作業日報は無意味?製造業で活用できない理由、日報の具体的な書き方・管理を解説
公開日:2025年03月14日
最終更新日:2025年03月14日
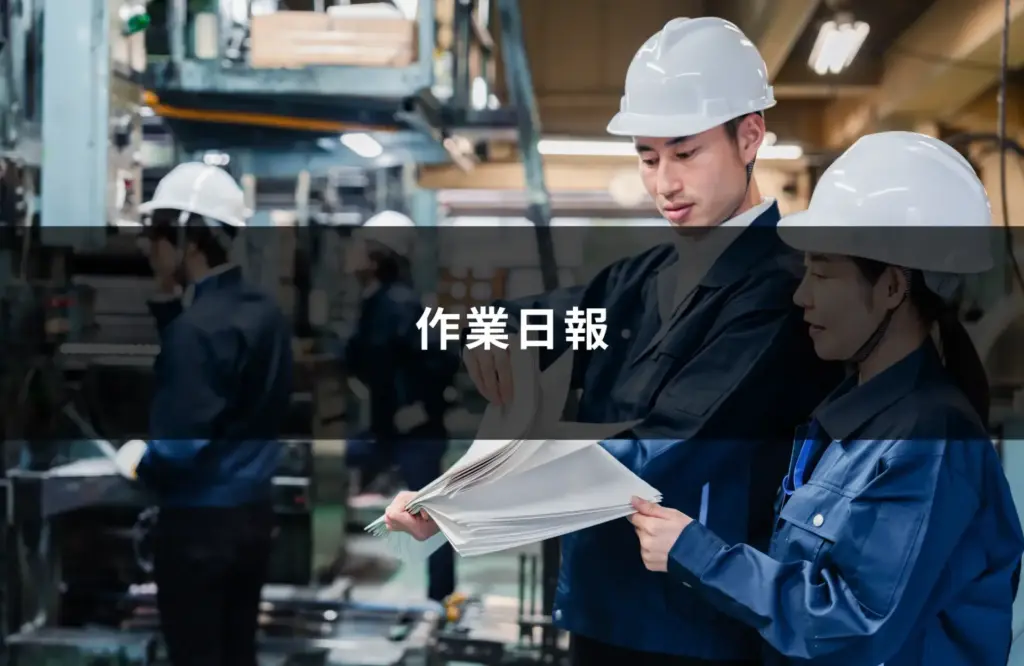
作業日報は、現場の状況を把握するための記録であり、生産性や品質向上に活用することが期待できます。しかし、形骸化して意味がない、と作業者や管理者が感じている現場も少なくありません。その原因は、目的の不明確さや情報の活用不足にあります。
本記事では、作業日報が無意味になりがちな理由、効果的な活用方法を解説します。また、作業日報の具体的な管理・運用方法についても紹介します。
作業日報とは
作業日報とは、製造現場を中心とした職場において、当日の作業内容や進捗を記録する帳票のことです。作業者は、その日の活動内容、時間配分、成果、課題について、作業日報として記録します。この記録は、管理者やチーム間で共有し、現場の作業効率や品質の改善に向けた取り組みのための情報源として活用されます。
作業日報が無意味になりがちな理由
作業日報は意味がない、と思われるケースも少なくありません。しかし、その原因の多くは、明確な目的が設定できていなかったり、運用方法が適切でないことにあります。
そもそも目的があいまい
作業日報には、職場ごとに目的を持たせるのが本来あるべき姿ですが、目的そのものがあいまいなケースも見受けられます。日報の記録には、例えば次のような目的が挙げられます。
- 情報共有:職場内に担当業務の状況を共有できるようにする
- 進捗管理:作業の進行状況を把握し、計画通り進んでいるか確認する
- 品質管理:不良品の発生状況や原因を記録し、品質向上につなげる
- 労務管理:作業員の労働時間や体調を管理し、適切な働き方を促す
- 業務改善:作業の無駄や問題点を発見し、効率向上や改善につなげる
- トラブル事例の蓄積:同様の事例が起こった際の参考資料となるように記録する
しかし、作業者が何のために記録するのか理解していなければ、どんな内容を書けば良いのか分かりません。職長や管理職にとって、活用価値のない情報となってしまい、結果として管理者やスタッフの時間を無駄にするだけになりかねません。
目的の周知が足りない
作業日報の目的が明確であっても、その目的が作業者全員に共有されていない場合、組織が活用できる記録にはなりません。作業日報で記録を残す目的をメンバーが理解していないと、日報が形骸化してしまいます。
