工場の設備管理・予備品管理の基本とは 設備保全はなぜ重要?具体的に解説
公開日:2025年02月07日
最終更新日:2025年02月07日
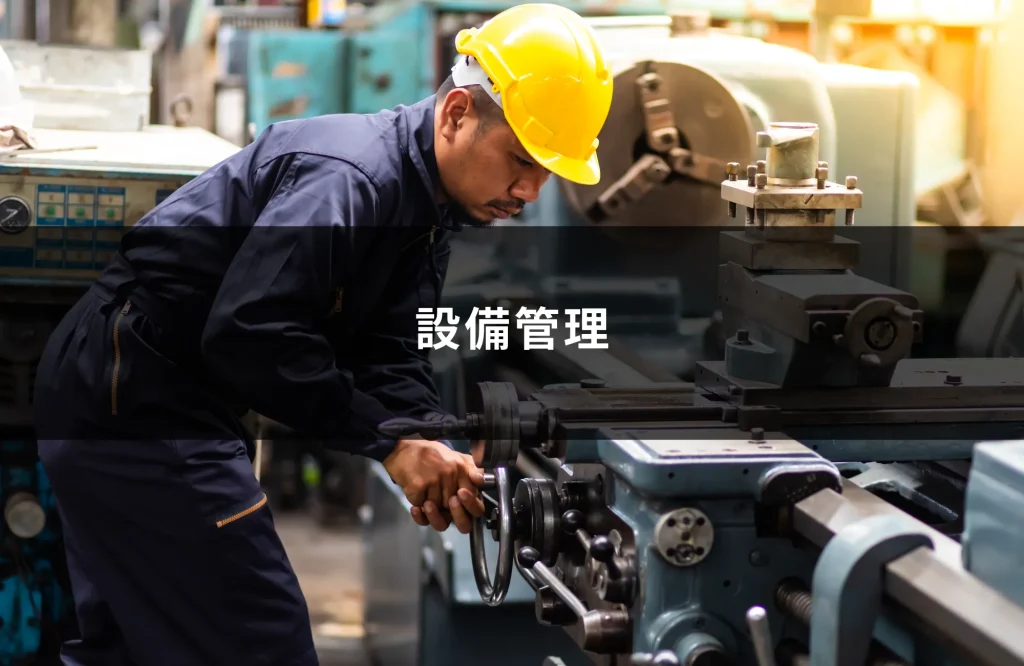
設備管理は、工場の安定稼働を支える鍵です。適切な保守・点検や予備品管理を行うことで、予期せぬトラブルを防ぎ、生産性向上やコスト削減にもつながります。
本記事では、設備管理の基本(事後保全・予防保全・予知保全の違いなど)や重要性、よくある課題から具体的な改善方法までわかりやすくご紹介。記事の後半では、設備管理を効率化する方法も具体的に解説します。工場運営の質をさらに高めるヒントにしていただけると幸いです。
工場での設備管理とは
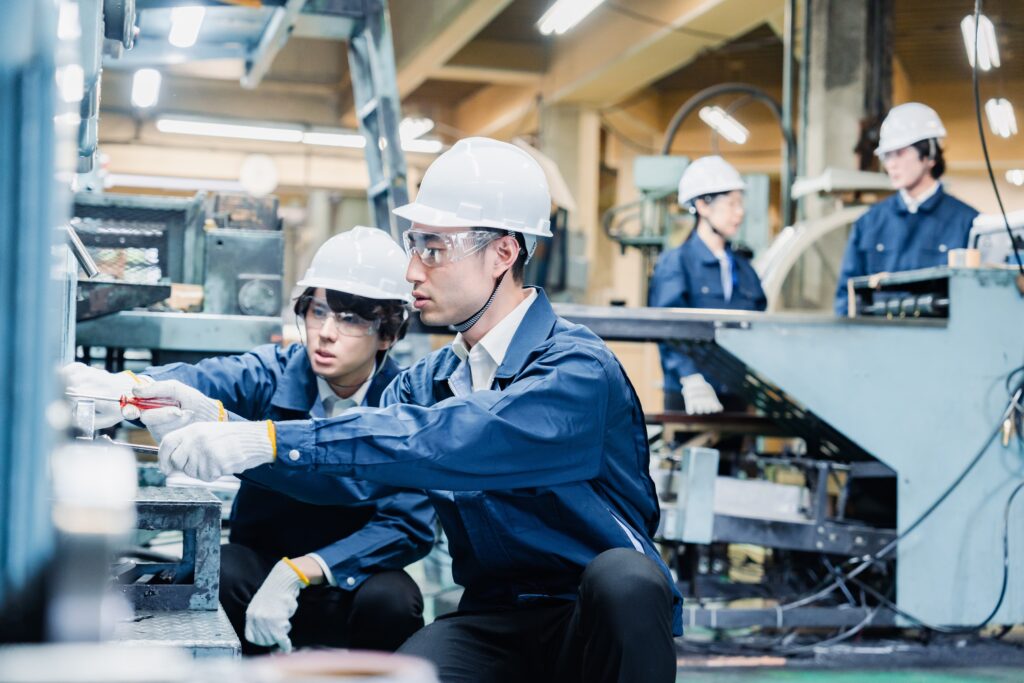
設備管理とは、工場内の機械や装置の安定した稼働を維持し、生産性や安全性を高めるための一連の活動を指します。
主な内容として、故障を防ぐための設備保全、予備品管理、設備の性能を向上させる改良保全、法定点検の実施、清掃や整理整頓(5S活動)、そしてエネルギー管理やデジタルツールを活用した効率的な管理などがあります。
本記事では、この中でも特に基本的な「設備保全」と「予備品管理」について解説していきます。
清掃や整理整頓(5S活動)はこちらの記事をお読みください。
設備管理の重要性と役割
設備管理を適切に実施することで、生産効率や品質の向上、コスト削減、安全な作業環境の確保を実現し、事業全体の効率を高める重要な役割を果たします。また、設備の故障やトラブルを防止し、遅延なく安定生産することで、企業の信頼性向上も期待できます。
生産効率と品質の向上
設備の状態は、生産効率や製品品質に大きな影響を与えます。適切な保守・管理が行われていれば、安定した生産が可能となり、業務効率化や作業工程の最適化、生産計画の柔軟性向上に繋がります。その結果、工場全体の生産性を高めることが可能です。
また、設備の不具合は製品品質にも直結します。例えば、温度や圧力の管理が重要な製造工程では、設備の精度低下により不良品が増え、リワーク(手直し)や廃棄が発生することでコストが膨らみます。さらに、品質のばらつきが増えると、顧客からの信頼を失い、企業のブランド価値にも悪影響を及ぼしかねません。
こうしたリスクを回避するためには、設備の定期点検や予防保全を徹底し、異常の兆候を早期に発見・対応することが重要です。安定した設備管理を行うことで、生産効率と品質を維持し、結果的にコスト削減と顧客満足度の向上につながります。
メンテナンスコストの削減
