製造業のリードタイムを短縮する4つの方法 ※過度な短縮にはデメリットもあり
公開日:2025年03月11日
最終更新日:2025年03月11日
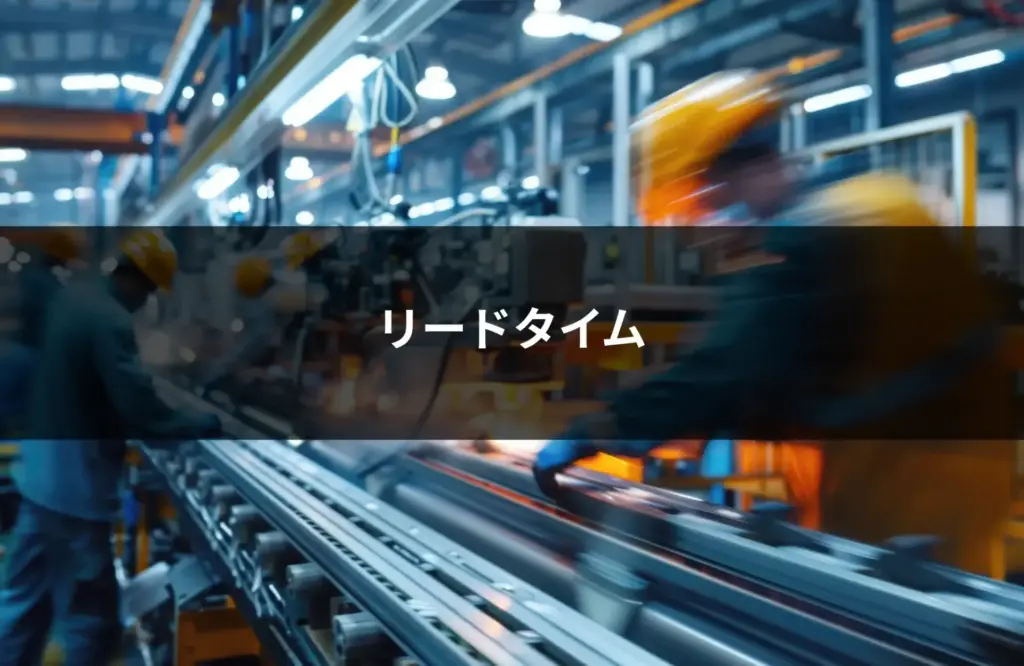
リードタイムの短縮は、製造業が競争力を高める上で重要です。しかし、リードタイムは短いほど良いというものではなく、品質やコストとのバランスも考慮する必要があります。このため、改善に苦慮している企業も多くいるかと思います。
当記事では、リードタイムとは何か、種類や計算方法、類似用語などの基本から、具体的な短縮方法や注意点を解説します。記事末では、生産管理システムでリードタイムの最適化に成功した企業事例も紹介します。
リードタイムとは
リードタイム(L/T)とは、発注(オーダー)から納品までに必要な時間を指します。製造業では、手番・先行日数・基準日程という言葉が使われるケースもあります。
また、製造業においては、製品開発・調達・生産・物流のそれぞれのプロセスごとのリードタイムという考え方もあり、いずれも「いかにリードタイムを短縮するか」が重要です。
リードタイムを短縮する重要性
リードタイム短縮には、具体的に以下のようなメリットがあります。
- 顧客対応力の向上:迅速な納品を可能にし、顧客満足度の向上につながる
- 市場競争力の強化:新製品をいち早く市場に投入し、競合他社に先行する
- 在庫管理の最適化:余分な在庫を保有する必要がなくなる
- コスト削減:在庫管理や保管のコスト削減でキャッシュルフロー改善に繋がる
- リスク低減:需要の変動や市場環境の変化に柔軟に対応できる
- 製造工程の効率化:むだな工程の削除や稼働率向上で生産が効率化できる
リードタイムを短縮すると、顧客にスムーズに製品が供給されるようになり、顧客満足度の向上に繋がります。また、需要の変化に柔軟に対応できるようになれば、市場競争力も強化できます。
また、リードタイムが短くなると在庫回転率を上げやすくなり、在庫を抱えることで発生するコストを削減できます。その結果、売上サイクルが早くなり、キャッシュフロー向上に繋がります。さらに、在庫を多く持たないことで、需要変動による在庫陳腐化のリスクも低減できるといえます。
