タクトタイムとは?計算方法、適切な設定のコツ、生産管理システムの活用方法まで詳しく解説
公開日:2024年05月27日
最終更新日:2025年02月28日
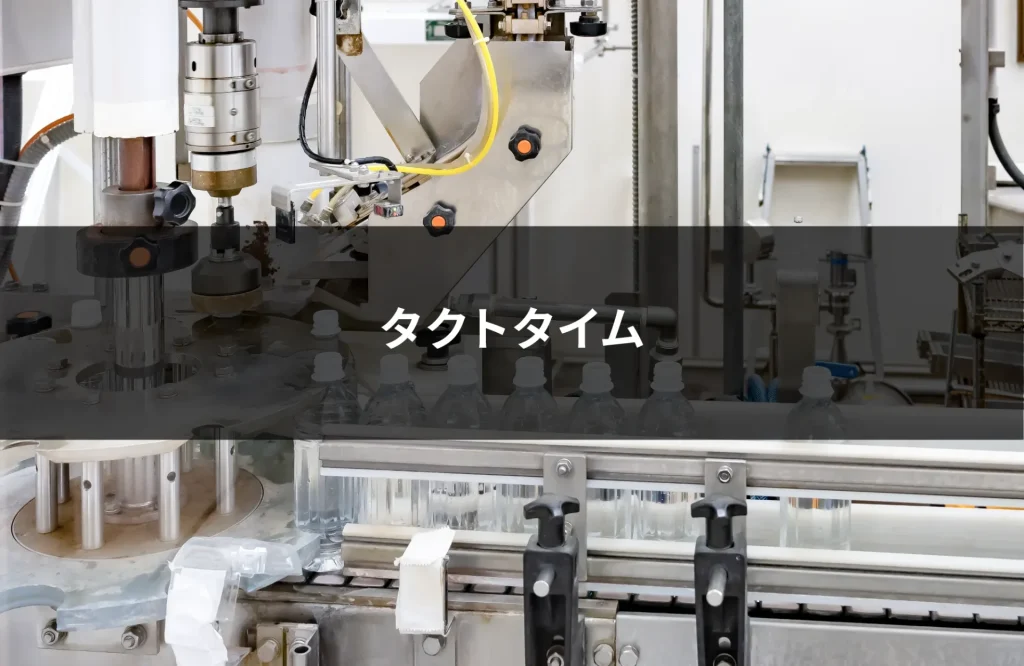
タクトタイムとは、目標となる生産ペースを示す指標です。特に繰り返し作業が多い現場において、生産性向上や在庫適正化を実現するために欠かせない管理項目です。本記事では、タクトタイムの計算方法をはじめ、混合されやすいサイクルタイムやリードタイムとの違いを詳しく解説します。
また、生産管理においてタクトタイムの設定が重要である理由、理想的なタクトタイムを設定する際に押さえるべき3つのポイントを紹介します。
タクトタイムとは:生産ペースの指標
タクトタイム(T/T)とは、お客様の注文に応じて、どれくらいのペースで製品1つを作ればよいかを示す時間の目安です。ピッチタイムと呼ばれることもあります。
生産計画を立てる際、1日単位で生産目標数量を決めていることも多いでしょう。しかし、「このペースで作り続けて目標を達成できるのか?」 や、「生産スピードに過不足がないか?」 を現場の作業者が感覚的に把握するのは難しいものです。
円滑な生産管理を実現するために、タクトタイムを適切に設定・管理することは重要なポイントとなります。
ちなみに「タクト」とは、指揮者が振る指揮棒であるタクトシュトックに由来し、拍子・リズムという意味があります。大人数の楽器演奏では、指揮者が均等なリズムを導くためにタクトを振ります。これが転じて、製造業では、生産のリズムを作るためにタクトタイムという言葉が使われるようになりました。
タクトタイムの計算方法
タクトタイムは、顧客からの注文をベースとした生産計画で決まり、以下の計算式で求めます。
タクトタイムの計算式
タクトタイム=利用可能な作業時間(1日の稼働時間) ÷ 需要量(1日の必要生産数)
例えば、1日の稼働時間が7時間(420分)で、1日に100個の製品を生産する必要がある場合、タクトタイムは4.7分と計算されます。これにより、4.7分ごとに1つの製品を完成させるペースで作業すれば、1日の生産目標を達成できることになります。
サイクルタイム・リードタイムとの違い
タクトタイムと関連する言葉に、サイクルタイムと 、リードタイムが挙げられます。特にサイクルタイムは、タクトタイムと混同して使われるケースも多いです。
