個別受注生産とは?多品種少量のお悩み事例と解決方法まで徹底解説
公開日:2024年10月28日
最終更新日:2024年11月07日
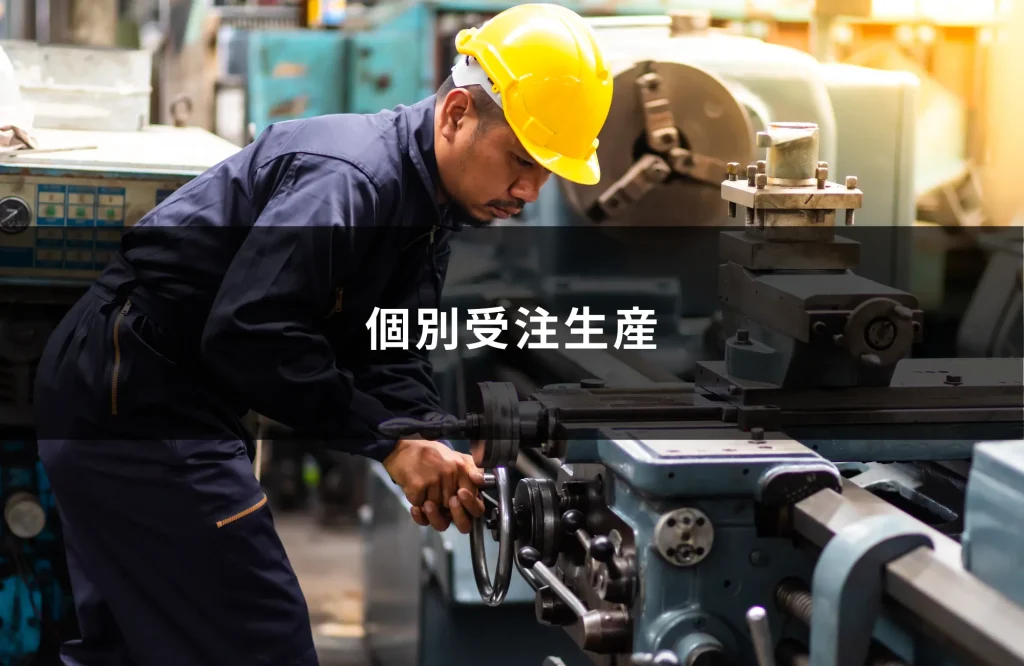
個別受注生産は、顧客の仕様に応じたオーダーメイドの製品を生産する方式で、多品種少量生産に最適です。本記事では、見込み生産と比較した個別受注生産の特徴から、連続生産やロット生産など他の生産方式との関係を解説します。また、在庫・納期・原価の管理に対する課題に対して、生産管理システム「スマートF」の導入事例を紹介し、課題解決から企業の生産効率向上につなげる具体的方法を提案します。
個別受注生産とは:多品種少量向けの注文対応型生産
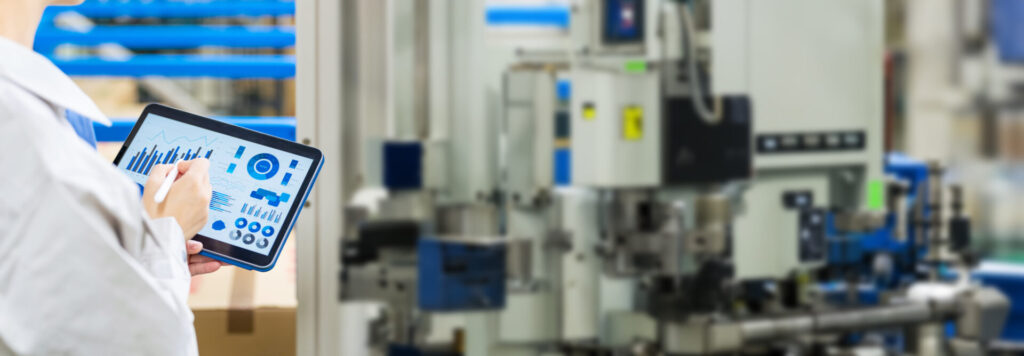
個別受注生産(Engineer to Order、ETO)は、顧客の指定する仕様に基づき、注文ごとに設計・製造を行う生産方式です。個別受注生産では、製品が標準化されておらず、受注ごとに異なる仕様で生産することが一般的で、多品種少量生産に向いています。一方で、顧客のリクエストに柔軟に対応することを求められるため、生産効率やコスト管理、在庫管理に工夫が必要です。
個別受注生産と見込み生産との違い
個別受注生産は顧客からの注文を受けてから設計・製造を開始しますが、見込み生産(Make to Stock)は需要予測に基づいて汎用製品を大量に生産します。個別受注生産、見込み生産について、主な違いは次の表の通りです。
生産方式 | カスタマイズ性 | 製品在庫リスク | 納入リードタイム | 生産効率 |
個別受注生産 | 〇(高い) | 〇(なし) | ×(長い) | ×(低い) |
見込み生産 | ×(低い) | ×(あり) | 〇(短い) | 〇(高い) |
どちらの生産方式も一長一短であり、市場や顧客ニーズに応じて、適切に選択することが望ましいと言えます。
その他の生産方法との関連
個別受注生産に関連する用語として、連続生産、ロット生産、ライン生産という考え方があります。
連続生産
連続生産は、長期にわたり同一製品を生産し続ける方式で、生産設備の稼働率が非常に高いため、固定費の分散効果が大きくコスト効率に優れています。石油精製、化学工業、食品加工などの業界で広く用いられています。
連続生産は標準化された大量生産向きであるため、個別受注生産される製品に適用することは多くありません。連続生産方式で、個別受注生産品を製造する場合、顧客の特性要望・納期などの要望にきめ細かく対応するのは困難です。また、品種切り替え時に段取り替えロスが多く発生しやすい、というデメリットもあります。
ロット生産