リードタイムの種類(プロセスごと)
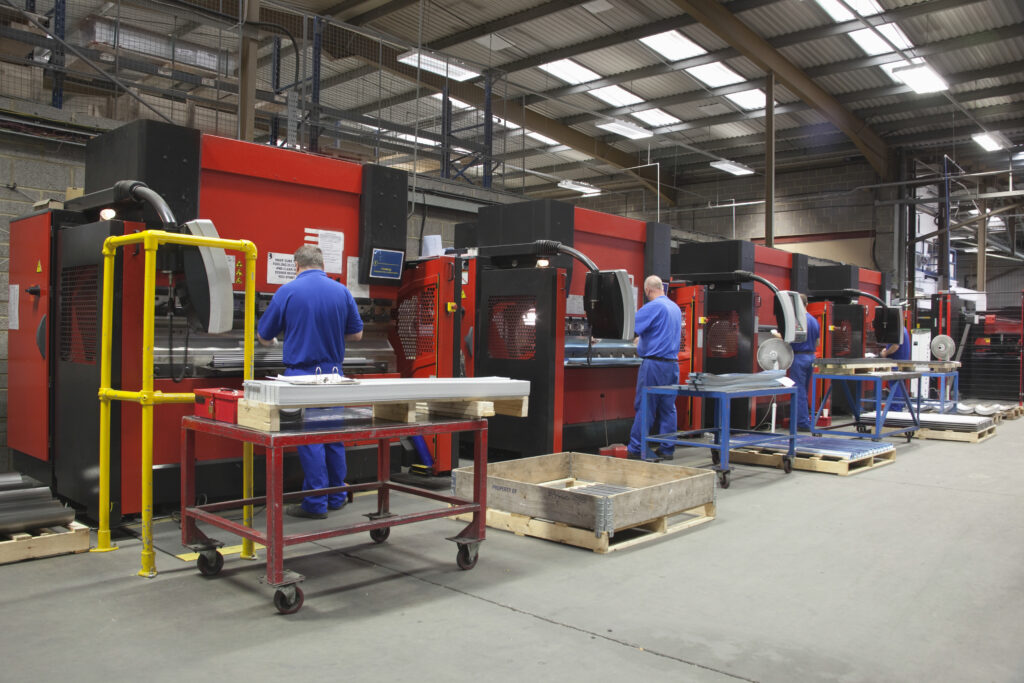
一般的なリードタイムが発注から納品までの期間を指すのに対し、特定のプロセスごとにリードタイムを分類するケースもあります。主な種類は以下のとおりです。
リードタイムの種類
- 開発リードタイム:製品の市場調査、設計、試作、検証に要する時間
- 調達リードタイム:部品や原材料の発注から納品までにかかる時間
- 製造(生産)リードタイム:製造から製品完成までの期間
- 物流リードタイム:出荷指示後、出荷~顧客に届くまでの期間
- トータルリードタイム:上記のすべてのリードタイムを含む合計時間
リードタイム短縮の際は、どのリードタイムにボトルネックがあるか分析することが必要です。
類似用語との違い
製造業では、リードタイムと似た用語も多く用いられます。それぞれ異なる意味を持つため、違いを理解すると役立ちます。
納期
納期とは、顧客が求める製品やサービスの納品期限を意味します。リードタイムは、製品が完成するまでの全工程でかかる時間(期間)を意味し、納期はその中で顧客に関わる部分を指します。
具体例を挙げると、「希望納期は10月30日」「この製品のリードタイムは15日だから、10月15日には発注しよう」といった使い方になります。
タクトタイム
タクトタイムとは、目標となる生産ペースを表す指標の一つです。顧客の需要に対し、1つの製品を完成させるための目標時間(理論値)で、標準作業の3要素の一つです。
サイクルタイム
サイクルタイムは、製品1個の生産に要する実際の時間を示します。主に、生産効率を上げるために「タクトタイム=サイクルタイム」を目指すための比較対象として用いられます。
スループットタイム
スループットタイムは、一定時間あたりの処理速度(生産能力・処理能力)を表します。製造業だけでなく、通信分野における処理速度、ソフトウェア開発における業務処理能力など、あらゆる評価指標として用いられます。
在庫回転期間
在庫回転期間は、在庫を売り切る(在庫が入れ替わる、回転する)までの平均日数を指し、在庫管理の指標として用いられます。