目的を共有するためには、次のように管理者側で誘導することも効果的でしょう。
- 作業日報の目的を明示し、テンプレートに沿って具体例な書き方を載せる
- 記載内容を管理者がチェックしてフィードバックを行い、目的意識を持たせる
膨大な情報を活用できていない
作業日報から得られる情報を、具体的な改善施策や意思決定に活用できていないケースも多いでしょう。作業日報には、生産量・作業時間・品質・不良発生状況・設備の状態・安全情報など、多くの情報が記録されます。しかし、これらが蓄積されるだけでは、日報がただ「記録するだけ」で終わってしまい、現場の問題点や改善ポイントが見逃されます。
例えば、不良品の発生データが毎日記録されていても、次のような分析が行われなければ、品質改善にはつながらないのです。
- どの工程で品質不良が多いのか
- どの作業員・時間帯で発生しやすいのか
- どの設備が問題を起こしているのか
作業日報を電子データとして取り込み、データ分析によって現場の課題を発見する仕組みが必要でしょう。
作業日報の記入がマンネリ化している
同じような記録を毎日行うことが義務化されると、作業日報の記入が形式的になり、十分に考えずに済ませてしまいがちです。特に日報をチェックされた形跡がなかったり、勤務終了間際に慌てて記録しがちであったりする場合には、この傾向がより顕著になりやすいでしょう。
このような場合、日報に管理者コメントを記入する、記載内容の不明点を問い合わせるなどの取り組みが効果的です。管理者側が日報を活用する意識が周知されれば、作業者は適度な緊張感を持って作業日報を記録するようになるでしょう。
製造業における作業日報の活用方法
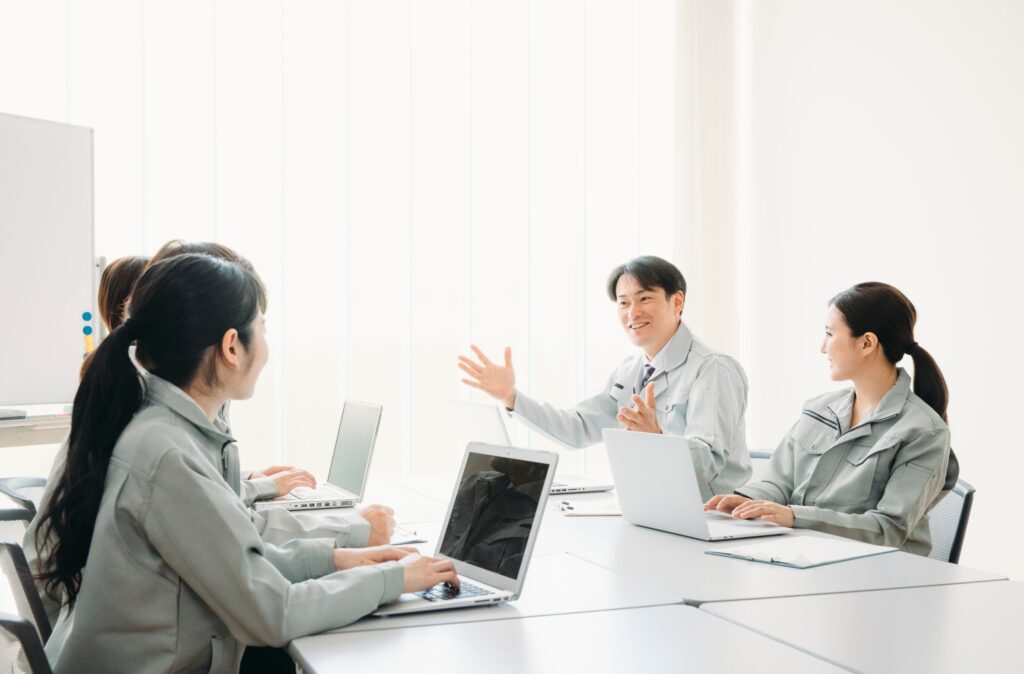
作業日報は単なる記録ツールではなく、製造現場の情報共有やカイゼンの推進に欠かせない存在です。ここでは、具体的な活用方法を紹介します。
作業進捗の報告
作業日報は、作業の進捗状況を記録・報告するツールです。現場の状況を見える化すれば、計画通りに作業が進んでいるかを管理者が把握しやすくなり、納期遵守の向上が期待できます。
作業進捗の報告では、どの作業がいつ完了したのか、または遅延が発生している場合はその程度と理由を具体的に記載します。一例ですが、ある工場における部品Aの組立作業について、次のような報告が挙げられます。
