品質管理とは?具体的事例を挙げて、考え方、管理手法、具体的手順まで徹底解説
公開日:2024年11月28日
最終更新日:2024年11月29日
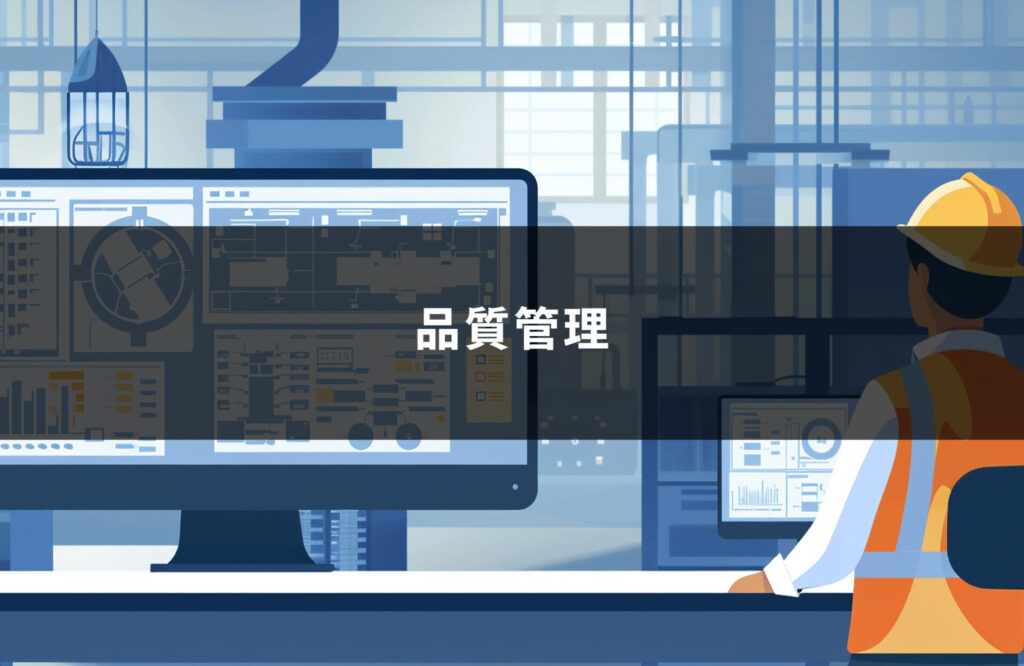
品質管理は、製造プロセスを管理することで、品質不良を最小限に留めるための取り組みです。本記事では、歴史的な背景や品質保証との違い、品質管理部門の役割と仕事内容について紹介します。また、基本的な考え方と関連するQMS規格、未然防止のための管理手順と具体的手法について事例を交えながら解説しました。さらに、品質改善に活用できる品質管理ツールについても取り上げ、現場での実践的な活用方法を詳述します。
品質管理とは?
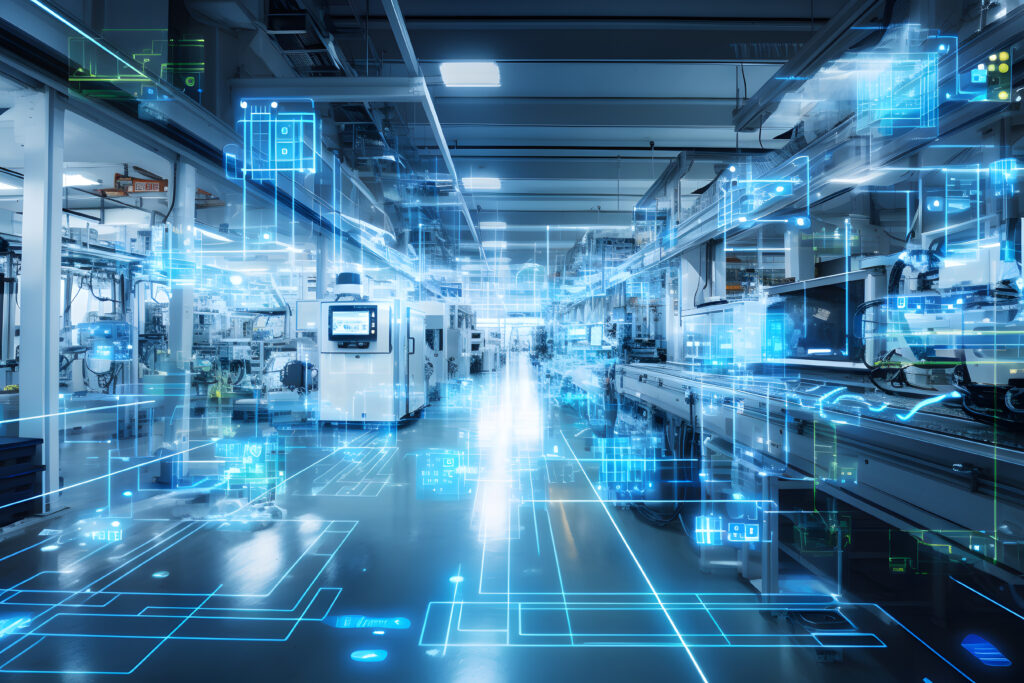
品質管理とは、狙い通りの製品品質を確保するためのプロセスです。製造業では、品質不良の発生を最小限に抑えることで、製品の信頼性向上とコスト削減が実現します。まず品質管理の歴史とその本質的な目的、また品質保証との違いについておさらいします。
品質管理の歴史
科学的な品質管理は、1920年代にアメリカで統計管理図が考案されたことが始まりです。工業的な大量生産の拡大に伴い不良品発生が大きな問題となり、製品の不良を減らすために企業や組織が品質管理の手法を発展させてきました。
日本では戦後、アメリカから統計的品質管理(Statistical Quality Control:SQC)が持ち込まれ、やがて全社的品質管理(Total Quality Control:TQC)へと発展しました。1980年代には、国際的な品質基準として品質マネジメントシステムISO 9001が制定され、グローバルでの品質管理が統一されるようになりました。
2000年代以降は、IoT(Internet of Things)や機械学習・AIなどのデジタル技術が品質管理に取り入れられるようになりました。これにより、リアルタイムでのデータ監視や予測分析が可能になり、多くの企業が活用を始めています。
品質管理とは、品質不良を最小限に留めるための取り組み
品質管理とは、製品品質の維持・向上を目的として、設計品質・顧客仕様からの逸脱を最小限に抑えるための取り組みです。製造プロセスにおける品質面での管理を行い、製品の出来栄え評価を関連付けて改善を進め、品質不良発生の最小化を図ります。
具体的な品質管理手法としては、以下のような方法が知られています。
- 統計的品質管理(SQC):統計的に製造工程のバラツキを管理する技術的手法
- 総合的品質管理(TQC):企業全体で品質向上に取り組むマネジメント手法
- 総合的品質経営(TQM):経営全体で品質管理を通して顧客満足度を向上させる取り組み
品質管理と品質保証の違い
品質管理と似た概念として、品質保証という概念があります。
