入出庫管理とは?紙・エクセルの課題やシステム・IoT・AI技術の活用方法を事例付きで解説
公開日:2023年11月17日
最終更新日:2025年02月03日
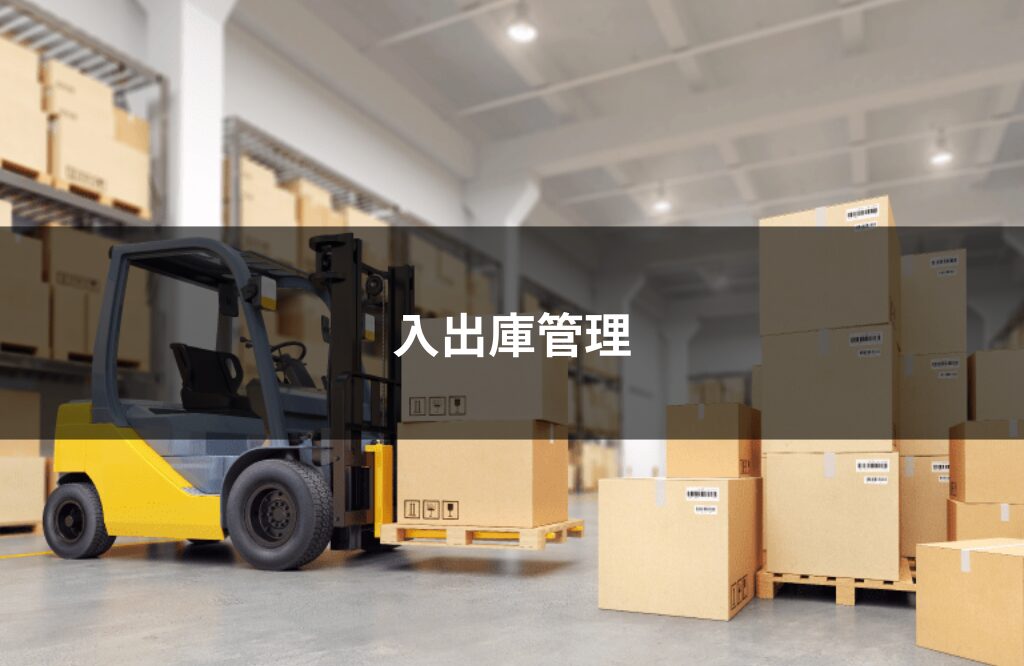
生産管理の重要な業務の一つに「入出庫管理」があります。入出庫管理を行うことで、現状の在庫状況を正しく把握し、過剰在庫や欠品の発生を防止できます。
しかし、入出庫管理を適切に行えている企業は意外と少なく、どこかで理論在庫と実在庫に差異が生じ、棚卸しで帳尻を合わせている企業が多いのが現実です。
本記事では、入出庫管理とは何か、その重要性や課題、紙・エクセル・システムを用いた具体的なやり方を解説します。後半には、在庫管理システムやIoT、AIなどの最新技術を用いた事例についても紹介します。
入出庫管理とは
入出庫管理とは、製品の入庫(倉庫に保管する)と出庫(倉庫から出す)を管理する業務を指します。製造業においては、生産管理部門が在庫状況の正確な把握を目的として、在庫の数量や状態、動きを管理する業務です。
入荷・出荷との違い
入庫・出庫と似た言葉に、入荷・出荷があります。企業によって同義として用いる場合もありますが、別の意味で管理する場合は、以下のように使い分けます。
入荷:仕入先から品物が入ってくること(入荷品に不具合がないか確認する場合は「入荷検品」とも)
入庫:入荷検品を倉庫へ保管すること
出荷:製品を得意先に発送する準備が整った状態(例:出荷品置き場に送り状ラベルを貼って保管した)
出庫:製品を特定の倉庫から取り出すこと(※在庫倉庫でピッキングした材料を製造現場に持っていく等も含む)
在庫管理システムなどでも、入荷と入庫は別機能として扱う場合があります。
参考:入荷検品のよくある課題と改善策:バーコード管理と在庫管理システムでミスをなくす方法
在庫管理との違い
入出庫管理は在庫管理業務の一つで、目的や範囲に違いがあります。入出庫管理と在庫管理の違いを表にまとめると以下のようになります。
項目 | 入出庫管理 | 在庫管理 |
目的 | 製品の入庫と出庫のプロセスを正確に管理し、効率化を図る | 在庫全体の最適化、過剰在庫や欠品を防ぎ、コスト削減を実現する |
管理対象 | 入庫・出庫時の具体的な製品の動きや流れ | 保管されている在庫全体の数量、価値、保管状況 |
範囲 | 倉庫や物流現場での入庫・出庫作業の管理に限定 | 入庫・出庫を含む在庫全体の管理 |