標準時間(スタンダードタイム)
標準時間(スタンダードタイム)とは、標準化された工程の所要時間を指します。正味作業時間と余裕時間(段取り替えや待ち時間など)の合計時間で、生産計画や工程管理で多く活用されます。
リードタイムの計算方法
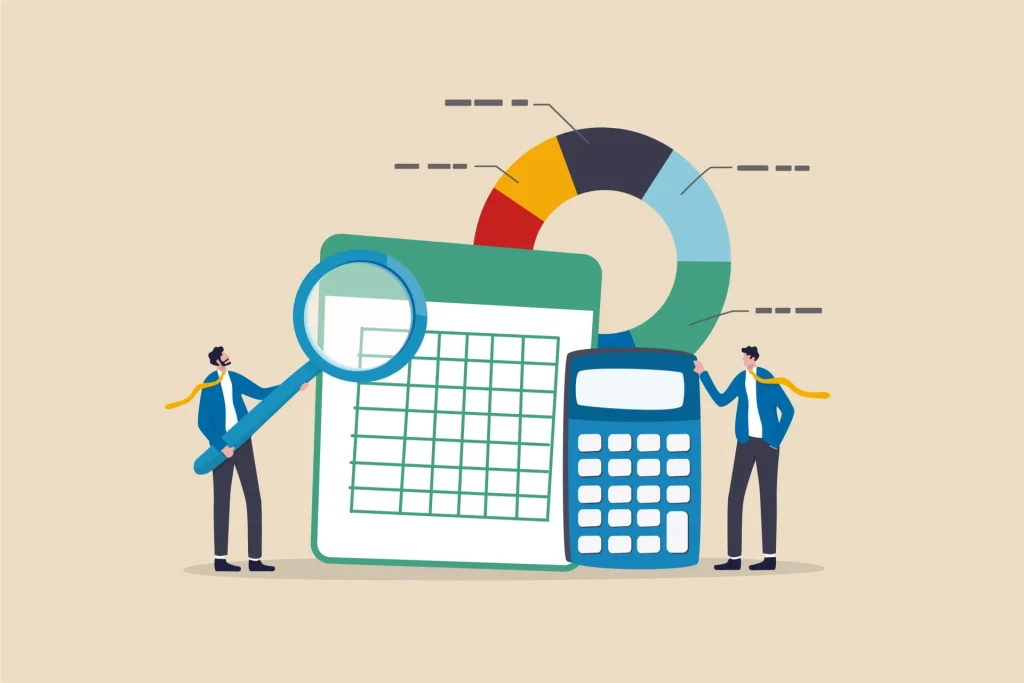
顧客からリードタイムの問い合わせを受けた際など、リードタイムを計算しなければならない場面が多々あるかと思います。リードタイムには、2つの計算方法があります。
フォワード法
フォワード法は、製造の作業開始日から各工程にかかる時間を積み上げる形で、リードタイムを計算する方法です。計画生産などに活用しやすい計算方法ですが、各工程の正確な時間を測定する手間がかかるというデメリットもあります。
<例>
調達リードタイム(3日)+生産リードタイム(7日)+物流リードタイム(5日)=トータルリードタイム(15日)
バックフォワード法
バックフォワード法は、納期を基準に逆算してリードタイムを計算する方法です。納期に合わせるための計画が立てやすいため、受注生産などに適しています。一方で、納期が厳しい場合には各工程に無理が生じる可能性があります。
<例>
納期が10月15日の場合:-物流リードタイム(5日)・生産リードタイム(7日)・調達リードタイム(8日)で配分など
各種リードタイムの短縮方法
開発リードタイム:設計仕様や部品の標準化
設計開発の時間を短縮するためには、仕様や部品の標準化が効果的です。開発のたびにすべてを一から開発するのではなく、共通品も活用することで、開発スピードを向上できます。図面管理システムなどを活用し、類似品情報を見つけやすくすることも効果的です。
また、共通部品を増やすと、在庫を適正化しやすいというメリットもあります。
調達リードタイム:発注業務効率化と仕入先見直し
調達リードタイムには、「仕入先に発注するまでの時間」と「発注後に仕入先から届くまでの時間」が含まれます。どちらに時間がかかっているかを把握し、切り分けて対処する必要があります。