適切な設備管理を行うことで、設備の稼働率が向上し、メンテナンスコストの削減も期待できます。計画的な点検や保守を実施すれば、設備の劣化を抑え、長期的に安定した運用が可能になります。その結果、設備の寿命が延び、更新や修理にかかる費用の負担を軽減できます。
また、予防保全や予測的な管理手法を導入すれば、設備の異常を早期に発見し、突発的なトラブルを防げます。メンテナンス作業を計画的に進めることで、不要なコストや時間の浪費を減らし、効率的な設備運用が実現できます。その結果、業務の遅延を防ぎながら、工場全体の生産性を高めることが可能です。
設備故障の防止による安全性確保
設備の突然の故障は、生産中断によるダウンタイム(稼働停止時間)や経済的損失をもたらすだけでなく、安全性の観点からも重大なリスクを引き起こします。例えば、設備の誤作動により作業員が予期せぬ事故に巻き込まれる可能性があり、最悪の場合、人的被害や法的責任が生じることもあります。
特に、工場やプラントなどの現場では、設備の異常が火災や爆発といった深刻な二次災害につながることもあり、企業全体の安定操業を脅かします。そのため、設備の定期点検と予防保全を徹底し、リスクを最小限に抑えることが不可欠です。
このように、設備管理を徹底することは、コスト削減にとどまらず、業務効率や生産性の向上にも寄与し、企業全体の持続的な成長を支える重要な要素となります。
設備保全の種類と違い
設備保全にはいくつかの種類があり、それぞれに特徴と適用範囲があります。主要な保全手法を解説し、それらの違いを紹介します。
事後保全とは
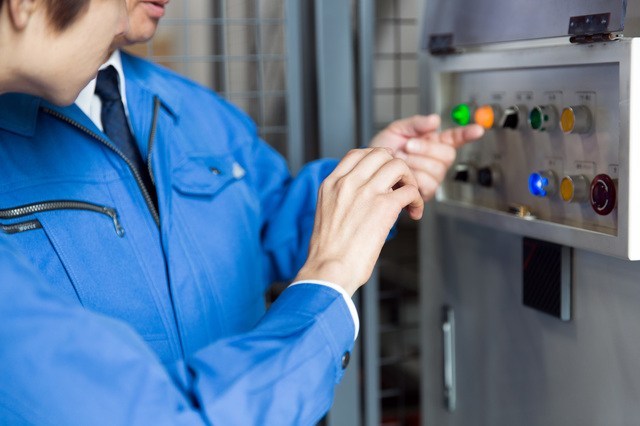
事後保全(Corrective Maintenance)は、設備が故障してから修理や交換を行う保全手法です。この方法は、設備を常に稼働させることを優先し、故障が発生した際に初めて対応するため、日常的な点検作業は必要ありません。初期コストが低い一方で、故障時の生産損失や修理費用が大きくなるリスクがあります。
事後保全のメリット
- 故障しない限り保全作業を行わないため、日常の保全コストを最小限に抑えられる
- 運用しながら状態を観察できる
事後保全のデメリット
- 突然の故障による生産停止リスクが高い
- 重大な故障の場合、修理コストが高額になる可能性がある
予防保全とは
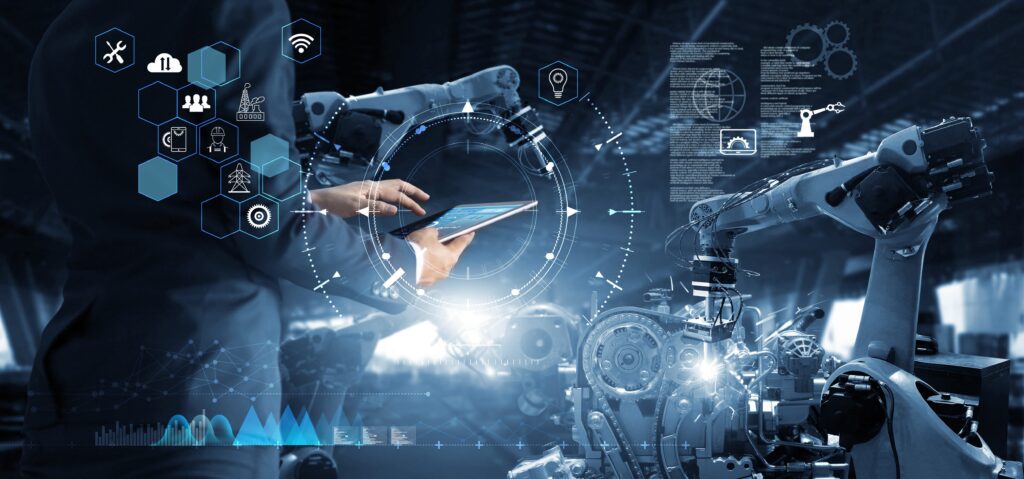
予防保全(Preventive Maintenance)は、定期的な点検やメンテナンスを行い、故障を未然に防ぐ手法です。決められたスケジュールに従って保全作業を実施するため、突然のトラブルを防ぎやすくなりますが、過剰な保全作業がコスト増加を引き起こす可能性もあります。
