QCDとは?製造業の生産効率を高める3要素 生産管理における改善方法を事例から解説
公開日:2023年08月22日
最終更新日:2024年11月28日
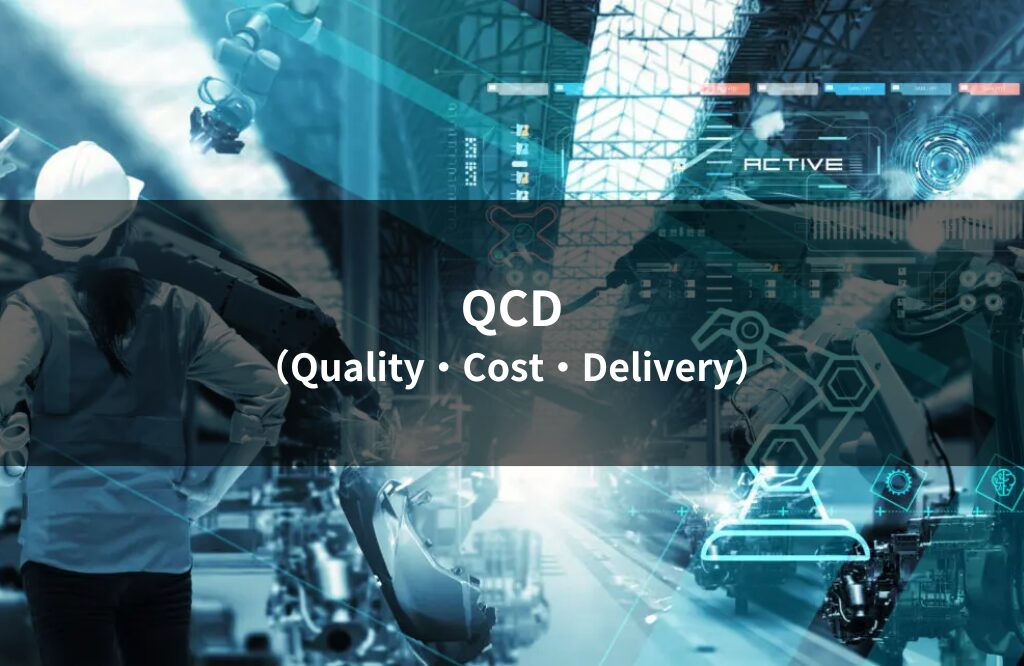
QCDとは、製造業が顧客満足度を高めるために必要な「品質・コスト・納期」を指します。生産管理や生産性向上において、これらをバランスよく最適化することが非常に重要です。
今回は、QCDとは何か、近年登場した派生語も含めて説明します。具体的なQCDの改善方法や、多くの企業が悩むQCD向上における課題、その課題を解決する方法の一つとして「生産管理システム」のメリットも解説します。記事の最後には、実際の成功事例も紹介しているので、参考にしていただけると幸いです。
QCDとは:Q=品質、C=コスト、D=納期
QCDとは、品質(Quality)、コスト(Cost)、納期(Delivery)の頭文字を取った言葉です。製造業の生産効率を向上させるための3要素であり、生産管理の基本とされます。
品質が向上すると顧客満足度が上がり、継続受注に繋がります。コストを少なく抑えられれば、企業の利益が増え、競争力の強化に直結します。そして、短納期で迅速な供給ができれば、顧客の信頼を獲得できます。
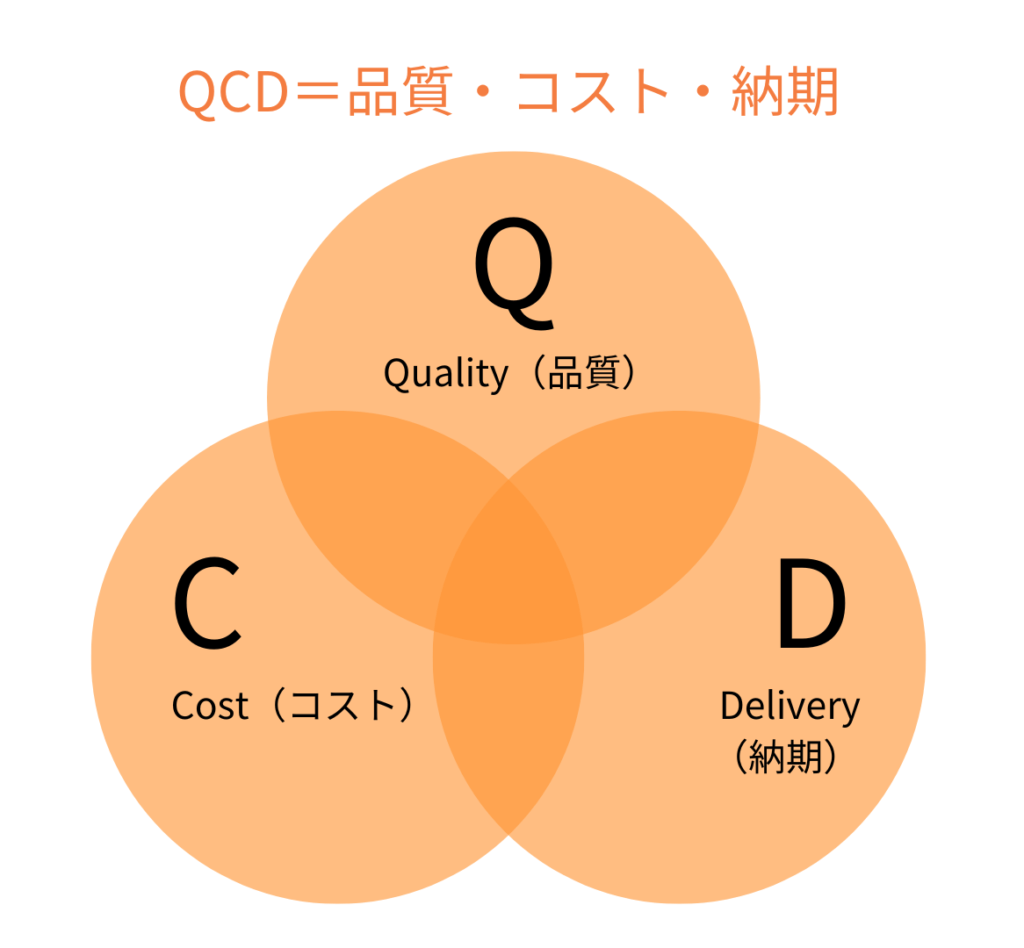
これらの3要素は相互に影響を与えるため、全体を最適化する総合的な管理が重要です。
優先すべきはQ=品質
QCDの3要素のうち、優先順位が最も高いのはQ(品質)、と言われるケースが多いです。まず品質の向上を目指し、顧客の要求を満たす製品を供給できるようになることで、顧客満足度に直結するためです。
品質を確保したうえで、コストや納期を管理することで、生産コストやリードタイムを削減し、競争力を高められます。
どれかを特化するのではなく「最適化」が重要
とはいえ、「品質が一番大事だから」と品質向上に注力しすぎることは、QCD改善とはいえません。これら3つの要素は相互に関連しており、いわばトレードオフの関係にあるからです。
品質を優先しすぎる例として、過剰な検査が挙げられます。品質を最重要と考えるなら、検査品目は多く、全数検査にて行うことが望ましいといえます。しかし、重要部品ではない製品や、不良率がきわめて低い製品において、それだけ緻密な検査をするのは得策ではありません。作業工数と製造コストが跳ね上がり、結果として納期が長くなってしまうからです。
