QC7つ道具とは?品質管理の基本から層別分析の組み合わせ方まで徹底解説
公開日:2024年12月05日
最終更新日:2024年12月05日

QC7つ道具は、製造業の品質管理において問題を可視化し、原因を特定したうえで改善に導くための基本的なツール群です。本記事では、パレート図や特性要因図、ヒストグラムなど、それぞれの各ツールの特徴と具体的な使い方を詳しく紹介します。また、層別分析も含めた実際の使い方について、具体的なデータで図示・分析して解説します。さらに、他の品質管理手法である新QC7つ道具、TPS、シックスシグマについても簡潔に纏めました。
QC7つ道具とは?
QC7つ道具は、製造現場における問題・課題を見える化し、原因を特定して改善するための基本的なツールです。特別な技術や高度な知識がなくても使えることが大きな特徴で、シンプルで汎用性が高く、広い範囲で効果的な手法として普及しました。
QC7つ道具の語源
日本における品質管理の第一人者である石川馨が、アメリカの品質管理理論に基づき、品質管理に必要な基本的な手法を「道具」として体系化したことに由来します。
QC7つ道具の「QC」とは「Quality Control」の略称、すなわち品質管理のことを指します。7つ道具とは、品質管理で活用する7種類の基本的手法を言い、「弁慶の7つ道具」になぞらえて名付けられました。
データで現場の問題を見える化するツール
QC7つ道具の主な目的は、データを使って現場の問題を「見える化」することです。製造工程をデータや事象で視覚的に整理することで、何が問題となっているのかを直感的に把握しやすくなります。さらに、見える化された問題について、原因を特定・改善するためにも、QC7つ道具は活用されます。
QC7つ道具を活用すると、経験・思い込みで実施する対策ではなく、事実・データに基づいた本質的な解決策を導き出すことができます。このため、ISO9001などの品質マネジメントシステムの基盤となっており、国際的に広く使われています。
QC7つ道具の種類
QC7つ道具は、JIS9024: 2003で規定される以下7つのツールから構成されます。
- パレート図
- 特性要因図(フィッシュボーン図)
- グラフ
- ヒストグラム
- 散布図
- 管理図
- チェックシート
