ABC分析とは 製造業の在庫管理への具体的な活用方法、注意点や方法まで解説
公開日:2024年05月28日
最終更新日:2025年01月29日
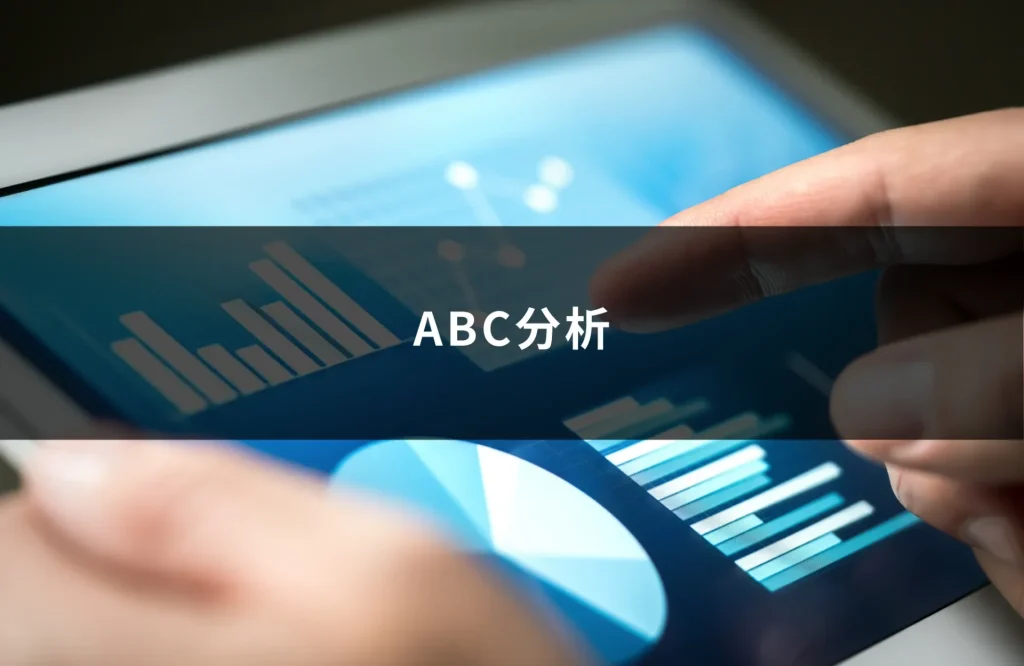
ABC分析とは、中堅、中小の製造業において効率的な在庫管理を行うために役立つ手法です。在庫の重要度を分析し、グループ分けして管理することで、在庫管理のリソース配分の最適化や、発注数・在庫数の検討などに役立てられます。
本記事では、ABC分析の具体的な分析方法、メリットや注意点、他の分析手法と組み合わせる手法について解説します。また、ABC分析に基づく在庫管理を効率化できる、在庫管理システムについても紹介します。
ABC分析とは
ABC分析は重点分析とも呼ばれ、在庫管理に限らず、品質管理や販売戦略の策定などさまざまな場面で利用されています。
在庫管理においては、在庫品を売上高や利益、販売数量などの観点から3つのグループ(A・B・C)に分類し、在庫管理状況を分析する手法として用います。ABC分析により、製品や部品在庫の品目ごとの価値や必要数、欠品時のリスクなどを定量化でき、最適な在庫管理方法を検討できます。
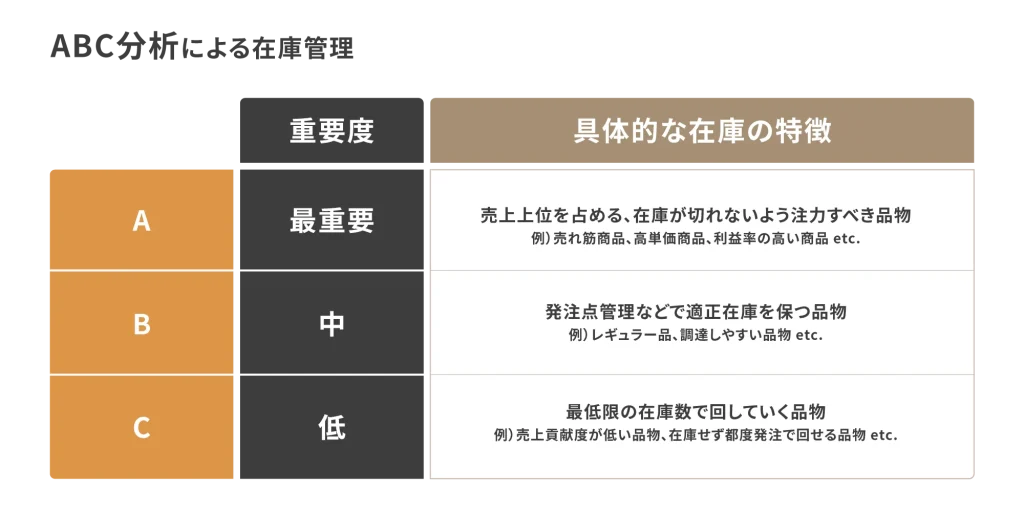
Aグループは、売上上位を占めるものや、高単価品など、欠品リスクが高い品物群です。在庫管理において、最も在庫切れを防ぐ必要がある品物といえます。
Cグループは、売上貢献が少ない製品が中心です。Cグループの製品を多く在庫しなければならない状況であれば、キャッシュフロー悪化の原因となる可能性があるため、製品の取り扱い自体を再検討することも考えられます。原材料の場合は、在庫せずに都度発注で回すべき品物群ともいえます。
Bグループは、A・Bどちらにも属さない品物群です。基本的には現状維持とし、売上比率が変わってきた場合などに再分析します。