サイクルタイム(C/T)は実際の生産時間、製品1個分の作業の完了にかかる時間を指します。リードタイム(L/T)とは、一般的に、まとまった製品数量について、工程の生産開始から終了までの全体の所要時間を指します。「製品1個をこの時間で生産できれば、需要に応えられる数量を生産できる」という理論値を示すのがタクトタイムで、実際の生産にかかった実測値がサイクルタイム、ということです。
用語 | 定義 | 目的 |
タクトタイム | 顧客需要に応じて決まる、製品1個の生産ペース(目標) | 生産計画の適正化 |
サイクルタイム | 製品1個の生産に要する時間(現場の実態) | 生産ラインの効率を評価 |
リードタイム | まとまった生産数量における、工程の開始から終了までの時間 | 顧客とのコミュニケーション、自社内の生産計画・納期管理に活用 |
なぜタクトタイムが重要なのか
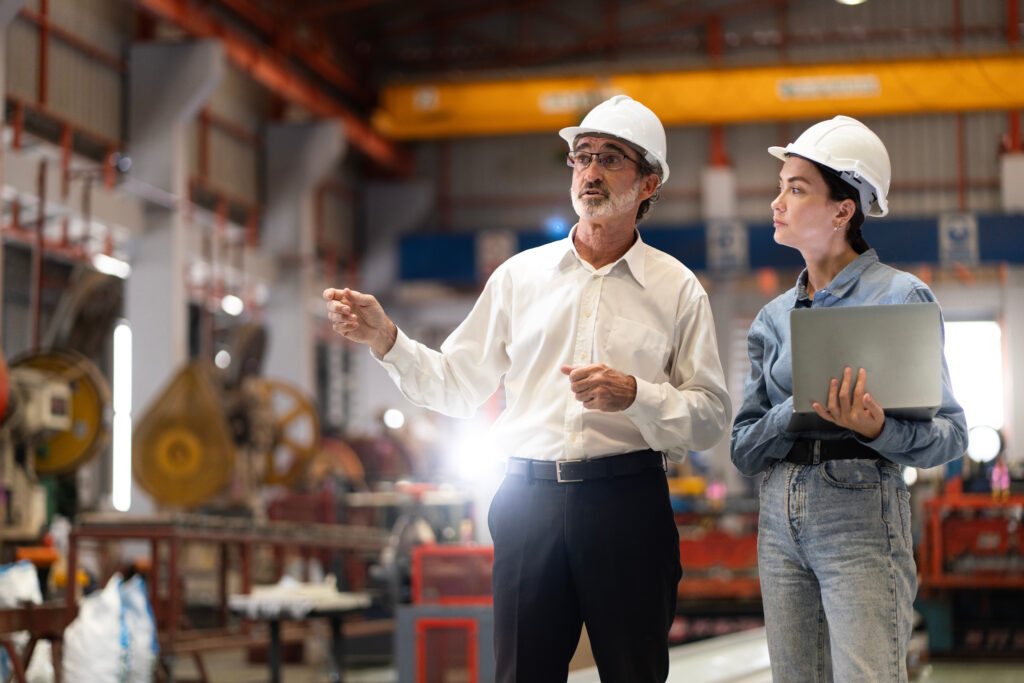
タクトタイムは製造現場で守るべき生産ペースの指標なので、顧客需要に基づく生産計画を確実に達成するために欠かせません。
特に、繰り返し作業が伴う生産ラインでは、製品1個ごとの僅かな遅れが積み重なり、生産性が下がりやすいという課題があります。タクトタイムを明確にすることで、生産活動において一定以上の作業効率を維持し、生産面・品質面の継続的な改善を実現します。
標準作業の3要素の一つが「タクトタイム」
最も効率的に作業できるように定めた製造現場のルールを標準作業と呼び、その3つの構成要素の一つがタクトタイムです。具体的には次の表のとおりです。
要素 | 役割 |
タクトタイム | 顧客の注文・希望納期に応えるために、必要な生産ペースを決める |
作業順序 | 各工程での作業の流れを最適化する |
標準手持ち | 部品・仕掛品が適正在庫量を保てるように管理する |
このように、標準作業の3要素は、現場の作業の効率化、品質の向上、安全性の確保に寄与し、生産性を改善するための重要な取り決めです。
タクトタイムは標準作業の中核
標準作業の3要素のうち、タクトタイムは作業順序や標準手持ちを設定する根拠となる中核的な要素です。
特に、短いタクトタイムが必達目標となる場合、生産時間を短縮できる作業順序を採用し、それに適した生産ラインを構築する必要があります。設備投資の負担が大きくなったり、技術的な難易度が高くなったとしても、目標のタクトタイムを実現できる工程設計が欠かせません。
