リーン生産方式とは:基本原則、TPSとの違い、生産管理システムの活用事例を紹介
公開日:2025年01月30日
最終更新日:2025年01月31日
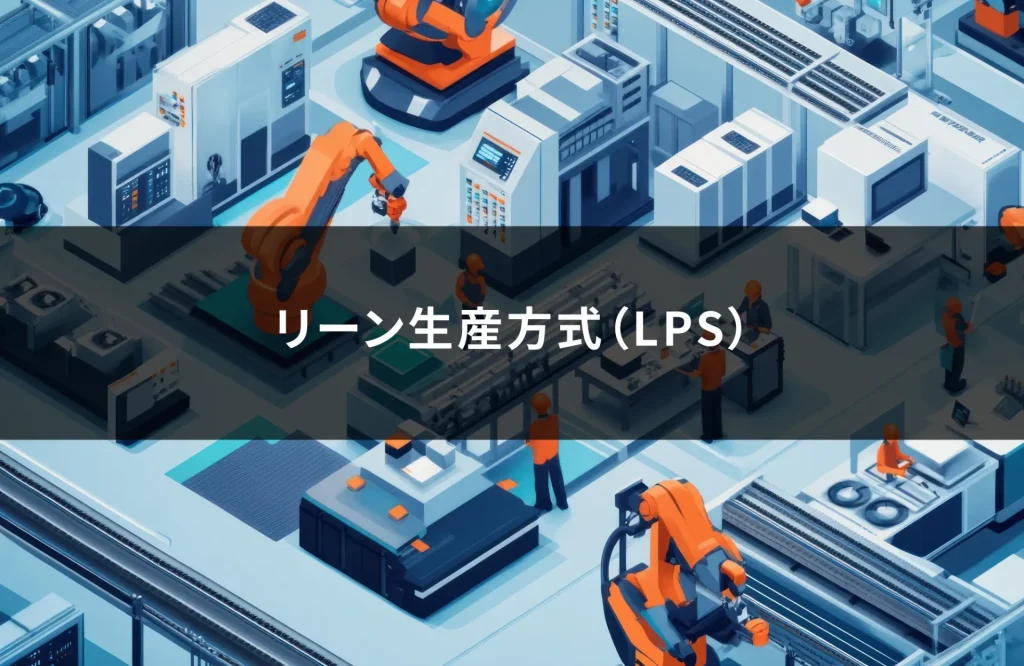
リーン生産方式は、業務プロセスの効率化を追求する手法で、トヨタ生産方式を汎用化させた枠組みです。本記事では、トヨタ生産方式とリーン生産方式との違い・共通点、リーン生産方式の基本5原則である顧客価値の定義、価値の流れの見える化、フローの最適化、プル型システムの確立、継続的改善について解説します。さらに導入時のデメリットを踏まえ、リーン生産方式導入を加速する生産管理システムの活用事例も紹介します。
リーン生産方式(LPS)とは
リーン生産方式(Lean Product System;LPS)は、ムダを排除することを軸とした業務プロセス改善の枠組みです。製造現場におけるムダをなくし、顧客にとって価値のある活動に集中することを目指します。近年では、製造業以外の分野にも応用されています。
リーン生産方式の発祥
リーン生産方式は、日本で生まれたトヨタ生産方式(Toyota Product System;TPS)をもとにして1990年代にアメリカで汎用化されました。
トヨタ生産方式は1940〜50年代の日本で生まれた概念です。戦後復興での資源不足を背景に、生産効率を高める手法として確立されました。1990年代になって、アメリカの企業で効率向上が課題となる中、トヨタの方式が注目されるようになりました。こうして製造業以外でも応用可能な形に発展し、書籍『リーン生産方式が企業を変える』をきっかけに広く普及しました。
リーン生産方式とトヨタ生産方式(TPS)の違い
リーン生産方式は、トヨタ生産方式における現場主義やチーム文化などの背景を抽象化して体系化され、他業界でも適用できる汎用的な考え方としています。リーン生産方式とTPSの相違点を簡潔にまとめると、次の表の通りとなります。
適用範囲 | 文化 | |
リーン生産方式(LPS) | 幅広い業種に適用可能 | 特別な文化背景を問わず適用可能 |
トヨタ生産方式(TPS) | 自動車産業の生産現場に特化 | 現場主義・チーム文化に根ざしたもの |
トヨタ生産方式とリーン生産方式に共通する考え方
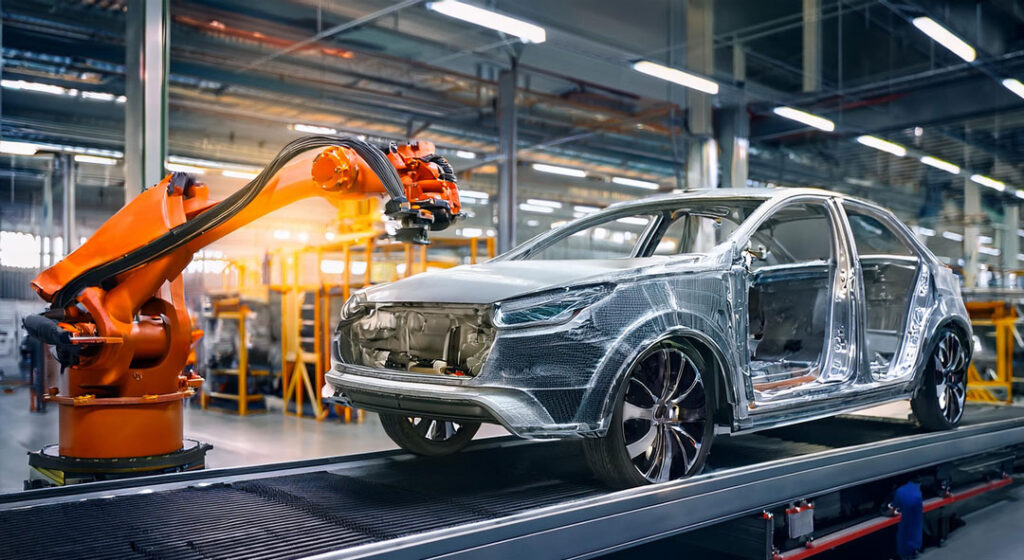