また、製造業では、ABC分析を通して販売数量を分析することで、受注生産と計画生産のどちらにするかなどを数値で判断できるようになるメリットもあります。
ABC分析のベースとなる「パレートの法則」
ABC分析は、イタリアの経済学者ヴィルフレド・パレートが提唱した「パレートの法則」に沿った分析手法です。パレートの法則とは、全体の成果の大部分が、比較的小さな要因や要素に由来するという経験則で「80:20の法則」とも呼ばれます。
製造業に例えると
- 売上の80%が、上位20%の製品や顧客によってもたらされる
- 製品の不良やクレームの80%が、原因の20%(特定の工程、部品、機械)に起因する
- 全在庫品目のうち、需要の80%が20%の品目で構成される
- 生産量の80%が、20%の主要設備によって生み出される
- 品質トラブルの80%が、20%の原材料や仕入れ先に由来する
などがあげられます。
パレートの法則は必ずしも正確な割合を示すものではありませんが、多くの分野で効率的な管理や戦略立案に役立つ考え方です。
ABC分析の目的
ABC分析を行う主な目的は、売上(利益)貢献の大部分を占める重要な製品(Aグループ)とそうではない多数の製品(Cグループ)を特定し、適切に管理することです。特に、Aグループ品の在庫不足による納期遅れや販売機会損失を防止したり、過剰な在庫を削減したりする重要性は高いと言えます。
例えば、ABC分析を行って在庫管理の方針を決める場合、
- Aグループ品目:需要予測を活用して安全在庫を確保し、在庫切れを防ぐ
- Bグループ品目:適切な発注量を維持し、管理コストを抑える
- Cグループ品目:在庫量を削減し、必要なときに都度発注する方針を採用する
などといった管理方法を検討できます。重要度に応じて管理方法を変えることで、保管スペースや予算を効率的に配分し、コスト削減と安定供給を実現できます。
ABC分析のメリット
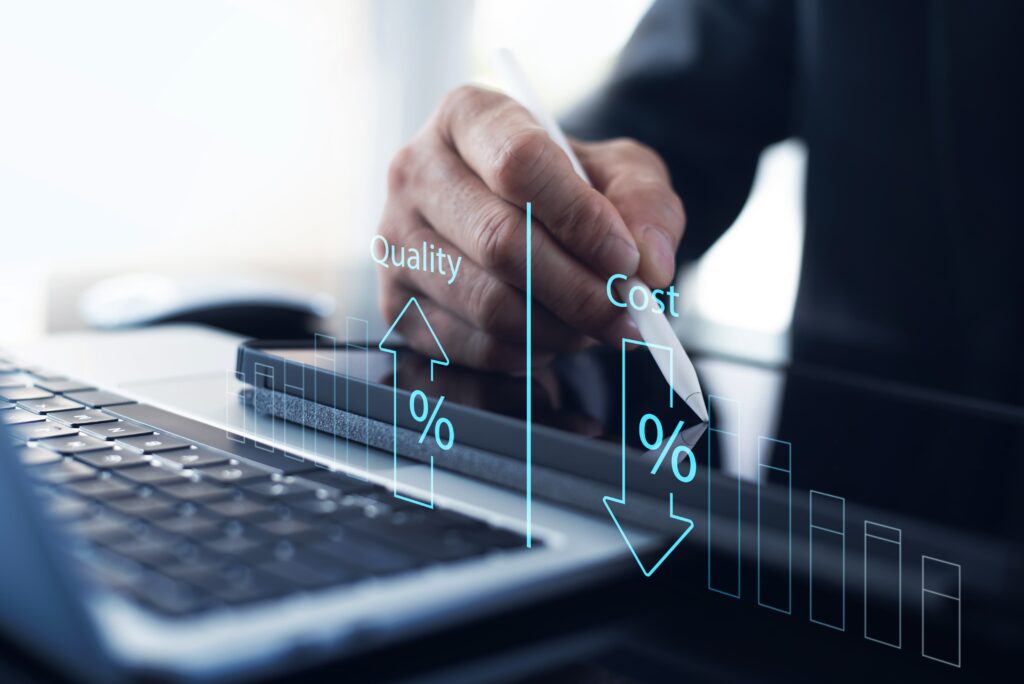
ABC分析を活用することで、在庫管理やサプライチェーンの最適化、生産効率の向上などさまざまなメリットが得られます。
