可動率とは?計算方法、稼働率との違い、可動率低下の要因と対策事例について解説
公開日:2025年02月16日
最終更新日:2025年02月17日
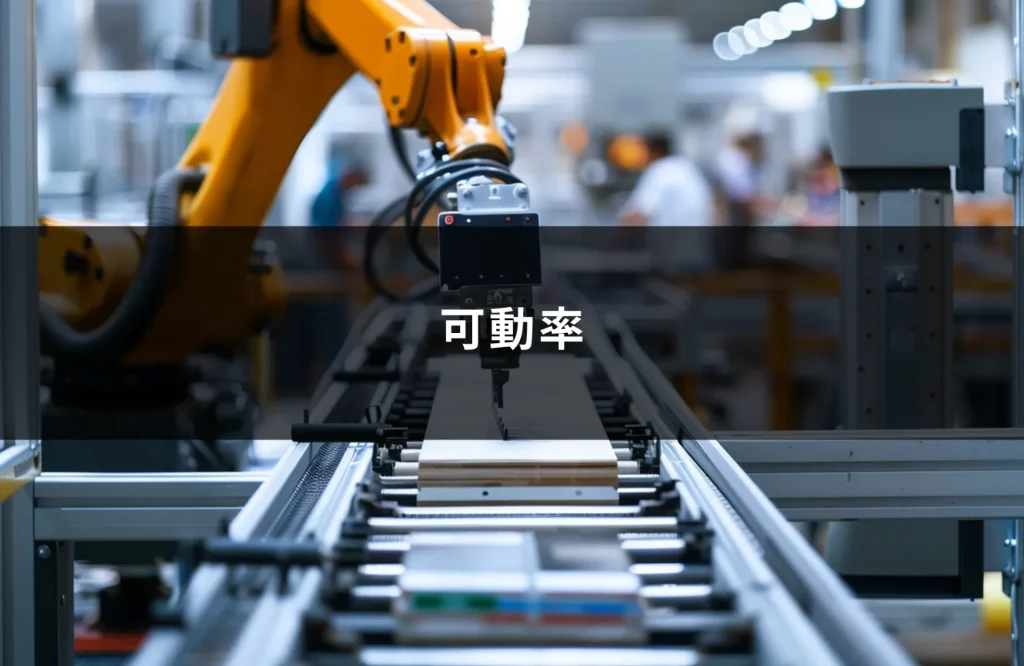
製造業における設備効率の指標である「可動率」。可動率の向上は、設備のフル活用による生産性向上や、トラブル抑制・納期遵守率の改善につながります。本記事では、可動率の基本概念から、生産性に関連する指標である稼働率やOEEとの違い、具体的な計算方法について解説します。さらに、可動率が低下する8つの要因を具体例を交えて紹介し、実践的な対策、効果的なシステム活用事例も紹介します。
可動率(べきどう率)とは
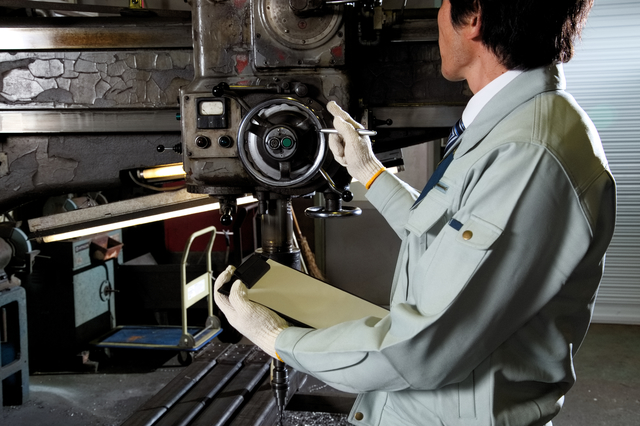
可動率(べきどうりつ、Operational Availability)は、設備の使用効率を示す指標の一つです。生産計画を考慮した設備の稼働予定時間に対して、実際に稼働していた時間の割合を示し、設備利用率の観点で生産性を評価できます。
生産性に関連する指標:可動率・稼働率・OEE
設備の生産性に関連する指標として、可動率以外に、稼働率・OEE(総合設備効率、Overall Equipment Effectiveness)が知られています。それぞれの指標の名称と説明、計算式は以下の表の通りです。
指標の名称 | 指標の説明 |
可動率 | 生産数量に対する理論上の稼働時間をベースとして、設備の使用効率を評価(単位生産量当たりで、どれだけ効率的に生産できているか) |
稼働率 | 設備の稼働可能時間をベースとして、稼働実績を評価(どれだけ生産設備が混雑しているか) |
OEE(総合設備効率) | 次の3要素で、設備効率を総合的に評価 ・可動率 ・性能効率:理想的な速度で生産した時間の割合 ・品質率:生産品の良品率 |
可動率は、細かな設備トラブルやメンテナンスの遅れ、段取りミスなど、オペレーション都合による設備の非稼働時間を見える化します。「設備が理論上動ける時間」を基準にしているため、こうした無駄な停止時間を改善することで向上できる指標です。