仕入先に発注するまでの間、在庫確認や発注計算に時間がかかっている場合は、システム活用などによる業務効率化が必要です。在庫管理と発注がシームレスに可能なシステム(生産管理システムなど)を活用すると、発注の自動化も可能です。
仕入先からの納入までに時間がかかっている場合は、仕入先への納期短縮交渉、場合によっては仕入先の見直しとなります。日頃からの仕入先との連携が重要です。
製造(生産)リードタイム:ムダの排除
製造リードタイム短縮の基本は、付加価値を生まないむだな作業の削減です。参考になる指標として、トヨタ生産方式の「7つのムダ」という考え方があります。
7つのムダ
- 加工
- 在庫
- 造り過ぎ
- 手待ち
- 動作
- 運搬
- 不良
- 手直し
例えば、動作のムダが多い場合は、工具や作業場の配置の見直しといった作業環境の改善案が考えられます。作業員の手が止まり、手待ちのムダが度々ある場合は、需要予測や生産計画の見直しも必要です。手待ちの原因が頻繁な設備故障であれば、設備修理なども改善案になり得るでしょう。
→ 参考記事:トヨタ方式から学ぶ「7つのムダ」をなくす方法
このように、製造リードタイムが延びる要因は多岐にわたります。各業務ごとのリードタイムのうち、短縮の難易度が高いものの一つです。
物流リードタイム:
物流リードタイムには「出荷リードタイム(出荷指示からピッキング、出荷準備完了まで)」と「配達リードタイム(出荷から配達完了まで)」があります。物流業界での改善で着手されやすい指標です。
製造業の事例では、在庫品の出荷がスムーズに行かず、出荷リードタイムが長くなるケースがあります。在庫品を探す時間がかかる場合は、在庫管理システムなどでのロケーション管理が効果的です。
難易度リードタイムの過度な短縮は禁物:改善時によくある失敗
リードタイム短縮は、多くの製造業の企業が試みる改善策です。しかし、改善方法が適切でないと、QCD全体が悪化し、品質やコストが犠牲になりやすいので注意が必要です。
QCDとは、生産効率を上げるための3要素「品質(Quality)・コスト(Cost)・納期(Delivery)」を指します。これらはトレード・オフの関係で、リードタイム短縮による短納期を重視しすぎると、他方の品質・コストが低下します。その結果、全体としてQCDが悪化してしまいます。