在庫管理の効率化
製造業では、保管スペースや管理コストが発生することから、全ての在庫品目を均等に管理するのは非効率です。ABC分析を活用して、在庫品目をA、B、Cグループに分類することで、発注管理の優先順位を明確化できます。
例えば、Aグループ品は、生産ラインに欠かせない高価な精密部品や需要の多い主要製品の部材のため、在庫量を常に適正に保つための定期的な在庫確認や、発注タイミングを短く設定するなどの重点的な管理が必要です。
一方で、BグループやCグループ品は、生産に直接影響しない補助材料や低頻度で使用される部品や製品に分類されるため、定期的な在庫見直しや、必要時に発注する方式を採用することで管理を簡素化できます。
サプライチェーンの最適化
Aグループ品は顧客需要が集中する主要製品の部材が該当するため、これらの品目については、信頼性が高く品質の安定したサプライヤーを選定し、長期契約を結ぶことで供給リスクを低減できます。
具体的には、複数のサプライヤーに依存するのではなく、主要サプライヤーと協力してリードタイムを短縮したり、安全在庫の設定を事前に協議します。さらに、緊急時に備えて代替供給ルートを確保し、供給の中断を防ぐ体制を整えるなど、サプライチェーンの最適化を検討できます(参考:2社購買とは)。
一方で、Cグループ品については、定期的な在庫補充ではなく、実際の消費状況に応じて発注を行う方式(都度発注、ジャストインタイム方式など)を活用することで、過剰在庫のリスクを回避します。
生産停止リスクの低減と生産効率の向上
Aグループ品を重点的に管理することで、部品不足が原因で生産ラインが停止するリスクを大幅に低減できます。
例えば、リードタイムに数ヶ月かかるAグループ品は、生産数日前に在庫不足が判明すると、生産停止や遅延を避けられません。そのため、納期管理を丁寧に行う必要があります。逆に、都度発注を行うCグループ品なら、生産数日前に欠品が判明しても急ぎ発注で間に合う可能性が高いため、こまめな在庫確認に手間をかける必要はありません。