一方で、稼働率は計画に基づいた指標なので、トラブルやメンテナンスの遅れなどによる設備には注目しません。稼働率は生産計画数量が少ない場合に下振れするため、石油化学業界など受注・需要と紐づけることが多い評価指標です。
また、OEEは、可動率に加え、他の切り口での生産性や品質維持の観点を追加したもので、総合的な設備効率の指標です。
可動率向上のメリット
可動率を向上させる最大のメリットは、製造業に欠かせない高価な設備をフル活用できることです。
設備当たりの生産性を高めると生産余力が生まれます。その結果、追加の設備投資が不要になったり、受注量を必要以上に抑制したりする必要がなくなります。
さらに可動率改善の取り組みを通して、次のようなメリットも享受できます。
- 設備トラブルの抑制:予期せぬ設備不具合による非稼働時間を減らす
- 整流化の加速:モノの流れを滞留させず、効率的な生産フローを実現する
- 納期遵守率の向上:計画通りの生産できる体制の構築を加速する
製造業における可動率の目安
代表的な製造業である自動車業界では、トヨタ生産方式(TPS)が広く浸透しており、その中で90%程度の可動率が理想とされます。
しかし、可動率の目安は業界や生産方式によっても異なります。例えば、食品業界では衛生管理や高頻度の清掃作業が伴うため、自動車業界よりもやや低く、80~90%を目指すケースが多いです。多品種少量生産の多い機械加工・部品製造などでは、段取り替えが多くなるため、70%程度を目標とする場合もあります。
一般的には、可動率が70%未満になると、設備保全の不足によるトラブル、生産に向けた段取り不備など、様々な改善の余地があると考えます。各業界や工場の状況、現状を踏まえたカイゼンの取り組みなどを踏まえ、職場ごとに適切な目標を設定することが重要です。
可動率の計算方法
可動率をはじめ、評価指標には正しい計算が欠かせず、データ収集も必要です。
稼働率の計算方法との違い