作業内容 | 入庫・出庫時の製品の受け入れ・出荷、検品、記録 | 在庫状況の確認、適正在庫の計算、発注や廃棄の判断 |
在庫管理は、入出庫を含む在庫全体の状況を最適に維持することを目的とした、広範な業務です。製品の数量や保管場所、価値、使用期限などを総合的に管理し、過剰在庫や欠品を防ぐことが目的です。
→ 在庫管理の効率化を実現する方法:製造業が直面する課題とその解決策
製造業での入出庫管理の重要性
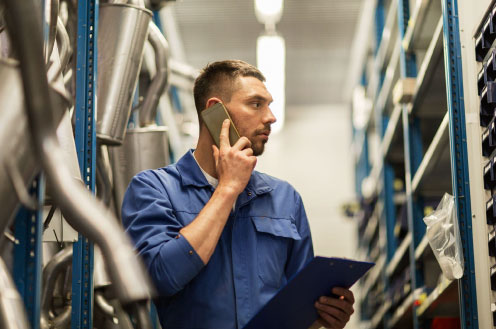
入出庫管理は、製品の品質保持、納期の正確性、コスト削減に直結します。製造業において入出庫管理が適切に行われていない場合、以下のような問題が発生します。
- 必要な原材料や部品が供給されず、生産計画が滞る
- 生産ラインの停止や納期遅延が発生し、顧客満足度の低下を招く
- 必要以上の原材料や製品を保管することになり、保管コストが増大する
- 欠品を補うための緊急発注や輸送コストが増大する
- トレーサビリティが確保されず、不良品や欠陥品が発生した場合に原因特定やリコール対応ができない
- 必要な製品を探す時間や手間が増え、作業効率が低下する
入出庫管理を適切に実施できなければ、生産コストが増大し、納期遅延などによる顧客への信頼性の低下にもつながります。そのため、製品や在庫は複数の項目で入出庫の記録を漏れなく管理し、問題が発生した際は、原因を特定できる体制を構築することが重要です。
入出庫管理に必要な項目
入出庫管理では、製品ごとに以下のような項目の記録が必要です。業種や扱う品目、どこまでのトレーサビリティが必要かによって、管理する情報の範囲は変わります。
入出庫管理の項目
- 製品情報:品番、品目分類
- 数量:入出庫数量、在庫数量
- 日時:入出庫日時
- 取引先情報:供給元、納品先
- 取扱担当者情報:担当者IDなど
- 保管場所情報:倉庫名や保管エリア
- 入出庫理由:仕入れ、新規入荷、返品など
- 状態情報:新品、再加工品、返品品など
- 単価や金額情報:製品の単価
- トレーサビリティ情報:ロット番号、シリアル番号など
これらの項目を正確に記録することで、在庫状況の正確な把握ができます。厳密なトレーサビリティを求められる場合は記録する項目が多くなるため、IoT機器を用いたシステム化や自動化が効果的です。例えばQRコードで入出庫管理を行うことで、記録漏れやミスを防止できます。
入出庫管理を行うメリット
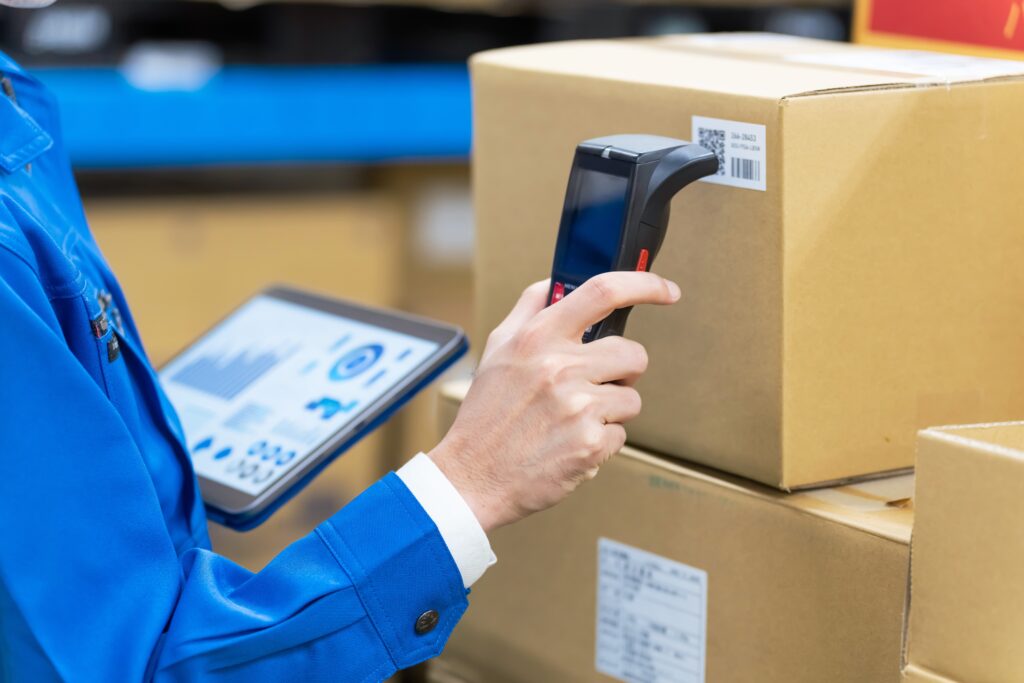