品質管理は社内での取り組みで、製造プロセスの管理・改善により不良品の発生を減らし、製品の設計品質を安定的に確保します。一方、品質保証は、顧客に対して行うもので、完成した製品から不良品を確実に排除して、製品が顧客仕様を満たすことを保証します。これらを簡潔にまとめたものが以下の表です。
品質管理 | 品質保証 | |
対象 | 社内 | 顧客 |
目的 | 製造プロセスの管理不良品の発生防止 | 製品の仕様・性能保証不良品の流出防止 |
品質管理の仕事内容
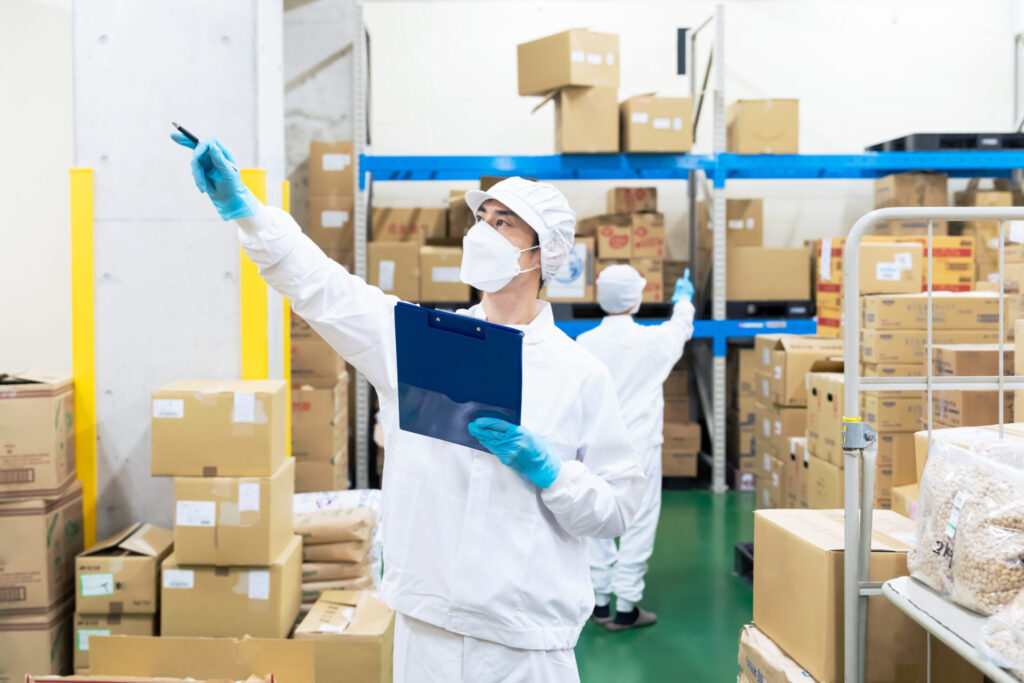
品質管理の主な仕事は、不良品の発生を防ぐために、製造工程や製品の出来栄えを監視・改善する仕組みを整備し、運用することです。適切な運用を行うためにも、品質管理部門、品質管理担当者、製造現場担当者がそれぞれの役割をしっかりと担い、連携することが不可欠です。
品質管理部門の役割:品質管理に関する仕組み整備
組織全体における品質管理体制の構築を主導し、各部門にその実行を促すことが品質管理部門の役割です。品質方針や品質管理に関わる規則・ルールを策定し、定期的に見直しを行い、現場での品質管理を社内で標準化します。
また、製造部門だけでは推進が難しい大規模な改善も、品質管理部門が行います。例えば、工程内の品質検査に関する抜本的見直し、トレーサビリティシステムの導入など、費用や手間がかかる改善は、製造部門だけでは実行が困難なことも多いです。このような品質改善の後押しをすることで、各部門の品質レベルを維持・向上を加速することができます。適切な品質管理を通して不良発生率を低減させ、部門として組織全体の業績向上を牽引します。
品質担当者の役割:品質管理と製造現場の橋渡し
品質方針や品質管理に関わるルールを製造現場に展開し、現場での品質問題をみつけたり改善活動を支援したりすることも品質管理担当者の役割です。
製造現場では品質管理に関して十分な知識を持っていないケースがあり、単に方針や規則を展開しただけでは適切な運用が難しいのが実情です。品質管理担当者は、複数の現場を担当することが多く、より広い視野を持って取り組める一方で、特定の製造現場の実態を詳しく把握することは難しいでしょう。このため、製造現場とコミュニケーションを密に取り、社内品質基準の浸透を促したり改善活動の進捗を管理したりする必要があります。
このような活動を通して、製造現場の不良発生や異常を迅速に検出し、早期解決を図ることができます。さらに、不良発生の未然防止ができるようにしたり支援することも重要です。
製造現場の役割:早期の異常検知と対策
製造現場における品質管理とは、品質方針やルールに従い、日々の製造工程の中で異常の早期検知と迅速な対策、さらに未然防止に努めることです。「品質管理部門があるから現場は製造に専念する」というスタンスでは、効果的な品質向上は望めません。
