予知保全とは?予防保全や予兆保全との違い、メリットを解説<導入事例付>
公開日:2020年03月03日
最終更新日:2025年03月25日
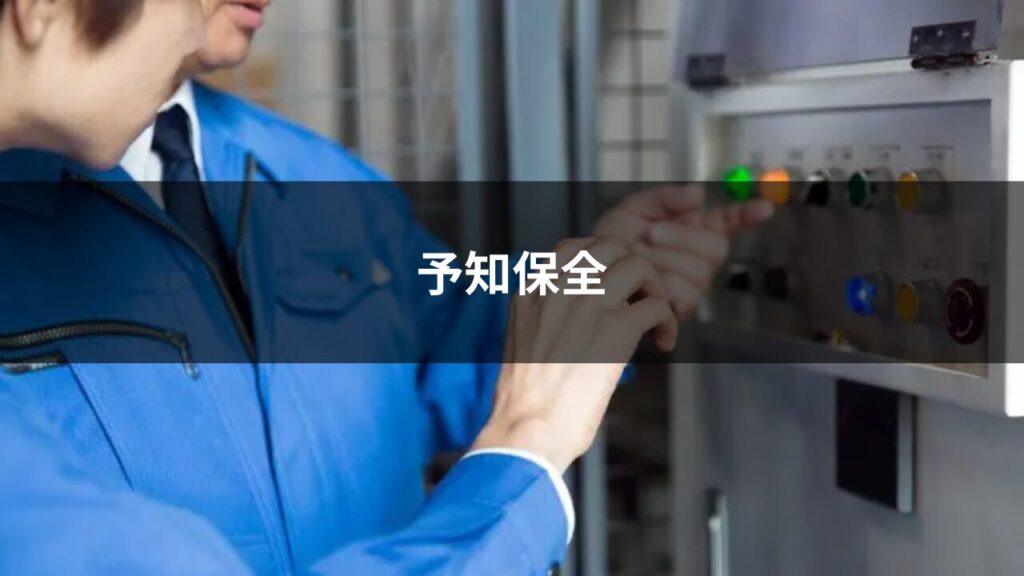
設備の突発的な故障を防ぎ、メンテナンスの効率を向上させる「予知保全」。従来の予防保全との違いを理解し、導入のメリット・デメリットを把握することが重要です。
本記事では、予知保全の基本や仕組み、予兆保全や予防保全との違いから、IoTやAIを活用した最新技術、導入事例まで解説します。現場での活用方法や導入の判断基準を知り、自社の生産性向上につなげましょう。
予知保全とは
予知保全(Predictive Maintenance)とは、設備の状態を常に監視し、故障履歴や運転データを分析、トラブルが発生する前の適切なタイミングで設備点検や部品交換を行う保全手法です。よりシンプルに言えば、「故障を予測し、壊れる前に対処する」ことが予知保全の本質といえます。
例:モーターの微細な異音や設備の異常な振動をリアルタイムで検出
予知保全では、設備と保全システムを繋ぐIoT技術や、AIによる分析技術などを活用します。そのため、予知保全を行うには、スマートファクトリーの実現が鍵となります。
予知保全が必要な理由:人手不足・属人化の解消
近年、予知保全の重要性が高まってきている背景には、設備保全担当者の人手不足の問題があります。予知保全ができると、保全経験が浅い担当者でも、設備のダウンタイム削減やコスト最適化が実現しやすくなるためです。
これまで熟練の保全担当者は、設備のわずかな異音や振動を経験的に察知し、早めの保全作業を行うことでダウンタイムを最小限に抑えてきました。しかし、経験則や感覚に頼る保全は属人化しやすく、誰もが再現できるわけではありません。ベテラン担当者が退職すると、十分な設備保全ができなくなるリスクがあります。
そこで、IoTやAIの技術を活用したデータ分析により、より客観的かつ高度な予知保全・予兆保全を行えるようになると、誰でも「先回りした保全」を実施できる環境が整います。今後も製造業の人材不足は進行することから、予知保全の重要性は高まっているといえます。
IoTに関する情報を確認されたい方は、「工場IoT化をするときの具体的な導入方法」や「工場をIoT化するメリット」の記事をお読みください。
予兆保全との違い
予知保全とよく比較される設備保全方法に、予兆保全(PdM: Predictive Maintenance)があります。
予兆保全とは、異常の兆候を検出し、統計的な予測を行うことで最適なメンテナンスを実施する手法です。IoTやAIを活用し、設備に設置されているセンサーで取得したデータを基に、異常が起きやすい兆候を発見します。
一方、予知保全は、故障履歴や状態監視データをもとに「故障が発生しそうなタイミング」を推定し、計画的に点検や交換を行う手法です。
近年では、IoT 技術の発展により、予知保全と予兆保全の境界は曖昧になりつつあります。多くの企業が、予兆保全を活用した高度な予知保全を取り入れています。
予防保全との違い