ロット生産は、特定の数量(ロット)単位で製品をまとめて生産する方式で、同じ設備を使用してロット単位で複数品種の製品を作り分けます。効率面では連続生産に及びませんが、製造品目変更時には連続生産よりも簡素な段取り替えで対応することができます。アパレル製品や電子部品など、規格品の製造で一般的に採用されています。
個別受注生産でも、ロット生産で対応することは珍しくありません。しかし、頻繁な段取り替えが必要となるため、生産性が低下しやすく、さらに生産計画が複雑になりがちです。
ライン生産
ライン生産は、生産工程を細かく分割して連続的に製品を組み立てる方式で、各工程での作業を効率的に分担することができます。細かすぎる仕様変更は困難ですが、仕様のバリエーションが限定的である場合には、個別受注生産品目をライン生産で対応することもあります。ただし、在庫管理、生産計画、その他オペレーションが複雑になるため、非常に難易度が高いといえます。
各工程が標準化されており、作業の効率性と均質性が確保されている場合は、ライン生産を採用することで1個あたりの生産コストを圧縮できます。実際に、コスト制約の厳しい自動車や家電製品などの生産に採用されています。
個別受注生産のメリット
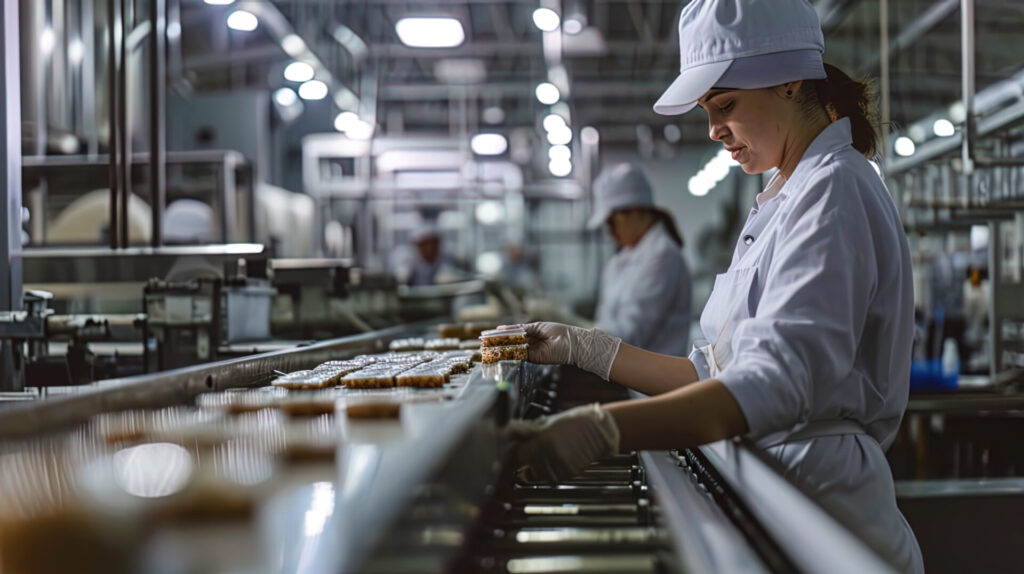
個別受注生産で期待できるメリットは、以下の2点です。
顧客ごとにオーダーメイド製品を提供できる
個別受注生産では、受注ごとに顧客指定の仕様を満たす製品を提供します。標準仕様品ではなく専用の設計であるため、顧客にとって使い勝手のよい製品に作りこむことが可能です。たとえば、次のように高度なカスタマイズが求められる製品には、個別受注生産が標準です。
- 産業機械業界:顧客仕様に合わせた工作機械・産業ロボット
- 医療機器業界:患者の体型・状態に合わせた義肢・補聴器
- 航空宇宙業界:航空機・ロケット本体、関連する部品
特注品やオーダーメイド品は、一般的な市場にはない高付加価値製品を提供することができます。顧客にとっては、自分専用にカスタマイズされた製品を手に入れられるため、価格が高くてもその価値を感じてもらいやすくなります。
<具体例>
高級家具やオーダーメイドの機械部品など、他社では作れないような特別な仕様の製品を作ることで、顧客はその製品に高い価値を感じ、長期的な関係構築につながることがあります。また、付加価値が高い製品ほど、企業の利益率も向上しやすいです。
在庫リスクがきわめて低い
使用する材料・部品や、生産した製品が不良在庫となるリスクが低いことも、個別受注生産の大きなメリットです。実際の注文を受けてから生産を開始するため、過剰在庫を抱えることで保管スペース・管理コストがかかったり売れ残りリスクが非常に低くなります。