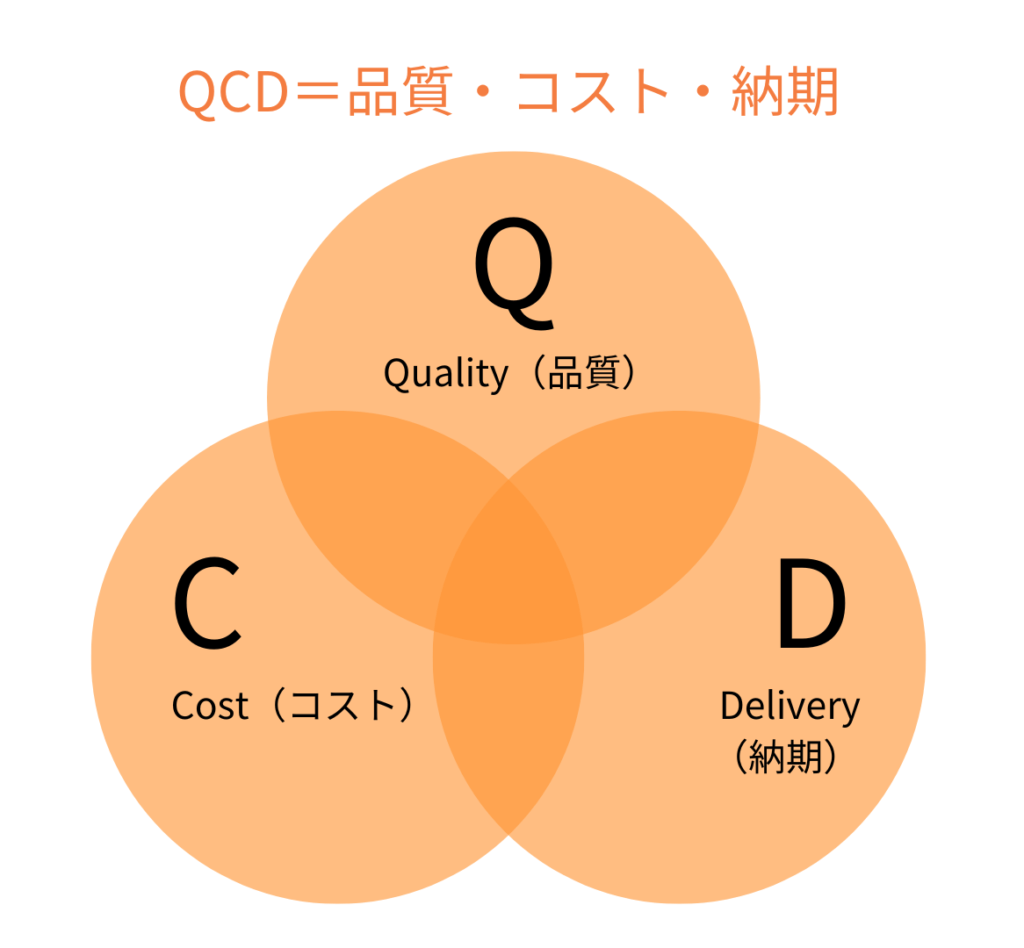
具体的には、以下のような失敗が起こりやすくなります。
無理なリードタイム短縮による品質低下
短縮を最優先すると、製品やサービスの品質が低下しやすくなります。
■リードタイム短縮を優先して品質低下する例
- 製造リードタイムを短くするために検査を減らし、不良率が上がってしまった
- 調達リードタイムの短さで仕入先を選び、不良品が多く届くようになった
このような品質低下が起きると、顧客満足度が低下し、ブランドイメージが損なわれる可能性があります。
リードタイム優先で在庫過多になる
在庫を多く持つと、生産や出荷が必要になった際に短いリードタイムで対応しやすくなります。しかし、在庫を多く持ちすぎて過剰在庫になってしまうと、在庫コストが膨らみ、キャッシュフロー悪化に繋がります。特に、工程数が多い製品を生産する企業では、仕掛品の滞留も要注意です。
目指すべきは、適切な安全在庫の設定です。生産のペースや在庫コストも考慮した安全在庫を設定し、在庫が適切に回るようになれば、リードタイムと在庫の双方を適正化できます。
関連部門間との連携不十分
上記のようなQCD悪化の事例は、部門間の連携不足で発生するケースも多々あります。リードタイム短縮は、製造、調達、物流など、複数の部門が関与します。適切なリードタイムを模索するためには、部門間連携が不可欠です。
適切なリードタイム改善は「現状把握」から始める
リードタイムを適切に短縮するには、まずは現在の生産やリードタイム状況を把握する必要があります。現状を知って初めて、どのリードタイムがボトルネックになっているかを分析できます。ボトルネックがわからないままにリードタイム改善をしようとすると、前述のように極端な改善に走りやすくなります。
特に、「製造リードタイム」の把握に課題のある企業が多い傾向にあります。製造リードタイムの分析をするには、各製造工程の工数を集計する必要があります。この集計は、紙やエクセルだと手間がかかるため、そもそも工数を集計していないという工場も多いのが現実です。
