工場の機械トラブルに悩まされないために|トラブル対策の2つのポイント
公開日:2020年03月03日
最終更新日:2025年07月22日
工場の製造担当者から責任者まで、製造業に携わる全ての人を悩ませる問題に、工場の機械トラブルが挙げられます。
工場の機械トラブルは、工場で発生するトラブルの中で一番頻繁に起こるといわれており、製造スケジュールやコストの増加、製造機会損失の面でも、企業に大きな打撃を与えます。
頻繁な機械トラブルによる損失を抑えるためにはトラブル対策のポイントを押さえ、オペレーションの中に組み込むことが重要です。
今回は、工場の機械トラブルに悩まされている製造業者のために、実際にあった事例なども紹介しながら、機械トラブル対策のポイントをお伝えします。
工場で発生する機械トラブルの5つの原因
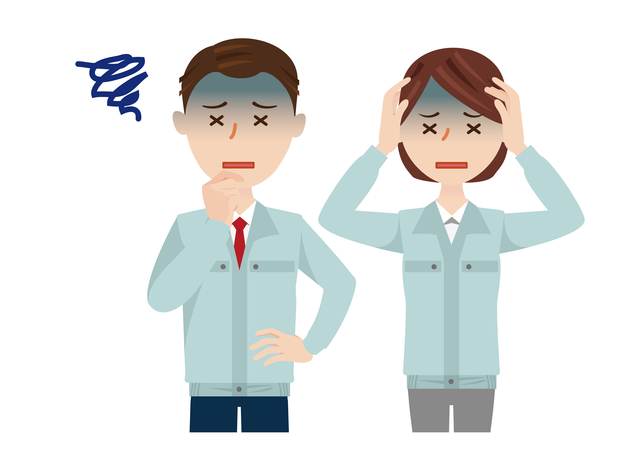
製造業の工場では、業種によって膨大な種類の機械設備があり、一言に機械のトラブルといっても発生する箇所はそれぞれ違いがあります。
ただ、トラブルが発生する原因は共通しているものが多く、軽微なトラブルから工場ライン全体を長時間停止せざるをえない深刻なトラブルまであります。
<工場で発生する一般的な機械トラブルの原因>
- 汚れや詰まりなどによる機械エラー
- 機械の設定や段取り替えのミス
- ワークの配置ミスやワーク不良
- 機械部品の老朽化・消耗によるトラブル
- 機械の故障
1~3の機械トラブルの原因は、中でも頻繁に起こるトラブルですが軽微なため、一部の機械の再起動や、設定の変更、清掃によりすぐに復旧することができます。
しかし、4~5の原因は、工場ラインの運転を長時間停止する必要があるなど比較的大きめなトラブルをもたらし、発生する損失もより深刻になる可能性があるので注意が必要です。
特に、4.部品の老朽化や消耗によるトラブルは、5.機械の故障にもつながるケースが多いので、一番注意して対策したいトラブルの原因となります。
機械の老朽化や消耗によって発生するトラブル例
実際の部品老朽化や消耗によるトラブルは、下記のような例があります。
- 消耗によるベアリングなどパーツの破損
- 粉砕機や切断機械などの羽根・刃部分の摩耗
- ベルト類の消耗
- バグハウスなどフィルター関係の詰まり など
機械のトラブルは、圧力や温度の上昇、回転数の低下などの異常をセンサーが感知したり、工場のオペレーターが各数値の変化により気づくことで発覚します。
実際に、大きめのトラブルが発生してしまうと、工程によっては不良品を発生させないよう一時的にしのぐことはできたとしても、根本的な解決を図るために、ある一定の時間、工場の運転を停止せざるをえません。
ここからは、機械トラブルの中でも、特に、工場の運転を一定時間停止せざるをえないトラブルによって発生する損失や、さらに深刻な損失を防ぐための対策についてお話しします。
機械トラブルによって発生する損失とは
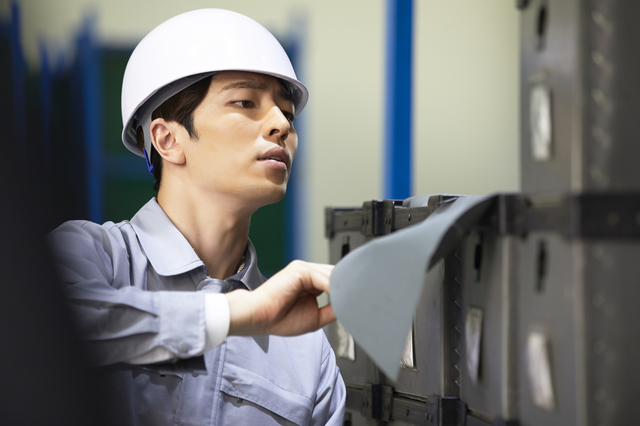
一定時間工場の運転を停止せざるをえない機械トラブルが発生すると、どのような損失が生まれてしまうのでしょうか?