それぞれのツールを適切に組み合わせてデータ・事象を整理し、問題解決につなげることができます。
パレート図
パレート図は、問題の発生頻度や影響度を視覚的に示し、「最も大きな影響を与える要因」を特定するツールです。これは、少数の原因が大部分の結果を引き起こすとされる、パレートの法則を見える化したものです。パレート図を使うことで、少数の重要な原因を明確にして、改善アクションの優先順位を適切に決めることができます。
例えば、金属加工製品Xの品質不良低減というテーマに取り組む際には、まず最初にパレート図を用いて品質不良の発生原因を調査します。この場合、次の図のように表面粗さ不良が最も多いため、これを改善することが費用対効果が大きいと結論付けられます。
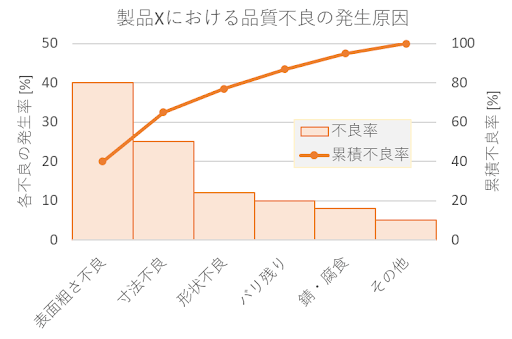
特性要因図(フィッシュボーン図)
特性要因図は、改善したい事象について、「4M1E」の観点で、要因を整理して一目で分かるようにするものです。ここでの「4M1E」とは、Man(人)・Machine(機械)、Material(材料)、Method(方法)、Environment(環境)を指します。
次の図は、加熱食品の加熱不良に関する特性要因図で、「4M1E」の観点で考えられる要因を抽出・整理したものです。このようにして想定原因をあらかじめ見える化することで、カンや思いこみによる場当たり的な対策を防ぎ、対策アクションの優先順位付けがしやすくなります。
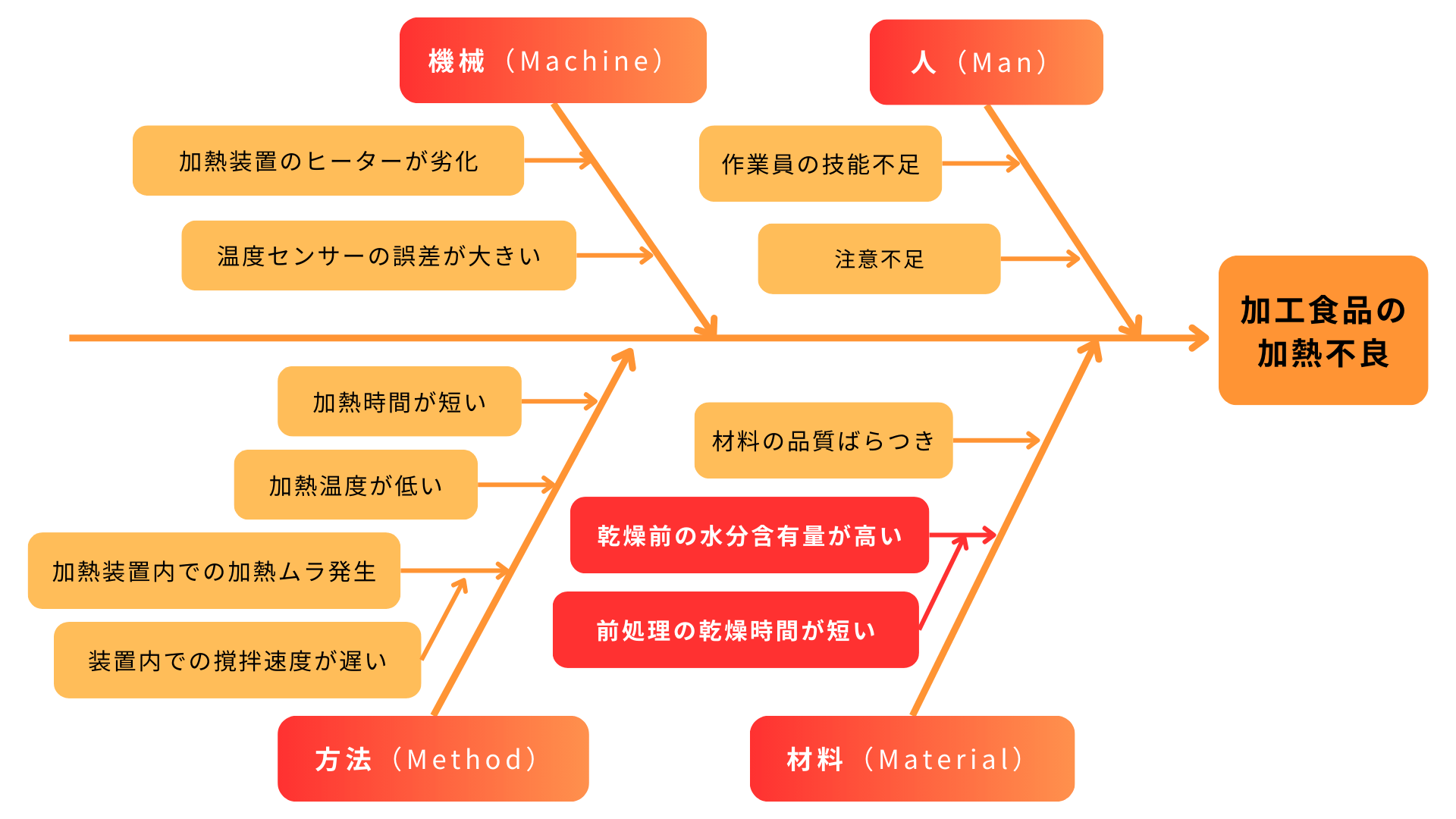
グラフ
グラフはデータを視覚化し、傾向やパターンを把握するための基本ツールです。品質管理によく使われるグラフと、それぞれの特徴は次の通りです。
- 棒グラフ: 数値の大きさを棒で表現した図で、複数項目の比較に適している
- 折れ線グラフ: 時系列データの変化を線で示した図で、トレンドや増減を見える化できる
- 円グラフ: 全体に対する各項目の割合を円で表現した図で、割合を視覚的に比較しやすい
- 帯グラフ: 複数の割合を横に並べた棒で表現した図で、データの階層が多い場合に比較しやすい
- レーダーチャート: 複数の評価項目を全体的に比較した図で、バランスを見える化できる
一例として、棒グラフ、円グラフを以下に示します。数値で直接示すよりも、直感的に状況を理解しやすいことがイメージできます。