一方で、品質管理の施策やテクニックを十分に理解した人材が不足していることも多いでしょう。このため、異常を発見したら一時的な異常処置に留まらず、品質管理部門などと連携して十分な原因究明を行ったうえで再発防止策を講じます。
現場の担当者が速やかに異常に気づける体制を整えることは、品質向上に大きく貢献します。また、近年では、工程データをリアルタイムで自動解析する技術が登場し、より確実な異常検知が可能になりつつあります。
品質管理の考え方
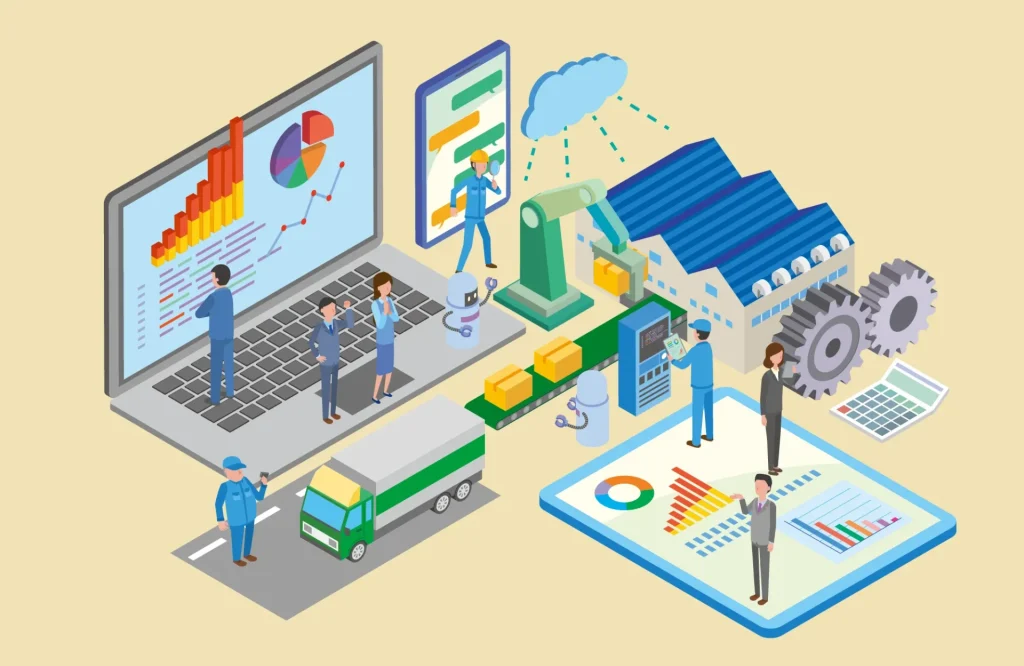
品質管理においては、再発防止、品質改善、未然防止の3つのアプローチが基本です。それぞれのアプローチによって品質向上の観点が異なり、問題発生の回避と改善が可能になります。また、これらを整理して要求事項をまとめた品質マネジメント(QMS)規格の中でも、具体的な品質管理の指針が示されています。
再発防止:多くの類似事例へ水平展開する
工程トラブルやこれに伴う品質不良の再発防止は、品質管理の代表的な取り組みの一つです。ここでの再発防止といえば、発生した問題に対して原因を徹底的に分析して根本的な対策を打つ、ということに留まりません。なぜなら、どこまで類似の想定トラブルを想定して、横展開できるかが最大のポイントであるからです。
ここでは、食品業界において、製品に金属異物の混入トラブルが発生した例を考えます。異物混入が発生した製造ラインの総点検を行ったところ、充てん装置のコンベアに使用されたボールチェーンの破片と判明しました。単に新品に交換するだけでは再発するため、破損しても異物混入に繋がりにくいチェーンに変更するのが最も基本的な再発防止です。
この再発防止策をどこまで横展開できるかがキーポイントです。同型式の装置についても同様の対策を行うのは最低限の再発防止です。工場内の製造ライン中において、製品に混入する可能性のある場所でボールチェーンを使用した個所を洗い出します。抽出されたリスクのある個所について、故障しにくいチェーン式に変更する、または設備の定期点検でボールチェーンの交換を行う、などの対策を実施します。
このように、類似事例への水平展開をすることで、より広い範囲での「再発防止」を行うことが可能となります。
品質改善:継続的にPDCAサイクルを回す
品質改善のためには、PDCA(計画、実行、確認、改善)サイクルを継続的に回すことが欠かせません。このサイクルを回し続けることで、品質が着実に改善され、製品の品質が向上します。
以下の表は、食品加工業界において、パッケージサラダの加工業者が、「すぐにサラダが変色する」という意見を受けた場合のPDCAサイクルです。鮮度保持の向上が課題であり、これに対して有効な改善が確認できるまで、PDCAサイクルを回します。