予防保全のメリット
- 定期的な点検やメンテナンスにより、重大な故障を防ぎ、生産ラインの停止リスクを軽減できる
- 部品交換や清掃を計画的に行うことで、設備を長期間安定して使用できる
予防保全のデメリット
- 定期点検や部品交換のための費用、人件費、設備停止による生産ロスが発生する
- 実際には問題のない部品や設備に対して、不必要な交換や点検を行うことで、コストが無駄になる場合がある
- 定期的な点検や部品交換を行っても、突発的な故障を完全に防ぐことはできないため、計画通りにいかない場合もある
予知保全とは
予知保全は、設備の稼働状態をリアルタイムで監視し、故障を予測して必要なときにだけ保全を行う手法です。これにより、最適なタイミングでの保全作業が可能となり、コスト削減と効率化が図れます。
近年はIoTやAI技術を活用し、センサーを使って設備の振動、温度、圧力などを常時監視し、異常兆候を検知するシステムが普及しています。予知保全は予防保全の次のステップとして、より効率的な保全方法として注目されています。
予知保全のメリット
- 必要なときだけ保全を行うため、メンテナンス効率が向上する
- 突然のトラブルを防ぎつつ、設備の稼働率を高く維持できる
- データを蓄積することで、長期的な設備改善に役立つ
予知保全のデメリット
- 高度な技術を要するため、初期導入コストが高くなる
- 専門的な知識を持つ人材の確保や教育が必要となる
各保全手法の比較検討
事後保全、予防保全、予知保全を比較すると、事後保全は初期費用が低いもののリスクが高く、予防保全は信頼性向上に寄与するもののコストが課題となる場合があります。一方、予知保全は初期投資が必要ですが、長期的な視点で見ると最も効率的な選択肢となります。
保全手法 | 特徴 | メリット | デメリット |
事後保全 | 故障後に修理・交換を行う | コストを抑えやすい | 突発的な故障リスクが高い |
予防保全 | 定期的に点検・交換を行う | 故障を未然に防ぎやすい | 過剰保全によるコスト増の可能性 |
予知保全 | 状態監視データから故障を予測 | 効率的な保全が可能 | 導入コストと運用の難しさ |
改良保全と設備の改善の違い
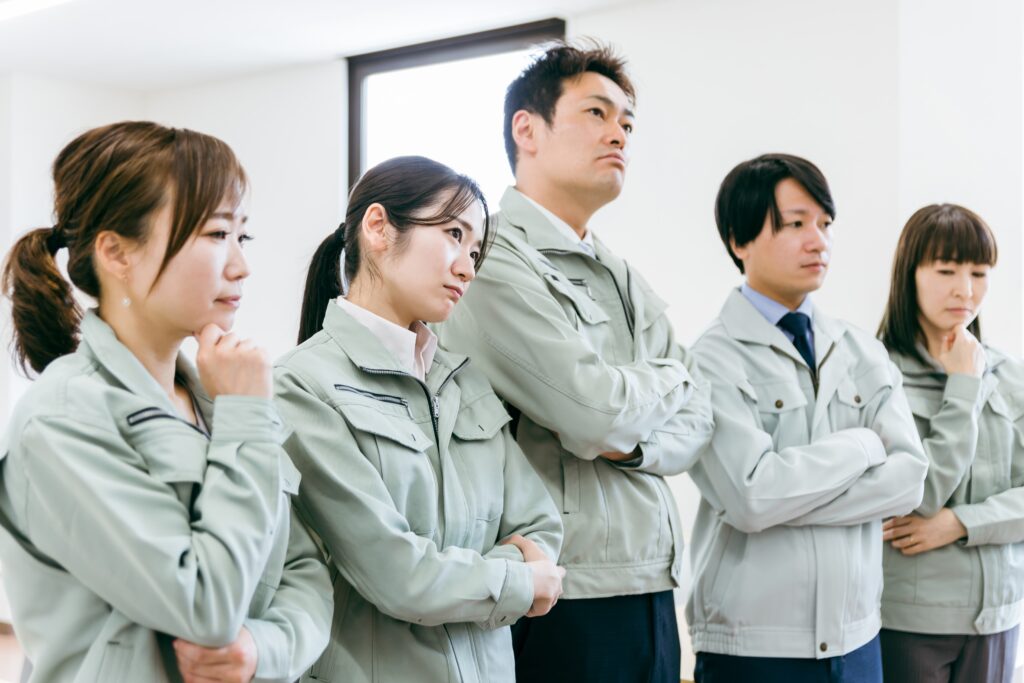
「改良保全」と「設備の改善」は似た概念ですが、厳密には異なります。「改良保全」は、「設備の改善」の一部に含まれます。
改良保全とは