入出庫管理を適切に行うと、次のようなメリットが得られます。
保管コストを削減できる
入出庫管理が正確に行えていると、過剰在庫の防止によるコスト削減効果が期待できます。
入出庫管理が不十分だと、必要以上の発注による過剰在庫が起きやすくなります。その結果、在庫保管コストの増大や、使用期限の超過による廃棄ロス多発など、コスト増加の原因となります。
不要な在庫を持たないことでコストを削減すると、資金を必要な設備などに投資できるため、企業全体の資金効率改善にもつながります。
欠品リスクを回避できる
入出庫管理を徹底することで、欠品のリスクを最小限に抑えることができます。これにより、納期遅延や販売機会の損失を防止できます。
入出庫管理が不十分だと、正確な最新の在庫数の把握が難しくなります。こういった現場では経験則による在庫管理に陥りやすく、要発注品を見逃し欠品が起きる可能性が高まります。適正な入出庫管理ができれば、このような在庫不足を回避し、生産ライン停止などのトラブルを防ぐことに繋がります。
トレーサビリティを強化できる
入出庫管理にてロット番号やシリアル番号を記録することで、製品の流通履歴を正確に追跡できるようになり、トレーサビリティを強化できます。
トレーサビリティを強化することで、リコール時の迅速な対応や、不良品発生時の原因特定が可能になります。また、食品や医薬品など品質管理が重要な業界では、適切な入出庫記録が法規制やISOの認定などにも関連するため、特に注意が必要です。
→ トレーサビリティシステムとは:導入事例やメリットなどを詳しく解説
入出庫管理の方法
入出庫管理の方法には、大きく分けて2通りのやり方があります。
手書きやエクセルでの管理
手書きやエクセルを用いた入出庫管理は、特に中小規模の事業やシステム導入前の企業で行われています。
手書きの入出庫管理では、入出庫時に棚札(棚カード)やノート、帳簿に記録を残す形で行います。エクセルを使用する場合は、入出庫管理表のテンプレートを作成し、データを手入力して管理します。
紙やエクセルによる入出庫管理の最大のメリットは、導入コストが低く、簡単に始められる点です。
システムでの管理
在庫管理システムや生産管理システムと、バーコードスキャナーやRFIDタグなどの端末を組み合わせることでリアルタイムなデータ更新が可能です。
入出庫管理をシステム化すると、手書きや手入力のような属人的な作業もなくせるため、人為的ミスや管理工数を大幅に削減できます。
手書き・エクセルの入出庫管理の課題