稼働率は、実際の操業時間と非操業時間から求めますが、可動率は設備を動かして実際に生産した時間(=稼働時間)に焦点を当てて計算します。稼働率、可動率それぞれについて、具体的な計算方法は次の図の通りです。
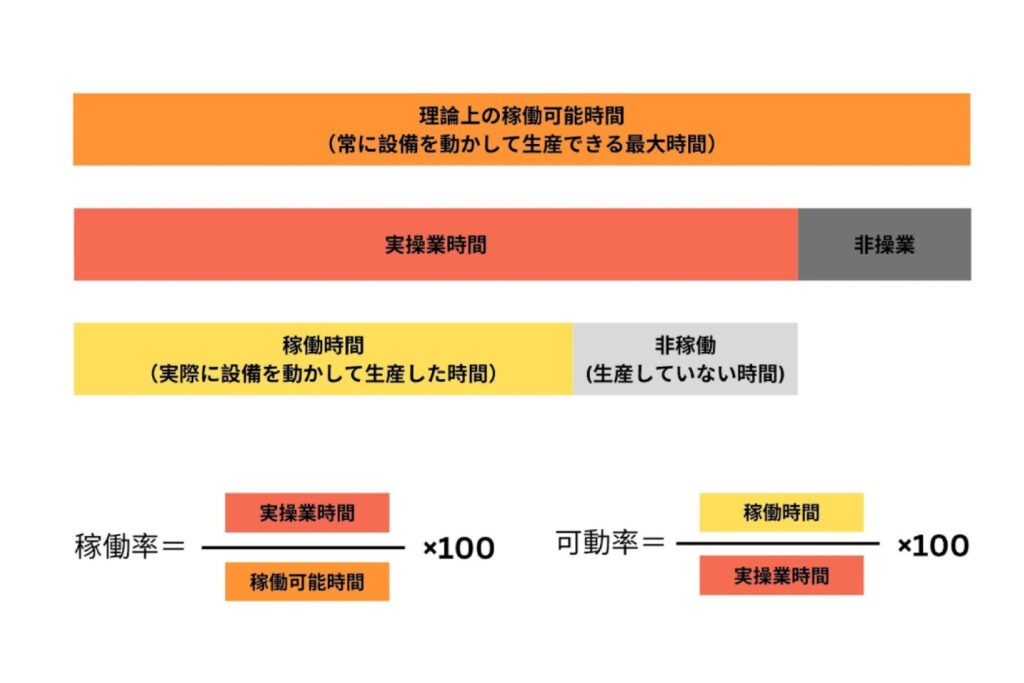
ただし、定期メンテナンスや始業点検時間を「理論上可能な稼働時間」に含めるかどうかは、各職場の実態に応じて判断されます。
計算に必要なデータと可動率計算の例
可動率の計算には、以下の4つのデータが必要です。
- 理論上の稼働可能時間:企業ごとの稼働日、稼働時間から算出される時間
- 実操業時間:生産計画から算出される稼働予定時間
- 非稼働時間:設備を動かしていない時間の合計
- 稼働時間:実際に設備を動かしてモノづくりをしていた時間
例えば、9時~17時で週5日勤務する企業において、1週間の操業記録から可動率を算出する場合を例に挙げます。計算に必要なデータは次の通りです。
- 理論上可能な稼働時間:8時間×5日で40時間
- 実操業時間:生産計画から算出される「稼働率」が80%の場合、40時間×75%で30時間
- 非稼働時間:メンテナンスや原材料入荷待ちなどの「非稼働時間」が9時間
- 稼働時間:30時間-9時間=21時間
この場合、可動率は(21時間 ÷ 30時間) ×100=70% と計算されます。
なお、計算上は稼働時間のみわかれば可動率が計算できることになりますが、実際には稼働時間の正確な記録が難しいケースもあります。しかし、上記3つの時間を測定すれば、次の式で正しい計算ができていることを確認できます。
理論上可能な稼働時間=稼働時間+非稼働時間+非操業時間
これらのデータの正確な把握によって、設備の稼働状態を正しく評価できるようになります。定期的なデータ収集と分析が実施できる体制を整えれば、必要な時に可動率の計算が実施でき、改善点を見つけやすくなります。
可動率が低下する要因と対策
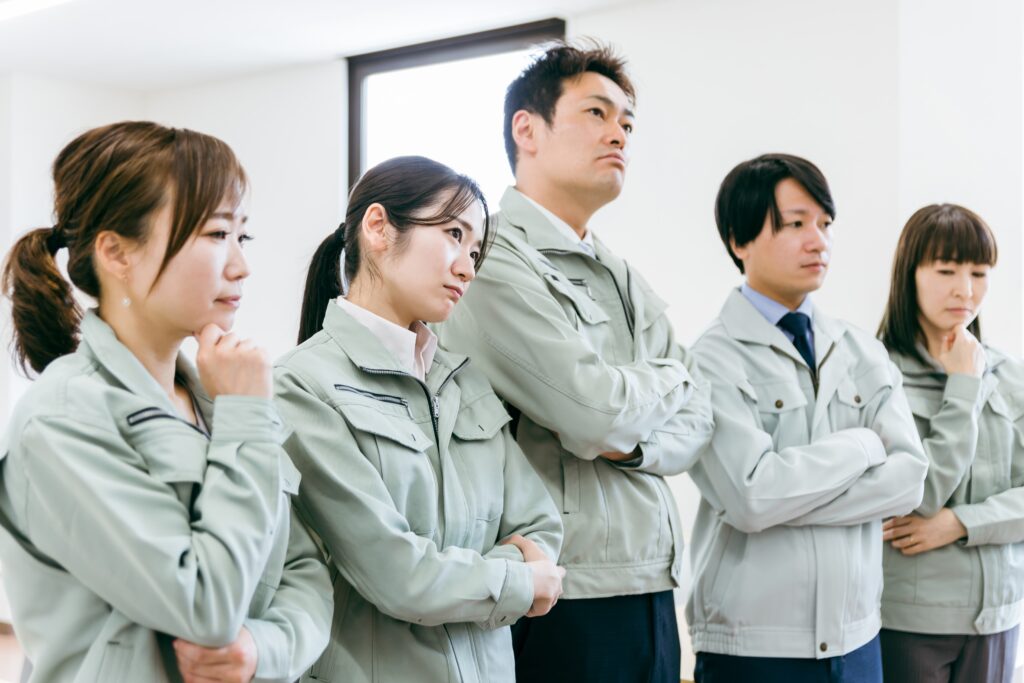
可動率低下の要因は多種多様ですが、よくある要因とその対策について解説します。
