段取り替えとは?QMSとの関係、ムダの探し方・削減方法・改善事例を紹介
公開日:2024年10月21日
最終更新日:2025年03月10日
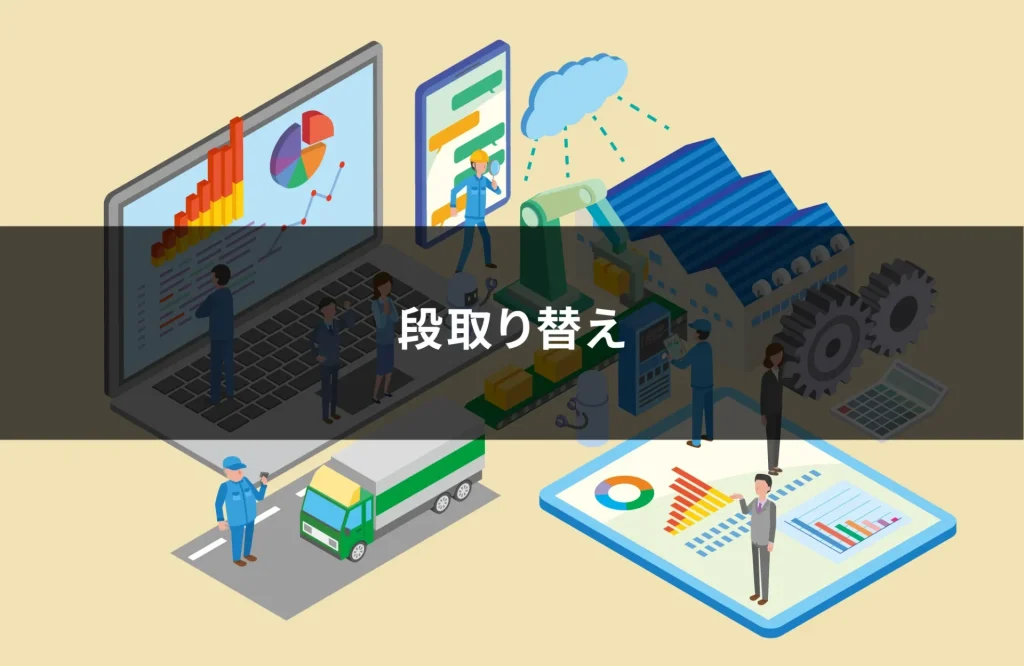
段取り替えは、製造業において生産性と品質を大きく左右する重要なプロセスの一つです。本記事では、段取り替えの基本的な意味やISO9001・IATF16949の要求事項との関係、効率化のポイントを解説します。そして、具体的な改善手法と事例も紹介します。ムダの探し方や排除方法、自動化、段取り改善のステップを学び、現場での生産性・品質向上を目指しましょう。
段取り替えとは
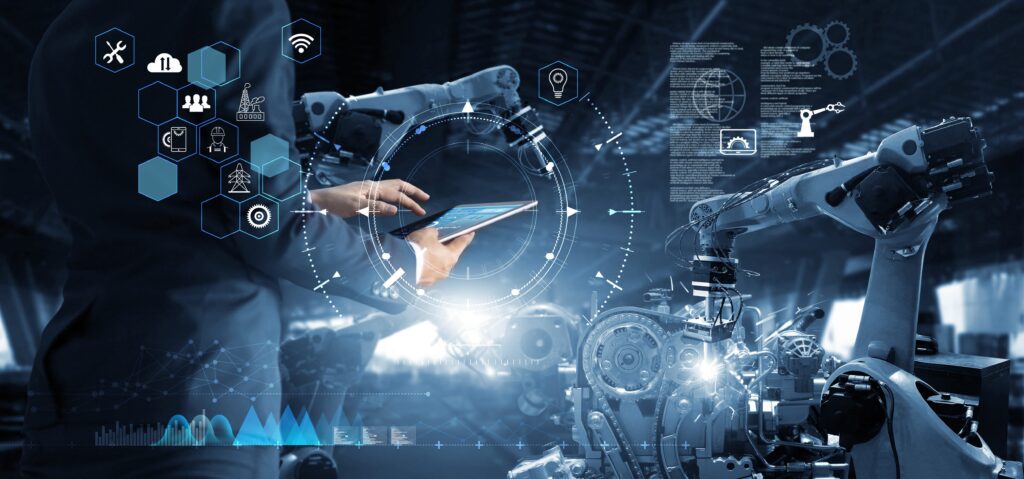
段取り替えは、製造プロセスの中で次の生産品目に切り替えるために必要な準備作業を指します。この工程は直接的な生産活動ではありませんが、生産効率に直結する作業であり、短縮することで生産性の向上につながります。
段取り替えの意味
段取り替えとは、複数の品目を生産する製造ラインにおいて、製品切替時に必要な準備作業です。より具体的には、品目切り替え前の生産が完了してから、次の生産において1ロット目の良品ができるまでの作業全てを指します。
例えば、次のような作業が段取り替えに該当します。
- プレス成形品に使用する金型交換
- マシニングセンタなどの研削加工機の設定条件変更
- 治具類を用いた位置決め調整
- 粉体材料投入の品種切り替え
この工程に要する時間が長いと、生産性が低下し、製品コスト増加につながります。多品種少量生産が求められる現代の製造業において、生産リードタイムの一部である段取り替えの効率化は欠かせません。
段取り替えとQMSの関係
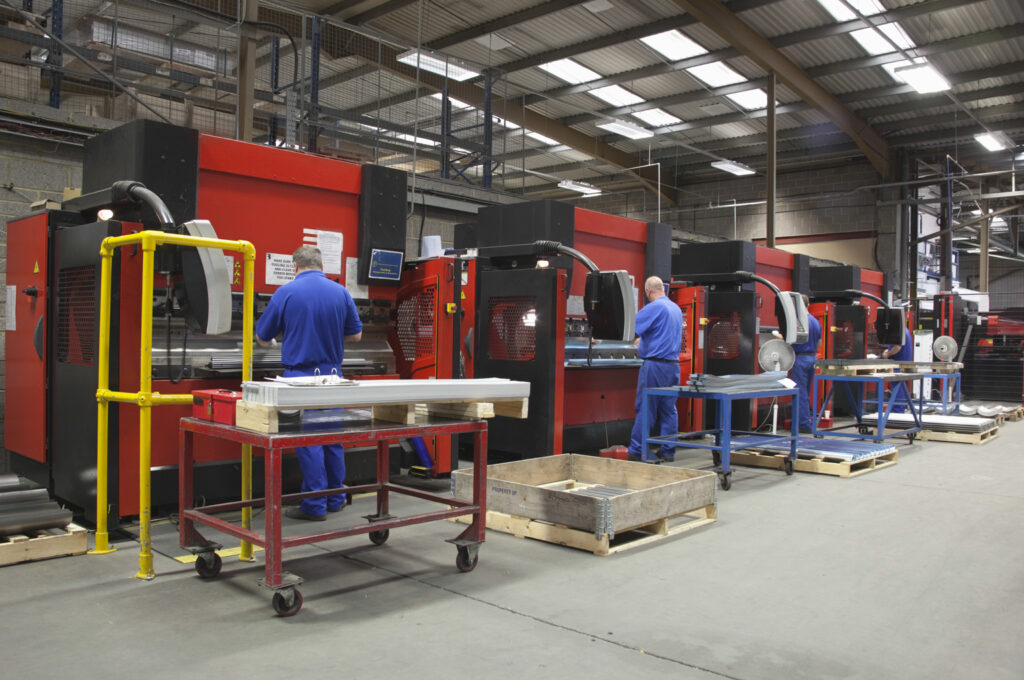
製造現場では効率的な段取り替えが望ましいですが、段取り替え直後は不具合が発生しやすいポイントでもあります。このため、QMS(品質管理システム)の観点からも、品質安定化のために注意を要するプロセスです。