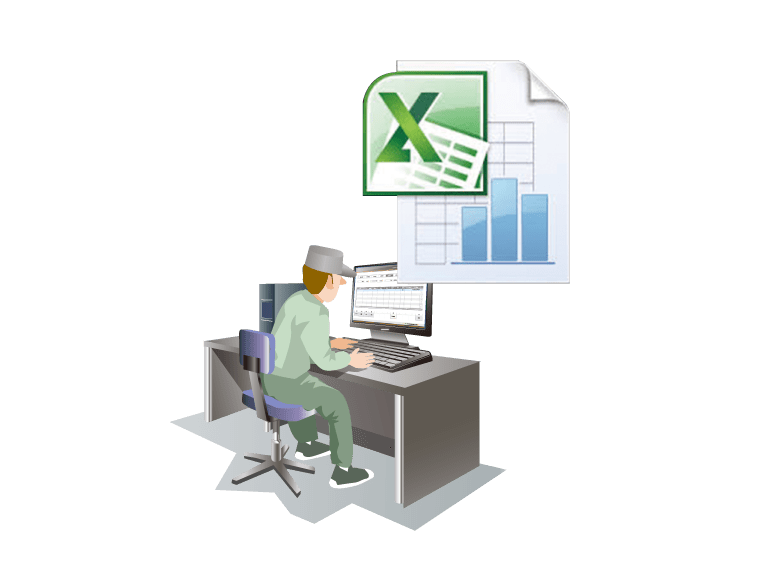
近年はクラウド型システムなどの選択肢も増え、多くの現場で入出庫管理がシステム化しつつあります。しかし、小規模な現場を中心に、手書きやエクセルでのアナログな管理を続けている企業もまだまだ多いのが現状です。
手書きやエクセルによる入出庫管理業務の主な課題は、以下3点です。
ヒューマンエラーが発生しやすい
手作業での入力や検品、記録作業に依存している場合、数量の誤記や製品情報の入力ミスが発生しやすくなります。
また、手書きの棚札からエクセルの在庫管理表へ、手入力で転記している事例も多々あります。この場合、手書きする時点での誤記ミスのリスクに加え、エクセルへの転記ミスが起きるリスクもあります。手書きかつ走り書きの文字が読みづらく、誤った在庫数を入力してしまったという声もよく耳にします。
このようなヒューマンエラーで在庫数の把握が難しくなると、欠品や過剰在庫などの問題を引き起こします。その結果、納期遅延や顧客満足度の低下など、企業の信用に悪影響を及ぼします。
在庫データと実態との不一致が発生する
上記のようなヒューマンエラーが重なると、記録上の在庫データと実際の在庫量が異なる状況が生じます。在庫データと実在庫数の不一致が発生すると、適切な在庫補充の判断ができなくなり、欠品や過剰在庫のリスクが高まります。
さらに、在庫差異を確認・調整する棚卸しの業務負荷も増加し、総じて現場の疲弊に繋がります。
また、在庫データの不一致はトレーサビリティも妨げ、不良品の追跡やリコール対応を困難にします。
業務負荷が高くなる
手書きやエクセルによるアナログ管理は、記録やデータ更新が手作業で行われるため、多くの時間と労力がかかります。また、複数の担当者が管理に関与する場合、データの整合性が取れず、重複作業が発生しやすくなります。
また、「紙やエクセルの在庫数が信用できないから」と、毎日現場で実在庫数を確認するという事例もよくあります。このような工数も重なると、さらに入出庫管理の手間が増えてしまいます。
これらの課題を解消するために、在庫管理システムなどに加えて、さまざまなIoTやAI技術が活用されています。
入出庫管理のIoT活用事例
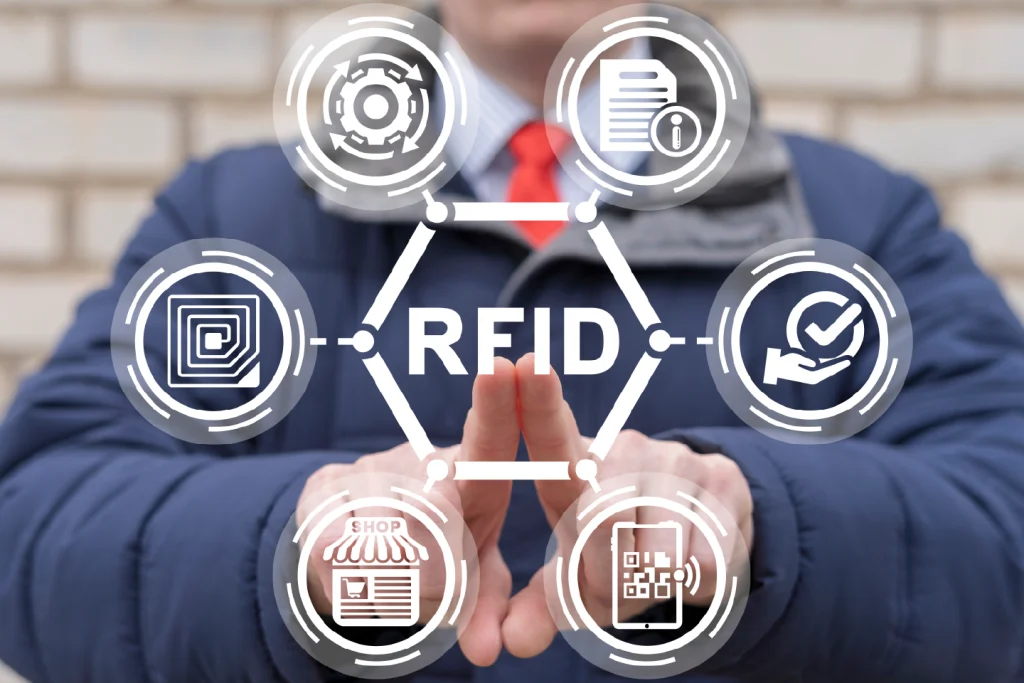
入出庫管理業務には、在庫管理システムを活用したさまざまなIoT事例があります。ここでは入出庫管理のIoT活用事例を紹介します。
QR・バーコード管理やRFIDを活用した自動化