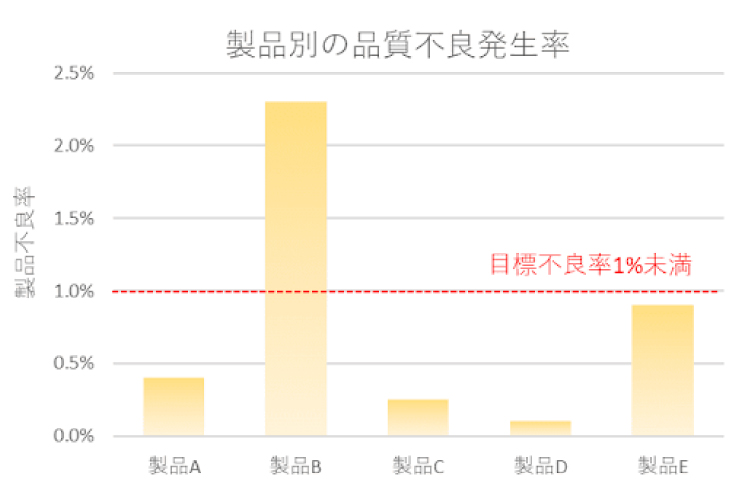
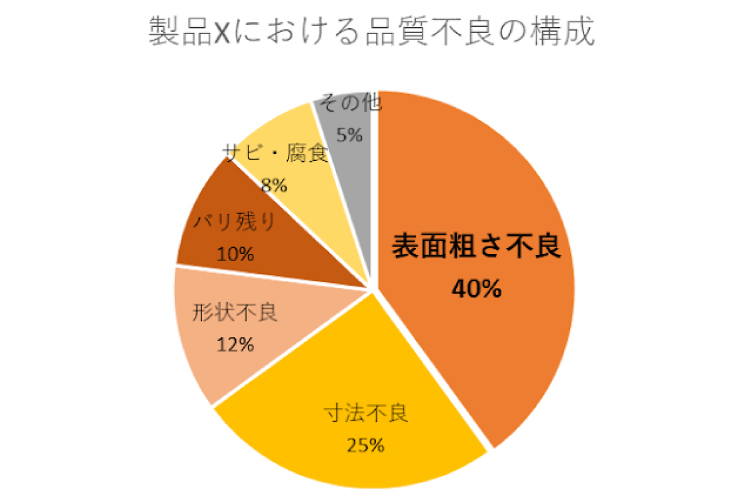
ヒストグラム
ヒストグラムは、データの分布を確認するためのツールで、製造プロセスが安定しているかどうかを一目で分かりやすく表現できます。例えば、金属加工製品Xの製品厚みについて、規格範囲10.0〜11.0mmに対する実績値をヒストグラムに示したものが次の図です。
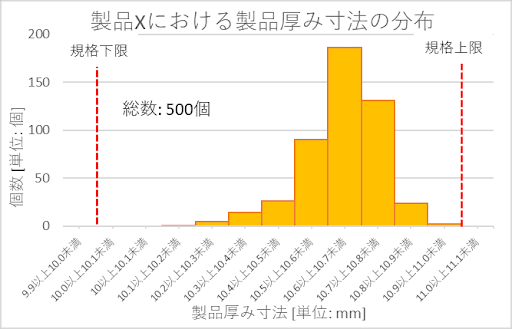
このヒストグラムから、以下のような事実が読み取れます。
- 厚み寸法はすべて規格値内におさまっていること
- ピーク値は規格中央よりもやや大きい方に偏っていること
- 工程能力について、規格上限付近の余裕はないが、規格下限は余裕があること
このように、グラフの形状を見ることで、測定したデータのピーク値、ばらつきなどを把握することができ、工程上の問題点などを推定するのに役立ちます。
散布図
散布図は、2つの変数の関係性を示すためのツールで、相関関係を視覚的に把握するのに有効です。一例として、製品出荷までの平均保管日数とサビ不良発生率、月平均温度と月ごとのサビ不良発生率の相関関係について、それぞれ散布図にまとめたものが次の図です。
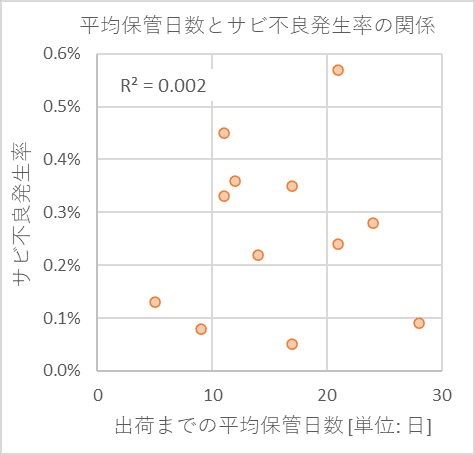
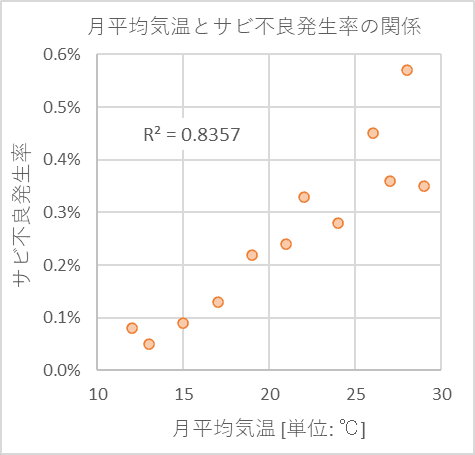
データを散布図で表すことで、注目した要因について、改善したい内容と関連があるかどうかを見極めることができます。この例では、出荷までの平均保管日数とサビ不良率に明確な相関は見られませんが、月平均気温とサビ不良発生率には強い相関があると分かります。そのため、サビ発生率を改善するには、特に気温の高い時期に特別な対策を講じる必要があると考えられます。
管理図
管理図は、工程や品質が安定しているかどうかを確認するためのツールです。時間の経過とともにデータを記録し、管理範囲の上下限(管理限界)を設定することで、工程の変動が許容範囲内であるかどうかを確認します。

管理限界を超えた場合だけでなく、以下に示す異常な傾向も、工程に不良や異常の兆候があることを示しています。こうした異常の原因を調べて、対策を行う必要があります。
