2024年07月08日
【在庫管理システム】在庫の見える化と年間1000時間以上の工数削減に成功!手作業や残業をなくすことで生産性を向上
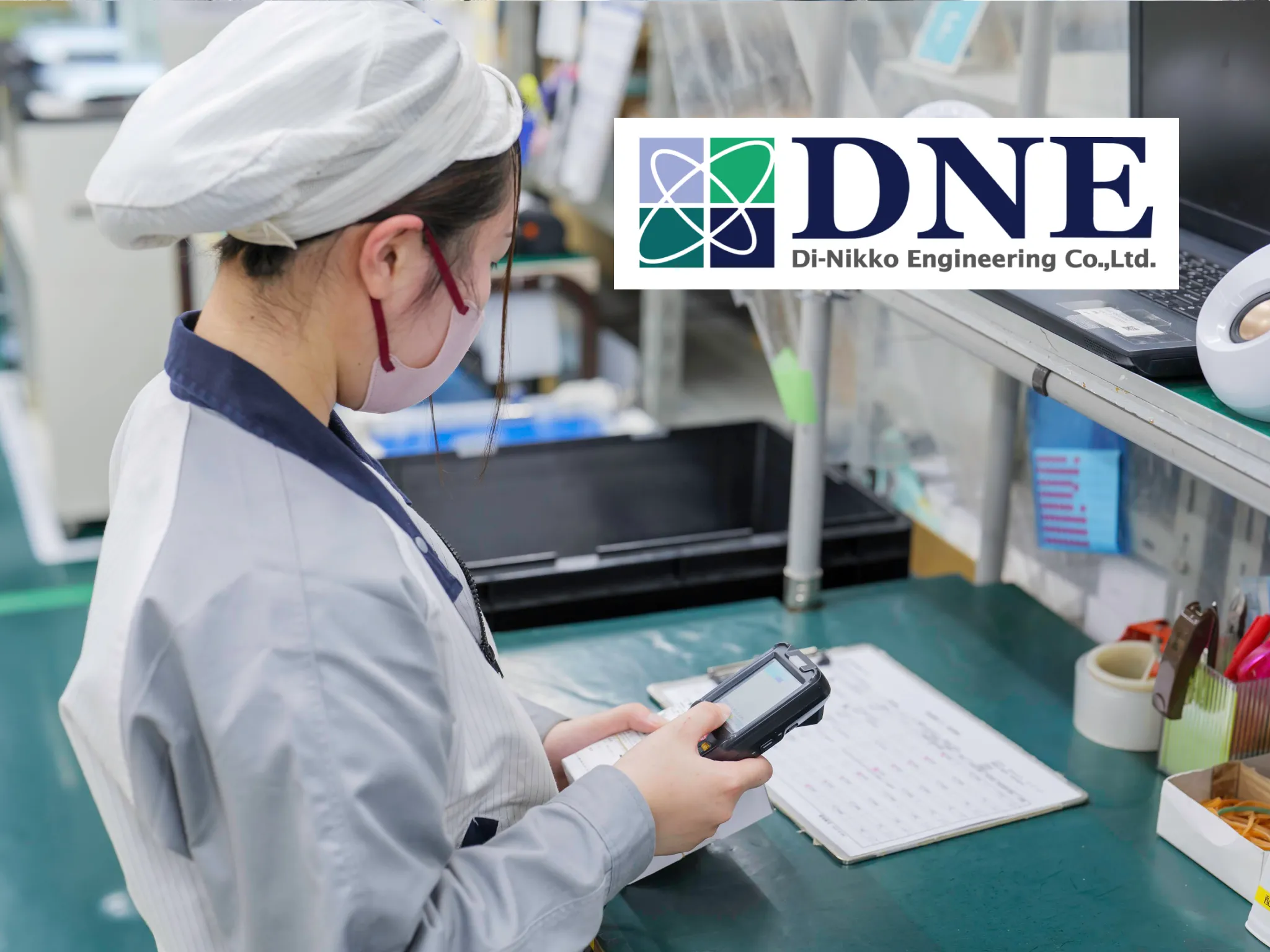
株式会社大日光・エンジニアリング
業界 | 基板実装業界 |
---|---|
会社規模 | 100~299人 |
機能 | 在庫管理 |
システム概要
課題
- 棚の部品在庫数が管理できていなかったため、倉庫内の在庫数が正しく把握できず、配膳時に部品欠品が発生していた
- 棚カードへの手書き記入に年間300~600時間の工数を割いていた
- 棚卸は手作業による棚カード集計・入力が中心で、10~12営業日必要だった
- 入荷品から急ぎ品を仕分ける作業の現場負荷が高く、ピーク時は20時頃までの残業が発生していた
解決策
- スマートFとハンディーターミナルの導入
- 入出庫をバーコード管理化
効果
- バーコード管理による正確な倉庫の部品在庫見える化に成功、どの製品が作れるか配膳前に把握可能に
- 棚カードをバーコード管理に置き換え、年間300時間以上を割いていた手書き作業がほぼゼロになった
- 棚卸の手入力作業はゼロになり、トータル棚卸工数を1000時間以上削減
- ハンディーターミナルで急ぎ品を受入処理するとアラートが出る仕組みを導入、急ぎ品の仕分け作業がなくなり残業ゼロを実現
導入の背景
業績拡大に伴う在庫増や顧客からの要望で、従来のアナログ管理を脱却する必要が出てきた
