予防保全とは?QMS規格との関連、予防保全の基本的考え方から具体例まで解説
公開日:2025年01月22日
最終更新日:2025年01月22日
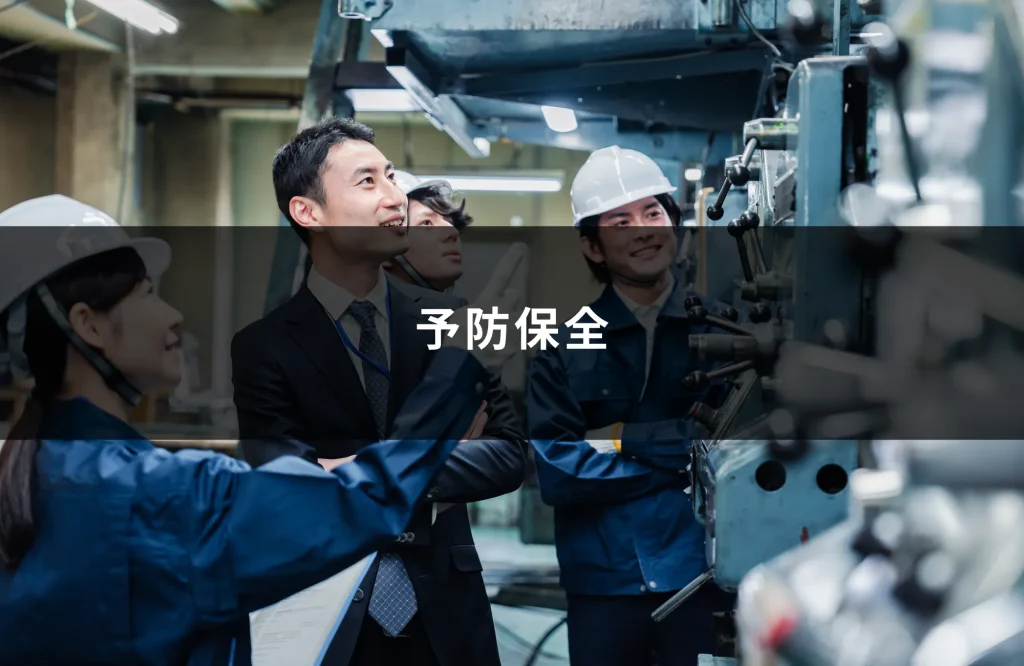
予防保全は、設備トラブルを未然に防ぎ、生産ラインの安定稼働を支える重要なメンテナンスの考え方です。本記事では、予防保全の基本概念から、目的と重要性、QMS規格との関連性、具体的な予防保全の種類、デメリットである過剰メンテナンスについても詳しく解説します。さらに、効果的な予防保全を行うための計画立案における具体的なポイント、保全に使用する部品の在庫管理についても紹介します。
予防保全(PM)とは
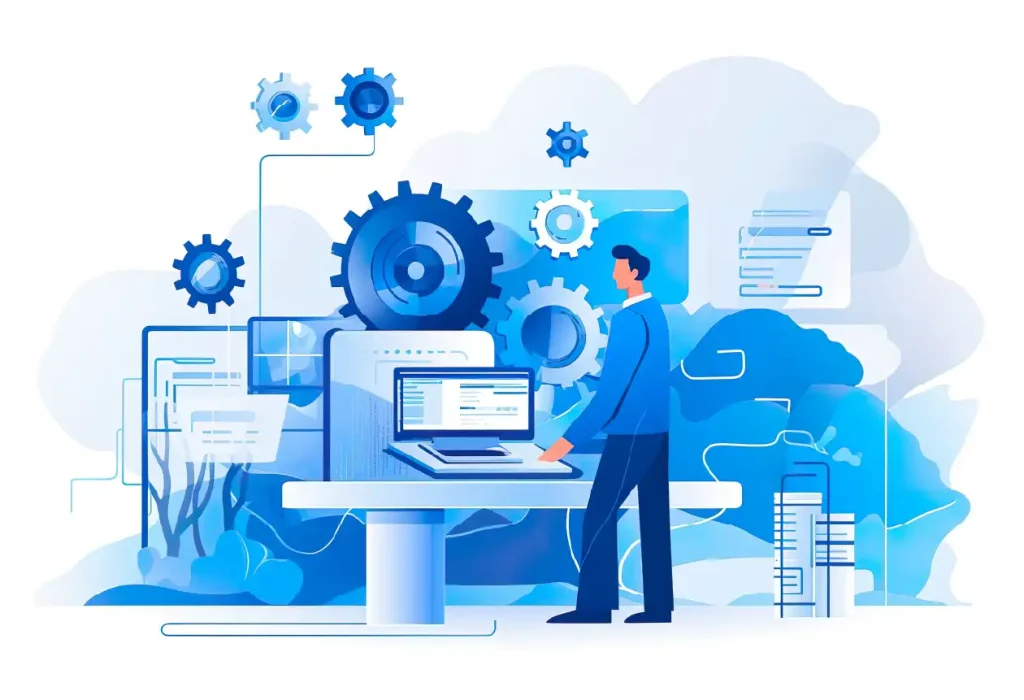
予防保全(Preventive Maintenance、 PM)とは、設備トラブルが起こる前に計画的なメンテナンスを行い、故障を未然に防ぐ方法です。突発的な故障やトラブルを未然に防ぎ、生産ラインの安定稼働を支えます。
予防保全の目的
予防保全の主な目的は、設備トラブルによる突発的な生産への悪影響を防ぎ、長期的な安定稼働を維持することです。
設備トラブルは予測が難しい場合も多いため、設備メーカーが推奨するメンテナンス頻度に基づいて、指定個所を中心とした点検実施の実施が望ましいでしょう。さらに、人員や部品の準備を計画的に行えるため、効率的で安定したリソースが活用可能となります。
このように、予防保全はムリのない形で、安定した製品供給体制を支える重要な役割を果たします。
予防保全の重要性
予防保全によって予期しない設備トラブルを防ぐことは、次の3つの観点で重要です。
- 運用リスクの低減:故障が原因の事故や安全上のリスクを最小限にする
- 品質維持のための基盤作り:設備不良が原因で製品品質への悪影響を防ぐ
- 企業の信頼性向上:納期遅れや不良品を防ぎ、顧客や取引先からの信用を高める
設備トラブルで生産ラインの稼働率が下がることでの影響は、製品の納期遅延を招くだけにはありません。挽回のためにムリな生産を行って、労働災害や品質不良が生じるリスクも増えてしまいます。また、トラブル後にメンテナンスを行う事後保全ばかりでは、応急処置的な設備対応が続くため、設備損傷が蓄積して致命的なトラブルに繋がる可能性もあります。
このように、予防保全は安定的な事業運営に欠かせない考え方といえます。
予防保全とQMS規格の関係