予防保全(Preventive Maintenance)も、予知保全と混同されやすい保全方法です。予防保全と予知保全の最も大きな違いは、状態把握によるダウンタイムの削減効果の度合いです。
予防保全(Preventive Maintenance)は時間基準保全(Time Based Maintenance)ともいい、、おおよその周期を決め、定期的にメンテナンスを行う保全方法です。たとえば、「半年ごとにオイル交換をする」といった計画的な保全が該当します。点検や交換のタイミングによっては突発的な故障を防ぎきれず、ダウンタイムが大きくなることもあります。
対して、予知保全は設備の状態を常に監視し、劣化状態や異常動作を把握することで、状態に合わせた最適なメンテナンスを行う保全方法です。状態基準保全(Condition Based Maintenance)とも呼びます。異常の兆候を捉えることで 修理箇所を明確に特定でき、ダウンタイムを最小限に抑えることが可能です。
■予知保全と予防保全の比較
予知保全 | 予防保全 | |
---|---|---|
導入コスト | 有り | 無し |
故障リスク | 低い | 中程度 |
ダウンタイム | 少い | 少~大 |
予知保全は、導入コストがかかるものの、センサーやデータ分析によって設備の状態を常に把握できるため、急な故障リスクを大幅に低減できます。
一方、予防保全は、定期的な点検や部品交換を計画的に実施することで設備の故障を防ぐ手法です。導入コストは低いですが、部品の摩耗具合に関係なく交換するため、まだ使える部品を早めに交換する可能性があります。
近年では、予防保全と予知保全を組み合わせ、コストと故障リスクのバランスを取りながら、より効果的な保全戦略を立てる企業が増えています。
予防保全に関して、詳細を知りたい方は 「予防保全とは?QMS規格との関連、予防保全の基本的考え方から具体例まで解説」 をお読みください。
予知保全が現場にもたらす4つのメリット
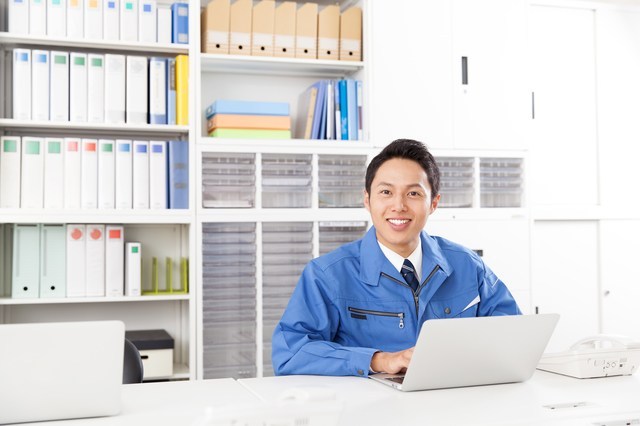
予知保全を実施し、設備の異常を事前に検知して適切な対応を行うメリットは、主に4点あります。いずれも、コスト削減・生産性向上・人材不足対策など、多くの企業が抱える課題の解決に繋がります。
設備の部品交換頻度が適切になる
予知保全が行えるようになると、最適なタイミングで部品の交換が可能になり、無駄な部品コストがかからなくなります。
予防保全では、一定の周期で部品交換を行うため、本来まだ使用できる部品でも交換することがあり、無駄が発生します。対して予知保全では、異常を感知した際に部品を交換します。「まだ使えるかもしれないが、設備トラブルを防ぐために交換する」という予防保全が不要になり、部品寿命を最大限に活用できるようになります。
保全の工数を削減できる
予知保全では、必要以上に保全担当者を配置する必要がないため、設備保全の工数削減が可能です。
また、設備管理の人手不足に悩む企業では、人手不足解消の効果も期待できます。保全業務には高度な知見やスキルが求められる一方、近年の少子高齢化の影響で人材不足が深刻化しています。予知保全を導入すると、常に最低限の人数で設備をモニタリングし、異常を検知した場合に最適な人員を最適なタイミングで配置できます。
