2024年09月10日
【生産管理システム】製品別原価管理・粗利分析が可能に!商品開発の予算化による開発スピード向上もできる体制に
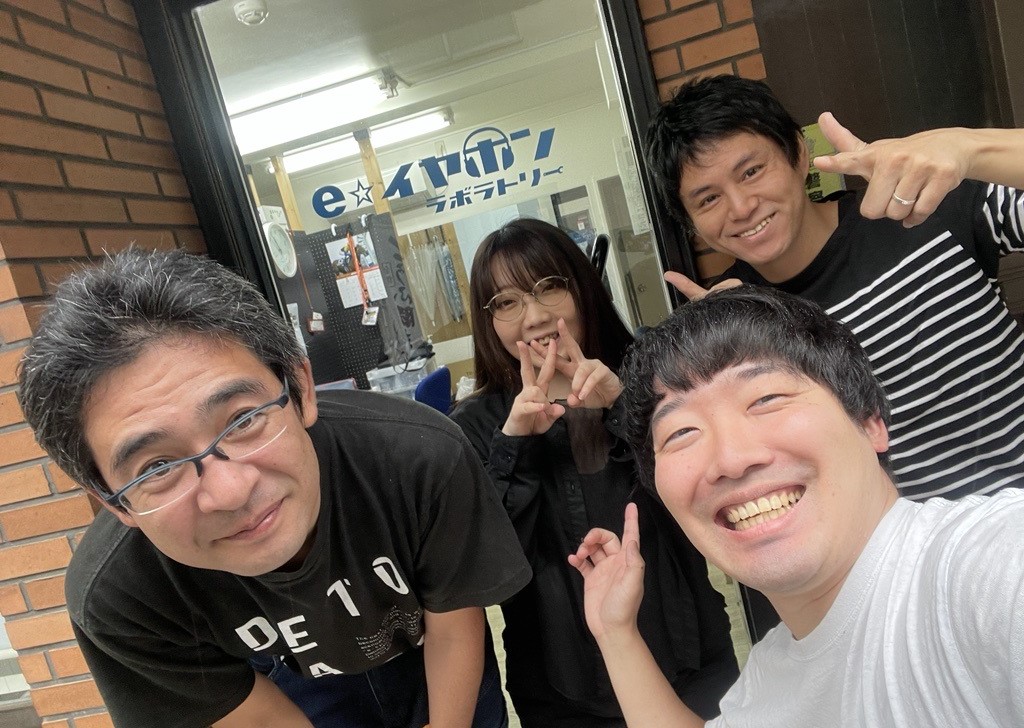
株式会社タイムマシン
業界 | 組立品業界 |
---|---|
会社規模 | 100~299人 |
機能 | 在庫管理、工程管理、生産管理 |
システム概要
課題
- 製品別の原価計算をするには、業務委託1~2名分の工数が必要となる見込みだった
- 在庫把握は月次の実地棚卸のみ、工数集計は行っていなかった
- 試作と通常製造分の材料をまとめて発注しており、研究開発費が把握できなかった
解決策
- スマートFの在庫管理・工数集計による自動原価管理を導入
効果
- スマートFで製品別原価管理が可能となり、40~80時間分の人件費・工数が不要になった
- リアルタイムな在庫管理とシステム工数集計により、詳細な粗利分析もできる体制に
- 研究開発費を把握したうえで予算化することで、開発スピード向上が実現可能に
導入の背景
内製の生産管理システムだと製品別原価計算が難しいと判断
日本最大級のイヤホン・ヘッドホン専門店「e☆イヤホン」を運営する、株式会社タイムマシン様。事業拡大の一環で自社製造部門を立ち上げられ、自社のIT部門にて生産管理システムを内製で作られていました。
しかし、製品別原価計算が必要になってきた中で、自社で原価管理機能まで作り込むとIT部門の工数が足りないと判断し、パッケージ型生産管理システムの検討を始められました。また、製造部門が大きくなる前に、製造業に豊富な導入実績のあるシステムに合わせて業界標準の運用をしておきたい、という思いもお持ちでした。
SmartF(スマートF)に決めた理由
多品種少量生産やオーダーメイド受注生産に対応でき、最も低コストに導入可能
SaaS型の生産管理システムを調べ始めた当初は、高額なシステムが多く、予算的に難しい状況でした。製造部門の売上規模を考えると、月額15万円以上のシステムは導入が難しいと考えられていました。
