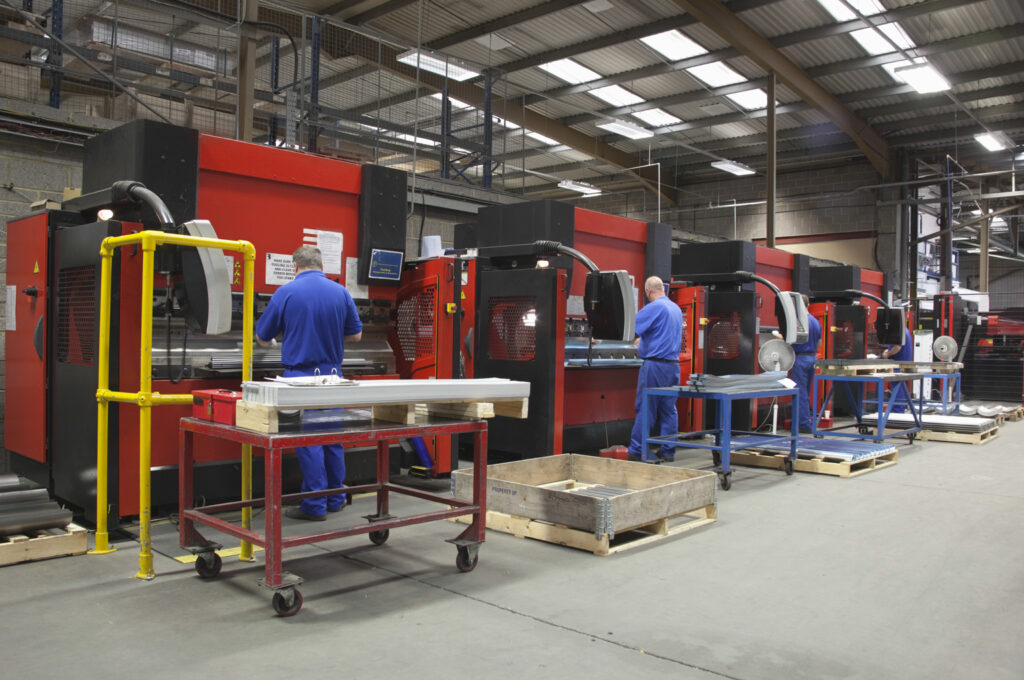
標準作業とは、製造現場で最も効率的な作業の手順や方法です。作業の効率化、品質の向上、安全性の確保に寄与し、製造現場における作業のばらつきを減少させるための重要な手法といえます。
標準作業が導入される主な製造現場は、繰り返し作業が行われる生産ラインです。この繰り返し作業を、最も効率的に行える設備やレイアウトを組み合わせ、標準作業を作り上げます。
標準作業の目的
標準作業の目的は、作業の効率性と品質を維持することにあります。具体的には、作業手順を統一し、全員が同じ方法で作業を行うことで、生産性の向上、品質の安定、新人教育の効率化、安全性の向上を図ります。これによりムダを削減し、トラブルの発生を防止します。
また、標準作業は、作業の改善を行うための基準にもなり、継続的な改善活動を促進する役割も果たします。トヨタ生産方式においても、標準作業を基準として改善していくことが基本とされています。特に、3M(ムリ・ムダ・ムラ)の削減には、基準となる標準作業が必要です。
標準作業のメリット
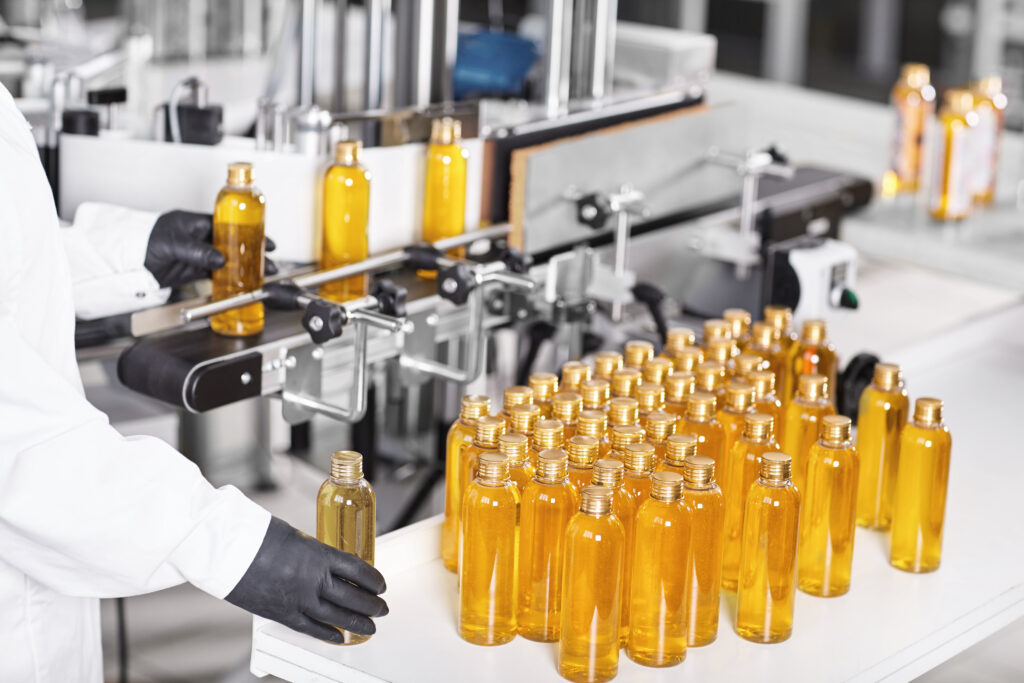
標準作業の導入は、次のようなメリットをもたらします。
作業効率の向上
標準作業を導入することで、作業のばらつきが減少し、一定の品質を保ちながら効率的に作業を進めることが可能になります。各作業員が同じ手順で作業を行うため、無駄な動きや待ち時間が削減され、作業効率が向上します。
また、全体の作業時間が短縮されることで、コスト削減にもつながり、企業の競争力を強化することができます。
品質の向上
標準作業を徹底することで、製品の品質が均一に保たれ、不良品の発生率が低下し、顧客満足度の向上につながります。
また、品質トラブルが減少することで、アフターサービスやクレーム対応にかかるコストや時間も削減することができます。
新人教育期間の短縮