トヨタ生産方式とリーン生産方式には、理念・手法に多くの共通点があります。特に、「ジャストインタイム」「自働化」「平準化」「カイゼン」は、双方の核となる考え方です。
ジャストインタイム(JIT)
ジャストインタイムは、必要なものを、必要なときに、必要な量だけ生産・供給する仕組みです。これにより、過剰在庫や生産遅延を防ぎ、最小限の資源で最大限の効率を生みます。生産計画と部品供給を同期させることが鍵であり、TPSとLPSに共通する中心的な考え方の一つです。
自働化
自働化は、機械や設備を自動運転させるだけでなく、異常検知時に自動停止し、早期に問題を知らせる仕組みのことで、TPSの重要概念の一つです。リーン生産方式でも、プロセスの「見える化」を通じて問題を早期に発見し解決するという点で、自働化の考え方を共有しています。
高品質を維持しながらムダな手戻り・不良品の削減を目指す取り組みを通して、品質管理の向上と生産効率化に寄与しています。
平準化
平準化とは、生産量や作業内容のムラをなくし、作業負荷や生産量を均等化する考え方です。平準化の徹底は、「ムダ・ムリ・ムラ(3M)」の排除に直結し、過剰な設備投資や作業工数の浪費を防ぎます。
リーン生産方式でも生産フローを均一化し、ボトルネックを解消することが重要視されます。これにより、安定生産を実現し、無駄な在庫や工程負荷の偏りを防ぎ、需要の変動が大きくても安定した生産を維持します。
リーン生産方式の基本となる5つの原則
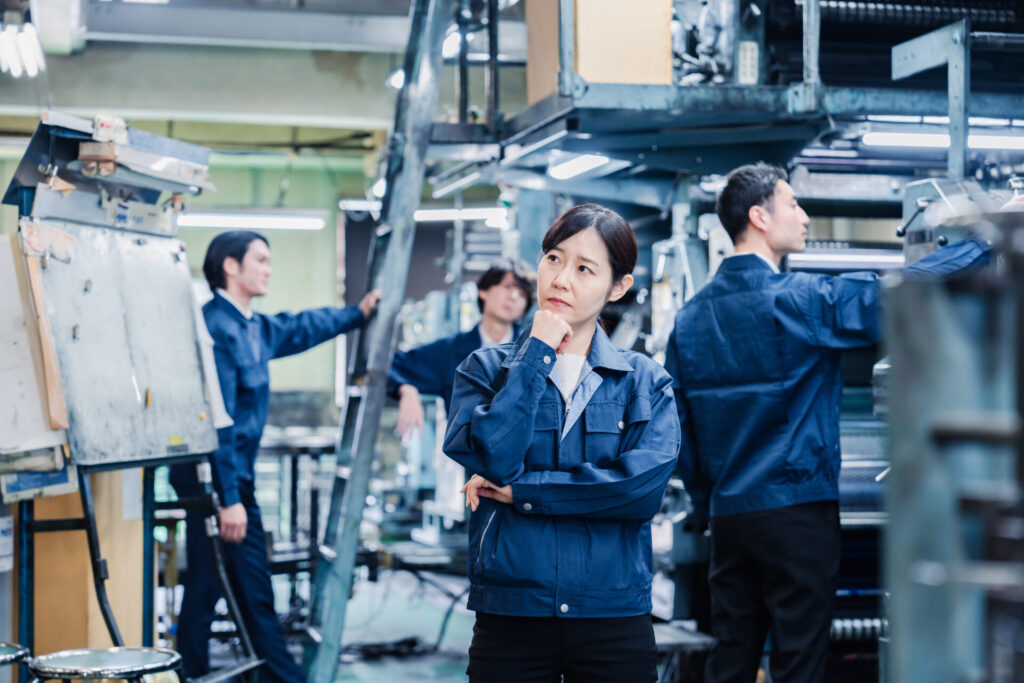
リーン生産方式は5つの基本原則から構成されています。
顧客視点で価値を定義
顧客目線で「価値」を定義し、それを軸とした業務プロセスの設計がリーン生産方式の出発点です。この価値定義が正確でなければ、対価の支払いに対して満足度の低い製品やサービスを生むリスクがあります。
顧客のニーズや要望を深掘りし、顧客にとって不要な機能・サービスを削減し、製品デザインやプロセスを顧客ニーズに直結する部分に集中します。これによって、顧客にとってのムダなコストや企業努力を排除できます。
価値の流れを見える化
製品が顧客に届くまでの全プロセスを明確にし、価値を生む活動とムダな活動に分けます。
全体像を把握することで、時間や資源が無駄になっている工程を特定してカイゼンにつなげ、ムダな在庫・工程を削減します。価値の流れの可視化には、工程の流れを示したフロー図やプロセスマップの活用などが有効です。
フローの最適化(整流化)