そのタイミングで、別件で展示会へ行った際、低コストなクラウド型生産管理システムがあることを知り、スマートFの紹介も聞いていただきました。3〜4社で比較検討された結果、スマートFはタイムマシン様の生産方式(多品種少量生産やオーダーメイド中心)に合う運用ができ、かつ最も低コストとのことで、導入を決めていただきました。
また、営業担当の対応が好印象だったことも決め手の一つでした。他に検討していたシステムベンダーは、電話口でシステム概要と金額感だけを伝える営業が多かった一方、ネクスタはタイムマシン様の課題を理解して最適な提案をしようとする姿勢が強く、信頼できると感じていただけました。
導入効果
自社でシステム開発する工数がなくなり、業務委託1~2名分の省人化
【導入前】製品別の原価計算をするには、業務委託1~2名分の工数が必要となる見込みだった
内製のシステムにおいて、製品別原価計算の機能開発は難易度が高く、もし自社開発するなら業務委託などで1名の採用が必要になる程の工数を試算していた。さらに、原価管理に必要な工数集計もエクセルなどで行うと、さらにもう1名の増員が必要だと見込んでいた。しかし、全社の売上比率がまだ低い製造部門での増員は、コストに見合わない状況だった。
【導入後】スマートFで製品別原価管理が可能となり、40~80時間分の人件費・工数が不要になった
パッケージ型の生産管理システムであるスマートFを入れたことで、自社で内製システムを作り込む工数はなくなった。業務委託1〜2名分にあたる、40〜80時間分の人件費・工数の発生を防止できた。
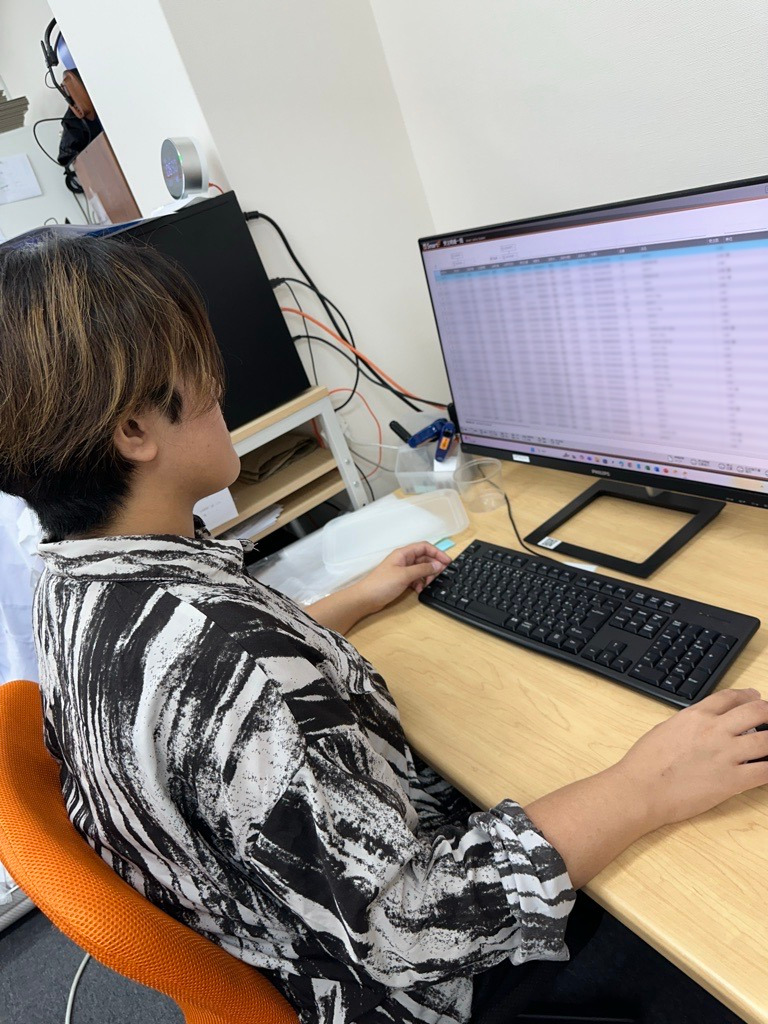
製品別原価管理に必要な、在庫の見える化や工数集計が可能に
【導入前】在庫把握は月次の実地棚卸のみ、工数集計は行っていなかった
製品別原価管理には、正確な在庫や労務費の管理が必須となる。しかし、以前は在庫を月末の実地棚卸でしか把握できておらず、想定の在庫数と差異があっても原因を突き止められなかった。また、工数集計も行っていなかったため、実際の労務費も計算できなかった。
会計処理時は、仕入金額・月末の材料在庫数・売上金額と、あらかじめマスタに登録している見込みの作業費などをもとに粗利を算出していた。このため、製造部門全体での粗利しか把握できず、細かい粗利分析ができなかった。
【導入後】リアルタイムな在庫管理とシステム工数集計により、詳細な粗利分析もできる体制に