標準作業の導入により、新人教育が効率的に行えるようになります。明確な作業手順があるため、新入社員は短期間で作業内容を理解し、習得することができます。これにより、新人が早期に戦力として活躍できるようになり、人材育成の効率が向上します。教育担当者の負担も軽減され、他の業務に集中することができるようになります。
安全性の向上
標準作業を守ることで、作業員の安全性が向上します。危険な作業手順や不適切な作業方法が排除されるため、労働災害のリスクが減少します。企業としても安全管理が徹底されていることをアピールできるため、社会的信頼を得ることができます。
標準作業の3要素
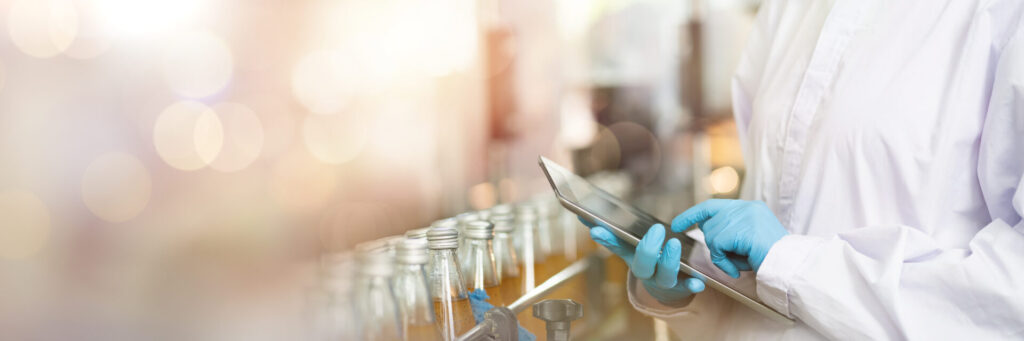
標準作業を作るには、以下3つの要素を決める必要があります。
- タクトタイム
- 作業順序
- 標準手持ち
これらを最適化することで、製造現場での作業効率と品質を向上させるための基本的な枠組みとしての標準作業となります。
タクトタイム
タクトタイムとは、製品が完成するために必要な作業時間のことです。この時間を守ることで、生産ラインがスムーズに動き、無駄な待ち時間を減少させることができます。
また、タクトタイムを基に生産計画を立てることで、従業員の作業負荷を均一に保つことができ、生産性の向上に繋がります。以下がタクトタイムの計算方法です。
タクトタイム=総生産時間÷生産しなければならない製品数
例えば、1時間で10個の製品を生産する必要がある場合、タクトタイムは「60分÷10個=6分/個」となります。
また、理論値のタクトタイムに対し、実際の生産時間は「サイクルタイム」といいます。タクトタイムの計算には余裕率を考慮しないため、付帯作業など含むサイクルタイムが、タクトタイムより長くなることがあります。標準作業をもとにした改善活動の際は、タクトタイムを目標の作業時間とし、実測値のサイクルタイムをタクトタイムに近づける取り組みが必要です。
作業順序