また、部品の供給タイミングをタクトタイムに合わせて調整すれば、在庫確認や一時保管によるムダが減り、スムーズな生産が実現します。
このように、タクトタイムの適切な設定は、生産ラインの全体最適を実現するための重要な指標 となります。
作業者・リーダー・管理者すべての立場で重要
作業者・リーダー・管理者それぞれの視点からも、タクトタイムの設定には以下のようなメリットが得られます。
- 作業者:作業ペースの意識により適度な緊張感を生み、繰り返し作業のマンネリ化を防ぐ
- リーダー:ムリ・ムラ・ムダを削減し、理想的なモノの流れ(整流化)に近づける
- 管理者:人的・設備リソースを最適化できる
このように、タクトタイムは、様々な立場の従業員の立場において、生産ラインの効率化・リソース管理に活用されます。
タクトタイム設定は生産効率改善の第一歩
生産ペースの基準であるタクトタイムを適切に設定することは、生産性を高め、無駄のない生産ラインを作るための第一歩です。タクトタイムを設定すると生産効率が上がる理由は次の通りです。
- 過剰生産の防止:必要な分だけ生産できる体制となり、不要な在庫を抱えずに済む
- 作業ペースの標準化:工程間・工程内のバラつきをなくし、ムダな動きを減らせる
- 作業遅れの早期発見:トラブルが発生してもすぐに気づき、迅速な対応ができる
ただし、これらの効果を十分に発揮するには、タクトタイムの適正化に向けた継続的なカイゼンが不可欠です。特に繰り返し作業の多い生産現場では、効率化を推進するための指標として、タクトタイムは極めて有効です。
タクトタイムとサイクルタイムの関係性
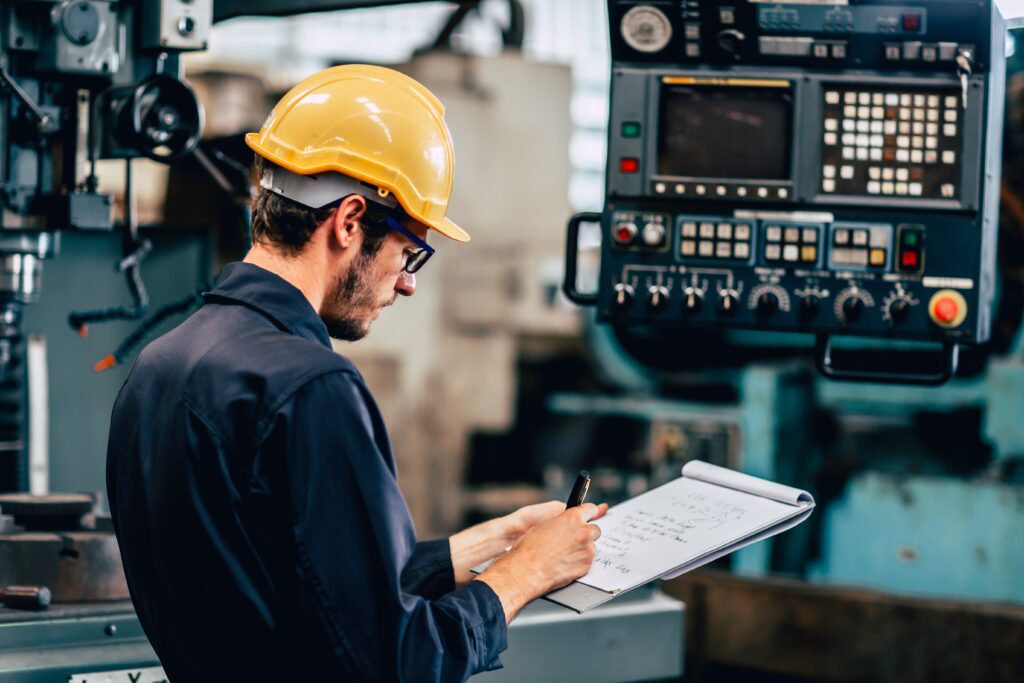
タクトタイムとサイクルタイムの関係は、生産効率を議論する上で重要な考え方です。
生産管理業務の中でタクトタイムを短縮すれば、多くの需要に応えられる生産計画となり、生産性向上を加速します。しかし、サイクルタイムとのバランスを取らなければ、現場にムリな負担をかけるリスクもあります。
そのため、タクトタイムを短縮する際は、サイクルタイムの最適化(工程改善・自動化・作業標準化)とセットで取り組むことが重要です。
「タクトタイム=サイクルタイム」が理想の状態
タクトタイムとサイクルタイムが同じ状態は、製品の需要と供給が釣り合っている理想的な状態です。
ネジの製造・販売を例に挙げて説明します。まず、ネジAの顧客出荷数をもとに、タクトタイムを算出します。顧客出荷数は1日当たり12600本で、1日の稼働は7時間(25200秒)とすると、以下の式よりタクトタイムは0.5秒/本となります。