また、データを基に供給計画を最適化することで、生産ラインでの部品供給がスムーズになり、設備の稼働率を向上でき、生産効率の向上につながります。
ABC分析のやり方
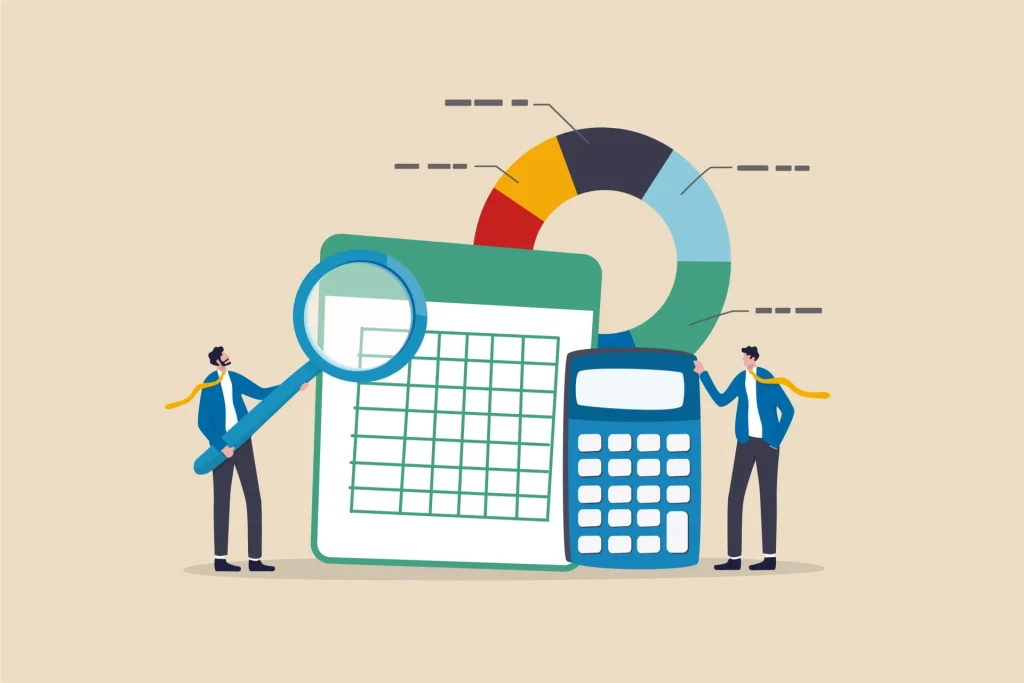
売上高をベースとしてABC分析を行う場合は、次のステップで行います。
- 各製品の売上げを算出して並べる
- 売上げの高い順番に並べる
- 累積額を集計する
- 累積構成比を計算する
- A・B・Cのグループ分けを行う
各製品の売上げを算出して並べる
まず、各製品の年間売上高や使用頻度などのデータを収集します。具体的には、原価管理システムや販売管理システムなどから製品名と売上高をリスト化し、リストアップしていきます。製品をA~Gの7種類とした場合、以下のようなリストになります。
■ABC分析 製品別売上高(例)
売上単価(万円) | 販売個数(個) | 合計売上(万円) | |
製品A | 10 | 400 | 4000 |
製品B | 5 | 200 | 1000 |
製品C | 3 | 400 | 1200 |
製品D | 8 | 300 | 2400 |
製品E | 20 | 80 | 1600 |
製品F | 6 | 400 | 2400 |
製品G | 7 | 100 | 700 |
売上げの高い順番に並べる
次に製品の合計売上高を高い順に並べ替えます。エクセルやスプレッドシートなどの表計算ソフトを使い、売上高の降順にデータを並べます。
売上単価(万円) | 販売個数(個) | 合計売上(万円) | |
製品A | 10 | 400 | 4000 |
製品D | 8 | 300 | 2400 |
製品F | 6 | 400 | 2400 |
製品E | 20 | 80 | 1600 |
製品C | 3 | 400 | 1200 |
製品B | 5 | 200 | 1000 |