作業順序は、製品を完成させる工程の具体的な手順を示すものです。これを明確にすることで、どの作業をどの順番で行うべきかが一目瞭然となり、混乱やミスを防ぐことができます。例えば、部品の取り付け順序や加工工程などが該当します。
作業順序がしっかりと決められていれば、新人でもすぐに作業を覚えられ、スムーズな生産が可能になります。
標準手持ち
標準手持ちとは、作業順序をもとに繰り返し生産活動をする中で、最低限必要となる仕掛品を指します。製造中の仕掛品を最低限に抑えることで、現場の作業スペースを確保し、作業効率を上げることができます。
ただし、標準手持ちを過度に減らすと、作業待ちが発生し、可動率低下に繋がります。タクトタイム・サイクルタイム・作業順序をふまえ、適切な数量を検討する必要があります。
また、標準手持ちとして決めた数量分の生産を終えたら、作業を止めるルールを作ることも重要です。そこで生産を続けると、造りすぎによるムダが発生し、作業スペースを圧迫してしまいます。作業を止めることで、作業者ごとの作業量や作業効率の差にも早く気づくことができ、早期改善に繋がります。
標準作業で使う「標準3票」
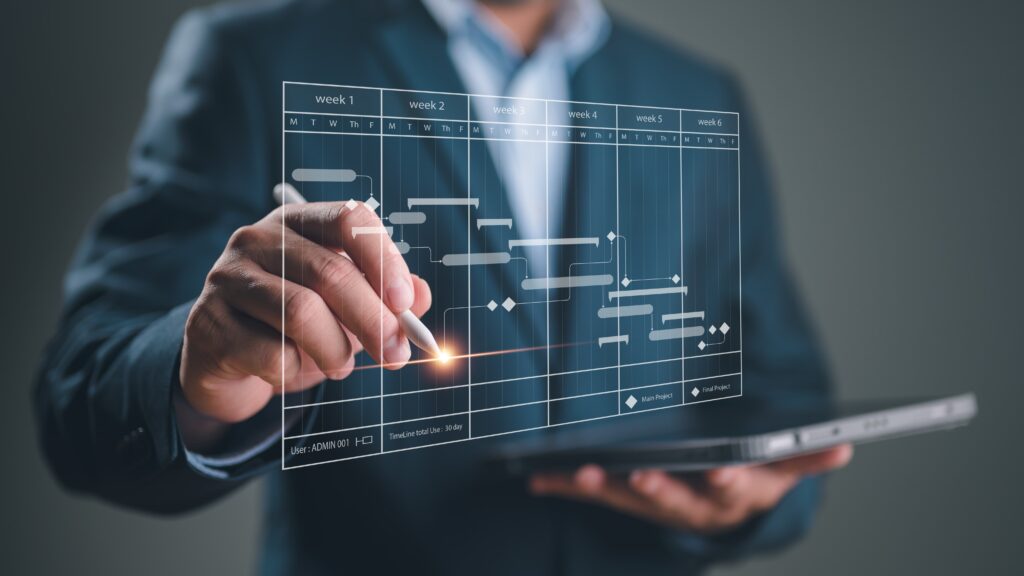
標準作業の実施において、「標準3票」と呼ばれる3つの表があります。
これらの表は、生産効率の向上、作業の効率化、新人教育の短縮に重要な役割を果たします。
工程別能力表
工程別能力表は、各工程ごとの加工能力を明確にするための表です。各工程の順番や使用する機械の情報を記載し、手作業時間・機械加工時間や段取り時間などを記録していくことで、工程別の加工能力を分析し、加工能力の低いボトルネックを発見します。加工能力は、以下の計算で求められます。
加工能力=稼働時間 ÷ (1個あたりの完成時間 + 1個あたりの刃具交換時間)
ボトルネックになっている工程を明らかにすることで、生産計画の策定や改善活動に役立ちます。また、工程間のバランスを取るための調整も容易になります。
標準作業組み合わせ票