- 7点以上が連続して中心線(CL)よりすべて上側または下側にいる
- 6点以上の上昇または下降が続く
- 周期的に増減する
- 中心線に近いデータが少ない
- データが上下交互に触れるパターンを示す
なお、QC7つ道具としては、管理図の代わりに、後述の層別分析を含める考え方もあります。
チェックシート
チェックシートは、現場でデータを簡単に記録・集計できるツールです。問題の発生頻度や発生箇所を記録し、定量的に分析するのに役立ちます。
チェックシートに決まった様式はありませんが、大きく分けて点検用と記録用の2つがあります。点検用チェックシートは、特定の作業や点検項目が確実に実施されたかどうかを確認するために使用されます。記録用チェックシートは、QCサークルでの改善活動など、特定の目的に沿ったデータの収集や記録を目的としています。
記録用チェックシートの例として、次のような金属加工製品の品質検査チェックシートを使うこともできます。
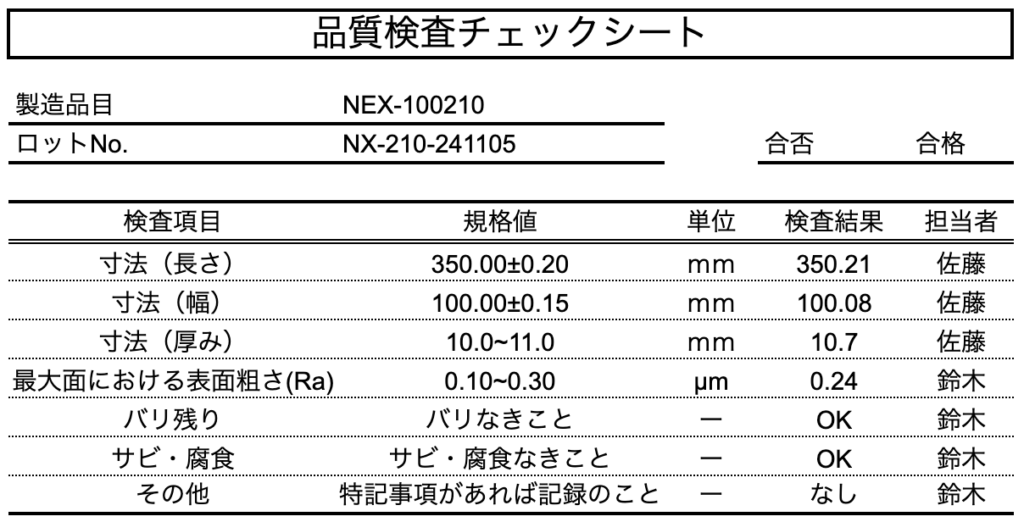
点検用、記録用いずれについても、あらかじめ項目がリスト化されていることで記録が容易となります。また、点検内容・基準を決めておくことで、同じ基準で品質確認を実施できます。用途に合わせたチェックシートを選び、目的に応じて様式を決めることで、実用的なチェックシートを作ることができます。
QC7つ道具の基本的な使い方【具体例付き】
QC7つ道具を効果的に使用するためには、問題を発見し、原因を分析し、改善策を実行する、というサイクルを繰り返します。ここでは、オーブンでクッキーを焼く製造工程を例に挙げ、QC7つ道具を使用した品質課題への取り組みの具体的な流れについて説明します。
製造プロセス・検査値を監視する
管理図やヒストグラムを使用して、製造工程が安定しているかを継続的に監視します。異常が発生する前に兆候を見つけることができれば、適切な対策を講じることができます。また、品質検査における検査値や工程パラメータのばらつきを視覚的に把握することで、速やかな課題の抽出が可能となります。