改良保全(かいりょうほぜん)とは、単なる設備の修理や維持ではなく、設備の性能向上や効率化を目的とした保全活動のことを指します。故障が発生した際に単に元の状態に戻すのではなく、原因を分析し、再発防止や性能向上のための改良を施します。
改良保全の例
- 頻繁に故障する部品を耐久性の高いものに交換
- 摩耗しやすい部品の材質を変更
- 清掃や点検のしやすさを考慮した設計変更
設備の改善とは
設備の改善は、より広い意味で設備の性能向上や効率化を目指す取り組み全般を指します。改良保全は「設備の改善」の一部に含まれますが、必ずしも故障や問題が発生した後の対応ではなく、より効率的な生産や運用を実現するための積極的な改善も含まれます。
設備改善の例
- 新しい技術を導入し、生産速度を向上
- 手動作業を自動化し、省力化を実現
- エネルギー効率の良い設備に更新
予備品管理の重要性
設備の安定稼働とコスト最適化を両立するために不可欠な業務の一つが、予備品管理です。適切な予備品管理を行うことで、設備故障時の迅速な対応が可能となり、生産中断による損失を最小限に抑えられます。一方で、過剰な在庫はコスト増加を招き、不足すれば業務に支障をきたします。
予備品管理とは
予備品管理は、必要な部品や消耗品を適切に在庫として保持し、設備トラブル時に迅速に対応する仕組みです。これにより、ダウンタイムを最小限に抑えることができます。特に重要なポイントとして以下が挙げられます。
- 迅速な対応:故障時に必要な部品を即座に供給し、生産中断を最小限に抑える
- 在庫コストの最適化:過剰在庫を防ぎつつ、不足によるリスクも最小限に抑える
- 長期的視点での計画:設備の寿命や使用頻度を考慮し、将来的な部品の需要を予測する
適正在庫の確保とコスト削減
予備品の適正在庫の確保は、保管コストと生産リスクのバランスを取るうえで重要です。過剰在庫はコストを圧迫し、一方で在庫不足は生産遅延を招くため、在庫水準の適正化やデジタルツールの活用などのアプローチが求められます。
予備品の適正在庫を維持する5つのポイント
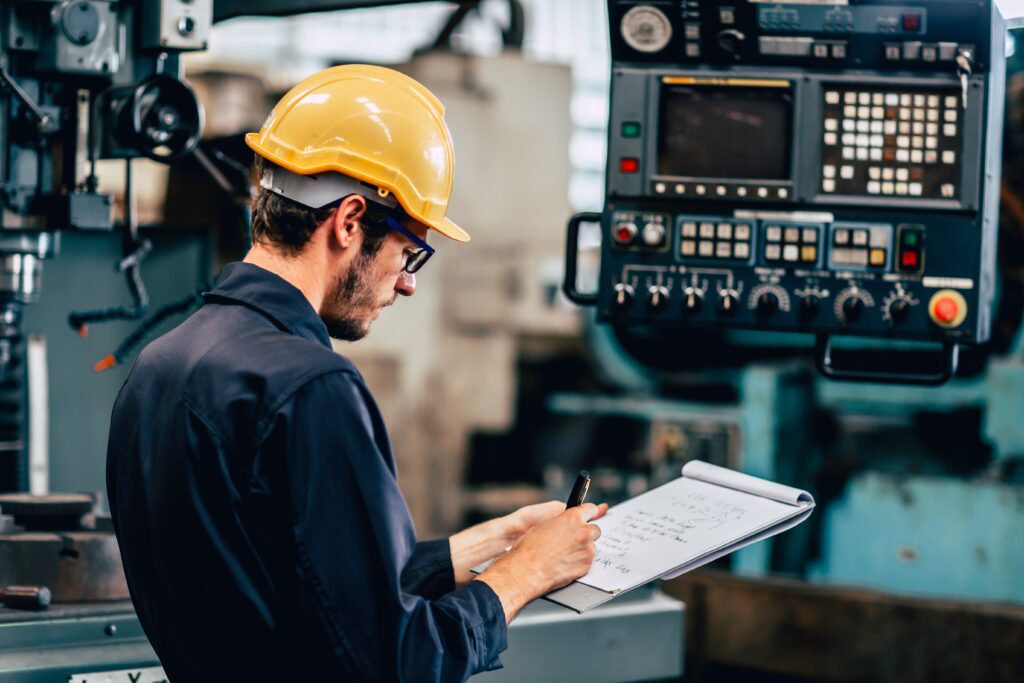
予備品や保守部品の在庫管理の最適化は、工場の設備管理における重要な課題の一つです。適正在庫を維持することで、設備のダウンタイムを最小限に抑え、コストを削減し、安定した生産体制を確保できます。
部品の重要度と使用頻度を考慮した在庫設定
すべての部品を同じように管理するのではなく、設備の稼働に不可欠な部品や使用頻度の高い部品を重点的に在庫管理することが重要です。そのために、設備の稼働状況に応じて、予備品を重要度・使用頻度で分類して管理します。