すべての工程で滞りなく流れる状態(整流化)を作り出し、業務プロセスにおける待ち時間を最小化します。
フローの設計では、各工程の役割と連携を明確にすることが重要です。具体的には次のようなアプローチが用いられます。
- ボトルネックの特定:プロセスを可視化して、遅れや滞留が発生する箇所を明確にする
- 工程の最適配置:作業ステーションを効率的に配置し、無駄な移動を削減する
フロー最適化により、生産時間が短縮され、コスト削減や顧客満足度向上につながります。この考え方は、トヨタ生産方式の「ジャストインタイム(JIT)」とも密接に関連しています。
プル型生産方式(後工程引取方式)を確立
顧客の需要に応じて生産を進める「プル型生産方式(後工程引取方式)」を採用するのも、リーン生産方式の特徴です。従来の計画に基づいて製品を生産する「プッシュ型生産方式」とは異なり、需給ギャップが発生しにくく、生産リードタイムの短縮も実現します。
プル型生産方式としては、例えば次のような仕組みが有名です。
- かんばん方式の活用:各工程が必要な材料・部品の「後工程引き取り(プル)」で生産が進行する
- 在庫の最小化:必要なタイミングで必要な量だけを生産するため、余剰在庫が削減される
工程の完璧を目指して改善を続ける
リーン生産方式はいわば完璧を追求するため、継続的なカイゼンが不可欠です。具体的には、以下のフローを繰り返します。
- 問題の発見: プロセスを観察し、無駄や改善可能な箇所を特定する
- 原因の分析: データや従来知見を活用し、問題の根本原因を明確にする
- 改善の実行: 根本原因に対処する改善策を実行する
- 効果の検証: 改善した結果を見える化し、期待する効果が得られているか確認する
この改善プロセスは、現場の作業員から経営層までが協力し合うことが必要で、中長期的に企業競争力を高めます。
リーン生産方式のデメリット
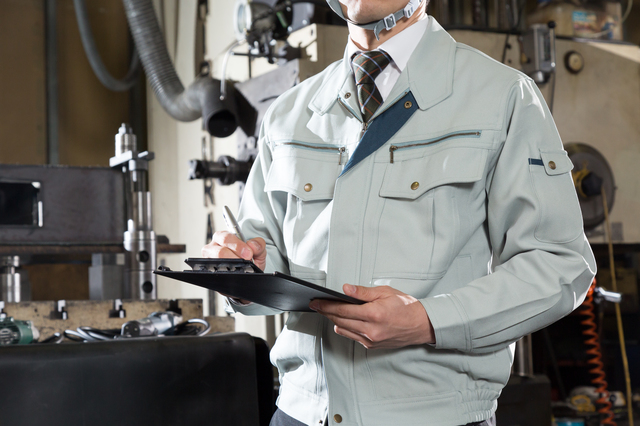
効率的に運用できれば多くのメリットが受けられるリーン生産方式ですが、いくつかの課題もあります。
精度の高い需要予測が必要
リーン生産方式では、必要な時に必要な量だけ原材料・部材を「プル」するため、精度の高い需要予測(フォーキャスト)が不可欠です。
在庫を最小限に抑える「プル型生産」の運用では、生産ラインやリソースの調整も需要予測に依存します。このため、僅かなサプライチェーンの遅れでメリットが失われてしまうリスクがあります。
発注時のスケールメリットが出にくい