ISO 9001における要求事項との関連
ISO 9001では段取り替えに関する直接的な要求はありませんが、品質管理の観点から次のような要求事項があります。
8.5.1. c)(前略) 製品およびサービスの合否判定基準を(中略)検証するために、適切な段階で監視および測定活動を実施する
ISO 9001:2015「8.5.1 製造及びサービス提供の管理」
段取り替え直後には品質が不安定になりやすいため、「適切な段階」として段取り替え前後に適切な監視が必要である、とも解釈できます。
IATF16949における要求事項ー8.5.1.3.作業の段取り替え検証
自動車産業の品質マネジメントシステムの国際規格であるIATF16949では、作業の段取り替えそのものに関する要求事項が定められています。「要求事項8.5.1.3 作業の段取り替え検証」における主な要求事項は次の通りです。
- 作業の立上げ、材料切替、作業変更では、段取り替え前後について検証すること
- 段取り替えの文書情報をもつこと
- 段取り替えの初品と終品の品質について、統計的方法で検証すること
- 段取り替え前後の検証結果について、工程・検査・承認の記録を残すこと
このように、段取り替え作業には、効率化のための取り組み以外に、品質リスクに応じて必要な検証を実施する必要があります。
段取り替えにおける品質管理上のキーポイント
段取り替えは、品質管理リスクと隣り合わせとなるため、次の2つのキーポイントに留意しましょう。
- 直後の品質確認:段取り替え直後は不具合が起きやすいため、品質検査を行う
- 効果を評価:不具合時は原因を調査し、次回の改善に生かす
このように、段取り替えにはリスクがあるため、適切なモニタリング・評価とセットで実施する必要があります。また、段取り替えそのものを減らすことで、品質リスクの低減にも繋がります。
段取り替えを効率的に行うためのポイント