自動車やOA機器、医療や社会インフラなど、幅広い業界で使われる電子基板の受託製造を手掛ける大日光・エンジニアリング様。部品点数や在庫点数が非常に多く、業績拡大のなかで扱う点数は更に増えています。その中で、部品倉庫内の「在庫の見える化」や、大量の部品在庫を効率的に管理する必要性が高まっていました。
生産管理システムは10年以上使用しているものの、受託案件ごとの製造に必要な部品の払い出し状況の確認までは管理できず、倉庫と製造現場にある在庫を区分した部品在庫の正確な情報を把握できませんでした。そのため、システム上では倉庫と製造現場にある在庫の合計数しか参照できませんでした。
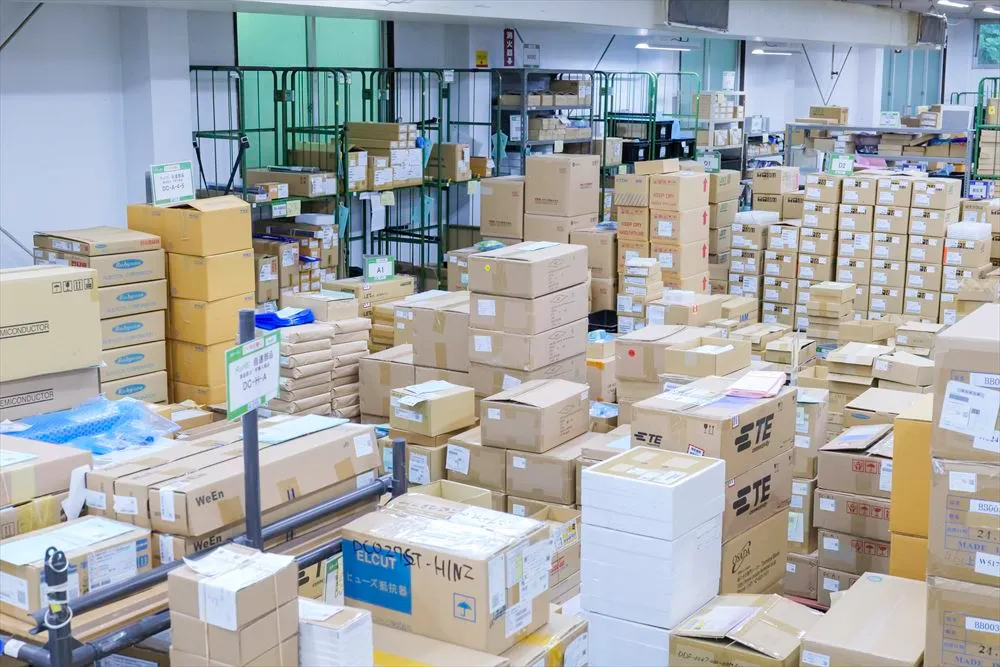
そこで、実際に倉庫内に保管されている在庫数は、システムではなく手書きの棚カード(棚札)で管理していました。倉庫にある膨大な在庫を手作業で管理するのは煩雑なうえに、管理の精度にも課題がありました。現場従業員からも、手間が多いアナログな在庫管理に対し、改善を求める声がありました。特に、年2回の棚卸作業については現場負担が大きく、強い改善要求を受けていました。
さらに、コロナ禍で問題となった電子部品の供給難も、在庫管理の重要性が高まる要因の一つとなりました。当時は、特定の部品が長く欠品したり、それに伴い他の部品が在庫過多になったりと、在庫の動きが非常に変則的でした。その状況下で、リアルタイムに在庫状況が見えないために、生産を進められない事態も多々起きました。顧客からも改善要望をいただき、システム導入がより急務となりました。
これら社内外からの声を受け、経営陣が部品管理のシステム化を推し進める方針を打ち出し、2020年前後から本格的に在庫管理システム導入の検討を開始しました。
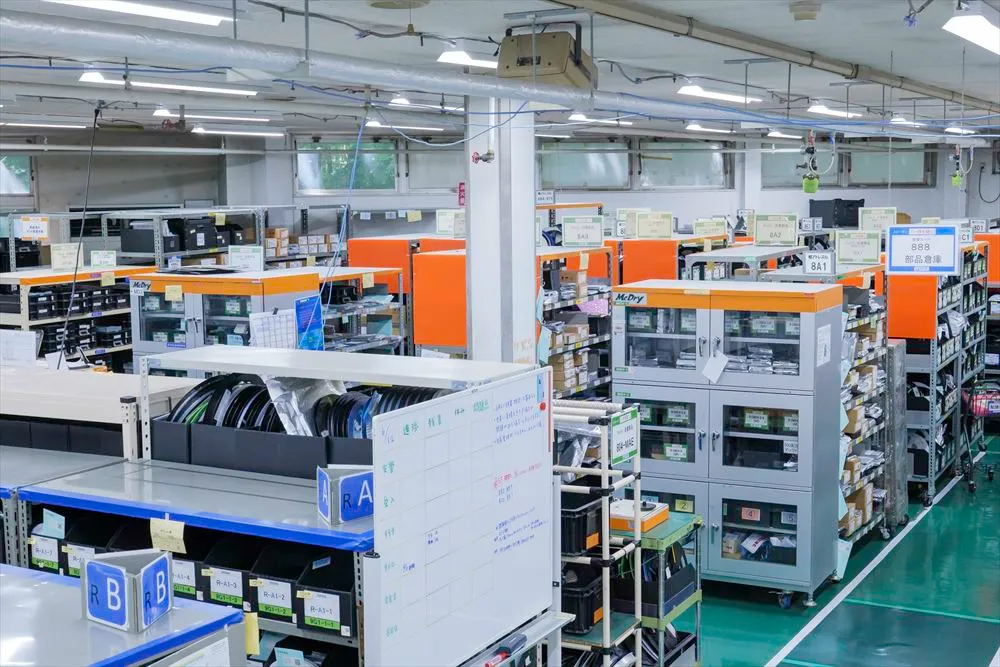