ダウンタイムを最小限に抑えられる
予知保全では、設備トラブルが起こる前に通常とは異なる振動や温度変化を感知できるため、設備トラブルの原因を迅速に特定できます。その結果、ダウンタイムを最小限に抑え、生産性の向上につながります。
予防保全でも設備トラブルを防ぐことはできますが、部品以外の原因でトラブルが発生することもあります。設備の停止後に対処するケースも出やすいため、どうしてもダウンタイムが長くなります。
保全担当者の教育コストが低下する
予知保全で属人的な保全業務をシステム化できると、保全担当者の教育コスト削減や人材不足の解消が期待できます。
従来の保全業務では、経験豊富な保全担当者が経験則で修理箇所を特定したり、故障前に対応したりする場面が多くありました。しかし、経験の浅い担当者は同じようには対応できず、技術習得まで時間が必要です。
AIやIoT、予知分析などの技術を活用する予知保全を導入すると、システムによる異常の特定ができるようになり、修理箇所を迅速に明確化できるようになります。
予知保全のデメリットと対策方法
予知保全には、デメリットもあります。それらを踏まえたうえで、導入を判断することが重要です。また、適切に対策を取れれば、デメリットを一定解消したうえで予知保全を導入できます。
導入コストが高い
予知保全を導入するには、センサー機器・IoTプラットフォーム・AI分析システム などの設備投資が必要です。
また、既存の設備にセンサーを取り付けたり、データを処理するためのインフラ(サーバーやクラウド環境)を整えたりする必要があり、初期コストが高くなる傾向があります。
予知保全のコスト対策
- 重要な設備から段階的に導入し、費用対効果を見極める
- クラウド型のサービスを活用し、初期投資を抑える
データ量が少ないとAIの判断精度が低い
AIによる異常予測は、大量のデータをもとに学習することで精度を向上 させます。
しかし、導入直後はデータが十分に蓄積されていないため、誤検知(正常なのに異常と判断する)や見逃し(異常なのに正常と判断する) が発生しやすくなります。
また、設備ごとの個別の特性 を考慮したデータがないと、AIの分析結果が実際の故障傾向と合わないこともあります。
予知保全のコスト対策
- 初期は人間の判断と併用しながら運用し、データを蓄積してAIの精度を向上させる
- 設備メーカーや他の工場でのデータを活用し、学習データを補強する
システムの運用・管理が難しい
予知保全を適切に運用するには、データ分析の専門知識が必要になります。
センサーから得たデータをどのように解釈し、どのタイミングでメンテナンスを実施するかを判断するには、エンジニアやデータサイエンティストの知見が求められます。
また、センサーやAIの設定が適切でないと、誤検知が多発し、かえって無駄な保全コストが増える可能性もあります。
予知保全の運用難易度の対策
- 社内でデータ活用スキルを持つ人材を育成する
- 専門業者や外部コンサルタントを活用し、運用の最適化を図る
- 設備ごとに「どの程度の異常なら修理が必要か」の基準を設定する
- 経験豊富な技術者とAIの分析を組み合わせ、最適なタイミングを判断する