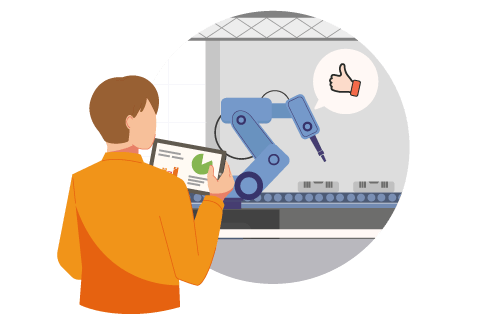
短時間で段取り替えを行うためには、計画立案、作業時の安全性の確保、情報の共有、そして効果の検証までさまざまなポイントを確認する必要があります。
段取り替え作業の少ない生産計画の立案
切り替え対象の品種・順序によって、段取り替えに必要となる時間は異なります。このため、効率的な段取り替えが進められるように、生産計画を計画立案することが望ましいです。
それぞれの設備で行われる段取り替え、全体のモノの流れを十分に分析したうえで、生産計画に落とし込みます。段取り替え作業そのものの効率化も大切ですが、一定期間内で段取り替えに必要となる作業を最小限度にする計画立案も重要です。これにより、段取り替え時の作業ミスを防ぐだけでなく、段取り替えによる品質異常リスクも最小化することができます。
段取り替え作業における安全性確保
強引な段取り替え作業、作業方法が標準化されていない段取り替え作業では、安全面でのリスクも高くなります。このため、安全に作業を進められる手順を確立したうえで、それを確実に守らせるために作業者への教育も必要です。
例えば、設備のブレーカーの電源を確実に切ること、適切な保護具を着用すること、その他の近道行為をしないことが挙げられます。生産性向上・品質安定化も重要ですが、それは安全が成り立って初めて実現します。
段取り替え情報の共有
段取り替えの改善には、情報共有が不可欠です。段取り替えを手早く実施する作業手順は属人的な暗黙知になりやすいものですが、誰もが同じ方法で実行できる形式知に転換しましょう。
また、この形式知を自工程・自部門・自社内に留まらせず、他工程・他部門・関係会社に展開することで、サプライチェーン全体での大幅な効率化が可能となります。以下の図は、トヨタグループで実施された段取り替え短縮の取り組みそのものの一例です。
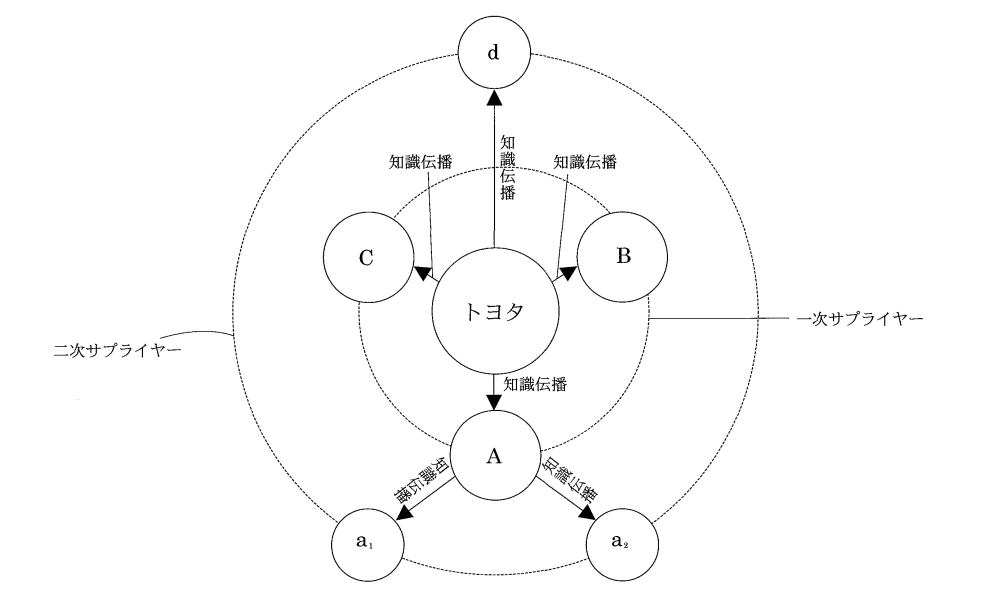
引用元:九州大学大学院経済学会『知識の共有による段取り替え時間の短縮 : トヨタグ ループを中心に 』