製品G | 7 | 100 | 700 |
累積額を集計する
並べ替えが完了したら、売上高を上位から順番に足し上げていき、累積額を算出します。累積額の集計により、特定の製品群がどれほど全体の売上高を占めているかが明確になります。
売上単価(万円) | 販売個数(個) | 合計売上(万円) | 累積額(万円) | |
製品A | 10 | 400 | 4000 | 4000 |
製品D | 8 | 300 | 2400 | 6400 |
製品F | 6 | 400 | 2400 | 8800 |
製品E | 20 | 80 | 1600 | 10400 |
製品C | 3 | 400 | 1200 | 11600 |
製品B | 5 | 200 | 1000 | 12600 |
製品G | 7 | 100 | 700 | 13300 |
累積構成比を計算する
次に、累積額を全体の総売上高で割り、累積構成比(%)を計算します。
構成比は、製品が全体の売上に占める割合を示します。累積構成比を計算することで、製品の重要度を数値化し、客観的に評価できるようになります。
売上単価(万円) | 販売個数(個) | 合計売上(万円) | 累積額(万円) | 累積比率 | |
製品A | 10 | 400 | 4000 | 4000 | 30.1% |
製品D | 8 | 300 | 2400 | 6400 | 48.1% |
製品F | 6 | 400 | 2400 | 8800 | 66.2% |
製品E | 20 | 80 | 1600 | 10400 | 78.2% |
製品C | 3 | 400 | 1200 | 11600 | 87.2% |
製品B | 5 | 200 | 1000 | 12600 | 94.7% |
製品G | 7 | 100 | 700 | 13300 | 100.0% |
A・B・Cのグループ分けを行う
最後に、累積構成比を基に製品をA・B・Cの3つのグループに分けます。グループ分け基準については、全体の構成を見ながら決定します。