QRコードやバーコード、RFIDによる管理は、入出庫作業の自動化を実現する代表的な手法です。以下の流れで、入出庫情報をシステムへ登録します。
- 製品のパッケージやパレットにRFIDタグやバーコードを付ける
- スキャナーやリーダーで情報を読み取る
- 入出庫の記録をリアルタイムでシステムに反映する
QR・バーコードやRFIDを導入すると、手書きや手入力の手間がなくなり、入力ミスや記録漏れを防止できます。なかでもQR・バーコード管理は、比較的安価に導入可能です。RFIDは、一括読み取りが可能となるため、大量の製品を取り扱う倉庫や物流センターでの検品時間を大幅に短縮できます。
また、在庫状況をリアルタイムで把握できるため、自動発注機能などと組み合わせることで、在庫補充や欠品防止を自動化できます。
→ 【事例】バーコード管理による在庫見える化で、人的ミスを削減!脱・属人化により担当者の作業負担も軽減
IoTセンサーとカメラによる自動検品
IoTセンサーやカメラを活用した自動検品システムは、入庫時や出庫時の品質管理や数量確認を効率化します。例えば、製品のバーコードやQRコードをカメラでスキャンし、同時に重量やサイズをIoTセンサーで測定することで、検品を迅速かつ正確に行うことが可能です。このようなセンサー・カメラの活用も、ヒューマンエラーや工数の削減に効果的です。
また、画像認識技術を組み合わせることで、不良品やラベルミスの自動検出も可能です。食品や医薬品のように、品質管理が厳しい業界では、温度や湿度をモニタリングするセンサーを活用し、適切な保管条件を確認することも行われています。
AGV(無人搬送車)による自動出庫システム
AGV(無人搬送車)は、IoT技術を活用した自動化システムの一環として、倉庫内の出庫作業を効率化する手段として注目されています。AGVは倉庫内のレイアウトに基づき、製品のピッキングや搬送を自動で行います。
製品の出庫指示がシステムからAGVに送信されると、最適なルートを計算し、指定された製品を出庫エリアまで搬送します。特に、労働力不足が課題となる現場では、AGVによる自動化で、人手不足の解消や生産性向上が図れます。
入出庫管理のAI活用事例
近年は、IoTによるデータ収集を活用する入出庫管理だけでなく、AI技術による最適化も図られています。ここでは入出庫管理のAI活用事例を紹介します。
需要予測による在庫最適化
AIを活用した需要予測を活用すると、将来必要となる在庫量を正確に見積もれるようになり、欠品や過剰在庫の防止が可能になります。