例えば、オーブンでクッキーを焼く工程において、オーブン内部の最高温度は重要なパラメータの一つです。クッキーは1日1回焼くため、オーブン処理日ごとの最高温度を管理図で表現しました。グラフ右のほうでは、中心線よりも下限側の点が続いていて、異常な傾向を示していることが分かります。
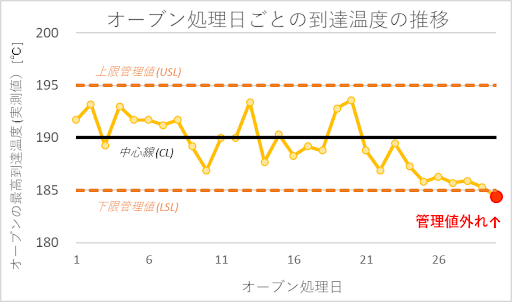
しかし、この事例では有効な対策を講じることができなかったため、下限管理値外れが発生してしまいました。
特性要因図で要因を整理する
まず、望ましくない事象について、考えられる要因を系統的に洗い出し、4M1E(人、機械、方法、材料、環境)の観点で整理します。抜け漏れがないように、十分な議論を重ねて特性要因図を作成することが重要です。
クッキーの事例において、オーブンの到達最高温度が低かったことに対する特性要因図を纏めました。これをもとに、優先順位をつけて分析を進めていきます。
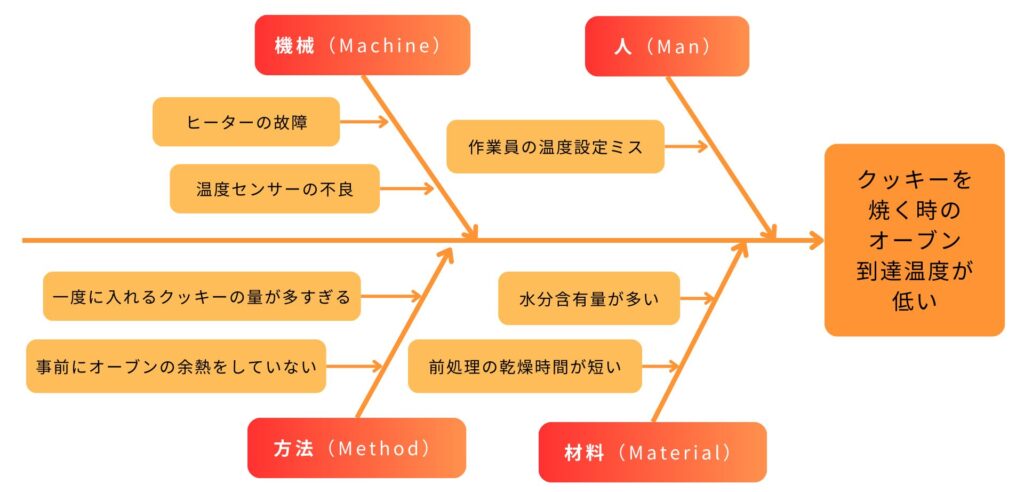
層別分析を組み合わせて問題を特定する
層別分析とは、データを異なる「層」(グループやカテゴリー)に分けて分析する手法で、データのばらつきや問題の原因をより明確にするために用います。データを細かく分けることで、それぞれの層における傾向や違いを見つけ、品質問題の原因・パターンを探しやすくなります。管理図の代わりに、この層別分析がQC7つ道具の一つとされることもあります。
層別分析では、4M1Eの観点で取得データを分けて、問題の原因となる対象を絞り込みます。特性要因図を参考にする具体例においては、次のような層別分析をすることが考えられます。
- 人による層別:作業者ごとの不良率を比較し、特定の作業者で不良が多い場合、その作業者に特有の問題があるかを調べる
- 機械による層別:使用する設備ごとに分けて分析し、特定の設備で不良率が高い場合、その設備に原因がある可能性を探る
- 材料による層別:材料ロット単位で比較し、特定の材料ロットで不良が多発する場合、その材料に問題がないか確認する
層別分析はパレート図やグラフ、チェックシートなど、他のQC7つ道具と組み合わせて使用することで、更に有効性が高まります。これにより問題の原因を絞り込むことができます。
クッキーの事例では、特性要因図で挙げた「材料の水分含有量が高い」という要因に注目して層別分析を行いました。具体的には、材料の全ロット(10個/ロット×10ロット)、管理値外れしたロット(1ロット)に分け、それぞれについて水分含有量と個数をヒストグラムで示した例が下記のとおりです。