特に高価な材料・部品を使用する製品では、過剰在庫を抱えることで資金が拘束されるリスクが減らせるため、企業のキャッシュフローの健全性が保たれます。さらに、モデルチェンジで過剰在庫が使えなくなるリスクも排除することができます。
この在庫リスクの低さは、見込み生産にはないメリットと言えます。需要予測に基づいて生産する見込み生産で発生しやすい在庫ロスは、個別受注生産では生まれにくくなります。
<具体例>
ある製品を100個作るとき、予測に基づいて200個分の材料を購入してしまうと、残りの100個分の材料が無駄になります。個別受注生産では、最初から100個分だけの材料を発注するため、余分なコストを発生させず、効率的に生産を進めることができます。
個別受注生産でよくある課題
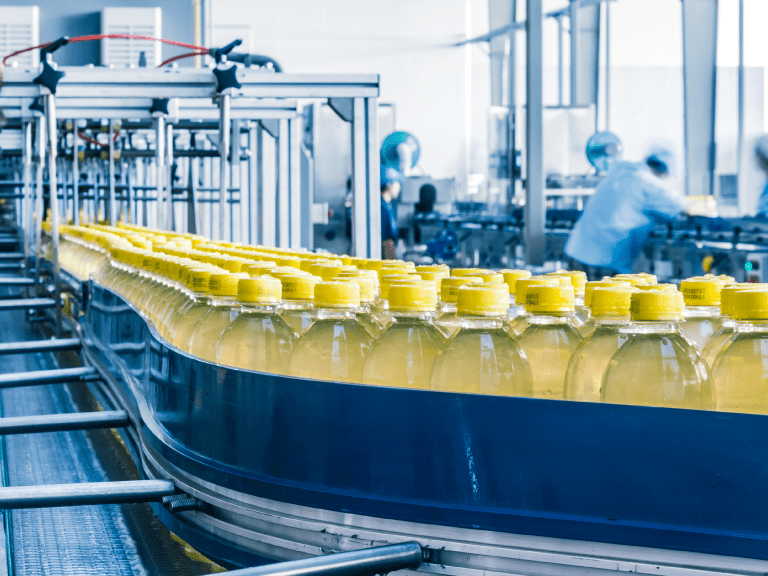
前述のようなメリットがある一方で、個別受注生産に特有の課題も存在します。
納期管理が複雑になる
個別受注生産では、顧客ごとに異なる製品仕様で納期を指定されるため、生産計画・納期管理が非常に複雑になります。各注文が異なるプロセスや材料を必要とするため、生産計画の立案やリソースの割り当てが容易ではありません。複数の注文が重なった場合や、サプライヤーからの材料供給が遅れた場合には、納期の遵守がさらに困難になります。さらに予期せぬトラブルが起こったときに、他の注文への影響が大きくなります。
しかし、納期遅延を起こしてしまうと、取引関係に悪影響を及ぼす可能性もあります。スケジュール管理ツールや生産管理システムを使って、常に進捗状況をリアルタイムで把握し、問題が起きた際には早めに対処できる体制を整えることが重要です。
生産効率が悪化しやすい
個別受注生産では、規格品の大量生産に比べると、生産効率が悪くなります。注文ごとに異なる仕様が要求されるため、頻繁な段取り替えが必要となり、生産ライン稼働率が悪化します。さらに、生産計画が複雑になり、無駄な作業や手戻りが発生する可能性も高まります。
生産効率を向上させるには、作業手順の簡略化や自動化などで段取り替えを効率化したり、部分的に作業手順を標準化するなどの工夫をするとよいでしょう。
原価管理に手間がかかる
個別受注生産では、製品ごとに材料や工数(作業時間)が異なるため、正確な原価を把握するために手間がかかります。具体的に難しい点は次の2点です。
- 製品ごとに工程が異なるため、コストを正確に把握しにくい
- 材料の種類・製品の歩留まり・所要時間が注文により変動し、製造コストが一定にならない