生産性向上・品質改善に関する検証
段取り替えを短縮するための作業手順変更では、生産性向上が期待できますが、その一方で品質リスクも伴います。
このため、段取り替えによりどの程度生産性が改善されたかを評価するだけでなく、懸念される品質リスクが最小化されているか定量的に検証する必要があります。
段取り替えの改善手法:基本編
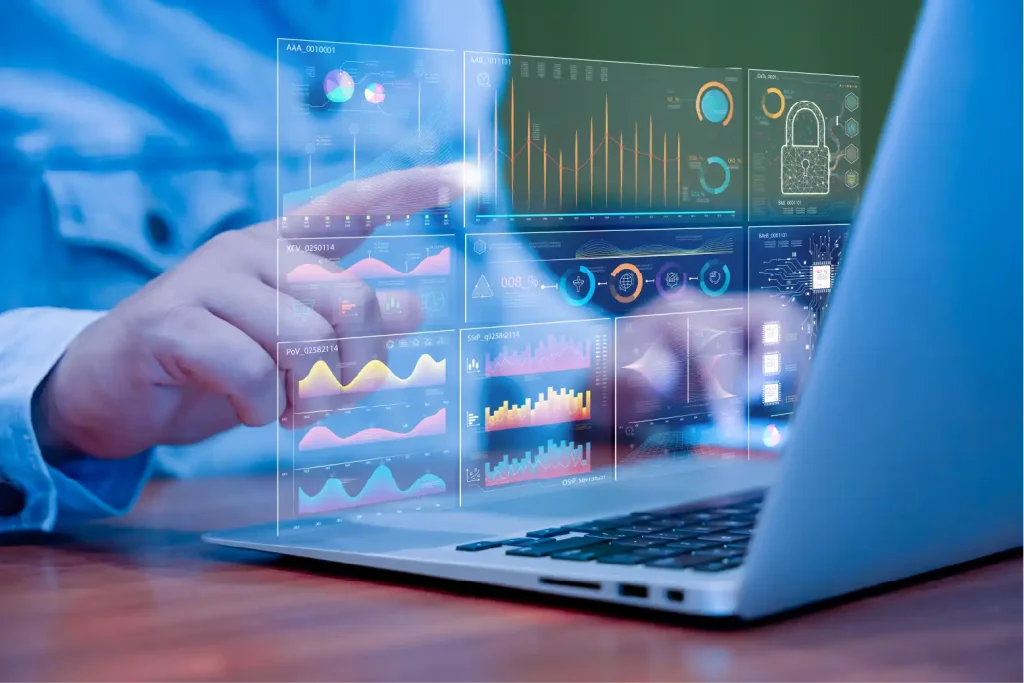
段取り替えの改善には、基本的な手法として、ムダ作業の洗い出し、作業の標準化、ポカヨケ(ミス防止)、自動化、5S活動などがあります。これらを組み合わせることで、段取り替えの効率化を目指します。
ボトルネックの把握
段取り替えの改善を進めるには、まず現在の段取り時間を正確に把握することが第一歩です。段取り替え作業の中でボトルネックとなる工程・作業を明確にすることで、生産性向上に最も効果的な改善ポイントを絞り込むことができます。
ムダ作業の洗い出し
ボトルネックとなる作業・工程を特定した後、ムダ作業の洗い出しを行います。製造現場において、ムダを徹底的に見つけるためには、トヨタ生産方式で示されている「7つのムダ」を参考にするとよいでしょう。
- 作りすぎのムダ
- 手待ちのムダ
- 運搬のムダ
- 加工そのもののムダ
- 在庫のムダ
- 動作のムダ
- 不良を作るムダ
「ムダ」と言っても様々な種類があります。このため、工程・作業を多角的に見直して小さな改善を積み上げることで、工程・作業としての大きな改善に繋げます。
標準化
作業の標準化は、「狭い意味での標準化」と「広い意味での標準化」の2つの観点から成り立っています。狭い意味での標準化は、作業手順や工程の統一を指し、作業標準書を用いて、誰が行っても同じ品質と効率で作業を行えるようにすることです。これにより、作業・工程単位での品質ばらつきを減らし、不良を作るムダを排除することができるようになります。