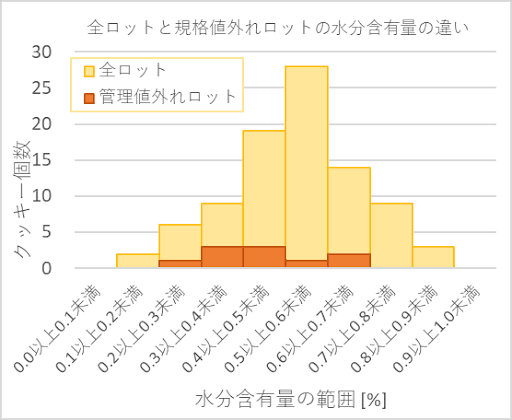
上記のヒストグラムでは、管理値外れロットは特別水分含有量が高くないので、管理値外れの要因ではないと判断できます。
このように、QC7つ道具と層別分析を組み合わせて、問題の特定につながるまで繰り返し分析を行います。分析を繰り返し行ったところ、ヒーターの故障がオーブン到達温度の管理値外れの原因であることが分かりました。
対策の効果を確かめる
問題を特定した後は、対策を実施してその効果を検証します。クッキーの事例では管理図で引き続き監視を行い、異常の兆候がないか確認すればよいでしょう。
定量的な分析が必要な場合は、対策前後におけるヒストグラムや散布図などを作成して、対策の効果を数値で把握します。データに基づく定量的な判断は、改善活動の信頼性を高めるために重要です。
参考:他の品質管理手法との比較
QC7つ道具は品質管理の基礎的なツールですが、他にも様々な品質管理の手法があります。
新QC7つの道具
新QC七7つ道具は、主に複雑な問題解決や品質改善のために、データやアイデアを整理・分析する際に使われる手法です。定性データを用いたり、複雑な問題を構造化したりすることで、チームでの意思決定をサポートします。具体的には次の7つの方法を指します。
- 親和図法:情報をグループ化し、問題の構造を整理する
- 連関図法:因果関係を視覚化し、複雑な問題の関係性を明確にする
- 系統図法:目標達成のための具体的な手段を階層的に整理する
- マトリックス図法:複数要素の関係を表で整理し、関連性を視覚化する
- マトリックスデータ解析法:数値データを分析し、要因間の関係性を明確にする
- アローダイヤグラム法:作業順序を矢印で表し、効率的な計画管理を行う
- プロセス決定プログラム図法(PDPC法):プロセス中の問題を予測し、対策を立案する
QC7つ道具と新QC7つ道具の違いは、以下の表の通りです。新QC7つ道具は、QC7つ道具よりも幅広い問題に対応できる一方で、使いこなしが難しいことが特徴です。
比較項目 | QC7つ道具 | 新QC7つ道具 |