予防保全は品質マネジメントシステム(QMS)とも密接に関連しています。実際に、ISO9001やIATF16949といった国際的な品質規格の要求事項においても、その重要性が強調されています。これらの規格は、予防的な取り組みを推奨することで、品質不良や生産停止を未然に防ぐプロセスを企業に求めています。
ISO9001要求事項
ISO9001では、7.1.3項、8.5.1項目、10.2項それぞれで、予防保全に関連した要求事項が定められています。それぞれの要求事項とその概要、予防保全との関連について、以下の表にまとめました。
要求事項 | 概要 | 予防保全との関連 |
7.1.3:インフラストラクチャ | 必要なインフラを明確にし、維持する | 生産設備を適切な状態に維持するため、予防保全を計画的に実施し、設備トラブルを防止する |
8.5.1:製品およびサービスの提供管理 | 提供プロセスを計画し、管理する | 設備管理を通して生産の安定性を確保し、不良品の発生や生産停止を未然に防ぐ |
10.2:不適合および是正処置 | 不適合の原因を特定し、再発防止を行う | 設備トラブルの原因を分析し、予防保全を見直すことで、不適合の再発防止を行う |
このように、予防保全の考え方は複数の要求事項と関連します。予防保全の計画策定時には、ISO9001の枠組みを参考に、考慮すべき観点の網羅性を確認してみるとよいでしょう。
IATF16949要求事項:8.5.1.5 TPM
自動車産業向けのIATF16949規格では、TPM(Total Productive Maintenance;全員参加型保全)の要求事項の中で、以下のように予防保全が規定されています。
8.5.1.5 TPM(Total Productive Maintenance)
『IATF 16949:2016 解説と適用ガイド-IATF認証取得及び維持のためのルール 第5版』
組織は、文書化したTPMシステムを構築し、実施し、維持しなければならない。そのシステムには最低限、次の事項を含めなければならない
(中略)
h) 予防保全の使用の方法
(後略)
このように、TPMの考え方に基づき、予防保全に関する仕組み化が求められています。具体的には、設備管理に関する社内規定やその実施基準で、予防保全の考え方を盛り込み、確実に実行できる体制を整えます。これらの規定・基準に則り、計画的かつ定期的なオーバーホール・メンテナンスを行い、設備の信頼性向上と生産プロセスの効率化を追求します。
自動車産業においては、単なる保全作業ではなく、全従業員が保全活動に積極的に関わり、日常の点検や設備の改善を行います。予防保全の取り組みは、安全性・競争力の高い製品を安定して生産する体制の構築を加速させます。