特に、設備が停止すると生産に大きな影響を与える「クリティカルパーツ」は、常に一定量を確保し、迅速に交換できる体制を整える必要があります。
例えば、故障時の影響が大きく、頻繁に交換が必要な部品は十分な在庫を確保します。一方、影響が少なく使用頻度が低い部品については、必要最低限の在庫に抑えることで、効率的な管理が可能となります。
また、設備のメーカー推奨の交換サイクルを参考にしながら、過去の交換履歴や故障発生率を分析し、在庫量を最適化することも有効です。これにより、必要な部品が不足することなく、かつ過剰な在庫を抱えないバランスの取れた在庫管理が実現できます。
消費データを基にした需要予測
過去の使用履歴を分析し、どの時期にどの部品がどれくらい消費されるのかを予測すると、より合理的な在庫管理を行うことができます。
例えば、設備の稼働率が高まる繁忙期には、特定の部品の消費量が増加することが予測されるため、それに合わせた在庫調整が求められます。
消費データを活用することで、在庫の適正化だけでなく、不要な在庫の削減にも繋がります。使用頻度が低いにもかかわらず大量に保管されている部品があれば、在庫削減の対象とすることで、倉庫スペースの有効活用やコスト削減が可能になります。
また、設備の稼働状況や生産計画と連動させることで、さらに精度の高い需要予測が可能になります。定期的なメンテナンス時期や設備の老朽化状況を考慮し、交換が必要になる部品を事前に手配することで、スムーズな運用が実現できます。
リードタイムを考慮した発注計画
適正在庫を維持するためには、供給業者ごとの納品リードタイムを把握し、計画的な発注を行うことが不可欠です。特に、納品までに時間がかかる海外調達品や特注品については、安全在庫を多めに確保しておく必要があります。
一方で、短期間で補充可能な部品については、過剰な在庫を持たず、必要に応じて発注することで無駄なコストを削減できます。
発注方式としては、一定の在庫量を下回った時点で自動的に補充する「定量発注方式」や、決められた期間ごとにまとめて発注する「定期発注方式」があります。設備の使用状況に応じて最適な方法を選択することが重要です。
また、サプライヤーとの緊密な連携を図ることで、より柔軟な発注管理が可能になります。例えば、供給業者の在庫状況を事前に把握し、納品の遅れが発生するリスクがある場合は、早めに調整を行うことで、欠品を防ぐことができます。欠品や遅延のリスクがある部品に関しては、複数のサプライヤーと契約を結び、調達先を分散する方法も効果的です。一社依存によるリスク軽減に有効です。
緊急時対応の仕組みを整備