一方で、製造コストを見誤ると、適切な販売価格を設定できず、利益が圧迫される可能性があります。原価管理システムを導入し、各工程のコストを細かく追跡することで、注文ごとの詳細なコスト分析が可能となり、正確な原価把握が実現できます。
生産管理システム選定時は「個別受注生産の対応可否」を確認
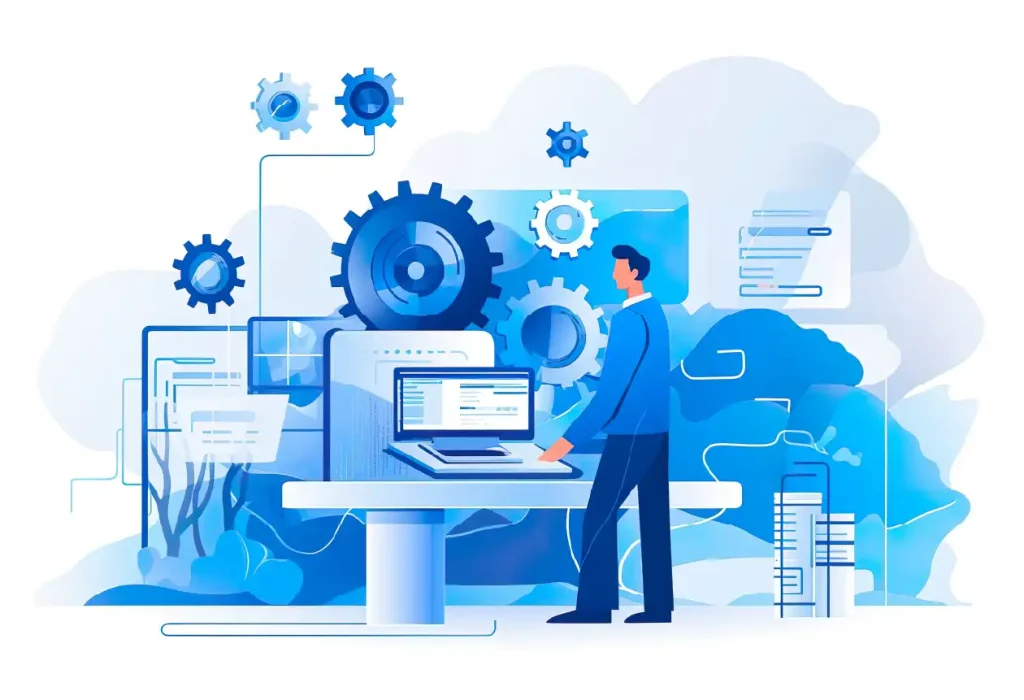
個別受注生産を採用している企業にとって、生産管理システムを適切に選定することは非常に重要です。個別受注生産特有の生産計画の管理だけでなく、在庫・納期・原価の管理に対応できれば、導入後の業務プロセスの大幅な効率アップが見込めます。
例えば、受注ごとの生産計画の立案、BOMの自動生成、納期管理の自動化など、個別受注生産特有の機能が実装されていることを事前に確認しましょう。
生産管理システム導入のメリット
生産管理システムは、個別受注生産に関するお悩みをサポートします。具体的には次の通りです。
BOM (部品表)のシステム管理
部品表(Bill of Materials)は製品の構成部品を一覧化したものです。これを生産管理システムで一元管理することで、部品の使用状況や手配状況をリアルタイムで把握できるため、部品の不足や過剰を防ぎ、適切な在庫管理が可能になります。
特に個別受注生産では、生産計画が複雑であるため、このようなシステムでの一元管理は部品などの在庫管理に効果的です。
工程管理の見える化
工程管理をシステム化することで、各工程の進捗状況をリアルタイムで可視化することができます。これにより生産トラブルを早期に発見することができ、迅速なリカバリー対応が可能です。
また、生産現場での進捗状況をデジタル化することで、現場と管理部門の連携がスムーズになり、工程・部署間での無駄な時間や作業を削減できるのも大きなメリットです。
納期管理の工数削減
生産管理システムの導入により、受注から出荷までの納期管理が効率化され、進捗確認や調整作業に必要な工数を大幅に削減できます。
システム上でリアルタイムの進捗状況を確認できるため、顧客への納期回答も迅速に行えるようになり、納期遅延のリスクを低減することが可能です。
原価の見える化
生産管理システムでは、工程や材料・部品ごとのコストが自動で計算され、リアルタイムで原価の見える化が実現されます。これにより、製品ごとの正確なコスト把握が可能となり、適正な販売価格を提示しやすくなります。
特に個別受注生産では、注文ごとに製造コストが大きく異なります。このため、生産管理システムを利用することで、材料費、労務費、その他経費などを容易に追跡し、原価管理の効率化・精度アップに繋がります。
生産に関するあらゆる情報を一元管理
生産管理システムを導入することで、材料の調達状況、生産計画と工程の進捗状況、在庫状況、納期、原価など、すべての生産情報を一元的に管理できます。