さらに、広い意味での標準化として、改善活動や問題解決の手法、マネジメントシステムなど、組織全体の方針やプロセスの統一があります。これにより、全従業員が共通の基準で活動し、品質と生産性の向上、リスクの低減を実現します。
ポカヨケ
段取り替え作業中の作業ミスを未然に防ぐため、ポカヨケ(単純な作業ミス防止)の仕組みを導入します。
例えば、特定の部品が誤って装着されないように専用治具を使用したり、作業順序の間違いを防ぐために工具の配置を工夫して適切な表示を設けたりする、などが挙げられます。
これにより、単純なヒューマンエラーを防ぎ、段取り替え後の品質不良や手戻りを最小限に抑えることができます。
5S活動への組み入れ
5S活動(整理、整頓、清掃、清潔、躾)の推進も、段取り時間替えの短縮に必要です。日々の業務に5S活動を組み込むことで、使用原料、工具・備品類などの整理整頓を推進することで、モノを探す作業を削減することができます。
5S活動には、使用頻度を考慮した定置管理などの施策も含めるとよいでしょう。これらを徹底することで、無駄な動作を減らすことができます。
QCサークル活動での継続改善
段取り替えの効率化は生産性や品質に大きな影響を与えます。そのため、現場の作業者が集まり、課題を話し合いながら改善するQCサークル活動として取り組むことが有効です。
QCサークル活動では、現場の作業者が日常の作業で感じる「手間がかかる」「ミスが多い」工程について意見を出し合い、段取り替えの改善点を見つけます。その知恵を活かして手間やミスの多い工程を改善し、段取り替えの改善点を見つけます。
この改善策により、段取り時間の短縮、段取り替えに伴う品質不良の低減を目指します。実際に改善策を実行する際には、想定されるリスクを十分に協議するとともに、改善策の実行前後における工数削減、品質不良の増減についても検証することが必要です。
自動化
段取り替えの一部を自動化することで、作業時間の短縮と品質の向上を図ります。自動化の導入は、段取り替えが頻繁に発生する作業や、手作業に時間がかかる工程から始めるのが効果的です。