例として
- Aグループ:累積構成比が70~80%を占める製品
- Bグループ:累積構成比が15~20%を占める製品
- Cグループ:残りの製品
といった決め方があります。
各製品の売上と累積構成比をグラフにすると以下のようなイメージになります。
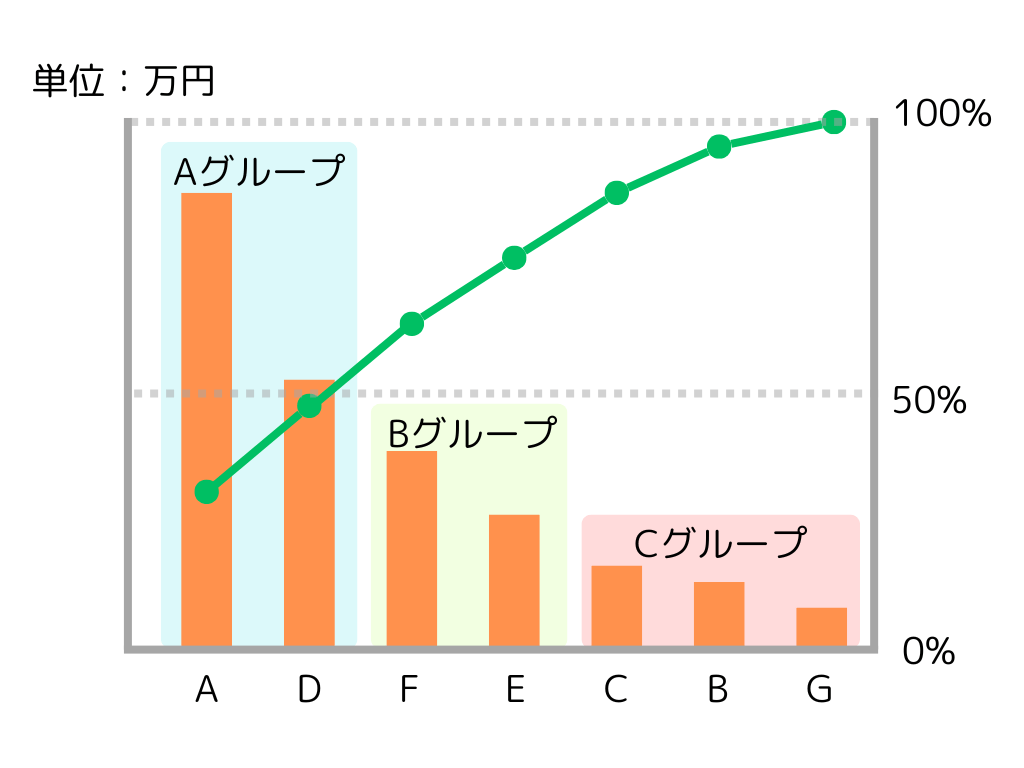
ABC分析の注意点
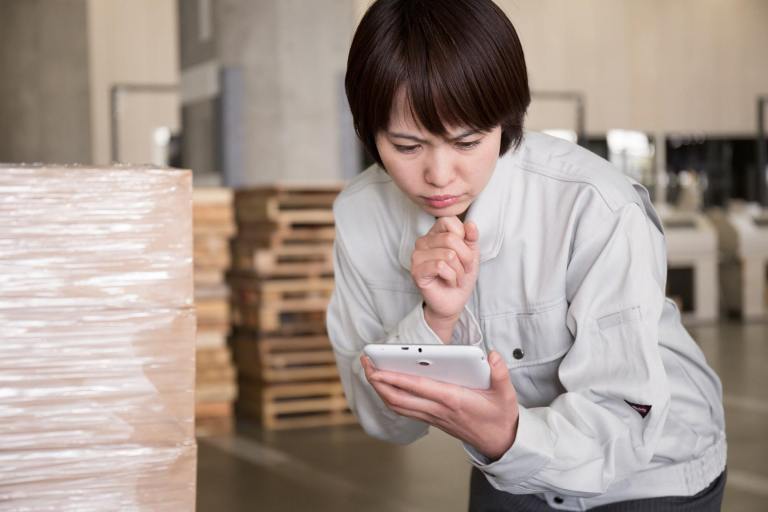
効率的な在庫管理に役立つABC分析ですが、適切に活用するためにいくつか注意点があります。
季節限定商品、見せ筋商品に注意する
季節限定商品や見せ筋商品など、特定の期間に集中して売上が上がる製品は、通常のABC分析では適切に評価できない場合があり、分析時に個別で評価する必要があります。
一時的に販売数量が増加している製品の場合、そのデータをもとに生産計画を立てないよう注意が必要です。
仕入先のリードタイム等を考慮しなければならない場合がある
仕入先のリードタイムや、その他の供給関係の問題も考える必要があります。例えば、海外工場に発注するためリードタイムが長い製品などは、売上構成として大きくなくても、注意して在庫管理する必要があります。単純な売上のみではなく、さまざまな状況を考慮し、総合的に判断する必要があります。
定期的な見直しが必要
ABC分析を実施して重要な製品が特定できても、市場は常に変化するため、定期的な見直しが必要です。必要在庫数に対して自動発注などの設定を設定している場合は、状況が変化していないか定期的にABC分析を実施しましょう。
複数の観点からグループ分けを行う
製品や在庫のグループ分けを行う場合、売上などの単独の観点ではなく、利益、販売数量、製造工数など複数の観点からABC分析を行うことが重要です。売上が大きく、販売数量が多くても利益が小さい製品であれば重要度が下がるなどの可能性があります。
ABC分析と他の在庫分析手法との組み合わせ