予防保全の種類
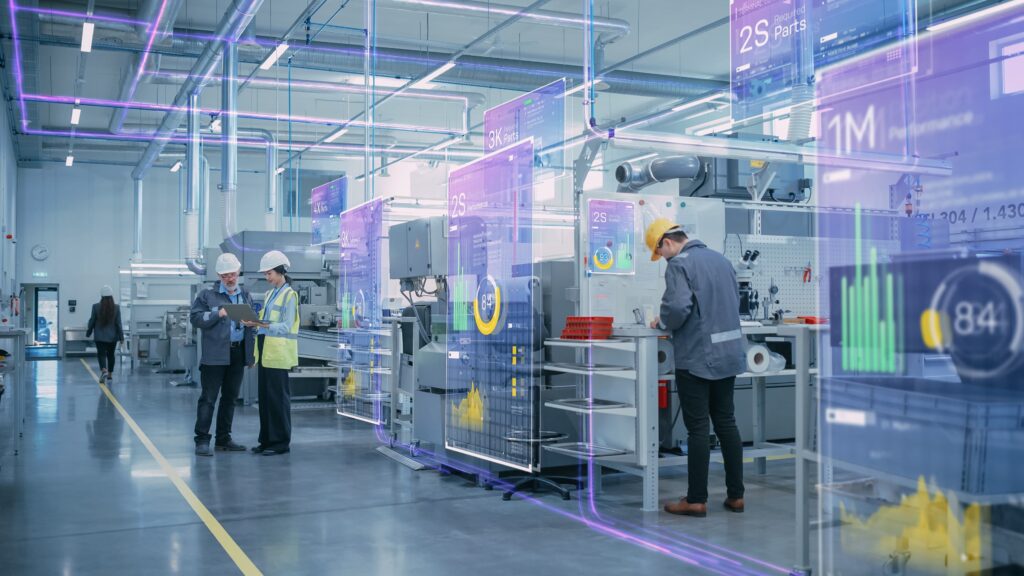
予防保全では、それぞれの設備や運用状況に応じて、メンテナンス周期を決定します。本来の意味での予防保全は、時間基準保全、利用基準保全が該当します。しかし、より広い意味では、状態基準保全や信頼性中心保全も予防保全の一種と考えることもできます。
時間基準保全 (TBM)
時間基準保全(Time-Based Maintenanca;TBM)は、設備の稼働時間・経過時間を基準として定期的にメンテナンスを実施する手法です。一定の稼働時間で故障や劣化の可能性が高くなるとみなし、点検や部品交換を実施します。
工場設備における駆動ベルトは消耗部品であり、一定の稼働時間や経過時間を基準に点検・交換を行うことが一般的です。例えば、製品・材料を運搬するコンベヤベルトは、長時間の稼働によって摩耗や緩みが発生します。突発的なベルト破断が起こると、生産ロスだけでなく設備の損傷にもつながり、未然防止が必要です。
このようなトラブルを防ぐため、一定期間(半年に1回など)ごとに計画的にベルトの点検・交換を行い、突発的な故障を防ぎます。
利用基準保全 (UBM)
利用基準保全(Usage-Based Maintenance;UBM)は、設備の稼働回数など、利用頻度に基づいてメンテナンスを行う手法です。特に使用頻度が高い設備や、特定の条件下で劣化が進む部品に対して有効です。
例えば、CNC工作機械における切削工具の交換は、加工量や摩耗状態を基準に行います。摩耗限界値に達すると加工精度が低下したり、品質不良発生リスクが高いため、例えば一定数量を加工する毎に交換します。
このように、UBMでは、設備の稼働状況をある程度の精度で把握する必要はありますが、効率的な予防保全を行うことができます。
状態基準保全 (CBM)・予知保全
状態基準保全(Condition-Based Maintenance;CBM)は、振動、温度、圧力などのパラメータによって設備の状態を監視し、異常が検出された場合に修理や調整を行う方法です。重大な不具合が発生する前兆を数値で捉えるため、効率的な保全作業が実現します。CBMをもとに保全を行うことを予知保全と表現することもあります。
IoT技術やビッグデータを活用して、設備の状態を常時監視し、故障する前に対処することで、ダウンタイムを最小限に抑えることが可能です。CBMや予知保全には高度な技術が必要となるものの、長期的な視点ではコスト削減や生産性向上に大きく貢献します。