標準作業組み合わせ票は、作業者一人ひとりが1サイクルの作業にかかっている時間を見える化し、改善に役立てるための表です。これらのデータをもとに、作業者と設備の最適な組み合わせを標準化していくことから、標準作業組合せ票と呼びます。
標準作業組合せ票では、1人の作業者が製品完成までの各工程にかかった手作業時間・機械加工時間・歩行時間の実測値を記入し、サイクルタイムがタクトタイムに収まっているかを可視化します。これらの計測は、作業を動画撮影して記録していくと正確かつ簡単です。
作業がタクトタイム内に収まっていない場合、標準作業組合せ票に記録された各作業のどこにムダがあるかを分析します。例えば、歩行時間が長いようであれば、機械などのレイアウトを変えて動線を改善する余地があるとわかります。ある機械での作業に時間が掛かっていれば、機械の生産性を見直したり、機械台数を増やしたりすることも検討できます。
このように、標準作業組合せ票は、人か機械どちらにボトルネックがあるかを明らかにすることにも役立ちます。
標準作業票
標準作業票は、作業者の動きや機械の配置をわかりやすく図解した表です。作業別能力表や標準作業組合せ票をもとに、各作業工程の具体的な手順や注意点も記載します。他にも、標準作業の3要素であるタクトタイム・作業順序・標準手待ち、品質チェック、安全注意の印なども明記します。
標準作業表を用いることで、作業者は誰でも同じ手順で作業を進めることができ、品質の一貫性が保たれます。また、標準作業票を定期的に見直すことで、改善活動にも役立ちます。
標準作業と作業標準の違い
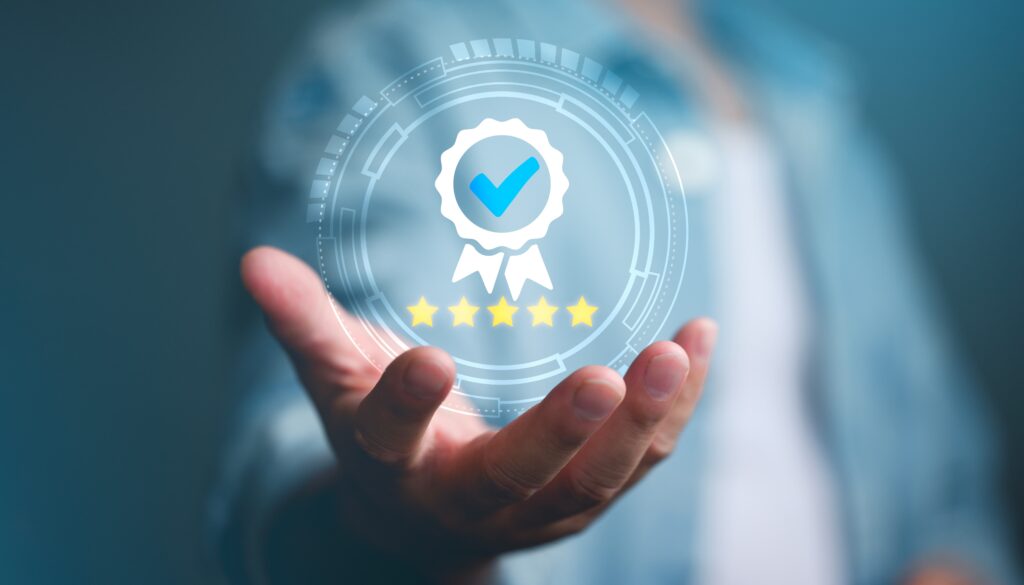
製造業の用語には、「標準作業」の他に「作業標準」という言葉もあります。これらは似た言葉ですが、異なる概念です。
標準作業とは、製品を完成させる工程において、一定の品質と効率を保つために標準化された「作業」を指します。作業標準は、標準作業を行うための基準やルールを示したものです。