例えば、金属やプラスチックを研削加工するための工作機械である、マシニングセンタの段取り替えについて考えます。工具の交換や治具の取り付けなど、手作業に多くの時間がかかりを短縮し、人的ミスのリスクも伴います。この段取り替えの自動化により、以下の効果が得られます。
自動化の効果 | 具体例 | 効果 |
作業時間の短縮 | ATC(自動工具交換装置) | 工具交換を数秒で実施 |
作業ミスの防止 | プログラムによる自動設定 | ヒューマンエラーの削減 |
生産効率の向上 | APC(自動パレット交換装置) | 機械の停止時間を短縮 |
例えば、ATCにより手動で10分かかっていた工具交換を数秒で行い、APCを使えば治具の取り付けも自動化できます。これにより、機械の稼働率が向上し、生産性が大幅に向上します。
段取り替えの改善手法:応用編
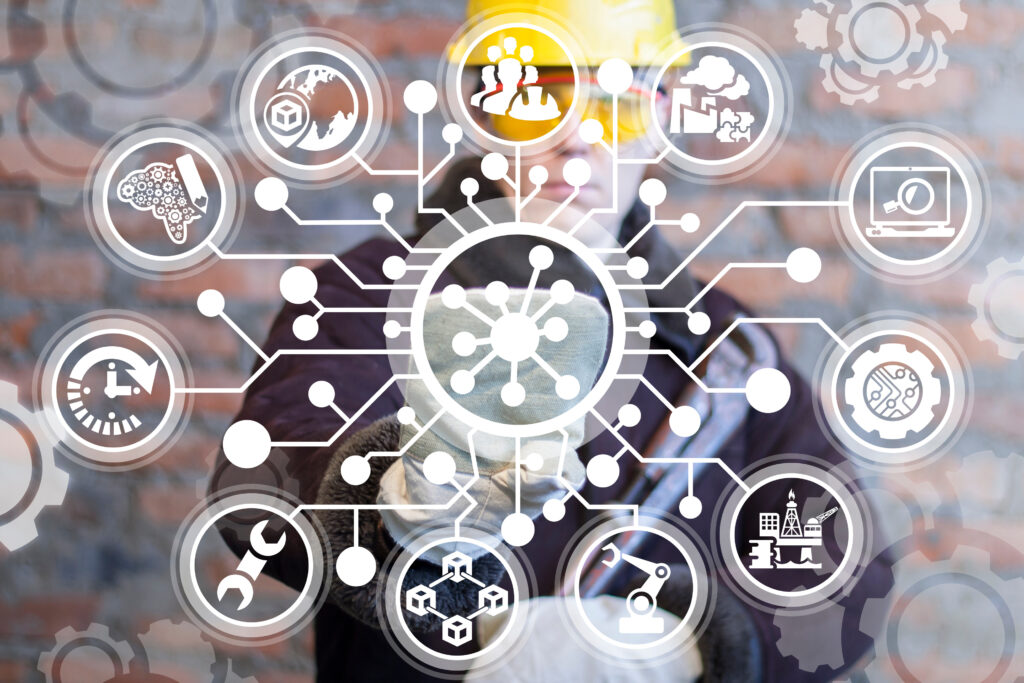
基本的な手法に加えて、応用的な改善手法を組み合わせると、より高い改善効果が期待できます。SMEDを目指した段取り替えの改善手順は次の通りです。
SMED(シングル段取り)に向けて
SMED(Single Minute Exchange of Die、シングル段取り)とは、段取り替えの時間を10分未満に短縮することを目指した手法をいいます。段取作業の単純化や工程共通化により生産の柔軟性を高め、設備の稼働率を最大化するために開発されました。
工程の単純化と共通化を進めることで、生産ラインや機械の停止時間を最小限に抑え、生産の切り替えを迅速に行うことです。これにより、以下の効果が期待できます。
- 生産リードタイム短縮:段取り替えの短縮で迅速な製品切り替えが可能
- 生産コスト削減:設備稼働率向上で機械停止時間を減少
- 小ロット生産実現:段取り替えの簡略化で少量多品種生産に対応
さらに段取り時間を短縮し、2分以内の段取り替えが完了するものを「ワンタッチ段取」とも言います。