もう一つのよくある例が、コスト低減のしすぎです。コストを抑えるために安価な原材料を調達したり、検査をおざなりにしたりすると、不良率が上がってしまいます。また、製造コストを下げるために作業員の人数を減らすと、納期が伸びたり、ストレスから不具合発生に繋がったりする場合もあります。
このように、QCDのどれか1つのみを極端に優先すると、他の2つに悪影響が出ます。QCDの各要素は総合的に関連していると理解し、最適化を目指すことが重要です。
QCDの派生語
近年は、QCD(品質・コスト・納期)だけでなく、他に重要な指標を追加した派生語も生まれてきています。製造業で使われるケースが多い派生語は、以下のとおりです。
■QCDの派生語一覧
派生語 | QCDに追加された指標 |
QCDS | S(Sefety:安全性、もしくはService:サービス) |
QCDSE | S(Sefety:安全性、もしくはService:サービス) E(Environment:環境) |
QCDSM | S(Sefety:安全性、もしくはService:サービス)M(Morale:士気) |
QCDSME | S(Sefety:安全性、もしくはService:サービス)M(Morale:士気)E(Environment:環境) |
PQCDSME | P(Productivity:生産性)S(Sefety:安全性)M(Morale:士気)E(Environment:環境) |
QCDF | F(Flexibility:柔軟性) |
QCDS
まず、QCDに「S(Sefety:安全性、もしくはService:サービス)を追加したQCDSがあります。
安全性(Safety)をうたう場合、製品仕様上の安全性や、製造現場・従業員の安全性を確保することを重視します。サービス(Service)をうたう場合は、顧客対応や納品後サポートなどのサービス充実を重視します。
製造業では、安全性を指すケースが多く、生産効率だけでなく安全な生産活動も重視する文脈で用います。労災リスクを減らし、従業員が安心して働ける現場を作り上げていくことも、生産活動の改善には重要といえます。
QCDSE・QCDSM・QCDSME
さらに、「E(Environment:環境)」を追加したものがQCDSM、「M(Morale:士気)」を追加したものがQCDSM、双方を追加したものがQCDSMEです。
これらは、企業の利益追求だけでなく、CSR(企業の社会的責を)の重要性も高まってきた背景で生まれた派生語です。環境問題や従業員満足度にも配慮し、生産活動やCSR活動を行うことで、企業が持続的に発展していくことを目指します。ちなみに、QCDSMEは、職場の6大任務とも言われます。