>部品A組立作業工程の進捗:目標100個→実績70個
>遅れの理由:前日の工程不良リカバリーのため
これにより、管理者は現場の状態を正しく把握し、適切な意思決定が可能になります。この例では、別のチームから作業者の応援を求めるなどにより、作業遅れの挽回を試みることもできます。また、進捗状況を可視化することで、従業員に対して納期遵守や品質意識へのモチベーションの維持・向上にも繋がります。
チーム間の円滑な情報共有
作業日報は、異なるチーム間での情報共有にも活用できます。特に交替勤務やシフト制勤務の場合、業務引継ぎが発生するため、現場の状況を正しく伝達する必要があります。具体的には、次のような報告が例示できます。
>明日実施予定であったプレス設備改造が一日前倒しで実施、本日午前に改造完了。
>プレス作業前のある作業がどのような確認手順が本日午後より変更になっている。
>新しい手順書を確認して進めること。
このような記録があれば、例えばタイムリーな問い合わせが難しい交替勤務の引継ぎであっても、状況を速やかに理解できます。さらに、後で読み返せば、設備改造の日程やその後の変更内容を参照できます。特に大規模な製造現場では、作業日報は部門間の情報伝達ミスによるトラブルや重複作業の回避に役立ちます。
トラブル実績の共有と蓄積
作業日報にトラブル実績を記録・蓄積することは、有効な活用方法の一つです。低頻度のトラブルであっても、同じ問題が繰り返し発生する場合、その発生状況や規則性を確認する証拠資料になります。
トラブルを記録する際には、以下の情報をできるだけ詳しく記載します。
- 発生した問題の詳細
- 想定される原因
- 具体的な対応策
- 対応結果
この情報は、当該工程を経た製品の履歴を追跡する際に役立つ、貴重なデータとなります。さらに、記録をチーム内で共有すれば、長期的な視点での生産性向上や品質向上に繋げられる可能性もあります。
製品履歴の追跡(トレーサビリティ)については、こちらで詳しく解説しています。
→トレーサビリティシステムとは:導入事例やメリットなどを詳しく解説
役に立つ作業日報の書き方
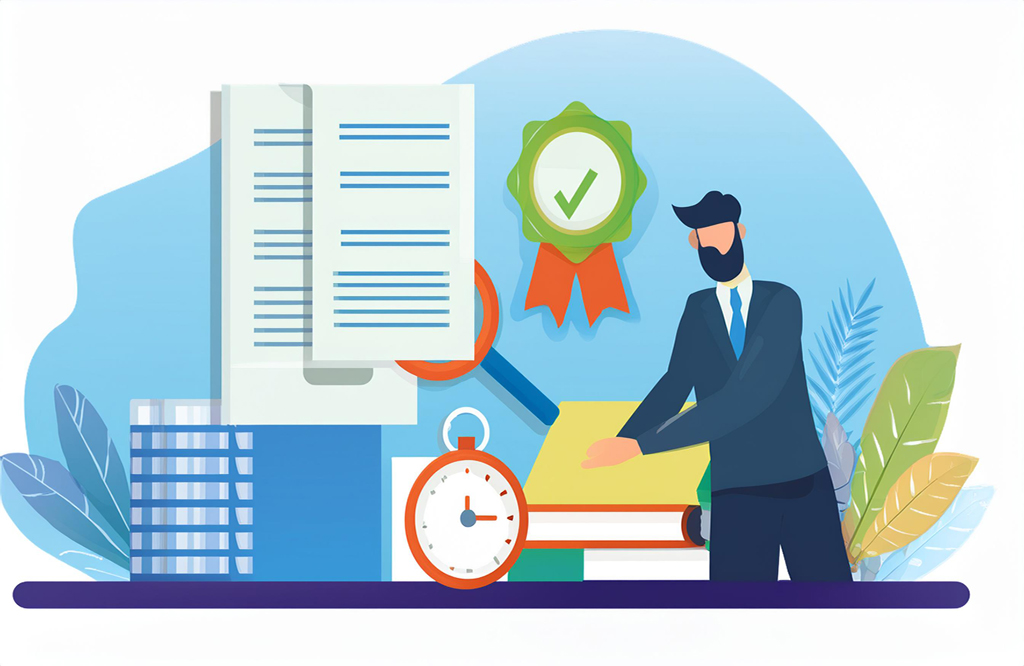
作業日報を業務の効率化や改善に繋げるためには、いくつかのポイントを押さえておく必要があります。
作業当日に記入する