チョコ停
チョコ停とは、設備や生産ラインが短時間で頻繁に停止する現象を指します。
微細な調整・設備トラブルや、前工程からの原材料・部品の供給遅れにより、数秒から数分停止することが日常茶飯事という現場も少なくありません。しかし、このチョコ停が積み重なると大きな生産機会の損失となり、可動率が低下します。
例えば、食品工場の包装ラインで、製品がコンベアに詰まって、過負荷アラームが発報したとします。このままラインを動かし続けることはできないため、一度設備を停止させ、コンベアの詰まりを取り除いてから稼働再開します。過負荷アラーム発報から稼働再開まで1分のチョコ停だったとしても、これが1時間に10回発生すれば、1日8時間当たり80分もの生産ロスとなります。
以下のような対策で、チョコ停の原因となる軽故障リスクを減らすことが大切です。
- 予防保全やIoT活用で故障を未然に防ぐ
- 作業者の点検スキルを向上させる
非効率な段取り替え
段取り替えの時間が長いと、設備停止時間が長くなるため、可動率を低下させる大きな要因です。段取り替え作業の効率化や標準化も重要です。
週40時間稼働のプレス工場を例に挙げると、金型交換とその調整に平均2時間を要していれば、これだけで可動率が5%低下します。
段取り替えやその調整作業を標準化したり、段取り替えの回数の少ない生産計画を立案したりすることで、可動率改善が実現します。
段取り替えについてはこちらの記事でも詳しく解説しています。
→段取り替えとは?QMSとの関係、ムダの探し方・削減方法・改善事例を紹介
原材料・部品の欠品
必要な原材料・部品が欠品すると生産が一時停止し、その生産ロス分だけ可動率が下がります。適切な発注と在庫管理で、部品不足のリスク低減が求められます。
ある機械部品工場の例では、組み立て工程で使用するボルトが頻繁に在庫切れとなり、月10時間以上のライン停止が発生していました。もし他の品目生産への振り替えができない場合、20日稼働、1日8時間稼働では、6%もの可動率低下につながります。
欠品とならないよう安全在庫を持つなどの対策によって、可動率低下リスクを下げることができます。