機械トラブルによって、工場のラインが停止している時間には下記の損失が発生します。
- 製造時間のロスによる機会損失(停止時間に製品製造ができないことによる損失)
- 人件費のムダ
- 不良品の発生
機械トラブルが発生することにより、製品が製造できないことに加え、復旧までの作業者の人件費がムダとなったり、不良品の発生などの損失が発生したりと、トラブルがあればあるほど工場は製造原価や管理費を上昇させてしまうことになります。
機械トラブルを深刻にする原因とは
機械トラブルによる損失をさらに深刻にしてしまう原因は、機械トラブルの事後対応にあります。
機械トラブルの事後対応が長引けば長引くほど、工場ラインの停止時間は長くなり、損失も比例して拡大します。
機械トラブル時の事後対応でよくある問題点
工場ラインを一定時間停止させる必要のある機械トラブルが発生した場合、下記の通り復旧作業が発生します。
- 緊急停止作業
- トラブルの原因究明
- 原因報告とトラブルを取り除く作業
- 不良品を取り除くための空運転
- 正常な製品ができるまでの立ち上げ運転
この事後対応を長引かせるケースに、トラブルが起きた際、長年勤めているメンテナンス担当者や製造作業者が不在である場合があります。
通常トラブルが起きた際は、熟練の担当者の経験から、トラブルの原因特定や解決が行われており、その担当者が退職した際や休暇を取っていた際にトラブルが発生し、原因究明に時間がかかり深刻なライン停止が起こってしまうというものです。
この時、対応策の手順を確認するためのマニュアルや、過去のトラブル情報がきちんと保管されておらず、それを探すのに時間がかかってしまうという問題もあります。
機械トラブルによる損失を深刻にするのは情報の共有不足
このように、機械トラブルで復旧までに時間がかかってしまい、損失を深刻なものにしてしまうのは、緊急停止作業から問題解決までの情報が誰でもわかるように蓄積されていなかったり、蓄積された情報をすぐに見つけられなかったりする、情報の共有不足が大きな原因です。
また、必要なパーツがすぐに見つからないなど、設備保全に対する管理自体が十分でないことも要因として挙げられます。
機械トラブルによる時間ロスが、まだ工場内だけの損失であればいいですが、急ぎの製造時にトラブルが起きてしまった場合に復旧が遅れると、納期を守れず取引先を失うことにもなりかねないので、しっかりと対策することが必要です。
トラブル対策のポイントとは
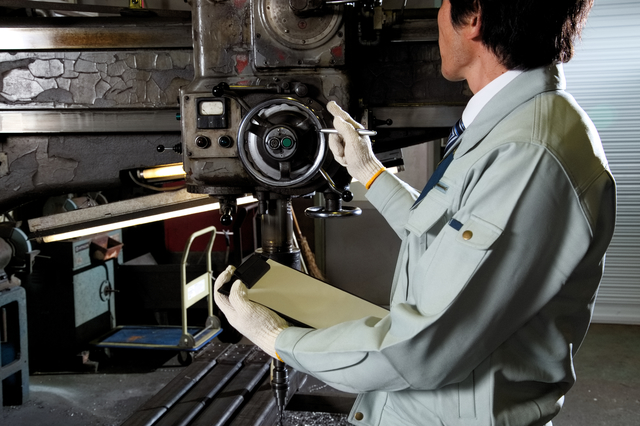
以上のような損失を発生させる機械トラブルを対策するポイントは、下記の通りです。
- 機械トラブル発生の回数を減らすこと
- 機械トラブル事後の対応をスムーズにすること
それぞれ見てみましょう。
機械トラブル発生の回数を減らすこと
大きめの機械トラブルで大半の原因となる機械の消耗によるトラブルは、適切な定期点検を実施することで、発生する回数を減らすことができます。
適切な定期点検を実施するためには、過去に実際発生したトラブルの頻度やトラブル時の現象を分析し、自社で適切な定期点検の時期と実施内容を決めなければなりません。
過去データの分析によって、どれくらいの頻度で点検を実施する必要があり、どのような点検・補修作業を行ったらいいのか判断することができ、点検により機械トラブルが発生する前に防ぐことができます。
機械トラブル事後の対応をスムーズにすること
機械トラブルの発生件数を抑えることができたとしても、100%トラブルを事前に防げるとは限りません。