リードタイム短縮に役立つ生産管理システムとは
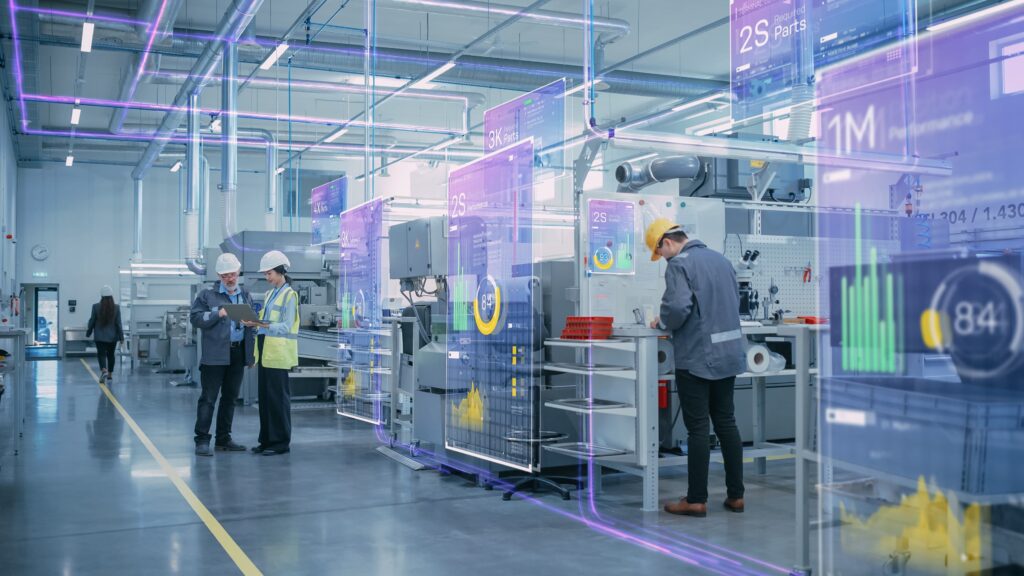
リードタイム短縮のための分析には、システムやツールの活用が効果的です。中でも「生産管理システム」は、収集が難しい生産データの自動集計や部門間共有に役立ちます。
生産管理システムのリードタイム短縮に役立つ機能
- 工数自動集計:デジタル作業日報で各工程の作業開始・終了時刻から工数を自動集計
- 在庫管理機能:安全在庫や発注点を設定し、リアルタイムに入出庫や在庫数を管理
- 発注管理機能:現在庫数を見ながらシームレスに発注、調達リードタイムや実際納期まで管理
工数集計の機能で製造リードタイムを収集・分析すると、人や設備によるバラつき、他製品と比べてリードタイムが長い製品などを発見しやすくなります。
また、在庫管理と発注管理を一つのシステムで一元管理すると、調達リードタイムと在庫数を紐づけて管理できます。実際に、生産管理システムの在庫管理機能でリードタイム分析をし、在庫金額を年間100万円削減できた企業の事例もあります。
事例の詳細はこちら:在庫管理のシステム化に成功!リアルタイムな在庫管理で年間100万円の在庫削減
また、クラウド型の生産管理システムを活用すると、同じデータベースを部門間で共有できます。クラウド型システムは、インターネット環境さえあれば、拠点が異なる担当者や在宅勤務の担当者も同じ情報を活用できるためです。リードタイム改善において、情報共有のための伝達の手間を削減できるメリットは大きいといえます。
22種類の生産管理システムをランキングで比較
初期費用相場や選び方のポイントをチェック
生産管理システムをそれぞれの特徴や初期費用相場などで比較したい場合は、「生産管理システムランキング」も是非ご覧ください。生産管理システムは、自社の製品・生産方式・企業規模などに適したものを導入しないと、得られるメリットが限定されてしまいます。事前適合性チェックや生産管理システムを選ぶ前に押さえておきたいポイントも解説していますので、製品選びの参考にしてみてください。