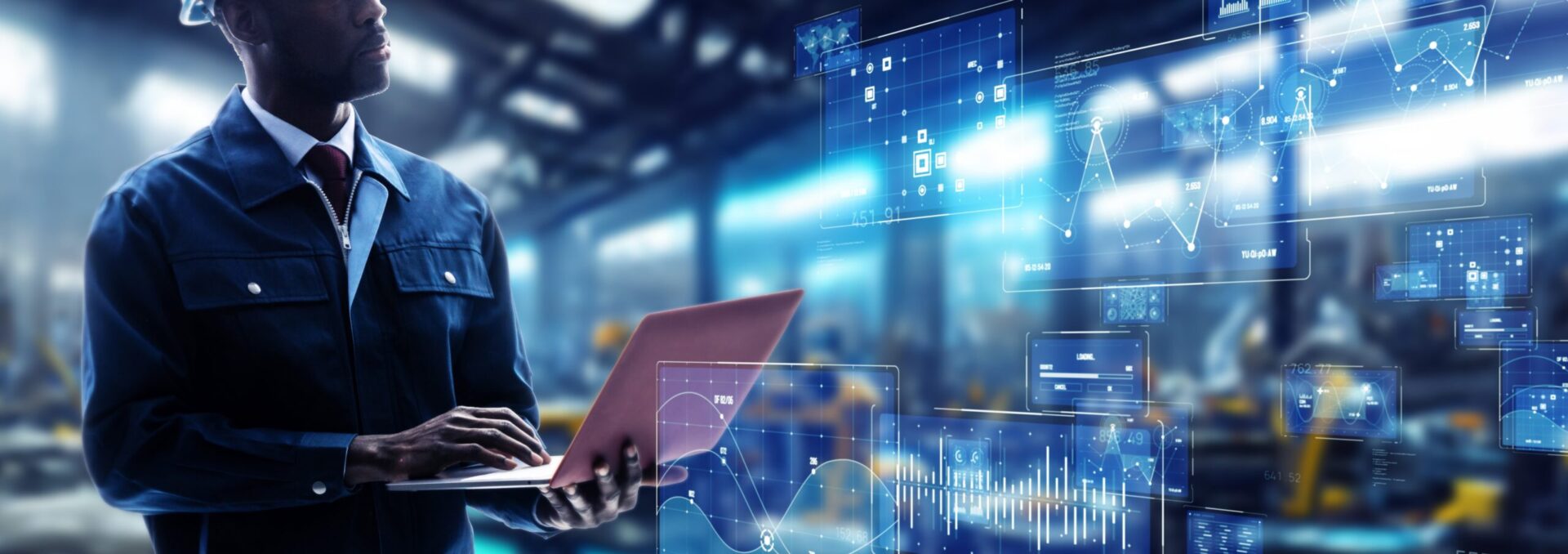
ABC分析は、他の在庫分析手法と組み合わせることで、さらに効率的な在庫管理が可能になります。
ここでは、ABC分析と在庫回転率分析、在庫回転期間分析、交差比率分析、死蔵在庫・緩動在庫分析を組み合わせた活用方法について解説します。
在庫回転率分析
在庫回転率分析は、一定期間内に在庫がどれだけ回転しているかを評価する手法です。回転率は以下の式で計算されます。
在庫観点率分析により、在庫が効率的に使用されているかを把握できます。
ABC分析でAグループに分類される重要品目は、回転率を高く維持することが理想的です。在庫回転率分析を併用することで、Aグループ品目の動きを定量的に評価し、適切な補充タイミングや量を検討できます。
一方、BやCグループの品目については、過剰な在庫を防ぎながらも、一定の回転率を維持するバランスが求められます。この組み合わせにより、重要品目を最優先にしつつ、全体の在庫効率を最大化することができます。
→ 在庫回転率とは
在庫回転期間分析
在庫回転期間分析は、在庫が消化されるまでにかかる日数を評価する方法です。在庫回転期間は以下の式で計算されます。
在庫回転期間分析を用いると、ABC分析で分類された各グループの品目がどれくらいの期間で消費されているかを把握できます。
特にAグループの品目で回転期間が長い場合、サプライチェーンや生産計画に改善の余地があることがわかります。
→ 在庫回転期間とは
交差比率分析
交差比分析は、在庫がどれだけの利益を上げているかを評価する方法です。交差比率は以下の式で計算されます。
交差比率は単に在庫がどれだけ速く動いているかだけでなく、どれだけの利益を生み出しているかも考慮します。
Aグループ商品については、在庫切れを防ぐために発注頻度を高めて売上を最大化させ、Bグループ商品は、需要予測を活用して過剰在庫を防ぎつつ、適正在庫を維持することを目指します。一方で、Cグループ商品については、基本的には在庫を最小限に抑えますが、交差比率が高い場合には積極的な販売促進や在庫量の見直しを行うなどの方針を立てられます。