ネットワークやシステム障害の影響を受けやすい
クラウド型の予知保全システムを導入している場合、ネットワーク障害やサーバーダウン によってデータの取得や分析ができなくなるリスクがあります。
また、サイバー攻撃の対象になる可能性もありますので、データのセキュリティ対策が重要です。
予知保全のシステム障害対策
- 重要な設備には、クラウドとローカルの両方でデータを管理する仕組みを導入する
- セキュリティ対策を強化し、データのバックアップを定期的に取得する
特に、設備はネットワークに対して脆弱であることが多いため、十分な対策を講じる必要があります。
予知保全システムは導入するべき?費用対効果の確認方法
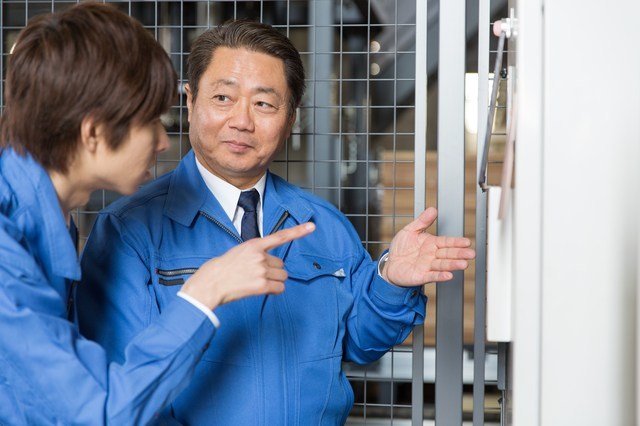
予知保全には多くのメリットがありますが、導入すべきかどうかは導入コストと削減できる費用を踏まえた費用対効果によって決まります。
具体的には、以下の指標から、「投資に対してどれだけのリターンが得られるか」を見積もります。
- 突発故障の削減によるダウンタイムコストの削減額
- 不要な保全作業の削減による人件費削減
- 生産性向上による売上改善効果
- 部品寿命延伸による消耗品費削減
一方で、人件費や工数削減の具体的な数値を算出するのは容易ではありません。予知保全システムを提供している企業に問い合わせ、人件費や工数削減の具体的な数値のシミュレーションを行ってもらうと、費用対効果での検討がしやすくなります。コスト感によっては、ダウンタイムの影響が大きい設備のみに予知保全システムを導入し、それ以外は予防保全を行うという選択肢もあります。
シミュレーションを依頼する前には、事前に自社の設備状況と対象設備の分析をしておくと、システムベンダーとの打ち合わせがスムーズになります。
具体的には、以下3点の要件を整理することをおすすめします。
自社の保全体制・業務フローの現状把握
予知保全の導入検討前に、自社の設備台帳、保全履歴、トラブル件数などを整理し、現状の課題を明確化します。突発故障が多い、部品の在庫管理が煩雑、定期保全の効果が不明確といった悩みがある場合、予知保全による改善余地は大きいです。
対象設備の予知保全の優先度付け
自社設備の特性をまとめ、予知保全に適している設備や優先度が高い設備を把握しておくことも重要です。以下のような設備は、予知保全の優先度が高いといえます。
- 故障時の影響が大きい中核設備(例:生産ラインのボトルネック機器)
- トラブルが頻発しやすい老朽化設備
- データが取得しやすい構造を持つ設備(振動、温度などが測定可能)
逆に、簡素な構造の設備や小型機器など、状態監視のコストに対して効果が見込みにくい設備には、予知保全システムの適用が難しい場合もあります。
社内IT/OTリソースの確認
IoTやAI導入には、データ収集から分析・運用まで一定の技術的体制が必要です。社内にIT・OTの専門人材がいない場合は、パートナー企業との連携を前提に進めるのが現実的です。
予知保全の仕組み・実際の流れ
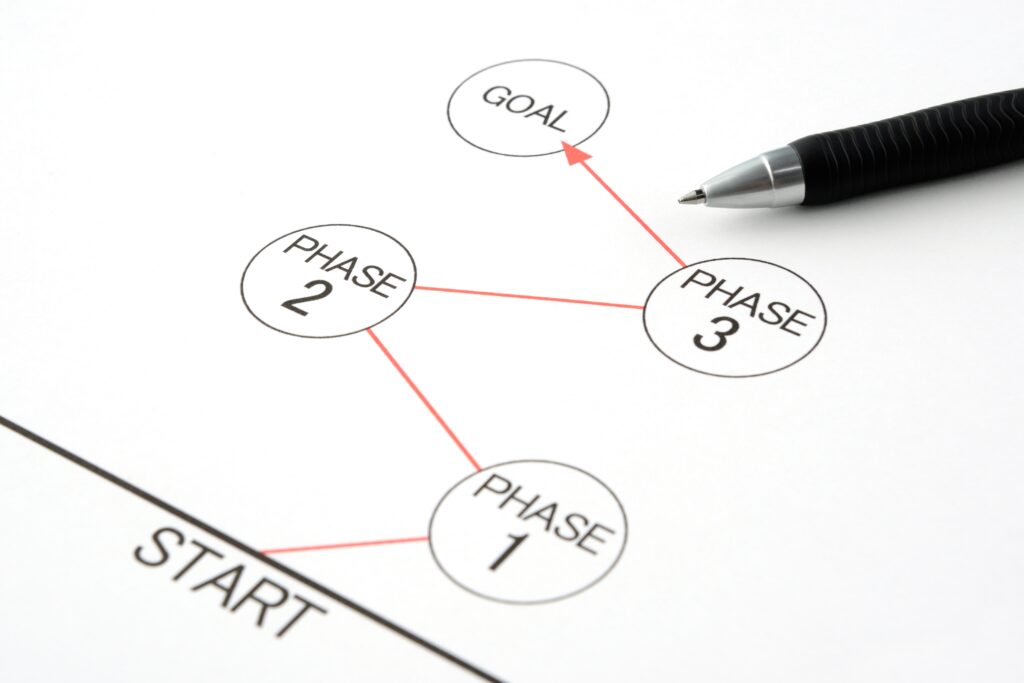