ボトルネック工程による待ち時間
生産ライン全体の処理能力を決めるボトルネック工程の存在により、他の工程が待機状態になることも可動率低下の要因となります。
一例として、工程ごとに時間当たり処理個数が異なる場合を考えます。工程1~工程5のうち、ボトルネック工程は最も処理個数の少ない工程3であり、工程4と工程5は工程3の仕掛品が来るまでの待ち時間が存在します。このような場合も、設備余力は非稼働時間となるため、可動率は低くなります。
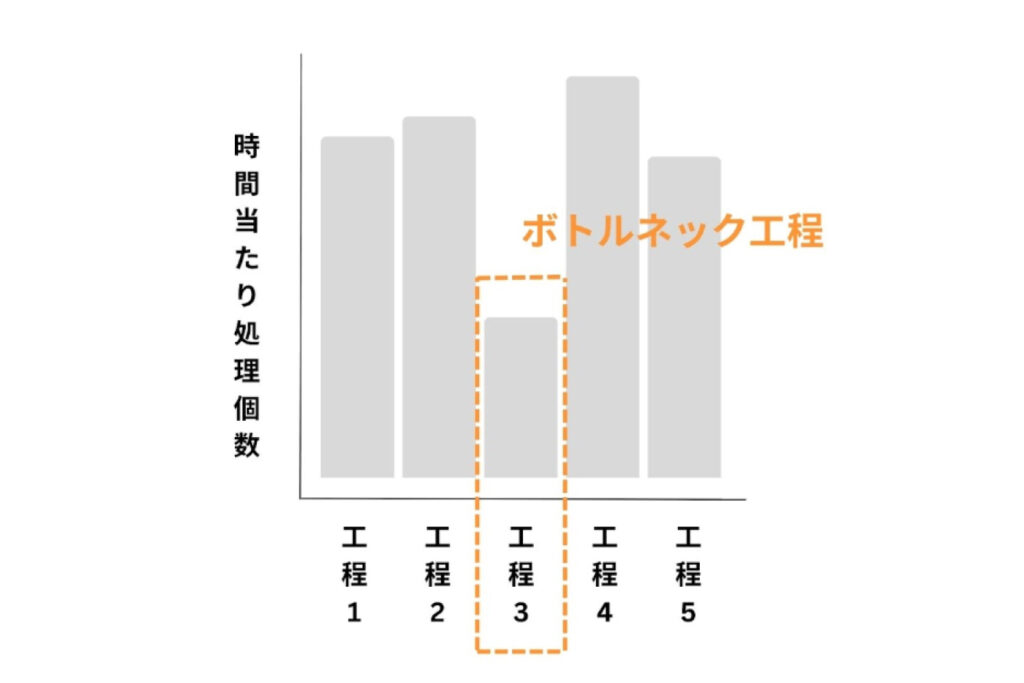
中長期的な需要増大が見込まれる場合には、ボトルネック工程を中心とした設備投資をすることも可動率の改善に有効でしょう。
設備の重故障
設備の重故障は、停止時間が増えるため、可動率低下の大きな原因の一つです。
ある工場では搬送コンベアのベルトの過負荷によって毎月1回故障し、復旧に3時間以上を要していました。1か月に160時間(20日×8時間)稼働のケースでは、これだけで可動率2%悪化となります。
予防保全や迅速な修理対応で、故障リスクを減らすことが大切です。
品質不良の多発
製品の品質不良が多発すると、再作業や手直し、設備調整のための停止時間が発生し、可動率が下がります。
とある電子部品工場では製品の表面研磨中に傷が多発し、不良率が5%に達していました。発生した不良品は、もう一度表面研磨による手直しを実施します。不良発生分の手直しに加えて、手直し専用の段取り時間も発生し、その分だけ可動率が低下します。
品質改善のための取り組みは、不良発生によるコスト低減のみならず、可動率の改善にも寄与する合理化アイテムです。
人為的なエラー
ヒューマンエラーは作業ミスや指示ミスが原因で発生し、設備停止や品質不良によって、可動率悪化を招くケースもあります。
一例ですが、製品包装機の品番設定ミスにより、梱包による不良率は月間で3%発生していました。梱包工程の手直しに必要となる時間は、そのまま可動率の低下に繋がります。