作業日報では、作業日ごとに業務実績を記録するため、記憶が新鮮である当日中の記入が基本です。作業中に直面した問題や気づいた改善点は、作業当日が最も正確に記述できます。時間が経つと記憶が薄れ、詳しい内容を思い出すのが難しくなってしまいます。
作業終了直後、あるいは小休憩のタイミングなどで、日報をこまめに記録する習慣をつけましょう。また、リアルタイムで記録を進めれば、後からまとめて記入する手間を省くこともできます。これにより、より情報密度が高く、信頼性の高い作業日報が作成できます。
目的・伝える相手を意識する
作業日報を書く際には、「どんな目的であるのか」と「誰に伝えるのか」を意識することが大切です。例えば、上司への進捗報告を目的とする場合と、チームメンバー間での情報共有が目的の場合では、記載の仕方を変えた方がよいでしょう。具体的には次のような点に留意します。
上司宛の場合
進捗状況、問題点と対応策、翌日の予定など、重要な情報を簡潔に記載
メンバー間の場合
作業内容、関連する情報、注意点などを具体的に詳しく記載
簡潔に必要な情報を書く
作業日報を書く際は、必要な情報を簡潔にまとめます。冗長な説明や不必要な情報は、読み手を混乱させ、重要なポイントを見逃す可能性があるためです。
以下に、良い例と悪い例を挙げて説明します。
悪い例
今日は概ね予定通り作業が進みました。午後になって少し遅れが出ましたが、なんとか挽回して最終的に商品Aを95個生産しました。
良い例
本日は製品Aを100個生産計画に対して、計画比5%減の95個生産となりました。午前中は計画通り50個生産しましたが、午後には部品供給が30分間遅れて一時稼働停止。その後、隣接ラインの応援で挽回しましたが、計画未達となりました。
悪い例では「概ね」という定性的な言葉で、計画に対して実績がどれだけであったのかが不明瞭です。また、作業遅れの原因、影響度、その挽回方法が不明瞭であり、何が起こったのかが読み取れません。良い例のように、計画と実績を結論として示し、その背景情報を補足します。このような書き方をすれば、読み手は状況を正確に理解できます。
普段と違う出来事は詳しく記録する
業務中に発生した「普段と違う」出来事は、作業日報で状況を詳しく記録します。具体的には次のような状況が挙げられます。
- 作業中に発生した設備トラブルや品質不良
- 製品仕様や業務フロー、作業環境の変化
- 他部門や取引先とのコミュニケーションで発生した問題