一例ですが、食品工場の搬送ライン用モーターでは、ベアリングの摩耗により異常振動が発生し、そのまま放置すると生産ラインの停止に繋がります。そこで、振動センサーで搬送ラインを常時監視し、閾値を超えたらアラートを発報させ、速やかにメンテナンスをする運用としました。
このように、設備の状態をリアルタイムで把握することで、状態に応じた適切なタイミングで保全を実施できます。これにより、突発的なライン停止を未然に防ぎながら、生産ロスと修理コストを最小限に抑えます。
予知保全・予防保全の違いについては、こちらの記事で詳しく解説しています。
信頼性中心保全 (RCM)
信頼性中心保全(RCM)は、航空業界が発祥の考え方で、設備やシステムの「機能」に焦点を当てたメンテナンス手法です。
まず、設備の故障モードに着目して、それぞれについて重要度やリスク評価を行います(FMEAの実施)。それぞれの故障による影響度の評価結果をもとに、最適な保全手法(時間基準保全、状態基準保全、運転しながらの対応)を選定します。重大な故障には状態監視を導入し、軽微な故障には計画的な点検や交換を行います。
送水ポンプ設備におけるRCMでは、故障モードとして「ベアリング摩耗」「シール劣化」「インペラ摩耗」が考えられます。それぞれについて、具体的な影響度と、RCMに基づく子保全方法は、以下の表の通りとなります。
故障モード | 具体的な影響 | RCMに基づく保全方法 |
ベアリング摩耗 | 異音・振動を引き起こし、ポンプ停止につながる | 振動センサーを用いて監視(CBM) |
シール劣化 | 水漏れ発生 | 一定の使用時間毎に交換を実施(TBM) |
インペラ摩耗 | 送液性能の低下 | 単位時間当たり送液量を監視(CBM)しつつ、運転しながら点検対応 |
このようにRCMは、故障の影響度に応じた効率的な保全が実現され、設備の安定稼働と保守コストの最適化を両立する考え方です。
予防保全のデメリット
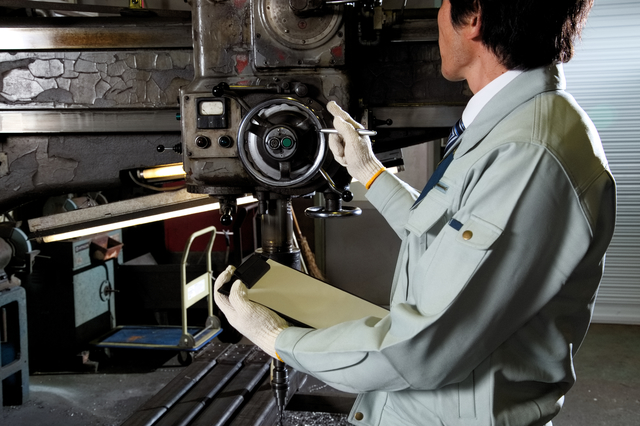
予防保全によって設備故障を未然に防ぐことができる一方で、次のようなデメリットも存在します。
メンテナンスが過剰になる
予防保全では、故障が発生する前にメンテナンスを行うため、まだ正常に機能している部品や設備でも交換を実施します。このデメリットは特に稼働率の変動が大きい設備において特に顕著となりやすいでしょう。
本来の意味での予防保全では、時間基準で保全を行うため、次のような理由で過剰メンテナンスとなる可能性があります。
- 状態を無視した計画:部品の状態に関係なく定期的な保全を実施