予知保全の仕組みは、主に データの収集・分析・異常予測・保全実施という4つのステップで構成されています。以下、それぞれのステップについて詳しく説明します。
データの収集
予知保全の基礎となるのは「データ」です。まず、設備に取り付けたセンサーから稼働データをリアルタイムに収集します。対象となるデータは、以下のようなものがあります。
- 温度(モーターや配管の異常な発熱を検出)
- 振動(ベアリングやギアの摩耗を察知)
- 電流・電圧(モーターや電気機器の負荷変動を把握)
- 音(異常なノイズや摩擦音を検知)
これらのデータは、PLCやエッジデバイス(エッジPC)、またはゲートウェイを経由して、クラウドやオンプレミスのデータベースに蓄積されます。
当然ですが、設備にセンサーが設置されていない場合は、新たに設置する必要があります。
データの分析
次に、収集したデータを、AIやIoTシステムによってリアルタイムで監視し、分析します。具体的には、設備データを統計分析やAI(機械学習・深層学習)によって処理し、設備の状態を評価します。
例えば、以下のような兆候を察知できます。
- 通常よりも振動が大きくなっている → ベアリングの摩耗が進行中
- モーターの電流値が増加している → 負荷がかかりすぎている可能性あり
- 異常な音が発生 → ベルトやギアの緩みの兆候
具体的な分析手法には、
- 時系列解析(トレンドの変化把握)
- クラスタリング(状態の分類)
- 主成分分析(異常パターンの抽出)
- 異常スコアリング(しきい値超えの検出)
などがあります。
異常の予測
上記の分析手法を組み合わせ、いつ頃異常が起きる可能性が高いかを予測します。 設備の「異常の兆し」や「劣化傾向」を自動で可視化していき「あと○○時間で故障する可能性が高い」 という予測を行います。
例えば、正常時には一定の振動レベルを保っていたポンプが、突如として微妙な振動変動を示したとします。 それがAIにより「劣化兆候」として認識され、警告が出れば、故障前に部品交換やメンテナンスが可能になります。
保全の実施
予測結果をもとに、設備の適切なタイミングでの点検・修理・部品交換 を実施します。
例えば、検出した異常に対して、以下のようなアクションを実施します。
- 軽微な異常 → 継続監視(しばらくデータを取りながら変化を確認)
- 中程度の異常 → 計画的なメンテナンスの実施(適切なタイミングで修理・交換)
- 深刻な異常 → 緊急対応(設備の停止・即時点検)
異常内容に対して、優先度をつけることで無駄なメンテナンスを減らしながら、急な故障を防ぐことができます。
予知保全の導入事例
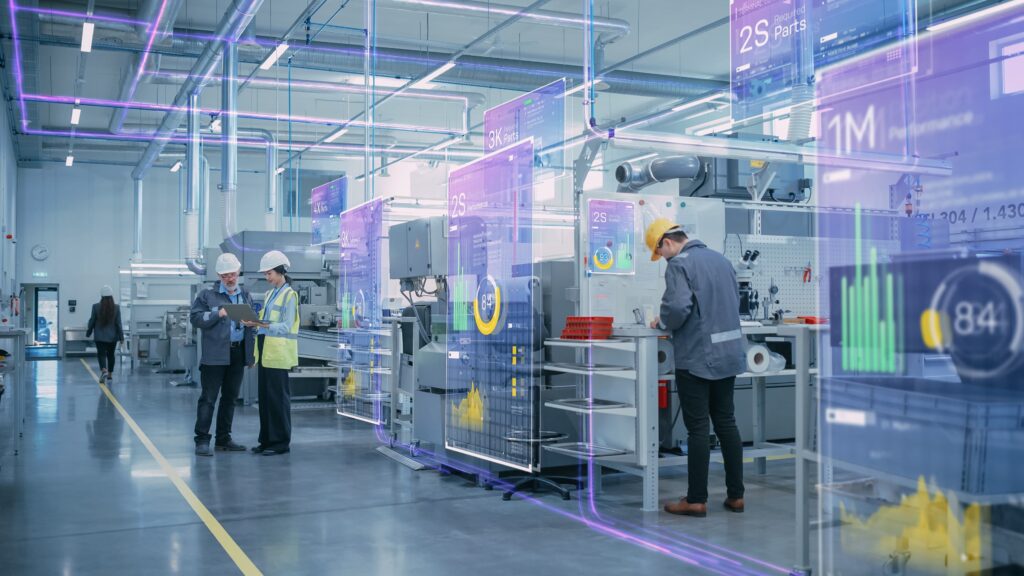
予知保全の導入に成功した企業事例も、検討時の参考になります。工数削減や保全精度向上など、他社が具体的にどのような効果を得られたかを確認できます。特に、自動車製造業などでは、予知保全で大きな導入効果を得られた事例が多々あります。
一例に、自動車部品工場で、高頻度で設備エラーが出ていた”かしめ機”に予知保全システムを導入した際に、設備エラーが6割減少および、ライン停止時間の7割減少した例があります。