製造現場の視点においても、環境にも配慮して生産活動を行うことは重要といえます。さらに、従業員がモチベーションを持って働けるようになれば、生産性の向上や離職防止にも繋がります。
PQCDSME
QCDにS(安全性)・M(士気)・E(環境)をくわえ、P(Productivity:生産性)も追加した、PQCDSMEという派生語もあります。改善活動を繰り返すことで、同じ時間に製造できる生産量を増やしていき、企業としての利益を上げ続けることを目指します。
特に、生産管理業務や改善活動では、生産性向上の視点は非常に重要です。
QCDF
QCDにF(Flexibility:柔軟性)を加えた派生語が、QCDFです。顧客の要望に柔軟に応え、顧客満足度を上げていくことを重視する考え方です。生産方式にて受注生産を採用している企業は、特に柔軟性が重要といえます。
QCD向上の実践方法
まずは、基本的なQCDの向上方法を、具体例を交えて解説します。
いずれも共通して重要なことは、現状把握できる管理体制を作り、実態を知ったうえで問題点を特定することです。QCD低下の真因を突き止めてから、具体的な改善策を検討していく必要があります。
品質管理
QCDの中でも優先度が高い品質向上には、品質管理の徹底が必要です。適切な品質管理で不良率を下げ、顧客満足度や企業の信頼性を上げることができます。また、再作業のリスクも低減できれば、コスト削減にも繋がります。
品質を向上させていくには、各生産工程の品質状況を確認し、品質問題が起きる工程(ボトルネック)を見つけ出す必要があります。改善後は効果をモニタリングし、さらに品質向上が見込める工程を見つけることを繰り返し、継続的に取り組んでいく必要があります。
具体的な手法としては、作業の標準化、定量的な品質評価基準の設定、そして定期的な監査・評価が効果的です。
例:ある工程で品質のバラつきが多い場合
品質のバラつきが、新人従業員とベテラン従業員の作業品質の差として出ている場合、作業標準書の作成や教育により、作業品質を一定にしていく改善が効果的です。
一方、設備のメンテナンス不足で品質にバラつきが出ている可能性が高い場合もあります。設備の修理をするだけでなく、修理サイクルの再検討もしてみるといいでしょう。
企業によっては、品質管理部門だけでなく、QCサークルや改善活動を通し、製造現場も巻き込んで品質改善に取り組むケースもあります。いずれの場合も、検査データを分析するだけではなく、現場の声をヒアリングすることが重要です。
コスト管理
コスト管理は、生産活動の効率性や競争力を示す要素です。QCDにおいては、品質や納期を維持しつつ、いかに低コストに生産できるかを追求する必要があります。