突発的な設備トラブルや部品の急な需要増加に対応するため、緊急時の在庫確保と供給体制を整備することが重要です。クリティカルパーツについては、通常在庫とは別に緊急用のストックを確保し、必要な際に即時対応できる体制を構築する必要があります。
また、サプライヤーとの連携を強化し、緊急時に迅速に部品を供給できる契約を事前に締結することも有効です。例えば、緊急時には優先的に部品を提供してもらえる契約を結ぶことで、迅速な調達が可能になります。
さらに、部品の共通化を進め、複数の設備で使用できる部品を統一する方法もあります。個別の部品ごとの在庫を減らしながら、リスクを分散することができます。例えば、類似した設備で使用するネジやベルトなどの消耗品を標準化(共通化)することで、在庫管理の手間を削減しつつ、調達の柔軟性を高めることが可能です。
デジタル技術の活用
デジタル技術を活用し、リアルタイムでの在庫監視を行うことも効果的です。IoTを活用すると現場の保守部品在庫をリアルタイムに見える化でき、在庫不足が発生しそうな場合には、即座にアラートを発する仕組みを導入できます。
IoT活用の具体例としては、在庫数を把握するセンサーや、QRコードやバーコードを活用したハンディ端末などがあります。
設備管理の主な手順
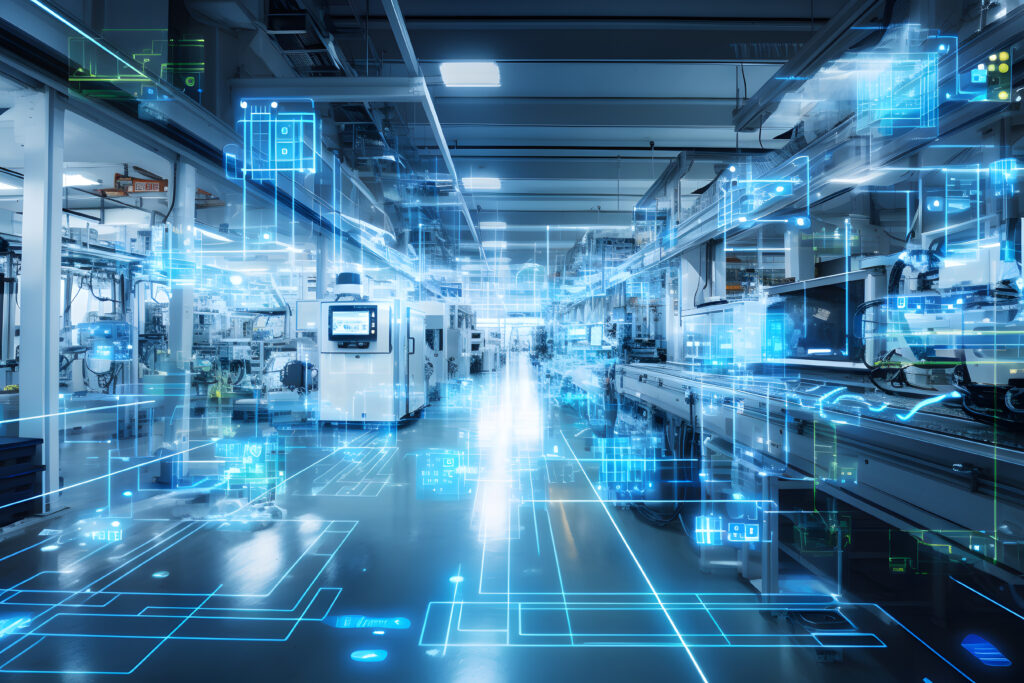
設備管理は、現状分析から目標設定、点検、記録、改善活動までの一連のプロセスを含みます。ここでは、具体的な手順を5つの順番で説明します。
現状分析と目標設定
まず、設備の現在の状態を正確に把握し、最適な稼働状態を定義することが重要です。そのために、稼働率や故障履歴を確認し、データを収集して主要な問題点を特定します。これに基づき、稼働率の向上やメンテナンスコストの削減といった具体的な目標を設定します。
点検計画の策定
計画的な点検スケジュールを設定することで、トラブルを未然に防ぎます。設備の使用頻度や環境条件を考慮し、適切な点検間隔を決定します。また、必要な点検項目や使用するツールを事前に明確化すると、作業効率を高めることができます。
点検・保全作業の実施
点検作業を円滑に進めるためには、標準的な手順を整備し、書類として明文化しておくことが重要です。作業前には安全対策を徹底し、点検中に問題箇所を特定した場合は迅速に対応します。
記録と分析
点検や修理の内容を記録し、設備の状態を可視化することで、管理精度を向上させます。メンテナンス管理システム(CMMS)を導入すれば、履歴のデータベース化やグラフによる可視化が容易になります。