スマートFに決めた理由
一部の拠点から低コストに導入し、自社に合うシステムかどうか試すことができた
在庫管理システムの導入を検討した際、東京ビッグサイトの展示会へ在庫管理ツールを探しに行きました。会場で商談した7〜8社のシステムのうち、そのうちの1つがスマートFでした。それらを比較検討し、最終的にスマートFに決定した一番の理由は、低価格でスモールスタートできる点が魅力だったからです。
今回の在庫管理システム導入に際し、「現場向けツールは試してみないとわからないことが多いため、まずは小さく導入したい」という思いがありました。そこで、まずは一部の拠点から導入し、そこで成功すれば他拠点に展開していこうと考えていました。しかし、当時は今以上にオンプレミス型システムが主流で、そのような提案ができるシステムがほとんどありませんでした。
スマートFは、当時まだまだ少なかったクラウド型システムで、スモールスタートが可能でした。さらに、クラウド型という特性上、他拠点への展開も簡単というメリットもありました。価格・サービス内容ともに同社のニーズに合致すると判断し、まずは試してみることにしました。
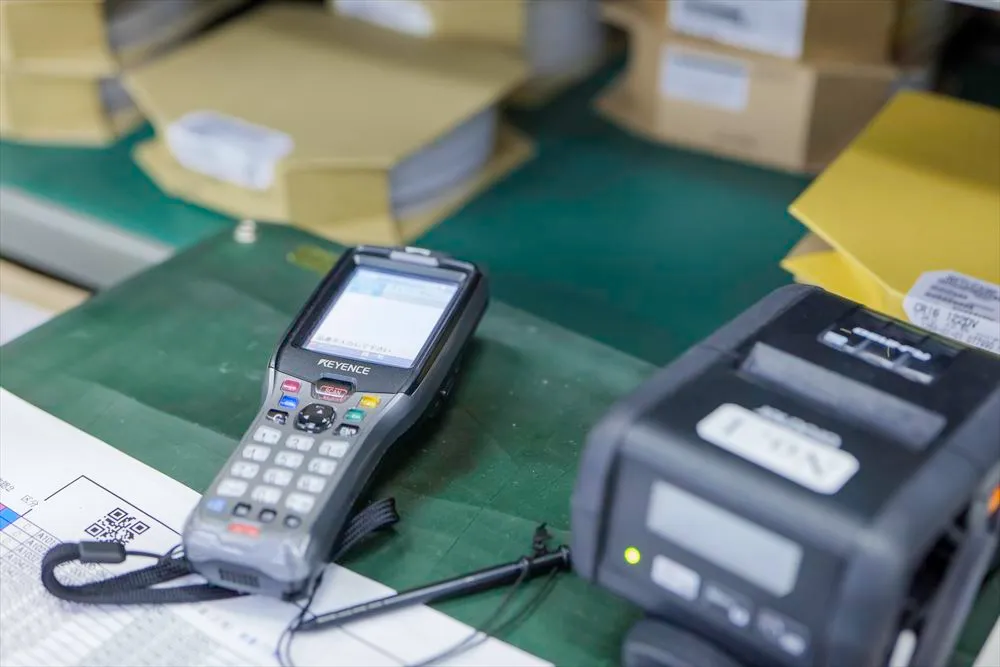
導入効果
部品在庫の見える化により、現在庫でどの製品を生産できるか正確に判断できるようになった
【導入前】各在庫がどの製造に配膳済か管理できなかったため、倉庫内の在庫数が正しく把握できず、配膳時に部品欠品が発生していた
既存システムでは、倉庫と製造現場の合計在庫数は確認できるものの、倉庫内に残っている在庫(=まだ製造現場に持ち出していない在庫)数や、各部品がどの製造に配膳済み(※)かまで管理できなかった。