リーン生産方式ではジャストインタイム方式を踏襲するため、大量発注によるコスト削減効果が出にくいというデメリットがあります。発注の小口化による影響には、例えば次のようなものがあります。
- 物流効率低下:小ロット配送を頻繁に行うため、製品個数・重量当たりの輸送費が増加
- サプライヤーの生産性低下:発注単位に合わせた少量生産体制により、製造コストが増加
在庫管理が煩雑
リーン生産方式では、需要の変化に応じて原材料の納期・供給量を頻繁に調整するため、結果として在庫管理が複雑になります。適切な運用のためには、各工程でのリアルタイムな在庫状況の把握が不可欠となり、在庫管理に要する負担はさらに大きくなります。
しかし、こうした管理にミスが起こってしまうと、原材料や製品の欠品を引き起こすリスクがあります。さらに、サプライヤーの出荷遅延や誤配送が発生した場合にも、全体の生産計画に大きな影響を与える場合もあります。
導入の初期コストがかかる
リーン生産方式を導入するには、生産プロセスの再設計・見直しや、新たなシステム・自働化設備の導入などによって、多額の初期投資が必要となります。導入時の従業員教育だけでなく、導入後の予期せぬシステム追加改修なども少なくありません。特に中小企業にとっては、多くの追加費用の負担が非常に大きくなります。
さらに、多額の初期投資に見合った効果が現れるまで時間がかかるため、短期的にメリットを感じにくいことも予想されます。こうした費用負担やリスクを考慮して、導入を躊躇する企業も少なくありません。
生産管理システムでリーン生産方式導入を加速できる
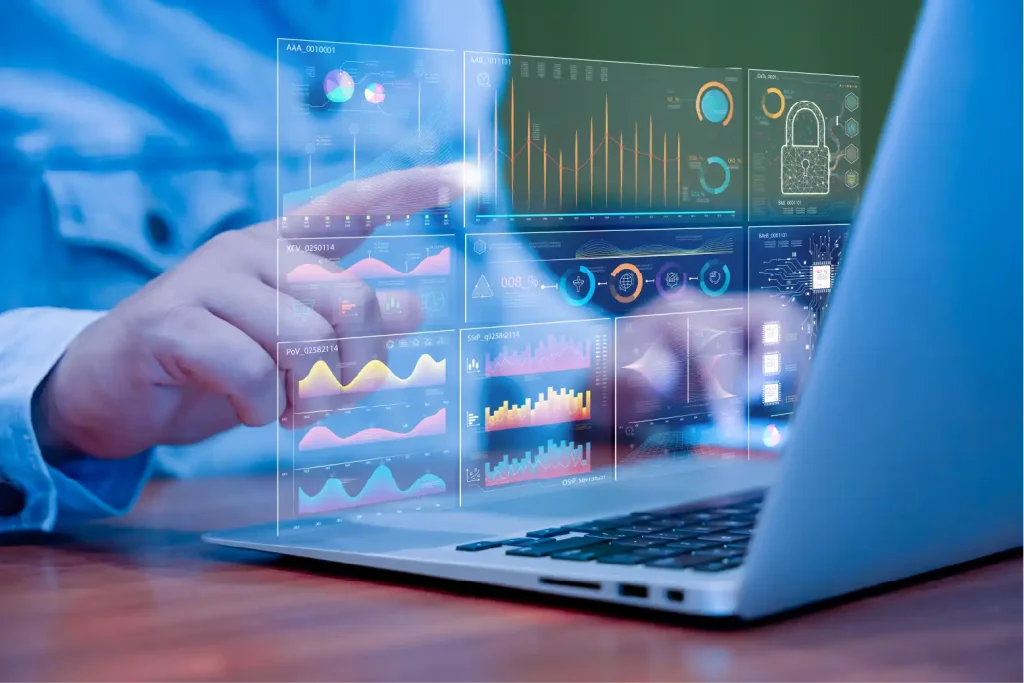
リーン生産方式導入の大きな課題の一つである在庫管理は、生産管理システムの導入によって大幅な効率化が可能です。生産管理システムを活用すれば、生産現場で属人化しやすい在庫状況をリアルタイムで共有し、発注・供給の判断を自動化できます。これにより、在庫管理における人的負担を軽減し、リーン生産方式の導入を加速できます。
特に、複雑な在庫管理の徹底に悩む企業にとって、生産管理システムの活用は、無駄を排除し、よりスムーズな運用を実現するための重要な投資と言えるでしょう。
しかし、ERPやSCMなどのシステムは高額であるため、投資に見合った活用ができるか不安に感じることも多いでしょう。しかし、最近は少額の初期費用でトライアルを実施できるシステムもあります。