はじめに、現状の生産コストを明確にします。材料費や労務費から製造原価を算出し、販売価格に対してどれくらいの利益が出ているかを確認します。その上で、どこにコスト圧縮の余地があるかを分析します。
例1:材料費高騰により製造原価が押し上げられている場合
サプライヤーへの価格交渉や、より安価なサプライヤーを探す方法があります。ただし、この材料が重要部品の場合は、安易に安価なサプライヤーへ切り替えず、しっかり品質評価も行う必要があります。
例2:労務費が想定より高い場合
作業時間が想定より長く、労務費を押し上げている場合は、製造工程の中にむだや非効率な作業がないか探します。ボトルネック工程の特定後は、品質低下しないように注意しながら改善していきます。
いずれも改善後は、定期的な品質評価を行いながら、改善の取り組みを継続して実施していきます。
納期管理
顧客に対する納期短縮を図る場合は、以下3つのリードタイムに分解し、課題や改善幅を検討します。
- 製造リードタイム
- 仕入先(購買)リードタイム
- 出荷リードタイム
社内の製造にかかる時間を短縮したい場合は、製造リードタイムに着目します。無駄を排除することで、生産性の向上と納期の短縮を図ります。
QCDのバランスは柔軟な調整も必要
前述の通り、QCDの3要素は互いにトレードオフの関係にあり、最適なバランスになったときに生産効率が最大化します。しかし、時と場合によっては、このバランスの調整が必要になることもあります。
例えば、競合他社が安価な製品を市場投下してきた場合は、自社の競争力を保つためにコスト低減の優先度を上げる必要があります。他にも、重大な品質不良を起こしてしまった後は、何より品質を優先した生産体制の再構築が最優先となります。
その時々の企業が優先すべきことに応じ、QCDのバランスを再考し、現時点でのベストな生産性を模索していくことが重要です。
QCD向上の取り組みでよくある課題
生産管理担当者や現場担当者が、QCD向上に向けた改善活動でしばしばつまづくポイントは、正確な現状把握です。
特に中小・中堅企業で、紙やエクセルでの管理が多い企業では、以下のような悩みをよく耳にします。
QCD改善の現状把握でよくある悩み
- 品質検査の記録が紙でしか残っておらず、エクセル集計のために手入力しなければならない
- コスト改善をしたいが、正確な製造原価を集計しておらず、仕入先からの納品書や紙の作業日報を一からまとめなければならない
- 作業日報をつけておらず製造リードタイムが把握できず、納期改善の余地が何処にあるかわからない