情報の一元管理により、正しい情報を正確に把握することが容易になります。その結果、部門間の連携が強化され、ミスや手戻りが減り、生産全体の業務効率が向上します。
個別受注生産に適した生産管理システム導入事例
最後に、生産管理システム「スマートF」における実際の導入事例を紹介します。個別受注生産における課題解決の具体的な手法として参考になります。
製品別の原価管理を実現した例
オーディオ機器の多品種少量生産やオーダーメイド製造を行うメーカーでは、個別受注生産における原価管理の難しさに直面しましたが、生産管理システムを導入し、原価管理の大幅な改善を図りました。
製品別の原価を正確に管理すべく、初めは自社で管理システムの開発を試みたものの、運用の複雑さや工数の多さがハードルとなっていました。そこで、パッケージ型の生産管理システムを導入し、各案件の材料費や工数をリアルタイムで把握し、複雑な原価を自動で計算できる体制を確立しました。複雑な個別受注生産の中でも、労務費や材料費の自動集計が可能となりました。
詳細はこちら:製品別原価管理・粗利分析が可能に!商品開発の予算化による開発スピード向上もできる体制に
複雑なエクセル管理が原因の属人化を解消した例
産業用ロボット事業を手掛ける企業では、個別受注生産における管理業務がExcelに依存しており、特定の担当者にしか業務内容が分からない「属人化」が大きな課題でした。具体的には、この属人化による問題として、データの不整合や入力ミス、進捗の遅延が頻発し、全体の生産効率が低下していました。
そこで、生産管理システムで情報を一元管理することで、業務の標準化を推進しました。システム導入後は、すべての工程がリアルタイムで見える化され、特定の担当者に依存することなく、誰でもデータを共有・確認できる体制が実現しました。結果として、作業ミスの減少、関連部門との在庫情報の共有が円滑になり、会社全体での業務効率が大幅に改善されました。
→複雑なエクセル管理が原因の属人化を解消した例はこちら:脱・複雑で属人的なエクセル在庫管理!受注案件単位の在庫管理はそのままに、業務標準化や工数削減、ミス削減まで実現
22種類の生産管理システムをランキングで比較
初期費用相場や選び方のポイントをチェック
生産管理システムをそれぞれの特徴や初期費用相場などで比較したい場合は、「生産管理システムランキング」も是非ご覧ください。生産管理システムは、自社の製品・生産方式・企業規模などに適したものを導入しないと、得られるメリットが限定されてしまいます。事前適合性チェックや生産管理システムを選ぶ前に押さえておきたいポイントも解説していますので、製品選びの参考にしてみてください。