7時間/日 × 60分/時間 × 60秒/分 = 25200 秒/日
12600本/日 ÷ 25200秒/日 = 0.5 秒/本
次にサイクルタイムについて考えます。ネジAの製造は、コイル状の材料を仕入れ、順に切断、圧造、転造して、最終製品となります。設備1台当たりの最大処理能力は各工程で異なりますが、設備台数を最適化して、生産ラインのサイクルタイムをネジ1本あたり0.5秒としています。
このサイクルタイムでは、1日7時間稼働すると、次の式より1日12600本生産できることになります。
0.5秒/本 × 60秒/分 × 60分/時間 × 7時間/日 =12600 本/日
つまり、この場合、タクトタイム・サイクルタイムともネジ1本あたり0.5秒です。このペースが守られていれば、顧客需要数と生産数が釣り合っており、欠品や過剰在庫が発生しない理想的な状態と言えます。
「タクトタイム<サイクルタイム」の場合の問題点
タクトタイムがサイクルタイムより短い場合、生産が需要に追いついていないといえます。
上記のネジAの例で、切断工程の設備不良が重なり、気づいた時にはサイクルタイムが0.5秒/本から半減し、1.0秒/本に低下したとします。この場合、この生産ライン全体のサイクルタイムも1.0秒/本となり、製造可能な本数は12600本/日から半減します。
しかし、顧客需要は変わらないので、タクトタイムも0.5秒/本のままです。この場合、製品の欠品が発生し、不足分は納期遅延や失注となります。
今回のケースの場合、タクトタイムを意識した運用であれば、サイクルタイムが少し下がった時点で問題が判明し、早期対策ができたかもしれません。
「タクトタイム>サイクルタイム」の場合の問題点
タクトタイムがサイクルタイムより長い場合、生産が需要を上回っていることを意味します。
例えば、1日当たりの顧客需要が12600本から半減して6300本となった場合を考えます。この場合、次の式より、1日7時間稼働を前提としたタクトタイムは0.5本/秒から0.25本/秒と計算されます。
7時間/日 × 60分/時間 × 60秒/分 = 25200 秒/日
6300本/日 ÷ 25200秒/日 = 0.25 秒/本
しかし、特別な指示をしなければサイクルタイムは0.5秒/本なので、ネジ1本あたり0.25秒の余裕が生まれます。このまま同様に生産を続けた場合、無駄な在庫が増えたり、過剰な生産コストが発生します。大幅な顧客需要の変動があった場合は生産計画を見直し、これに基づいたタクトタイムに合わせた生産ペースの調整が必要です。