現状分析と課題点の把握
ボトルネックとなっている工程・作業について、まず最初に現状の段取り替え作業を詳しく分析し、どこに改善の余地があるかを把握します。ビデオ撮影等によるタイムスタディを行い、各作業にどれだけの時間がかかっているかを計測します。
これにより、段取り替え作業のどの部分に無駄があり、どこを改善すべきかどこを改善すべきかが明確になります。例えば、工具の準備や設定に多くの時間を費やしている場合、そのプロセスを見直すことで改善の余地が見えてきます。
内段取りと外段取りに分類
段取り替え作業は、内段取りと外段取りに分類して考えます。
内段取り:機械を停止して行う必要のある作業(例:治具の交換や調整)
外段取り: 機械の稼働中に進められる準備作業(例:次の工具や材料の準備)
機械の稼働中に並行して実施できる作業は生産リードタイムには直結しないため、内段取りを減らす改善策が効果的です。
内段取りの外段取り化
内段取りを外段取りに変えることは段取り替え時間短縮のキーポイントであり、SMEDの最も基本的な考え方の一つです。設備の停止時間を最小限に抑えることに繋がります。
例えば、次の生産品種で必要な工具や部品の準備をあらかじめ行い、機械設備の停止中に必要な作業を減らす工夫が相当します。専用の治具スタンドや、セットアップ用のツールカートを導入することも、作業者が段取り替えをスムーズに行うために有効です。
内段取り時間の削減
内段取り時間の削減は、作業手順を簡素化し、必要最小限の動作で作業を行うことが目標です。複数作業を並行して進めたり、段取り替え専用治具の導入により調整作業を排除したりすることが効果的です。
また、治具や工具の取り付けを容易にするクイックチェンジ装置を導入することでも、段取り時間を短縮できます。さらには、設計部門と協力し、使用する工具をできるだけ共通化すると、段取り作業自体を減らせます。
外段取り時間の削減
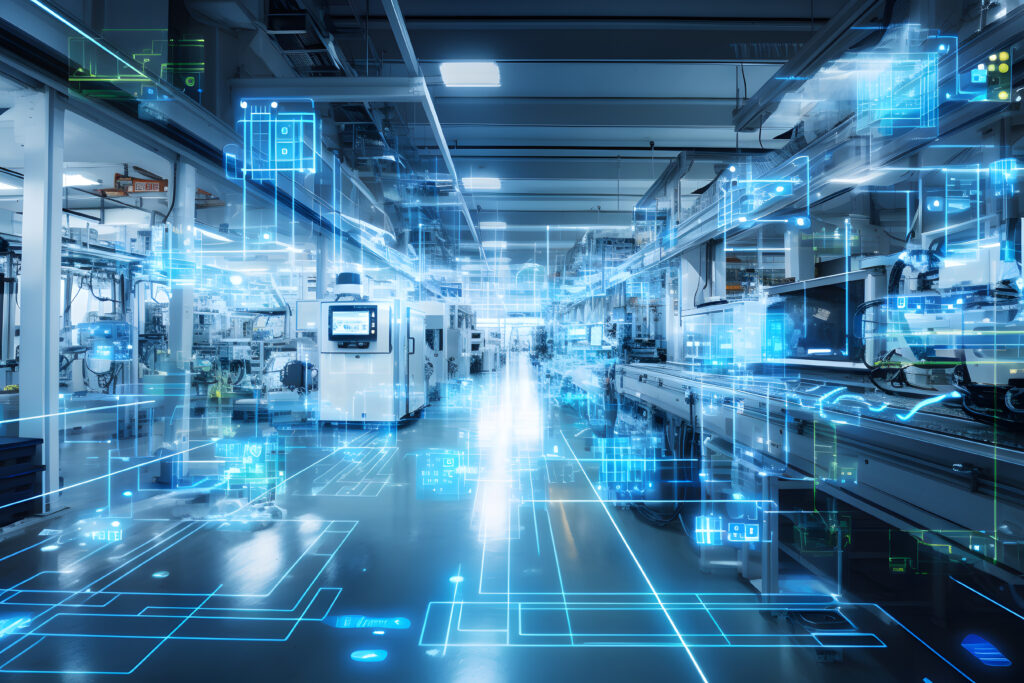