稼働率や故障頻度のデータを分析し、改善点を抽出することが次のステップにつながります。
改善活動とPDCAサイクルの実施
継続的な改善を行うことで、設備管理の精度を高めます。そのために、計画(Plan)→ 実行(Do)→ 検証(Check)→ 改善(Act) のPDCAサイクルを繰り返し、運用効率を向上させます。
また、作業員や関連部門からのフィードバックを積極的に取り入れ、管理手法のさらなる向上を図ります。
PDCAサイクルの詳細についてはこちらの記事をお読みください。
設備管理で直面する主な課題と解決策
設備管理にはさまざまな課題があり、それぞれが生産性や運営コストに影響を与えます。ここでは、代表的な課題とその解決策について説明します。
人的リソースの不足
設備管理を担う技術者の不足は、多くの企業で共通する課題です。特に熟練技術者が退職すると、知識や経験の継承が難しくなります。少子高齢化の影響もあり、人手不足の問題は今後さらに深刻化することが予想されます。
解決策として、従業員向けの定期的なトレーニングや教育プログラムを実施し、スキル向上を図ることが有効です。また、外部の専門業者に一部の業務を委託することで負担を軽減し、CMMSやIoT技術を活用して作業効率を向上させるのも有効な手段です。
老朽化した設備への対応
設備の老朽化は故障頻度の増加や維持費の上昇だけでなく、生産効率の低下にもつながります。
対応策として、老朽化の進行状況を定期的に把握し、計画的な更新を行うことが重要です。
また、修繕や予防保全の頻度を最適化し、老朽化設備の寿命を延ばすことも可能です。場合によっては、レンタル機器や中古設備の活用も一つの選択肢になります。
コスト管理の難しさ
設備管理では、点検・保全費用、予備品コスト、ダウンタイムによる損失など、さまざまなコスト要因が発生します。そのため、コスト管理が煩雑になりがちです。
解決策として、年間の保全費用や設備更新費用を事前に見積もり、計画的に管理することが重要です。
また、在庫管理システムを活用して在庫や消耗品の使用を追跡し、無駄を削減するのも有効な方法です。長期的な視点で投資を行い、初期コストが高くても将来的にコスト削減が見込める設備を導入することも検討すべきでしょう。
情報の一元管理の必要性
設備管理の情報が分散していると、問題発生時の対応が遅れるだけでなく、データ活用も難しくなります。特に、紙やエクセルによる設備保全や予備品管理を行っている工場では、管理が属人的になりやすいと言えます。
この課題を解決するためには、メンテナンス管理システム(CMMS)やERPシステムを導入し、情報を一元管理することが有効です。さらに、各部署間でリアルタイムにデータを共有できる環境を整えることで、迅速な対応が可能になります。