Plan | ・目標:サラダ製品の鮮度を維持して、鮮度劣化による変色を軽減する ・改善策:変色の原因と考えられる「洗浄工程」や「包装工程」の見直し。 ・具体的な改善案: ①洗浄後の乾燥時間を見直す ②包装フィルムの酸素透過率を調整する ③冷却工程の温度管理を強化する |
Do | ①洗浄工程の変更 :乾燥時間の短縮により、葉の水分保持を増やし、鮮度が保たれるかを確認 ②包装フィルムの変更 :酸素透過率の低いフィルムを使用し、包装内の酸素量を低減 ③冷却温度の管理強化 :冷却工程の温度をより厳密に設定し、変色を抑制する |
Check | ・データ収集 :一定期間保存し、変色の改善有無についてデータ収集 条件ごとに出荷前後で数日間観察し、サラダの色や硬さなどの変化を記録 ・顧客からのフィードバック :変更後の製品を出荷し、小売業者からのフィードバック結果を確認 |
Act | 改善の標準化 :改善効果があると確認できた場合、新しい手法を標準作業として導入。 次の課題の設定 :効果が不十分であれば、冷却温度や酸素透過率の再調整など、別の改善策を計画 |
未然防止:リスクに基づいて考える
未然防止の観点から、潜在的なリスクを事前に把握し、対策を講じることで不良の発生を未然に防ぐことが重要です。リスクアセスメントを通じて、リスクに応じた優先度をつけて予防的な対策を施すことで、品質トラブルの防止が可能です。
医療機器業界では、製品不良が人体に致命的な影響を及ぼす恐れがあるため、未然防止が重要です。一例として、手術用カテーテルの微小な傷によって、血管への挿入中に破損するリスクが判明したケースを考えます。
製造工程を精査したところ、微小な傷は使用設備の摩耗にあると特定しました。対策として、機械部品の定期点検・交換スケジュールの設定、高精度カメラによる傷検知システムの導入、工程内検査の強化が実施されました。このように、実際にインシデントが起こる前にリスクに基づく未然防止策は、品質管理の主要な構成要素の一つといえます。
品質マネジメント規格の要求事項
品質管理に関する国際規格の中でも、基本的な考え方から具体的取り組みに関する要求事項までが規定されています。主な国際規格は次の通りです。
- ISO 9001:顧客満足と品質向上を実現させるための品質管理の枠組み
- IATF 16949:ISO9001を基盤とした自動車業界向けの品質規格
- ISO 13485:医療機器業界において、安全性と法規制への適合を重視した品質規格
- ISO 22000:食品業界における製造から流通までの安全管理の指針を示す国際規格
品質マネジメントシステム(QMS)については、こちらの記事で詳しく解説しています。
→QMS(品質マネジメントシステム)を徹底解説:QMS構築の基本と具体的な運用方法
攻めの品質管理に必要なこと