生産管理システムの活用事例
生産管理システムを活用することで、リーン生産方式の課題を克服し、効率化がさらに進みます。
管理効率化で過剰在庫を圧縮
金属加工・組立業界の企業では、かんばん方式での発注管理において、二重発注や在庫過多が頻繁に発生するという課題を抱えていました。このような問題に対しては、生産管理システムの導入が一般的な解決策とされています。生産管理システムを活用すれば、在庫状況をリアルタイムで把握し、適正な在庫量を維持できるようになることが期待されます。
その企業では、システム導入前までは正確な在庫数や在庫金額も把握できておらず、生産管理システムに必要な機能も判断できない状況でした。このような状況でシステム導入を進めると、後になって別機能の追加が必要となり、高額の追加費用がかかるケースもあります。
そこで、安価な初期費用で、導入コンサルティング付きのトライアルが可能な生産管理システムを導入しました。その結果、発注管理の簡素化と在庫のリアルタイム管理が実現。さらに二重発注の解消や在庫量適正化によって、入荷確認のための工数が大幅に圧縮され、年間100万円の過剰在庫の削減にも繋がりました。
詳しい事例紹介はこちら:
【在庫管理システム】在庫管理のシステム化に成功!リアルタイムな在庫管理で年間100万円の在庫削減
ハンディ端末の活用で、出荷確認のムダを低減
生産管理システムとハンディ端末を連携すれば、手作業によるミスをなくし、二重確認の手間が削減できます。
バイク用品を取り扱う企業では、ダブルチェック体制で出荷前に目視確認を行っていたものの、月に8回程度の出荷ミスが常態化していました。生産管理システムとバーコードスキャン機能付きのハンディ端末を併用することで、出荷ミスがゼロとなり、出荷前の検品スピードも従来の4倍まで向上しました。
詳しい事例紹介はこちら:
【出荷検品システム】ハンディ端末を用いた出荷検品で出荷ミス0/作業効率4倍アップを実現
22種類の生産管理システムをランキングで比較
初期費用相場や選び方のポイントをチェック
生産管理システムをそれぞれの特徴や初期費用相場などで比較したい場合は、「生産管理システムランキング」も是非ご覧ください。生産管理システムは、自社の製品・生産方式・企業規模などに適したものを導入しないと、得られるメリットが限定されてしまいます。事前適合性チェックや生産管理システムを選ぶ前に押さえておきたいポイントも解説していますので、製品選びの参考にしてみてください。