「普段と違う」を記録する際は、「何が、いつ、どのように起きたのか」を具体的に記載します。記録からトラブルの原因を正確に特定でき、再発防止や業務改善の取り組みにつながります。
以下は、ねじ締工程での工程トラブル報告に関する作業日報の例です。
悪い例
トラブルで生産ラインの品質異常が発生。機械の再調整で解消した。
良い例
9時25分に第2組立ラインのねじ締工程で、締め付けトルク異常が判明。規定トルク3.0±0.3N・mに対して2.5N・mへ低下。当日生産品の少なくとも5個で異常を確認。11時10分にトルク設定を再調整し、検査工程で抜き取り検査を実施して問題なきことを確認済。再調整前の製品の詳しい確認も必要だが、本日未完了。
悪い例では、ライン名・日時が不明瞭で、具体的な不良と再調整で実施した内容が不明確です。良い例ではこれらの点が明瞭であり、対象製品の取り扱いについても正しく読み取れます。このように、具体的に記録することで、状況を正確に理解することができ、追加対応事項の漏れがなくなり、原因究明もスムーズに進みます。
作業日報の管理方法
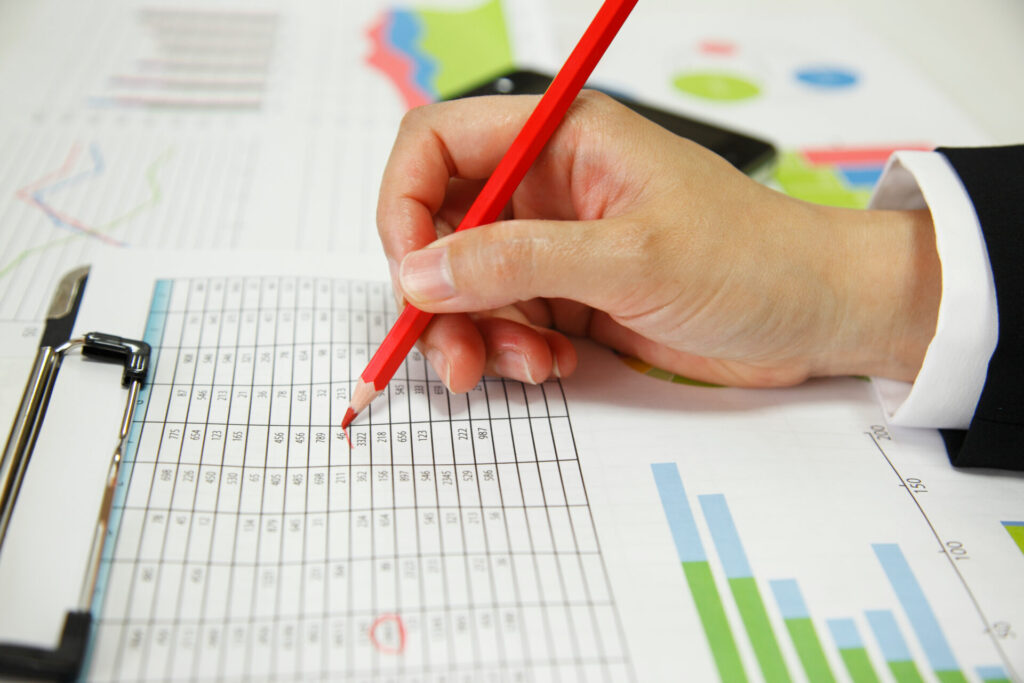
作業日報の管理は、業務の効率化と精度向上に直結します。従来の紙帳票、エクセル管理、生産管理システムを活用した作業日報管理について、それぞれの特徴とメリット・デメリットを紹介します。
紙の記録帳票での管理
作業日報の最も原始的な管理方法は、紙媒体の記録です。紙とペンのみで導入・運用が実現できるため、小規模な現場やシステム構築が難しい環境で広く採用されています。特別な機器が不要で、誰でもすぐに利用可能です。また、現場でイレギュラーな状況が発生した場合、フレキシブルに対応できるというメリットもあります。
しかし、紙媒体による記録は、手書き時のヒューマンエラーによる記録ミス、文字の判読性の問題が発生しやすいです。さらに、データを分析するためには、電子データ化のための入力が必須ですが、この際に転記ミスが起こるリスクも高いです。
PCを使用したエクセル管理
作業日報として、作業場や事務所のPCでエクセルへ入力する方法も一般的です。電子データ化されているため、手書きデータを転記する必要はなく、データの保持も容易です。あらかじめテンプレート化した作業日報フォーマットを使用すれば、効率よくデータ入力・集計が実施できます。さらに、関数やVBA機能を活用すれば、日報データを自動的に集計可能です。