設定品番のミスによる可動率悪化を防ぐために、バーコード読み込みシステム導入によって手入力を減らすなどの対策が挙げられます。
過剰受注
過剰な注文を受けると、設備や作業者に無理な負荷をかけ、設備の過負荷稼働や段取り増加、トラブルの頻発を招きます。これらのトラブルやそのリカバリーのために設備停止時間が長くなり、それが可動率低下という形で顕在化します。
可動率改善に役立つ製造業向けシステム2つ
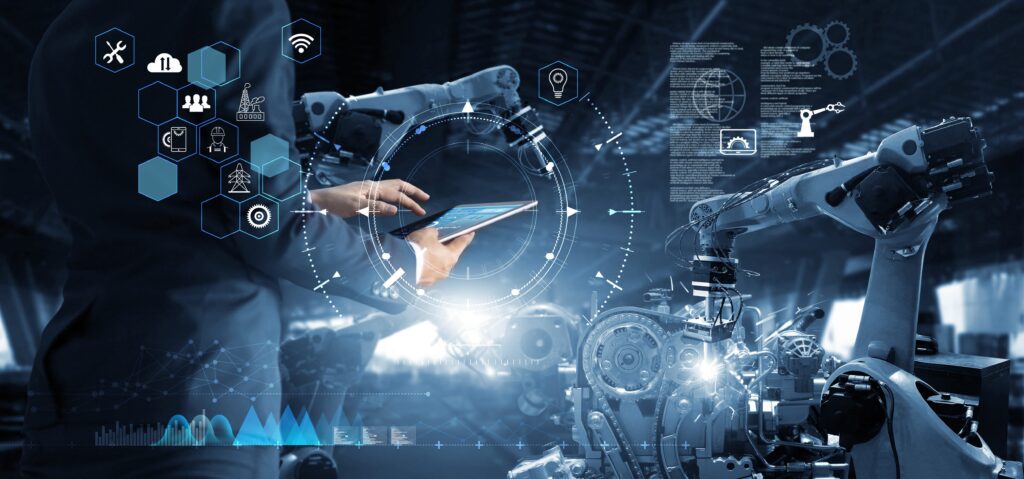
可動率の改善には、製造業向けのパッケージシステムの使用が効果的です。
生産管理システム
生産管理システムによる支援は、可動率の現状把握をしたり、改善に向けた対策を行ったりする上で欠かせません。具体的には次のようなメリットがあります。
- 非効率な段取り替え回数を減らす生産計画を立てやすくなる
- 稼働状況をリアルタイムで把握し、トラブル発生による稼働停止時間を短縮する
- 在庫管理機能の活用によって、欠品リスクを減らせる
実際に、ある製薬企業では、生産管理システムで将来在庫を自動計算し、発注リードタイムの長い原材料の欠品による生産ロスをなくすことができました。
→将来在庫の自動計算を実現した事例はこちら
設備管理システム
設備の軽故障によるチョコ停や設備重故障を防ぐためには、設備の適切な点検・保全を支援する設備管理システムが有効です。設備関連の予備品在庫を管理することで、設備故障による長期停止リスクを減らすこともできます。
→設備管理システム16選!機能や特徴、導入メリット、選び方をまとめて紹介
22種類の生産管理システムをランキングで比較
初期費用相場や選び方のポイントをチェック
生産管理システムをそれぞれの特徴や初期費用相場などで比較したい場合は、「生産管理システムランキング」も是非ご覧ください。生産管理システムは、自社の製品・生産方式・企業規模などに適したものを導入しないと、得られるメリットが限定されてしまいます。事前適合性チェックや生産管理システムを選ぶ前に押さえておきたいポイントも解説していますので、製品選びの参考にしてみてください。