AIによる需要分析では、過去の販売データ、季節変動、天候、イベント情報などを基に需要を予測します。特に、需要変動が激しい業界では、AIによる予測が在庫管理の精度を大幅に向上させます。
ピッキング作業の最適化
入出庫管理において特に時間と労力がかかるピッキング作業も、AIを活用することで効率化が可能です。AIが倉庫内の製品配置を分析し、最短ルートを計算することで、ピッキング作業の効率が向上します。
さらに、作業者の動線を最適化するだけでなく、必要な製品を事前に自動で準備する機能を持つシステムもあります。これにより、作業時間が短縮されるだけでなく、作業者の負担軽減にもつながります。
入出庫管理を効率化できる在庫管理システムの選び方
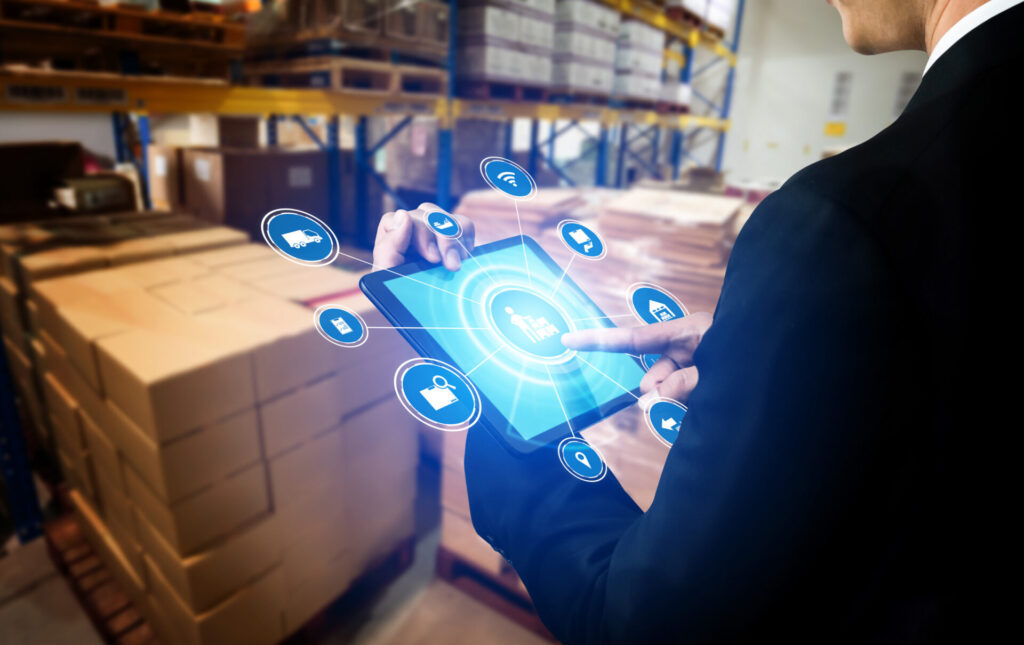
在庫管理システムを導入すると、紙・エクセルによる入出庫管理の課題である、人為的ミスや在庫差異、属人的な業務の工数圧迫などの解消が期待できます。実際に在庫管理システムを選ぶ際は、入出庫管理の効率化に必要な以下機能がどこまで入っているか比較検討することをおすすめします。
- 入出庫記録
- ハンディ端末等との連携機能
- 発注機能
- 需要予測
在庫管理システムを検討する際は、入出庫記録だけでなく、ハンディ端末等との連携が可能かどうかも確認することをおすすめします。IoTツールの連携なしで活用すると、システムに在庫数などを手入力する必要があるため、人為的ミスや工数の削減効果が限定的になってしまいます。また、在庫管理システムには、IoTツールと標準連携できるものと、有料オプションとなってしまうものがあるので、そこも要確認です。
さらに、発注機能も備えていれば、現在庫数を見ながら発注する作業がワンストップで行えるようになります。
在庫管理システムの導入の流れはこちら:
製造業向け在庫管理システム22選!機能や特徴、導入メリット、選び方をまとめて紹介
需要予測機能まであれば、発注計画の精度も高くなります。しかし、需要予測機能まで備えたシステムは高額になりやすいため、検討できる企業は一部に留まるかもしれません。
予算を抑える方法の一つとして、「在庫管理機能つきの生産管理システム」という選択肢もあります。
生産管理システムでは、在庫情報を「生産計画」や「受注実績」と紐づけて一元管理できます。将来生産に使用する在庫数・入荷予定数・現在庫数から所要量を自動計算できるため、将来の在庫計画に役立てられます。