※配膳:案件ごとに必要な部品を予め払い出し(準備)しておくこと
そのため、電子部品の供給難になった際に、配膳作業時に欠品が判明する事態が頻発。その度に生産計画の変更をしなければならなかった。また1時間程かけて配膳した部品をばらし、再度別の製品向けに配膳し直す作業が発生した。その融通作業が増えることで、部品がどこにあるかが更に把握しづらい状況にも繋がっていた。
電子部品の供給難ピーク時は、1日およそ30案件を回すうち、ほぼすべての案件がこのような欠品状態に陥り、生産が滞る状況に悩まされていた。
【導入後】バーコード管理による正確な倉庫の部品在庫見える化に成功、どの製品が作れるか配膳前に把握可能に
スマートFとバーコード管理を活用し、入出庫をリアルタイムに登録・更新する運用を導入。部品の入荷時や、倉庫内部品の出庫時は、バーコード読み取りによる出庫登録を行うようにした。製造現場への在庫引当が管理できるようになったことで、どの製造向けに何点払い出したか把握できるようになった。
この在庫の見える化に成功によって、出庫時点の倉庫内在庫から、どの製品が生産できるかを正確に判断できるようになり、生産遅延や生産停止の防止に繋がった。
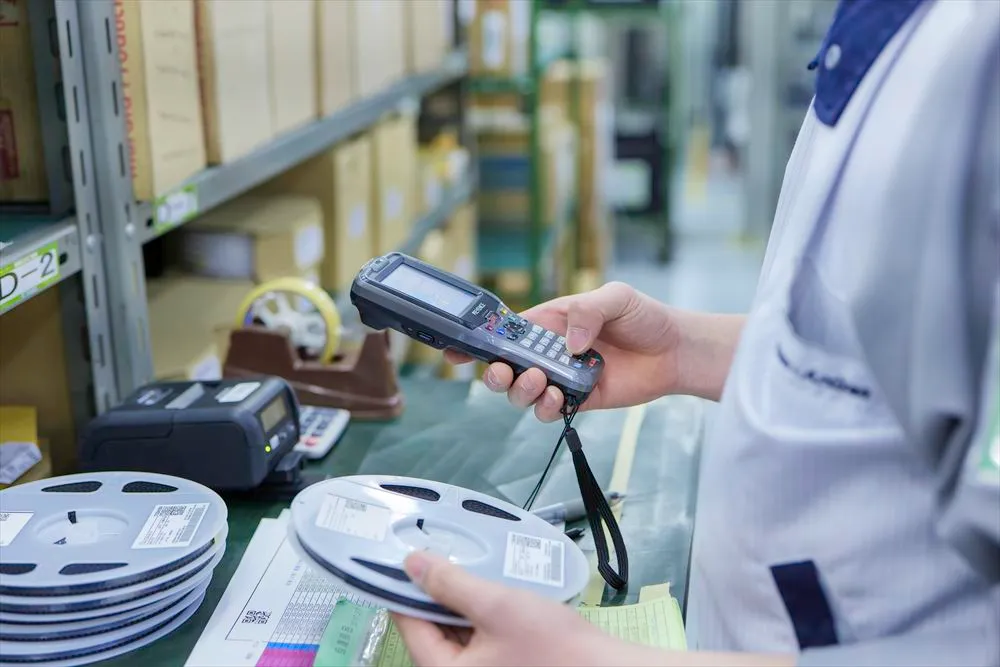
手書きの棚カードをバーコード管理に置き換え、入出庫の工数を年300~600時間(およそ30%)削減
【導入前】棚カードへの手書き記入に年間300~600時間の工数を割いていた