すぐにシステム化が難しい場合は、ネットワーク上に共有ファイルを作成し、管理することから始めてもいいでしょう。
まとめ:設備管理業務を効率化するには
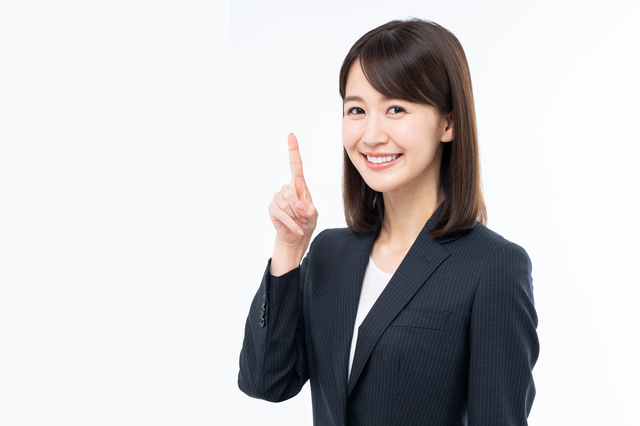
設備管理の負担を軽減し、より高い生産性を実現するためには、業務の効率化が不可欠です。
作業フローの見直し
現状の作業フローを検証し、無駄なステップを削減することで業務の効率を向上させます。具体的には、5S活動(整理・整頓・清掃・清潔・しつけ)やLEAN手法を導入することで、作業時間の短縮と精度の向上が期待できます。
LEAN手法とは、過剰生産、待ち時間、在庫の滞留、不要な動作や検査などのムダを削減しながら効率的な生産や業務運営を実現する管理手法です。
コミュニケーションの強化
現場と管理部門、技術者間の情報伝達をスムーズにすることも業務効率化には欠かせません。デジタルチャットツールやクラウドベースの情報共有プラットフォームを活用することで、トラブル時の迅速な対応が可能になります。
教育とスキル向上
技術者のスキル向上に向けて、技術に関する研修や故障解析スキルの強化を実施し、知識の標準化と作業品質の均一化を図ります。ポリテクセンターなどの外部の教育機関での研修も有効です。
アウトソーシングの活用
専門業者に一部の設備管理業務を委託することで、社内リソースをより戦略的な業務に集中させることが可能になります。ただし、委託業者の選定は慎重に行い、品質やコストを十分に検討する必要があります。
システムや自動化技術の活用
センサーやIoT関連の製品を導入し、設備の状態をリアルタイムで監視することで、異常発生時に即座にアラートを発信する仕組みを構築できます。例えば、温度や振動センサーを活用すれば、トラブルを未然に防ぐことが可能です。
また、設備管理システムの導入で管理のミスや工数を削減することも効果的です。
参考:設備管理システム16選!機能や特徴、導入メリット、選び方をまとめて紹介
22種類の生産管理システムをランキングで比較
初期費用相場や選び方のポイントをチェック
生産管理システムをそれぞれの特徴や初期費用相場などで比較したい場合は、「生産管理システムランキング」も是非ご覧ください。生産管理システムは、自社の製品・生産方式・企業規模などに適したものを導入しないと、得られるメリットが限定されてしまいます。事前適合性チェックや生産管理システムを選ぶ前に押さえておきたいポイントも解説していますので、製品選びの参考にしてみてください。