ただし、入力ミスや集計ミスのリスクに加え、ファイル管理やバックアップ体制の不備によりデータが消失しやすいという欠点もあります。複数人での作業を前提とするものの、リアルタイムでの共有が困難であり、データの一貫性を維持するための運用ルール整備も欠かせません。さらに、自動化のため複雑なマクロ・関数を設定すると、知識のない人が自動集計機能を無意識に破壊してしまうケースも少なくありません。
生産管理システムの活用
生産管理システムを利用した作業日報は、リアルタイムで複数担当者入力の同時入力が可能であり、トレーサビリティにも優れています。システムで自動的にデータを整理・見える化できるため、属人化させずに高度なデータ分析が可能です。
生産管理システム上で作業実績を登録すれば、人的エラーを最小限に抑え、正確なデータ収集が実現できます。また、IoTデバイスやセンサーとの連携により、システムへの自動的なデータ取り込みも可能です。
一方で、システム導入には費用が必要で、初期設定やカスタマイズに時間がかかります。さらに、現場スタッフへの教育や運用ルールの徹底が不可欠です。
効率的な作業日報の運用とは
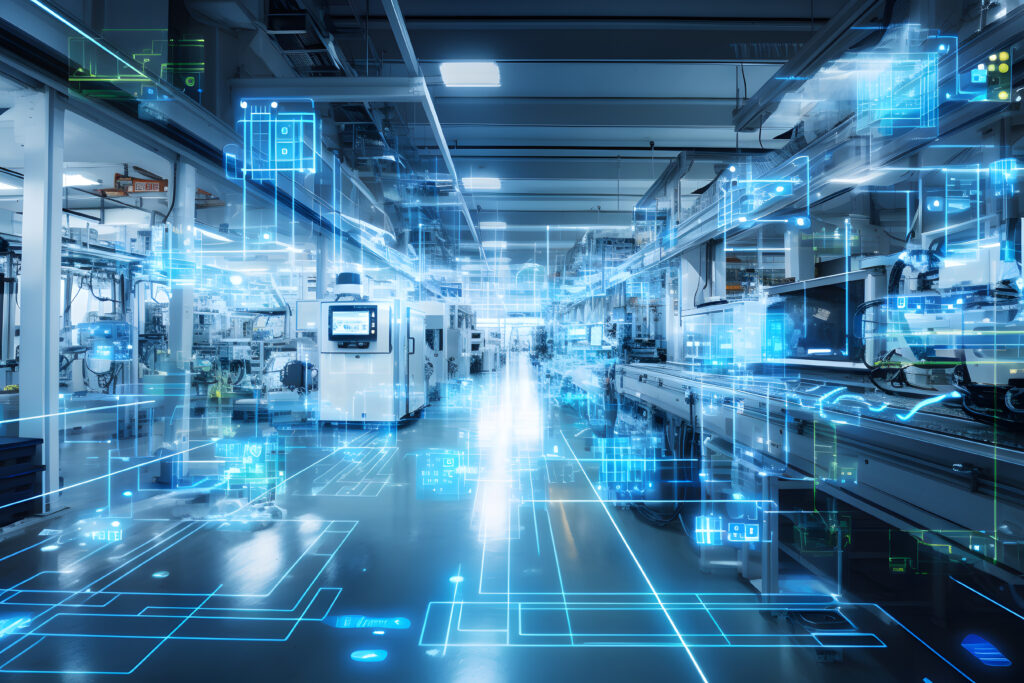
効率的な日報運用を実現するには、単にシステムツールを導入するだけでは不十分です。現場の実情に即した運用に沿って、全体の作業フローとして効率化を進めることが重要です。
システム導入による自動化・効率化の促進
システムの活用は、作業日報の手作業を大幅に削減し、属人化を排除しつつ正確かつ迅速なデータ蓄積を加速します。また、リアルタイムでの進捗状況の把握が可能となり、情報供給・意思決定がスピーディーかつ円滑になります。
特に、IoTやクラウドサービスとの連携は、拠点を跨いだ一元管理が可能となり、活用できる情報の量・質の向上も期待できます。
ハンディ端末を活用したリアルタイム入力
作業現場にハンディ端末を導入すれば、その場で記録できるため作業日報の記入時間の短縮が可能です。これ以外にも以下のようなメリットがあります。
- リアルタイム入力が基本となるので、忘却・記憶誤りによる誤情報入力のリスクが低い
- 必要な情報が入力されないと、エラーが発報し、情報欠損を防ぐ
- トラブルを検知しやすいため、管理者も異常に気づきやすく、早期対処が可能となる
- 品番・ロット情報をQRコードやバーコード読み取りにすることで、品番誤入力を防ぐ