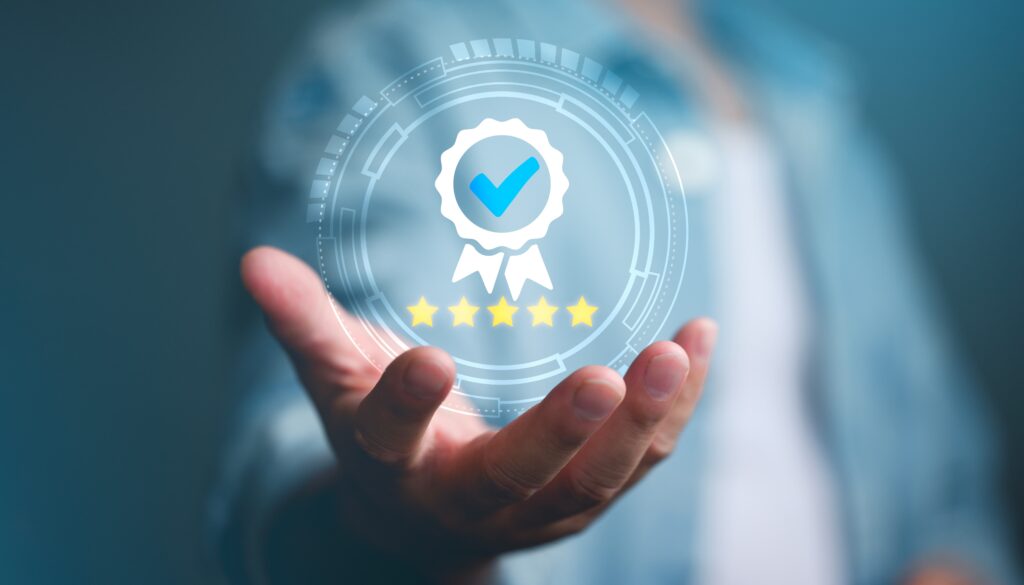
攻めの品質管理では、再発防止だけでなく未然防止を強く意識します。工程・製品検査のデータにトレーサビリティを持たせて関連付けることで、トラブルの予兆を早期に発見し、事前に対策を取ることができます。
再発防止から未然防止へ
攻めの品質管理を実現するためには、未然防止に重点を置いた施策が最も有効であることを認識する必要があります。
一般的な品質管理では再発防止に目が向きがちですが、これはあくまで対症療法に過ぎません。品質課題の真の原因をより高い視点で捉え、多くの製品や工程に水平展開することが未然防止の第一歩です。
また、品質管理はトラブルが発生した後の対応だけではありません。製品設計や工程設計の段階から、リスクを基に可能な限り多くの問題を想定することも重要です。リスクベースの考え方を取り入れることで、有効な対策を講じやすくなり、量産時により効果的な未然防止が可能になります。
トレーサビリティの確保
未然防止に主眼を置いた品質管理では、履歴を精緻に分析することが基本であるため、トレーサビリティの確保が欠かせません。製品の製造工程に関する履歴や素材・部品の情報を追跡することで、工程における異常に対して、データをもとに対策立案できるようになります。
自動車産業では不良品が死亡事故に繋がるため、特に未然防止が重視されています。自動車産業向けQMS規格であるIATF16949では、この重要性を考慮して規格要求事項で明文化されています(要求事項8.5.2.1。
工程データ管理と品質検査結果の関連付け
記録された工程履歴と品質検査結果を関連付けて分析することで、品質向上に役立つ新しい知見が得られます。これにより、適切な不良の検知方法や事前の兆候の発見、発生原因の特定が容易になります。様々な工程データの分析によりリスク要因を特定でき、品質改善の優先順位付けや対策立案に役立ちます。
一例として、電子部品業界において、絶縁性や熱伝導率を上げるために使われるセラミックス基板の成形工程を例に挙げます。この工程では、金型に粉を詰めたのち、強い圧力をかけてプレスすることで基板を成形しますが、寸法の不良率が高いことが課題でした。
様々な工程解析の結果、狙い寸法からの乖離にはプレス圧の影響が最も支配的であるとわかりました。プレス圧力が不足すると、セラミックス基板の粉末が十分に圧縮されず、狙いの寸法からの乖離が大きくなり、寸法不良が発生しやすくなります。これをデータで示したものが次の図です。
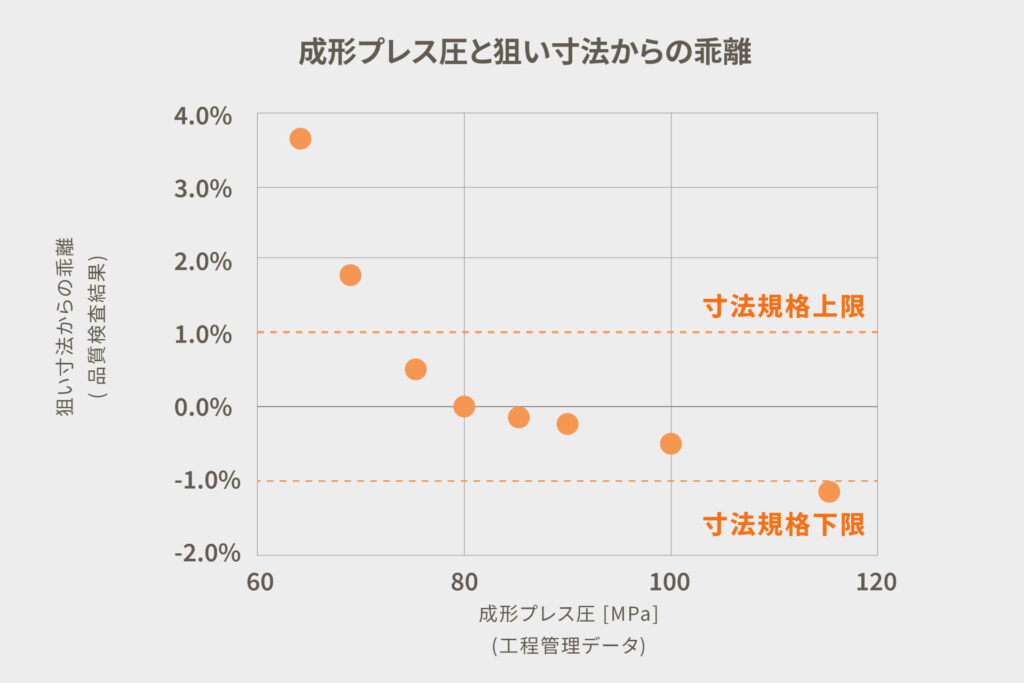
従来は成形プレス圧を75MPaで実施していましたが、寸法規格上限外れのリスクが高い状況を示しています。現状では品質ばらつきの影響で不良発生リスクが高いため、プレス圧を上げることで改善の見込みがあると判断できます。