スマートFで入出庫情報をリアルタイムに更新することで、常に最新在庫数が見えるようになった。工数集計も、スマートFで作業の開始・終了登録をすることで記録し、自動集計できる。これらのデータから、製品別原価や粗利を簡単に把握・分析できる体制になった。
研究開発費を把握したうえで予算化することで、開発スピード向上
【導入前】試作と通常製造分の材料をまとめて発注しており、研究開発費が把握できなかった
日々の在庫数を管理できていなかったため、現場担当者は経験則にて発注を行っていた。また、同社は商品企画も現場主導で進めており、試作用の材料発注なども現場で行う。しかし、試作用材料も通常製造分とあわせて発注することが多く、試作の作業時間(人件費)も記録していなかったため、経理上の研究開発費を正確に把握できなかった。
【導入後】研究開発費を把握したうえで予算化することで、開発スピード向上が実現可能に
スマートFでリアルタイムに更新される在庫情報をもとに、経験に頼らない正確な発注ができるようになった。また、製品別原価と研究開発費を分けて分析できるようになったことで、あらかじめ商品開発の予算を現場に渡すことも実現可能に。現場が商品開発の稟議を作成する手間をなくし、予算内で開発に取り組めるようになることで、商品開発のスピード向上が期待できる。
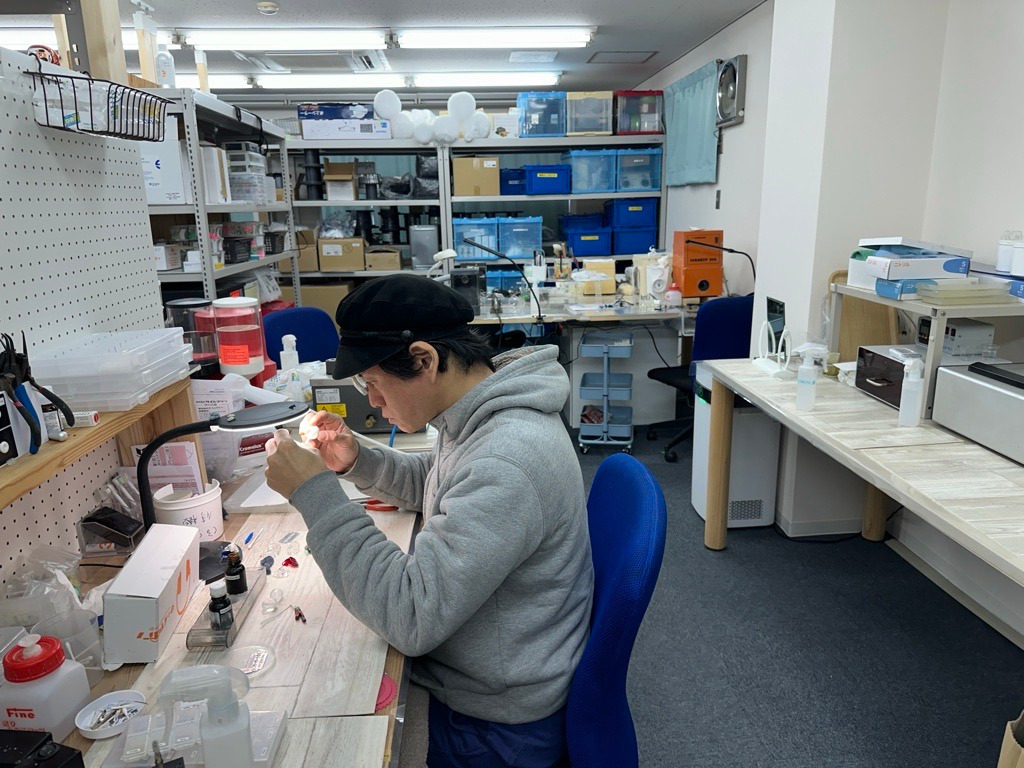
お客様の声
【システム導入担当者の声】
予算が限られた中での問い合わせでも、ネクスタ社の営業担当の方は親身に当社の課題を聞いていただき、安心感がありました。また、導入支援担当の方も、自社システムとスマートFの併用方法まで提案してくださいました。
また、スマートFの導入が、自社の業務棚卸をする良い機会になったとも感じています。今まで製造部門での業務は、現場以外から見えにくい状態だったので、それらをしっかり整理できたことも良かったと感じています。
今後はさらにスマートFを使い込み、粗利改善に役立てていきたいです。発注連携など、まだ活用していない機能も徐々に運用していこうと思います。
【現場担当者の声】