以前の入出庫管理は、手書きの棚カードで行っていた。材料を製造現場へ持ち出す際の出庫や、戻り在庫の入庫の度に、作業者が手書きで記入していた。1日の平均入庫数が約150点あり、1枚手書きするのに約30秒かかっていたので、月25時間程の工数が発生し、棚カードへの記入にかなりの工数を使っていた。
また、手作業による入出庫管理は、先入れ先出しの徹底度合いが拠点によって異なるという、属人的な課題の要因にもなっていた。
【導入後】棚カードをバーコード管理に置き換え、年間300時間以上を割いていた手書き作業がほぼゼロになった
現在、根室工場のほぼ全ての棚カードを、スマートFとバーコード管理に置き換え済み。月25~50時間を割いていた入出庫の手書き記録がゼロになった。年間でみると、300~600時間、およそ30%の工数削減に成功した。
さらに、エリア管理やロット管理にくわえて、シリアル管理の導入にも成功。異なるロットを出庫しようとすると、ハンディーターミナル上にアラートが表示される機能により、先入先出判定もバーコード読込で可能となった。この結果、品質管理の徹底も実現できた。
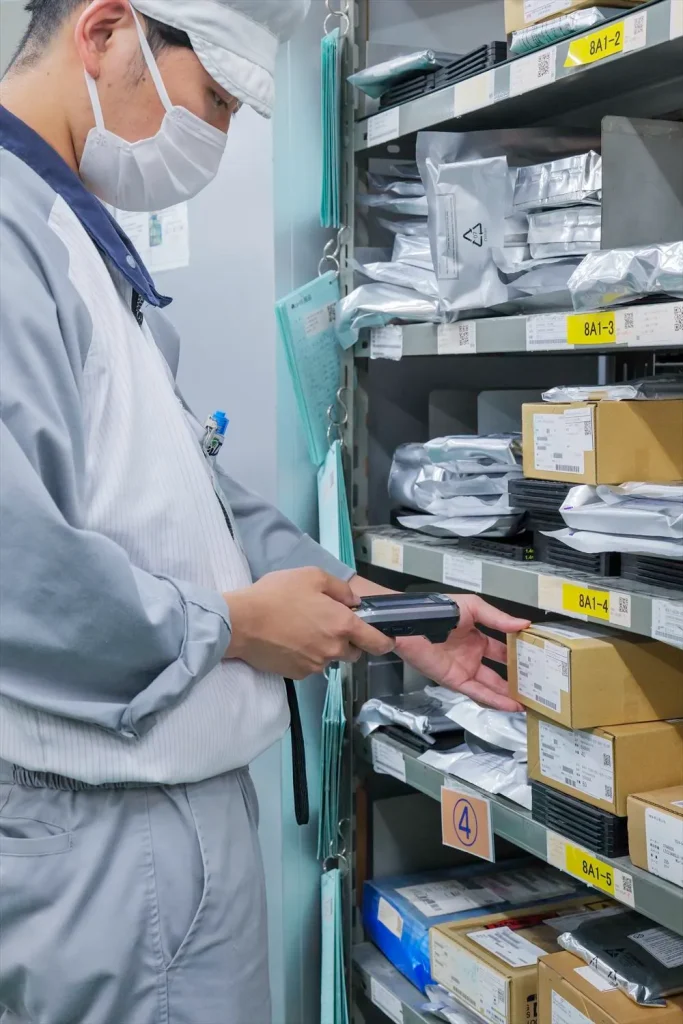
入出庫ペーパレス化の結果、棚卸工数40%以上の削減が実現可能に
【導入前】棚卸は手作業による棚カード集計・入力が中心で、10~12営業日必要だった
棚卸は年2回、倉庫と製造現場で10~12営業日かけて行っていた。在庫の約80%以上は倉庫にあるため、倉庫棚卸は特に負荷が大きかった。
倉庫内の棚卸では、棚カード集計と配膳表照合の2つの方法で行っていた。倉庫に保管されている在庫は、手書きの棚カードをエリア別に集計し、エリア別の棚卸結果を既存システムへ入力していた。大きい拠点では200以上のエリアがあるため、他部門にも手伝ってもらいながら棚卸する必要があった。配膳を終え製品単位に集められた在庫は、既存システムから出力した配膳表をもとに棚卸を行っていた。こちらも、他部門にサポートしてもらう場合があった。