- 一律な基準の適用:使用環境や負荷を考慮せず、統一基準で保全を実行
- 安全重視の頻度増加:故障リスク回避のため、余裕を持たせた頻繁な保全を計画
- メーカー推奨の盲信:責任回避のため、設備メーカーの推奨頻度をそのまま採用
このように、過剰なメンテナンスが行われると、結果的にコストや人的リソースを浪費するリスクがあります。設備によっては、頻繁な分解・組立作業そのものが設備劣化を早める可能性もあります。
IoT・DXの投資コストがかかる
広義の予防保全を行う場合には、最新のIoT技術やデジタルトランスフォーメーション(DX)を活用することが望ましく、そのための初期の設備投資が必要になります。
特に、データ収集のためのセンサーや監視システムの導入にはコストがかかるため、特に中小企業にとっては大きな負担となる場合も少なくありません。
予防保全に必要なこと
予防保全を効果的に行うためには、精緻な計画立案、保全に使用する部品の管理が必要です。
精緻な計画立案
予防保全を実施するためには、まず設備の使用状況や部品寿命に基づいたメンテナンス計画を立てます。具体的な手順は次の通りです。
- 設備の特性と重要度の把握:保全の優先順位を決める
- メーカー推奨の保全頻度を確認:メーカー推奨条件を確認し、計画に反映する
- 保全作業の頻度と範囲の設定:点検や交換の頻度と対象箇所を具体化する
- 生産スケジュールとの調整:生産への影響の少ない保全日程を計画する
- リソースの計画:必要な人員、工具、部品を確保する
適切な時期に適切な保守作業を実施できるよう、計画を緻密に立てることで、無駄なコストを削減し、設備の稼働率を維持します。
予備品の在庫管理
保全に使用する部品の発注リードタイムが長い、または交換頻度が高い場合、予備品を持ち在庫管理することも重要です。特に、多くの設備を保有している工場では、関連する予備品の数も多く、在庫管理に悩む企業も少なくありません。
さらに、保全部品のサイズ・重量が大きかったり、部品そのものが高価であったりする場合には、特に正確な在庫管理が求められます。
22種類の生産管理システムをランキングで比較
初期費用相場や選び方のポイントをチェック
生産管理システムをそれぞれの特徴や初期費用相場などで比較したい場合は、「生産管理システムランキング」も是非ご覧ください。生産管理システムは、自社の製品・生産方式・企業規模などに適したものを導入しないと、得られるメリットが限定されてしまいます。事前適合性チェックや生産管理システムを選ぶ前に押さえておきたいポイントも解説していますので、製品選びの参考にしてみてください。