はじめは、原価管理のために必要なシステムを導入するというイメージが湧きませんでしたが、今はスマートFの重要性を実感してきています。手間なく原価を計算し、製造部門で使うお金を整理することで、面白い商品開発にもチャレンジしていけるのではないかと考えています。
今までは、大きな新商品開発の稟議を上げるため、1週間ほどかけて準備することもありました。スマートFでの粗利分析をもとに、あらかじめ予算を頂ければ、稟議の準備に手間をかける必要がなくなります。今まで以上に製品企画・開発により注力できるようになると思うので、よりスピーディに旬な新商品を開発していきたいです。
株式会社ネクスタ:営業担当の声
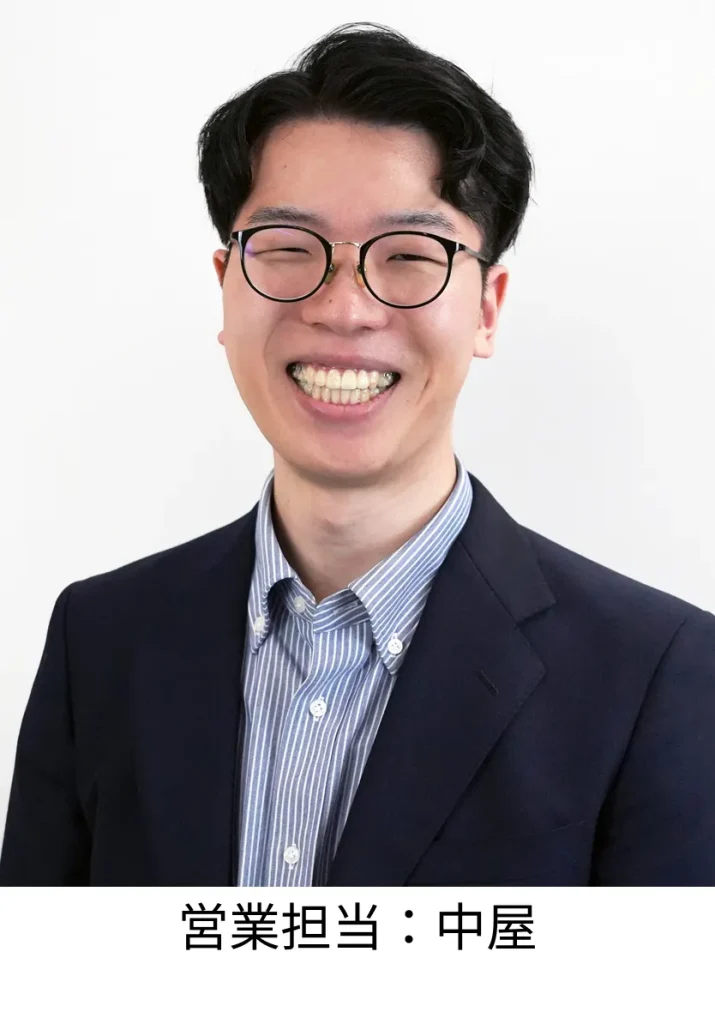
初回の電話で下記2点をお伺いした際、スマートFでしか解決できないと思い、課題の詳細をヒアリングさせていただきました。その上で、スマートFで解決できることやメリットをPRさせていただき、WEB打合せで詳しくご紹介する運びとなりました。
①製造部門を立ち上げるにあたり、内製でのシステム構築を試みた。しかし、外注管理や原価管理などの開発難易度が高い機能、全体を網羅した機能などが必要なため、仮に開発ができても個別仕様かつ自社メンテとなり、今後の保守に多くの費用と時間がかかる。
②他社システムは導入初期から高額な費用が発生し、運用できるかどうか分からない状況では、導入ハードルが高い
WEB打合せではまず、課題と今の運用を整理しつつ、内製システムの画面を拝見しました。そして、タイムマシン様にあったマスタの作り方と運用の流れを、スマートFのデモを実施しながらご提案いたしました。
株式会社ネクスタ:導入支援担当の声

【運用提案する上で心掛けたこと】
多品種少量生産、オーダーメイド製品の製造・販売されている事を考慮した提案を心掛けました。具体的には、全てをマスタで細かく登録するのではなく、入力の自由度を持たせることのできる汎用的な品番や、途中で製造工程が変更されても簡易に編集できるよう、使いやすさを保持したまま利用できるようご提案させていただきました。
【導入時を振り返って】
導入初期は、お電話や打ち合わせを通して、スマートFの機能・運用の理解を深めていただくようフォローさせていただきました。最終的には、ご担当者様が自ら設定を行い、動作検証を進めていただけるまで機能に習熟していただけました。