機械トラブルが発生した事後の対応をスムーズにすることで、トラブルが発生したとしても深刻な損失を防ぐことができます。
なお、事後対応をスムーズにするためには、事後対応時に必要な作業マニュアルや同様のトラブル内容が誰でもすぐにわかる状態にしておくことが重要でしょう。
しかし、事後対応フローでも見てきたとおり、機械トラブルへの対応は対応者のノウハウ頼りになっているケースが多く、紙でトラブルの報告書が作成されている場合も、同様のトラブルがいつ起こったのかわかりにくく、すぐに確認することができない工場がほとんどです。
近年は、こういった機械トラブルを減少させ、事後スムーズに対応策がとれるよう、トラブル情報の蓄積・簡単な情報アクセスができる設備保全システムが、パッケージで安価に購入できるようになりました。
設備保全システムを活用することで、適切な点検の実施からトラブルの対応、パーツの保管管理まで、機械トラブルを防ぐための一連の保全作業を多方面から効率的にしてくれます。
どのように役立つのか具体的に想像していただくため、実際に、設備保全システムを活用した例を次で紹介します。
設備保全システムを活用して機械トラブルが1/2になった事例
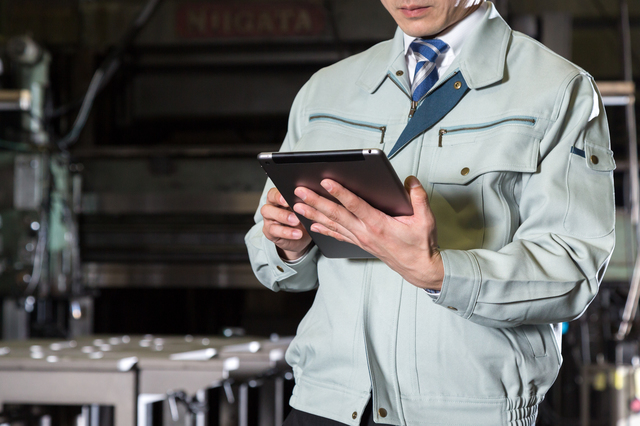
ある自動車部品メーカーでは、工場の機械トラブルが発生した際、トラブルの記録報告書を手書き作成しファイリングして管理していました。
ところが、頻繁に作業者による記入漏れが発生し、管理者がすべての過去のトラブルを把握できない状態になっており、トラブル対応にも時間がかかっていました。
そこで、スマホ端末とセンサーによる設備管理システムを導入し、過去のトラブルが把握できる状態を目指しはじめました。導入の際は、予め予想されるトラブルをシステムに登録しておき、該当する箇所のセンサーに稼働信号の受信機を設置しておきます。
これによりトラブルが起きると、あらかじめ設定しおいた担当者へ通知が発信され、すぐにトラブルに対して対応できるようになりました。
また、同じ箇所で前回発生した際のトラブル対応の内容を確認でき、修繕作業に必要な情報がすぐにわかるようになり、その際に必要なパーツについても画面上で確認できるため、事後対応の時間が大幅に削減されました。
その結果、設備保全システムを導入してからというもの、トラブルの原因特定がしやすくなり、事後対応の作業効率も大幅にアップしました。また、過去のデータから、点検箇所や頻度を見直すことで、トラブルは導入前の1/2まで減少し、生産性の向上につながったのです。
工場の機械トラブルを減らして生産性を向上させよう
工場の機械トラブルを減らすためには、人材に蓄積されたノウハウだよりでトラブルを解消するのではなく、トラブルの情報をシステムに蓄積し、トラブルが起きた際に、必要な情報へ即時アクセスできる体制をととのえることが重要です。
当社ネクスタも他社保全システムと比較すると、非常に安価なパッケージでの設備保全システムを提供しています。効果があるか不安という方のために、トライアル導入も用意しております。機械トラブルでお困りの方は、ぜひ一度ネクスタまでご相談ください。
22種類の生産管理システムをランキングで比較
初期費用相場や選び方のポイントをチェック
生産管理システムをそれぞれの特徴や初期費用相場などで比較したい場合は、「生産管理システムランキング」も是非ご覧ください。生産管理システムは、自社の製品・生産方式・企業規模などに適したものを導入しないと、得られるメリットが限定されてしまいます。事前適合性チェックや生産管理システムを選ぶ前に押さえておきたいポイントも解説していますので、製品選びの参考にしてみてください。