既存システムへの入力は、棚カードに貼付しているQRコードをスキャンして部番を呼び出し、区画コードで識別してエリア別の棚卸結果を手入力するという流れだった。この手入力作業では、2拠点で約5000部番の登録に4~6時間ほど掛かっていた。
【導入後】棚卸の手入力作業はゼロになり、トータル棚卸工数を1000時間以上削減
スマートFとハンディーターミナルによる入出庫管理、かつスマートFと既存システムをCSV連携することで、4~6時間かかっていた棚卸時の既存システムへの手入力作業はなくなった。
さらに、棚卸工数においても大きな削減効果を得られた。2022年11月の棚卸において、担当者の工数をすべて合計した棚卸工数が約2900時間だったのに対し、2023年11月は約1500時間まで圧縮。1000時間を超える工数削減に成功した。
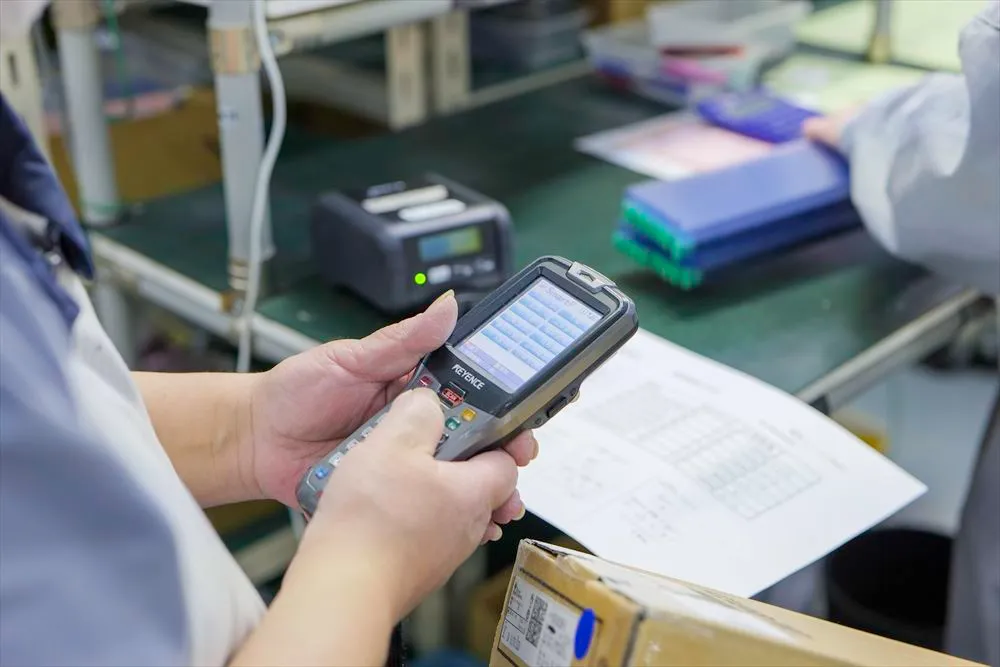
入荷受入時に急ぎ品を発見する機能により、急ぎ品の仕分け作業がゼロに。入荷担当者の残業ゼロも実現
【導入前】入荷品から急ぎ品を仕分ける作業の現場負荷が高く、ピーク時は20時頃までの残業が発生していた
日々大量に受け入れている入荷品から、すぐに製造に回す必要がある急ぎ品を見つける仕分け作業が、現場の負担になっていた。