ハンディ端末の導入・管理コストはかかりますが、工程管理・品質管理の観点で合理化を推進することができます。ただし、作業環境に応じて、防塵・防水対応などの特殊な端末を選定する必要があり、液体や腐食性の原料を多用する現場への導入が困難なケースもあります。
デジタルツール導入時の教育とサポート
新しいツールを導入する際には、スタッフへの教育と運用サポートが欠かせません。特に高齢のスタッフやIT機器になじみの薄い作業者には、丁寧なサポートが必要となります。
操作やトラブル時に速やかに問い合わせできるように、管理体制を構築する必要があります。
イレギュラーが記録しやすい紙帳票も併用
デジタル化の最大のデメリットはイレギュラーへの対応が難しい点であり、一部紙媒体の記録帳票の併用が望ましいです。定常業務の範疇であれば記録不要ですが、システムに入力できない内容については紙帳票へ記録します。
紙帳票に記録された内容の中で、頻度の高い項目については、後から機能追加によりデジタル化を進めるとよいでしょう。
作業実績の電子化に成功した導入事例の紹介
あるセラミックス製品の製造会社では、現場で記入した手書きの作業実績表をエクセルに転記・集計しており、その管理に多大な手間と時間がかかっていました。また、リアルタイムでの進捗管理・在庫確認ができないため、確認事項が発生するたびに現場で確認が必要でした。
そこで工程管理システムとハンディ端末を導入し、作業日報としてシステム上での作業実績登録を行う運用としました。その結果、月間100時間のエクセル入力作業が不要となり、工程進捗・在庫情報をリアルタイムに把握できるようになりました。
このように作業日報の電子化・システム運用は、企業の生産管理・在庫管理の大幅な効率化を実現できます。
実際の導入事例はこちらで詳しく紹介しています。
→【工程管理システム】ハンディ端末を用いた作業記録でエクセル管理の工数削減を実現
22種類の生産管理システムをランキングで比較
初期費用相場や選び方のポイントをチェック
生産管理システムをそれぞれの特徴や初期費用相場などで比較したい場合は、「生産管理システムランキング」も是非ご覧ください。生産管理システムは、自社の製品・生産方式・企業規模などに適したものを導入しないと、得られるメリットが限定されてしまいます。事前適合性チェックや生産管理システムを選ぶ前に押さえておきたいポイントも解説していますので、製品選びの参考にしてみてください。