現状を正確に把握できないと、課題特定や改善が難しくなります。上記のような悩みを持つ企業は、生産管理システムを導入することで、QCD改善に大いに役立てることができます。近年はクラウド型のシステムもあり、少ない初期費用で導入できるため、検討する価値はあります。
QCD向上に役立つ生産管理システムとは
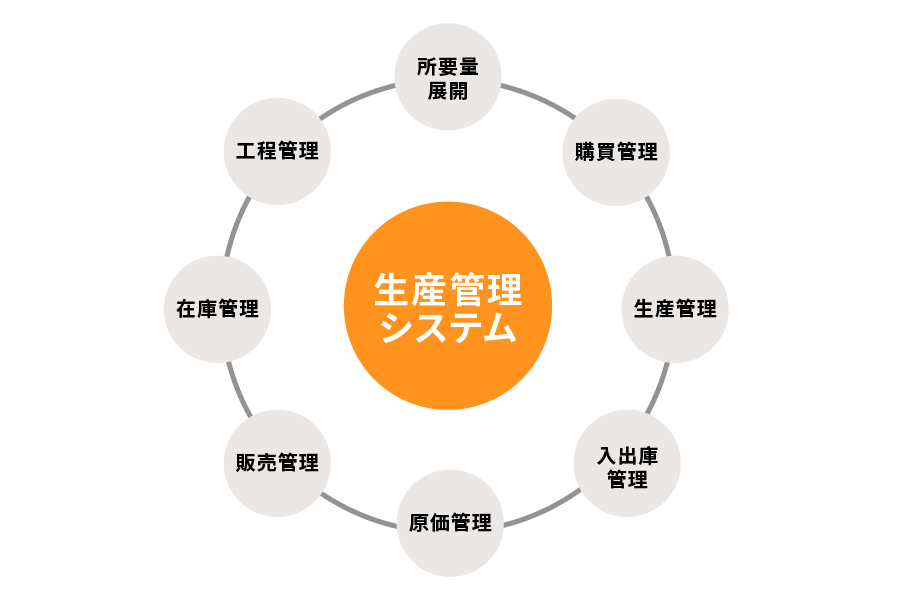
生産管理システムとは、在庫や工程、生産計画、納期、原価品質など、生産にまつわる情報を一元管理できるシステムです。QCDに役立つ主な機能は、以下3点です。
- 品質・原価・納期を手間なく一元管理
- IoT活用でリアルタイムに実績収集
- ミスや工数の削減でQCD改善に直接役立つ
どちらも、多くの企業がQCD向上の中で課題となる、現状把握で役立つ機能といえます。
品質・原価・納期を手間なく一元管理
生産管理システムで、QCDの3要素に関する情報をまとめて管理できると、現状把握の工数が大幅に短縮できます。
生産管理システムの「品質管理」機能例
品質管理においては、各工程ごとの検査内容をシステム上に登録し、検査結果データを簡単に参照できます。紙の検査成績書を1枚ずつ見返す手間なく、傾向分析ができます。
生産管理システムの「原価管理」機能例
入荷検品時に仕入単価を入力し、デジタル作業日報で作業工数を記録しておくと、製品別単価を自動的に集計できます。各原価をエクセルや電卓で足し上げる作業は必要ありません。
生産管理システムの「納期管理」機能例
生産計画の立案時に納期を設定し、納期が迫ったらアラートを出すことができます。また、デジタル作業日報で作業実績を登録しておけば、計画に対し実際にかかった工数の比較も簡単に行えます。
このように、QCDの現状分析のためのデータ収集は、生産管理システム上で自動化できます。
IoT活用でリアルタイムに実績収集
QCDの現状分析のためのデータ収集は、生産管理システムとIoTツールを連携すると、より手間なく行うことができます。
例えば、生産管理システム上で作業日報を記録する場合、製造現場にノートパソコン等を持ち込めない場合もあるかと思います。そんなときに、QRコードやバーコードをスキャンできるハンディ端末を使えると、省スペースで簡単に作業登録が可能です。ハンディ端末で入力した情報は即時、生産管理システムに反映されるため、事務所のパソコンからでもリアルタイムな情報を確認できます。
他にも、在庫の入出荷時にQRコードやバーコードを活用する企業も多くあります。生産現場でも使いやすいIoTツールを活用することで、よりリアルタイムな実績収集が可能となります。