具体的な仕分け作業は、1日の入荷品受け入れを終えてから、手作業で急ぎ品を探していくという流れ。ピーク時の入荷数は1日約300点に上り、そこから10~15点ほどの急ぎ品を手作業で探さねばならなかった。時には、入荷と急ぎ品の仕分けのために、入荷検品担当者が20時頃まで残業しなければならない日もあった。
【導入後】ハンディーターミナルで急ぎ品を受入処理するとアラートが出る仕組みを導入、急ぎ品の仕分け作業がなくなり残業ゼロを実現
スマートF導入から1年後、ハンディーターミナルで急ぎ品のバーコードを読み取るとアラートメッセージが出る機能の追加を要望。ネクスタ社内で機能を新規開発し、現場へ導入した。この新機能により、あらかじめ急ぎ品の情報をスマートFのマスタに入力しておくことで、受入作業中に急ぎ品と通常品を仕分けられるようになった。急ぎ品を手作業で探す手間がなくなったことにくわえ、電子部品の供給回復や他の改善活動の効果もあり、現在は入荷業務を定時(17時)までに終えられるようになった。
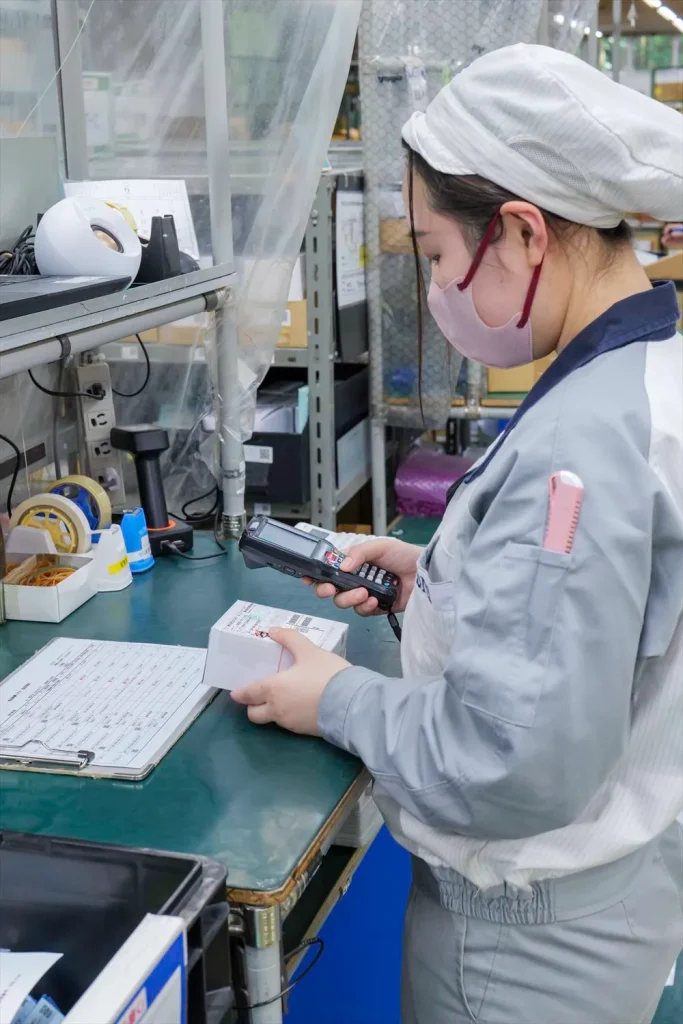
お客様の声
コロナ禍での電子部品の供給難は本当に深刻で、在庫管理体制の改善が急務となりました。とはいえ、現場との相性を見ながらITツールを導入したいという思いがあったので、当時少数派だったクラウド型サービスのスマートFから試すことができよかったと思います。まずは一部の拠点から始め、徐々に拠点展開していくことで導入リスクを抑えられました。トライアル導入時は、機器レンタル等も対応していただき助かりました。正確な在庫管理による計画生産で、顧客満足度の向上にも繋がっていると思います。
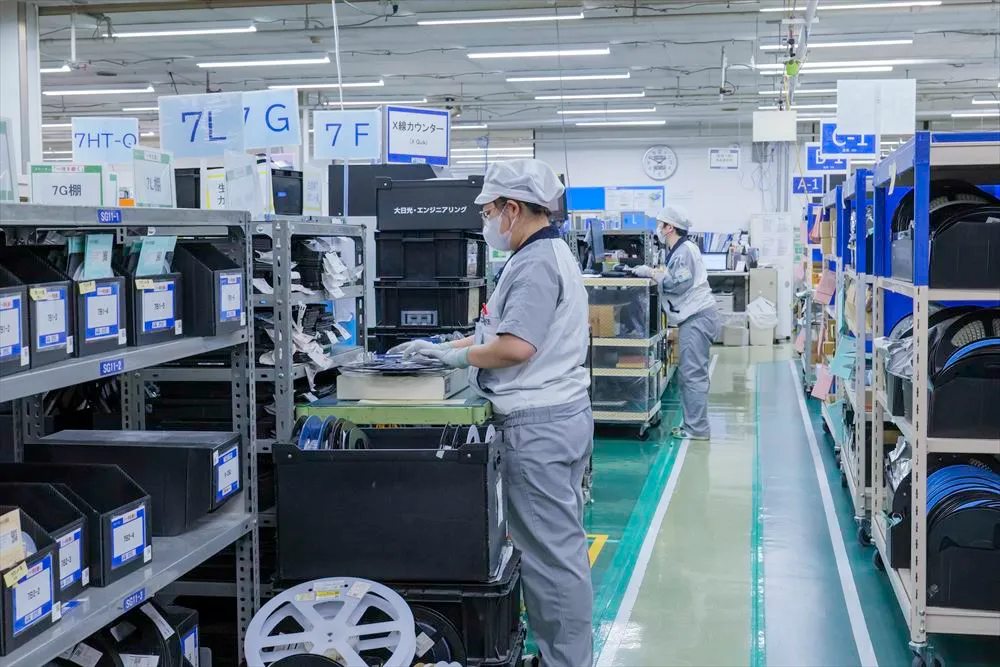