例えば、標準作業は「部品Aを取り、ネジBで固定する」といった具体的な「作業」を示し、作業標準は「部品Aの位置やネジBの規格」などの「ルール(標準)」を示します。これらを適切に使い分けることで、製造現場での品質や効率をさらに向上させることができます。
標準作業の作り方
標準作業を作成するためには、まず現行の作業内容を詳細に観察し、分析することが必要です。
次に、各作業ステップの無駄を取り除き、最も効率的で一貫性のある方法を見つけ出します。その後、見つけた最適な作業手順を文書化し、図解や写真を用いてわかりやすくまとめます。
最後に、作業者に対して標準作業のトレーニングを行い、実際の現場での適用を確認しながら、必要に応じて改善を加えていくことが重要です。これにより、標準作業の定着と継続的な改善が図れます。
よくある課題と解決方法
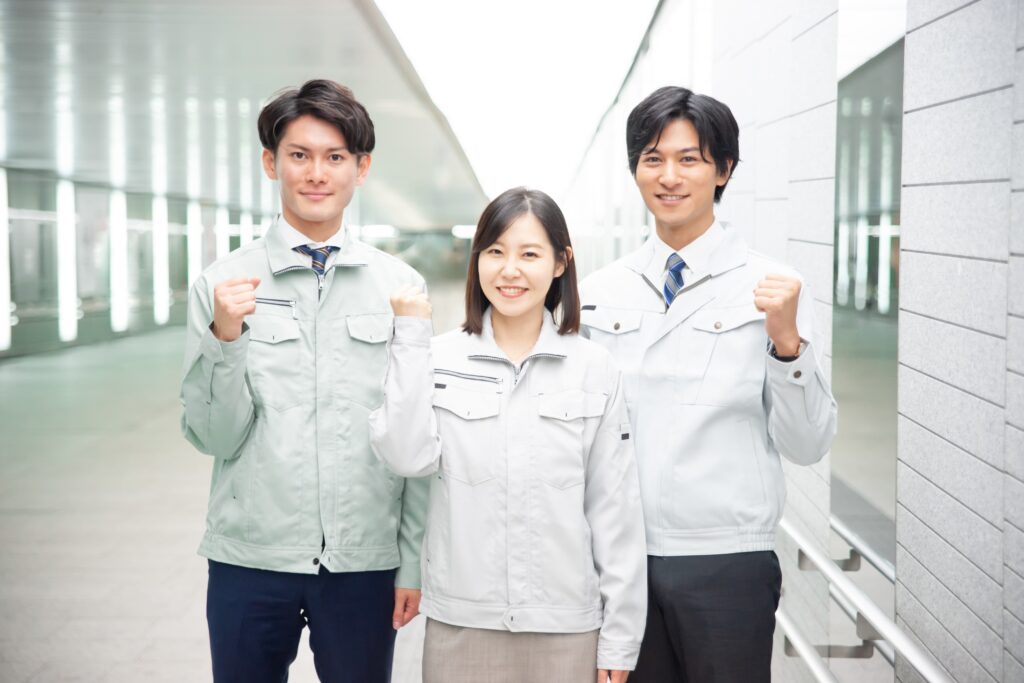
標準作業を導入する際に直面するよくある課題とその解決方法について説明します。
現場での標準化が進まない
標準作業の導入が進まない原因として、現場の理解不足や抵抗感が挙げられます。
これを解決するためには、まず標準作業の重要性とそのメリットを現場の従業員に理解してもらうことが必要です。具体的には、定期的な教育・トレーニングの機会を設け、成功事例を共有することで、現場の意識を高めることが効果的です。
また、トップダウンではなく、現場の意見を取り入れたボトムアップのアプローチを取ることで、従業員の協力を得やすくなります。標準作業を導入する際には、現場のリーダーを巻き込み、率先して実践してもらうことも重要です。
一度作った標準作業を変えずに使い続ける
一度作った標準作業を変えずに使い続けていると、変化する現場環境に対応できず、効率低下や品質問題を引き起こす原因となります。
これを防ぐためには、定期的な見直しと改善が必要です。具体的には、標準作業を定期的にレビューする仕組みを作り、現場からのフィードバックを収集し、必要に応じて改善を行うことが重要です。