このように、工程管理データと品質検査結果を関連付けられれば、重要な工程データを絞り込み、適切な対策で不良品質を未然防止することができます。
重要な工程・検査データの見える化
工程や検査データの重要な指標を見える化することで、工程や製品における異常発生やその兆候を早期に検知できます。
トレーサビリティの確保だけでは、異常が発生した後の事後処理の精度向上に留まります。しかし、工程データは多数あるため、それらすべてを頻繁に確認するのは現実的ではありません。このため、品質検査結果と関連付けて重要な指標を絞り込み、そのデータが誰でも速やかに確認できるよう、見える化しましょう。
一例として、金属製品の油圧プレスによる加工を挙げます。油圧プレス機は時間経過とともにオイルが劣化して油圧が低下する等の理由で、製品がうまくプレスできなくなることがあります。
ある事例では、製品厚み不良の原因究明のため、プレス機メンテナンス直後から月ごとの製品厚み寸法の推移を箱ひげ図で見える化しました。この分析により、メンテナンス後18か月で管理値の上限を超え、不良が発生していたことが確認されました。さらに、12か月目以降から徐々に厚みが増しており、不良発生の兆候がその時点で見え始めていたことも明らかになりました。
このように、重要指標をあらかじめ見える化しておけば、不良が発生する前にメンテナンスを実施する判断が可能になります。
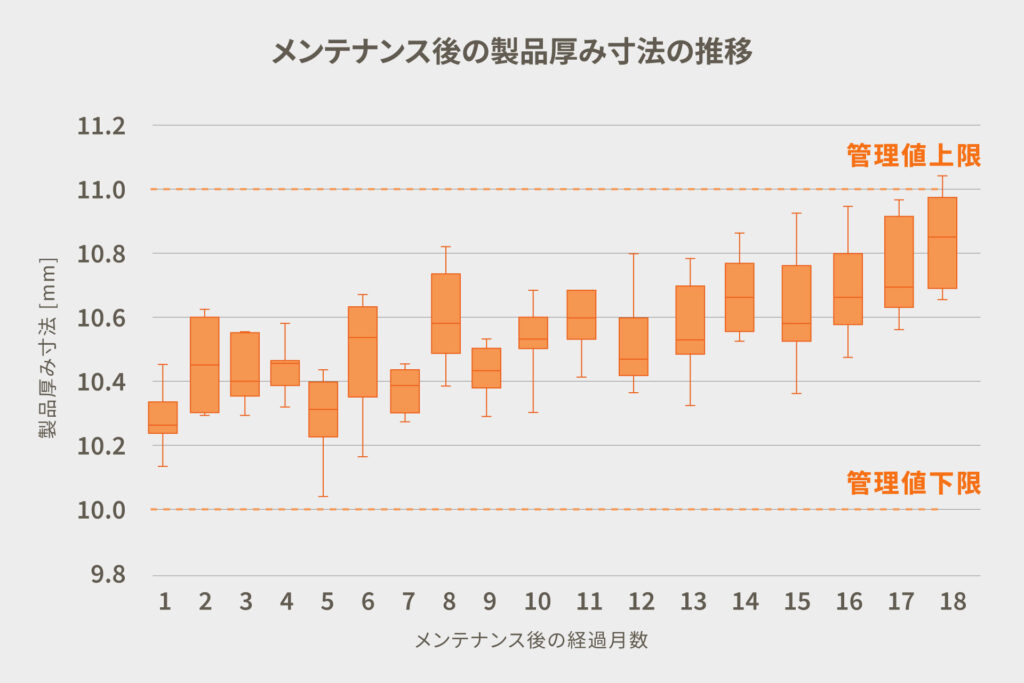
リアルタイム検知と即時対応
センサーやIoT技術の活用により、リアルタイムで異常を検知し、品質不良の発生を未然に防げる可能性を高められます。
重要な工程・検査データの見える化は必要ですが、手作業で集計していると対応が遅れがちです。そこでIoT技術を導入することで、工程管理値を逸脱した際にアラームを発報させ、製造中のトラブルを即座に検出できるようになります。さらに、機械学習も組み合わせれば、管理値の範囲内で発生する異常の兆候も捉え、早い段階で適切な対応が可能になります。
品質管理ツール
品質管理には、問題解決や品質改善に役立つツールが多数あります。以下、具体的なツールについて解説します。
QC7つ道具
QC7つ道具は、基本的な品質管理ツールであり、問題を特定したり、問題の原因を分析して改善計画を策定するために使用されます。具体的には、以下の7つのツールがあり、これらに層別分析を含めることもあります。
- パレート図:問題の原因を重要度の高い順に並べて表示する図
- 特性要因図:問題の原因を体系的に分類し、視覚的に整理する図
- ヒストグラム:データの分布を棒グラフで示し、傾向を可視化する図
- チェックシート:データの収集や整理を行うために使う表形式のツール
- グラフ:データを視覚化し、傾向や変動などをわかりやすく表示する図