クラウドベースのシステムであれば、複数拠点での情報共有や、低コストでのスモールスタートも可能です。
入出庫管理のシステム化成功事例
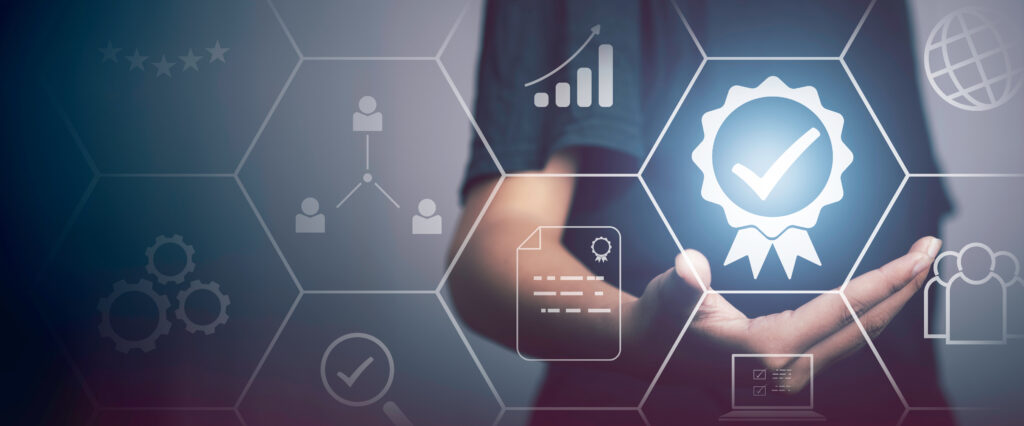
実際に、入出庫管理に在庫管理システムや生産管理システムを導入し、ミスや工数の削減に成功した事例を紹介します。
バーコード管理によるリアルタイム入出庫を実現し、納期回答もスムーズに
ある金属加工の製造会社様は、入出庫管理にシステムを使っていたものの、ハンディ端末などのIoTツールは活用されていませんでした。そのため、仕入先からの納品書を見ながら手入力などの属人的な作業が必要で、正確な入出庫管理はできていない状況でした。そのため、発注時は現場に都度在庫数を確認しに行っていました。
そこで、クラウド型の生産管理システムを導入し、入出庫管理はハンディターミナルによるバーコード管理を導入しました。リアルタイムの在庫管理を実現したことで、現場確認の頻度が大幅に減っただけでなく、顧客からの納期確認に対してスムーズに対応できるようになりました。
詳細:【生産管理システム】手入力の手間をなくし年間200時間以上の工数削減!アナログ管理特有のヒューマンエラーも大幅削減
手書き棚カードをシステムに置き換え、年間300時間以上の工数削減
ある基板実装業界の企業様は、棚カードによる入出庫管理を行っていました。毎日の平均入庫数が150点ほどあり、工数圧迫の問題があったのはもちろん、管理の徹底度が拠点に寄って異なるという属人化の課題もありました。
そこで、在庫管理システムとハンディ端末による入出庫管理を導入し、棚カードの業務をシステムに置き換えました。入出庫の手間を年間300~600時間削減できたうえに、誤ったロットの出庫を防ぐアラートを出す機能で先入先出の徹底も実現しました。
詳細:【在庫管理システム】在庫の見える化と年間1000時間以上の工数削減に成功!手作業や残業をなくすことで生産性を向上
22種類の生産管理システムをランキングで比較
初期費用相場や選び方のポイントをチェック
生産管理システムをそれぞれの特徴や初期費用相場などで比較したい場合は、「生産管理システムランキング」も是非ご覧ください。生産管理システムは、自社の製品・生産方式・企業規模などに適したものを導入しないと、得られるメリットが限定されてしまいます。事前適合性チェックや生産管理システムを選ぶ前に押さえておきたいポイントも解説していますので、製品選びの参考にしてみてください。