また、改善活動を奨励し、従業員が提案した改善案を評価・採用することで、継続的な改善が進みます。変化に柔軟に対応できる標準作業の体制を築くことが求められます。
従業員が標準作業を守らない
従業員が標準作業を守らない原因として、標準作業が現場の実情に合っていない場合や、作業手順の理解不足、意識の低さが挙げられます。
これを解決するためには、標準作業を従業員が理解しやすい形で提供することが重要です。具体的には、作業手順を簡潔にまとめたマニュアルやビジュアルガイドを作成し、定期的なトレーニングを行います。
また、従業員の意見を取り入れた標準作業の改善を行うことで、現場に適した作業手順を確立します。さらに、標準作業を守ることの重要性を強調し、守らない場合のリスクについても明確に伝えることが必要です。
作業環境の変化に対する柔軟性も重要
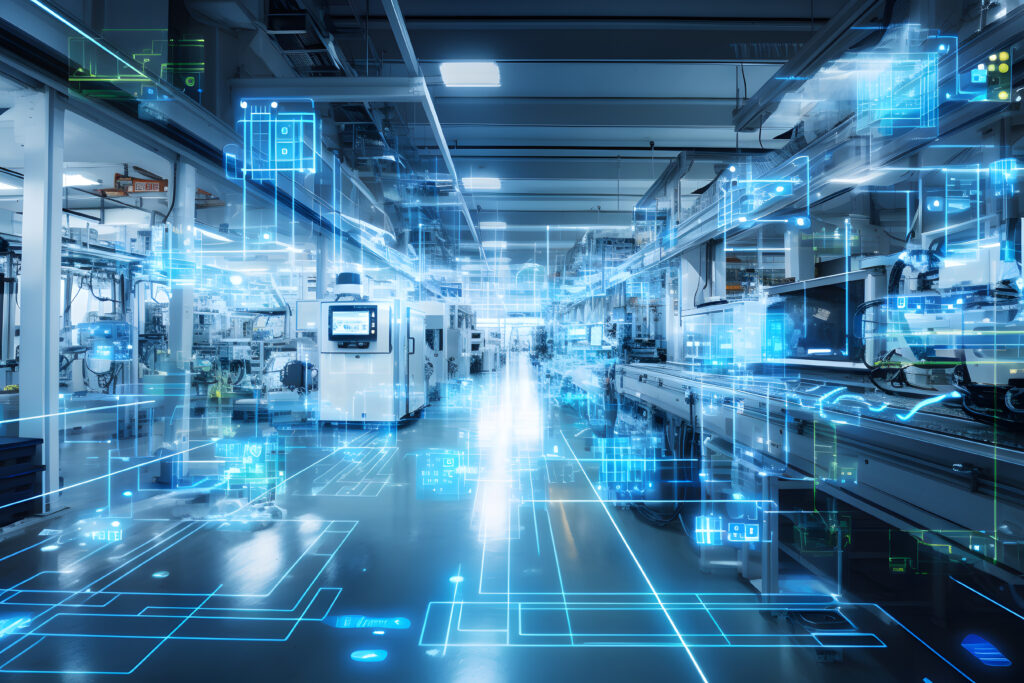
製造現場では、顧客の要求や技術の進化など、常に変化が求められます。こうした変化に迅速に対応できる柔軟な標準作業の設計が重要です。
標準作業は、効率と品質を保つための基盤ですが、状況に応じて適切に見直し、修正する必要があります。例えば、新しい機械の導入や工程の改善があった場合、標準作業もそれに合わせて更新することで、無駄を減らし、より高いパフォーマンスを実現できます。柔軟な対応ができる標準作業こそが、持続的な成長を支える鍵となります。
22種類の生産管理システムをランキングで比較
初期費用相場や選び方のポイントをチェック
生産管理システムをそれぞれの特徴や初期費用相場などで比較したい場合は、「生産管理システムランキング」も是非ご覧ください。生産管理システムは、自社の製品・生産方式・企業規模などに適したものを導入しないと、得られるメリットが限定されてしまいます。事前適合性チェックや生産管理システムを選ぶ前に押さえておきたいポイントも解説していますので、製品選びの参考にしてみてください。