- 管理図:工程が安定しているかを監視するために用いる図
- 散布図:2つの変数の関連性や相関を視覚化して示す図
新QC7つ道具
新QC七つ道具は、複雑な問題や品質改善の場面で、データやアイデアを整理・分析する手法です。定性データを使い、問題を分かりやすく構造化することで、込み入った内容をチーム間で共有し、スムーズな意思決定を促します。具体的には、次の7つの方法です。
- 親和図法:情報をグループ化し、問題を構造的に整理
- 連関図法:因果関係を視覚化し、複雑な問題を整理
- 系統図法:目標達成の手段を階層的に整理する
- マトリックス図法:複数要素の関係を表で整理し可視化
- マトリックスデータ解析法:数値データを分析し要因の関係性を明確化
- アローダイヤグラム法:作業順序を矢印で示し、計画を管理
- PDPC法:プロセス上の問題を予測し、対策を立案
FTA:故障の木解析
FTA(Fault Tree Analysis)は、製品・システムの不具合の原因について、発生原因を特定し、対策を立てるための解析手法です。1960年代に航空宇宙分野で開発され、現在は自動車や医療機器など多くの産業で使用されています。
FTAでは、望ましくない事象(故障)から原因を辿り、故障の要因をツリー構造で整理します。想定される原因を一覧化して整理することで本質原因の抜け漏れを防ぎ、確実性の高い対策が立てやすくなります。
一例として、金属製品におけるプレス寸法が狙いよりも厚いという不具合に対して、FTAを図示したものが次の図です。このように抽出された要因を見える化して現状の評価を行い、優先順位をつけて考えられる対策の検討を実施します。

FMEA:故障モード影響解析
FMEA(Failure Mode and Effects Analysis)は、製品や工程で起こりうる不具合とそのリスクを事前に分析し、優先順位をつけて対策を行う品質管理手法です。
FMEAでは、故障モードごとに具体的な原因・影響を記載し、それぞれの原因について、発生頻度、重大度、検出のしやすさを評価します。これらを掛け合わせた評価点(RPN)を算出し、評価点が高いから優先的に対策を講じてリスクを低減します。この手法は、自動車産業を中心とした製造業などで広く活用され、製品・工程設計におけるリスク管理に貢献します。
以下の表は、金属製品のプレス工程で実施したFMEAの一部です。設備・工程ごとに想定される不良を見える化することで、品質不良の発生しにくい工程を作りこむことができます。
設備・工程 | 故障モード | 故障の原因 | 故障影響 | 影響度 | 頻度 | 検出度 | 評価点RPN |
プレス工程 | 油圧低下 | 油圧オイルの劣化油圧シールの劣化油圧ポンプの摩耗 | 寸法不良 | 3 | 8 | 2 | 48 |