死蔵在庫・緩動在庫分析
死蔵在庫と緩動在庫分析は、動きが少ないまたは全くない在庫を特定する手法です。
- 死蔵在庫: 一定期間(例:6カ月以上)全く動きがない在庫
- 緩動在庫: 動きが非常に遅い在庫
これらの在庫は、資金の無駄な固定や保管費の発生につながります。
ABC分析では、Cグループの品目が過剰在庫や死蔵在庫となりやすい傾向があります。死蔵在庫・緩動在庫分析を活用することで、これらの在庫を特定し、値引き販売や廃棄処分を計画できます。
また、AグループやBグループの品目で動きの悪い在庫があれば、過剰生産や需要予測の精度に問題がある可能性があります。
ABC管理に在庫管理システムが役立つ理由
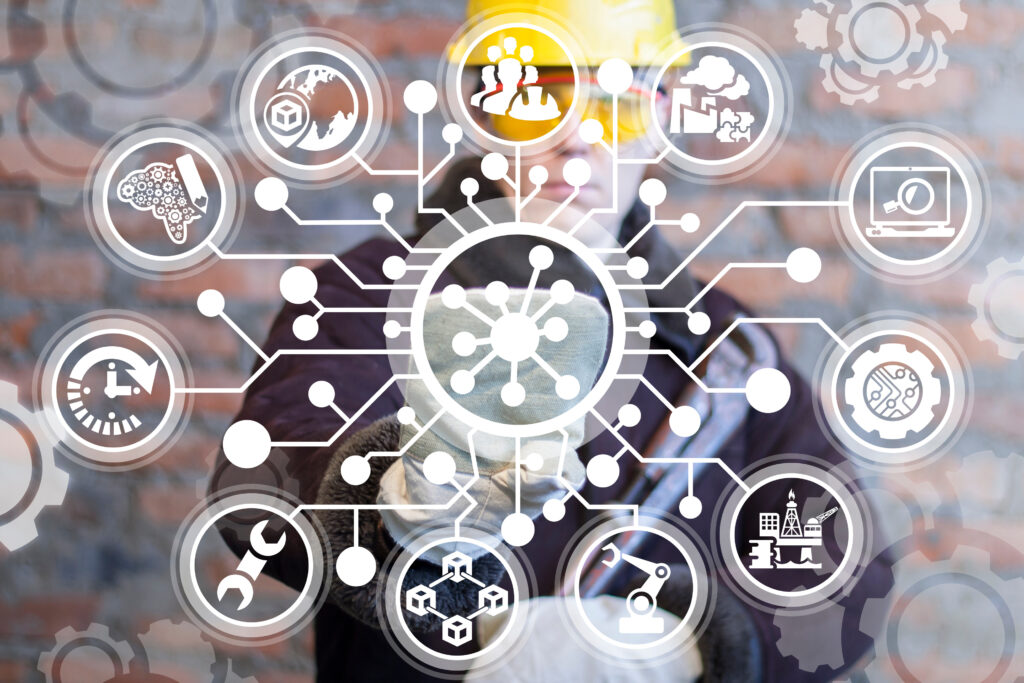
ここまで見てきた通り、ABC分析は適切な在庫管理を行う上で非常に重要な手法です。しかし、市場の変化により定期的に見直す必要があり、その都度売り上げデータや販売数量を集計すると手間と時間がかかります。
効率的にABC分析を行うためには、日々の生産状況から在庫データを自動的に集計・分析・可視化する機能を備えた、在庫管理システムの利用がおすすめです。クラウド型などの月額制システムを利用すれば、初期投資が数千万円規模で必要となるオンプレミス型と比較して低コストで導入できます。
22種類の生産管理システムをランキングで比較
初期費用相場や選び方のポイントをチェック
生産管理システムをそれぞれの特徴や初期費用相場などで比較したい場合は、「生産管理システムランキング」も是非ご覧ください。生産管理システムは、自社の製品・生産方式・企業規模などに適したものを導入しないと、得られるメリットが限定されてしまいます。事前適合性チェックや生産管理システムを選ぶ前に押さえておきたいポイントも解説していますので、製品選びの参考にしてみてください。