タクトタイム設定における3つのポイント
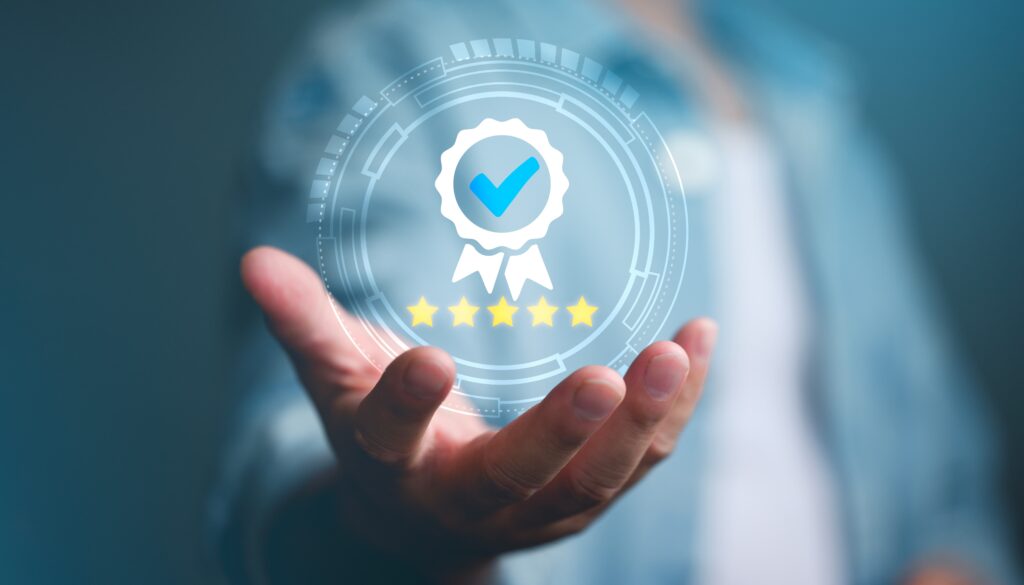
タクトタイムは、顧客受注量から単に計算して終わりではありません。タクトタイムの設定には、正確な受注量を把握し、生産状況に合わせて適切に設定・管理していく必要があります。
顧客の注文量を正しく把握する
タクトタイムを決める基本は、顧客の注文量を正確に把握することです。注文量を過大に見積もると過剰生産により在庫が増加し、過小に見積もると欠品が発生して納期遅延を招きます。
受注生産の場合には、実際の受注状況や顧客から提供される需要予測(フォーキャスト)をもとに、生産計画に落とし込みます。これに対して、見込み生産では、生産計画を立てる時点で注文量が確定していません。そのため、過去の受注実績データの分析や、機械学習・AIを活用した需要予測などを行い、予測精度を高めます。
生産余力を考慮する
生産には予期せぬトラブルが発生するため、タクトタイムの設定では、ある程度の余裕(バッファ)を織り込む必要があります。
品質不良や機械トラブルなど、工程改善を重ねれば減らせるトラブルもありますが、未然防止が難しい突発的な作業者の欠勤なども影響します。このようなトラブルについて、バッファの目安は次の表のとおりです。
トラブル内容 | バッファの考え方の目安 |
品質不良 | 製品歩留まりを考慮して、生産余力を見込む |
設備トラブル | タクトタイムの5~10%程度の余力を見込む |
作業者の欠勤 | 数人規模のチームで、作業者1名分の負荷を分散できるようにする |
具体的なトラブル内容は起こってみないとわかりませんが、日々起こる小さなトラブルを吸収できる程度の余力は持つべきです。ただし、余力を大きく取りすぎると無駄の多い非効率なラインになるため、実際の現場の状況を踏まえて、適正な余裕を設けるようにしましょう。
定期的な見直しルールを決めておく
一度設定したタクトタイムは、定期的な見直しが必要であり、その頻度・タイミングに関するルールが必要です。頻繁なタクトタイムの変更は現場の混乱を招くケースも多く、タイムリーな変更は現実的ではありません。
毎日の実績確認や月単位での受注状況分析、一定以上の市場変化があった場合など、見直しルールをあらかじめ決めておきます。これにより、最適なタクトタイムを維持でき、生産効率の改善につながります。