部品倉庫で業務を行う資材部門には、年配者や外国人研修生も多数います。はじめはハンディーターミナルの扱いに不安がありましたが、現在は各人慣れてくれたようです。近年はスマートFの外国語対応なども進めているようなので、海外の方もより使いやすくなるようなアップデートにも期待したいです。スマートFは導入後も週次でバージョンアップがあり、新しい機能が追加されていくので、また自社に合う機能が増えると嬉しいです。
株式会社ネクスタ:導入支援担当の声
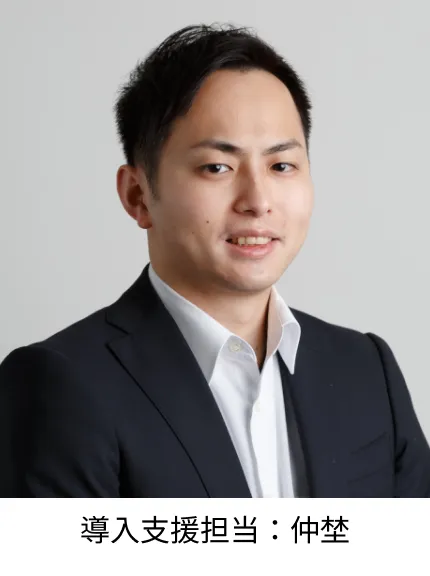
【運用提案する上で心掛けたこと】
大日光・エンジニアリング様では入出庫の作業件数が非常に多いため、ハンディ―ターミナルでの登録工数をできるだけ少なくできる運用を検討しました。また、荷受けと棚入れ、製造への配膳など、担当者が細かく分かれており、製品形態によって登録方法が異なることもあるため、現場の方のご意見をしっかりとヒアリングして理解することに努めました。
【導入時を振り返って】
作業件数が他のユーザー様と比較しても多いため、同時に数十台の端末で作業する際のシステム負荷に課題がありました。最初の棚卸では運用や仕様の調整が必要で、棚卸完了までに多くの時間を費やしてしまったことを受け、システムのバージョンアップとサーバーのスペックアップを実施。棚卸をスムーズに登録できるようになり、スマートFの処理速度向上のきっかけにもなりました。
また、入庫や出庫、移動等の基本的な動作や、登録を間違えたときの復旧方法など、大日光・エンジニアリング様の対応を通して様々な運用の仕組みを確立できました。お陰様でスマートFもより便利なプロダクトに成長できたと思います。改めて感謝申し上げます。