対象データ | 主に定量データ | 数値化しにくい定性データ複雑な関係性や構造 |
使用目的 | 定量データを整理することで、製造現場の問題解決をサポート | 多くの情報・複雑な課題を構造化し、チームでの意思決定をサポート |
使いやすいさ | シンプルで現場従業員も使いやすい | やや高度で、グループ作業に適する |
適用範囲 | 製造工程や品質管理など、個別の問題の原因分析に特化 | 設計、企画、サービス、マーケティングなど、複雑な課題や部門連係を必要とする場面 |
トヨタ生産方式(TPS)
トヨタ生産方式(TPS)は、無駄をなくし効率的かつ高品質な生産を目指す手法で、ジャストインタイムや自働化、カイゼンを柱としています。
QC7つ道具では、個別の製造プロセスに着目した品質問題の解決に使われます。一方で、TPSはサプライチェーンも含めたシステム全体の最適化を通して、組織全体の生産性を向上させる取り組みです。
シックスシグマ
シックスシグマは、統計的手法を用いた品質改善と業務効率化のための方法論です。シックスシグマは、次に示す5つのステップ(DMAIC)を通じて、プロセスの改善と最適化を行います。
- Define(定義):改善したい問題や目標を明確に定義
- Measure(測定):プロセスのパフォーマンスを測定し、ベースラインを設定
- Analyze(分析):データを分析して問題の根本原因を特定
- Improve(改善):原因に対する具体的な改善策を実行
- Control(管理):改善が維持されるよう、プロセスを監視・管理
QC7つ道具はシンプルで現場従業員や品質管理担当者でも使いやすく、現場での品質改善に適しています。一方で、シックスシグマは、データ分析の専門家が統計的な手法を駆使して、プロセス全体の品質改善を行う際に用いられます。
22種類の生産管理システムをランキングで比較
初期費用相場や選び方のポイントをチェック
生産管理システムをそれぞれの特徴や初期費用相場などで比較したい場合は、「生産管理システムランキング」も是非ご覧ください。生産管理システムは、自社の製品・生産方式・企業規模などに適したものを導入しないと、得られるメリットが限定されてしまいます。事前適合性チェックや生産管理システムを選ぶ前に押さえておきたいポイントも解説していますので、製品選びの参考にしてみてください。