ただし、受注数量の急増で大幅なタクトタイム短縮が求められたとしても、設備・製品設計上実現が難しい場合もあります。このような場合には、タクトタイムではなく、操業時間の延長も視野に入れましょう。
タクトタイムの最適化には生産管理システムが効果的
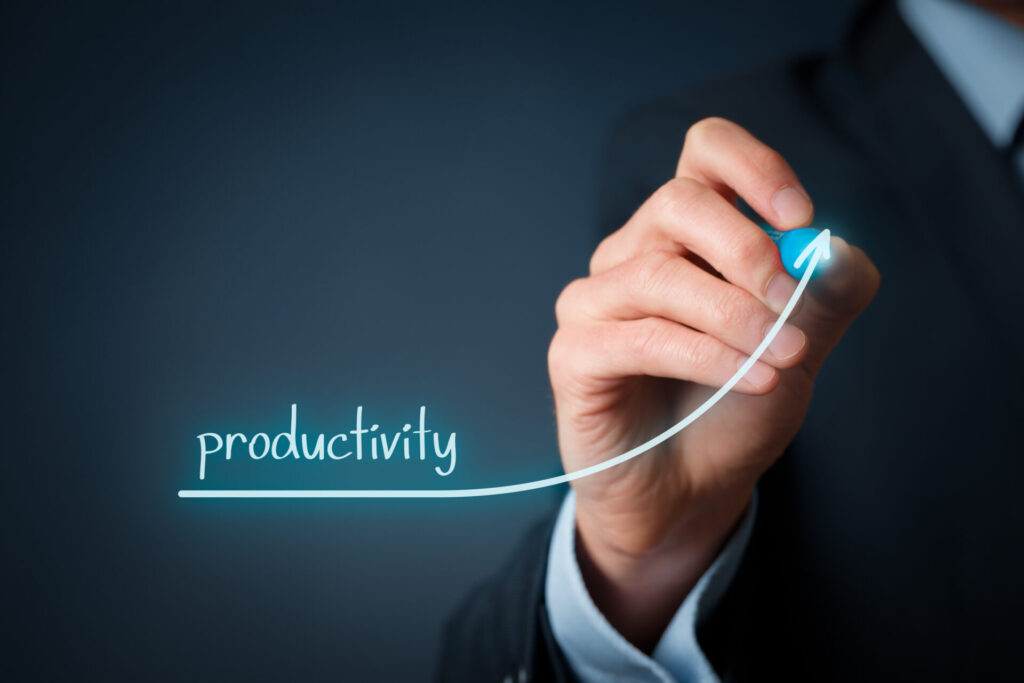
タクトタイムの最適化には、生産管理システムの導入が効果的です。受注状況の一元管理・共有が可能であり、生産ラインのサイクルタイムやリードタイムをリアルタイムに確認できます。
生産管理システムとは
生産管理システムとは、製造業における生産活動を一元管理するためのツールです。
生産管理システムを導入することで、生産計画の立案や進捗管理が効率化され、リアルタイムで生産情報を正確に記録し、正確なデータを活用できるようになります。システム上であらかじめタクトタイムを設定しておけば、サイクルタイムの変化をアラーム検知してリアルタイムで確認できるケースもあります。
生産管理システムを活用すれば、タクトタイムを最適化できる
タクトタイムの最適化を進めるには、受注状況、製造現場の生産状況を正確に把握することが第一歩です。しかし、現実には多品種生産や工程数の多さから、製造品目ごとの注文数や実際の生産負荷をタイムリーに確認できないケースも少なくありません。
そこで、生産管理システムを活用することで、品目別の受注情報・納期情報を簡単かつ正確に記録・参照できます。これにより、タクトタイムの設定に必要な情報を、集計しやすくなります。
また、生産負荷状況を設備別に見える化できるため、生産ラインのボトルネック(サイクルタイム>タクトタイムの工程)を早期に特定可能です。こうして得られた情報は、タクトタイム設定だけでなく、生産ラインの改善にも活用でき、作業手順や設備配置、人的リソースの最適化にもつながります。
22種類の生産管理システムをランキングで比較
初期費用相場や選び方のポイントをチェック
生産管理システムをそれぞれの特徴や初期費用相場などで比較したい場合は、「生産管理システムランキング」も是非ご覧ください。生産管理システムは、自社の製品・生産方式・企業規模などに適したものを導入しないと、得られるメリットが限定されてしまいます。事前適合性チェックや生産管理システムを選ぶ前に押さえておきたいポイントも解説していますので、製品選びの参考にしてみてください。