ミスや工数の削減でQCD改善に直接役立つ
生産管理システムを導入すると、ミスや工数の削減が期待できるため、QCD向上に直接的な効果もあります。
もし、外観や品番が似ている原材料の誤使用が起きている場合、生産管理システムとIoTツールでの正誤チェックでミスを防止できます。目視確認からシステムによる機械的チェックにするだけで、QCDの品質改善に直結する効果が出せます。
生産管理システム導入によるQCD向上の成功事例
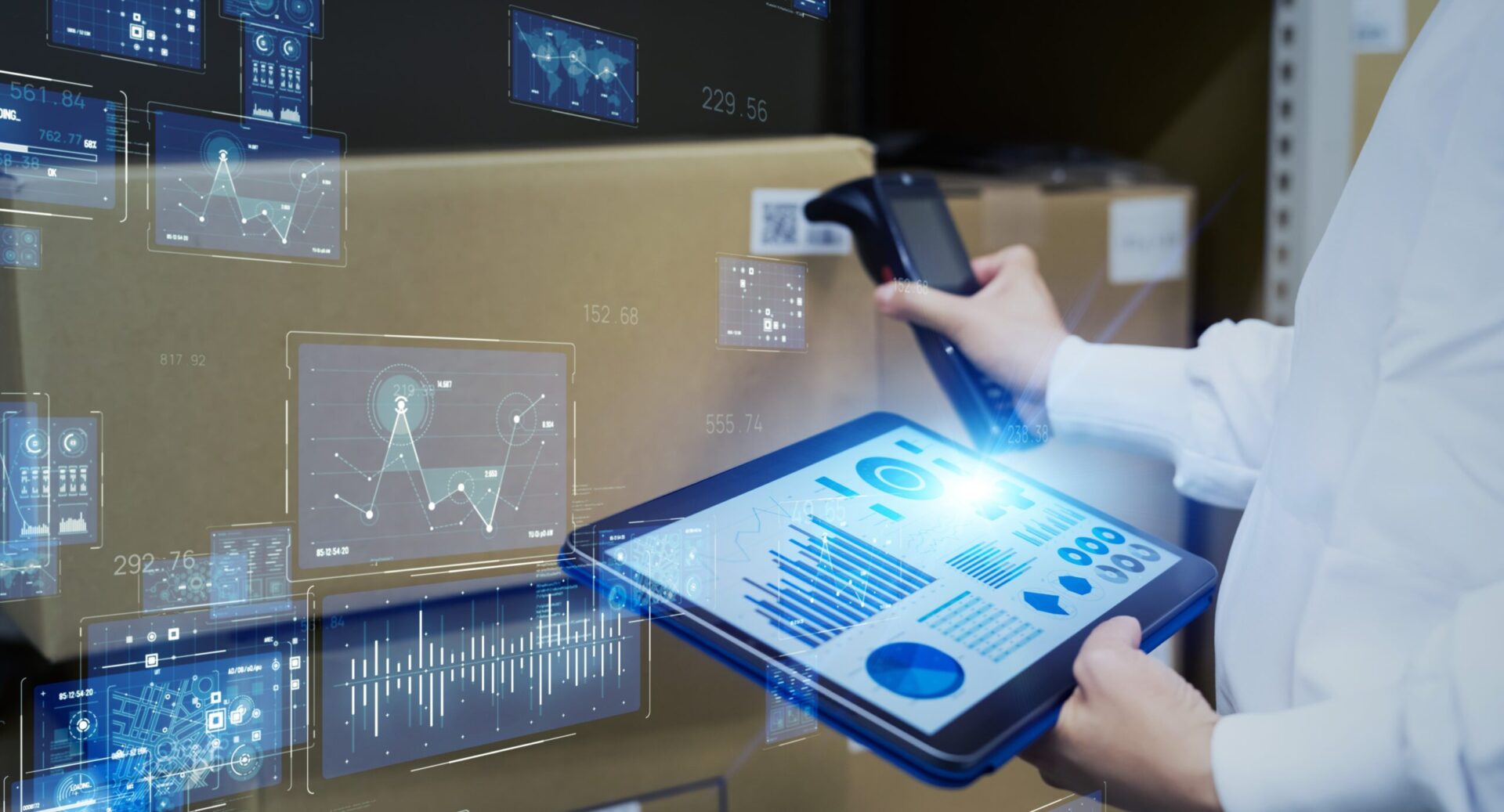
実際に、生産管理システムの導入によってQCDの向上に成功した事例を紹介します。中小・中堅企業を中心に2社、解説します。
品質改善の成功例
化粧品業界のA社は、類似原料や期限切れ原料の誤投入が年数回起きていました。原料チェックは作業員の目視確認が中心で、新人などの不慣れな作業員が判断を誤るヒューマンエラーがなかなかなくせない状況でした。
そこで同社は、生産管理システムとハンディ端末による、工程飛ばしのチェックを導入しました。次工程とは異なる原材料や、期限切れの原材料のQRコードをスキャンするとエラーとなるため、誰でも製造指示書通りに製造を進められるようになりました。
その結果、原材料の誤使用・誤投入は年間0件となり、廃棄ロスによって発生していた年間損失額の数千万円もゼロとなりました。
詳細:誤使用・誤投入0件、年間損失額の数千万円が0円に!ハンディ端末で工数削減・属人化解消も成功
コスト削減の成功例
組立品業界のB社は、ダブルビン方式で在庫を管理しており、常に発注点以上の安全在庫を持つ運用をしていました。社内の現場DX推進により、在庫管理機能がある生産管理システムを導入し、改めてシステムによる在庫分析を行いました。
改めて在庫や仕入先リードタイム分析をしたところ、多くの部品が安全在庫を持つ必要がないことが判明しました。安全在庫を持っていた部品の多くを都度発注に切り替えた結果、年間約100万円の在庫削減を実現できました。
詳細:在庫管理のシステム化に成功!リアルタイムな在庫管理で年間100万円の在庫削減
22種類の生産管理システムをランキングで比較
初期費用相場や選び方のポイントをチェック
生産管理システムをそれぞれの特徴や初期費用相場などで比較したい場合は、「生産管理システムランキング」も是非ご覧ください。生産管理システムは、自社の製品・生産方式・企業規模などに適したものを導入しないと、得られるメリットが限定されてしまいます。事前適合性チェックや生産管理システムを選ぶ前に押さえておきたいポイントも解説していますので、製品選びの参考にしてみてください。