プレス圧力の設定ミス | 寸法不良 | 寸法不良 | 2 | 8 | 5 | 80 |
SPC:統計的工程管理
SPC(Statistical Process Control)は、データをもとに製造工程を監視し、品質を安定させる管理手法です。収集した工程データを統計的に分析し、異常発生リスクを事前に見積もることで、課題を抽出しやすくなります。
中心的なツールは、管理図と工程能力指数Cpkを用いた管理の2つです。管理図は、データの平均(中心線)と管理限界を基に工程のばらつきを視覚化し、異常を即座に検出します。Cpk管理では、統計的に工程のばらつきと中心値のズレを評価し、規格を満たす製品を安定して作る実力があるかを判定します。
SPCは、データに基づいた客観的な品質管理が可能で、早期発見によるトラブル未然防止、工程の安定化に役立ちます。一方で、データを継続的に収集する必要があり、解析にやや専門知識が必要です。
MSA:測定システム解析
MSA(Measurement Systems Analysis)は、測定データの信頼性を確保するため、測定システムの誤差やばらつきを評価する手法です。具体的には、次の5つの観点で測定が安定し正確に行われているかを確認します。
- 繰り返し性:同一測定者・装置で測定を繰り返した際のばらつきを評価
- 再現性:異なる測定者や装置で測定した際のばらつきを評価
- 直線性:測定範囲で、測定値と実際の値の差が一定かを評価
- バイアス:測定値と真値の差を確認し、偏りを評価
- 安定性:長期間の測定精度が維持されているかを確認
これにより、測定データに偏りや誤差がないかを確認し、計測値の信頼性を高めます。判断指標の正確性が担保されるため、測定データをもとに判断をして問題ないことが証明できます。
品質管理システムやソフトウェアでの解析自動化
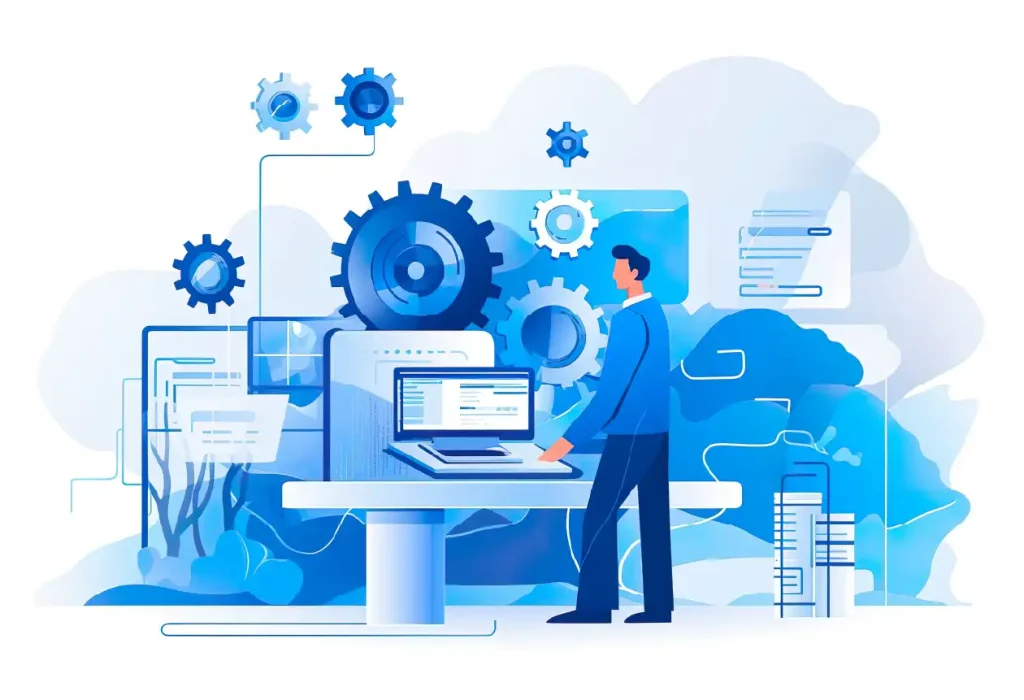
品質管理における解析は複雑で専門知識を要します。このため、この解析を品質管理システムやソフトウェアで自動化することで、データのトレーサビリティや信頼性、速報性が確保でき、品質向上活動が効率化されます。
製造業向けの品質管理システムについては、こちらで解説しています。
製造業向け品質管理システム13選!機能や特徴、導入メリット、選び方をまとめて紹介
22種類の生産管理システムをランキングで比較
初期費用相場や選び方のポイントをチェック
生産管理システムをそれぞれの特徴や初期費用相場などで比較したい場合は、「生産管理システムランキング」も是非ご覧ください。生産管理システムは、自社の製品・生産方式・企業規模などに適したものを導入しないと、得られるメリットが限定されてしまいます。事前適合性チェックや生産管理システムを選ぶ前に押さえておきたいポイントも解説していますので、製品選びの参考にしてみてください。