減少した理由は、予知保全システムを導入したことにより、1日にでている”設備エラーの回数”と”止まっていた時間”の見える化ができるようになったことにより、適格な対処ができるようになったためです。
■見える化できたことで分かったこと
発生していた問題 |
---|
5秒以上の設備エラーが月30件以上も発生していた ライン停止時間が1ヶ月に1時間半以上もでていた |
多かった設備エラーの種類 |
ワークの配置ズレ ガイドやセンサの位置調整ミス ゴミ詰まり |
↓↓↓ 見える化できたことで明確になった対策 ↓↓↓
対策 |
---|
ワークやガイド、センサーなどの位置ズレをなくすために、品番ごとにわかるような目印テープを貼る 毎日生産開始時にゴミ詰まりチェック&清掃 |
的確な対策を行うことができるようになった結果、この設備の設備エラーが6割削減し、ライン停止時間は7割削減しました。
他にも、以下のような事例があります。
大手自動車部品メーカー事例
主要生産ラインに振動センサーとAI異常検知を導入
トラブル発生の30時間前に異常兆候を検出し、ダウンタイムを80%削減
中堅食品メーカー事例
主要生産ラインに振動センサーとA冷却装置のファンモーター異常を音センサーで監視
誤検知を防ぐためにAIで環境ノイズを学習させ、保全精度を向上
中小製造業(精密加工)事例
社内にIT人材が少なかったが、外部ベンダーと連携してパッケージ型予知保全システムを試験導入
限定的なラインでの運用からスタートし、導入効果を見ながら段階的に拡大中
予知保全は中小・中堅企業でも導入しやすくなりつつある
経済産業省やスマートファクトリー推進団体などによると、国内製造業における予知保全の導入率はまだ20~30%程度です。特に、中小・中堅企業では、予知保全までできていない工場が多いのが現状です。
一方、AIやクラウド型サービスの普及により、コストや技術面のハードルは下がりつつあります。中小企業でも十分に予知保全を導入可能なフェーズに入ってきたことから、今後の成長余地は大きいといえます。
まとめ
予知保全は、設備の故障リスクを大幅に低減し、ダウンタイムを最小限に抑える という大きなメリットがありますが、導入コストやデータ不足、運用の難しさなどの課題もあります。
特に、データ量が少ないとAIの判断精度が低下するため、導入初期は人間の判断と併用しながら精度を向上させていくことが重要です。
今後、AI技術やIoTの進化 により、これらのデメリットも徐々に解消されていくと考えられます。
企業ごとに適切な導入計画を立て、コストと効果のバランスを取りながら運用することが成功の鍵となります。ネクスタをはじめとする予知保全システム提供企業に相談し、具体的なシミュレーションを依頼することを推奨します。
22種類の生産管理システムをランキングで比較
初期費用相場や選び方のポイントをチェック
生産管理システムをそれぞれの特徴や初期費用相場などで比較したい場合は、「生産管理システムランキング」も是非ご覧ください。生産管理システムは、自社の製品・生産方式・企業規模などに適したものを導入しないと、得られるメリットが限定されてしまいます。事前適合性チェックや生産管理システムを選ぶ前に押さえておきたいポイントも解説していますので、製品選びの参考にしてみてください。