外段取りの時間を削減は、作業者の無駄な移動や準備時間の短縮により、段取り替えに必要な工数低減を目指します。
例えば、製造現場内で実行できる工夫としては、工具や材料を定位置に配置し、すぐに取り出せるように整理整頓することが効果的です。
また、事前に必要な作業手順や材料リストを確認し、必要な準備を全て終えてから段取り替えを行うことで、外段取りの時間を最小限に抑えられます。内段取りと同様に、使用するパーツ類をできるだけ共通化することで、段取りに必要な工具類の種類を減らせば、さらなる外段取り時間を削減できます。
具体的な段取り改善例
段取り替えを改善するための具体的な例として、適正な在庫管理が挙げられます。段取り替えに必要な原材料・設備保守部品の在庫管理の適正化に関する事例を紹介いたします。
保守部品の在庫管理最適化
保守部品を適正に在庫管理することは、段取り時間の短縮に繋がります。もし、重要な保守部品の欠品を起こした場合、保守部品のリードタイム分の段取り時間が延長されます。
詳細:【在庫管理システム】老朽化したシステムを刷新し、保守部品の在庫管理を最適化!
原材料在庫欠品の低減
段取り替えを迅速に行うためには、必要な原材料を適正に管理することも必要です。原材料の欠品を起こした場合、原材料がすべて納入されるまで設備を停止することになったり、品種切り替えのための段取り回数が増えたりする、等の影響が出てしまいます。
詳細:【原料在庫管理システム】毎日の原料在庫数の確認の手間を95%削減
22種類の生産管理システムをランキングで比較
初期費用相場や選び方のポイントをチェック
生産管理システムをそれぞれの特徴や初期費用相場などで比較したい場合は、「生産管理システムランキング」も是非ご覧ください。生産管理システムは、自社の製品・生産方式・企業規模などに適したものを導入しないと、得られるメリットが限定されてしまいます。事前適合性チェックや生産管理システムを選ぶ前に押さえておきたいポイントも解説していますので、製品選びの参考にしてみてください。